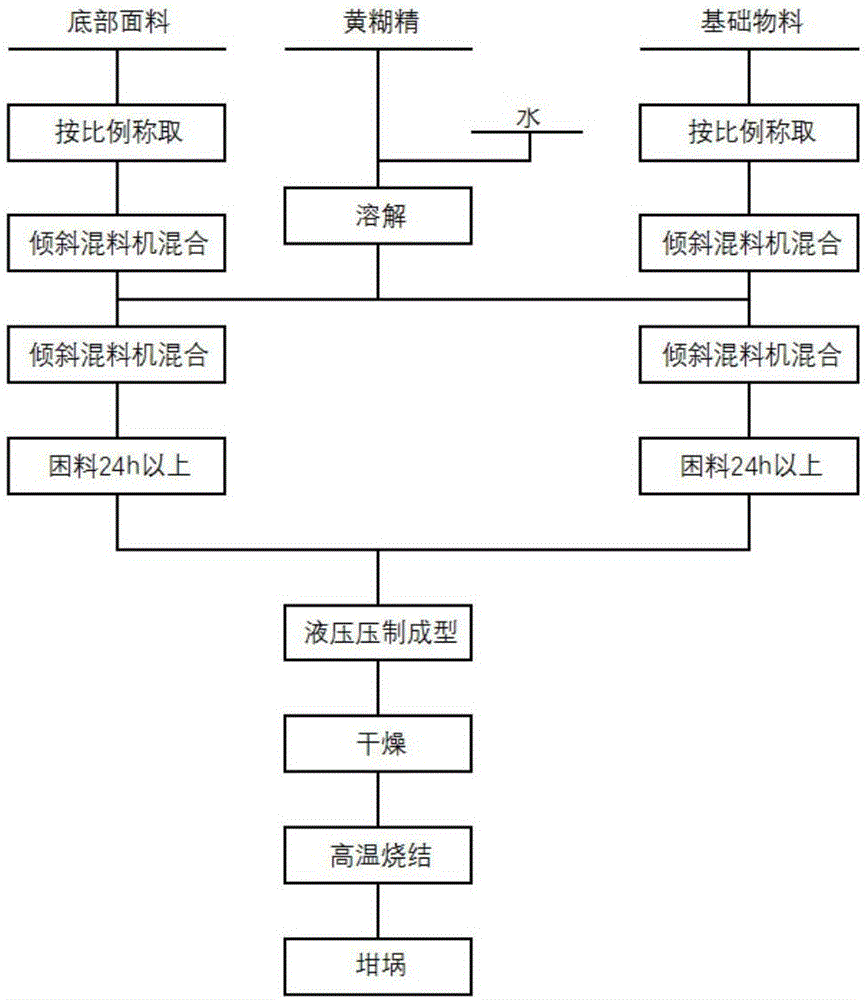
本发明锂电池材料
技术领域:
,具体涉及一种锂电专用高循环特种陶瓷坩埚及其制备方法。
背景技术:
:锂电池正极材料必须经过高温窑炉的焙烧,烧成过程须采用坩埚来装载。我国使用的坩埚材料从材质上大体分为五类:硅铝质坩埚、硅铝镁质坩埚、半硅质坩埚、粘土-熔融石英质坩埚和碳化硅坩埚。用于锂离子电池正极材料生产的坩埚材质,主要是莫来石质或莫来石-堇青石质及刚玉莫来石质。目前合成锂离子电池正极材料实际生产中,一般都采用高温固相合成法,高温固相合成法工艺简单且对设备要求不高,适合规模化生产。该法将所需要原料直接以固态形式,通过机械高速搅拌混合,然后在高温下焙烧,冷却后经过破碎、过筛而得。在高温焙烧过程中,由于正极原料对坩埚的侵蚀比较大,要求坩埚具有高强的耐侵蚀性。现有的坩埚材料主要存在以下问题:(1)使用寿命短。锂离子电池正极材料合成过程中所用的坩埚一般为刚玉质、莫来石质、石英质和堇青石质耐高温坩埚,由于合成锂离子电池正极材料的原料在合成过程中会分解产生渗透力和反应活性强的氧化锂,对耐高温坩埚有侵蚀作用,此外,坩埚材料在高温后快速冷却时,随着使用次数的增加,容易产生裂纹,坩埚的热震稳定性受到破坏,最终使耐高温坩埚的使用寿命大大降低;(2)坩埚材料抗侵蚀性差。抗侵蚀性是锂离子电池正极材料在合成过程中的一个重要指标,由于锂离子在与坩埚接触的过程中,锂离子能够将坩埚中的si、al和mg等离子析出,从而破坏坩埚微观结构,使坩埚遭到侵蚀,在坩埚表面出现一层蓝白色的侵蚀层,导致坩埚使用寿命缩短;(3)坩埚热震稳定性变差。坩埚在使用过程中,环境温度的急剧变化会使坩埚产生裂纹,最终剥离甚至开裂,坩埚随着材料合成过程中温度的升、降变化,产生膨胀或收缩,如果收缩和膨胀受到的束缚不能够自由发展时,坩埚材料内部会产生应力,由于其热膨胀较大,热导率和弹性比较小,抗应力能力差,导致其热震稳定性较差,另外由于其它原因,会有烧成不充分的坩埚,这种坩埚在窑炉上高温使用时,一些烧成变化继续进行,使得坩埚的体积发生膨胀或者收缩,这种不可逆的体积变化,也会导致坩埚出现裂痕;(4)坩埚强度低。坩埚通常是双层或多层入窑炉,随着自动化程度的提高,坩埚要承担自身的重量和合成材料的重量,同时还要受到进出窑炉、装卸物料的机械作用力,所以坩埚需要有足够的机械强度。在高温下,强度不足会使坩埚产生塑性变形,因此坩埚需要足够的高温机械强度、高的荷重软化温度和抗蠕变性能;(5)坩埚材料易起皮、掉渣和污染产品。在坩埚使用过程中,含锂化合物先于含钴化合物对坩埚进行侵蚀,形成一种复合化合物并且从中析出,导致产生剥离甚至脱落现象,从而使产品受到污染。国内使用的坩埚主要来自日本、韩国以及国产,坩埚材料在使用过程中,日本的坩埚最为优异,韩国次之,国产的最差。日韩坩埚在辊道窑炉上的使用过程中,寿命大约在25~30次,单个坩埚的售价在200~300元之间,而在推板窑炉上,部分使者反馈使用几次之后坩埚就出现了开裂现象。