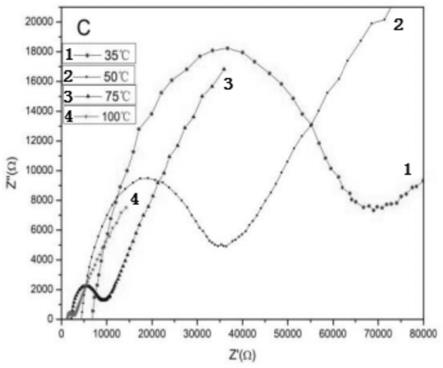
1.本发明涉及锂离子电池材料技术领域,特别涉及一种氧化物型固体电解质薄膜及其制备方法。
背景技术:2.在目前的电池领域研究中,锂离子电池具有体积小、质量轻、能量密度高、电化学窗口宽、环境友好等优越性能而且应用广泛,但目前传统的液态锂离子电池内部的电解液易燃易爆,因此安全性问题受到了广泛关注。对比之下,固体电解质的性质稳定,能完美地解决这类安全性问题,固体电解质主要分为氧化物型与硫化物型,而氧化物型包含石榴石、钙钛矿、nasicon、lisicon等结构型。其中,石榴石型固体电解质li7la3zr2o
12
(llzo)在锂离子电池的应用上具有良好的前景,具有良好的热稳定性,宽的电化学窗口和高的安全性等优点。
3.问题1:锂镧锆氧石榴石型固体电解质,它具有两种物相:四方相和立方相,在室温下锂镧锆氧石榴石型固体电解质的物相主要是四方相,四方相中锂的位点被锂完全占据,锂离子移动的几何空间较小,锂离子传输十分困难,导致室温下锂镧锆氧石榴石型固体电解质的导电能力十分差,其离子电导率较小。这些问题严重制约llzo的应用。
4.如果将固体电解质制备成薄膜型材料,会大大降低锂离子的扩散时间与全固态电池的总阻抗,可以弥补llzo在离子电导率方面的不足。目前已报道llzo薄膜中,由于制备方法、基底要求等问题,这些llzo电解质薄膜还不能在全固态电池中取得应用。
5.问题2:目前已有的薄膜制备方法,脉冲激光沉积法能控制llzo薄膜取向生长,但沉积面积小,大规模制造受限;磁控溅射法沉积速率慢,制备出的电解质薄膜电导率低;且这两种方法都需要基于真空环境进行,条件严苛。金属有机气相沉积在沉积速度和形貌控制方面有着显著的优势;原子层沉积法作为界面改性的一种常用方法,可以将固体电解质层均匀地沉积在各种复杂基底的表面。可以看出研究者们已通过各种方法能够制备出llzo超薄电解质薄膜,且能精确控制薄膜的厚度。但是由于上述介绍的制备方法,由于自身的局限性,如严苛的制备条件、高要求的基底材料、非晶薄膜较低的离子电导、制备成本高等,使得这类的llzo薄膜电解质还没有被有效地应用在全固态电池中。
6.因此,本领域急需一种新型固态电解质制备方法。
技术实现要素:7.鉴于此,本发明提出一种氧化物型固体电解质薄膜及其制备方法,可以在较短的时间及简单的工艺制得具有优异电化学性能的高离子电导率固体电解质薄膜,可以应用于全固态电池中,并且成本低,可工业化生产。
8.本发明的技术方案是这样实现的:一种氧化物型固体电解质薄膜的制备方法,包括以下步骤:(1)水基前驱体溶液制备:
9.按照相应的化学计量比,取锂盐、镧盐、锆盐、铝盐、钙盐、柠檬酸、乙二醇、粘结剂
和表面活性剂,与去离子水混合,搅拌加热,制备0.11
‑
0.13mol/l前驱体溶液,所述前驱体的化学通式为li
6.55+x
al
0.15
la3‑
x
ca
x
zr
2(
oh)
24
,x为0
‑
0.15;所述锂盐、柠檬酸和乙二醇的摩尔比为1:0.09
‑
0.11:0.9
‑
1.1;其中li含量在化学计量比基础上过量10%,由于锂在高温烧结过程中易挥发,为了弥补高温烧结过程中的锂损失,因此称量锂盐时需在化学计量比基础上过量10%。
10.(2)将步骤(1)制得前驱体溶液加入到超声喷涂仪的注射器中,将裁好的硅基片放在超声喷涂仪的样品台上,以流速0.008
‑
0.011ml/min进行喷涂至硅基片上,流速过大会导致溶液在硅基片表面区域性聚集,不利于形成薄膜;
11.样品台打开加热至110
‑
130℃,喷涂循环次数为三次,每次包含横向喷涂一层和纵向喷涂一层,三次共喷涂六层,当循环次数为1
‑
2次(2
‑
4层)时循环次数过少,溶液无法完全附着在硅基片表面;循环次数为4次(8层)时,溶液会在硅基片表面聚集无法均匀分布;
