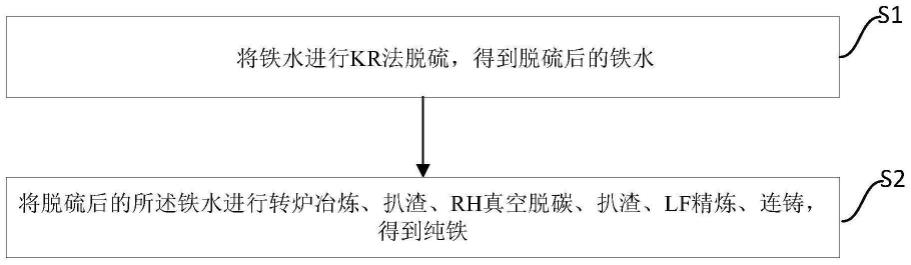
1.本技术涉及钢铁冶炼技术领域,尤其涉及一种纯铁的冶炼方法。
背景技术:2.高品质特种钢专用纯铁主要用于航空航天等尖端科技领域高温合金的生产,生产工艺复杂、技术含量高、冶炼难度大。用户对产品纯度要求很高,尤其对磷、硫、硅、锰含量提出极其苛刻的控制要求。
3.目前,国内冶炼工艺一些钢铁企业能生产普通的工业纯铁,但很难稳定批量生产高纯度、极低磷、硫、硅、锰含量工业纯铁。
技术实现要素:4.本技术实施例提供了一种纯铁的冶炼方法,以解决现有纯铁的冶炼方法所得纯铁的品质较低,无法满足航空航天等尖端科技领域高温合金的使用要求的技术问题。
5.第一方面,本技术实施例提供了一种纯铁的冶炼方法,所述冶炼方法包括:
6.将铁水进行kr法脱硫,得到脱硫后的铁水;
7.将脱硫后的所述铁水进行转炉冶炼、扒渣、rh真空脱碳、扒渣、lf精炼、连铸,得到纯铁;
8.其中,以质量分数计,脱硫后的所述铁水中硫含量≤0.0008%;转炉冶炼后铁水中磷含量≤0.002%、硫含量≤0.0015%、硅含量≤0.008%、锰含量≤0.01%。
9.进一步地,所述kr法脱硫采用分段脱硫法,具体过程为:
10.0~3min,以每吨铁水计,脱硫剂加入量为4~5kg,搅拌转速80~100r/min,结束时扒渣;
11.3~7min,以每吨铁水计,脱硫剂加入量为2~4kg,搅拌转速50~70r/min,结束时扒渣;
12.7~12min,以每吨铁水计,脱硫剂加入量为2~3kg,搅拌转速80~100r/min,结束时扒渣。
13.进一步地,所述转炉冶炼采用双渣法转炉冶炼。
14.进一步地,所述双渣法转炉冶炼的工艺参数包括:转炉吹炼时长为4~5min;目标出钢温度为1610~1630℃;二次造渣时,以每吨铁水计,白灰加入量为20-25kg,轻烧白云石加入量为5-10kg。
15.进一步地,所述rh真空脱碳的工艺参数包括:rh顶枪以氧气为载气喷吹石灰粉,所述氧气的流量为200-400nl/min,所述石灰粉的喷吹速率为50-100kg/min,喷吹时间为4-6min;以质量分数计,rh真空脱碳后铁水中碳含量≤0.0012%、磷含量≤0.0018%。
16.进一步地,所述石灰粉的喷吹量按式1进行控制;
17.式1:m
cao
=230.4ln[%p]+1859.1;
[0018]
式1中:m
cao
为石灰粉加入量,单位为kg;[%p]为转炉终点磷含量,%。
[0019]
进一步地,所述lf精炼的工艺参数包括:采用白灰、铝矾土和萤石进行二次造渣,以每吨铁水计,渣量为5-10kg,精炼渣碱度(cao%/sio2%)≥7,炉渣t.fe≤0.5%;以质量分数计,lf精炼后铁水中硫含量≤0.0008%。
[0020]
进一步地,所述纯铁的碳含量为0.0005-0.0015%。
[0021]
进一步地,所述纯铁的硫含量为0.0004-0.001%。
[0022]
进一步地,所述纯铁的磷含量为0.0007-0.002%,锰含量为0.008-0.015%,硅含量为0.003-0.008%。
[0023]
本技术实施例提供的上述技术方案与现有技术相比具有如下优点:
[0024]
本技术实施例提供了一种纯铁的冶炼方法,该冶炼采用“kr+转炉+扒渣+rh+扒渣+lf+连铸”生产工艺,各个工艺逐步控制铁水中硫元素、磷元素、硅元素、锰元素含量,尤其是,kr法脱硫结束后铁水硫含量控制在≤0.0008%,转炉冶炼后控制磷含量≤0.002%、硫含量≤0.0015%、硅含量≤0.008%、锰含量≤0.01%,从而获得超低磷、硫、硅、锰的高品质工业纯铁,达到航空航天等尖端科技领域高温合金的使用要求。
