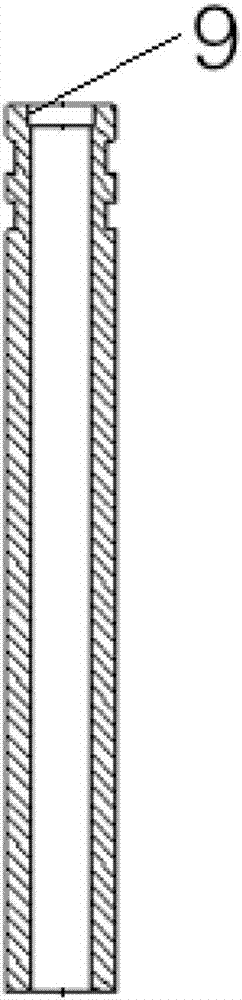
本发明创造属于光纤预制棒研发和制造
技术领域:
,尤其是涉及一种套管预制棒及其制造方法。
背景技术:
:光纤预制棒由芯棒和包层两部分组成,根据其组合结构可分为套管法和直接外部沉积法两种类型。套管法是光纤预制棒的芯棒和包层各自单独制备,然后进行组合并在线或离线熔缩成完整预制棒的一种方法。套管法的芯棒是实心棒体,套管是空心管,即为光纤预制棒的包层部分。直接外部外部沉积法是在芯棒外部直接沉积包层的方法。制造光纤预制棒芯棒的方法主要为化学气相沉积法,其主流工艺包括:改进的化学气相沉积工艺;微波等离子体化学气相沉积工艺;外部气相沉积工艺和气相轴向沉积工艺等。光纤预制棒包层的制备方法包括化学气相沉积法和物理沉积法两种类型。气相沉积主要指VAD和OVD等,物理方法主要指先进等离子体气相沉积工艺。在线套管法制备预制棒及拉丝工艺的流程主要包括以下几个步骤:(1)套管的制备以及拉锥;(2)芯棒的制备;(3)套管和芯棒的HF清洗;(4)芯棒和套管组装成成预制棒;(5)在高温下熔融预制棒组件并进行拉丝。熔融或拉丝时,必须对芯棒和套管之间的空腔进行抽真空处理,防止光纤中气泡或气线的产生。现有的套管预制棒技术主要采用的方法是:将制备的芯棒下端插入套管中与锥头部位接触,上部利用特殊的密封装置固定,并对套管和芯棒的空腔进行抽真空处理。这种装配的方式安装繁琐,操作复杂,且芯棒在插入套管时存在摩擦,一旦产生摩擦,容易导致碎屑掉落,有可能产能拉丝断纤、衰耗异常、强度差等现象,也容易造成气线、气泡问题。而且,这种装配方式很难保证芯棒与套管的同轴度,若芯棒偏离套管的中心,在拉制光纤时易造成芯层和包层之间的同轴度偏差。套管预制棒目前都是套管和芯棒分开放置,单独运输,然后在线组装好进行拉丝。技术实现要素:有鉴于此,本发明创造旨在克服上述现有技术中存在的缺陷,提出一种套管预制棒及其制造方法,可以有效地改善光纤的几何特性。为达到上述目的,本发明创造的技术方案是这样实现的:一种套管预制棒,包括套管组件、以及垂直插入套管组件内的芯棒组件;所述套管组件包括套管、套管上部的尾管、以及尾管内壁固定的定位环、以及尾管顶端用于密封的抽真空卡盘;所述芯棒组件包括芯棒以及芯棒上端与定位环配合的定位块;所述芯棒与套管同轴;穿过抽真空卡盘,设有用于抵住定位块的顶杆。进一步,所述定位块呈圆柱型结构,其直径大于芯棒直径;所述定位块的外壁与定位环的内壁配合。进一步,所述芯棒下端设有锥头。进一步,所述芯棒顶端与定位块焊接固定。进一步,所述尾管内壁设有用于安装定位环的卡槽。进一步,所述套管上端与尾管焊接。一种制造上述套管预制棒的方法,步骤如下:①制备芯棒;②将芯棒下端利用火焰车床拉锥处理,形成锥头;③将上述芯棒顶端与直径大于芯棒直径的定位块焊接固定,焊接后的芯棒组件的弓曲度控制在0.5mm/m以内;④套管下部打磨形成倒角,之后将倒角位置拉制成锥形尖端;⑤切除套管下部的锥形尖端,形成通气孔;⑥将上述套管的上端与尾管焊接固定,制成套管组件;⑦在尾管内壁的上部加工出用于安装定位环的卡槽;⑧将芯棒组件插入套管组件内,安装定位环,使定位环内壁与芯棒组件的定位块贴合,定位环外壁与卡槽内壁贴合;⑨在尾管顶端安装抽真空卡盘,将顶杆由抽真空卡盘外侧插入,抵住芯棒组件的定位块顶端。进一步,步骤②中,芯棒下端的锥头需经磨床打磨倒角。进一步,步骤⑥中,焊接后,保证套管与尾管接缝处无凸起或气线。相对于现有技术,本发明创造具有以下优势:本发明创造提供的套管预制棒的制造方法,可以适用于不同类型的芯棒和套管。采用定位环与定位块的组合设计,可以减少芯棒在插入套管时与套管内壁的碰撞、摩擦,减少套管预制棒拉丝过程中产生气线和气泡。