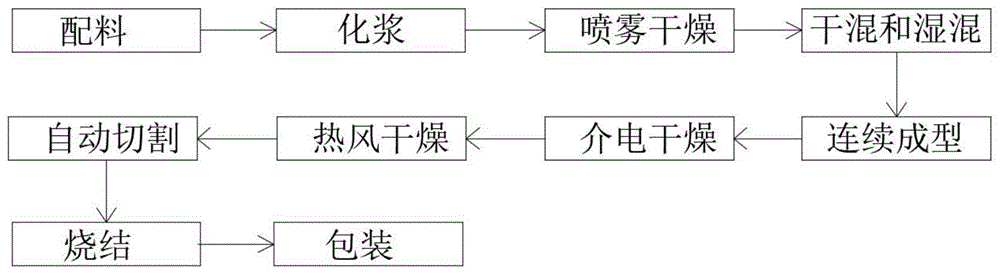
本发明属于蜂窝陶瓷载体
技术领域:
,涉及一种堇青石蜂窝陶瓷载体及其制备方法,具体涉及一种高孔密度(750-900cpsi)、超薄壁(2-2.5mil)堇青石质蜂窝陶瓷催化剂载体制备方法。
背景技术:
:众所周知,汽油机因化石燃料的燃烧会排放含碳氢、一氧化碳和氮氧化物(二氧化氮和一氧化氮)的废气,这些废气会造成大气污染。为实现汽油机的排气净化,需要在排气系统中安装基于堇青石蜂窝陶瓷催化剂载体的三效催化转化器(twc),且在污染物超低排放限值和油耗限值的双重制约下,要求蜂窝陶瓷催化剂载体必须具有更高的孔密度、更薄的格子壁厚,对于孔密度750-900cpsi、壁厚2-2.5mil的高孔密度超薄壁堇青石蜂窝陶瓷催化剂载体,获得高热冲击能力和高烧制成品率的核心控制指标为热膨胀系数。因此,蜂窝陶瓷厂商一直研究降低堇青石蜂窝陶瓷热膨胀系数工艺技术方法。如早在20世纪80年代美国专利us4280845中便提出通过选用片状粗晶滑石和增大滑石的粒度来减少蜂窝陶瓷制品的cte,其主要原理是当氧化镁原料,例如滑石的粒度较大且烧结前驱体批料的升温速率较快时,易发生液相烧结,形成的堇青石晶体较大且排列较好,具有较低的热膨胀系数,此专利中提出如果要获得较低的热膨胀系数,镁源的粒径(如滑石)最佳介于26μm-50μm,氧化铝的粒径最佳为0.5μm-3μm才能获得较佳的热膨胀系数。但是随着法规的升级,薄壁蜂窝陶瓷因为具有更大的比表面积能够涂覆更多的催化剂,提高转化效率,并且因为较薄的壁能够减少基材的质量从而实现冷启动而受到广泛关注。对于国六法规,受关注载体壁厚是2.5mil甚至2mil,为了生产超薄壁的蜂窝陶瓷,所使用原材料的粒径必须符合一定的要求,如果粒径较大那么堇青石前驱体批料,挤出成型时很容易出现产品的断筋,缺筋等缺陷,甚至无法形成连续的蜂窝状结构,同时粒径太大则难以挤出,无法成形。因此,采用细粒度的原材料生产薄壁的蜂窝陶瓷是一种趋势,但是由于滑石粒度降低产品的热膨胀系数会增加,蜂窝陶瓷的热冲击性能降低。同时,超薄壁蜂窝陶瓷的强度降低,抵抗热应力的能力下降,需要超薄壁蜂窝陶瓷热膨胀系数比厚壁蜂窝热膨胀系数更低才能满足高的抗热冲击性要求。为了得到热膨胀系数低的且壁薄的蜂窝陶瓷,国外的各大载体制造厂商在减少滑石粒径的同时极大的减少了铝源的粒径或者高岭土的粒径,如专利cn1379744a,cn101374786a,cn1329582a等,这些专利的共同之处是引入了一种比表面积达到180μm,纳米级的活性氧化物-勃姆石,从而大大降低了铝源的粒径使得滑石和铝源的粒度之比较大,从而使得制品有较低的cte,而且粒度极细的铝源有增加制品强度的功能,这更利于薄壁蜂窝陶瓷应用的。另外,当前技术中降低蜂窝陶瓷cte的另一种技术是引入较多的生高岭土,一般生高岭土的用量≥12质量%,如cn1329581a,这是因为有文献阐述,如专利us2008032091a1,高岭土的用量越高,制品中微裂纹的数量越多,而微裂纹在受热过程中的闭合会降低制品的cte。但是当前引入勃姆石(粒径≤0.5μm)降低铝源粒径从而获得较低cte和较高强度蜂窝陶瓷的技术大大增加了生产成本,因为粒度很细铝源的价格,如勃姆石,是粒径较粗铝源(粒径1-6μm)的3-5倍,因此这种薄壁蜂窝陶瓷性能的提高是以增加生产成本为代价的;而通过增加生高岭土用量引入微裂纹降低制品cte的方法,虽然不会增加原材料的成本,但是引入生料过多会降低制品烧结工序的合格率,另外引入较多生料导致产品产生较多微裂纹会降低产品的强度,这对于需要高强度的薄壁产品是不利的。