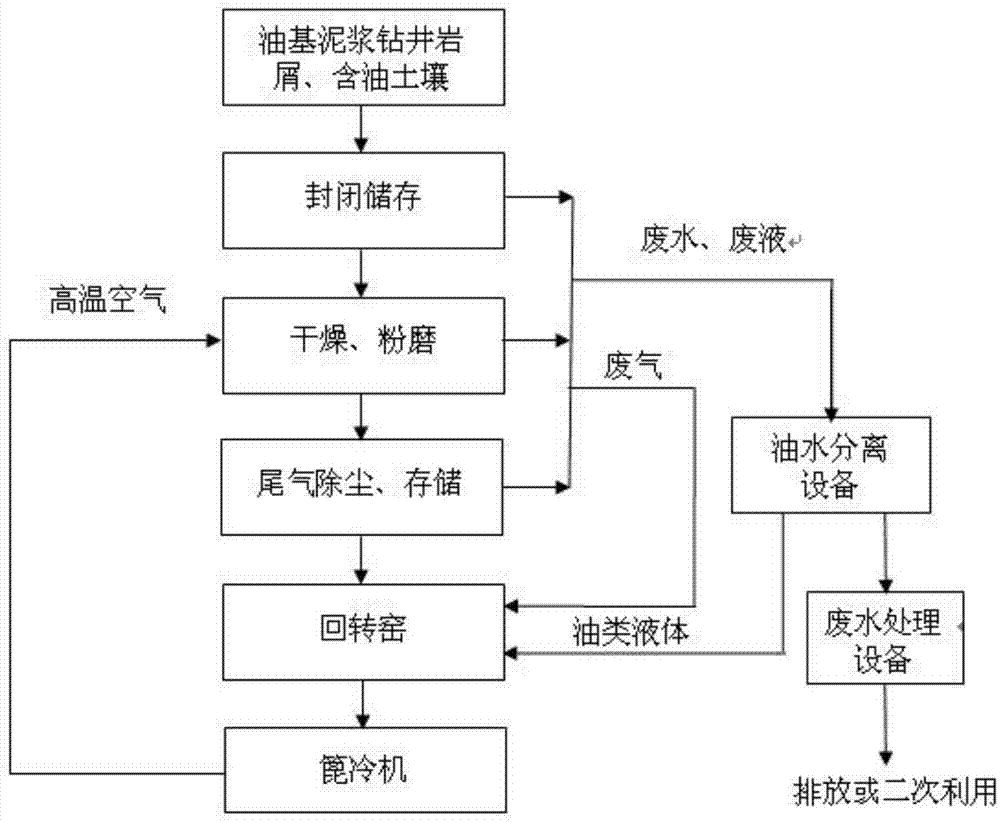
本发明属于固体废弃物的处理
技术领域:
,涉及水泥窑协同处理废弃物的技术方法,尤其涉及一种利用水泥窑协同处理油气井钻采过程中产生的固体废弃物:油基泥浆钻井岩屑、含油土壤,制备硅酸盐水泥的设备及其方法。
背景技术:
:油基钻井泥浆是以白油或柴油作连续相的钻井液,相对于水基钻井泥浆,具有抗高温、抗盐钙侵蚀,有利于井壁稳定、润滑性好、对油气层损害小等优点。在复杂井、页岩气井中得到广泛运用。但在采用油基泥浆进行油气资源开发钻井过程中,产生大量的油基泥浆钻井岩屑。油基泥浆钻井岩屑中除地层矿物外,还含有基油(柴油或白油)、乳化剂、润湿剂、亲油胶体、石灰、加重材料等物质,其危害环境的主要成分是烃类、盐类、各种聚合物、木质素磺酸盐、重晶石及某些金属离子如汞、铜、砷、铬、锌、铅等。我国每年废弃泥浆排放总量约为100多万m3,含油土壤为石油开采、输送过程中由于泄露污染的土壤,土壤中石油类物质超过一定含量,对周围生态环境、地下水和人体健康均产生严重影响显。这类废弃物如果不进行安全的无害化处理,势必要对生态环境造成严重的影响,形成较大的环境污染隐患,对其周边的土壤、植被、地表水和地下水造成严重污染。油基泥浆钻井岩屑、含油土壤组成复杂,含有大量有害成分,因此不能采用水基泥浆钻井岩屑的处理方法处理,如中国专利申请cn201510049025.5、cn201710838873.3。目前油基泥浆钻井岩屑有效处理方法主要有热分解、生物处理。中国专利申请cn200520000600.4、201710425759.8、cn201711008576.2均采用的高温热分解方法对岩屑进行处理。热分解方法存在两大问题:一是需要外加能源将岩屑加热到高温,导致资源浪费严重。需要另外建设大量污染治理装置,且飞灰仍然属于危险废物;二是对产生的有害气体物质没有完善的处理工艺措施,容易形成二次污染。中国专利申请cn201611090583.7、cn201710022627.0采用生物发酵的方式进行处理,该种方法对环境条件苛刻、处理量少、处理周期长、成本高,如控制不当,还易造成对当地生态环境的破坏,该类处理技术尚不成熟。中国专利申请cn201711480693.9利用油基钻井岩屑制备低热硅酸盐水泥熟料,先采用离心方法脱油、脱水,加入吸附剂后与水泥生料混合粉磨,然后进入回转炉煅烧。然而由于油基泥浆钻井岩屑中含有大量的有机物,在未进入预分解炉前,高分子有机物就分解成有机气体,不能达到回转窑的高温区,无法利用高温对其进行分解,尾气会对大气产生严重污染。因此该方法只能处理高温处理后的岩屑,需要额外增加预处理工艺。此外,该专利申请是利用岩屑生产低热水泥,我国低热水泥用量占比极少,所以采用该方式处理岩屑的能力极低。专利201110071245.x公布了一种水泥窑协同处理污染土的方法,通过将污染土破碎、粉磨、烘干后经窑尾送入回转窑,磨机尾气送入窑尾预然室或分解炉。该专利中采用了选粉机选粉工艺,因此不适用于成分复杂、比重差异过大的固废,比如油基泥浆钻井岩屑,这是由于岩屑中含有较高比例的重晶石,其密度远大于其他组分。此外,油基泥浆岩屑、含油土壤中含有大量有机物,导致干燥后的尾气中含有大量有机物,而窑尾的温度偏低,且含氧量不足,不利于分解有机物,也不利于达到利用有机物燃烧降低水泥生产能耗的目的。