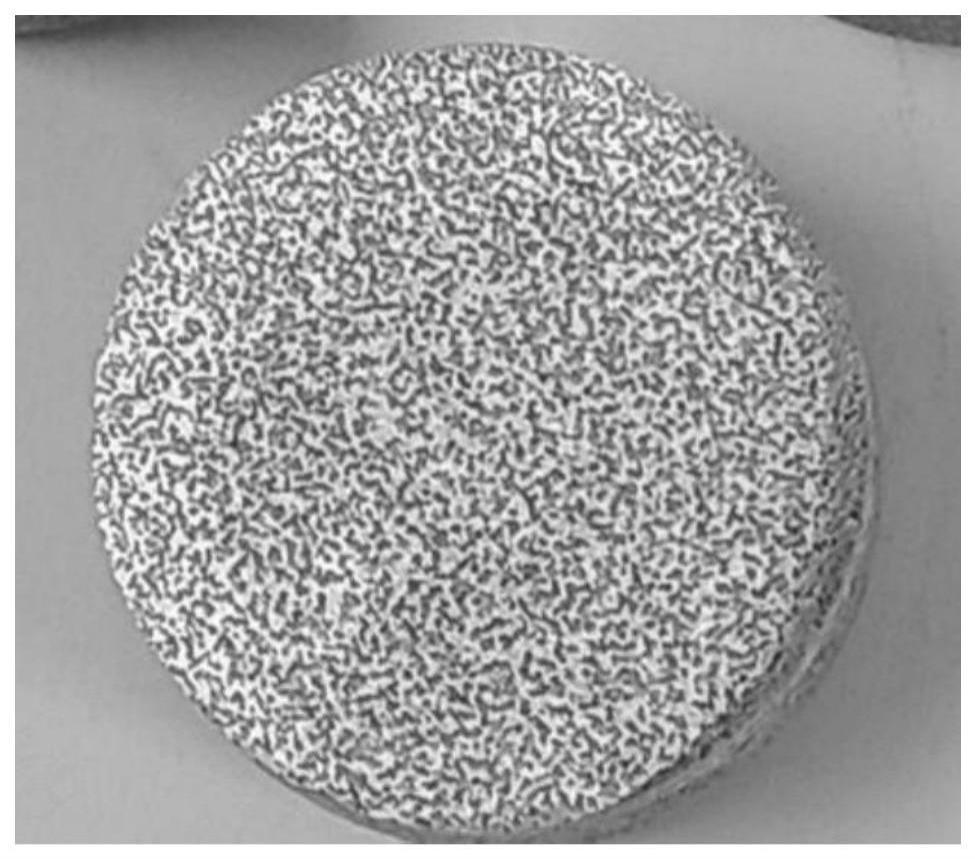
1.本发明属于铝合金精炼剂制备技术领域,具体涉及一种再生铝合金精炼剂及其制备和使用方法。
背景技术:2.再生铝合金是以回收的废铝为主要原材料熔炼配制而成,由于废铝来源复杂,携带或镶嵌大量潮湿的非金属物,如油污、油漆、涂料、纸张、塑料、橡胶、泥土等,当废铝熔化成铝合金液后,铝合金液含有大量的气体和夹杂物,这些气体和夹杂物如果留在再生铝合金中,将形成气孔、孔洞、疏松等缺陷,会割裂再生铝合金基体,破坏再生铝合金的组织连续性,成为再生铝合金断裂的裂纹源和裂纹扩展方法,降低再生铝合金的力学性能、导热导电性能、耐腐蚀性能和抗疲劳性能等。因此,在再生铝合金生产过程中必须对铝合金液进行除气除渣处理,降低再生铝合金的含气量和含渣量。采用精炼剂对再生铝合金液进行精炼是目前最常用的除气除渣方法,而精炼剂的除气除渣效率将直接决定再生铝合金的含气量和含渣量。
3.公布号cn111424186的专利公开了一种再生铝熔体用高效复合精炼剂及其制备方法和使用方法,所述精炼剂由以下质量分数的各组分组成:kcl10-20%,mgcl25-10%,caf20-8%,alf320-30%,kno310-15%,nano 0-10%,na2b4o720-40%,na3alf610-25%,稀土化合物5-10%,以上各组分之和为100%。
4.公布号cn110241322的专利公开了一种再生铝合金精炼剂,精炼剂各成份按重量份计如下:nacl 30-40份,kcl 30-35份,mgcl220-25份,naf 20-25份,na3alf610-15份,caf22-5份。
5.公布号cn108359810的专利公开了一种环保型再生铝精炼剂及其使用方法,精炼剂各组分的质量百分比为:nacl 10-40%,kcl 10-40%,na3alf65-18%,nano320-40%,碳粉2-4%,稀土氧化物0.5-10%,稀土氧化物为la2o3、ceo2和y2o3中的任意一种或任意两种及两种以上。
6.公布号cn102226239的专利公开了一种铝或铝合金熔体净化处理用精炼熔剂及其制备方法,该精练剂原料配方是由以下组分构成的粉体混合物:nacl25-35%,kcl 25-35%,na3alf6和/或k3alf615-25%,na2so4和/或k2so44-10%,caco3和/或na2co33-10%,ref3和/或recl33-6%,nacl与kcl的质量比为1:1,re为ce或la。
7.公布号cn102041396的专利公开了一种铝及铝合金用精炼剂的制备方法,精炼剂由以下质量百分比的配料组成:nacl 30-85%、na2sif65-40%、na2so45-40%、caf22-20%、c6cl60.5-10%。
8.公布号cn104388730的专利公开了一种铝合金用高效精炼剂及其制备方法,精炼剂由以下质量份数的各组分组成:nacl 30-35份、kcl 25-28份、na3alf68-10份、na2co33-5份、naf 2-5份、na2so42-5份、cas 2-3份。
9.公布号cn109207770的专利公开了一种铝及铝合金熔炼精炼剂及其制备方法,包