技术实现要素:本发明的目的是提供一种三效催化转化器(twc)用高孔密度(750-900cpsi)、超薄壁(2-2.5mil)堇青石质蜂窝陶瓷催化剂载体制备方法,基于低热膨胀系数的设计,使蜂窝陶瓷催化剂载体具有高的抗热冲击能力和高的产品烧制合格率。本发明是通过以下技术方案实现的:一种twc用高孔密度超薄壁堇青石蜂窝陶瓷载体,所述载体的孔密度为750-900cpsi,壁厚为2-2.5mil,所述载体中堇青石晶相含量大于96%,按质量分数计,所述载体由以下组分制成:二氧化硅50.8%-52.0%,氧化铝34.2%-35.6%,氧化镁13.1%-14.3%。本发明还提供一种twc用高孔密度超薄壁堇青石蜂窝陶瓷载体的制备方法,包括如下步骤:(1)将无机料、有机分散剂与纯净水搅拌化成泥浆,然后使用喷雾干燥装置将无机粉体雾化干燥,形成流动性优异的粉料;(2)将粉料与有机粘结剂干混,然后加入润滑剂以及分散介质进行湿混使得混合物形成具有塑性的泥丸;(3)将步骤(2)所得泥丸进行挤出成型,形成生坯,将生坯进行介电干燥,热风烘干,切割,烧成,最终制成蜂窝陶瓷制品,所述无机料中包括针状生高岭土。进一步地,上述步骤(1)中,无机料中还包括滑石、煅烧高岭土、氧化铝、电熔石英。进一步地,所述针状生高岭土在无机料中质量含量1-26.5%,优选为2-16%,更优选为2-15.4%;其中,针状生高岭土的d50为1-20μm,优选为4-10μm,针状生高岭土的长径比≥8,优选为≥12,。进一步地,滑石在无机料中的质量含量为38-44%,优选为39-43%,更优选为39.26-42.25%;其中滑石的d50为3-30μm,优选为10-15μm;氧化铝在无机料中质量含量为13-28%,优选为15-27%,更优选为16.24-26.14%;其中氧化铝的d50为3-10μm,优选为4-7μm;二氧化硅在无机料中质量含量为6-14%,优选为8-13%;其中二氧化硅的d50为1-0μm,优选为4-8μm;煅烧高岭土在无机料中质量含量为0-32%,优选为2.7-30.0更优选为5.92-29.00,其中高岭土的d50为1-6μm,优选为2-5μm。进一步地,上述步骤(2)中,有机粘结剂为纤维素醚粘结剂、聚乙烯醇,优选为羟乙基纤维素、冷水速溶型聚乙烯醇、羟丙基纤维素醚中的1种或2种以上的组合;有机粘结剂的加入量为无机料质量的2-8%,优选为4-7%;润滑剂为硬脂酸酯类润滑剂,优选为硬脂酸乙醇酯,硬脂酸甘油酯硬脂酸丁醇酯中1种或2种以上的组合;润滑剂的加入量为无机料质量的1-5%,优选为2-4%。进一步地,步骤(2)中分散介质为纯净水,干混和湿混所用装置为高速浆叶式混料机。本发明还保护了twc用高孔密度超薄壁堇青石蜂窝陶瓷载体在汽油车三元催化剂载体中的应用。由以上的技术方案可知,本发明的有益效果是:1)该高岭土的长径比较大,大于8,粒径较粗,d50在1μm-20μm之间,该高岭土在塑性挤出成型过程中非常容易定向排列,滑石、氧化铝以针状生高岭土为模板,形成堇青石,利于堇青石晶体的定向生长和排列,可以降低制品的cte;2)针状生高岭土非常容易定向排列,不需要滑石定向排列,所可以使用滑石种类没有限制,可以是所有晶体形貌滑石,包括用结晶粒状滑石、结晶片状微晶滑石、结晶片状粗晶滑石;3)针状生高岭土比叠片状生高岭土的直径细,容易与滑石、氧化铝形成堇青石,因此不需要使用超细(d50≤1μm)氧化铝和纳米级氧化铝,与当前引入勃姆石的技术相比大大降低了生产的成本;4)针状生高岭土的定向排列,给制品生坯提供了高的生坯强度,高的生坯强度抵抗烧结过程中内外温差产生的内应力,提高烧成合格率。