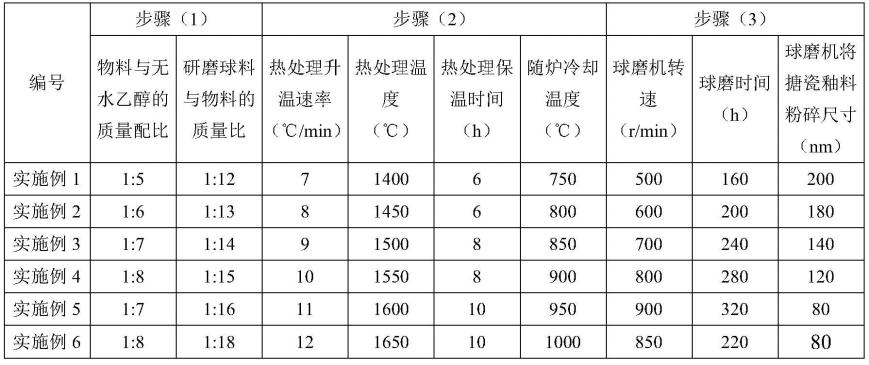
1.本发明涉及一种涂层用物料及涂层的制备方法,尤其涉及一种在钢表面制备耐蚀搪瓷涂层的物料及其制造方法。
背景技术:2.随着经济的迅速发展,市场对矿产品需求也随之大幅度增加,矿业开发规模也随之加大。伴随着矿业开发规模的迅速扩大,产生的选矿尾矿数量将不断增加。加之近年来许多可利用的金属矿品位日益降低,为了满足矿产品日益增长的需求,选矿规模越来越大,因此产生的选矿尾矿数量也开始增加。而大量堆存的尾矿,会给矿业、环境及经济等造成不少难题。
3.搪瓷是在金属表面上涂覆一层或多层瓷釉料,经高温烧制,金属基体与瓷釉发生物理、化学反应,在金属基体界面析晶而得到的一层致密的涂层。搪瓷可以兼备金属材料和陶瓷材料的优点,其具有类似于陶瓷的化学稳定性和金属的强度,对各种浓度的无机酸碱、盐、有机弱酸、有机溶剂都具有良好的抗侵蚀作用,而且安全无毒,易于洗涤、清洁,是生活与工业生产中重要防腐材料。
4.搪瓷釉料一般可以由基体剂、助熔剂、乳浊剂、密着剂、着色剂等构成。其中,基体剂占瓷釉总量的40~60%,其是决定搪瓷釉主要性能的成分,主要由氧化硅、氧化铝、氧化锆、氧化钛等。着色剂主要是赋予搪瓷釉以各种颜色,以达到彩饰效果的成分,这类氧化物的用量一般为0.1~2.5%。
5.我国每年产生的尾矿量在5亿吨以上,这其中大部分均是铁尾矿。铁尾矿的主要成分为sio2、cao、mgo、al2o3和fe2o3,这些组分是构成搪瓷的重要组分。基于此,本发明期望获得一种利用铁尾矿在高强钢表面制备耐蚀搪瓷涂层的物料及方法,其可以利用铁尾矿在高强钢表面制备耐蚀搪瓷涂层,实现对铁尾矿的有效利用,从而缓解环境污染问题,实现资源的再生利用,具有十分广阔的应用前景。
技术实现要素:6.本发明的目的之一在于提供一种利用铁尾矿在高强钢表面制备耐蚀搪瓷涂层的物料,该物料可以利用废弃物铁尾矿在高强钢表面制备耐蚀搪瓷涂层,实现对铁尾矿的有效利用,从而缓解环境污染问题,实现资源的再生利用,其具有十分广阔的应用前景。
7.为了实现上述目的,本发明提出了一种利用铁尾矿在高强钢表面制备耐蚀搪瓷涂层的物料,其各组分物质量百分含量为:
8.cao:11~13%;mgo:3~5%;al2o3:6~9%,coo:1~3%,tio2:5~10%,余量为铁尾矿。
9.在本发明上述的技术方案中,物料中铁尾矿的有效成分是sio2,其余各组分的设计原理如下所述:
10.本技术方案对搪瓷涂层成分的主晶相进行设计,旨在获得一种以透辉石为主晶相
的搪瓷涂层,基于此设计下述各组分及其含量:
11.cao:在本发明所述的物料中,添加适量的cao组分的主要是为了引入ca元素,其不仅可以与铁尾矿中的sio2协同配合在搪瓷内部形成网络状结构,还可以用于提高后续得到的耐蚀搪瓷涂层的硬度。基于此,在本发明所述的物料中,将cao组分的质量百分含量控制在11~13%之间。
12.mgo:在本发明所述的物料中,添加适量的mgo可以用于改善搪瓷内部微观结构,从而对内部空洞起到填充作用。基于此,在本发明所述的物料中,将mgo组分的质量百分含量控制在3~5%之间。
13.al2o3:在本发明所述的物料中,al2o3可以起到黏结作用,其可以使不同物料之间更好的熔融。基于此,在本发明所述的物料中,将al2o3组分的质量百分含量控制在6~9%之间。
14.coo:在本发明所述的物料中,coo能够作为着色剂,使搪瓷拥有良好的光泽和颜色,提高搪瓷的美学性能。基于此,在本发明所述的物料中,将coo组分的质量百分含量控制在1~3%之间。
