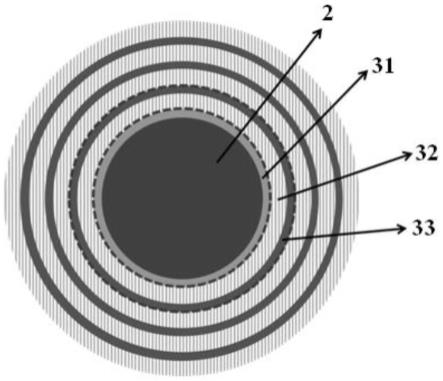
1.本发明涉及材料制造技术领域,尤其涉及一种基于等离子喷涂-激光熔覆制备复合构件的方法。
背景技术:2.难熔金属-陶瓷复合材料既具有陶瓷材料的低热导率、高耐磨耐蚀性能,又兼具难熔金属的高熔点、高韧性和优良的抗烧蚀性能,广泛应用于武器装备、航空航天等领域。目前,针对形状简单的难熔金属-陶瓷复合材料的零部件,通常利用粉末冶金的方法进行制备,主要包括将难熔金属-陶瓷复合材料粉体球磨均匀化、压制成型、烧结致密化、机械加工等步骤,所制得的零部件致密度高、力学性能优异。然而,利用粉末冶金的方法针对回转体构件等异形件进行难熔金属-陶瓷复合材料制备时,压制成型难度高,同时需要采用机加工去除芯部大量难熔金属-陶瓷复合材料,造成材料浪费、增加生产成本,且芯部的高耐磨耐蚀、高熔点的难熔金属-陶瓷复合材料不易去除,也对利用粉末冶金法制备回转体构件等异形件的制备造成困难。
3.专利文献cn114147436a中公开了一种具有周期性性梯度渐变结构复合构件的制备方法,其通过在石墨芯轴表面采用等离子喷涂陶瓷层、陶瓷-金属层与金属层,以及等离子喷涂后采用热等静压扩散处理,再利用机加工去除容易处理的石墨芯轴等手段,从而实现回转体构件等异形件的制备。然而,该手段中等离子喷涂层(即陶瓷层、陶瓷-金属层与金属层)的致密度、孔隙率、晶粒大小及各层之间的结合强度与热等静压工艺中的高温高压直接相关,即若需要获得致密化程度高、孔隙率少、晶粒小的等离子喷涂层,需要热等静压工艺中提供较高的烧结温度与加载压力,工艺复杂,生产能耗大、成本高,危险系数大,不利于难熔金属-陶瓷复合材料的回转体构件等异形件的大批量制备。
技术实现要素:4.针对以上现有技术存在的问题,本发明的目的在于提供一种基于等离子喷涂-激光熔覆制备复合构件的方法,以解决上述背景技术中存在的问题,该方法适用于回转体构件等异形件的制备,无需进行高温高压处理、有效节约生产能耗,生产成本低,安全性高,适用于难熔金属-陶瓷复合材料的回转体构件等异形件的大批量制备。
5.本发明的目的通过以下技术方案实现:一种基于等离子喷涂-激光熔覆制备复合构件的方法,其特征在于:包括:步骤a、石墨芯模的制备;步骤b、采用等离子喷涂在石墨芯模表面喷涂第二基体层;步骤c、采用激光熔覆在第二基体层表面制备交替层,交替层为难熔金属层与陶瓷层相互交替叠加;步骤d、采用等离子喷涂在步骤c的交替层表面制备缓和层;步骤e、循环进行步骤c与步骤d且最外层为交替层,得到高致密复合构件;步骤f、机加工去除石墨芯模,获得高致密异形构件。
6.作进一步优化,所述步骤 a具体为:根据所需制备的复合构件的形状及尺寸,设计
并机加工出两端具有夹持端的石墨芯模;所述石墨芯模采用具有优异的高温强度、化学稳定性和机械加工特性的石墨材料(即三高石墨),石墨材料密度≥1.8g/cm3。
7.作进一步优化,所述第二基体层、难熔金属层、缓和层的材料相同;均为w、mo、ta难熔金属单质中的任一种或w/mo、mo/la、w/ta难熔合金中的任一种。
8.作进一步优化,所述陶瓷层的材料为zro2、al2o3、ysz、la2zr2o7中的一种或多种。
