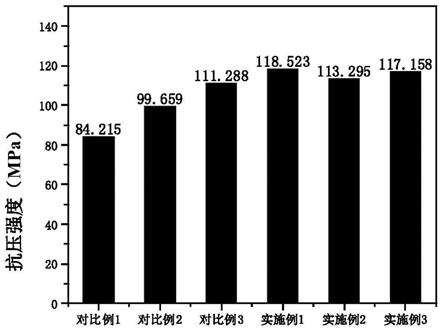
1.本发明属于建筑材料领域,尤其涉及一种钢渣基碳化材料及其制备方法和应用。
背景技术:2.钢渣原为炼钢过程的产生的废渣,是生铁中的少量的金属元素和硅、硫等杂质在煅烧过程中形成的各种氧化物,主要分为电炉钢渣、平炉钢渣和转炉钢渣3种。钢渣中含有硅酸二钙、硅酸三钙、氧化钙和氧化镁等成分,使用合适的处理工艺和制备方法,便可以将钢渣变废为宝,充分利用。
3.科技发展带来的化石燃料的燃烧和排放,加剧了温室效应。因此,亟需一种既能解决钢渣的不合理利用又能解决二氧化碳排放的实施方案,进而减少污染并提高资源的利用率。
技术实现要素:4.针对现有技术不足,本发明的目的在于提出一种钢渣基碳化材料及其制备方法和应用,解决了钢渣的不合理利用和二氧化碳的排放问题。
5.本发明的目的通过以下技术方案实现:
6.一种钢渣基碳化材料的制备方法,包括如下步骤:
7.(1)在钢渣中加入干炉渣、石英砂尾矿、粉煤灰、石粉、矿粉、硅灰和脱硫石膏,并混合均匀得到钢渣混合物,再加入增强剂并研磨混匀,得到拌合物;按质量百分数计,钢渣混合物中,钢渣85~93%、干炉渣1~5%,石英砂尾矿1~5%、粉煤灰1~5%、石粉0.4~3%、矿粉0.4~3%、硅灰0.2~3%和脱硫石膏0.2~3%;
8.(2)将步骤(1)制备得到的拌合物压制成所需的坯体,然后进行碳化处理后烘干,即制备得到所述钢渣基碳化材料。
9.优选的,步骤(1)所述增强剂加入的质量占钢渣的2.6~12%。
10.优选的,步骤(1)所述增强剂为碳酸氢钠、柠檬酸、焦磷酸钠、硫酸镁和丁二醇中的至少一种。
11.优选的,步骤(1)所述增强剂使用时需配置成浓度为5~20wt%的溶液。
12.优选的,步骤(1)所述钢渣为转炉钢渣、平炉钢渣和电炉钢渣中的至少一种。
13.优选的,步骤(1)所述钢渣的粒径为60目~200目。
14.优选的,步骤(1)所述干炉渣和石英砂尾矿的粒径为60目~100目。
15.优选的,步骤(1)所述石粉为白云石粉,其目数为200目;所述矿粉为s140 级矿粉。
16.优选的,步骤(2)所述压制的压强在8mpa~30mpa,保压时间在60s~300s。
17.优选的,步骤(2)所述碳化处理的碳化压力为0.05mpa~0.5mpa、碳化浓度为10%~100%,碳化时间为2h~72h。碳化处理时的相对湿度为32~98%。
18.上述一种钢渣基碳化材料的制备方法制备得到的钢渣基碳化材料。
19.上述钢渣基碳化材料在制备建筑材料中的应用。
20.本发明涉及的机理:
21.钢渣碳化时,水分子扩散到钢渣的粗孔、毛细孔以及凝胶孔中,并向钢渣颗粒内部扩散。钢渣中的碱性金属阳离子浸出,周围的co2扩散到钢渣表面,与水反应生产h2co3,然后电离成hco
3-、co
32-等离子,硅酸盐矿物水化生成 c-s-h凝胶,ca
2+
与碳酸根反应生产方解石。
22.石英砂尾矿和干炉渣等复配料(粉煤灰、石粉、矿粉、硅灰和脱硫石膏) 具有完善级配的作用,减小颗粒间的空隙,排出空隙中的部分水分,使自由水增加,从而使浆体流动性增大,同时增加拌和物的密实度。弥补了表面粗糙的缺点,克服形貌效应的不良影响,有效堆积使过渡区密实化,改善了“次中心区过渡层”的结构,起到到晶核作用和匀化效应。加入增强剂后,钙离子与极性基团络合形成配位共价键,促进了钙离子等金属离子的溶解,提高了碳化反应活性,产生更多的碳酸盐,进而提高了强度。
23.与现有技术相比,本发明的有益效果包括:
24.本发明利用工业废料钢渣、炉渣和粉煤灰等复配料制备高性能碳化制品,解决了钢渣占地、利用率低的问题,同时,本发明碳化时吸收和固定工业废气排放的二氧化碳,绿色环保。通过加入辅料和增强剂,提高了碳化制品的抗压强度、碳化深度和碳化程度,在碳化28h后强度最高可达到118mpa。