国产坩埚在抗腐蚀性和节能降耗方面基本都没有达到国外中等水平,大部分厂家都是采用手工模具敲打或者简单机械摩擦震动的成型工艺,主打低质低价的生产销售模式。各大厂家生产的坩埚,随着使用次数的增加,或多或少都有起皮、脱落、变形、开裂及底部粘料的现象,给产品品质带来了较大的安全隐患,且随着国内自动化生产线及日韩辊道窑炉的大规模使用,国内坩埚已经越来越不能满足生产的需求,辊道窑炉自动化生产线要求坩埚底部平整度空隙≤1.5㎜,而国内厂家能够保证的是不大于2mm,这将给辊道窑炉生产过程带来极大的安全隐患。随着各种新型锂离子电池正极材料的出现和发展,高电压钴酸锂、高镍两元和镍钴铝的开发,以及电动汽车市场的高度活跃,对锂离子电池正极材料用坩埚的需求量日益加大。随着正极材料制备行业自动化程度的提高,对坩埚材料的性能也提出了新的要求。坩埚材料首先应该具有良好的抗侵蚀性能、热震稳定性、抗扭曲性、气氛适应性和一定的强度,此外在使用过程中不能起皮、掉渣,不能带入磁性异物污染产品。cn105669223a公开了一种用于锂电池正极材料焙烧的坩埚,包括底面和侧壁,底面和侧壁形成用于焙烧的凹腔,坩埚包括基体和工作层,工作层在基体工作面上,基体的成分包括莫来石、刚玉、高岭土、氧化铝粉、石英和堇青石,工作层的成分包括钾长石、熔融石英、莫来石、红柱石、刚玉、氧化铝粉和氧化锆粉,制造坩埚时,先以干法成型的方式将工作层压在基体工作面上。本发明能有效地提高用于锂电池正极材料焙烧的坩埚的使用寿命,降低制造成本。cn102491773a公开了一种高晶体莫来石-堇青石质高温工业陶瓷及其生产方法,原料包括主晶相材料和结合复合基质料,以及适量的复合微晶成核剂,焙烧工艺包括二段恒温烧成法和二段复合晶化合成反应,该发明的耐火制品,具有抗氧化性能优异、耐火度高、使用温度高和热膨胀系数低等优点,然而该发明陶瓷的使用寿命数据未知。cn103311498a公开了一种焙烧坩埚及其制备方法,制备方法为先将莫来石、堇青石、氧化铝、刚玉、高岭土、活性氧化镁、锂辉石和结合剂混合均匀并压制成生坯,再将氧化锆、锂辉石、氧化铈、刚玉和结合剂混合均匀,并使混合物均匀分布生坯表面,通过设备再次压制,得到坩埚半成品,最后将坩埚半成品干燥后进行烧成,该发明陶瓷的使用寿命数据同样未知。综上所述,仍需开发一种可以广泛应用于锂离子电池正极材料的坩埚,这种坩埚应具有较长的使用寿命,较好的材料抗侵蚀性、强度和热震稳定性,不易起皮和掉渣,能够满足用户全自动化流水线生产模式的生产。技术实现要素:为解决现有技术中存在的问题,本发明的目的之一是提供一种锂电专用高循环特种陶瓷坩埚。本发明的目的之二是提供上述坩埚的制备方法。为实现以上目的,本发明采用以下技术方案:一种锂电专用高循环特种陶瓷坩埚,所述坩埚包括以细颗粒耐腐蚀材料为主料的表面工作层和以热膨胀系数小、耐高温材料为主料的基体层,所述细颗粒耐腐蚀材料的粒径范围是0~2mm,所述表面工作层厚度大于2mm,所述基体层主料的热膨胀系数范围是(2.8~3.2)×10-6,耐高温范围是≤1300℃。优选地,所述表面工作层包括以下重量份计的原料:高岭土5~30份,白刚玉30~70份,氧化铝5~15份,莫来石5~60份,粘结剂1~5份,锂辉石粉2~10份,堇青石1~20份,水1~5份。