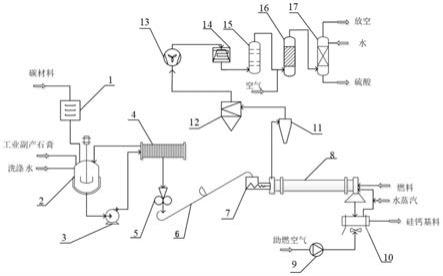
1.本发明涉及固体废弃物资源化技术领域,具体涉及工业副产石膏的资源化处理,尤其涉及一种工业副产石膏制备硅钙基料与硫酸的装置及方法。
背景技术:2.随着工业的快速发展,天然石膏资源在开采与消耗的同时,会排放大量的工业副产石膏,其中工业副产石膏是指工业生产中因化学反应生成的以硫酸钙为主要成分的副产品或废渣,也称化学石膏或工业废石膏,主要包括脱硫石膏、磷石膏、柠檬酸石膏、氟石膏、盐石膏、味精石膏、铜石膏、钛石膏等,其中脱硫石膏和磷石膏的产生量约占全部工业副产石膏总量的85%。我国每年9000 万吨硫酸的60-70%最终形成磷石膏,年排放量约8000万吨,累积堆存量超过5 亿吨,已经成为威胁长江生态的头号污染源。脱硫石膏随着煤电的发展,逐年递增,目前年排放量7500万吨,累积堆存量约1.3亿吨,在西部地区成为环保难题。钛白行业每生产1吨钛白粉,副产4-5吨钛石膏,每年高达2000万吨以上,成为制约行业发展的难题。
3.目前,工业副产石膏的用途包括水泥缓凝剂、石膏板、石膏砌块、石膏砂浆等,尤其是一般发电企业均配套有水泥粉磨站,直接消纳粉煤灰与脱硫石膏,脱硫石膏利用率达到了70%以上。磷石膏由于含有磷、氟等有害物质,生产的石膏建材稳定性较差,利用率低,只有30%,多用在矿井充填、水泥添加剂和石膏板中,用量小,再加之磷石膏多集中在云南、贵州、湖北、重庆及四川等地,产量集中,石膏建材附加值低,市场辐射半径小,严重制约了石膏建材产品市场的扩展。
4.利用石膏作为原料生产硫酸,实现硫酸的循环无疑是解决磷石膏等工业副产石膏问题最有利的技术之一,引起了广泛的关注,我国建成了十几套石膏制酸装置。国内也有鲁北化工,贵州金正大等企业建设了十万吨规模的石膏分解制硫酸和水泥的装置。
5.cn108675270a公开了一种磷石膏制硫酸联产水泥熟料的系统和方法,系统包括通过管路依次连接的酸解装置、第一固液分离装置、多级选洗装置、第二固液分离装置、干燥装置、粉磨装置和热分解装置;其中,第二固液分离装置的入口连接多级选洗装置的下层浆液出口;热分解装置的气相出口连接二氧化硫制硫酸装置的气相入口,热分解装置的固相出口连接水泥烧成装置的入口。通过酸解装置和多级选洗装置的配合,实现了磷石膏的高效深度净化,提高了水泥等资源化产物的品质;所得洁净磷石膏热分解后提高了钙资源的回收率,且分解产物中易分离得到具有高附加值的活性氧化钙;实现了大幅消纳磷石膏的目的,彻底消除磷石膏带来的巨大环境危害,实现磷石膏的高值化利用。
6.cn104555946a公开了一种由硫磺气体还原石膏制硫酸联产水泥熟料的方法,包括制备高温硫磺气体、生料配置和预热、石膏还原、石膏还原产物制水泥熟料和尾气制硫酸等步骤,包括按水泥熟料工艺要求配置水泥生料,经计量后依次通过一级旋风分离器、二级旋风分离器、三级旋风分离器和四级旋风分离器,最后与五级旋风分离器出口的高温气体进行换热后进入石膏还原炉,控制石膏还原炉内温度为800-950℃,让制备得到的高温硫磺气
体与水泥生料进行气固反应,得到反应产物固体cas和气体so2,由五级旋风分离器分离出来的固体物料经下料溜管进入回转煅烧窑,在窑内经过热炉气逐步预热升温至水泥熟料要求的煅烧温度1300-1450℃,并控制回转煅烧窑尾气中氧气的体积浓度在<2%的条件下,发生硫化钙与石膏的固—固反应分解,得到固体cao和气体 so2;固体物料经高温煅烧制成硅酸盐水泥熟料,并由窑头排入冷却机回收热量,气体so2进入还原炉;还原炉出口尾气在五级旋风分离器出口补入适量空气,氧化燃烧过量的硫后,依次通过四级旋风分离器、三级旋风分离器、二级旋风分离器和一级旋风分离器降温后,进入后续常规的硫酸生产工序进行除尘净化、转化、吸收制取硫酸。
