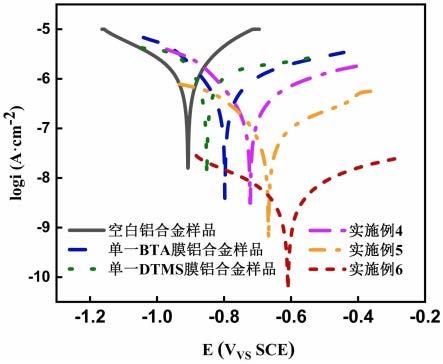
1.本发明属于金属防腐蚀技术领域,涉及一种铝合金表面气相组装复合硅烷膜及其制备方法。
背景技术:2.铝合金具有高比强度、低密度和优良加工性能等优点,在现代工业体系中得到广泛应用。同时,自然形成的氧化铝薄膜可以防止其在轻度腐蚀环境中的腐蚀。但是,铝合金的氧化膜在腐蚀性介质中容易被破坏,这会引起铝合金基体的腐蚀,如点蚀、晶间腐蚀等,因此,铝及其合金表面需要处理以提高其防腐能力。
3.铬酸盐转换膜多年来一直用于抑制铝合金的腐蚀,它们除了增强的防腐蚀保护外,还对有机涂层具有良好的附着力。由于这些铬酸盐的致癌特性,人们一直需要寻找环境友好的缓蚀剂,硅烷因其环保和良好的防腐性能而被提出作为铬酸盐的替代品。
4.专利cn102677039a公开了一种铝及铝合金表面硅烷稀士复合保护膜及其制备方法,是由预处理后的铝或铝合金依次浸没在处理液a(γ-氨丙基三乙氧基硅烷、无水乙醇和蒸馏水混合后调ph值10-13)和处理液b(氯化稀土盐、过氧化氢溶液、氢氧化钠和蒸馏水混合后调ph值4-5)中然后于60-140℃固化后得到的复合保护膜。此专利进行硅烷处理后,滴干过程时间长,会产生生锈的问题,不利于推广应用。
5.专利cn106929863a公开了一种提升铝合金表面硅烷膜性能的方法,将btespt硅烷偶联剂、乙醇、去离子水、甲基丙烯磺酸钠混合后,搅拌6-10min,成膜液制备完成,水解3-5h;将铝合金材料放入制备完成的成膜液中,2-5min后,向成膜液中加入成膜液重量0.03-0.05倍重的磷酸二异辛酯,继续浸泡,取出铝合金材料,将其放置在通风处静置,制得成品。此专利操作过程繁琐,使用磷酸二异辛酯对环境有害,也不利于生产应用推广。
6.虽然硅烷在金属表面处理液中得到应用,但较难有快速便捷的成膜质量;原液存放周期较长,易于发生缩合,槽液在气温较高、氟离子含量高时也都会影响质量。而且,硅烷自组装膜层太薄,对腐蚀性介质侵蚀的阻挡作用有限,限制了其推广应用。
技术实现要素:7.本发明的目的就是为了克服上述现有技术存在的单一硅烷膜不致密、硅烷处理后滴干时间长和硅烷膜耐蚀性不理想等缺陷而提供一种铝合金表面气相组装复合硅烷膜及其制备方法,本发明采用气相组装的方式制备复合硅烷膜,加快了硅烷成膜的速度,操作简单,节约成本,安全环保,提高硅烷膜的耐腐蚀性能,这对复合硅烷膜的发展具有重大意义。
8.本发明的目的可以通过以下技术方案来实现:
9.本发明的技术方案之一在于,提供一种铝合金表面气相组装复合硅烷膜的制备方法,该制备方法包括以下步骤:
10.(1)铝合金经打磨、拋光处理和清洗后备用,将处理好的铝合金试样放置密闭容器上方,并将气相组装药品有机硅烷化合物和增效剂置于密闭容器底部,气相组装药品和铝
合金试样不直接接触,保持一定距离;
11.(2)控制一定的组装温度和一定的组装时间,即在铝合金试样表面形成了复合硅烷膜。
12.进一步地,步骤(1)中有机硅烷化合物为长链烷基硅烷,该长链烷基硅烷的烷基链长为8-16个碳原子,包括十二烷基三甲氧基硅烷(dtms)或十四烷基三甲氧基硅烷。
13.进一步地,步骤(1)中增效剂为有机杂环化合物,包括苯并三氮唑(bta)或苯并咪唑。
14.进一步地,步骤(1)中气相组装药品的用量按组装空间的容积为30-300g/m3。
15.进一步地,步骤(1)中有机硅烷化合物和增效剂的质量比为1:(0.3-1.2)。
16.进一步地,步骤(1)中铝合金试样与气相组装药品的距离为3-15cm。
17.优选地,步骤(1)中铝合金试样与气相组装药品的距离为3cm。
18.进一步地,步骤(2)中组装温度为25-70℃,组装时间为2-48h。