括以下组份:nacl 40-60份、cas 12-18份、a1f38-16份、mgf24-8份、mg2n38-15份、na3a1f63-11份、na2sif64-8份、c2cl60.5-1.0份、石墨15-25份、泥炭土10-20份、dyf32-6份、cef32-8份。
10.从生产实践和文献资料检索结果来看,现有精炼剂存在以下一种或多种问题:(1)精炼剂的除气除渣效率仍然偏低,增加精炼剂的用量虽然可以提高除气除渣效果,但会对再生铝合金造成二次污染,增大再生铝合金中碱金属的含量,增加铝渣的排放量,增加生产成本。(2)精炼剂普遍含有大量的氟盐、硝酸盐、硫酸盐和六氯乙烷等成分,导致精炼过程产大量刺激性难闻的气体和烟雾,加重环境污染,危害人体健康。(3)精炼剂普遍含有大量的钠盐,容易导致再生铝合金的钠含量超标,增加再生铝合金发生钠脆断裂的风险。(4)渣铝分离效果差,增加了再生铝合金的损耗和铝渣的处理难度等。(5)精炼剂的功能单一,难以满足高品质高性能再生铝合金的生产需要。因此,现有再生铝合金精炼剂及其制备方法仍有待改进和发展。
技术实现要素:11.针对背景技术中提到的问题,本发明的目的是提供一种再生铝合金精炼剂及其制备和使用方法,通过优化精炼剂的成分组成和制备方法,提高精炼剂的除气除渣效率,降低再生铝合金的含气量和含渣量,提高再生铝合金的品质和性能,减少烟气和铝渣的排放量,以解决背景技术中提到的问题。
12.本发明的上述技术目的是通过以下技术方案得以实现的:
13.一种一种再生铝合金精炼剂,其特征在于,由以下质量百分比的成分组成:mgcl230-35%,kcl 25-30%,cacl210-15%,kbf45-10%,k2tif65-10%,baco35-10%,ycl33-6%。
14.本发明还提供了一种再生铝合金精炼剂的制备方法,依次包括以下步骤:
15.s1、按精炼剂的成分组成和质量百分比,选用mgcl2、kcl、cacl2、kbf4、k2tif6、baco3和ycl3为原材料进行配料;
16.s2、将配料在80-100℃加热3-5小时进行烘干脱水;
17.s3、将烘干脱水后的配料在900-1100℃加热1-2小时进行重熔,然后冷却凝固至室温;
18.s4、将重熔后的精炼剂破碎、筛选和包装,得到所述再生铝合金精炼剂。
19.较佳的,所述s1中所述mgcl2、kcl、cacl2、kbf4、k2tif6、baco3和ycl3的纯度≥99.5%。
20.较佳的,所述s3中所述重熔是在真空度10-20pa的真空炉内进行重熔。
21.较佳的,所述s4中所述再生铝合金精炼剂的颗粒尺寸≤1毫米。
22.本发明还提供了一种再生铝合金精炼剂的使用方法,具体包括:所述再生铝合金精炼剂的用量占再生铝合金液重量的0.2-0.4%。
23.综上所述,本发明主要具有以下有益效果:
24.(1)本发明再生铝合金精炼剂具有更高的除气除渣效率,加入0.3%的精炼剂,除气率到55%以上,除渣率达到50%以上,可显著降低再生铝合金的气渣含量。
25.(2)本发明再生铝合金精炼剂对再生铝合金有细化变质和改性作用,可提高再生铝合金的力学性能、导热导电性能、耐腐蚀性能和疲劳性能。
26.(3)本发明再生铝合金精炼剂中的氟盐含量少,不含硝酸盐、硫酸盐和六氯乙烷,因而减少了刺激性难闻的气体的排放,使用更加环保。
27.(4)本发明再生铝合金精炼剂具有良好的渣铝分离效果,可以减少铝的损耗和铝渣的排放量,降低铝渣的处理难度。