12.每喷涂一层后放在磁力搅拌器上加热445
‑
455℃处理;
13.(3)将步骤(2)喷涂好的硅基片进行烧结,以2.8
‑
3.2℃/min的升温速率升温至1095
‑
1105℃保温,烧结温度过高或烧结时间过长会导致硅基片变形不利于溶液在其表面成膜,薄膜电导率降低,烧结温度过低或烧结时间过短会导致反应不完全,无法完全形成所需的样品纯相,产生各种各样的杂相,不利于样品性能;然后自然冷却至室温,制得li
6.55+x
al
0.15
la3‑
x
ca
x
zr2o
12
固体电解质薄膜。
14.本发明还提供,将铝盐替换为等摩尔量的镓盐,制得li
6.55+x
ga
0.15
la3‑
x
ca
x
zr2o
12
固体电解质薄膜;或者将铝盐替换为等摩尔量的铁盐,制得li
6.55+x
fe
0.15
la3‑
x
ca
x
zr2o
12
固体电解质薄膜。
15.进一步的,步骤(1),所述锂盐为硝酸锂,所述镧盐为六水合硝酸镧,所述锆盐为硝酸氧锆,所述铝盐为九水合硝酸铝,所述钙盐为四水合硝酸钙或者无水硝酸钙;所述粘结剂为粘结剂speek
‑
psi
‑
li;所述表面活性剂为表面活性剂f127。
16.进一步的,步骤(1),所述粘结剂和表面活性剂均为前驱体溶液总质量的9.8%
‑
10.2%。
17.进一步的,步骤(1),所述搅拌加热的温度为85
‑
95℃,优选90℃。
18.进一步的,步骤(2),所述搅拌加热的方式为水浴加热或者油浴加热。
19.进一步的,步骤(2),所述磁力搅拌器上加热445
‑
455℃处理的时间为5
‑
6min。
20.进一步的,步骤(2),所述前驱体溶液加入到超声喷涂仪的注射器中体积量为9
‑
10ml。
21.进一步的,步骤(3),所述保温的时间为1
‑
3h,优选1h。
22.一种氧化物型固体电解质薄膜的方法,包括以下步骤:(1)水基前驱体溶液制备:
23.取硝酸锂、六水合硝酸镧、硝酸氧锆、九水合硝酸铝、四水合硝酸钙、柠檬酸、乙二醇、粘结剂speek
‑
psi
‑
li、表面活性剂f127,与去离子水混合,搅拌加热,制备0.12mol/l前驱体溶液,所述前驱体的化学通式为li
6.55+x
al
0.15
la3‑
x
ca
x
zr
2(
oh)
24
,x为0
‑
0.15;所述锂盐、柠檬酸和乙二醇的摩尔比为1:0.1:1;
24.(2)将步骤(1)制得前驱体溶液加入到超声喷涂仪的注射器中,将裁好的硅基片放在超声喷涂仪的样品台上,以流速0.01ml/min进行喷涂至硅基片上,样品台打开加热至120℃,喷涂循环次数为三次,每次包含横向喷涂一层和纵向喷涂一层,三次共喷涂六层,每喷
涂一层后放在磁力搅拌器上加热450℃处理5min;
25.(3)将步骤(2)喷涂好的硅基片进行烧结,以3℃/min的升温速率升温至1100℃,保温1h,然后自然冷却至室温,得到目标产品li
6.55+x
al
0.15
la3‑
x
ca
x
zr2o
12
。
26.一种氧化物型固体电解质薄膜,由本发明任一项所述的氧化物型固体电解质薄膜的制备方法制得。
27.与现有技术相比,本发明的有益效果是:
28.(1)本发明首先制备水基前驱体溶液,通过超声波喷涂在硅基片上对溶液进行喷涂,最后采用高温热处理得到固体电解质薄膜,可以在很短的时间及简单的工艺制备得到高离子电导率电解质薄膜,化学通式为li
6.55+x
al
0.15
la3‑
x
ca
x
zr2o
12
、li
6.55+x
ga
0.15
la3‑
x
ca
x
zr2o
12
、li
6.55+x
fe
0.15
la3‑
x
ca
x
zr2o
12
。
29.(2)本发明将固体电解质制备成薄膜型材料,大大降低锂离子的扩散时间与全固态电池的总阻抗,弥补了llzo在离子电导率方面的不足。本发明所制备的固体电解质在室温下的主要物相为立方相,立方相中锂的位点被锂不完全占据,整个结构中存在大量的锂空位,这为锂离子的传输提供通道,从而大大提高该类型固体电解质的导电能力,在室温下就具有较高的导电能力,其离子电导率较大。