7.cn112694067a公开了一种磷石膏生产水泥联产硫酸的生产方法,该方法将磷石膏经过预处理净化降低其中的不溶磷、水溶磷杂质和大部分游离水,与还原剂进行捏合造粒后的物料直接送入带有流态化预热功能的还原分解一体化转窑中,在煤粉燃烧下控制气相气氛进行分步加热、干燥、脱水、还原分解;还原分解后产生的二氧化硫气体经过除尘净化后用于生产硫酸;还原分解后的物料进入水泥熟料烧成的氧化煅烧窑中,在煤粉燃烧下控制气相气氛进行加热矿化烧成水泥熟料。
8.然而,现有技术中利用工业副产石膏生产水泥联产硫酸包括石膏还原与水泥烧成(石膏还原产物制水泥熟料)两个关键步骤,但石膏分解过程温度为 1200-1350℃,需要还原气氛,而水泥烧成温度为1300-1450℃,需要氧化气氛,反应过程存在着温度的交叉,气氛难以保证,在一个回转窑中很难控制,窑内物料极易结疤,因此操作温度要求在极其狭窄的区间控制,煤耗高,又导致回转窑处理强度下降,助燃空气量增大,烟气so2的浓度随之减少,导致后续硫酸装置效率低,投资大。此外,水泥烧成过程中容易夹裹着未反应的石膏等,使得水泥质量不稳定,无法获得合格的水泥产品。因此,石膏生产水泥联产硫酸存在着投资大、能耗高、水泥质量不稳定和硫酸制造成本高等问题,技术没有得到大规模的应用,成为行业公认的技术难题。
9.现有技术中利用工业副产石膏生产水泥联产硫酸,往往是将工业副产石膏与水泥生料提前混合,再将生产水泥与硫酸交织完成,控制难度较大。本发明提供了一种工业副产石膏制备硅钙基料与硫酸的装置及方法,将石膏与焦炭粉化浆混合,减少了石膏干燥和粉料均化过程,并专以分解石膏为目标,煅烧易于控制,改变反应气氛,降低了分解反应温度,石膏煅烧得到的硅钙基料不仅可以用于生产减碳型水泥熟料,还可以用于酸性土壤调节剂、粘合剂等其他用途,提高产品经济价值。
技术实现要素:10.鉴于现有技术中存在的问题,本发明提供了一种工业副产石膏制备硅钙基料与硫酸的装置及方法,所述装置包括依次连接的化浆混合器、固液分离器、滤饼破碎器、干燥分解反应器;在所述化浆混合器上设置碳材料入口、石膏入口、洗涤水入口以及浆料出口;在所述干燥分解反应器设置燃料入口与助燃气入口;所述干燥分解反应器的气体出口与二氧化硫制硫酸装置的气体入口相连接,所述干燥分解反应器的固体出口与硅钙基料收集器的入口相连接。利用本发明所述装置可以实现工业副产石膏与碳材料的化浆混合,将固液分离得到的滤饼与燃料、助燃气混合进行还原热解,回收热解气体中的so2获得硫酸产品,得到的硅钙基料不仅可以用于生产减碳型水泥熟料,还可以用于酸性土壤调节剂、粘合剂等
其他用途,提高产品经济价值。
11.为达此目的,本发明采用以下技术方案:
12.本发明的目的之一在于提供一种工业副产石膏制备硅钙基料与硫酸的装置,所述装置包括依次连接的化浆混合器、固液分离器、滤饼破碎器、干燥分解反应器;
13.其中,在所述化浆混合器上设置碳材料入口、石膏入口、洗涤水入口以及浆料出口,所述浆料出口与所述固液分离器的入口相连接,所述固液分离器的固体出口与所述滤饼破碎器的入口相连接;
14.在所述干燥分解反应器设置燃料入口与助燃气入口;所述干燥分解反应器的气体出口与二氧化硫制硫酸装置的气体入口相连接,所述干燥分解反应器的固体出口与硅钙基料收集器的入口相连接。
15.利用本发明所述装置可以实现工业副产石膏与碳材料的化浆混合,将固液分离得到的滤饼与燃料、助燃气混合进行还原热解,回收热解气体中的so2获得硫酸产品,得到的硅钙基料不仅可以用于生产减碳型水泥熟料,还可以用于酸性土壤调节剂、粘合剂等其他用途,提高产品经济价值;将工业副产石膏与碳材料进行化浆混合,减少了石膏干燥和粉料均化过程,并专以分解石膏为目标,煅烧易于控制,改变反应气氛,降低了分解反应温度。
16.值得说明的是,本发明所述化浆混合器优选为带搅拌桨的槽式设备,材质为耐酸材质,并设置液位计等计量仪表。