专利201210011334.x利用水泥窑协同处理固体危险废弃物,通过对固废进行干化、破碎、粉磨预处理,废气进入水泥窑尾烟室处理,固废粉料通过气力输送送至水泥窑窑尾烟室。由于该专利的高温空气引自水泥厂余热尾气,因此不适用于干燥含油固体废弃物,更不能将尾气引入回转窑高温处理。此外,通过气力输送将固废粉体送入窑尾,将影响从回转窑进入分解窑高温气流的温度,从而影响整个窑外分解工艺,增加煤耗成本。专利201610026080.7公布了一种水泥窑焚烧污染土的处理方法,该专利将污染土经破碎后直接送入窑尾进行处理。由于污染土只经过简单破碎,与生料不能充分混合反应,最终将导致水泥质量波动。上述技术所述的工艺流程未全流程控制处理过程中可能产生的二次污染,不满足水泥窑处理危险固体废弃物的相关要求。技术实现要素:本发明旨在提供一种利用水泥窑协同处理钻井固体废弃物,如废油基泥浆钻井岩屑、含油土壤制备系列硅酸盐水泥的设备和方法。本发明采用硅酸盐水泥生产系统,在全封闭状态下将产生的有害气体引入回转窑高温燃烧分解;油井泥浆钻井岩屑、含油土壤经烘干后脱除水分,粉磨达到一定细度作为硅质原料,在全封闭状态下从高温入口送入水泥生产系统,与水泥生料反应生成硅酸盐水泥熟料;油基泥浆中油类物质替代部分燃料;利用水泥窑高温段分解voc、二噁英,利用水泥窑现有末端治理设施处理烟粉尘、氮化物等大气污染物,解决了油基泥浆岩屑、含油土壤处理过程中的二次污染,达到了对油基泥浆钻井岩屑、含油土壤的无害化、减量化和资源化综合利用的目的。为了实现上述发明目的,本发明首先提供了以下利用水泥窑协同处理钻井废弃物的设备:利用水泥窑协同处理钻井废弃物的设备,包括水泥回转窑,其特征是:还包括钻井废弃物存储与处理封闭系统、废气收集封闭处理系统、废水废液收集处理系统;所述钻井废弃物为油基泥浆钻井岩屑或含油土壤;废弃物封闭存储与处理系统,系统包括微负压储存库、高温粉磨设备、微负压干粉仓、密封输送设备和计量投料设备;微负压储存库中暂存的钻井废弃物经密封输送设备输送进入高温粉磨设备,经干燥粉磨后进入全封闭的微负压干粉仓暂存,通过计量投料设备进入回转窑;整个系统为全封闭;废气收集封闭处理系统,所述废气包括危险废物微负压储存库废气、粉磨废气、微负压干粉仓废气;系统包括废气收集风机及管道、高温气流管道、废气管道;由回转窑篦冷机热风口引入的热风通过高温气流管道送至高温粉磨设备一端,从高温粉磨设备另一端经管道回送至篦冷机、回转窑进行高温燃烧分解;废水废液收集处理系统,所述废水废液包括设备场地冲洗废水、微负压储存库渗滤液;系统包括废水废液收集管沟、密封输送设备、油水分离设备、油类废液入窑设备、废水处理回收和排放设备。进一步所述微负压储存库用于储存钻井废弃物,微负压储存库顶部设置负压风机,通过排气管道与篦冷机、回转窑或三次风管联接。进一步所述计量投料设备包括联接于微负压干粉仓出料口的称量装置和投料装置;微负压干粉仓与高温粉磨设备封闭联接用于接收经干燥、粉磨的粉体;称量装置为自动称量装置,投料装置的投料口设置于回转窑窑头或窑尾。进一步所述投料装置为风送粉体投料装置,包括鼓风机、风力粉体输送管和粉体供料机,粉体供料机入口联接干粉储库、出口联接风力粉体输送管,风力粉体输送管喷口与回转窑燃料喷煤口相邻。