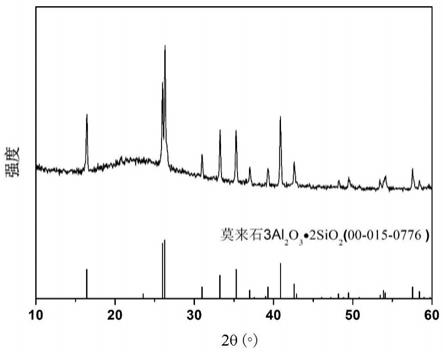
[0001]
本发明属于材料领域,具体涉及一种高强高韧莫来石陶瓷薄板及其制备方法。
背景技术:[0002]
陶瓷薄板是由粘土和其他无机非金属材料经成型、高温烧成等工艺制备而成的板状陶瓷制品。陶瓷薄板的原料通常包含粘土、石英、长石等矿物,坯体经过高温烧成后形成以玻璃相、石英和莫来石为主要组成的致密体。其中,晶体含量对陶瓷板的强度有重要影响。莫来石的来源主要有从粘土的分级产物偏高岭石中生成的颗粒或鳞片状的一次莫来石、以及从熔体中析出的少量针状二次莫来石。其中,针状莫来石能够相互交织形成网络结构,起类似晶须补强玻璃的作用,有利于改善晶体与玻璃体的结合状态,从而提高陶瓷板的强度。游离石英的来源主要是原料中的石英。传统的陶瓷板中石英含量较高,莫来石含量较低,而且主要是一次莫来石,即使通过添加煅烧铝矾土或莫来石纤维,都难以大幅度提高陶瓷板的强度和韧性。
[0003]
莫来石是以3al2o3·
2sio2结晶相为主要成分的耐火原料,具有良好的高温力学、高温热学性能。莫来石在自然界中的储量很少,但是用于人工合成莫来石的原料较为普通而且在自然界的种类有很多种。莫来石的合成方法可以分为固相合成反应和溶胶凝胶法、液态工艺(例如水热法)和气相合成工艺。按常用的固相和液相合成工艺来分,可以将合成的莫来石分为烧结莫来石和熔融莫来石。利用莫来石制备的高温结构材料大多数用于制作高温炉的前膛以及各种窑炉的内衬,此外还可应用于电子封装材料、光学材料和与其他材料通过复合制备出性能更好的复合材料。莫来石原料在建筑陶瓷上的应用主要是以莫来石晶须(纤维)的形式少量加入到坯体中以到达一定的增强作用,但是莫来石晶须的引入不会大幅度减少陶瓷中石英的含量,这使得目前的制备工艺不能从根本上解决游离石英带来的微裂纹问题,从而无法克服陶瓷薄板在生产和加工的过程中产生的破损。
技术实现要素:[0004]
为克服上述缺点和不足,本发明的目的在于提供一种高强高韧莫来石陶瓷薄板及其制备方法,极大程度提高陶瓷薄板中莫来石相的含量,能够解决游离石英带来的微裂纹,从而避免或最小化陶瓷薄板在搬运、切割、铺贴过程中的破损,拓宽产品的应用领域。
[0005]
第一方面,本发明提供一种高强高韧莫来石陶瓷薄板。所述陶瓷薄板的原料组成包括莫来石粉55~70重量份、低温熔块15~30重量份和粘土10~20重量份。现有的高强陶瓷薄板配方使用的原料含有大量石英,烧成后晶相以石英为主。而本发明的陶瓷薄板配方体系明显区别于常规的陶瓷薄板,其原料不含石英,烧成后晶相以莫来石为主,在增强陶瓷薄板强度的基础上,可以避免游离石英相变引起的微裂纹缺陷。
[0006]
较佳地,所述陶瓷薄板的物相组成包括:以质量百分比计,莫来石相50~65%和非晶玻璃相35~50%。现有常规陶瓷薄板的物相组成包含非晶相、石英、莫来石等,而且该莫来石相多数是由高岭土等黏土和长石在烧成过程中生成的一次莫来石。更重要的是,由于
该莫来石是由黏土和长石在反应过程中产生,所以陶瓷板烧成后的物相组成中莫来石相的含量在极大程度上受到限制,例如通常仅在20wt%以下。本发明通过在陶瓷薄板的原料组成中引入大量的莫来石粉,借助该莫来石粉和低温熔块的配合作用,即可形成以莫来石为单一晶相或者主晶相的物相组成。
[0007]
本发明所述陶瓷薄板的莫来石相包括低温熔块在烧成过程中形成熔体使得部分莫来石粉熔融后作为二次莫来石相析出的针状莫来石、以及未被熔融的起到骨架和增强作用的莫来石粉。换句话说,熔块在烧成过程中形成熔体使得部分莫来石粉熔融后生成针状莫来石,而未被熔融的莫来石粉起到骨架和增强的作用,最后经高温烧成得到以单相莫来石或莫来石为主晶相的陶瓷薄板。
[0008]
较佳地,所述莫来石粉的al2o3含量≥40%,优选为40~70%。使用高al2o3含量的莫来石粉可以显著提高烧成后陶瓷薄板中莫来石晶相的含量。
[0009]
较佳地,所述低温熔块的烧成温度在1000℃以内。熔块的烧成温度介于熔块的始融温度和流动温度之间。通过控制低温熔块的烧成温度和使用量,能够使得低温熔块将部分莫来石粉熔融,并在陶瓷板烧成温度下形成致密的陶瓷坯体。