9.本技术首先通过在石墨芯模表面通过等离子喷涂制备第二基体层,起到易于脱模的作用、避免激光直接在石墨芯模表面进行熔覆而出现难熔金属与石墨芯模表面结合的问题;通过在第二基体层或缓和层表面进行难熔金属层的激光熔覆,一是利用激光熔覆过程中的激光散火对等离子喷涂层实现重熔,从而细化等离子喷涂层的晶粒、减小等离子喷涂层的孔隙、提高等离子喷涂层的致密度,二是利用激光熔覆的难熔金属层对等离子喷涂层的孔隙实现封孔,实现等离子喷涂层的完全致密化、避免出现孔隙,三是通过难溶金属层与第二基体层或缓和层之间的同质相容性,提高交替层与第二基体层、交替层与缓和层之间的结合强度,减小交替层与第二基体层、交替层与缓和层之间的应力,避免第二基体层、交替层与缓和层之间出现明显界限,确保构件的整体性。
10.同时,通过第二基体层、交替层、缓和层、交替层、缓和层、
…
、交替层之间的交替叠加,通过等离子喷涂的金属层(即缓和层)形成对激光熔覆交替层之间的应力缓和,从而缓解大厚度的激光熔覆交替层的内应力,避免制备过程中由于应力 过大而出现分层、脱落、剥离等问题;并且,在制备第二基体层或缓和层后均进行交替层的激光重熔,与等离子喷涂后进行热等静压扩散的方案相比,不会出现由外层向内层的涂层之间致密度与晶粒的梯度变化,确保每层等离子喷涂层致密度与晶粒大小的一致性, 从而保证最终构件的性能的均匀性。此外,通过难熔金属层与陶瓷层的交替叠加,有效缓解金属与陶瓷间热膨胀系数差异造成热应力积累的问题,避免陶瓷层由于应力累积而出现开裂、裂纹扩展等问题,配合难熔金属层与第二基体层、难熔金属层与缓和层之间的应力缓和,进一步避免各层之间的相互剥离、开裂或形成明显界线的问题,保证构件的均匀性与整体性。
11.作进一步优化,所述第二基体层的厚度为0.5~1mm,所述缓和层的厚度为0.5~1mm。
12.作进一步优化,所述交替层的内层与外层均为难熔金属层(即交替层通过难熔金属层与第二基体层、缓和层、外部空气层接触)。
13.作进一步优化,交替层的总厚度为2.5~5mm且交替层的交替层数为3、5或7层;交替层中单层厚度为0.6~1.2mm。
14.优选的,所述陶瓷层厚度大于难熔金属层厚度。
15.作进一步优化,所述等离子喷涂参数为:喷涂功率30~36kw,喷涂距离100~150mm,送粉速率10~50g/min。
16.作进一步优化,所述激光熔覆参数为:难熔金属层:激光功率1.2~1.8kw,送粉速率80~120g/min;陶瓷层:激光功率2.2~3kw,送粉速率20~60g/min。
17.作进一步优化,所述高致密异形构件的壁厚为10~30mm。
18.本发明具有如下技术效果:本技术采用等离子喷涂+激光熔覆的复合工艺手段,同时配合第二基体层、交替层、缓和层的结构设计,实现了难熔金属-陶瓷复合材料构件的制备;相比于传统的等离子
喷涂技术,本技术通过激光熔覆实现对制备的等离子喷涂层的重熔,使得等离子喷涂层致密性高、沉积效率高、层与层之间的连接强度高,且有效减少构件中孔洞、裂纹等缺陷;同时通过等离子喷涂层(第二基体层或缓和层)实现对交替层与石墨芯模、交替层与交替层之间的应力缓和,从而避免层与层之间应力过大而出现剥落、开裂等问题,确保复合材料构件具有优异的综合性能。与等离子喷涂后进行热等静压扩散相比,本技术用于应力缓解的各等离子喷涂层一致性好、不会出现明显的梯度差异,同时有效节省能耗、节约生产成本、缩短工艺周期,安全性高,适用于工业化大批量生产制造。
附图说明
19.图1为本发明实施例中复合构件制备过程中的宏观结构示意图。
20.图2为本发明实施例中复合构件制备过程中的横向截面的微观机构示意图。