通过这种组合设计,可以实现芯棒在套管中的的准直和对中的功能,能够优化光纤的芯包同心度,提高光纤的品质。通过这种组装方式满足长距离运输要求,减少了在光纤车间提供洁净装配间,减少了光纤生产员工的装配时间,提高了拉丝设备的效率。附图说明构成本发明创造的一部分的附图用来提供对本发明创造的进一步理解,本发明创造的示意性实施例及其说明用于解释本发明创造,并不构成对本发明创造的不当限定。在附图中:图1为本发明创造的结构示意图;图2为本发明创造中套管的的结构示意图;图3为本发明创造中定位环的结构示意图。附图标记说明:1-套管;2-尾管;3-定位环;4-抽真空卡盘;5-芯棒;6-定位块;7-顶杆;8-锥头;9-卡槽。具体实施方式需要说明的是,在不冲突的情况下,本发明创造中的实施例及实施例中的特征可以相互组合。在本发明创造的描述中,需要理解的是,术语“中心”、“纵向”、“横向”、“上”、“下”、“前”、“后”、“左”、“右”、“竖直”、“水平”、“顶”、“底”、“内”、“外”等指示的方位或位置关系为基于附图所示的方位或位置关系,仅是为了便于描述本发明创造和简化描述,而不是指示或暗示所指的装置或元件必须具有特定的方位、以特定的方位构造和操作,因此不能理解为对本发明创造的限制。此外,术语“第一”、“第二”等仅用于描述目的,而不能理解为指示或暗示相对重要性或者隐含指明所指示的技术特征的数量。由此,限定有“第一”、“第二”等的特征可以明示或者隐含地包括一个或者更多个该特征。在本发明创造的描述中,除非另有说明,“多个”的含义是两个或两个以上。在本发明创造的描述中,需要说明的是,除非另有明确的规定和限定,术语“安装”、“相连”、“连接”应做广义理解,例如,可以是固定连接,也可以是可拆卸连接,或一体地连接;可以是机械连接,也可以是电连接;可以是直接相连,也可以通过中间媒介间接相连,可以是两个元件内部的连通。对于本领域的普通技术人员而言,可以通过具体情况理解上述术语在本发明创造中的具体含义。下面将参考附图并结合实施例来详细说明本发明创造。一种套管预制棒,如图1至3所示,包括套管组件、以及垂直插入套管组件内的芯棒组件;所述套管组件包括套管1、套管1上部的尾管2、以及尾管2内壁固定的定位环3、以及尾管2顶端用于密封的抽真空卡盘4;所述芯棒组件包括芯棒5以及芯棒上端与定位环3配合的定位块6;所述芯棒与套管同轴;穿过抽真空卡盘4,设有用于抵住定位块的顶杆7。上述定位块呈圆柱型结构,其直径大于芯棒直径;所述定位块的外壁与定位环的内壁配合。上述芯棒下端设有锥头8。上述芯棒顶端与定位块焊接固定。上述套管上端与尾管焊接。上述尾管内壁设有用于安装定位环的卡槽9。下面提供一种制造上述套管预制棒的方法,步骤如下:①制备芯棒;②将芯棒下端利用火焰车床拉锥处理,形成锥头;③将上述芯棒顶端与直径大于芯棒直径的定位块焊接固定,焊接后的芯棒组件的弓曲度控制在0.5mm/m以内;④套管下部打磨形成倒角,之后将倒角位置拉制成锥形尖端;⑤切除套管下部的锥形尖端,形成通气孔;⑥将上述套管的上端与尾管焊接固定,制成套管组件;⑦在尾管内壁的上部加工出用于安装定位环的卡槽;⑧将芯棒组件插入套管组件内,安装定位环,使定位环内壁与芯棒组件的定位块贴合,定位环外壁与卡槽内壁贴合;⑨在尾管顶端安装抽真空卡盘,将顶杆由抽真空卡盘外侧插入,抵住芯棒组件的定位块顶端。将上述组装而成的套管预制棒插入拉丝炉中,插上抽真空的气管,升温后拉丝即可。在步骤②中,芯棒下端的锥头需经磨床打磨倒角。在步骤⑥中,焊接后,保证套管与尾管接缝处无凸起或气线。