附图说明
25.图1是实施例1~3和对比例1~3的产物的抗压强度测试柱状图。
26.图2是实施例1~3和对比例1~3的产物的碳化程度统计结果柱状图。
27.图3是实施例1~3和对比例1~3的产物的碳化深度的统计结果柱状图。
具体实施方式
28.为了使本发明的目的、技术方案及优点更加清楚明白,以下结合实施例,对本发明进行进一步详细说明。应当理解,此处所描述的具体实施例仅仅用以解释本发明,并不用于限定本发明。
29.实施例和对比例所选用的原料的来源一致,所使用的不锈钢模具也是相同的。
30.实施例1
31.一种钢渣基碳化材料的制备方法,步骤如下:
32.(1)在9.5g钢渣中加入0.4g干炉渣、0.25g石英砂尾矿、0.2g粉煤灰、0.05g 石粉、0.05g矿粉、0.025g硅灰和0.025g脱硫石膏,并混合均匀得到钢渣混合物;
33.(2)取0.05g丁二醇、0.2g碳酸氢钠和1.3g水充分混合得到增强剂溶液,并将增强剂溶液与步骤(1)所述的钢渣混合物在玛瑙研钵中研磨混匀,得到拌合物;
34.(3)将步骤(2)的拌合物放入不锈钢模具中,30mpa压力下保压120s,压制成钢渣坯体,将钢渣胚体置于碳化罐中进行碳化处理,二氧化碳浓度为 95%、压强为0.15mpa、相对湿度为50%、碳化时间为28h,碳化处理结束后将样品取出后,置于烘箱进行烘干处理,即得到钢渣基碳化材料。
35.实施例2
36.一种钢渣基碳化材料的制备方法,步骤如下:
37.(1)在9.5g钢渣中加入0.15g干炉渣、0.4g石英砂尾矿、0.15g粉煤灰、 0.1g石粉、0.1g矿粉、0.025g硅灰和0.025g脱硫石膏,并混合均匀得到钢渣混合物;
38.(2)取0.05g丁二醇、0.2g碳酸氢钠和1.3g水充分混合得到增强剂溶液,并将增强剂溶液与步骤(1)所述的钢渣混合物在玛瑙研钵中研磨混匀,得到拌合物;
39.(3)将步骤(2)的拌合物放入不锈钢模具中,30mpa压力下保压120s,压制成钢渣坯体,将钢渣胚体置于碳化罐中进行碳化处理,二氧化碳浓度为 95%、压强为0.15mpa、相对湿度为50%、碳化时间为28h,碳化处理结束后将样品取出后,置于烘箱进行烘干处理,即得到钢渣基碳化材料。
40.实施例3
41.一种钢渣基碳化材料的制备方法,步骤如下:
42.(1)在9.5g钢渣中加入0.15g干炉渣、0.15g石英砂尾矿、0.4g粉煤灰、 0.1g石粉、0.1g矿粉、0.05g硅灰和0.05g脱硫石膏,并混合均匀得到钢渣混合物;
43.(2)取0.05g丁二醇、0.2g碳酸氢钠和1.3g水充分混合得到增强剂溶液,并将增强剂溶液与步骤(1)所述的钢渣混合物在玛瑙研钵中研磨混匀,得到拌合物;
44.(3)将步骤(2)的拌合物放入不锈钢模具中,30mpa压力下保压120s,压制成钢渣坯体,将钢渣胚体置于碳化罐中进行碳化处理,二氧化碳浓度为 95%、压强为0.15mpa、相对湿度为50%、碳化时间为28h,碳化处理结束后将样品取出后,置于烘箱进行烘干处理,即得到钢渣基碳化材料。
45.对比例1
46.一种钢渣基碳化材料的制备方法,步骤如下:
47.(1)取10.5g钢渣和1.3g水于玛瑙研钵中研磨混匀,得到拌合物;
48.(2)将步骤(1)的拌合物放入不锈钢模具中,30mpa压力下保压120s,压制成钢渣坯体,将钢渣胚体置于碳化罐中进行碳化处理,二氧化碳浓度为 95%、压强为0.15mpa、相对湿度为50%、碳化时间为28h,碳化处理结束后将样品取出后,置于烘箱进行烘干处理,即得到钢渣基碳化材料。