优选地,所述基体层包括以下重量份计的原料:莫来石10~60份,高岭土5~20份,氧化铝0~10份,碳酸镁1~10份,堇青石10~50份,滑石5~20份,镁铝尖晶石0~10份,红柱石0~10份,粘结剂1~5份,水1~5份。优选地,所述白刚玉为100~325目的白刚玉颗粒和10~100目的白刚玉粉末按照重量比为(0.1~0.5):1的混合物。优选地,所述莫来石为电熔莫来石m70。优选地,所述莫来石为0.1~1mm的m45烧结莫来石和1~5mm的m45烧结莫来石按照重量比为(0.1~0.5):1的混合物。优选地,所述粘结剂为黄糊精,所述氧化铝为α-氧化铝微粉。优选地,所述基体层中的堇青石为小于8目的堇青石和300~355目的堇青石按照重量比为1:(0.1~0.5)的混合物。一种锂电专用高循环特种陶瓷坩埚的制备方法,包括以下步骤:(1)按配比称取表面工作层各原料,将黄糊精溶解于水,将高岭土、白刚玉、氧化铝微粉、电熔莫来石、锂辉石粉和堇青石混合,加入预先溶解好的黄糊精溶液混合;(2)按配比称取基体层各原料,将黄糊精溶解于水,将烧结莫来石、高岭土、氧化铝微粉、碳酸镁、堇青石、滑石、电熔镁铝尖晶石和红柱石混合后加入预先溶解好的黄糊精溶液混合均匀;(3)将步骤(1)制备得到的表面工作层材料加到模具底部,压制得到表面工作层;(4)将步骤(2)制备得到的基体层材料均匀布满整个模具,压制得到半成品;(5)将步骤(4)的半成品干燥后烧成。优选地,步骤(3)压制前,先将步骤(1)和(2)制备得到的表面工作层材料和基体层材料放置在密封的容器中进行困料,放置时间大于24h。优选地,步骤(3)和(4)压制采用全自动坩埚液压成型机,液压机的吨位≥500t。步骤(5)所述干燥的温度为50~200℃,干燥的时间大于12h。优选地,步骤(5)所述烧成的时间为30~40h,温度为1250~1450℃。坩埚在压制过程中是倒着压制的,坩埚在使用过程中表面工作层与电池的正极材料接触。本发明的有益效果1、本发明的坩埚表面工作层材料采用耐腐蚀材料细颗粒为主料,基体层材料采用热膨胀系数小、耐温高的材料为主料,减缓了底部起皮和粘料的时间,解决侧面和底部开裂现象;2、本发明坩埚坯体具有一定的强度,坯体干燥后再放入窑中烧结,烧成后的坩埚底部平整度相比其他窑炉烧成的效果好,能够满足用户全自动化流水线生产模式的生产;3、与现有技术产品相比,本发明的坩埚气孔率低、体积密度高、抗蠕变性好、抗热震性好和使用寿命长等优点,适用于锂电池正极材料的高温烧结。附图说明图1为本发明坩埚的制备工艺流程图。具体实施方式以下是本发明的具体实施例,并结合附图说明对本发明的技术方案作进一步的描述,但本发明并不限于这些实施例。实施例1本实施例提供了a1~f1六种表面工作层材料和对应的a2~f2六种基体层材料,具体配方如表1所示。