17.作为本发明优选的技术方案,在所述碳材料入口处设置碳材料粉碎机。
18.优选地,在所述化浆混合器与所述固液分离器之间的管路上设置化浆混合泵。
19.作为本发明优选的技术方案,在所述化浆混合器上设置循环水入口,所述固液分离器的液体出口与所述循环水相连接。
20.优选地,所述固液分离器包括混合过滤机,优选为高压压滤机,并配置隔膜压榨和气吹系统,可以大幅度降低滤饼含水量。
21.作为本发明优选的技术方案,在所述干燥分解反应器的入口处设置反应进料器,具备计量功能,保证进料准确,使得高温段来的高温烟气与进料滤饼接触,完成干燥与煅烧过程。
22.优选地,所述干燥分解反应器包括石膏分解窑。
23.优选地,所述石膏分解窑为回转煅烧窑,通过旋转回转结构,能够实现硫酸钙的干燥与分解,属于整个装置的核心设备。
24.作为本发明优选的技术方案,在所述干燥分解反应器与所述硅钙基料收集器之间设置冷却机,在所述冷却机上开设固体冷却入口、固体冷却出口、冷却气体入口与冷却气体出口,所述固体冷却入口与所述干燥分解反应器的固体出口相连接,所述固体冷却出口与所述硅钙基料收集器的入口相连接,所述冷却气体出口与所述干燥分解反应器的助燃气入口相连接。
25.优选地,在所述冷却机的冷却气体入口处设置助燃引风机。
26.值得说明的是,本发明所述装置通过设置冷却机,不仅可以利用助燃引风机吹入的助燃气给硅钙基料进行降温,还可以利用硅钙基料给助燃气进行预热,实现节能降耗。
27.作为本发明优选的技术方案,所述二氧化硫制硫酸装置包括依次连接的除尘装置、so2转化器与硫酸吸收塔。
28.优选地,所述除尘装置包括依次连接的旋风除尘器、静电除尘器、烟气引风机、湿式除尘器与气体干燥塔。
29.值得说明的是,本发明所述二氧化硫制硫酸装置与硫铁矿制硫酸装置基本一致,此处不再赘述。
30.本发明的目的之二在于提供一种利用目的之一所述装置进行工业副产石膏制备硅钙基料与硫酸的方法,所述方法包括如下步骤:
31.(1)化浆混合:将工业副产石膏与碳材料、洗涤水进行化浆混合,经固液分离得到滤饼和滤液;
32.(2)将步骤(1)得到的滤饼破碎后,在燃料与助燃气的燃烧供热下进行还原热解,得到热解气体和硅钙基料;
33.(3)将步骤(2)得到的热解气体经氧化和吸收后制得硫酸。
34.本发明所述工业副产石膏制备硅钙基料与硫酸的方法将工业副产石膏与碳材料直接进行化浆混合,将固液分离得到的滤饼在高温烟气下进行还原热解,使得工业副产石膏中的硫酸钙与碳材料中的碳反应生成氧化钙和二氧化硫、二氧化碳,而所述还原热解依靠燃料与助燃气进行燃烧产生的高温烟气来供热,得到热解气体和硅钙基料;回收热解气体中的so2获得硫酸产品,尾气达标排放,得到的硅钙基料不仅可以用于生产减碳型水泥熟料,还可以用于酸性土壤调节剂、粘合剂等其他用途,提高产品经济价值。
35.本发明所述方法将工业副产石膏与碳材料进行化浆混合,减少了石膏干燥和粉料均化过程,并专以分解石膏为目标,煅烧易于控制,改变反应气氛,降低了分解反应温度,即,将现有技术中分解反应温度从1350℃以上降至 1000-1200℃;值得说明的是,滤饼在高温烟气下进行的还原反应,主要还原剂为化浆混合中引入的碳材料,而燃料与助燃气进行燃烧产生的高温烟气中的氢气等还原性气体也起到辅助的还原性作用。
36.值得说明的是,本发明所述方法中步骤(2)所述还原热解优选在回转煅烧窑中进行,破碎后的滤饼在回转煅烧窑的固体入口进入,并且同燃料与助燃气进行燃烧产生的高温烟气逆流接触,先被干燥脱水,后在高温烟气下进行还原热解,使得工业副产石膏中的硫酸钙与碳材料中的碳反应生成氧化钙和二氧化硫、二氧化碳,得到热解气体和硅钙基料;;进一步地,直接利用助燃气入口通入一股水蒸汽,增加回转煅烧窑中水蒸汽的量,通过控制水蒸汽的量来间接增加回转煅烧窑中氢气的含量。