需要说明的是,上述的芯棒采用管内法或管外法制备,在芯棒中含有掺Ge的芯层和纯SiO2(或掺F的SiO2)的内包层组成,将沉积烧结后的芯棒在预制棒折射率测试系统(PK2600)测试合格后,再根据芯包比将芯棒延伸到合适的外径,以进行下一步操作。制作芯棒组件时,芯棒的下端利用火焰车床拉锥处理,芯棒的锥头再经过磨床打磨倒角,防止芯棒组件在插入套管组件时划伤套管内壁,芯棒的上端和定位块利用火焰车床焊接,定位块呈圆柱型结构,直径大于芯棒直径,焊接后保证接头位置无明显凸起且接缝处无气泡存,同时芯棒组件的弓曲度在1mm/m。优选控制在0.5mm/m。另外,芯棒下端的拉锥以及芯棒上端与定位块的焊接均采用等离子焊接车床实现,可以减小光纤在1383nm的水峰。加工好的芯棒组件再经过HF酸和纯水处理,腐蚀量控制在0.5mm,经高纯氮气干燥后用洁净袋包好备用。制作套管组件时,套管下部首先通过磨床打磨形成外倒角,再将套管下端倒角部位拉制成锥形,同时切除套管锥形顶端的部位,形成通气孔。套管上部通过磨床打磨内倒角,然后与尾管焊接,焊接后接缝处无凸起或气线,同时套管组件的弓曲度<0.5mm/m。尾管内腔进行开槽处理,用于放置定位环,定位环外壁和尾管接触,定位环内壁和芯棒组件中的定位块接触,尾管上方放置抽真空卡盘用于密封。套管下部的锥形可以将套管在石墨炉中通过掉锥实现,保证锥部的形状。将加工好的套管组件再经过HF酸和纯水处理,腐蚀量控制在0.2mm。经高纯氮气干燥后利用手灯将套管锥头的通气孔封住,待锥头冷却后继续用高纯氮气干燥,而后用洁净袋包好。组装本套管预制棒时,首先把下端密封的套管转移到运棒车上,将套管竖直放置,在尾管内腔的凹槽放置用HF酸和纯水处理过的定位环,再将芯棒组件沿垂直方向缓慢地插入尾管定位环中,由于有定位环的存在,芯棒在插入套管时减少了芯棒与套管内壁的碰撞、摩擦。待芯棒下端和套管锥部接触后,再把顶杆垂直插入尾管中,压住定位块,将抽真空卡盘缓慢地穿过顶杆,落到尾管的正上方,通过锁紧装置将抽真空卡盘和顶杆都锁死。芯棒在套管中保持准直、对中的功能,同时在运输套管棒时不会产生晃动,满足长途运输的条件。本发明创造中各部件具体结构设置如下:芯棒:其外径OD1的范围是:OD1<ID3,长度L1的范围是:1200~1700mm。套管:其内径ID2的范围是:(OD1+1)~(OD1+4)mm,长度L2的范围是L2≥(L1+30)mm,外径OD2由光纤的设计决定。尾管:其外径OD3与套管外径一致,其内径ID3的范围是70~85mm,其长度L3由光纤拉丝塔最小允许长度决定。尾管内腔凹槽的外径OD4的范围是(OD3-60)~(OD3-40)mm,其内径ID4的范围是(ID3-25)~(ID3-15)mm,凹槽到套管的距离L4≤L2。定位环:其外径OD5的范围(ID4-1)~(ID4-0.5)mm,其内径ID5的范围是ID2≤ID5≤ID4,其距离尾管顶部的距离L5范围是L5≤L2-L4,其固定在尾管内腔的凹槽上部,材质是高纯石英砂,并进行抛光处理。定位块:其外径OD6的范围是(ID5-1)~(ID5-0.5)mm,其长度L6由尾管内腔凹槽的位置决定,范围是L4≤L6≤L2。同样地,其材质也是高纯石英砂,并进行抛光处理。实施例1利用VAD工艺制备的粉末棒经过烧结、延伸处理后制成一根芯棒。通过PK2600的测试芯棒的折射率剖面,得出其包芯比4.20。芯棒的长度是1500mm,直径为36mm。定位块的长度1200mm,直径60mm。将芯棒下端在火焰车床上拉锥处理,芯棒上端和定位块在火焰车床上焊接,焊接后芯棒组件的弓曲度控制在0.2mm/m。再将芯棒组件用HF和纯水进行处理,处理后放入干燥柜待用。采用外径是130mm,内径37mm的套管,首先在火焰车床上将套管和尾管焊接,尾管的外径150mm,内径82mm,长度1250mm。