附图说明
[0025]
此处的附图被并入说明书中并构成本说明书的一部分,示出了符合本发明的实施例,并与说明书一起用于解释本发明的原理。
[0026]
为了更清楚地说明本发明实施例或现有技术中的技术方案,下面将对实施例或现有技术描述中所需要使用的附图作简单地介绍,显而易见地,对于本领域普通技术人员而言,在不付出创造性劳动性的前提下,还可以根据这些附图获得其他的附图。
[0027]
图1为本技术实施例提供的一种纯铁的冶炼方法的流程示意图。
具体实施方式
[0028]
下面将结合具体实施方式和实施例,具体阐述本发明,本发明的优点和各种效果将由此更加清楚地呈现。本领域技术人员应理解,这些具体实施方式和实施例是用于说明本发明,而非限制本发明。
[0029]
在整个说明书中,除非另有特别说明,本文使用的术语应理解为如本领域中通常所使用的含义。因此,除非另有定义,本文使用的所有技术和科学术语具有与本发明所属领域技术人员的一般理解相同的含义。若存在矛盾,本说明书优先。
[0030]
除非另有特别说明,本发明中用到的各种原材料、试剂、仪器和设备等,均可通过市场购买得到或者可通过现有方法制备得到。
[0031]
高品质特种钢专用纯铁主要用于航空航天等尖端科技领域高温合金的生产,生产工艺复杂、技术含量高、冶炼难度大。用户对产品纯度要求很高,尤其对磷、硫、硅、锰含量提出极其苛刻的控制要求。
[0032]
目前,国内冶炼工艺一些钢铁企业能生产普通的工业纯铁,但很难稳定批量生产高纯度、极低磷、硫、硅、锰含量工业纯铁。
[0033]
本发明实施例提供的技术方案为解决上述技术问题,总体思路如下:
[0034]
第一方面,本技术实施例提供了一种纯铁的冶炼方法,所述冶炼方法包括:
[0035]
将铁水进行kr法脱硫,得到脱硫后的铁水;
[0036]
将脱硫后的所述铁水进行转炉冶炼、扒渣、rh真空脱碳、扒渣、lf精炼、连铸,得到纯铁;其中,以质量分数计,脱硫后的所述铁水中硫含量≤0.0008%;转炉冶炼后铁水中磷含量≤0.002%、硫含量≤0.0015%、硅含量≤0.008%、锰含量≤0.01%。
[0037]
本技术实施例提供了一种纯铁的冶炼方法,该冶炼采用“kr+转炉+扒渣+rh+扒渣+lf+连铸”生产工艺,各个工艺逐步控制铁水中硫元素、磷元素、硅元素、锰元素含量,尤其是,kr法脱硫结束后铁水硫含量控制在≤0.0008%,转炉冶炼后控制磷含量≤0.002%、硫含量≤0.0015%、硅含量≤0.008%、锰含量≤0.01%,从而获得超低磷、硫、硅、锰的高品质工业纯铁,达到航空航天等尖端科技领域高温合金的使用要求。
[0038]
本技术中,kr(kambara reactor)法脱硫具体为kr机械搅拌法,是将浇注耐火材料并经过烘烤的十字形搅拌头,浸入铁水包熔池适宜深度,借其旋转产生的漩涡,经过称量的脱硫剂由给料器加入到铁水表面,并被旋涡卷入铁水中使氧化钙基脱硫粉剂与铁水充分接触反应,达到脱硫目的。
[0039]
本技术中,转炉冶炼又称为转炉炼钢(converter steelmaking),是以铁水、废钢等为主要原料,不借助外加能源,靠铁液本身的物理热和铁液组分间化学反应产生热量而在转炉中完成炼钢过程。
[0040]
本技术中,rh真空脱碳又被称为rh真空循环脱气精炼法,本技术主要采用的是深脱碳处理模式。
[0041]
本技术中,lf精炼又被称为lf(ladle furnace)精炼技术,是炉外精炼的主要方法之一。
[0042]
作为本发明实施例的一种实施方式,所述kr法脱硫采用分段脱硫法,具体过程为:
[0043]
0~3min,以每吨铁水计,脱硫剂加入量为4~5kg,搅拌转速80~100r/min,结束时扒渣;