28.(5)本发明再生铝合金精炼剂不含钠盐,避免了再生铝合金中钠含量超标而引发钠脆断裂的风险。
29.说明书附图
30.图1为采用实施例1精炼剂精炼后再生铝合金圆锭的腐蚀图。
31.图2为采用实施例2精炼剂精炼后再生铝合金圆锭的腐蚀图。
32.图3为采用实施例3精炼剂精炼后再生铝合金圆锭的腐蚀图。
33.图4为采用对比例1精炼剂精炼后再生铝合金圆锭的腐蚀图。
34.图5为采用对比例2精炼剂精炼后再生铝合金圆锭的腐蚀图。
具体实施方式
35.下面对本发明实施例中的技术方案进行清楚、完整地描述,显然,所描述的实施例仅仅是本发明一部分实施例,而不是全部的实施例。基于本发明中的实施例,本领域普通技术人员在没有做出创造性劳动前提下所获得的所有其他实施例,都属于本发明保护的范围。
36.实施例1
37.再生铝合金精炼剂,由以下质量百分比的成分组成:mgcl232.5%,kcl28.1%,cacl211.9%,kbf48.4%,k2tif66.3%,baco37.3%,ycl35.5%。制备方法依次包括以下步骤:(1)按精炼剂的成分组成和质量百分比,选用纯度≥99.5%的mgcl2、kcl、cacl2、kbf4、k2tif6、baco3和ycl3为原材料进行配料;(2)将配料在90℃加热4小时进行烘干脱水;(3)选择真空度15pa的真空炉将配料在1000℃加热1.5小时进行重熔,然后冷却凝固至室温;(4)将重熔后的精炼剂破碎、筛选和真空包装,得到颗粒尺寸≤1毫米的再生铝合金精炼剂。
38.实施例2
39.再生铝合金精炼剂由以下质量百分比的成分组成:mgcl230.1%,kcl29.6%,cacl210.3%,kbf49.8%,k2tif65.3%,baco39.6%,ycl35.3%。制备方法依次包括以下步骤:(1)按精炼剂的成分组成和质量百分比,选用纯度≥99.5%的mgcl2、kcl、cacl2、kbf4、k2tif6、baco3和ycl3为原材料进行配料;(2)将配料在100℃加热3小时进行烘干脱水;(3)选择真空度20pa的真空炉将配料在900℃加热2小时进行重熔,然后冷却凝固至室温;(4)将重熔后的精炼剂破碎、筛选和真空包装,得到颗粒尺寸≤1毫米的再生铝合金精炼剂。
40.实施例3
41.再生铝合金精炼剂由以下质量百分比的成分组成:mgcl234.1%,kcl25.5%,cacl214.2%,kbf45.7%,k2tif69.8%,baco35.1%,ycl35.6%。制备方法依次包括以下步骤:(1)按精炼剂的成分组成和质量百分比,选用纯度≥99.5%的mgcl2、kcl、cacl2、kbf4、k2tif6、baco3和ycl3为原材料进行配料;(2)将配料在80℃加热5小时进行烘干脱水;(3)选择真空度10pa的真空炉将配料在1100℃加热1小时进行重熔,然后冷却凝固至室温;(4)将重熔后的精炼剂破碎、筛选和真空包装,得到颗粒尺寸≤1毫米的再生铝合金精炼剂。
42.对比例1
43.再生铝合金精炼剂由以下质量百分比的成分组成:mgcl232.5%,kcl28.1%,cacl211.9%,kbf48.4%,k2tif66.3%,baco37.3%,ycl35.5%。制备方法依次包括以下步骤:(1)按精炼剂的成分组成和质量百分比,选用纯度≥99.5%的mgcl2、kcl、cacl2、kbf4、k2tif6、baco3和ycl3为原材料进行配料;(2)将配料在90℃加热4小时进行烘干脱水;(3)将配料混合破碎、筛选和真空包装,得到颗粒尺寸≤1毫米的再生铝合金精炼剂。