焊接后接头位置无气线,同时焊接后套管组件弓曲度满足0.1mm/m。利用数控车床将尾管上端开槽处理,开槽后内径91mm,距离尾管上端距离30mm。套管下端利用火焰车床拉锥或者通过加热炉掉锥处理,形成10-20mm的通气孔,然后将套管组件利用HF和纯水处理,将干燥好的套管组件下端的通气孔用氢氧焰喷灯封锥。将芯棒组件和套管组件在洁净室进行装配。首先将套管组件利用行车转移到运棒小车上,将套管组件竖直放置,将用HF和纯水处理过的定位环安装在尾管的槽内固定,然后将芯棒组件垂直插入尾管中,固定在定位环处。再将顶杆插入尾管中,顶住芯棒组件中的定位块,再将抽真空卡盘固定在尾管上端,用锁紧装置锁死。确保芯棒组件在套管组件里面无晃动。再用洁净袋将套管预制棒包装好,运输到拉丝车间,当然也可以装箱,满足长距离运输条件。将套管预制棒组件挂到拉丝塔挂棒机构上,将抽真空管子插上真空泵,即可完成套管预制棒的拉丝准备工作。光纤的拉丝数据如下表1所示,均满足G652D光纤的参数要求。表1新型结构套管预制棒的光纤参数实施例2利用VAD工艺制备的粉末棒经过烧结、延伸处理后制成一根芯棒。通过PK2600的测试芯棒的折射率剖面,得出其包芯比3.90。芯棒的长度是1700mm,直径为39mm。定位块22的长度1200mm,直径60mm。将芯棒下端在火焰车床上拉锥处理,芯棒上端和定位块在火焰车床上焊接,焊接后芯棒组件的弓曲度控制在0.2mm/m。再将芯棒组件用HF和纯水进行处理,处理后放入干燥柜待用。套管使用外径是150mm的套管,内径43mm,首先在火焰车床上将套管和尾管焊接,尾管的外径150mm,内径82mm,长度1250mm。焊接后接头位置无气线,同时焊接后套管组件弓曲度满足0.1mm/m。利用数控车床将尾管上端开槽处理,开槽后内径91mm,距离尾管上端距离30mm。套管下端利用火焰车床拉锥或者通过加热炉掉锥处理,形成10~20mm的通气孔,然后将套管组件利用HF和纯水处理,将干燥好的套管组件下端的通气孔用氢氧焰喷灯封锥。将芯棒组件和套管组件在洁净室进行装配。首先将套管组件利用行车转移到运棒小车上,将套管组件竖直放置,将用HF和纯水处理过的定位环安装在尾管的槽内固定,然后将芯棒组件垂直插入尾管中,固定在定位环处。再将顶杆插入尾管中,顶住芯棒组件中的定位块,再将抽真空卡盘固定在尾管上端,用锁紧装置锁死。确保芯棒组件在套管组件里面无晃动。再用洁净袋将套管预制棒包装好,运输到拉丝车间,当然也可以装箱,满足长距离运输条件。将套管预制棒组件挂到拉丝塔挂棒机构上,将抽真空管子插上真空泵,即可完成套管预制棒的拉丝准备工作。光纤的拉丝数据如下表2所示,均满足G.652D光纤的参数要求。表2新型结构套管预制棒的光纤参数芯包同心度误差截止波长1310模场直径零色散波长1383nm衰耗umnmumnmdB/km0.212859.3413080.278本发明采用定位环和定位块组合的新型结构,解决了芯棒在垂直插入套管内壁的摩擦,同时利用定位环确保了芯棒在套管中的准直和对中的功能,保证了芯棒和套管的同轴度。本发明创造是将芯棒垂直地插入套管中,既不造成芯棒在套管内壁的摩擦,也保证了芯棒在套管中的同轴度,同时组装好的套管预制棒可以直接运输到光纤拉丝塔进行抽真空作业,继而完成拉丝作业,减少了在光纤车间组装的环节。通过这种组装方式满足长距离运输要求,减少了在光纤车间提供洁净装配间,减少了光纤生产员工的装配时间,提高了拉丝设备的效率。以上所述仅为本发明创造的较佳实施例而已,并不用以限制本发明创造,凡在本发明创造的精神和原则之内,所作的任何修改、等同替换、改进等,均应包含在本发明创造的保护范围之内。当前第1页1 2 3