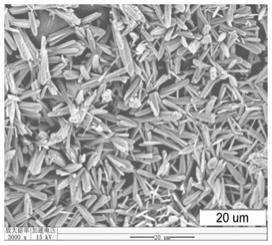
1.本申请涉及但不限于新型建筑材料技术领域,尤其涉及但不限于石膏基建筑材料,具体地涉及但不限于一种天然硬石膏基胶凝材料及其制备方法。
背景技术:2.无机胶凝材料按硬化条件可分为水硬性胶凝材料和气硬性胶凝材料两类。所谓气硬性胶凝材料,是指只能在空气中硬化并保持或继续提高其强度的胶凝材料,如石灰、石膏、水玻璃等。所谓水硬性胶凝材料,指不仅能在空气中,而且能更好地在水中硬化,保持并继续发展其强度,如各种水泥。气硬性胶凝材料一般只适合用于地上或干燥环境,不宜用于潮湿环境,更不可用于水中。水硬性胶凝材料是指不仅能在空气中硬化,而且能更好地在水中硬化并保持或继续提高其强度的胶凝材料,如水泥。水硬性胶凝材料既适用于地上,也适用于地下或水中。
3.我国天然硬石膏矿产资源丰富,储量居世界首位。目前,大多数天然硬石膏矿床未开发,仅有少数天然硬石膏矿床如南京、邵东、太原、兴宁、重庆等矿床被开采。一般而言,石膏是一种气硬性胶凝材料,其耐水性能差,水化速率较慢、凝结时间较长、胶凝性能较差,极大限制了石膏基材料的应用。
技术实现要素:4.以下是对本文详细描述的概述。本概述并非是为了限制权利要求的保护范围。
5.为了有效扩大天然硬石膏的使用范围,本申请提出了一种新型的天然硬石膏基胶凝材料体系,为天然硬石膏资源化利用提供了新的途径。
6.具体地,本申请提供了一种天然硬石膏基胶凝材料,该天然硬石膏基胶凝材料的制备原料包括:天然硬石膏100重量份,氟石膏5
‑
80重量份,水泥3
‑
15重量份,粉煤灰0
‑
10重量份,硅灰0
‑
5重量份,以及硫铝酸盐0.5
‑
4重量份。
7.在本申请的实施方式中,天然硬石膏基胶凝材料的制备原料包括天然硬石膏100重量份,氟石膏20
‑
50重量份,水泥5
‑
15重量份,粉煤灰5
‑
8重量份,硅灰1
‑
4重量份,以及硫铝酸盐0.5
‑
3重量份。
8.在本申请的实施方式中,天然硬石膏和氟石膏的细度为80
‑
200目,粒度为74μm
‑
178μm。
9.在本申请的实施方式中,硫铝酸盐可以为kal(so4)2·
12h2o或硫酸铝。
10.在本申请的实施方式中,水泥可以为32.5#普通硅酸盐水泥或者42.5#普通硅酸盐水泥。
11.在本申请的实施方式中,粉煤灰可以为ⅱ级粉煤灰。
12.在本申请的实施方式中,硅灰的粒度可以为200
‑
1000目。
13.本申请还提供了一种上述天然硬石膏基胶凝材料的制备方法,所述制备方法包括:
14.(1)煅烧硫铝酸盐得到煅烧的硫铝酸盐;
15.(2)将天然硬石膏与氟石膏混合球磨后与煅烧的硫铝酸盐混合得到第一石膏混合物,将第一石膏混合物与水混合搅拌得到料浆,对料浆进行养护得到第二石膏混合物;
16.(3)将第二石膏混合物球磨、过筛、然后与水泥、可选的粉煤灰和可选的硅灰混合并煅烧、陈化得到所述天然硬石膏基胶凝材料。
17.在本申请的实施方式中,在步骤(1)中,煅烧是在150℃至500℃下进行并持续0.5h
‑
3h。
18.在本申请的实施方式中,在步骤(2)中,第一膏混合物质量:水的质量为大于等于1;
19.任选地,在步骤(2)中,
20.氟石膏与天然硬石膏混合前先在10℃至30℃的温度和20
‑