44.对比例2
45.目前市售铝合金精炼剂由以下质量百分比的成分组成:nacl 26.1%,na2sif610.6%,na2so418.1%,caf26.9%,c6cl69.3%,na2s2o314.3%,naf 15.7%,该精炼剂是对原材料烘干脱水后直接破碎和混合得到。
46.验证例
47.将实施例1-3和对比例1-2铝合金精炼剂在同样的条件下用于adc10再生铝合金的精炼除气除渣,实验炉为20吨蓄热式燃气熔铝炉,再生铝合金液重量为18吨,采用纯度99.9%的氩气为载流介质将精炼剂喷吹入再生铝合金液,精炼时再生铝合金液的温度为720℃,精炼时间为25分钟,精炼剂加入量为0.3%。实验过程中记录精炼剂的使用情况,包括再生铝合金液燃烧情况、排烟量、烟气味、渣铝分离情况、铝渣粘稠状况,最后将铝渣收集进行称量,铝渣重量越小,代表铝渣中含铝量越少,渣铝分离效果越好,结果如表1所示。从表1可看到,实施例1-3制备的精炼剂,精炼时烟气不刺鼻,排放量小,精炼时铝水燃烧轻微,渣铝分离容易,铝渣松散,铝渣量少。对比例1的精炼剂由于未进行重熔,渣铝分离效果略差,铝渣量略多。而对比例2所用的市售精炼剂,精炼时烟气刺鼻,排放量大,铝水燃烧严重,渣铝分离难,铝渣粘稠,铝渣排放量也大。通过比较可以看到,本发明再生铝合金精炼剂使用时更加环保,渣铝分离效果更容易,有利于减少铝的损耗和铝渣的排放量。
48.表1精炼剂的精炼效果对比情况
49.实施例1实施例2实施例3对比例1对比例2烟气量小小小小大烟气味不刺鼻不刺鼻不刺鼻不刺鼻刺鼻铝水燃烧情况轻微轻微轻微轻微严重渣铝分离情况易易易难难铝渣状态松散松散松散粘稠粘稠铝渣重量/kg335.1345.6330.4379.3405.8
50.采用hda-v测氢仪和analyze podfa测渣仪现场检测精炼前后炉内再生铝合金液的含氢量和含渣量,将精炼前炉内再生铝合金液的含氢量、含渣量分别减去精炼后炉内再生铝合金液的含氢量、含渣量,再除以精炼前炉内再生铝合金液的含氢量、含渣量,分别得到精炼剂的除气率和除渣率,结果如表2和表3所示。从表2和表3可看到,实施例1-3精炼剂的除气率达到55%以上,除渣率达到50%以上,而对比例1精炼剂的除气率为50.4%,除渣率为45.9%,对比例2市售精炼剂的除气率只有47.8%,除渣率只有41.2%,通过比较可以看到,本发明再生铝合金精炼剂具有更高的除气除渣效率。
51.表2精炼前后再生铝合金液的含氢量和除气率
[0052][0053]
表3精炼前后再生铝合金液的含渣量和除渣率
[0054] 精炼前含渣量/(mm2/kg)精炼后含渣量/(mm2/kg)除渣率/%实施例10.3580.17451.4实施例20.3630.18150.1实施例30.3540.16952.3对比例10.3570.19345.9对比例20.3590.21141.2
[0055]