进一步所述投料装置为螺旋供料装置,包括干粉螺旋供料管和粉体供料机,粉体供料机入口联接干粉储库、出口经干粉螺旋供料管与回转窑燃料喷煤管联接。进一步所述投料装置的投料口设置于回转窑窑尾,投料装置为螺旋供料装置;包括粉体供料机和干粉螺旋供料管,粉体供料机入口联接干粉储库、出口经干粉螺旋供料管设置于回转窑窑尾。本发明所述高温粉磨设备包括高温磨机,高温磨机为风扫式磨机、气流磨或冲击磨的一种,在热风对物料烘干的同时进行粉磨;热风来自冷却熟料的空气,温度80-600℃。本发明所述废水废液收集处理系统用于收集处理全系统排放的液体,通过收集设备将废水废液送至集中处理设备,经油水分离后,油类液体作为部分替代燃料经入窑设备送回转窑燃烧,废水符合标准后综合利用或排放。本发明还公开了一种利用水泥窑协同处理钻井废弃物的方法,其特征是:采用上述协同处理钻井废弃物的设备;具体包括以下方法:1)将钻井废弃物储存于微负压储存库中,并通过密封输送系统送至干燥和粉磨系统的高温磨机进行干燥和粉磨;2)由回转窑篦冷机热风口引入热风通过管道输送至高温粉磨设备,高温粉磨设备尾端将尾气通过管道回送至回转窑,利用1000-1500℃高温燃烧分解尾气中的有机物;其中,引入高温粉磨设备的热风温度保持80~600℃;粉磨干粉颗粒目数≤50目;3)经干燥后干粉储存于微负压干粉仓,通过称量装置和投料装置投料于回转窑;其中干粉加入量为生料重量的2-20%;4)干粉与生料在回转窑煅烧共同反应生成硅酸盐水泥熟料,经冷却、粉磨后制备成系列硅酸盐水泥、油井水泥、道路水泥或抗硫水泥。上述方法3)中投料于回转窑包括由回转窑窑头与喷煤管喷口相邻直接投料或与喷煤管窑外混合后投料、或于窑尾直接投料。本发明高温磨机可以采用风扫式磨机、气流磨或冲击磨,在热风对物料烘干的同时进行粉磨。钻井废弃物中的油基泥浆钻井岩屑、含油土壤均含有一定的水分,普通磨机无法完成原料的粉磨处理,通过引入热风,经干燥后通过机械或风力的作用,将原料磨细至入窑要求。本发明与现有技术相比,其优点在于:1、本发明利用水泥窑协同处理油基泥浆钻井岩屑、含油土壤,只需要对现有水泥生产线及其污染治理设施进行部分适应性改造,油基泥浆钻井岩屑、含油土壤可作为全替代料,废油类物质可作为部分燃料替代煤粉,能够减少吨产品的燃煤、硅质材料消耗,且不会新增污染物排放,能够将该类危险固体废弃物进行有效处理,实现危险固体废弃物处理的资源化、减量化、无害物的目的。2、油基泥浆钻井岩屑、含油土壤在高温粉磨时,磨机尾气引入回转窑。尾气中的有机物进入回转窑后燃烧,由于窑内最高温度在1500℃以上,且高温(>1000℃)维持时间超过4秒,这能充分分解油基泥浆钻井岩屑中的各类有机物,不会产生voc、二恶英等有害物质,燃烧形成h2o、co2、no2气体,no2在窑尾sncr工艺处理后形成n2气体,最终均以无害气体状态进入大气。3、岩屑、含油土壤在经干燥粉磨后,并不能完全脱除有机物,需要从高温入口进入水泥生产系统中,本发明特别通过窑头高温区进入,粉体进入回转窑的最高温度区域,有利于有机物完全分解,同时不影响水泥质量。4、该系统采用全封闭模式,并针对危险废物处理过程中可能产生的污染物进行处置,有效避免生产过程中产生的废气、废水废液、固废对环境造成二次污染。