37.作为本发明优选的技术方案,步骤(1)所述工业副产石膏包括磷石膏和/ 或脱硫石膏。
38.优选地,步骤(1)所述工业副产石膏的硫酸钙含量为60-75wt%,例如60wt%、 63wt%、65wt%、68wt%、70wt%、72wt%或75wt%等,二氧化硅含量为2-15wt%,例如2wt%、5wt%、8wt%、10wt%、11wt%、13wt%或15wt%等,但并不仅限于所列举的数值,上述数值范围内其他未列举的数值同样适用。
39.优选地,步骤(1)所述碳材料包括焦炭。
40.优选地,步骤(1)所述碳材料的粒径为100-200目,例如100目、120目、 140目、150目、170目或200目等,但并不仅限于所列举的数值,上述数值范围内其他未列举的数值同样适用。
41.优选地,步骤(1)所述碳材料的固定碳含量≥80wt%,二氧化硅含量≤8wt%。
42.优选地,在步骤(1)中,所述工业副产石膏中的硫酸钙与所述碳材料的质量比为10:(1-2),例如10:1、10:1.2、10:1.5、10:1.7、10:1.9或10:2(即,5:1) 等,但并不仅限于所列举的数值,上述数值范围内其他未列举的数值同样适用。
43.优选地,在步骤(1)中,所述工业副产石膏与所述洗涤水的质量比为1:(2-3),例如1:2、1:2.1、1:2.3、1:2.5、1:2.7、1:2.8或1:3等,但并不仅限于所列举的数值,上述数值范围内其他未列举的数值同样适用。
44.优选地,步骤(1)所述混合的搅拌时间为30-60min,例如30min、35min、 40min、45min、50min、55min或60min等,但并不仅限于所列举的数值,上述数值范围内其他未列举的数值同样适用。
45.优选地,将步骤(1)得到的滤液作为所述洗涤水进行循环利用,得到的滤液既可以直接循环利用,又可以回收滤液中的磷等无机盐后再循环利用。
46.作为本发明优选的技术方案,步骤(2)所述助燃气的温度为150-200℃,例如150℃、160℃、170℃、180℃、190℃或200℃等,但并不仅限于所列举的数值,上述数值范围内其他未列举的数值同样适用。
47.优选地,步骤(2)所述助燃气中水蒸汽含量为10-20wt%,例如10wt%、 11wt%、13wt%、15wt%、17wt%、19wt%或20wt%等,但并不仅限于所列举的数值,上述数值范围内其他未列举的数值同样适用。
48.本发明所述方法通过在助燃气中直接通入一股水蒸汽,优选0.5mpa的水蒸汽,并控制助燃气中水蒸汽含量为10-20wt%,可以增加干燥分解反应器中水蒸汽的量,进而间接增加干燥分解反应器中氢气的量;并且,反应器中氢气的量一般控制在0.1-0.5%。
49.优选地,步骤(2)所述燃料包括固体燃料、液体燃料或气体燃料中的任意一种或至少两种的组合。
50.优选地,所述固体燃料包括煤粉。
51.优选地,所述液体燃料包括甲醇和/或柴油。
52.优选地,所述气体燃料包括煤气、天然气或液化气中的任意一种或至少两种的组合。
53.值得说明的是,本发明步骤(2)所述燃料优选为煤粉,可以大大降低成本。
54.优选地,步骤(2)所述燃料与助燃气的燃烧温度为1400-1500℃,例如1400℃、1420℃、1450℃、1460℃、1480℃或1500℃等,但并不仅限于所列举的数值,上述数值范围内其他未列举的数值同样适用。
55.优选地,步骤(2)所述还原热解的温度为1000-1200℃,例如1000℃、1050℃、 1100℃、1150℃或1200℃等,但并不仅限于所列举的数值,上述数值范围内其他未列举的数值同样适用。