[0010]
较佳地,所述陶瓷薄板的断裂模数为100~150mpa。
[0011]
较佳地,所述陶瓷薄板的规格是长1200~2400mm
×
宽600~1200mm
×
厚度2~5mm。
[0012]
第二方面,本发明提供上述任一项所述的高强高韧莫来石陶瓷薄板的制备方法。所述制备方法包括以下步骤:按照陶瓷薄板的原料组成称量原料后,将原料湿法球磨以形成浆料;然后将浆料造粒并成型制得坯体;将坯体烧成获得高强高韧莫来石陶瓷薄板。
[0013]
较佳地,所述陶瓷薄板的最高烧成温度为1180~1250℃,烧成周期为40~90分钟。
附图说明
[0014]
图1是本发明实施例1的莫来石陶瓷薄板的xrd图;图2是本发明实施例1的莫来石陶瓷薄板的sem图;图3是本发明对比例1的陶瓷薄板的xrd图。
具体实施方式
[0015]
通过下述实施方式进一步说明本发明,应理解,下述实施方式仅用于说明本发明,而非限制本发明。在没有特殊说明的情况下,各百分含量指质量百分含量。
[0016]
以下示例性说明所述高强高韧莫来石陶瓷薄板的制备方法。
[0017]
按照陶瓷薄板的原料组成称料。作为示例,所述陶瓷薄板的原料组成包括莫来石粉55~70重量份、熔块15~30重量份和粘土10~20重量份。
[0018]
目前市场上的莫来石粉根据铝的含量可分为m45、m60、m70。例如m45的al2o3含量通常为40~45wt%。作为示例,莫来石粉的化学组成可包括:以质量百分比计,sio225~55%,al2o
3 40~73%。
[0019]
本发明直接以莫来石粉为原料,相对于现有技术中以高岭土或铝矾土等原料生成莫来石相,不仅可以省略石英原料的使用,而且有利于大幅度提高陶瓷产品中莫来石晶体含量。
[0020]
上述莫来石粉的粒径可为100目以上。
[0021]
本发明上述陶瓷薄板的原料组成中除了含有大量的莫来石粉以外,还包括低温熔块。所述熔块的烧成温度在1000℃以内。在相同化学组成的条件下熔块的烧成温度比生料釉低,始熔温度更低,烧成温度范围更宽。通过引入低温熔块不仅可以降低烧成温度、扩大烧成范围、减少针孔缺陷,而且使用低温熔块才能实现较少量的熔块对大量莫来石粉的部分熔融,大幅度提高陶瓷薄板中莫来石晶相的含量,实现在陶瓷砖烧成温度内制备出致密的陶瓷薄板。
[0022]
一些实施方式中,所述低温熔块占陶瓷薄板原料的质量百分比为15~30%。在现有使用高岭土和长石形成莫来石的技术方案中,通常熔块仅作为低温熔剂,含量约为3~5%左右。本发明和上述技术方案在低温熔块含量上的差异,再次说明本发明“借助莫来石粉和低温熔块的配合,形成高含量莫来石晶相”的创新性。
[0023]
作为示例,所述熔块的化学组成包括:以质量百分比计,sio
2 55~65%,al2o
3 6~15%,r2o 5~20%,ro 6~25%,b2o
3 0~15%。其中,r2o指的是碱金属氧化物,ro指的是碱土金属氧化物。
[0024]
上述黏土的种类不受限制。粘土的主要作用是提供si、al成分,且利于坯体成型。
[0025]
所述陶瓷薄板的原料组成还可以包括低于10重量份的长石。同样,长石的种类也不受限制。钾长石或者钠长石均可以适用于本发明。少量长石的加入有利于烧成。
[0026]
本发明的创新点是利用莫来石粉和低温熔块,在现有陶瓷砖烧成制度下得到以单相莫来石晶体的陶瓷薄板,具有高强度高韧性的特征。不仅如此,现有陶瓷板中的莫来石相多数从粘土的分级产物偏高岭石中生成颗粒或鳞片状的一次莫来石,或者少量从富铝的长石熔体中析出针状的二次莫来石,整体的莫来石含量较低。本发明通过直接加入莫来石粉大幅度提高莫来石相的含量,并通过对部分莫来石的熔融析出大量二次莫来石。
[0027]
将陶瓷薄板的原料湿法球磨以形成浆料。例如,向55~70重量份莫来石粉、15~30重量份低温熔块,10~20重量份粘土和0~10重量份长石中加入35重量份水进行湿法球磨。球磨过程中,物料:研磨球:水的质量比可为1:2:0.35,球磨转速为20~30转/分钟,球磨时间为15~20小时。球磨完成后,将获得的浆料过筛,250目筛余≤1wt%。上述浆料的比重为1.68~1.70。将过筛后的浆料干燥,经造粒采用压机成型。