30.(3)相较于已存在的薄膜电解质制备方法(磁控溅射、脉冲激光沉积等),由于方法自身的局限性,如严苛的制备条件、高要求的基底材料、非晶薄膜较低的离子电导、制备成本高等,使得这类llzo电解质薄膜还没有被有效地应用在全固态电池中。而本发明采用超声波喷涂法不仅制得的固态电解质具有优异的电化学性能,而且制备过程简单、合成条件灵活可行、化学组分易于控制、成本低、适宜工业化生产。因此本发明制备的固体电解质薄膜可应用于全固态电池。
附图说明
31.图1为实施例1氧化物型固体电解质薄膜li
6.6
al
0.15
la
2.95
ca
0.05
zr2o
12
的制备流程图。
32.图2实施例1氧化物型固体电解质薄膜li
6.6
al
0.15
la
2.95
ca
0.05
zr2o
12
的xrd图。由图2能够看到不同烧结时间下的各个峰与立方相图谱大致对应。在27
°
~30
°
之间各组样品均只存在(400)峰,不存在(004)峰,可知所获得的样品主晶相均为立方相结构。
33.图3实施例1氧化物型固体电解质薄膜li
6.6
al
0.15
la
2.95
ca
0.05
zr2o
12
的sem图。如图3从左至右分别是样品在1000倍和2000倍下拍摄的电镜图。能看到晶粒尺寸大小不均匀。存在一些孔洞和间隙,导致密度下降。
34.图4为实施例1氧化物型固体电解质薄膜li
6.6
al
0.15
la
2.95
ca
0.05
zr2o
12
在不同温度下的eis图谱;通过计算离子电导率与烧结时间呈反比,在室温下为2.28
×
10
‑5s/cm。
35.图5为实施例5氧化物型固体电解质薄膜li
6.6
ga
0.15
la
2.95
ca
0.05
zr2o
12
在不同测试温度下的eis图谱;通过计算离子电导率在室温下最高可达2.28
×
10
‑5s/cm。
36.图6为实施例6氧化物型固体电解质薄膜li
6.6
fe
0.15
la
2.95
ca
0.05
zr2o
12
在不同测试温度下的eis图谱;通过计算离子电导率在室温下最高可达1.14
×
10
‑6s/cm。
具体实施方式
37.为了更好理解本发明技术内容,下面提供具体实施例,对本发明做进一步的说明。
38.本发明实施例所用的实验方法如无特殊说明,均为常规方法。
39.本发明实施例所用的材料、试剂等,如无特殊说明,均可从商业途径得到。
40.一、产品制备
41.实施例1氧化物型固体电解质薄膜的制备
42.(1)水基前驱体溶液制备:原料混合:按照相应的化学计量比,对硝酸锂(lino3)、六水合硝酸镧(la(no3)
3`
6h2o)、硝酸氧锆(zro(no3)2)、九水合硝酸铝(al(no3)
3`
9h2o)、四水合硝酸钙(ca(no3)
2`
4h2o)、柠檬酸、乙二醇、粘结剂speek
‑
psi
‑
li、表面活性剂f127进行相应的称量,化学计量比为li:la:zr:al:ca=6.6:2.95:2:0.15:0.05(132:59:40:3:1),其中li含量在化学计量比基础上过量10%,由于锂在高温烧结过程中易挥发,为了弥补高温烧结过程中的锂损失,因此称量硝酸锂(lino3)时需过量10%。其中,硝酸锂、柠檬酸和乙二醇的摩尔比为1:0.1:1,粘结剂和表面活性剂的加入量均为前驱体溶液总质量的10%。将原料与适量的去离子水混合,一同加入到烧杯中,开启磁力搅拌器,水浴加热搅拌,加热温度90℃,直至原料完全混合溶解,搅拌过程中注意观察溶液量变化,加入去离子水以维持溶液浓度不变,制备0.12mol/l前驱体溶液,溶液呈透明状,所述前驱体的化学通式为li
6.6
al
0.15
la
2.95
ca
0.05
zr