19.优选地,步骤(2)中组装温度为25℃,组装时间为24h。
20.优选地,步骤(2)中组装温度为50℃,组装时间为24h。
21.进一步地,所述的有机硅烷化合物和增效剂进行混合同时组装。
22.进一步地,所述的有机硅烷化合物和增效剂进行不同组装单元的顺序组装。
23.优选地,先组装有机硅烷化合物,然后再组装增效剂。
24.本发明的技术方案之一在于,提供一种铝合金表面气相组装复合硅烷膜,该复合硅烷膜由所述的制备方法制备得到。
25.自组装膜技术目前是一项被广泛应用的技术,该技术具有成膜速度快、缺陷少、覆盖率高、成本低等优点,在腐蚀防护领域,使用自组装膜技术对金属表面进行修饰和处理达到抑制腐蚀的效果。气相自组装膜技术是指具有适当结构的活性分子通过挥发,在金属基体等材料表面,自发形成有序结构膜的一种技术,具有操作方便、药品使用少、缓蚀效率高及不存在废液排放等特点。
26.升高温度能够提高组装药品的气相挥发能力,从而在铝合金试样表面形成质量良好的自组装膜,组装顺序能够进一步提升有机硅烷化合物和增效剂的协同作用。
27.与现有技术相比,本发明具有以下优点:
28.(1)本发明通过气相自组装的方式在铝合金表面形成了自组装膜,操作简便,并且无污染;
29.(2)本发明采用的有机硅烷化合物中的烷基链对苯并三氮唑分子具有很好的相容性,苯并三氮唑分子可以作为刚性的填料分子进入长链硅烷在铝合金表面形成的疏水阻挡层中,提高铝合金表面气相组装复合硅烷膜的致密性,有效提高了铝合金材料的耐蚀性。
附图说明
30.图1为本发明实施例中铝合金样品的接触角测试结果图:(a)对比例1、(b)对比例2、(c)对比例3、(d)实施例1、(e)实施例2、(f)实施例3、(g)实施例4、(h)实施例5和(i)实施例6;
31.图2为本发明实施例中铝合金样品的析氢实验结果图:(a)对比例1、(b)对比例2、(c)对比例3、(d)实施例1、(e)实施例2、(f)实施例3、(g)实施例4、(h)实施例5和(i)实施例
6;
32.图3为本发明对比例1至3以及实施例1至3中铝合金样品电极在模拟大气腐蚀水溶液中电化学测试的阻抗谱图;
33.图4为本发明对比例4至6以及实施例4至6中铝合金样品电极在模拟大气腐蚀水溶液中电化学测试的阻抗谱图;
34.图5为本发明对比例1和4中铝合金样品电极在模拟大气腐蚀水溶液中电化学测试的等效电路图;
35.图6为本发明对比例2和5以及实施例1、2、4和5中铝合金样品电极在模拟大气腐蚀水溶液中电化学测试的无warburg阻抗等效电路图;
36.图7为本发明对比例3和6以及实施例3和6中铝合金样品电极在模拟大气腐蚀水溶液中电化学测试的有warburg阻抗等效电路图;
37.图8为本发明对比例1至3以及实施例1至3中铝合金样品电极在模拟大气腐蚀水溶液中电化学测试的开路电位与浸泡时间曲线图;
38.图9为本发明对比例4至6以及实施例4至6中铝合金样品电极在模拟大气腐蚀水溶液中电化学测试的开路电位与浸泡时间曲线图;
39.图10为本发明对比例1至3以及实施例1至3中铝合金样品电极在模拟大气腐蚀水溶液中电化学测试的极化曲线图;
40.图11为本发明对比例4至6以及实施例4至6中铝合金样品电极在模拟大气腐蚀水溶液中电化学测试的极化曲线图。
具体实施方式
41.下面结合具体实施例对本发明进行详细说明。本实施例以本发明技术方案为前提进行实施,给出了详细的实施方式和具体的操作过程,但本发明的保护范围不限于下述的实施例。
42.下述各实施例中所采用的设备如无特别说明,则表示均为本领域的常规设备;所采用的试剂如无特别说明,则表示均为市售产品或采用本领域的常规方法制备而成,以下实施例中没有做详细说明的均是采用本领域常规实验手段就能实现。