附图说明图1为twc用高孔密度超薄壁堇青石蜂窝陶瓷载体制备工艺流程图;图2为针状生高岭土形貌;图3为针状生高岭土用量与制品热膨胀系数图;图4为针状生高岭土用量与烧成合格率系数图;图5为本发明制品中堇青石定向排列图。具体实施方式下面将结合实施例对本发明的实施方案进行详细描述,但是本领域技术人员将会理解,下列实施例仅用于说明本发明,而不应视为限制本发明的范围。实施例中未注明具体条件者,按照常规条件或制造商建议的条件进行。所用试剂或仪器未注明生产厂商者,均为可以通过市售购买获得的常规产品。本发明的实施例及具体性能列于表2中,编号e1-e25,本发明的对比例及具体性能列于表3中,编号c1-c8。实施例和比较例的制备方法都是将无机料、有机分散剂与水搅拌化成泥浆,然后使用喷雾干燥将无机粉体雾化干燥,形成流动性好的粉料;将喷雾干燥好的粉料与其质量6%的有机粘结剂通过桨叶式高速混料机,干混均匀,然后加入无机料质量4%的润滑剂以及无机料质量24%的水进行湿混使得混合物形成具有一定塑性的泥丸,然后将这些泥丸在连续挤出机进行抽真空精炼、均化,挤出成型,形成生坯,所述生坯直径是4英寸,高度6英寸,壁厚2-2.5mil的产品,所述蜂窝陶瓷体的每平方英寸孔数是750-900,然后进行介电干燥,热风烘干,切割,烧成,最终制成蜂窝陶瓷制品。表1本实施例所用原料信息原料编号原料名称产地粒度(d50)形貌描述t1粒状滑石中国莱州10.0μm结晶为粒状t2微晶滑石美国12.8μm结晶为片状微晶t3微晶滑石澳大利亚11.6μm结晶为片状微晶t4粗晶滑石加拿大14.8μm结晶为片状粗晶t5粗晶滑石芬兰15.0μm结晶为片状粗晶k1针状生高岭土中国苏州4.5μm长径比约20k2针状生高岭土中国叙永7.6μm长径比约50k3针状生高岭土新西兰9.8μm长径比约200k4片状生高岭土美国乔治亚州5.8μm叠片状kc1煅烧高岭土中国茂名4.5μm叠片状kc2煅烧高岭土美国乔治亚州3.6μm叠片状a1氧化铝中国铝业5.5μm-a2氧化铝法国铝业5.0μm-fs电熔石英中国连云港5.0μm不定型bm勃姆石美国0.18μm纳米级表2实施例所用成分表及性能表表3对比例所用成分表及性能表从表3的对比利中可以看出,随着针状生高岭土用量增加,热膨胀系数随之降低,即使使用不同产地、不同长径比的针状高岭土,不同产地、不同种类、不同粒径的滑石、不同产地、不同粒径的煅烧高岭土、不同产地、不同粒径氧化铝,都得到非常低的热膨胀系数。只要针状生高岭土加入量≥2%,热膨胀系数能降低到≤3.0×10-7/℃(室温-800℃),当针状生高岭土加入量达到15.4%时,热膨胀系数能最低降低到≤1.6×10-7/℃(室温-800℃),与对比例c1、c2相比较,针状生高岭土非常显著降低产品的热膨胀系数,同时,提高了制品抗热冲击温度。本发明的所有实施例中的制品抗热冲击温度达到≥1000℃。从图4中可以看出,随着针状生高岭土用量增加,烧成合格率略微降低,但针状生高岭土用量≤9%时,烧成合格率都是100%,即使加入量达到15.4%,烧成合格率还是达到99%。e3(针状生高岭土用量10%,烧成合格率99.9%)与对比c1(生高岭土用量10%,烧成合格率97.5%)比较,可以看出,针状生高岭土显著提高烧成合格率。以上所描述的实施例是本发明一部分实施例,而不是全部的实施例。本发明的实施例的详细描述并非旨在限制要求保护的本发明的范围,而是仅仅表示本发明的选定实施例。基于本发明中的实施例,本领域普通技术人员在没有作出创造性劳动前提下所获得的所有其他实施例,都属于本发明保护的范围。当前第1页12