表1a1~f1六种表面工作层材料配方表2a2~f2六种基体层材料配方实施例2本实施例提供了锂电专用高循环特种陶瓷坩埚的制备方法,工艺流程如图1所示,具体包括以下步骤:(1)按配比称取表面工作层各原料,将黄糊精溶解于水,将高岭土、白刚玉、氧化铝微粉、电熔莫来石、锂辉石粉和堇青石混合,加入预先溶解好的黄糊精溶液混合;(2)按配比称取基体层各原料,将黄糊精溶解于水,将烧结莫来石、高岭土、氧化铝微粉、碳酸镁、堇青石、滑石、电熔镁铝尖晶石和红柱石混合后加入预先溶解好的黄糊精溶液混合均匀;(3)将步骤(1)制备得到的表面工作层材料加到模具底部,压制得到表面工作层;(4)将步骤(2)制备得到的基体层材料均匀布满整个模具,压制得到半成品;(5)将步骤(4)的半成品干燥后烧成。步骤(3)压制前,先将步骤(1)和(2)制备得到的表面工作层材料和基体层材料放置在密封的容器中进行困料,放置时间大于24h。步骤(3)和(4)压制采用全自动坩埚液压成型机,液压机的吨位≥500t。步骤(5)所述干燥的温度为50~200℃,干燥的时间大于12h,烧成的时间为30~40h,温度为1250~1450℃。实施例3采用实施例1提供的六种配方和实施例2提供的方法,制备得到对应的a~f六种锂电专用高循环特种陶瓷坩埚,步骤(3)压制前,先将步骤(1)和(2)制备得到的表面工作层材料和基体层材料放置在密封的容器中进行困料,放置时间大于24h。步骤(3)和(4)压制采用全自动坩埚液压成型机,液压机的吨位≥500t。步骤(5)所述干燥的温度为75℃,干燥的时间大于12h,烧成的时间为35h,温度为1350℃。坩埚的常温抗压强度和使用寿命如表3所示。表3坩埚的常温抗压强度和使用寿命坩埚编号常温抗压强度/mpa使用寿命(次)a7530b7735c8855d9560e8545f8240对比例1采用实施例1中提供的表面工作层d1和基体层d2的配方和实施例2提供的方法,制备得到对应的g~i三种锂电专用高循环特种陶瓷坩埚。坩埚g在步骤(3)压制前,步骤(1)和(2)制备得到的表面工作层材料和基体层材料未经困料直接压制。步骤(3)和(4)压制采用全自动坩埚液压成型机,液压机的吨位≥500t。步骤(5)所述干燥的温度为75℃,干燥的时间大于12h,烧成的时间为35h,温度为1350℃。坩埚h在步骤(3)压制前,先将步骤(1)和(2)制备得到的表面工作层材料和基体层材料放置在密封的容器中进行困料,放置时间为12h。步骤(3)和(4)压制采用全自动坩埚液压成型机,液压机的吨位≥500t。步骤(5)所述干燥的温度为75℃,干燥的时间大于12h,烧成的时间为35h,温度为1350℃。坩埚i在步骤(3)压制前,先将步骤(1)和(2)制备得到的表面工作层材料和基体层材料放置在密封的容器中进行困料,放置时间大于24h。步骤(3)和(4)压制采用全自动坩埚液压成型机,液压机的吨位≥500t。步骤(5)所述干燥的温度为75℃,干燥的时间大于12h,烧成的时间为35h,温度为1500℃。坩埚a与坩埚g~i的坩埚的常温抗压强度和使用寿命如表4所示。表4坩埚的常温抗压强度和使用寿命对比对比例2本对比例比较了本发明的坩埚和三种市售坩埚的单耗、使用寿命和成本比例,具体如表5所示。表5坩埚a和三种市售坩埚的单耗、使用寿命和成本比例对比当前第1页12