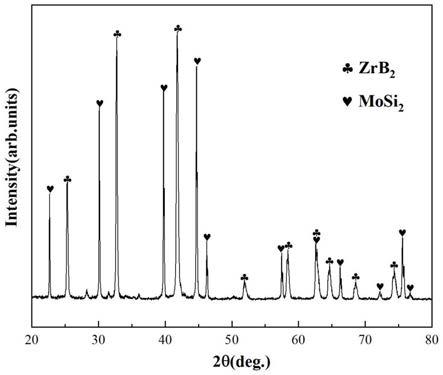
一种基于zrb2非平衡态合金化修饰的高阻氧涂层及制备方法
技术领域
1.本发明涉及一种高阻氧涂层及制备方法,尤其适用于碳材料技术领域使用的一种基于zrb2非平衡态合金化修饰的高阻氧涂层及制备方法。
背景技术:2.碳结构材料(c/c复合材料或石墨)因其密度低、比强度高、力学性能好、抗热震性好等优点,作为国防和民用领域不可缺少的结构材料,在航空航天高温构件中得到了广泛的应用。然而,400℃以上在空气中易氧化的特性严重制约了碳结构材料的应用。因此,涂层技术是提高碳结构材料高温性能的最佳选择。
3.近年来,zrb2的高熔点和化学稳定性使其在抗氧化涂层领域备受关注,然而,zrb2氧化产物b2o3的释放会导致涂层疏松多孔化,损耗涂层阻氧结构,生成气孔与裂纹等缺陷。目前,为了提升zrb2的抗氧化性能,由于mosi2较好的氧化抗性,国内外研究人员采用如包埋法,原位反应法,喷涂法,浆料法等涂层制备工艺制备了zrb2‑
mosi2涂层,通过mosi2氧化生成的玻璃膜对zrb2密封保护,可以显著降低其氧化损耗。
4.文献1“y.jiang,d.feng,h.q.ru,et.al.oxidation protective zrb2‑
mosi2‑
sic
‑
si coating for graphite materials prepared by slurry dipping and vapor silicon infiltration[j].surface&coatings technology,2018,339:91
‑
100”报道了采用浆料法和气相渗硅法在石墨基体表面制备了致密的单层zrb2‑
mosi2‑
sic
‑
si涂层。在1600℃空气中氧化150h后,涂层的失重率仅为0.21%,在室温至1200℃之间热冲击100个循环后,增重为0.11%。
[0005]
文献2“w.z.zhang,y.zeng,l.gbologah,et.al.preparation and oxidation property of zrb2‑
mosi2/sic coating on carbon/carbon composites[j].transactions of nonferrous metals societyofchina,2011,21:1538
‑
1544”报道了采用渗碳法制备sic内涂层,采用浆料喷涂法制备zrb2‑
mosi2外涂层。结果表明,在1000℃和1500℃氧化30h和10h后,zrb2‑
mosi2/sic涂层样品的质量损失分别为5.3%和3.0%。
[0006]
文献3“y.r.niu,h.y.wang,z.w.liu,et.al.microstructure evolution of zrb2‑
mosi2composite coatings atmiddle andhightemperatures[j].surface&coatings technology,2015,273:30
‑
38”报道了采用低压等离子喷涂技术制备了不同mosi2含量的zrb2基复合涂层。结果表明,zrb2‑
40vol.%mosi2涂层在1200℃氧化6h后的总氧化层厚度约为17
‑
22μm,在1500℃氧化6h后的总氧化层厚度约为264
‑
270μm。因此,zrb2相与mosi2相的复合,可以充分利用mosi2的成膜能力,与zrb2相的氧化产物过渡族金属氧化物和b2o3,融合生成复相玻璃层,降低氧气渗透率,提高zrb2相的抗氧化防护能力。
[0007]
然而,在目前的制备方法中,涂层的原料主要以机械混料为主,此方式导致涂层中物相难以混合均匀,极大影响涂层中zrb2相与mosi2相的分布均匀性。一旦氧气进入涂层内部,不均匀分布的mosi2很难在第一时间提供对zrb2的保护,从而弱化zrb2相对mosi2相的保护,极大影响涂层阻氧性能的深度提升。