采用强酸对再生铝合金圆锭进行腐蚀,通过观察腐蚀孔洞的情况来定性比较精炼剂的除气除渣效果,腐蚀孔洞越少,代表精炼剂的除气除渣效果越好,实施例1-3的精炼剂和对比例的1-2精炼剂精炼后再生铝合金圆锭的腐蚀情况分别如图1-5所示。通过对图1-5进行比较可以看到,采用实施例1-3制备的再生铝合金精炼剂精炼后,再生铝合金圆锭的腐蚀孔洞数量比较少,表明实施例1-3制备的再生铝合金精炼剂具有更好的除气除渣效果。
[0056]
对精炼后炉内的再生铝合金液进行取样浇铸成再生铝合金圆锭,对再生铝合金圆锭的拉伸力学性能和导电性能分别进行检查,结果如表4所示。从表4可看到,采用实施例1-3制备的再生铝合金精炼剂对再生铝合金液进行精炼,制备得到的再生铝合金的强度、塑性和导电率都明显高于对比例1制备的精炼剂和对比例2市售铝合金精炼剂精炼制备得到的再生铝合金,说明采用本发明制备得到的铝再生合金精炼剂对再生铝合金液进行精炼,可以减少再生铝合金液的含气量和含渣量,最终可以提高再生铝合金的力学性能和导电性能。
[0057]
表4精炼后再生铝合金的拉伸力学性能和导电率
[0058][0059]
实施例4
[0060]
一种再生铝合金精炼剂,所述精炼剂含有mgcl2和kcl,mgcl2的质量百分比为30-35%,kcl的质量百分比为25-30%。
[0061]
mgcl2和kcl是精炼剂的主要成分,主要作用降低精炼剂的熔解温度,提高精炼剂的除气除渣效率。mgcl2的熔点为712℃,kcl的熔点为770℃,当对精炼剂进行高温重熔后,mgcl2和kcl可形成mgcl2·
kcl共晶体,mgcl2·
kcl共晶体的熔点仅为490℃,可显著降低精炼剂的熔点,当精炼剂加入到再生铝合金液后,部分mgcl2·
kcl共晶体直接与再生铝合金液反应生成沸点仅为182.7℃的alcl3,alcl3形成气泡在上浮过程中将吸附部分氢气和夹杂物,达到除气除渣效果。部分mgcl2·
kcl共晶体在高温再生铝合金液的热作用下直接分解释放出cl
+
离子,cl
+
离子再与再生铝合金液中的氢气反应生成hcl气泡,hcl气泡在溢出再生铝合金液的过程中又进一步吸附带走再生铝合金液中的al2o3等夹杂物,从而起到高效的除气除渣作用。
[0062]
进一步地,所述精炼剂含有cacl2,cacl2的质量百分比为10-15%。
[0063]
再生铝合金主要是al-si合金,现有技术通常都是在精炼除气除渣后在再生铝合金液中添加金属锶或者铝锶合金的形式来细化变质再生铝合金中的粗大si相,但添加锶元素容易导致再生铝合金液重新吸氢而导致再生铝合金的含气量增加。发明人通过大量实验研究后发现,在精炼剂中加入10-15%的cacl2,当cacl2与高温再生铝合金液接触后发生置换反应生成alcl3,alcl3沸点仅为183℃,在高温再生铝合金液中形成气泡,气泡在上浮过程中将再生铝合金液中的氢气和al2o3等夹杂物一起带出液面,起到除气除渣的效果。同时置换出来的ca元素进入到再生铝合金液,对si相进行细化变质,使粗大的针状si相转变成细小均匀的颗粒状或纤维状,可大幅提高再生铝合金的强度和塑性,而且加cacl2的方式不会引起再生铝合金液重新吸氢而导致再生铝合金的含气量上升。
[0064]
进一步地,所述精炼剂含有kbf4和k2tif6,kbf4的质量百分比为5-10%,k2tif6的质量百分比为5-10%。
[0065]