2(
oh)
24
。
43.(2)将步骤(1)配制好的前驱体溶液取约10ml加入到超声喷涂仪的注射器中,用前驱体溶液对管路进行清洗,将裁好的硅基片放在可加热样品台上,设定好程序进行喷涂,以流速0.01ml/min进行喷涂至硅基片上;样品台打开加热至110
‑
130℃,本实施例加热至120℃,喷涂循环次数为三次,每次包含横向喷涂一层和纵向喷涂一层,三次共喷涂六层。每喷涂一层后放在磁力搅拌器上加热450℃处理5min。如此反复直至全部层数喷涂结束;
44.(3)使用扁形镊子将步骤(2)喷涂好的硅基片取出放入到马弗炉中进行烧结,以3℃/min的升温速率升温至1100℃,保温1
‑
3h,本实施例保温1h,然后自然冷却至室温,得到目标产品li
6.6
al
0.15
la
2.95
ca
0.05
zr2o
12
固体电解质薄膜样品。使用扁形镊子取出样品,密封保存。
45.二、产品性能测试
46.1.测试方法
47.(1)xrd测试
48.xrd测试采集相应的特征峰,与数据库中的标准立方相与四方相峰值进行比较,判断是否生成我们所需的产品物相,同时也能观测到杂质峰的出现。本发明采用d2
‑
phaser型号仪器,在40kv电压下cu靶射线源,扫描范围10
°
到80
°
。
49.(2)扫描电子显微镜(sem)及能谱测试
50.本发明采用phenom prox型号扫描电子显微镜对掺杂固体电解质样品进行微观形貌分析,观测样品的结晶情况、晶粒是否均匀、致密度等等。能谱测试得到各个元素在样品中的分布情况。
51.(3)交流阻抗(eis)测试
52.本发明采用1470e型号电化学工作站,振动幅度10mv,频率范围1mhz到0.1hz。测试交流阻抗是对固体电解样品电导率直观的表征方式,锂离子导体的交流阻抗由晶界、晶粒
阻抗及其相对应的电容组成。电导率计算公式如下:
53.σ=l/(πr2)r
54.式中符号:σ:电导率;r:陶瓷样品半径;r:总电阻;l:陶瓷样品厚度。
55.样品在25度到150度范围内测量四个以上阻抗值,按照上式得出离子电导率后,可通过阿伦尼乌斯公式进行活化能的计算:
56.lnσ=lnσ0‑
ea/rt
57.式中符号:ea:活化能;r:摩尔气体常数;t:热力学温度(k)。
58.2.测试结果
59.图2为实施例1氧化物型固体电解质薄膜li
6.6
al
0.15
la
2.95
ca
0.05
zr2o
12
的xrd图。由图2能够看到不同烧结时间下的各个峰与立方相图谱大致对应。在27
°
~30
°
之间各组样品均只存在(400)峰,不存在(004)峰,可知实施例1所获得的样品主晶相均为立方相结构。
60.图3为实施例1氧化物型固体电解质薄膜li
6.6
al
0.15
la
2.95
ca
0.05
zr2o
12
的sem图。如图3从左至右分别是样品在1000倍和2000倍下拍摄的电镜图。能看到晶粒分布较为均匀,这意味着样品有良好的导电性能。
61.图4为氧化物型固体电解质薄膜li
6.6
al
0.15
la
2.95
ca
0.05
zr2o
12
在不同测试温度下的eis图谱;通过计算离子电导率在室温下最高可达4.76
×
10
‑6s/cm。
62.参照实施例1制备工艺,调整硝酸锂、六水合硝酸镧、四水合硝酸钙用量比例,还可以将九水合硝酸铝替换为硝酸镓或硝酸铁,其他制备步骤与实施例1保持一致,分别制备实施例2至6固体电解质薄膜样品。
63.序号产品的化学通式lilazralgacafe实施例1li
6.6
al
0.15
la
2.95
ca
0.05
zr2o
12
6.602.952.000.1500.050实施例2li
6.55
al
0.15
la3zr2o
12
6.553.002.000.15000实施例3li
6.55
ga
0.15
la3zr2o
12
6.553.002.0000.1500实施例4li