技术实现要素:[0008]
为了克服上述现有技术的不足,本发明提供了一种基于zrb2非平衡态合金化修饰的高阻氧涂层制备方法,制备方法简单,通过自蔓延高温合成与sps热压烧结相结合的方式强化mosi2与zrb2的化学键连,克服传统机械混合方式的不均匀性,提高mosi2对zrb2的保护,增强涂层对碳基体的抗氧化能力。
[0009]
本发明所采用的技术方案是:本发明的基于zrb2非平衡态合金化前驱体,以质量分数:5
‑
30%锆,5
‑
30%钼,10
‑
60%硅,10
‑
60%硼混合原料并制成圆柱坯体,在燃烧合成反应釜内以自蔓延高温合成法制备获得具有合金化特性的非平衡态合金化前驱体zrb2‑
mosi2的混合体。
[0010]
一种使用基于zrb2非平衡态合金化前驱体的修饰高阻氧涂层制备方法,包括:将制备得到的非平衡态合金化前驱体zrb2‑
mosi2混合体进行破碎干燥,之后利用模具将非平衡态合金化前驱体包裹在需要制备高阻氧涂层的碳基体外侧,之后对碳基体进行放电等离子sps烧结,最终在碳基体表面上生成zrb2‑
mosi2高阻氧涂层。
[0011]
一种基于zrb2非平衡态合金化修饰的高阻氧涂层的制备方法,具体步骤如下:
[0012]
s1配料与混料:采用锆粉、硅粉、钼粉、硼粉为原料,按照质量分数:5
‑
30%锆,5
‑
30%钼,10
‑
60%硅,10
‑
60%硼称取原料粉末,利用球磨机混料,使粉体充分混合均匀;
[0013]
s2压制成型:将混合均匀的粉料干燥后倒入在钢制模具中,然后对钢制模具中的粉料加压,压力为20mpa
‑
200mpa,保压时间为5s
‑
60s的条件下,通过压片机将粉料冷压成型为圆柱坯体,作为燃烧合成所需的前驱体;
[0014]
s3合成非平衡态合金化前驱物:首先将压制好的圆柱坯体放入燃烧合成反应釜中,压坯的上柱头贴近钼制的电阻丝;然后向反应釜内填充ar气对圆柱坯中的混合分料进行惰性保护;通过电加热钼丝预热圆柱坯体,直至引发圆柱坯体的自蔓延反应为止;圆柱坯体开始燃烧合成反应后关闭电阻丝电源,等待反应完全并冷却,即可得到完全反应的非平衡态前驱体zrb2‑
mosi2的混合体;
[0015]
s4采用破碎机将得到的燃烧合成后的非平衡态前驱体破碎5min
‑
200min,随后放入烘箱进行干燥;
[0016]
s5对待添加高阻氧涂层的碳基体表面进行处理:使用400目的砂纸打磨碳基体直至表面平整,随后用酒精超声清洗,最后放入烘箱干燥;
[0017]
s6装模:在石墨模具内使用步骤(3)得到的非平衡态前驱物将步骤(5)处理后的碳基体进行全包裹,具体的,首先在石墨模具充填一层非平衡态前驱物,然后放入碳基体后再填充一层非平衡态前驱物即可实现碳基体被前驱体粉体均匀包裹;包裹层的厚度根据需要设置;
[0018]
s7进行放电等离子sps烧结:将石墨模具放入sps烧结炉中进行烧结处理,烧结温度为1200℃
‑
1900℃,升温速率为5℃/min
‑
200℃/min,压力为5mpa
‑
50 mpa,保温时间5
‑
min300min,最终实现在碳基体表面上制备zrb2‑
mosi2高阻氧涂层。
[0019]
进一步,所述的锆的粒度≤45μm,纯度≥99.9%,钼的粒度≤3μm,纯度≥99.95%,硅的粒度≤40μm,纯度≥99.9%,硼的粒度≤3μm,纯度≥95%。
[0020]
进一步,所述的碳基体为石墨或c/c复合材料。
[0021]
进一步,所述步骤s1中使用的锆的、钼、硅、硼的利用球磨机粉碎,球磨机转速为
50
‑
1000r/min,球磨时间为0.5
‑
10小时。
[0022]
进一步,上述步骤s6中,通过控制填充前驱体粉体的质量来控制基体四周所覆盖非平衡态前驱体粉体的厚度,约为碳基体厚度的0.1