56.优选地,步骤(2)所述还原热解的反应停留时间为60-90min,例如60min、 65min、70min、75min、80min、85min或90min等,但并不仅限于所列举的数值,上述数值范围内其他未列举的数值同样适用。
57.值得说明的是,本发明所述方法中燃料与助燃气在1400-1500℃下进行燃烧,产生的1400-1500℃高温烟气为破碎后的滤饼接触换热,使得滤饼中的硫酸钙与碳在1000-1200℃下还原热解,控制反应停留时间为60-90min,反应生成氧化钙和二氧化硫、二氧化碳,进
而得到热解气体和硅钙基料。
58.优选地,步骤(2)所述热解气体的so2含量为6-12wt%,例如6wt%、6.5wt%、 7wt%、8wt%、8.5wt%、9wt%、9.5wt%、10wt%、11wt%或12wt%等,但并不仅限于所列举的数值,上述数值范围内其他未列举的数值同样适用。
59.优选地,步骤(2)所述硅钙基料的氧化钙含量为65-85wt%,例如65wt%、 70wt%、75wt%、80wt%或85wt%等,二氧化硅含量为10-30wt%,例如10wt%、 15wt%、20wt%、25wt%或30wt%等,硫酸根含量≤1wt%,但并不仅限于所列举的数值,上述数值范围内其他未列举的数值同样适用。
60.作为本发明优选的技术方案,所述方法包括如下步骤:
61.(1)化浆混合:将工业副产石膏与碳材料、洗涤水搅拌30-60min进行化浆混合,控制所述工业副产石膏中的硫酸钙与所述碳材料的质量比为10:(1-2),并且控制所述工业副产石膏与所述洗涤水的质量比为1:(2-3),经固液分离得到滤饼和滤液;
62.其中,所述工业副产石膏包括磷石膏和/或脱硫石膏;所述工业副产石膏的硫酸钙含量为60-75wt%,二氧化硅含量为2-15wt%;所述碳材料包括粒径为 100-200目的焦炭;所述碳材料的固定碳含量≥80wt%,二氧化硅含量≤8wt%;将得到的滤液作为所述洗涤水进行循环利用;
63.(2)将步骤(1)得到的滤饼破碎后,在燃料与助燃气的燃烧供热下进行还原热解,所述还原热解的温度为1000-1200℃,反应停留时间为60-90min,得到热解气体和硅钙基料;
64.其中,所述燃料与助燃气在1400-1500℃下进行燃烧,产生的1400-1500℃高温烟气为破碎后的滤饼接触换热;所述助燃气的温度为150-200℃,所述助燃气中水蒸汽含量为10-20wt%;所述热解气体的so2含量为6-12wt%;所述硅钙基料的氧化钙含量为65-85wt%,二氧化硅含量为10-30wt%,硫酸根含量≤1wt%;
65.(3)将步骤(2)得到的热解气体经氧化和吸收后制得硫酸。
66.与现有技术方案相比,本发明至少具有以下有益效果:
67.(1)本发明所述装置利用浆料混合的方式,实现工业副产石膏与碳材料的均匀混合,更利于后续还原分解的进行,并且混合原料中并未加入粘土等制备水泥熟料所需的原料,设备极为简单,省略了工业副产石膏的干燥系统、物料均化装置(固固混合装置)等,减少了均质化设备,大幅度简化了反应原料的处置流程;
68.(2)本发明所述装置仅仅设置了一个干燥分解反应器,将工业副产石膏的干燥与煅烧分解有机耦合,减少了工业副产石膏制备硫酸联产水泥熟料设置的 4-6级预热器,进一步简化了装置;
69.(3)本发明所述装置与方法将工业副产石膏与碳材料进行化浆混合,减少了石膏干燥和粉料均化过程,并专以分解石膏为目标,煅烧易于控制,改变反应气氛,降低了分解反应温度;
70.(4)本发明所述装置与方法的制备产物为硅钙基料,替代了现有技术中的水泥熟料,使得对反应器的控制从必须保证石膏分解率和水泥熟料烧成率的双重指标,降低为仅仅控制石膏分解率一个指标,控制难度大幅度减低;而且,得到的硅钙基料不仅可以用于生产减碳型水泥熟料,还可以用于酸性土壤调节剂、粘合剂等其他用途,提高产品经济价值;