k2tif6和kbf4的主要作用是润湿al2o3等夹杂物,促进夹杂物与再生铝合金液的分离,提高除渣效率。kbf4的熔点为530℃,k2tif6的熔点为840℃,虽然k2tif6的熔点较高,但k2tif6和kbf4混合一起加入到再生铝合金液后,k2tif6和kbf4混合物可与再生铝合金液反应生成kalf4、k3alf6和tib2,反应得到的kalf4和k3alf6呈熔盐状态,表面张力大,不与再生铝合金液浸润,对al2o3等夹杂物具有很好的溶解润湿作用,促进al2o3等夹杂物与再生铝合金液分离后被气泡俘获上浮。反应得到的副产物tib2为高熔点高硬度的一微米左右的细小粒子,可充当再生铝合金液凝固时的异质形核核心,起到对再生铝合金的晶粒细化作用。k2tif6和kbf4的含量不宜过低,否者对再生铝合金的晶粒细化和对夹杂物的润湿效果不明显,含量也不宜过高,否者会产生大量kalf4、k3alf6熔渣而腐蚀工具和污染环境。
[0066]
进一步地,所述精炼剂含有baco3,baco3的质量百分比为5-10%。
[0067]
fe是再生铝合金中的杂质元素,由于废铝来源复杂,夹杂着各种铁钉、铁线、铁块等,导致再生铝合金中的fe元素含量较高,fe元素在再生铝合金常常形成粗大的针状或片状富fe相,会严重损害再生铝合金的力学性能、耐腐蚀性能等,也是导致现有再生铝合金品质不高的重要原因。为了消除fe元素的危害同时提高精炼剂的除气除渣效率,发明人通过大量实验研究后发现,在精炼剂中加入5-10%的baco3,不仅可以提高精炼剂的除气除渣效率,而且还对再生铝合金中的富fe相具有良好的细化变质效果,可将粗大的针状或片状富fe相细化变质成为细小均匀的颗粒状富fe相,不仅可以消除粗大针状或片状富fe相对力学性能、耐腐蚀性能的损害,而且还能提高再生铝合金的强度,取得意想不到的双重效果。虽然baco3的熔点较高,但baco3与其它氯盐和氟盐混合重熔、破碎后,baco3与其它氯盐和氟盐形成共晶体,在高温再生铝合金液中极易发生分解,分解成co2与bao,co2无色无味,co2气泡在上浮过程中可吸收氢气和捕获al2o3等夹杂物,达到除气除渣的效果。bao可与al发生置换反应,ba元素进入到再生铝合金液后对粗大富fe相具有很好的细化变质作用,可以提高再生铝合金的强度。
[0068]
进一步地,所述精炼剂含有ycl3,ycl3的质量百分比为3-6%。
[0069]
由于再生铝合金含有大量的si元素以及其它元素,导致再生铝合金的导热导电性能通常都比较低,这极大限制了再生铝合金的应用。为了在提高精炼剂的除气除渣效率同时还能提高再生铝合金的导热导电性能,现有技术通常是添加稀土元素,但稀土的价格较高,导致生产成本大幅上升。发明人通过大量实验研究后发现,在精炼剂中加入3-6%的ycl3,ycl3的熔点为721℃,当ycl3与高温再生铝合金液接触后发生反应生成沸点仅为183℃的alcl3,alcl3在再生铝合金液中形成气泡,气泡在上浮过程中将吸附带走氢气和al2o3等夹杂物,起到除气除渣的效果。同时置换出来的y元素进入到再生铝合金液中,对fe、si原子堆垛结晶起到阻碍作用,将铝基体内fe、si原子迁移到晶界,可大幅提高再生铝合金的导热导电性能,提高导热导电性能的效果比添加稀土元素更好,而且还可以降低再生铝合金的生产成本。
[0070]
本发明第二方面提供了一种再生铝合金精炼剂的制备方法,其特征在于,依次包括以下步骤:
[0071]