‑
3倍。
[0023]
与现有技术相比,本发明的有益效果是:
[0024]
1)利用采用锆粉、硅粉、钼粉、硼粉一步合成具有化学键连的金属化前驱物mosi2‑
zrb2,克服传统机械混合所导致的涂层中相分布不均匀性的问题。
[0025]
2)mosi2‑
zrb2的合金化zrb2氧化会产生b2o3气体,在涂层内部的气体向外挥发时,mosi2生成的sio2玻璃膜具有密封惰化的作用,可以阻挡氧气的挥发,防止产生让外界氧气进入的气孔,从而实现保护效果;
[0026]
3)通过自蔓延高温合成的快速合成工艺实现合金化粉体的非平衡态化,可以提高涂层的致密性,减少氧气渗入对zrb2的氧化腐蚀。
[0027]
4)具有化学键连的mosi2‑
zrb2的合金化粉体,在sps热压烧结方式下,强化非平衡态合金化前驱物的化学键连,进一步增强mosi2对zrb2相的改性与保护效果,提高zrb2相的抗氧化防护能力。
[0028]
5)通过自蔓延高温合成非平衡态合金化前驱物与sps热压烧结相结合的方式,可以实现涂层在较低温度下的烧结,抑制晶粒异常长大对涂层性能的影响。
[0029]
6.本发明所用方法简单实用,可以显著提升zrb2‑
mosi2涂层的抗氧化性能,提升对碳基体的氧化防护,且涂层综合性能优异,具有广阔的发展前景。
附图说明
[0030]
图1为本发明实施例1制备的zm1非平衡态前驱体粉体的xrd图谱;
[0031]
图2为本发明实施例1制备的zm1非平衡态前驱体粉体的高分辨tem图;
[0032]
图3为本发明实施例1制备的碳基体表面zm1高阻氧涂层在1700℃氧化100min后的横截面sem照片;
[0033]
图4为本发明实施例2制备的zm2非平衡态前驱体粉体的xrd图谱;
[0034]
图5为本发明实施例2制备的zm2非平衡态前驱体粉体的高分辨tem图;
[0035]
图6为本发明实施例2制备的碳基体表面zm2高阻氧涂层在1700℃氧化100min后的横截面sem照片;
[0036]
图7为本发明实施例3制备的zm3非平衡态前驱体粉体的xrd图谱;
[0037]
图8为本发明实施例3制备的zm3非平衡态前驱体粉体的高分辨tem图;
[0038]
图9为本发明实施例3制备的碳基体表面zm3高阻氧涂层在1700℃氧化100min后的横截面sem照片;
[0039]
图中:1
‑
复相玻璃层,2
‑
未氧化涂层,3
‑
碳基体。
具体实施方式
[0040]
为了加深对本发明的理解,下面结合附图和实施例对本发明进一步说明:
[0041]
本发明公开的一种基于zrb2非平衡态合金化前驱体,以质量分数:5
‑
30%锆粉,5
‑
30%钼粉,10
‑
60%硅粉,10
‑
60%硼粉混合并制成圆柱坯体,在燃烧合成反应釜内以自蔓延高温合成法制备获得具有合金化特性的非平衡态合金化前驱体zrb2‑
mosi2的混合体。
[0042]
本发明的一种使用权利要求1所述基于zrb2非平衡态合金化前驱体的修饰高阻氧涂层制备方法:将制备得到的非平衡态合金化前驱体zrb2‑
mosi2混合体进行破碎干燥,之后利用模具将非平衡态合金化前驱体包裹在需要制备高阻氧涂层的碳基体外侧,之后对碳基体进行放电等离子sps烧结,最终在碳基体表面上生成zrb2‑
mosi2高阻氧涂层。
[0043]
一种基于zrb2非平衡态合金化修饰的高阻氧涂层的制备方法,其具体步骤如下:
[0044]
s1配料与混料:采用锆粉、硅粉、钼粉、硼粉为原料,按照质量分数:5
‑
30%锆,5
‑
30%钼,10
‑
60%硅,10
‑
60%硼称取原料粉末,利用球磨机混料,球磨机转速为50
‑
1000r/min,球磨时间为0.5
‑
10小时,最终使粉体充分混合均匀;
[0045]
s2压制成型:将混合均匀的粉料干燥后倒入在钢制模具中,然后对钢制模具中的粉料加压,压力为20mpa
‑