71.(5)本发明所述装置与方法创造性地将水蒸汽通入干燥分解反应器中,通过改变反应器的反应气氛中水蒸汽的含量,提高了反应器中氢气浓度,从而大幅度降低反应温度并提高分解速率。
附图说明
72.图1是本发明实施例1所述工业副产石膏制备硅钙基料与硫酸的装置的示意图;
73.图2是本发明应用例1所述工业副产石膏制备硅钙基料与硫酸的方法的流程图;
74.图中:1-碳材料粉碎机;2-化浆混合器;3-化浆混合泵;4-固液分离器;5
‑ꢀ
滤饼破碎器;6-滤饼提升机;7-反应进料器;8-干燥分解反应器;9-助燃风机; 10-冷却机;11-旋风除尘器;12-静电除尘器;13-烟气引风机;14-湿式除尘器;15-气体干燥塔;16-so2转化器;17-硫酸吸收塔。
具体实施方式
75.下面结合附图并通过具体实施方式来进一步说明本发明的技术方案。
76.为更好地说明本发明,便于理解本发明的技术方案,本发明的典型但非限制性的实施例如下:
77.实施例1
78.本实施例提供了一种工业副产石膏制备硅钙基料与硫酸的装置,如图1所示,所述装置包括依次连接的化浆混合器2、固液分离器4、滤饼破碎器5、干燥分解反应器8;
79.其中,在所述化浆混合器2上设置碳材料入口、石膏入口、洗涤水入口以及浆料出口,所述浆料出口与所述固液分离器4的入口相连接,在所述化浆混合器与所述固液分离器4之间的管路上设置化浆混合泵2;在所述碳材料入口处设置碳材料粉碎机1;所述固液分离器4的固体出口与所述滤饼破碎器5的入口相连接;在所述化浆混合器2上设置循环水入口,所述固液分离器4的液体出口与所述循环水相连接;所述固液分离器4包括混合过滤机;
80.在所述干燥分解反应器8的入口处设置反应进料器7,通过滤饼提升机6实现滤饼破碎器5与反应进料器7之间的连接;所述干燥分解反应器8包括石膏分解窑,所述石膏分解窑为回转煅烧窑;
81.所述干燥分解反应器8的固体出口与硅钙基料收集器(未示出)的入口相连接;在所述干燥分解反应器8设置燃料入口与助燃气入口;在所述干燥分解反应器8与所述硅钙基料收集器之间设置冷却机10,在所述冷却机10上开设固体冷却入口、固体冷却出口、冷却气体入口与冷却气体出口,所述固体冷却入口与所述干燥分解反应器8的固体出口相连接,所述固体冷却出口与所述硅钙基料收集器的入口相连接,所述冷却气体出口与所述干燥分解反应器8的助燃气入口相连接;在所述冷却机的冷却气体入口处设置助燃引风机9;
82.所述干燥分解反应器8的气体出口与二氧化硫制硫酸装置的气体入口相连接,所述二氧化硫制硫酸装置包括依次连接的旋风除尘器11、静电除尘器12、烟气引风机13、湿式除尘器14、气体干燥塔15、so2转化器16与硫酸吸收塔 17。
83.应用例1
84.本应用例提供了一种利用实施例1所述装置进行工业副产石膏制备硅钙基料与硫酸的方法,如图2所示,所述方法包括:
85.将工业副产石膏与破碎后的碳材料、洗涤水进行化浆混合,经固液分离得到滤饼和滤液;将得到的滤液作为化浆混合所需洗涤水进行循环利用;将滤饼破碎后,在燃料与含有水蒸汽的助燃气的燃烧供热下进行还原热解,将所得固体利用助燃空气冷却后得到硅钙基料,将所得烟气经除尘净化后,与空气混合进行so2转化,随后加水进行硫酸吸收后得到硫酸;
86.具体包括如下步骤:
87.(1)化浆混合:
88.将硫酸钙含量为60wt%、二氧化硅含量为15wt%的磷石膏1000kg,加入到化浆混合器2中;将洗涤水2000kg加入到化浆混合器2中,控制固液比为1:2;将固定碳含量≥80wt%、二氧化硅含量≤8wt%的焦炭经碳材料粉碎机1粉碎成粒径为100目的焦炭粉,取60kg焦炭粉加入到化浆混合器2中,控制磷石膏中的硫酸钙与焦炭粉的质量比为10:1;搅拌30min进行化浆混合,利用化浆混合泵3 将浆液送至固液分离器4中进行固液分离,得到滤饼和滤液;将得到的滤液作为所述洗涤水进行循环利用;
