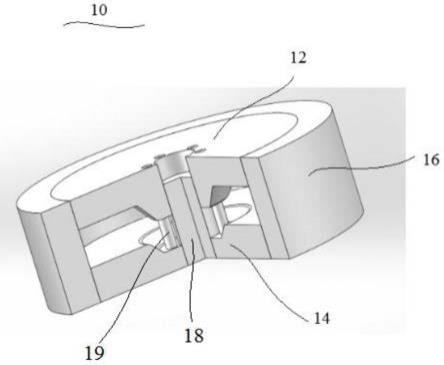
1.本发明涉及粉末冶金技术领域,特别是涉及制动盘生坯成形模具、成形方法及制动盘的近净成形方法。
背景技术:2.铝基复合材料汽车制动盘,轻量化效果明显。为提高制动盘的高温性能,使制动盘可以在苛刻的制动工况下服役,提高铝基复合材料中增强相的体积分数是一种有效的手段。然而,增强相含量的增加会提升制动盘的机加工难度,特别的,孔加工过程中可能导致裂纹等缺陷的产生。
3.粉末锻造工艺可用于制备高体积分数陶瓷颗粒增强铝基复合材料,该工艺较为成熟,通常工序为:先压制形状简单的生坯,如环状、柱状的生坯;随后烧结,再经过锻造,充型制动盘的整体结构,包括鹅颈结构、盘帽等,最后机加工成最终的成品。然而该工艺存在锻造过程中物料的流动不易控制的问题,例如,对于高体积分数碳化硅增强铝基复合材料,锻造充型制动盘盘帽等结构的过程中,可能出现陶瓷颗粒分布不均匀的现象。可以预见的是,如果锻造前,生坯结构已近似于锻造工件,则锻造可近似于复压,锻造过程主要为材料的致密化,物料流动距离短,陶瓷颗粒的分布可有效控制。
4.因此,为了实现制动盘的近净成形,同时减小材料在整形过程中的流动,理想状态下需要将制动盘生坯直接设计为制动盘产品的结构,这就需要制动盘生坯的盘帽结构垂直于摩擦环,这样的结构设计会导致压制结束后,生坯的盘帽结构紧贴成形模具的上下模,且弹性后效作用还会导致其嵌入上下模的腔体中,脱模过程中需要施加外力依次顶出上下模,导致脱模困难的同时也容易受到损坏。
技术实现要素:5.基于此,有必要提供一种制动盘生坯成形模具,该模具可成形结构近似于制动盘的生坯,在便于脱模的同时,还可使后续整形过程主要为材料的致密化,有效缩短物料流动距离,并使陶瓷颗粒的分布可控,实现制动盘的近净成形。
6.一种制动盘生坯成形模具,包括上模、下模和阴模,所述上模和下模围合在所述阴模内形成封闭性模腔,用于成形制动盘生坯,所述上模的压制表面包括第一盘体压制表面、第一盘颈压制表面、第一盘帽压制表面及分别与所述第一盘体压制表面、第一盘颈压制表面相切的第一圆角曲面和分别与所述第一盘颈压制表面、第一盘帽压制表面相切的第二圆角曲面,所述第一圆角曲面和第二圆角曲面的半径分别为5mm~10mm,h1与l1的比值为0.577~1.732,其中h1为a点和b点之间的轴向距离,l1为a点与b点之间的径向距离,所述a点为第一盘体压制表面与第一圆角曲面的任意切点,所述b点为第一盘帽压制表面与第二圆角曲面的任意切点;
7.所述下模的压制表面包括第二盘体压制表面、第二盘颈压制表面、第二盘帽压制表面及分别与所述第二盘体压制表面、第二盘颈压制表面相切的第三圆角曲面和分别与所
述第二盘颈压制表面、第二盘帽压制表面相切的第四圆角曲面,所述第三圆角曲面和第四圆角曲面的半径分别为5mm~10mm,h2与l2的比值为0.577~1.732,其中h2为c点和d点之间的轴向距离,l2为c点和d点之间的径向距离,所述c点为第二盘体压制表面与第三圆角曲面的任意切点,所述d点为第二盘帽压制表面与第四圆角曲面的任意切点。
8.在其中一个实施例中,所述上模一体成形。
9.在其中一个实施例中,所述下模一体成形。
10.在其中一个实施例中,所述模具还包括芯轴,所述上模和下模分别具有穿透第一盘帽压制表面和第二盘帽压制表面的中心轴向通孔,所述芯轴与上下模的中心轴向通孔配合,用于成形制动盘生坯中心孔。
11.在其中一个实施例中,所述模具还包括若干导柱,所述上模和下模分别具有穿透第一盘帽压制表面和第二盘帽压制表面的周向轴向通孔,所述若干导柱与上下模的周向轴向通孔配合,用于成形制动盘生坯螺栓孔。
12.一种制动盘生坯成形方法,包括以下步骤:
13.提供上述任一项所述的制动盘生坯成形模具;
14.将陶瓷颗粒增强铝基复合材料原料粉末混合均匀后,置于所述模具内压制成形,得到制动盘生坯。