[0044]
3~7min,以每吨铁水计,脱硫剂加入量为2~4kg,搅拌转速50~70r/min,结束时扒渣;
[0045]
7~12min,以每吨铁水计,脱硫剂加入量为2~3kg,搅拌转速80~100r/min,结束时扒渣。
[0046]
本技术中,kr脱硫阶段采用分段脱硫法,将铁水中的硫含量控制在≤0.0008%,其优势在于前期硫含量高、脱硫剂加入量大、搅拌相对较弱;后期硫含量较低,硫元素传质成为限制性环节,该阶段采用强搅拌、低脱硫剂加入量。通过上述方法硫含量能稳定控制到≤0.0008%。在一些具体实施例中,脱硫剂可采用如电石脱硫剂、镁脱硫剂等市售产品。
[0047]
作为本发明实施例的一种实施方式,所述转炉冶炼采用双渣法转炉冶炼。
[0048]
作为本发明实施例的一种实施方式,所述双渣法转炉冶炼的工艺参数包括:转炉吹炼时长为4~5min;目标出钢温度为1610~1630℃;二次造渣时,以每吨铁水计,白灰加入量为20-25kg,轻烧白云石加入量为5-10kg。
[0049]
本技术中,转炉冶炼采用双渣法控制磷含量,转炉吹炼4min-5min左右,根据前期化渣情况提枪倒渣,要求将炉渣倒出70%以上,二次造渣要求白灰控制在吨钢20-25kg,轻烧控制在吨钢5-10kg,测量完tsc后在二级模型计算动态矿石量基础上增加300-500kg,模型目标碳按0.03%,目标温度按1610~1630℃,较佳地,1620℃控制,当计算温度达到目标出钢温度后提枪,确保转炉终点氧>600ppm,碳≤0.03%。控制磷含量≤0.002%、硫含量≤
0.0015%、硅含量≤0.008%、锰含量≤0.01%。出钢过程严格控制下渣,出钢时加入5-6kg/t小粒白灰和0.8-1.0kg/t萤石。
[0050]
作为本发明实施例的一种实施方式,所述rh真空脱碳的工艺参数包括:rh顶枪以氧气为载气喷吹石灰粉,所述氧气的流量为200-400nl/min,所述石灰粉的喷吹速率为50-100kg/min,喷吹时间为4-6min;以质量分数计,rh真空脱碳后铁水中碳含量≤0.0012%、磷含量≤0.0018%。
[0051]
本技术中,转炉冶炼出钢后,进行钢包一次扒渣,后进行rh深真空脱碳处理模式,全部炉次钢液进入真空室后吹氧3-5min进行脱碳,吹氧脱碳结束后利用rh多功能顶枪以氧气为载气喷吹石灰粉,氧气流量控制在200-400nl/min,石灰粉喷吹速率为50-100kg/min,喷吹时间控制在4-6min,利用高氧条件进行脱磷,脱磷结束后加铝脱氧,并循环3-6min,rh结束碳含量≤0.0012%、磷含量≤0.0018%。
[0052]
作为本发明实施例的一种实施方式,所述石灰粉的喷吹量按式1进行控制;
[0053]
式1:m
cao
=230.4ln[%p]+1859.1;
[0054]
作为本发明实施例的一种实施方式,所述lf精炼的工艺参数包括:采用白灰、铝矾土和萤石进行二次造渣,以每吨铁水计,渣量为5-10kg,精炼渣碱度(cao%/sio2%)≥7,炉渣t.fe≤0.5%;以质量分数计,lf精炼后铁水中硫含量≤0.0008%。
[0055]
本技术中,rh结束后进行钢包二次扒渣,扒除高氧化性、高磷含量渣,扒渣后亮面达到95%以上,后进入lf造还原性渣进行脱硫、升温及合金化。lf精炼采用白灰、铝矾土和萤石进行二次造渣,渣量控制在吨钢5-10kg,精炼渣碱度(cao%/sio2%)≥7,炉渣t.fe≤0.5%,化渣后进行强搅拌脱硫,底吹强度控制在4-6nl/min
·
t,搅拌时间5-10min,lf精炼结束时钢液硫含量控制在0.0008%以下。lf精炼结束后进行板坯连铸。