15.tio2:在本发明所述的物料中,tio2与上述coo组分的作用相似,tio2同样具有改善搪瓷表面色泽,提高美学性能的作用,其可以使搪瓷拥有良好的光泽和颜色。基于此,在本发明所述的物料中,将tio2组分的质量百分含量控制在5~10%之间。
16.相应地,本发明的另一目的在于提供一种利用铁尾矿在高强钢表面制备耐蚀搪瓷涂层的方法,该方法生产简单,其可以采用废弃物铁尾矿作为主要原材料,通过引入少量石灰石、白云石和砂岩为校正原料,并配合添加适当外加剂,优化热处理制度及基础搪瓷组成,在高强钢表面有效制备物理、化学以及力学性能均优良的耐蚀搪瓷涂层。
17.为了实现上述目的,本发明提出了上述利用铁尾矿在高强钢表面制备耐蚀搪瓷涂层的方法,其包括步骤:
18.(1)采用研磨球料和无水乙醇对物料进行粉碎和混合,所述物料的各组分物质量百分含量为:cao:11~13%;mgo:3~5%;al2o3:6~9%,coo:1~3%,tio2:5~10%,余量为铁尾矿;
19.(2)将粉碎后的物料进行烘干,然后放入高温炉内进行热处理,得到的块状玻璃态物质,将块状玻璃态物质初步研磨成粉末状,得到搪瓷釉料;
20.(3)采用球磨机将搪瓷釉料粉碎至纳米级;
21.(4)将纳米级的搪瓷釉料与辅料调制成浆料;
22.(5)将所述浆料涂覆在经过预处理的高强钢板表面,并进行干燥;
23.(6)在高温炉中烧制一段时间,取出冷却,得到耐蚀搪瓷涂层。
24.在本发明的上述技术方案中,本发明所述的方法可以利用铁尾矿在高强钢表面制备耐蚀搪瓷涂层,实现对铁尾矿的有效利用,从而缓解环境污染问题,实现资源的再生利用。
25.在本发明所述的方法中,基于烧结法制备的纳米耐蚀搪瓷涂层,能够很好地附着于高强钢板表面形成一道有效的物理屏障。经实验测试发现,该耐蚀搪瓷涂层的耐氯离子和氢离子的腐蚀效果非常明显,能够大幅提升高强在服役过程中的耐腐蚀能力。此外,由于耐蚀搪瓷涂层自身硬度较大,与金属基体的结合性较好,相比于其他涂层也可以在更长的
时间里对高强钢板起到保护作用。
26.进一步地,在本发明所述的方法中,在步骤(1)中,所述物料与无水乙醇的质量配比为1:(5~10)。
27.在上述技术方案中,控制物料与无水乙醇的质量配比为1:(5~10),可以保证物料充分混合均匀,减少在研磨过程中产生的热量。
28.进一步地,在本发明所述的方法中,在步骤(1)中,所述研磨球料与所述物料的质量比为1:(12~18)。
29.在上述技术方案中,控制研磨球料与物料的质量比为1:(12~18),不仅能够有效提高研磨效率,以更短的时间达到所需的物料颗粒直径,其也能使得物料粒径更加均匀。
30.进一步地,在本发明所述的方法中,在步骤(2)中,所述热处理的工艺为:以7~12℃/min的速率升温至1400~1650℃,保温4~10h,再随炉冷却至750~1000℃,然后从炉内取出置于冷水中进行水淬。
31.在本发明所述的方法中,可以进一步地对步骤(2)中的热处理工艺进行优化,以保证上述各种原料能够得到充分熔融,提高搪瓷釉料的烧结成功率。
32.进一步地,在本发明所述的方法中,在步骤(3)中,采用球磨机将搪瓷釉料粉碎至80~200nm。
33.在上述技术方案中,可以优选的控制球磨机将搪瓷釉料粉碎至80~200nm,以保证所采用的搪瓷釉料粉末达到纳米级,使得搪瓷涂层内部结构更加致密。
34.进一步地,在本发明所述的方法中,在步骤(3)中,球磨机的转速为500~900r/min,并且/或者球磨时间为160~360h。
35.在本发明的上述技术方案中,控制球磨机的转速为500~900r/min,并且/或者球磨时间为160~360h,可以保证搪瓷釉料被球磨粉碎至纳米级