89.(2)将步骤(1)得到的滤饼利用滤饼破碎器5破碎后,经滤饼提升机6 运送至反应进料器7中,准确计量后进入干燥分解反应器8中,与1400℃的高温烟气逆流接触换热实现干燥脱水,然后在干燥分解反应器8内,破碎后的滤饼在1000℃下进行还原热解,控制反应停留时间为90min,使得破碎后的滤饼中的碳和硫酸钙反应生成氧化钙和二氧化硫、二氧化碳;将得到的固体物料导入冷却机10,与助燃风机9吹入的助燃空气进行接触换热,得到冷却至150℃的硅钙基料400kg,所述硅钙基料的氧化钙含量为65wt%,二氧化硅含量为 30wt%,硫酸根含量为0.9wt%;与固体物料在冷却机10换热后的助燃空气温度为150℃,与作为燃料的煤粉一起燃烧后喷入干燥分解反应器8的固体出口以提供热量,燃料与助燃气在1400℃下进行燃烧,产生的1400℃的高温烟气向反应进料器7流动并为破碎后的滤饼接触换热;同时,与作为燃料的煤粉一起喷入 0.5mpa的水蒸汽,水蒸汽的量为助燃空气量的10wt%,水蒸汽量的增加,改变了煅烧气氛,间接增加了氢的含量,氢含量达到0.1%,得到热解气体;
90.(3)将步骤(2)得到的热解气体在干燥分解反应器8内与进料滤饼换热后,温度为200℃,二氧化硫含量为6wt%,先依次经过旋风除尘器11、静电除尘器12、烟气引风机13、湿式除尘器14进行除尘净化,再进入气体干燥塔15 进行脱水干燥,随后进入so2转化器16将so2转化为so3,最后进入硫酸吸收塔17利用水进行吸收,得到98wt%硫酸430kg,尾气达标放空。
91.应用例2
92.本应用例提供了一种利用实施例1所述装置进行工业副产石膏制备硅钙基料与硫酸的方法,具体包括如下步骤:
93.(1)化浆混合:
94.将硫酸钙含量为65wt%、二氧化硅含量为12wt%的磷石膏1000kg,加入到化浆混合器2中;将洗涤水2200kg加入到化浆混合器2中,控制固液比为1:2.2;将固定碳含量≥80wt%、二氧化硅含量≤8wt%的焦炭经碳材料粉碎机1粉碎成粒径为120目的焦炭粉,取78kg焦炭粉加入到化浆混合器2中,控制磷石膏中的硫酸钙与焦炭粉的质量比为10:1.2;搅拌40min进行化浆混合,利用化浆混合泵 3将浆液送至固液分离器4中进行固液分离,得到
滤饼和滤液;将得到的滤液作为所述洗涤水进行循环利用;
95.(2)将步骤(1)得到的滤饼利用滤饼破碎器5破碎后,经滤饼提升机6 运送至反应进料器7中,准确计量后进入干燥分解反应器8中,与1420℃的高温烟气逆流接触换热实现干燥脱水,然后在干燥分解反应器8内,破碎后的滤饼在1050℃下进行还原热解,控制反应停留时间为80min,使得破碎后的滤饼中的碳和硫酸钙反应生成氧化钙和二氧化硫、二氧化碳;将得到的固体物料导入冷却机10,与助燃风机9吹入的助燃空气进行接触换热,得到冷却至160℃的硅钙基料390kg,所述硅钙基料的氧化钙含量为70wt%,二氧化硅含量为 25wt%,硫酸根含量为0.8wt%;与固体物料在冷却机10换热后的助燃空气温度为160℃,与作为燃料的煤粉一起燃烧后喷入干燥分解反应器8的固体出口以提供热量,燃料与助燃气在1420℃下进行燃烧,产生的1420℃的高温烟气向反应进料器7流动并为破碎后的滤饼接触换热;同时,与作为燃料的煤粉一起喷入 0.5mpa的水蒸汽,水蒸汽的量为助燃空气量的14wt%,水蒸汽量的增加,改变了煅烧气氛,间接增加了氢的含量,氢含量达到0.2%,得到热解气体;
96.(3)将步骤(2)得到的热解气体在干燥分解反应器8内与进料滤饼换热后,温度为220℃,二氧化硫含量为8wt%,先依次经过旋风除尘器11、静电除尘器12、烟气引风机13、湿式除尘器14进行除尘净化,再进入气体干燥塔15 进行脱水干燥,随后进入so2转化器16将so2转化为so3,最后进入硫酸吸收塔17利用水进行吸收,得到98wt%硫酸460kg,尾气达标放空。