21.图3为本发明实施例中复合构件制备过程中的纵向截面的微观机构示意图。
22.其中,1、夹持端;2、石墨芯模;3、复合材料层;31、第二基体层;32、交替层;321、难熔金属层;322、陶瓷层;33、缓和层。
具体实施方式
23.下面将结合本发明实施例中的附图,对本发明实施例中的技术方案进行清楚、完整地描述,显然,所描述的实施例仅仅是本发明一部分实施例,而不是全部的实施例。基于本发明中的实施例,本领域普通技术人员在没有做出创造性劳动前提下所获得的所有其他实施例,都属于本发明保护的范围。
24.实施例1:一种基于等离子喷涂-激光熔覆制备复合构件的方法,其特征在于:包括:步骤a、石墨芯模的制备:根据所需制备的复合构件的形状及尺寸,设计并机加工出两端具有夹持端的石墨芯模(如图1所示的拉瓦尔形石墨芯模);石墨芯模采用具有优异的高温强度、化学稳定性和机械加工特性的石墨材料(即三高石墨),石墨材料密度≥1.8g/cm3。
25.步骤b、采用等离子喷涂在石墨芯模表面喷涂第二基体层:将石墨芯模的夹持端固定于旋转夹持工装上(采用本领域常见的旋转夹持工装即可),采用等离子喷涂设备在石墨芯模表面喷涂第二基体层;第二基体层的材料为mo金属单质;第二基体层厚度为0.5mm;等离子喷涂参数为:喷涂功率30kw,喷涂距离100mm,送粉速率35g/min;步骤c、采用激光熔覆在第二基体层表面制备交替层,交替层为难熔金属层与陶瓷层相互交替叠加;具体为:首先通过激光熔覆在第二基体层的表面制备覆盖金属层,难熔金属层的材料为mo金属单质,难熔金属层的厚度为0.6mm;激光熔覆的参数为:激光功率1.2kw,送粉速率90g/min;然后通过激光熔覆在难熔金属层表面覆盖陶瓷层,陶瓷层的材料为zro2,陶瓷层厚度为0.8mm;激光熔覆的参数为:激光功率2.2kw,送粉速率30g/min;
交替叠加制备难熔金属层与陶瓷层且最外层为难熔金属层,交替层的总层数为7层,总厚度为4.8mm;步骤d、采用等离子喷涂在步骤c的交替层表面制备缓和层:采用等离子喷涂设备在交替层的难熔金属层表面喷涂缓和层;缓和层的材料为mo金属单质;缓和层厚度为0.5mm;等离子喷涂参数为:喷涂功率30kw,喷涂距离100mm,送粉速率35g/min;步骤e、循环进行步骤c与步骤d且最外层为交替层,直至石墨芯模外壁复合材料的厚度为10.6mm,得到高致密复合构件;步骤f、机加工去除石墨芯模,获得高致密异形构件;例如:采用车刀去除石墨芯模夹持端,再采用内孔钻头将石墨芯模的轴整体顶出,最后采用车刀或铣刀对构件内部与外壁进行多余材料的去除。
26.实施例2:一种基于等离子喷涂-激光熔覆制备复合构件的方法,其特征在于:包括:步骤a、石墨芯模的制备:根据所需制备的复合构件的形状及尺寸,设计并机加工出两端具有夹持端的石墨芯模(如图1所示的拉瓦尔形石墨芯模);石墨芯模采用具有优异的高温强度、化学稳定性和机械加工特性的石墨材料(即三高石墨),石墨材料密度≥1.8g/cm3。