36.进一步地,在本发明所述的方法中,在步骤(4)中,所述辅料包括粘土、膨润土、硫酸镁。
37.进一步地,在本发明所述的方法中,在步骤(5)中,涂覆的厚度为0.6~0.8mm;并且/或者干燥温度为100~130℃。
38.在本发明的上述技术方案中,控制涂覆的厚度为0.6~0.8mm,可以保证纳米浆料能够均匀的平铺在金属基体表面。相应地,也可以优选的控制干燥温度为100~130℃,以使纳米浆料丧失流动性,较为紧密的贴合在金属基体表面。
39.进一步地,在本发明所述的方法中,在步骤(6)中,烧制温度为330~410℃,并且/或者烧制时间为10~25min。
40.在本发明上述技术方案中,控制轧制烧制温度为330~410℃,并且/或者烧制时间为10~25min,主要是为了保证搪瓷釉料得到充分的烧结而不至于产生过烧的现象。
41.进一步地,在本发明所述的方法中,在步骤(6)中,在烧制过程中,炉内温度以60~100℃/h的升温速度升温至烧制温度。
42.进一步地,在本发明所述的方法中,在步骤(6)中,所述高温炉内通有氮气,氮气体积占炉内总体积的50%~90%;在烧制前,所述高温炉内的温度被预热至180℃以上。
43.在上述技术方案中,为了保证高温炉内环境气氛稳定良好,排除烧结过程中所产生的不良气体对烧结过程本身的影响,在本发明所述的高温炉中,还可以有氮气,其体积可
以占炉内总体积的50%~90%。
44.本发明所述的利用铁尾矿在高强钢表面制备耐蚀搪瓷涂层的物料及方法相较于现有技术具有如下所述的优点以及有益效果:
45.本发明所述的利用铁尾矿在高强钢表面制备耐蚀搪瓷涂层的物料及方法可以利用铁尾矿在高强钢表面制备耐蚀搪瓷涂层,实现对铁尾矿的有效利用,从而缓解环境污染问题,实现资源的再生利用,其具有十分广阔的应用前景。
46.在某些优选的实施方式中,本发明可以利用铁尾矿作为主要原材料,引入少量石灰石、白云石和砂岩做为校正原料,并添加适当外加剂,通过优化热处理制度及基础搪瓷组成,从而在高强钢表面有效制备物理、化学以及力学性能均优良的耐蚀搪瓷涂层。
具体实施方式
47.下面将结合具体的实施例对本发明所述的利用铁尾矿在高强钢表面制备耐蚀搪瓷涂层的物料及方法做进一步的解释和说明,然而该解释和说明并不对本发明的技术方案构成不当限定。
48.实施例1-6
49.实施例1-6均采用以下步骤,利用铁尾矿在高强钢表面制备耐蚀搪瓷涂层:
50.(1)结合铁尾矿中sio2,cao,mgo,al2o3以及feo等所占比例,确定烧结搪瓷涂层的物料各组分物质量百分含量为:cao:11~13%;mgo:3~5%;al2o3:6~9%,coo:1~3%,tio2:5~10%,余量为铁尾矿。将上述物料置于行星球磨机,采用湿磨法,将物料与无水乙醇混合,并同时向研钵中加入研磨球料,对物料进行粉碎和混合。其中,物料与无水乙醇的质量配比为1:(5~10);研磨球料与所述物料的质量比为1:(12~18)。
51.(2)将粉碎后的物料进行烘干,除去多余水分,然后放入高温炉内进行热处理,控制热处理的工艺为:以7~12℃/min的速率升温至1400~1650℃,保温4~10h,再随炉冷却至750~1000℃,然后从炉内取出置于冷水中进行水淬,得到的块状玻璃态物质,将块状玻璃态物质初步研磨成粉末状,得到搪瓷釉料。
52.(3)打开行星球磨机,设置其转速为500~900r/min,球磨时间为160~360h,可以每隔8小时更换或补充一次无水乙醇和研磨球料,如此往复进行操作,直至将搪瓷釉料粉碎至纳米级,具体可以粉碎至80~200nm。