[0056]
综上所述,本发明在kr脱硫阶段采用分段脱硫法,将铁水中的硫含量控制在≤0.0008%,其优势在于前期硫含量高、脱硫剂加入量大、搅拌相对较弱;后期硫含量较低,硫元素传质成为限制性环节,该阶段采用强搅拌、低脱硫剂加入量。通过上述方法硫含量能稳定控制到≤0.0008%。转炉采用双渣法,重点控制磷、锰、硅含量,rh采用吹氧脱碳和氧气喷吹石灰粉脱磷,利用高氧化性条件脱碳和脱磷,完成后钢液脱氧。进lf之前扒除高氧化性钢包渣,lf重新造还原性渣进行脱硫。以上方法在精炼过程中把脱碳、脱磷和脱硫工序分开,并针对不同工序需要的顶渣条件进行炉渣调整,保证了钢液含量的稳定性。
[0057]
下面结合具体实施例,进一步阐述本发明。应理解,这些实施例仅用于说明本发明而不用于限制本发明的范围。下列实施例中未注明具体条件的实验方法,通常按照国家标准测定。若没有相应的国家标准,则按照通用的国际标准、常规条件、或按照制造厂商所建议的条件进行。
[0058]
实施例1
[0059]
本例提供一种纯铁的冶炼方法,如图1所示,冶炼采用“kr+转炉+扒渣+rh+扒渣+lf+连铸”生产工艺。具体包括:
[0060]
铁水预处理kr脱硫采用分段脱硫法,前3min脱硫剂加入量4kg/t,搅拌头转速80r/min,后进行第一次扒渣;3-7min脱硫剂加入量3kg/t,搅拌头转速50r/min,后进行第二次扒渣;7-12min脱硫剂加入量2kg/t,搅拌头转速100r/min,后进行第三次扒渣,结束后铁水硫含量控制为0.0007%;
[0061]
转炉冶炼采用双渣法控制磷含量,转炉吹炼4min-5min左右,根据前期化渣情况提枪倒渣,要求将炉渣倒出70%以上,二次造渣要求白灰控制在吨钢20-25kg,轻烧控制在吨钢5-10kg,测量完tsc后在二级模型计算动态矿石量基础上增加300-500kg,模型目标碳按0.03%,目标温度按1620℃控制,当计算温度达到目标出钢温度后提枪,确保转炉终点氧>600ppm,碳≤0.03%。控制磷含量≤0.002%、硫含量≤0.0015%、硅含量≤0.008%、锰含量≤0.01%。出钢过程严格控制下渣,出钢时加入5-6kg/t小粒白灰和0.8-1.0kg/t萤石;
[0062]
出钢后,进行钢包一次扒渣,后进行rh深真空脱碳处理模式,全部炉次钢液进入真空室后吹氧4min进行脱碳,吹氧脱碳结束后利用rh多功能顶枪以氧气为载气喷吹石灰粉,氧气流量控制在300nl/min,石灰粉喷吹速率为80kg/min,喷吹量按如下控制:m
cao
=230.4ln[%p]+1859.1,式中:m
cao
为石灰加入量,kg;[%p]为转炉终点磷含量,%。
[0063]
计算可得喷吹量为400kg,喷吹时间控制为5min,利用高氧条件进行脱磷,脱磷结束后加铝脱氧,并循环5min,rh结束碳含量为0.001%、磷含量为0.0015%;
[0064]
rh结束后进行钢包二次扒渣,扒除高氧化性、高磷含量渣,扒渣后亮面达到97%,后进入lf造还原性渣进行脱硫、升温及合金化,lf精炼采用白灰、铝矾土和萤石进行二次造渣,渣量控制在吨钢8kg,精炼渣碱度(cao%/sio2%)≥7,炉渣t.fe≤0.5%,化渣后进行强搅拌脱硫,底吹强度控制在5nl/min
·
t,搅拌时间8min,;lf精炼结束时钢液硫含量控制为0.0005%,lf精炼结束后进行板坯连铸。
[0065]
本实施例中高纯度工业纯铁成品成分如下表1所示。
[0066]
表1成品成分/%(以质量分数计)
[0067]
成分csimnpsal要求范围≤0.0015≤0.01≤0.01≤0.002≤0.0010.015-0.04实际值0.00120.0080.0090.00150.00060.032