90%的湿度的条件下陈化1天至3年;所述氟石膏陈化优选为1年至3年;氟石膏本身是无水石膏,陈化过程能够使无水石膏转化为二水石膏或半水石膏,陈化时间越长,二水石膏越多。使用陈化1年至3年的氟石膏与天然硬石膏混合水化能够有利地加促天然硬石膏的水化过程。
21.天然硬石膏与氟石膏的细度为80
‑
200目,粒度为74μm
‑
178μm;
22.养护是在温度15℃至25℃,湿度rh60
‑
90%的恒温恒湿条件下进行1
‑
7天。
23.在步骤(3)中,过筛为过80
‑
200目筛;任选地,煅烧为在鼓风干燥箱中于150℃至200℃下进行1h
‑
2h。
24.本申请的天然硬石膏基胶凝材料的制备方法选择掺入氟石膏,使天然硬石膏、氟石膏和硫铝酸盐激发剂先经过水化养护,三组分相互作用形成水化的石膏混合物,再煅烧该水化的石膏混合物并与水泥等其他组分混合球磨,使其活化性能得到充分提高,从而大大提高了天然硬石膏基胶凝材料的强度、保温性和耐水性。而使用单一的天然硬石膏作为石膏原料而不掺入氟石膏,或将各类激发剂、天然硬石膏、氟石膏直接混合球磨不经过水化养护和煅烧过程,则都不能使其活化性能得到充分提高。故使用本申请的方法得到的天然硬石膏基胶凝材料的性能更好。因此,本申请所得的胶凝材料的强度更高、保温隔热性和耐水性都更好,具有更加优异的胶凝性能。
25.本申请实施方式提供的天然硬石膏基胶凝材料与现有的石膏基胶凝材料相比具有以下优点:
26.(1)保温隔热效果更好;
27.(2)耐水性能好;
28.(3)绿色环保无污染;
29.(4)高强度,对室内空气湿度有微调作用,有良好的呼吸性能。
30.本申请的天然硬石膏基胶凝材料由于具有优异的耐水性和保温性,有广泛的应用,比如可以用作地板材料、自流平材料等。
31.本申请的其它特征和优点将在随后的说明书中阐述,并且,部分地从说明书中变得显而易见,或者通过实施本申请而了解。本申请的目的和其他优点可通过在说明书、权利要求书以及附图中所特别指出的结构来实现和获得。
附图说明
32.附图用来提供对本申请技术方案的进一步理解,并且构成说明书的一部分,与本申请的实施例一起用于解释本申请的技术方案,并不构成对本申请技术方案的限制。
33.图1是实施例1的天然硬石膏基胶凝材料水化产物的高倍(3000
×
)扫描电镜图。
34.图2是天然硬石膏100重量份和陈化1年的氟石膏25重量份混合加水充分水化3年的水化产物的高倍(2000
×
)扫描电镜图。
35.图3是天然硬石膏水化8年的水化产物的高倍(2000
×
)扫描电镜图。
36.图4是陈化1年的氟石膏加水充分水化3年的水化产物的高倍(2000
×
)扫描电镜图。
具体实施方式
37.为使本申请的目的、技术方案和优点更加清楚明白,下文中将结合附图对本申请的实施例进行详细说明。需要说明的是,在不冲突的情况下,本申请中的实施例及实施例中的特征可以相互任意组合。
38.天然硬石膏购自皖北煤电集团含山恒泰非金属材料分公司;氟石膏购自河南三门峡,主要成分为无水硫酸钙,ph值为8.5;十二水硫铝酸钾购自国药集团化学试剂有限公司;水泥为钻牌32.5#早早强复合硅酸盐水泥;粉煤灰购自白山市热电厂,ii级;硅灰购自埃肯中国公司,200
‑
1000目。
39.实施例1
40.一种天然硬石膏基胶凝材料的制备方法,包括:
41.步骤1:称量2.22重量份十二水硫铝酸钾置于马弗炉300℃煅烧1h,取出置于干燥器中,冷却,得到煅烧的硫铝酸钾作为激发剂;