15.在其中一个实施例中,所述压制成形的条件为:以0.5mm/s~1mm/s的加压速率加压至25mpa~50mpa,保压5s~10s,再以0.5mm/s~1mm/s的加压速率加压至100mpa~200mpa,保压5s~10s。
16.一种制动盘近净成形方法,包括以下步骤:
17.提供上述方法制得的制动盘生坯;
18.将所述制动盘生坯依次进行烧结和整形,以使所述制动盘生坯由第一盘颈压制表面成形的表面径向向内移动直至与第一盘帽压制表面成形的表面垂直,同时使所述制动盘生坯由第二盘颈压制表面成形的表面径向向外移动直至与第二盘帽压制表面成形的表面垂直,得到制动盘。
19.在其中一个实施例中,所述烧结的条件为:在真空环境中,以3℃/min~5℃/min的升温速率升温至300℃~350℃,保温60min~90min;再在保护性气体氛围中,以3℃/min~5℃/min的升温速率升温至550℃~640℃,保温45min~90min;随炉降温至200℃以下出炉。
20.在其中一个实施例中,所述整形的温度为480℃~550℃,压力为100mpa~300mpa,保压时间为10s~20s。
21.上述制动盘生坯成形模具,通过第一圆角曲面、第二圆角曲面、第三圆角曲面和第四圆角曲面的设计及相关参数的设定,使成形的制动盘生坯结构接近制动盘,在便于脱模的同时,还可使后续整形过程主要为材料的致密化,有效缩短物料的流动距离,并使陶瓷颗粒的分布可控,实现制动盘的近净成形。
22.此外,通过芯轴、导柱的设计,也可使中心孔和螺栓孔在成形过程中实现,避免了后续孔加工导致裂纹产生的问题。
23.上述制动盘近净成形方法得到的制动盘,产品尺寸接近成品图纸尺寸,可大大减少后续的机加工成本,提高制动盘的生产效率。
附图说明
24.图1为一实施方式的制动盘生坯成形模具结构示意图;
25.图2为图1中上模的剖面示意图;
26.图3为图1中下模的剖面示意图;
27.图4为一实施方式的制动盘生坯结构示意图;
28.图5为一实施方式的制动盘结构示意图。
具体实施方式
29.为了便于理解本发明,下面将对本发明进行更全面的描述,并给出了本发明的较佳实施例。但是,本发明可以以许多不同的形式来实现,并不限于本文所描述的实施例。相反地,提供这些实施例的目的是使对本发明的公开内容的理解更加透彻全面。
30.除非另有定义,本文所使用的所有的技术和科学术语与属于本发明的技术领域的技术人员通常理解的含义相同。本文中在本发明的说明书中所使用的术语只是为了描述具体的实施例的目的,不是旨在于限制本发明。本文所使用的术语“和/或”包括一个或多个相关的所列项目的任意的和所有的组合。
31.此外,需要说明的是,在本文中压制表面指的是与原料粉末接触用于使其成形的表面。
32.请参阅图1,为一实施方式的制动盘生坯成形模具10,包括上模12、下模14和阴模16,上模12和下模14围合在阴模16内,形成封闭性模腔,用于成形如图4所示的制动盘生坯20。
33.其中,上模12如图2所示,其压制表面包括第一盘体压制表面122、第一盘颈压制表面124、第一盘帽压制表面126及分别与第一盘体压制表面122、第一盘颈压制表面124相切的第一圆角曲面123和分别与第一盘颈压制表面124、第一盘帽压制表面126相切的第二圆角曲面125。
34.即,第一盘体压制表面122与第一盘颈压制表面124采用第一圆角曲面123光滑过渡,a点为第一盘体压制表面122与第一圆角曲面123的任意切点。
35.第一盘颈压制表面124与第一盘帽压制表面126采用第二圆角曲面125光滑过渡,b点为第一盘帽压制表面126与第二圆角曲面125的任意切点。
36.进一步的,a点与b点之间的径向距离为l1,a点与b点的轴向距离为h1,h1与l1的比值在0.577~1.732范围内,且第一圆角曲面123和第二圆角曲面125的半径分别为5mm~10mm。
37.需要说明的是,h1的值可以根据设计的制动盘的尺寸确定。