53.(4)将纳米级的搪瓷釉料与辅料调制成浆料,辅料可以包括粘土、膨润土、硫酸镁以及其他类似物。
54.(5)将浆料涂覆在经过预处理的高强钢板表面,敲击钢板背面使釉料自然流动平整,控制涂覆的厚度为0.6~0.8mm;涂覆完成后,在温度为100~130℃下进行干燥,完成干燥后转入高温炉中。需要说明的是,高强钢板的预处理步骤可以包括:对待涂高强钢板进行表面喷砂处理,以消除钢板表面多余杂质和氧化皮等,喷砂处理完毕后用砂轮机再对钢板表面进行打磨,控制砂轮机转速为:480~1200r/min,以保证钢板表面无任何残留物,直至待涂钢板显出亮银色效果;最后用无水乙醇+丙酮对待涂钢板表面进行清洗,烘干。
55.(6)在高温炉中烧制一段时间,在烧制过程中,炉内温度以60~100℃/h的升温速度升温至烧制温度,控制烧制温度为330~410℃,控制烧制时间为10~25min,烧制完成后取出冷却,得到耐蚀搪瓷涂层。其中,高温炉内通有氮气,氮气体积占炉内总体积的50%~
90%。为了实现更好的技术效果,在烧制前,高温炉内的温度可以被预热至180℃以上。
56.需要说明的是,在本发明中,本发明所述的实施例1-6均满足本发明设计规范要求。实施例1-6中均选取br1500hs作为高强钢板。
57.表1列出了实施例1-6中利用铁尾矿在高强钢表面制备耐蚀搪瓷涂层的物料的各组分物质量百分含量。
58.表1.(wt.%,余量为铁尾矿)
[0059] caomgoal2o3cootio2实施例111%3%6%1%5%实施例211%3%6%1%6%实施例312%4%7%2%7%实施例412%4%8%2%8%实施例513%5%9%3%9%实施例613%5%9%3%10%
[0060]
表2-1和表2-2列出了实施例1-6在上述工艺步骤中的具体工艺参数。
[0061]
表2-1.
[0062][0063]
表2-2.
[0064][0065]
将经过实施例1-6最终得到的具有耐蚀搪瓷涂层的成品钢板分别取样,并对各实施例成品钢板的耐蚀搪瓷涂层进行表面微观形态的观察和分析,而后进行测试试验,并将各实施例的测试试验结果分别列于表3中。
[0066]
相关试验测试手段为:控制试验条件为静止,以3.5wt.%nacl溶液作为腐蚀液,实验温度为25℃。电化学测试采用动电位极化曲线进行测试,测出1cm2面积大小的涂层试样的极化曲线,参比电极为饱和甘汞电极(sce),扫描区间为-0.35~-0.25v,扫描速率为1mv/s。
[0067]
通过上述试验操作可以求得各实施例的腐蚀电流密度和自腐蚀电位。
[0068]
表3列出了实施例1-6的成品钢板的测试试验结果和耐蚀搪瓷涂层的观察分析结果。
[0069]
表3.
[0070][0071]
从表3中可以看出,本发明实施例1-6中制备得到的耐蚀搪瓷涂层具有良好的耐蚀性,其中实施例3得到的耐蚀搪瓷涂层的自腐蚀电位最高,因此其耐蚀性最优,具有明显的耐海水腐蚀的倾向,其能够有效阻挡氯离子渗透进入金属基体表面,有效提高金属基板的耐蚀能力,并进一步延长其使用寿命。
[0072]
需要说明的是,本案中各技术特征的组合方式并不限本案权利要求中所记载的组合方式或是具体实施例所记载的组合方式,本案记载的所有技术特征可以以任何方式进行自由组合或结合,除非相互之间产生矛盾。
[0073]
还需要注意的是,以上所列举的实施例仅为本发明的具体实施例。显然本发明不局限于以上实施例,随之做出的类似变化或变形是本领域技术人员能从本发明公开的内容直接得出或者很容易便联想到的,均应属于本发明的保护范围。