27.步骤b、采用等离子喷涂在石墨芯模表面喷涂第二基体层:将石墨芯模的夹持端固定于旋转夹持工装上(采用本领域常见的旋转夹持工装即可),采用等离子喷涂设备在石墨芯模表面喷涂第二基体层;第二基体层的材料为mo/la合金;第二基体层厚度为0.7mm;等离子喷涂参数为:喷涂功率33kw,喷涂距离125mm,送粉速率25g/min;步骤c、采用激光熔覆在第二基体层表面制备交替层,交替层为难熔金属层与陶瓷层相互交替叠加;具体为:首先通过激光熔覆在第二基体层的表面制备覆盖金属层,难熔金属层的材料为mo/la合金,难熔金属层的厚度为0.8mm;激光熔覆的参数为:激光功率1.5kw,送粉速率100g/min;然后通过激光熔覆在难熔金属层表面覆盖陶瓷层,陶瓷层的材料为al2o3,陶瓷层厚度为1.0mm;激光熔覆的参数为:激光功率2.6kw,送粉速率40g/min;交替叠加制备难熔金属层与陶瓷层且最外层为难熔金属层,交替层的总层数为5层,总厚度为4.4mm;步骤d、采用等离子喷涂在步骤c的交替层表面制备缓和层:采用等离子喷涂设备在交替层的难熔金属层表面喷涂缓和层;缓和层的材料为mo/la、合金;缓和层厚度为0.7mm;等离子喷涂参数为:喷涂功率33kw,喷涂距离125mm,送粉速率25g/min;步骤e、循环进行步骤c与步骤d且最外层为交替层,直至石墨芯模外壁复合材料的厚度为10.2mm,得到高致密复合构件;步骤f、机加工去除石墨芯模,获得高致密异形构件;例如:采用车刀去除石墨芯模
夹持端,再采用内孔钻头将石墨芯模的轴整体顶出,最后采用车刀或铣刀对构件内部与外壁进行多余材料的去除。
28.实施例3:一种基于等离子喷涂-激光熔覆制备复合构件的方法,其特征在于:包括:步骤a、石墨芯模的制备:根据所需制备的复合构件的形状及尺寸,设计并机加工出两端具有夹持端的石墨芯模(如图1所示的拉瓦尔形石墨芯模);石墨芯模采用具有优异的高温强度、化学稳定性和机械加工特性的石墨材料(即三高石墨),石墨材料密度≥1.8g/cm3。
29.步骤b、采用等离子喷涂在石墨芯模表面喷涂第二基体层:将石墨芯模的夹持端固定于旋转夹持工装上(采用本领域常见的旋转夹持工装即可),采用等离子喷涂设备在石墨芯模表面喷涂第二基体层;第二基体层的材料为w/ta合金;第二基体层厚度为1mm;等离子喷涂参数为:喷涂功率36kw,喷涂距离150mm,送粉速率45g/min;步骤c、采用激光熔覆在第二基体层表面制备交替层,交替层为难熔金属层与陶瓷层相互交替叠加;具体为:首先通过激光熔覆在第二基体层的表面制备覆盖金属层,难熔金属层的材料为w/ta合金,难熔金属层的厚度为1mm;激光熔覆的参数为:激光功率1.8kw,送粉速率80g/min;然后通过激光熔覆在难熔金属层表面覆盖陶瓷层,陶瓷层的材料为la2zr2o7,陶瓷层厚度为1.2mm;激光熔覆的参数为:激光功率3kw,送粉速率50g/min;交替叠加制备难熔金属层与陶瓷层且最外层为难熔金属层,交替层的总层数为3层,总厚度为3.2mm;步骤d、采用等离子喷涂在步骤c的交替层表面制备缓和层:采用等离子喷涂设备在交替层的难熔金属层表面喷涂缓和层;缓和层的材料为w/ta合金;缓和层厚度为1mm;等离子喷涂参数为:喷涂功率36kw,喷涂距离150mm,送粉速率45g/min;步骤e、循环进行步骤c与步骤d且最外层为交替层,直至石墨芯模外壁复合材料的厚度为16.8mm,得到高致密复合构件;步骤f、机加工去除石墨芯模,获得高致密异形构件;例如:采用车刀去除石墨芯模夹持端,再采用内孔钻头将石墨芯模的轴整体顶出,最后采用车刀或铣刀对构件内部与外壁进行多余材料的去除。
30.尽管已经示出和描述了本发明的实施例,对于本领域的普通技术人员而言,可以理解在不脱离本发明的原理和精神的情况下可以对这些实施例进行多种变化、修改、替换和变型,本发明的范围由所附权利要求及其等同物限定。