5、该方法处理量大,以一条5000吨/d的水泥生产线计算,生料用量约为7500吨,岩屑掺量以10%(水泥生料占比)计算,每天可处理750吨,每年处理量可达20万吨。6、油基泥浆钻井岩屑中主要的有机物为白油或精制柴油(2-10%)。该类有机物是经过特殊的深度精制后的矿物油,其基本组成为饱和烃结构,芳香烃、含氮、硫物质含量接近为零,燃烧值高达11000千卡/千克,是标煤的1.5倍,是一种优质燃料。有机物在高温气流烘干作用下气化,最终进入回转窑燃烧,可有作为燃料替代部分煤粉,降低水泥生产能耗。7、钻井岩屑、含油土壤的主要成分均为二氧化硅,与水泥生料中硅质材料的化学成分接近,可部分替代硅质原材料生产水泥熟料,达到降低水泥原材料用量的目的。8、岩屑进入回转窑中与生料发生固相反应生成硅酸盐水泥熟料,岩屑中的重金属固溶在熟料的各类矿物相晶格中取代ca、al、si等元素,而不再以简单的化合物形式存在,水泥水化形成的水泥石可完全稳定封固金属元素,达到无害处理的目的。9、岩屑中的重晶石是一种能耗的水泥生产矿化剂,能有效提高水泥熟料,特别是硅酸二钙的活性。10、油基泥浆岩屑经烘干、粉磨后,岩屑颗粒明显细化、分散良好,其粉体细度与水泥生料细度接近,可有效参与水泥熟料的固相反应,不会对水泥质量产生影响。11、油基泥浆钻井岩屑经储库、粉磨、干粉仓的均化过程后,能有效避免岩屑来源不同造成的成分波动。附图说明图1是本发明水泥窑协同处理工艺流程图;图2是本发明干粉原料从窑头进入回转窑装置结构示意图;图3是本发明干粉原料从喷煤管进入回转窑装置结构示意图;图4是本发明干粉原料从窑尾进入回转窑装置结构示意图;图5是岩屑xrd图谱;图6是岩屑dt-dsc分析图。图中,1是微负压储存库,2是钻井废弃物,3是上料机,4是密封输送管道,5是高温磨机,6是高温气流管道,7是负压风机,8是微负压干粉仓,9是二次风入口,10是篦冷机,11是废气管道,12是煤粉喷管,13是回转窑,14是风力粉体输送管,15是罗茨风机,16是称量装置,17是粉体供料机,18是干粉螺旋供料管,19是螺旋供料电机,20是煤风风机,21是煤粉供料管,22是三次风管,23是旋风预热器。具体实施方式下面结合具体实施方式对本发明进一步说明,具体实施方式是对本发明原理的进一步说明,不以任何方式限制本发明,与本发明相同或类似技术均没有超出本发明保护的范围。结合附图,以下各含量均为重量百分比含量,单位:%。实施例1本例油基泥浆岩屑取自四川某页岩气钻井经固液分离后的岩屑,化学成分、物相组成及热学性能检测结果见表1、图4和图5。其中表1具体说明了岩屑的化学成分组成及含量;图4是岩屑的xrd衍射图谱,检测结果表明,岩屑中主要含有石英、石灰石、白云石、重晶石、云母等矿物相。图5为岩屑tg-dsc检测结果,分析表明在200℃温度范围内的重量损失为2.49%,该部分重量损失大部分为水分挥发,在200-600℃范围的重量损失为8.81%,该部分重量损失为有机物分解,因此可知,岩屑中的水分含量较少,大部分烧失量是由白油挥发所致。