[0068]
实施例2
[0069]
本例提供一种纯铁的冶炼方法,冶炼采用“kr+转炉+扒渣+rh+扒渣+lf+连铸”生产工艺。具体包括:
[0070]
铁水预处理kr脱硫采用分段脱硫法,前3min脱硫剂加入量5kg/t,搅拌头转速90r/min,后进行第一次扒渣;3-7min脱硫剂加入量4kg/t,搅拌头转速70r/min,后进行第二次扒渣;7-12min脱硫剂加入量3kg/t,搅拌头转速100r/min,后进行第三次扒渣,结束后铁水硫含量控制为0.0008%;
[0071]
转炉冶炼采用双渣法控制磷含量,终点控制磷含量为0.0016%、硫含量为0.0012%、硅含量为0.008%、锰含量为0.01%。出钢过程严格控制下渣,出钢时加入5kg/t小粒白灰和1.0kg/t萤石;
[0072]
出钢后,进行钢包一次扒渣,后进行rh深真空脱碳处理模式,全部炉次钢液进入真空室后吹氧5min进行脱碳,吹氧脱碳结束后利用rh多功能顶枪以氧气为载气喷吹石灰粉,氧气流量控制在300nl/min,石灰粉喷吹速率为80kg/min,喷吹量按如下控制:
[0073]mcao
=230.4ln[%p]+1859.1,式中:m
cao
为石灰加入量,kg;[%p]为转炉终点磷含量,%。
[0074]
计算可得喷吹量为375kg,喷吹时间控制为4.7min,利用高氧条件进行脱磷,脱磷结束后加铝脱氧,并循环5min,rh结束碳含量为0.0009%、磷含量为0.0013%;
[0075]
rh结束后进行钢包二次扒渣,扒除高氧化性、高磷含量渣,扒渣后亮面达到97%,后进入lf造还原性渣进行脱硫、升温及合金化;lf精炼结束时钢液硫含量控制为0.0006%;lf精炼结束后进行板坯连铸。
[0076]
本实施例中高纯度工业纯铁成品成分如下表2所示。
[0077]
表2成品成分/%(以质量分数计)
[0078]
成分csimnpsal要求范围≤0.0015≤0.02≤0.015≤0.002≤0.0010.015-0.04实际值0.00110.0120.0110.00130.00070.029
[0079]
综上所述,本技术实施例提供了一种工业纯铁冶炼的方法,通过该方法能生产出超低磷、硫、硅、锰的工业纯铁,产品能满足航空航天用超纯工业纯铁的需求。通过该方法生产的工业纯铁碳含量稳定控制在0.0005-0.0015%、硫含量控制在0.0004-0.001%、磷含量控制在0.0007-0.002%、锰含量控制在0.008-0.015%、硅含量控制在0.003-0.008%。
[0080]
需要说明的是,在本文中,诸如“第一”和“第二”等之类的关系术语仅仅用来将一个实体或者操作与另一个实体或操作区分开来,而不一定要求或者暗示这些实体或操作之间存在任何这种实际的关系或者顺序。而且,术语“包括”、“包含”或者其任何其他变体意在涵盖非排他性的包含,从而使得包括一系列要素的过程、方法、物品或者设备不仅包括那些要素,而且还包括没有明确列出的其他要素,或者是还包括为这种过程、方法、物品或者设备所固有的要素。在没有更多限制的情况下,由语句“包括
……”
限定的要素,并不排除在包括所述要素的过程、方法、物品或者设备中还存在另外的相同要素。
[0081]
以上所述仅是本发明的具体实施方式,使本领域技术人员能够理解或实现本发明。对这些实施例的多种修改对本领域的技术人员来说将是显而易见的,本文中所定义的一般原理可以在不脱离本发明的精神或范围的情况下,在其它实施例中实现。因此,本发明将不会被限制于本文所示的这些实施例,而是要符合与本文所申请的原理和新颖特点相一致的最宽的范围。