43.本实施例的铝合金试样采用aa6061铝合金试片(10cm
×
10cm
×
1mm)。
44.本实施例复合硅烷膜的缓蚀性能评价办法如下:利用电化学工作站(chi660c)进行电化学阻抗谱,判断气相自组装膜的缓蚀能力;利用析氢实验,考察铝合金表面气相自组装膜的耐蚀性能;利用接触角测量仪(jc2000c1),测量铝合金表面的亲疏水性。
45.实施例1:
46.一种铝合金表面气相组装复合硅烷膜及其制备方法,包括以下步骤:
47.将0.1g十二烷基三甲氧基硅烷和0.1g苯并三氮唑均匀混合放在1l容器的底部,aa6061铝合金试片经金相砂纸打磨、拋光处理,然后依次用无水乙醇、去离子水清洗后,放在容器顶部,与药品相距3cm,放置完毕后将容器密闭处理。将密封好的容器放入25℃电热烘箱中24h,结束后,得到表面形成了复合硅烷膜的铝合金样品。
48.一种铝合金样品表面的亲疏水性测试,包括以下步骤:
49.在室温下,用接触角测量仪测量铝合金试样表面的接触角(cas),每滴测试液的体
积为4μl,在试样表面选取五个不同的位置进行接触角测量,取测试结果的平均值作为试样表面接触角的最终测量值,采用量角法对接触角的数据进行分析。
50.一种铝合金样品的析氢实验,包括以下步骤:
51.通过加入5%氢氧化钠溶液将3%氯化钠溶液调节至ph值为12。将上述40μl碱性溶液通过移液器,滴到铝合金样品表面,并观察铝合金样品表面溶液内变化,记录第一个氢气气泡出现的时间。
52.一种铝合金样品的电化学阻抗谱测试,包括以下步骤:
53.将铝合金样品做成工作电极,并采用三电极体系进行电化学阻抗谱测试,铂电极作为辅助电极(ce),饱和甘汞电极(sce)作为参比电极(re),测量电解液为模拟大气腐蚀水(100mg/l硫酸根离子、100mg/l氯离子和100mg/l碳酸氢根离子)。电化学阻抗采用5mv的正弦信号,扫描频率为100khz至0.01hz。极化曲线以1mv/s的速度进行扫描。
54.实施例2:
55.一种铝合金表面气相组装复合硅烷膜及其制备方法,包括以下步骤:
56.将0.1g苯并三氮唑放在1l容器的底部,aa6061铝合金试片经金相砂纸打磨、拋光处理,然后依次用无水乙醇、去离子水清洗后,放在容器顶部,与药品相距3cm,放置完毕后将容器密闭处理。将密封好的容器放入25℃电热烘箱中12h。再将苯并三氮唑取出,放置0.1g十二烷基三甲氧基硅烷放在1l容器的底部,放置完毕后将容器密闭处理。将密封好的容器放入25℃电热烘箱中12h,结束后,得到表面形成了复合硅烷膜的铝合金样品。
57.一种铝合金样品的性能测试与实施例1相同。
58.实施例3:
59.一种铝合金表面气相组装复合硅烷膜及其制备方法,包括以下步骤:
60.将0.1g十二烷基三甲氧基硅烷放在1l容器的底部,aa6061铝合金试片经金相砂纸打磨、拋光处理,然后依次用无水乙醇、去离子水清洗后,放在容器顶部,与药品相距3cm,放置完毕后将容器密闭处理。将密封好的容器放入25℃电热烘箱中12h。再将十二烷基三甲氧基硅烷取出,放置0.1g苯并三氮唑放在1l容器的底部,放置完毕后将容器密闭处理。将密封好的容器放入25℃电热烘箱中12h,结束后,得到表面形成了复合硅烷膜的铝合金样品。
61.一种铝合金样品的性能测试与实施例1相同。
62.实施例4:
63.一种铝合金表面气相组装复合硅烷膜及其制备方法,包括以下步骤:
64.将0.1g十二烷基三甲氧基硅烷和0.1g苯并三氮唑均匀混合放在1l容器的底部,aa6061铝合金试片经金相砂纸打磨、拋光处理,然后依次用无水乙醇、去离子水清洗后,放在容器顶部,与药品相距3cm,放置完毕后将容器密闭处理。将密封好的容器放入50℃电热烘箱中24h,结束后,得到表面形成了复合硅烷膜的铝合金样品。