表1油基泥浆钻井岩屑的化学成分组成及含量,单位:%;loisio2al2o3fe2o3caomgok2ona2oso3tio2clbao22.7038.869.653.628.872.202.040.854.310.441.195.01实施例2本例含油土壤取自长庆某开采平台附近的污染土壤,化学成分见表2,其成分同样是以氧化硅、氧化铝、氧化铁、氧化钙为主,且与钻井岩屑的成分接近。表2含油土壤的化学成分组成及含量,单位:%;烧失量caosio2al2o3fe2o3mgoso3k2ona2o21.609.8941.3610.808.332.010.251.200.87实施例3采用实施例1中的岩屑与水泥原材料进行配料,设计为普通硅酸盐水泥熟料的成分,在1450℃下进行煅烧30min,熟料中掺入5%的二水石膏粉磨成水泥,比表面积控制在342±10m2kg范围。具体配料方案、熟料化学成分及水泥性能见表3、表4和表5。表3配料方案表4熟料化学成分检测,单位:%;指标losssio2al2o3fe2o3caomgoso3f-caoirr2ocl-试样0.3122.843.585.1663.402.750.730.370.360.410.037标准≤3.0////≤5.0≤3.5/≤0.75≤0.75≤0.06表5水泥物理性能根据检测结果可知,采用岩屑制备的硅酸盐水泥熟料化学成分正常,f-cao含量低,loss、ir、r2o、cl-等指标均满足标准gb175-2017的硅酸盐水泥pi的相关要求,说明岩屑对水泥煅烧、质量无不良影响。根据表5水泥物理性能结果可知,水泥强度性能达到62.5的强度等级,凝结时间亦满足标准中的相关要求。实施例4采用实施例1中的岩屑与水泥原材料进行配料,用于生产g级油井水泥熟料。生料在1450℃下进行煅烧30min,熟料中掺入5%的二水石膏粉磨成水泥,比表面积控制在290±10m2kg范围。具体配料方案见表6,油井水泥物理性能检测结果见表7;表6配料方案,单位:%;表7水泥物理性能表7为掺入岩屑制备的油井水泥物理性能,从检测结果可知,水泥浆的游离液、稠化时间、抗压强度均满足gb/t10238-2015中关于g级高抗的相关指标要求。实施例5采用图2所示工艺方案处理实施例1中的油基泥浆钻井岩屑。首先将钻井废弃物2(本例为岩屑)存储在微负压储存库1内,微负压储存库1为全钢封闭结构,地面硬化防渗处理,设置负压风机7。岩屑从微负压储存库1经密封输送带4输送至高温磨机5,同时从水泥生产系统中的篦冷机10引入高温空气,气体入磨温度为350℃,粉磨时间20min。出磨岩屑粉体细度为0.08mm方孔筛筛余为5%;出磨尾气进入废气管道11。粉磨后的岩屑干粉通过输送机进入微负压干粉仓8,经供料器18进入供料机19,通过罗茨风机17和气力粉体输送管16进入窑尾。岩屑干粉的掺量为15%(生料内掺计算),替代硅质材料。实施例6采用图3所示工艺方案处理含油土壤。首先将钻井废弃物2(本例为含油土壤)存储在微负压储存库1内,从微负压储存库1经密封输送带4输送至高温磨机5,同时从水泥生产系统中的篦冷机10引入高温空气,气体入磨温度为200℃,粉磨时间20min。出磨岩屑粉体细度为0.08mm方孔筛筛余为8%;出磨尾气进入废气管道11。粉磨后的岩屑干粉通过输送机进入微负压干粉仓8,经供料器18进入供料机19,通过螺旋输送机21、岩屑干粉螺旋供料管20送入煤风风管,同煤粉一起进入喷煤管12。当前第1页12