(1)按精炼剂的成分组成和质量百分比,选用mgcl2、kcl、cacl2、kbf4、k2tif6、baco3和ycl3为原材料进行配料;
[0072]
(2)将配料在80-100℃加热3-5小时进行烘干脱水;
[0073]
(3)将烘干脱水后的配料在900-1100℃加热1-2小时进行重熔,然后冷却凝固至室温;
[0074]
(4)将重熔后的精炼剂破碎、筛选和包装,得到所述再生铝合金精炼剂。
[0075]
步骤(1)中所述原材料可以是工业产品或工业副产品,但要保证原材料的纯度,不要含有太多杂质和水分,否者会影响精炼剂的除气除渣效率和对再生铝合金造成二次污染。作为优选地,选择纯度≥99.5%的mgcl2、kcl、cacl2、kbf4、k2tif6、baco3和ycl3作为原材料。
[0076]
步骤(2)中所述烘干是采用烘烤箱或加热炉进行高温加热,加热温度不宜太低,加热时间不宜太短,否者脱水不彻底。加热温度也不宜太高,否者会引起原材料发生热分解或氧化。
[0077]
步骤(3)中所述重熔是在真空条件下进行重熔,以避免发生原材料的氧化和蒸发。作为优选地,选择真空度10-20pa的真空炉进行重熔。
[0078]
现有技术制备铝合金精炼剂都是将原材料烘干脱水后直接混合得到成品精炼剂,这种制备方法虽然工艺简单,生产成本低,但没有充分发挥精炼剂成分之间的相互作用,这也是现有精炼剂普遍存在除气除渣效率偏低的一个重要原因。发明人通过实验研究后惊奇地发现,将原材料烘干脱水后再进行重熔,可使精炼剂的成分之间相互融合结晶,一是可以显著降低精炼剂的熔点,使精炼剂更容易熔解于再生铝合金液中,二是精炼剂的成分在再生铝合金液中可发生更好的物理化学作用,产生更好的除气除渣效果,提高精炼剂的除气除渣效率。重熔温度不能低于900℃,时间不能低于1小时,否者无法使原材料彻底熔解重新结晶。重熔温度也不用过高,时间也不用过长,否则会增加原材料的损耗和生产成本。优选地,将烘干脱水后的配料在1000℃加热1.5小时,可使精炼剂充分融合结晶。
[0079]
步骤(4)中所述破碎和筛选是采用破碎机和振动筛选机进行,包装是采用真空包装,以避免精炼剂吸水受潮。筛选得到的精炼剂的颗粒尺寸不宜过大,否者会影响精炼剂喷吹精炼的操作和除气除渣效果。作为优选地,所述精炼剂的颗粒尺寸≤1毫米。
[0080]
本发明第三方面提供了一种再生铝合金精炼剂的使用方法,采用惰性气体为载体,将占再生铝合金液重量0.2-0.4%的精炼剂喷吹进入再生铝合金液中,使精炼剂与再生铝合金液充分接触和反应,带走再生铝合金液中的氢气和夹杂物。所述惰性气体可以是氮气、氩气或者氮气和氩气的混合气体。作为优选地,选择纯度≥99.9%的氩气。精炼时再生铝合金液的温度不宜太高,否则会增加铝的烧损,温度也不能太低,否者会影响除气除渣的效果,作为优选地,精炼时再生铝合金液的温度为700-730℃。精炼剂的用量不宜太低,否者达不到理想的除气除渣效果。精炼剂的用量越大,除气除渣效果也越好,但也会增加生产成本和烟雾、铝渣的排放量。作为优选地,精炼剂的用量占铝合金液重量的0.3%。
[0081]
尽管已经示出和描述了本发明的实施例,对于本领域的普通技术人员而言,可以理解在不脱离本发明的原理和精神的情况下可以对这些实施例进行多种变化、修改、替换和变型,本发明的范围由所附权利要求及其等同物限定。