38.对应的,下模14如图3所示,其压制表面包括第二盘体压制表面142、第二盘颈压制表面144、第二盘帽压制表面146及分别与第二盘体压制表面142、第二盘颈压制表面144相切的第三圆角曲面143和分别与第二盘颈压制表面144、第二盘帽压制表面146相切的第四圆角曲面145。
39.即,第二盘体压制表明142和第二盘颈压制表面144采用第三圆角曲面143光滑过渡,c点为第二盘体压制表面142与第三圆角曲面143的切点。
40.第二盘颈压制表面144与第二盘帽压制表面146采用第四圆角曲面145光滑过渡,d
点为第二盘帽压制表面146与第四圆角曲面145的切点。
41.进一步的,c点与d点之间的径向距离为l2,c点与d点之间的轴向距离为h2,h2与l2的比值在0.577~1.732范围内,且第三圆角曲面143和第四圆角曲面145的半径分别为5mm~10mm。
42.需要说明的是,h2的值可以根据设计的制动盘的尺寸确定。
43.通过设定a点、b点之间轴向距离与径向距离的比值在0.577~1.732范围内,且同时限定第一圆角曲面123和第二圆角曲面125的半径分别为5mm~10mm,可使该上模12压制成形的生坯表面如图4中22所示。
44.通过设定c点、d点之间轴向距离h2与径向距离l2的比值在0.577~1.732范围内,且同时限定第三圆角曲面143和第四圆角曲面145的半径分别为5mm~10mm,可使该下模14压制成形的生坯表面如图4中24所示。
45.通过限定模具四个圆角曲面的半径分别在5mm~10mm范围内,且h1与l1的比值在0.577~1.732范围内,h2与l2的比值在0.577~1.732范围内,可成形如图4所示的制动盘生坯20,在便于脱模的同时,还可使后续整形过程主要为材料的致密化,有效缩短物料流动距离,并使陶瓷颗粒的分布可控,实现制动盘的近净成形。
46.进一步的,如图1所示,上述模具10还包括芯轴18,上模12设有穿透第一盘帽压制表面126的中心轴向通孔(图未标),下模14设有穿透第二盘帽压制表面146的中心轴向通孔(图未标),芯轴18与上下模的中心轴向通孔配合,用于成形如图4所示的中心孔26。
47.进一步的,上述模具10还包括若干导向柱19,上模12设有穿透第一盘帽压制表面126的周向轴向通孔(图未标),下模14设有穿透第二盘帽压制表明146的周向轴向通孔(图未标),上述若干导柱19与上下模的周向轴向通孔配合,用于成形如图4所述的螺栓孔28。
48.上述模具10,可在压制成形阶段实现中心孔26和螺栓孔28的成形,避免了后续通过机加孔导致裂纹等缺陷产生的问题。
49.一实施方式的利用上述模具成形制动盘生坯,进而近净成形制动盘的方法,包括以下步骤s110~s130:
50.s110、提供如图1所示的制动盘生坯成形模具10。
51.s120、将陶瓷颗粒增强铝基复合材料原料粉末混合均匀后,置于上述模具10内压制成形,得到如图4所示的制动盘生坯20。
52.需要说明的是,本技术的制备工艺适用于现有任意配方组成的陶瓷颗粒增强铝基复合材料,优选适用于陶瓷颗粒体积含量为25%~70%的陶瓷颗粒增强铝基复合材料。
53.压制成形的条件为:以0.5mm/s~1mm/s的加压速率加压至25mpa~50mpa,保压5s~10s,再以0.5mm/s~1mm/s的加压速率加压至100mpa~200mpa,保压5s~15s。
54.s130、将上述制动盘生坯20依次进行烧结和整形,得到如图5所示的制动盘。
55.其中,烧结的条件为:在真空环境中,以3℃/min~5℃/min的升温速率升温至300℃~350℃,保温60min~90min;再在保护性气体氛围(如氮气)中,以3℃/min~5℃/min的升温速率升温至550℃~640℃,保温45min~90min;随炉降温至200℃以下出炉。
56.整形的温度为480℃~550℃,压力为100mpa~300mpa,保压时间为10s~20s。
57.整形过程中,制动盘生坯20由第一盘颈压制表面124成形的表面径向向内移动直至与第一盘帽压制表面126成形的表面垂直,同时,制动盘生坯20由第二盘颈压制表面144