42.步骤2:称取25重量份的陈化1年的氟石膏,球磨过200目筛,粒度为178μm,得到氟石膏原料粉;陈化1年的氟石膏是二水硫酸钙和半水硫酸钙混合物,其中二水硫酸钙达到20.1%;
43.步骤3:称取100重量份的天然硬石膏,与氟石膏原料粉混合、球磨30min;然后与煅烧的硫铝酸钾混合均匀,得到第一石膏混合物;
44.步骤4:将第一石膏混合物与充足拌合水(第一石膏混合物:拌合水质量质量=1)搅拌均匀得到料浆;
45.步骤5:将上述料浆置于恒温恒湿箱(温度15℃至25℃,湿度rh60
‑
90%)养护3天得到第二石膏混合物,然后置于45℃鼓风干燥箱烘干,磨至粉末颗粒可以过80目筛得到第二石膏混合物粉末;
46.步骤6:将第二石膏混合物粉末与普通硅酸盐水泥5重量份、粉煤灰5重量份、硅灰2重量份充分混合均匀,球磨20min,然后置于鼓风干燥箱在150℃至200℃下煅烧1h
‑
2h,冷却至室温,陈化后得到天然硬石膏基胶凝材料。
47.实施例2
48.一种天然硬石膏基胶凝材料的制备方法,与实施例1的区别在于步骤2中,陈化1年的氟石膏的掺量为15重量份。
49.实施例3
50.一种天然硬石膏基胶凝材料的制备方法,与实施例1的区别在于步骤2中,氟石膏原料为陈化半年的氟石膏,掺量为15重量份。陈化半年的氟石膏是二水硫酸钙和半水硫酸钙混合物,其中二水硫酸钙达到13.6%。
51.实施例4
52.一种天然硬石膏基胶凝材料的制备方法,与实施例1的区别在于不加硅灰,即,步骤6为:将第二石膏混合物粉末与普通硅酸盐水泥5重量份、粉煤灰5重量份充分混合均匀,球磨20min,然后置于鼓风干燥箱在150℃至200℃下煅烧1h
‑
2h,冷却至室温,陈化后得到天然硬石膏基胶凝材料。
53.实施例5
54.一种天然硬石膏基胶凝材料的制备方法,与实施例1的区别在于不加粉煤灰,即,步骤6为:将第二石膏混合物粉末与普通硅酸盐水泥5重量份、硅灰2重量份充分混合均匀,球磨20min,然后置于鼓风干燥箱在150℃至200℃下煅烧1h
‑
2h,冷却至室温,陈化后得到天然硬石膏基胶凝材料。
55.对比例1
56.一种天然硬石膏基胶凝材料的制备方法,与实施例1的区别在于不加氟石膏,即,步骤1后直接执行步骤3
‑
6,其中步骤3为:称取100重量份的天然硬石膏,球磨30min;然后与煅烧的硫铝酸钾混合均匀,得到第一石膏混合物。
57.对比例2
58.32.5#普通硅酸盐水泥。
59.对比例3
60.普通建筑石膏。
61.性能测试
62.试件成型及强度测定
63.按照抗折强度和抗压强度根据标准gb/t 17669.3
‑
1999《建筑石膏力学性能的测定》的规定,测试养护至3d和28d的实施例1
‑
5和对比例1的胶凝材料以及对比例3的抗折抗压强度。按照《硅酸盐水泥、普通硅酸盐水泥》(gb175—1999)和(gb/t17671—1999)《水泥胶砂强度检验方法(iso法)》的规定,测试养护至3d和28d的32.5#普通硅酸盐水泥抗折抗压强度。
64.保温隔热效果
65.将实施例1
‑
5和对比例1的胶凝材料与适量(标准稠度用水量)拌合水混合搅拌均匀后,制成10cm*10cm*9.5cm的板材;将未处理的硬石膏(标准稠度用水量)拌合水混合搅拌均匀后,制成10cm*10cm*9.5cm的板材;将普通建筑石膏与适量(标准稠度用水量)拌合水混合搅拌均匀后,制成10cm*10cm*9.5cm的板材;将32.5#水泥加入适量(标准稠度用水量)拌合水制成10cm*10cm*9.5cm的板材;分别测试其导热系数。测试仪器为湘科