65.一种铝合金样品的性能测试与实施例1相同。
66.实施例5:
67.一种铝合金表面气相组装复合硅烷膜及其制备方法,包括以下步骤:
68.将0.1g苯并三氮唑放在1l容器的底部,aa6061铝合金试片经金相砂纸打磨、拋光处理,然后依次用无水乙醇、去离子水清洗后,放在容器顶部,与药品相距3cm,放置完毕后将容器密闭处理。将密封好的容器放入50℃电热烘箱中12h。再将苯并三氮唑取出,放置
0.1g十二烷基三甲氧基硅烷放在1l容器的底部,放置完毕后将容器密闭处理。将密封好的容器放入50℃电热烘箱中12h,结束后,得到表面形成了复合硅烷膜的铝合金样品。
69.一种铝合金样品的性能测试与实施例1相同。
70.实施例6:
71.一种铝合金表面气相组装复合硅烷膜及其制备方法,包括以下步骤:
72.将0.1g十二烷基三甲氧基硅烷放在1l容器的底部,aa6061铝合金试片经金相砂纸打磨、拋光处理,然后依次用无水乙醇、去离子水清洗后,放在容器顶部,与药品相距3cm,放置完毕后将容器密闭处理。将密封好的容器放入50℃电热烘箱中12h。再将十二烷基三甲氧基硅烷取出,放置0.1g苯并三氮唑放在1l容器的底部,放置完毕后将容器密闭处理。将密封好的容器放入50℃电热烘箱中12h,结束后,得到表面形成了复合硅烷膜的铝合金样品。
73.一种铝合金样品的性能测试与实施例1相同。
74.对比例1:
75.一种铝合金及其制备方法,包括以下步骤:
76.aa6061铝合金试片经金相砂纸打磨、拋光处理,然后依次用无水乙醇、去离子水清洗后,放在容器顶部,放置完毕后将容器密闭处理。将密封好的容器放入25℃电热烘箱中24h,结束后,得到铝合金样品。
77.一种铝合金样品的性能测试与实施例1相同。
78.对比例2:
79.一种铝合金表面气相组装缓蚀膜及其制备方法,包括以下步骤:
80.将0.1g苯并三氮唑放在1l容器的底部,aa6061铝合金试片经金相砂纸打磨、拋光处理,然后依次用无水乙醇、去离子水清洗后,放在容器顶部,与药品相距3cm,放置完毕后将容器密闭处理。将密封好的容器放入25℃电热烘箱中12h,结束后,得到表面形成了缓蚀膜的铝合金样品。
81.一种铝合金样品的性能测试与实施例1相同。
82.对比例3:
83.一种铝合金表面气相组装硅烷膜及其制备方法,包括以下步骤:
84.将0.1g十二烷基三甲氧基硅烷放在1l容器的底部,aa6061铝合金试片经金相砂纸打磨、拋光处理,然后依次用无水乙醇、去离子水清洗后,放在容器顶部,与药品相距3cm,放置完毕后将容器密闭处理。将密封好的容器放入25℃电热烘箱中12h,结束后,得到表面形成了硅烷膜的铝合金样品。
85.一种铝合金样品的性能测试与实施例1相同。
86.对比例4:
87.一种铝合金及其制备方法,包括以下步骤:
88.aa6061铝合金试片经金相砂纸打磨、拋光处理,然后依次用无水乙醇、去离子水清洗后,放在容器顶部,放置完毕后将容器密闭处理。将密封好的容器放入50℃电热烘箱中24h,结束后,得到铝合金样品。
89.一种铝合金样品的电化学阻抗谱测试与实施例1相同。
90.对比例5:
91.一种铝合金表面气相组装缓蚀膜及其制备方法,包括以下步骤:
92.将0.1g苯并三氮唑放在1l容器的底部,aa6061铝合金试片经金相砂纸打磨、拋光处理,然后依次用无水乙醇、去离子水清洗后,放在容器顶部,与药品相距3cm,放置完毕后将容器密闭处理。将密封好的容器放入50℃电热烘箱中12h,结束后,得到表面形成了缓蚀膜的铝合金样品。
93.一种铝合金样品的电化学阻抗谱测试与实施例1相同。
94.对比例6:
95.一种铝合金表面气相组装硅烷膜及其制备方法,包括以下步骤:
96.将0.1g十二烷基三甲氧基硅烷放在1l容器的底部,aa6061铝合金试片经金相砂纸打磨、拋光处理,然后依次用无水乙醇、去离子水清洗后,放在容器顶部,与药品相距3cm,放置完毕后将容器密闭处理。将密封好的容器放入50℃电热烘箱中12h,结束后,得到表面形成了硅烷膜的铝合金样品。
97.一种铝合金样品的电化学阻抗谱测试与实施例1相同。
98.如图1所示,相比空白、单一苯并三氮唑膜和单一十二烷基三甲氧基硅烷膜,组装复合硅烷膜的铝合金样品表面亲疏水性发生变化,表面形成有机物保护膜。
99.如图2所示,相比空白、单一苯并三氮唑膜和单一十二烷基三甲氧基硅烷膜,组装复合硅烷膜的铝合金样品产生第一个氢气气泡的时间较久,表明复合硅烷膜的缓蚀能力强于单一组份膜。
100.缓蚀效率ηr按如下公式计算:
[0101][0102]
其中,r
p
为组装有缓蚀膜的铝合金样品电极的极化电阻,r
p,0
为空白铝合金样品电极的极化电阻。
[0103]
如图3和4所示,组装复合硅烷膜的铝合金样品的阻抗圆弧半径明显大于空白和单一组分膜铝合金样品电极的阻抗圆弧半径,体现出气相组装膜对于铝合金腐蚀过程的抑制作用。
[0104]
如图5至7所示,rs表示溶液电阻,rf和r
ct
分别表示组装膜的电阻和电荷转移电阻,cpef和cpe
dl
是常数相位元件,分别代表了表面薄膜电容和双层电容。
[0105]
如图8和9所示,与空白和单一组分膜铝合金样品电极相比,组装复合硅烷膜的铝合金样品电极具有更高的开路电位值,表明复合硅烷膜对铝合金样品的腐蚀过程具有更好的抑制作用。
[0106]
如图10和11所示,与空白和单一组分膜铝合金样品电极相比,组装复合硅烷膜的铝合金样品电极的腐蚀电位正向移动,腐蚀电流减小,表明复合硅烷膜对铝合金样品电极的腐蚀阳极过程有明显的抑制。腐蚀电流密度随着装配温度的升高而大幅降低,表明升高温度可以提高复合硅烷膜对铝合金样品的保护。
[0107]
表1对比例1至6以及实施例1至6中铝合金样品电极在模拟大气腐蚀水溶液中的电化学阻抗拟合参数
[0108][0109]
如表1所示,经过气相组装修饰过的aa6061铝合金极化电阻(r
p
)远大于空白电极的r
p
值,表明气相组装膜提高了aa6061铝合金的耐腐蚀性能,很好的抑制了铝合金的腐蚀。实施例3铝合金样品与实施例1铝合金样品和实施例2铝合金样品相比,保护效率最高为85.9%;实施例6铝合金与实施例4铝合金样品和实施例5铝合金样品相比,保护效率最高为97.8%。
[0110]
阴极和阳极的tafel斜率分别为βc和βa,腐蚀电位和腐蚀电流密度分别为e
corr
和i
corr
。极化曲线以测定电流密度i随电极电位e的值变化的曲线来表示。通常采用tafel外推法确定腐蚀电流密度。保护效率ηi的计算方式如下:
[0111][0112]
其中,i
corr,0
和i
corr
分别为空白铝合金样品电极和组装有缓蚀膜的铝合金样品电极的腐蚀电流密度。
[0113]
表2对比例1至6以及实施例1至6中铝合金样品电极在模拟大气腐蚀水溶液中的电化学极化拟合参数
[0114][0115]
如表2所示,组装复合硅烷膜的铝合金样品电极的腐蚀电位较空白铝合金样品和单一组分膜铝合金样品电极的腐蚀电流明显降低。其中,实施例3和实施例6铝合金样品的保护效率较高,分别为91.4%和94.7%。
[0116]
上述的对实施例的描述是为便于该技术领域的普通技术人员能理解和使用发明。熟悉本领域技术的人员显然可以容易地对这些实施例做出各种修改,并把在此说明的一般原理应用到其他实施例中而不必经过创造性的劳动。因此,本发明不限于上述实施例,本领域技术人员根据本发明的揭示,不脱离本发明范畴所做出的改进和修改都应该在本发明的保护范围之内。