[0028]
将坯体干燥。所述干燥温度可为110~140℃,干燥时间可为120~180min,干燥后坯体水分控制在1wt%以内。
[0029]
最后,将坯体烧成以获得高强高韧莫来石陶瓷薄板。所述陶瓷薄板的最高烧成温度为1180~1250℃,烧成周期为40~90分钟。
[0030]
上述莫来石陶瓷薄板的制备过程中,熔块在烧成过程中形成熔体使得部分莫来石粉熔融后生成针状莫来石,而未被熔融的莫来石粉起到骨架和增强的作用,最后经高温烧成得到以单相莫来石或莫来石为主晶相的陶瓷薄板。
[0031]
参见图1可以看出,本发明陶瓷薄板的物相组成可包括:以质量百分比计,莫来石相50~65%和非晶玻璃相35~50%。
[0032]
参见图2可以看出,存在长度3μm以上的针状莫来石晶体。这是因为低温熔块在烧成过程中形成熔体使得部分莫来石粉熔融后生成针状莫来石。
[0033]
另外,未被熔融的莫来石粉起到骨架和增强的作用,最后经高温烧成得到以单相莫来石或莫来石为主晶相的陶瓷薄板。一些实施方式中,所述陶瓷薄板的断裂模数为100~
150mpa。
[0034]
本发明的莫来石陶瓷薄板配方合理,制备简单,有效地降低了材料的吸水率同时提高了材料的韧性和抗冲击性能,有优异的力学性能,而且提高了制备效率,降低了生产成本,具有很好的市场前景。
[0035]
还可以对所述陶瓷薄板进行后加工。该后加工包括但不限于包括施釉、印花、釉烧和切割抛光。
[0036]
实施例1(1)称取al2o3含量为70%的莫来石粉55重量份、熔块30重量份、粘土10重量份和长石5重量份,将其球磨混合制得浆料;(2)将浆料喷雾造粒后干压成型得到坯体;(3)将坯体高温烧成制得陶瓷薄板,最高烧成温度是1250℃,烧成周期是40min。
[0037]
实施例1制备的陶瓷薄板规格为长2400mm
×
宽1200mm
×
厚度3.5mm。按国家标准gb/t 23266-2009《陶瓷板》的试验方法,本实施例制得的莫来石陶瓷薄板的吸水率为0.10%,断裂模数为150mpa。
[0038]
实施例2(1)称取al2o3含量为40%的莫来石粉70重量份、熔块20重量份和粘土10重量份,将其球磨混合制得浆料;(2)将浆料喷雾造粒后干压成型得到坯体;(3)将坯体高温烧成制得陶瓷薄板,最高烧成温度是1180℃,烧成周期是90min。
[0039]
实施例2制备的陶瓷薄板规格为长1200mm
×
宽600mm
×
厚度2.5mm。按国家标准gb/t 23266-2009《陶瓷板》的试验方法,本实施例制得的莫来石陶瓷薄板的吸水率为0.05%,断裂模数为127mpa。
[0040]
实施例3(1)称取al2o3含量为60%的莫来石粉55重量份、熔块15重量份、粘土20重量份和长石10重量份,将其球磨混合制得浆料;(2)将浆料喷雾造粒后干压成型得到坯体;(3)将坯体高温烧成制得陶瓷薄板,最高烧成温度是1200℃,烧成周期是65min。
[0041]
实施例3制备的陶瓷薄板规格为长1800mm
×
宽900mm
×
厚度3mm。按国家标准gb/t 23266-2009《陶瓷板》的试验方法,本实施例制得的莫来石陶瓷薄板的吸水率为0.08%,断裂模数为142mpa。
[0042]
对比例1(1)称取泥料22重量份、白砂32重量份、钾钠石粉46重量份,将其球磨混合制得浆料;(2)将浆料喷雾造粒后干压成型得到坯体;(3)将坯体高温烧成制得陶瓷薄板,最高烧成温度是1250℃,烧成周期是40min。
[0043]
该对比例制备的陶瓷薄板的规格与实施例1基本相同。参见图3可以看出,所述陶瓷薄板的烧成后物相组成包括:以质量百分比计,非晶相59%、石英27%、莫来石相12%,其他2%。按国家标准gb/t 23266-2009《陶瓷板》的试验方法,本对比例制得的陶瓷薄板的断裂模数是59mpa。
[0044]
上述实施例为本发明较佳的实施方式,但本发明的实施方式并不受上述实施例的
限制,其他的任何未背离本发明的精神实质与原理下所作的改变、修饰、替代、组合、简化,均应为等效的置换方式,都包含在本发明的保护范围之内。