200mpa,保压时间为5s
‑
60s的条件下,通过压片机将粉料冷压成型为圆柱坯体,作为燃烧合成所需的前驱体;
[0046]
s3合成非平衡态合金化前驱物:首先将压制好的圆柱坯体放入燃烧合成反应釜中,压坯的上柱头贴近钼制的电阻丝;然后向反应釜内填充ar气对圆柱坯中的混合分料进行惰性保护;通过电加热钼丝预热圆柱坯体,直至引发圆柱坯体的自蔓延反应为止;圆柱坯体开始燃烧合成反应后关闭电阻丝电源,等待反应完全并冷却,即可得到完全反应的非平衡态前驱体zrb2‑
mosi2的混合体;
[0047]
s4采用破碎机将得到的燃烧合成后的非平衡态前驱体破碎5min
‑
200min,随后放入烘箱进行干燥;
[0048]
s5对待添加高阻氧涂层的碳基体表面进行处理:使用400目的砂纸打磨碳基体直至表面平整,随后用酒精超声清洗,最后放入烘箱干燥;
[0049]
s6装模:在石墨模具内使用步骤(3)得到的非平衡态前驱物将步骤(5)处理后的碳基体进行全包裹,具体的,首先在石墨模具充填一层非平衡态前驱物,然后放入碳基体后再填充一层非平衡态前驱物即可实现碳基体被前驱体粉体均匀包裹;通过控制填充前驱体粉体的质量来控制基体四周所覆盖非平衡态前驱体粉体的厚度,包裹层的厚度根据需要设置,最佳厚度约为碳基体厚度的0.1
‑
3倍;
[0050]
s7进行放电等离子sps烧结:将石墨模具放入sps烧结炉中进行烧结处理,烧结温度为1200℃
‑
1900℃,升温速率为5℃/min
‑
200℃/min,压力为5mpa
‑
50 mpa,保温时间5
‑
min300min,最终实现在碳基体表面上制备zrb2‑
mosi2高阻氧涂层。
[0051]
实施例1:
[0052]
通过自蔓延合成非平衡态前驱体粉体的xrd如图1所示,高分辨tem图如图2所示,高阻氧涂层在1700℃氧化100min后的横截面形貌如图3所示,。
[0053]
步骤(1):配料与混料:采用锆、硅、钼、硼粉为原料,其纯度≥99.0%,粒度≤50μm,按照质量分数16.1%锆,50.5%钼,3.8%硼和29.6%硅称取粉末,记作zm1,随后以300r/min的转速球磨5h使粉体充分混合均匀;
[0054]
步骤(2):压制成型:将混合均匀的粉料干燥后倒入在钢制模具中,采用压力约为200mpa,保压时间约为30s的条件下,通过压片机将其冷压成型为圆柱坯体,作为燃烧合成所需的前驱体;
[0055]
步骤(3):合成非平衡态合金化前驱物:首先将压制好的样品放入燃烧合成反应釜中,压坯的上柱头贴近钼制的电阻丝;其次,填充ar气对粉料进行惰性保护;再次,通过电加
热钼丝预热样品,直至其引发自蔓延反应为止。随后,燃烧合成开始反应后关闭电源,等待反应完全;最后,样品冷却后,将即可得到所设计的前驱物;
[0056]
步骤(4):将得到的燃烧合成的硬质样品放到破碎机中进行破碎15min,随后放入烘箱进行干燥;
[0057]
步骤(5):碳基体的表面处理:用400目的砂纸打磨碳基体直至表面平整,随后用酒精超声清洗,最后放入烘箱干燥;
[0058]
步骤(6):在石墨模具内,用经过步骤(3)得到的非平衡态前驱物将经过步骤(5)处理后的碳基体包裹,在基体的上下部分别填充一定量的非平衡态前驱体粉体,实现碳基体被非平衡态前驱体粉体均匀包裹,石墨基体四周所覆盖非平衡态前驱体粉体的厚度约为石墨基体厚度的0.6倍;
[0059]
步骤(7):sps烧结:将装好试样的模具放入sps烧结炉中进行烧结处理,烧结参数为:烧结温度1500℃,升温速率100℃/min,压力30mpa,保温时间5min,在碳基体表面得到高阻氧涂层。
[0060]
实施例2:
[0061]
通过自蔓延合成非平衡态前驱体粉体的xrd如图4所示,高分辨tem图如图5所示,高阻氧涂层在1700℃氧化100min后的横截面形貌如图6所示。
[0062]