成形的表面径向向外移动直至与第二盘帽压制表面146成形的表面垂直,得到如图5所示的制动盘30。
58.上述制动盘近净成形方法得到的制动盘产品尺寸接近成品图纸尺寸,可大大减少后续的机加工成本,提高制动盘的生产效率。经检测,上述方法制得的制动盘内部致密,无气孔及细小裂纹,且颗粒分布均匀,满足制动要求。
59.以下为具体实施例。
60.实施例1
61.采用如步骤s110~s130的方法近净成形制动盘,其中模具如图1所示,h1=40mm,l1=35mm,h2=20mm,l2=20mm,第一圆角曲面的半径为5mm、第二圆角曲面的半径为5mm、第三圆角曲面的半径为5mm、第四圆角曲面的半径为5mm。原料粉末为sic颗粒体积含量为40%的铝基复合材料。
62.经检测,实施例1得到的制动盘外形完整,中心孔与螺栓孔充型完全,与图纸尺寸的差值在0.3mm以内。超声探伤显示制动盘内部致密无缺陷,无气孔及细小裂纹。取样测试结果表明,材料内部陶瓷颗粒分布均匀。
63.对比例1
64.对比例1与实施例1基本相同,不同的是,成形模具l1的值设计为10mm,h1/l1=4。
65.结果发现,压制成形后,生坯无法与上模和下模直接分离,未能成功脱模,后续未进行烧结与整形工序。
66.对比例2
67.对比例2与实施例1基本相同,不同的是,成形模具第三圆角曲面的半径为0mm、第四圆角曲面的半径为0mm,即上述两处位置没有进行倒角。
68.结果发现,压制成形脱模后,生坯出现了大尺寸裂纹与缺角,且经烧结和整形,裂纹仍然无法消除。因此,对比例2试制的制动盘,若想消除裂纹影响,需预留5mm以上的加工余量,无法实现制动盘的近净成形,制动盘的成品率偏低。
69.实施例2
70.采用如步骤s110~s130的方法近净成形制动盘,其中模具如图1所示,h1=40mm,l1=35mm,h2=25mm,l2=25mm,第一圆角曲面的半径为10mm、第二圆角曲面的半径为10mm、第三圆角曲面的半径为10mm、第四圆角曲面的半径为10mm。原料粉末为sic颗粒体积含量为48%的铝基复合材料。
71.经检测,实施例2得到的制动盘外形完整,中心孔与螺栓孔充型完全,与图纸尺寸的差值在0.3mm以内。超声探伤显示制动盘内部致密无缺陷,无气孔及细小裂纹。取样测试结果表明,材料内部陶瓷颗粒分布均匀。
72.实施例3
73.采用如步骤s110~s130的方法近净成形制动盘,其中模具如图1所示,h1=40mm,l1=69.3mm,h2=25mm,l2=43.3mm,第一圆角曲面的半径为5mm、第二圆角曲面的半径为5mm、第三圆角曲面的半径为10mm、第四圆角曲面的半径为10mm。原料粉末为sic颗粒体积含量为20%的铝基复合材料。
74.经检测,实施例3得到的制动盘外形完整,中心孔与螺栓孔充型完全,与图纸尺寸的差值在0.3mm以内。超声探伤显示制动盘内部致密无缺陷,无气孔及细小裂纹。取样测试
结果表明,材料内部陶瓷颗粒分布均匀。
75.实施例4
76.采用如步骤s110~s130的方法近净成形制动盘,其中模具如图1所示,h1=40mm,l1=23.1mm,h2=25mm,l2=14.5mm,第一圆角曲面的半径为10mm、第二圆角曲面的半径为10mm、第三圆角曲面的半径为5mm、第四圆角曲面的半径为5mm。原料粉末为sic颗粒体积含量为70%的铝基复合材料。
77.经检测,实施例4得到的制动盘外形完整,中心孔与螺栓孔充型完全,与图纸尺寸的差值在0.3mm以内。超声探伤显示制动盘内部致密无缺陷,无气孔及细小裂纹。取样测试结果表明,材料内部陶瓷颗粒分布均匀。
78.以上所述实施例仅表达了本发明的几种实施方式,其描述较为具体和详细,但并不能因此而理解为对本发明专利范围的限制。应当指出的是,对于本领域的普通技术人员来说,在不脱离本发明构思的前提下,还可以做出若干变形和改进,这些都属于本发明的保护范围。因此,本发明专利的保护范围应以所附权利要求为准。