6.55
fe
0.15
la3zr2o
12
6.553.002.000000.15实施例5li
6.6
ga
0.15
la
2.95
ca
0.05
zr2o
12
6.602.952.0000.150.050实施例6li
6.6
fe
0.15
la
2.95
ca
0.05
zr2o
12
6.602.952.00000.050.15
64.实施例2:单独掺杂al元素,其高离子电导率氧化物电解质薄膜化学通式为li
6.55
al
0.15
la3zr2o
12
,所使用的原料为lino3、la(no3)3、zro(no3)2、al(no3)3粉末。
65.实施例3:单独掺杂ga元素,其高离子电导率氧化物电解质薄膜化学通式为li
6.55
ga
0.15
la3zr2o
12
,所使用的原料为lino3、la(no3)3、zro(no3)2、ga(no3)3粉末。
66.实施例4:单独掺杂fe元素,其高离子电导率氧化物电解质薄膜化学通式为li
6.55
fe
0.15
la3zr2o
12
,所使用的原料为lino3、la(no3)3、zro(no3)2、fe(no3)3粉末。
67.实施例5:双掺杂ga元素和ca元素,其高离子电导率氧化物电解质薄膜化学通式为li
6.6
ga
0.15
la
2.95
ca
0.05
zr2o
12
,所使用的原料为lino3、la(no3)3、zro(no3)2、ga(no3)3、ca(no3)2粉末。
68.实施例6:双掺杂fe元素和ca元素,其高离子电导率氧化物电解质薄膜化学通式为li
6.6
fe
0.15
la
2.95
ca
0.05
zr2o
12
,所使用的原料为lino3、la(no3)3、zro(no3)2、fe(no3)3、ca(no3)2粉末。
69.图5为实施例5氧化物型固体电解质薄膜li
6.6
ga
0.15
la
2.95
ca
0.05
zr2o
12
在不同测试温
度下的eis图谱;通过计算离子电导率在室温下最高可达2.28
×
10
‑5s/cm。
70.图6为实施例6氧化物型固体电解质薄膜li
6.6
fe
0.15
la
2.95
ca
0.05
zr2o
12
在不同测试温度下的eis图谱;通过计算离子电导率在室温下最高可达1.14
×
10
‑6s/cm。
71.对比例1
72.在实施例1的基础上,水基前驱体溶液制备工艺不变,不采用超声波喷涂仪器进行喷涂,而采用旋涂方式在硅基片表面进行溶液附着,将表面涂好溶液的硅基片放入马弗炉中烧结,烧结工艺不变。前驱体溶液未能均匀地附着在硅基片表面,相较于超声波喷涂,获得的电解质宏观及微观性能都有所下降。
73.对比例2
74.在实施例1的基础上,水基前驱体溶液制备工艺不变,不采用超声波喷涂仪器进行喷涂,而采用浸涂方式在硅基片表面进行溶液附着,将表面涂好溶液的硅基片放入马弗炉中烧结,烧结工艺不变。与对比例1类似,前驱体溶液未能均匀地附着在硅基片表面,相较于超声波喷涂,获得的电解质宏观及微观性能出现下降。
75.对比例3
76.在实施例1的基础上,调整喷涂循环次数,循环次数为两次(四层),水基前驱体溶液无法完全附着在硅基片表面。
77.对比例4
78.在实施例1的基础上,调整喷涂循环次数,循环次数为四次(八层),水基前驱体溶液会在硅基片表面聚集无法均匀分布。
79.对比例5
80.在实施例1的基础上,调整烧结温度为1300℃,硅基片变形,不利于水基前驱体溶液在其表面成膜,薄膜电导率降低。
81.对比例6
82.在实施例1的基础上,调整烧结温度为800℃,反应不完全,无法完全形成所需的样品纯相,产生各种各样的杂相,不利于样品性能。
83.以上所述仅为本发明的较佳实施例而已,并不用以限制本发明,凡在本发明的精神和原则之内,所做的任何修改、等同替换、改进等,均应包含在本发明的保护范围之内。