步骤(1):配料与混料:采用锆、硅、钼、硼粉为原料,其纯度≥99.0%,粒度≤50μm,按照质量分数48.3%锆,25.4%钼,14.8%硅和11.5%硼称取粉末,记作zm2,随后以400r/min的转速球磨3h使粉体充分混合均匀;
[0063]
步骤(2):压制成型:将混合均匀的粉料干燥后倒入在钢制模具中,采用压力约为210mpa,保压时间约为25s的条件下,通过压片机将其冷压成型为圆柱坯体,作为燃烧合成所需的前驱体;
[0064]
步骤(3):合成非平衡态合金化前驱物:首先将压制好的样品放入燃烧合成反应釜中,压坯的上柱头贴近钼制的电阻丝;其次,填充ar气对粉料进行惰性保护;再次,通过电加热钼丝预热样品,直至其引发自蔓延反应为止。随后,燃烧合成开始反应后关闭电源,等待反应完全;最后,样品冷却后,将即可得到所设计的前驱物;
[0065]
步骤(4):将得到的燃烧合成的硬质样品放到破碎机中进行破碎100min,随后放入烘箱进行干燥;
[0066]
步骤(5):碳基体的表面处理:用400目的砂纸打磨碳基体直至表面平整,随后用酒精超声清洗,最后放入烘箱干燥;
[0067]
步骤(6):在石墨模具内,用经过步骤(3)得到的非平衡态前驱物将经过步骤(5)处理后的碳基体包裹,在基体的上下部分别填充一定量的非平衡态前驱体粉体,实现碳基体被非平衡态前驱体粉体均匀包裹,石墨基体四周所覆盖非平衡态前驱体粉体的厚度约为石墨基体厚度的0.55倍;
[0068]
步骤(7):sps烧结:将装好试样的模具放入sps烧结炉中进行烧结处理,烧结参数为:烧结温度1600℃,升温速率150℃/min,压力40mpa,保温时间8min,在碳基体表面得到高阻氧涂层。
[0069]
实施例3:
[0070]
通过自蔓延合成非平衡态前驱体粉体的xrd如图7所示,高分辨tem图如图8所示,
高阻氧涂层在1700℃氧化100min后的横截面形貌如图9所示。
[0071]
步骤(1):配料与混料:采用锆、硅、钼、硼粉为原料,其纯度≥99.0%,粒度≤50μm,按照质量分数64.6%锆,15.3%硼,12.7%钼和7.4%硅称取粉末,记作zm3随后以200r/min的转速球磨8h使粉体充分混合均匀;
[0072]
步骤(2):压制成型:将混合均匀的粉料干燥后倒入在钢制模具中,采用压力约为180mpa,保压时间约为40s的条件下,通过压片机将其冷压成型为圆柱坯体,作为燃烧合成所需的前驱体;
[0073]
步骤(3):合成非平衡态合金化前驱物:首先将压制好的样品放入燃烧合成反应釜中,压坯的上柱头贴近钼制的电阻丝;其次,填充ar气对粉料进行惰性保护;再次,通过电加热钼丝预热样品,直至其引发自蔓延反应为止。随后,燃烧合成开始反应后关闭电源,等待反应完全;最后,样品冷却后,将即可得到所设计的前驱物;
[0074]
步骤(4):将得到的燃烧合成的硬质样品放到破碎机中进行破碎200min,随后放入烘箱进行干燥;
[0075]
步骤(5):碳基体的表面处理:用400目的砂纸打磨碳基体直至表面平整,随后用酒精超声清洗,最后放入烘箱干燥;
[0076]
步骤(6):在石墨模具内,用经过步骤(3)得到的非平衡态前驱物将经过步骤(5)处理后的碳基体包裹,在基体的上下部分别填充一定量的非平衡态前驱体粉体,实现碳基体被非平衡态前驱体粉体均匀包裹,石墨基体四周所覆盖非平衡态前驱体粉体的厚度约为石墨基体厚度的0.65倍;
[0077]
步骤(7):sps烧结:将装好试样的模具放入sps烧结炉中进行烧结处理,烧结参数为:烧结温度1700℃,升温速率200℃/min,压力20mpa,保温时间10min,在碳基体表面得到高阻氧涂层。
[0078]
本发明的实施例公布的是较佳的实施例,但并不局限于此,本领域的普通技术人员,极易根据上述实施例,领会本发明的精神,并做出不同的引申和变化,但只要不脱离本发明的精神,都在本发明的保护范围内。