tm drpl
‑
i导热系数测试仪,由湘潭市仪器仪表有限公司制造。
66.凝结性能
67.根据标准gb/t 17669.4
‑
1999《建筑石膏净浆物理性能的测定》对实施例1
‑
5、对比例1和3的材料进行测试,根据标准gb 1346
‑
2011
‑
t《水泥标准稠度用水量、凝结时间、安定性检测方法》对对比例2的32.5#普通硅酸盐水泥进行测试。
68.耐水性能
69.根据《石膏基建材与应用》(王祁青编著,化学工业出版社)这本书中的第一章第四节中的第六小节对实施例1
‑
5、对比例1
‑
3的材料进行测试。
70.上述测定结果如下表1所示:
71.表1材料性能测试结果
[0072][0073]
从表1数据可以看出,实施例所得的胶凝材料的初凝时间与对比例2相当,终凝时间相比对比例2明显缩短了,但是初凝和终凝时间都比对比例1的凝结时间要缩短很多,符合胶凝材料施工性能的时间要求。实施例中的3d(即,3天)和28d(即,28天)的抗折、抗压强度比对比例2要稍大,这说明本发明所得的复合胶凝材料力学性能良好。
[0074]
实施例2和实施例3的数据表明使用陈化一年的氟石膏(其中二水硫酸钙达到20.1%)得到的天然硬石膏基胶凝材料的力学性能优于使用陈化半年的氟石膏(其中二水硫酸钙达到13.6%)得到的天然硬石膏基胶凝材料的力学性能。
[0075]
本申请实施例的胶凝材料力学强度优于32.5#普通硅酸盐水泥,并且实施例1的力学强度优于42.5#普通硅酸盐水泥(42.5#普通硅酸盐水泥28天后的抗压强度为42.5mpa),说明本申请实施例制备得到的天然硬石膏基胶凝材料强度更高。
[0076]
实施例1
‑
5所得天然硬石膏基胶凝材料的软化系数明显高于普通建筑石膏,表明本申请实施例的胶凝材料耐水性能相比普通建筑石膏材料的耐水性能有了大幅提高。并且,实施例1
‑
5的天然硬石膏基胶凝材料的保温性也明显高于32.5#普通硅酸盐水泥,实施例1
‑
3的天然硬石膏基胶凝材料的耐水性明显高于32.5#普通硅酸盐水泥。
[0077]
形貌检测
[0078]
为了说明掺入氟石膏对天然硬石膏水化过程的影响,对单一天然硬石膏水化产物、单一氟石膏水化产物、天然硬石膏和氟石膏混合水化产物以及本申请实施例1的天然硬石膏基胶凝材料水化产物分别进行形貌检测。其中,水化前,对各材料进行预处理使得各原料的粒度为178μm,过80目筛。
[0079]
图1显示晶体直径不同、长径比不同,相互交叉度高搭接好,在相互搭接的柱状晶粒之间填充着直径较小的细长晶粒。图2显示晶体呈柱状,长径比有大有小,晶体生长的方向不同,晶体相互交叉搭接。图3显示晶体呈密集的粒状,彼此难以交叉搭接。图4显示晶体呈柱状堆叠,彼此堆叠比较疏松,没有相互之间的交叉搭接。
[0080]
形貌检测结果表明,天然硬石膏中掺入氟石膏后的水化过程有利于形成晶体的相
互交叉和搭接,使天然硬石膏基胶凝材料的强度、保温性和耐水性都得到大大提高。
[0081]
虽然本申请所揭露的实施方式如上,但所述的内容仅为便于理解本申请而采用的实施方式,并非用以限定本申请。任何本申请所属领域内的技术人员,在不脱离本申请所揭露的精神和范围的前提下,可以在实施的形式及细节上进行任何的修改与变化,但本申请的专利保护范围,仍须以所附的权利要求书所界定的范围为准。