49.对比例2
50.一种钢渣基碳化材料的制备方法,步骤如下:
51.(1)在9.5g钢渣中加入0.4g干炉渣、0.25g石英砂尾矿、0.02g粉煤灰、 0.05g石粉、0.05g矿粉、0.025g硅灰和0.025g脱硫石膏,并混合均匀得到钢渣混合物;
52.(2)取1.3g水充分与步骤(1)所述的钢渣混合物在玛瑙研钵中研磨混匀,得到拌合物;
53.(3)将步骤(2)的拌合物放入不锈钢模具中,30mpa压力下保压120s,压制成钢渣坯体,将钢渣胚体置于碳化罐中进行碳化处理,二氧化碳浓度为 95%、压强为0.15mpa、相对湿度为50%、碳化时间为28h,碳化处理结束后将样品取出后,置于烘箱进行烘干处理,即得到钢渣基碳化材料。
54.对比例3
55.一种钢渣基碳化材料的制备方法,步骤如下:
56.(1)取10.50g钢渣,再取0.05g丁二醇、0.2g碳酸氢钠和1.3g水充分混合得到增强剂溶液;将钢渣和增强剂溶液于玛瑙研钵中研磨混匀,得到拌合物;
57.(2)将步骤(1)的拌合物放入不锈钢模具中,30mpa压力下保压120s,压制成钢渣坯体,将钢渣胚体置于碳化罐中进行碳化处理,二氧化碳浓度为 95%、压强为0.15mpa、相对湿度为50%、碳化时间为28h,碳化处理结束后将样品取出后,置于烘箱进行烘干处理,即得到钢渣基碳化材料。
58.性能测试:
59.1.抗压强度测试
60.采用sans万能试验机对样品的抗压强度进行测试,下降速度是0.5mm/s。
61.实施例1~3和对比例1~3的产物的抗压强度测试结果见图1。
62.从图1可以得出:将对比例1和对比例2比较可知加入复配料后,强度提高15.4mpa。这是因为石英砂尾矿和干炉渣等辅料具有减小颗粒间的空隙,排出空隙中的部分水分,使自由水增加,从而使浆体流动性增大,同时增加拌和物的密实度。有效堆积使过渡区密实化,改善了“次中心区过渡层”的结构,起到到晶核作用和匀化效应。将对比例1和对比例3比较可知,加入增强剂后,强度提高27.073mpa。钙离子与极性基团络合形成配位共价键,促进了钙离子等金属离子的溶解,提高了碳化反应活性,产生更多的碳酸盐,进而提高了强度。将对比例1和实施例1比较可知,加入复配料和增强剂后,两者协同作用,强度提高34.30mpa。分别将实施例2~3与对比例1~3对比,也能够得到类似的结果。
63.2.碳化程度
64.将样品打碎研磨,放入坩埚中得到质量m1,放入厢式炉中烧到500℃保温 2h,得到质量m2,得到的粉末在1000℃煅烧中继续煅烧,保温2h,称得质量 m3。在对样品进行xrf测试,得到样品cao、al2o3、fe2o3和mgo的百分比含量a,通过公式得到cao的碳化程度,其中44g/mol 为co2的相对分子质量,56g/mol是cao的相对分子质量。
65.依次计算出al2o3、fe2o3和mgo的碳化程度,相加得到样品的碳化程度,实施例1~3和对比例1~3的产物的碳化程度统计结果见图2。从图2可以得出:加入增强剂和复配料后,促进了钙离子等金属离子的溶解,提高了碳化反应活性,产生更多的碳酸盐,进而提高了碳化程度。
66.3.碳化深度
67.将半径10mm柱状样品从中间沿纵截面切开,每个样品滴加10滴浓度为 2wt%的酚酞溶液,通过样品变色情况,用游标卡尺测量,得到样品的碳化深度,实施例1~3和对比例1~3的产物的碳化深度的统计结果见图3。从图3可以得出:与碳化程度相同,加入复配料和增强剂后,形成了更多的碳酸盐,碳化深度也提高了。
68.以上所述本发明的具体实施方式,并不构成对本发明保护范围的限定。任何根据本发明的技术构思所做出的各种其他相应的改变与变形,均应包含在本发明权利要求的保护范围内。