97.应用例3
98.本应用例提供了一种利用实施例1所述装置进行工业副产石膏制备硅钙基料与硫酸的方法,具体包括如下步骤:
99.(1)化浆混合:
100.将硫酸钙含量为70wt%、二氧化硅含量为8wt%的磷石膏1000kg,加入到化浆混合器2中;将洗涤水2600kg加入到化浆混合器2中,控制固液比为1:2.6;将固定碳含量≥80wt%、二氧化硅含量≤8wt%的焦炭经碳材料粉碎机1粉碎成粒径为160目的焦炭粉,取112kg焦炭粉加入到化浆混合器2中,控制磷石膏中的硫酸钙与焦炭粉的质量比为10:1.6;搅拌50min进行化浆混合,利用化浆混合泵3将浆液送至固液分离器4中进行固液分离,得到滤饼和滤液;将得到的滤液作为所述洗涤水进行循环利用;
101.(2)将步骤(1)得到的滤饼利用滤饼破碎器5破碎后,经滤饼提升机6 运送至反应进料器7中,准确计量后进入干燥分解反应器8中,与1460℃的高温烟气逆流接触换热实现干燥脱水,然后在干燥分解反应器8内,破碎后的滤饼在1100℃下进行还原热解,控制反应停留时间为75min,使得破碎后的滤饼中的碳和硫酸钙反应生成氧化钙和二氧化硫、二氧化碳;将得到的固体物料导入冷却机10,与助燃风机9吹入的助燃空气进行接触换热,得到冷却至180℃的硅钙基料370kg,所述硅钙基料的氧化钙含量为75wt%,二氧化硅含量为 15wt%,硫酸根含量为0.6wt%;与固体物料在冷却机10换热后的助燃空气温度为180℃,与作为燃料的煤粉一起燃烧后喷入干燥分解反应器8的固体出口以提供热量,燃料与助燃气在1460℃下进行燃烧,产生的1460℃的高温烟气向反应进料器7流动并为破碎后的滤饼接触换热;同时,与作为燃料的煤粉一起喷入 0.5mpa的水蒸汽,水蒸汽的量为助燃空气量的16wt%,水蒸汽量的增加,改变了煅烧气氛,间接增加了氢的含量,氢含量达到0.3%,得到
热解气体;
102.(3)将步骤(2)得到的热解气体在干燥分解反应器8内与进料滤饼换热后,温度为260℃,二氧化硫含量为10wt%,先依次经过旋风除尘器11、静电除尘器12、烟气引风机13、湿式除尘器14进行除尘净化,再进入气体干燥塔 15进行脱水干燥,随后进入so2转化器16将so2转化为so3,最后进入硫酸吸收塔17利用水进行吸收,得到98wt%硫酸500kg,尾气达标放空。
103.应用例4
104.本应用例提供了一种利用实施例1所述装置进行工业副产石膏制备硅钙基料与硫酸的方法,具体包括如下步骤:
105.(1)化浆混合:
106.将硫酸钙含量为75wt%、二氧化硅含量为4wt%的磷石膏1000kg,加入到化浆混合器2中;将洗涤水2800kg加入到化浆混合器2中,控制固液比为1:2.8;将固定碳含量≥80wt%、二氧化硅含量≤8wt%的焦炭经碳材料粉碎机1粉碎成粒径为180目的焦炭粉,取135kg焦炭粉加入到化浆混合器2中,控制磷石膏中的硫酸钙与焦炭粉的质量比为10:1.8;搅拌55min进行化浆混合,利用化浆混合泵3将浆液送至固液分离器4中进行固液分离,得到滤饼和滤液;将得到的滤液作为所述洗涤水进行循环利用;
107.(2)将步骤(1)得到的滤饼利用滤饼破碎器5破碎后,经滤饼提升机6 运送至反应进料器7中,准确计量后进入干燥分解反应器8中,与1480℃的高温烟气逆流接触换热实现干燥脱水,然后在干燥分解反应器8内,破碎后的滤饼在1150℃下进行还原热解,控制反应停留时间为70min,使得破碎后的滤饼中的碳和硫酸钙反应生成氧化钙和二氧化硫、二氧化碳;将得到的固体物料导入冷却机10,与助燃风机9吹入的助燃空气进行接触换热,得到冷却至190℃的硅钙基料350kg,所述硅钙基料的氧化钙含量为80wt%,二氧化硅含量为 10wt%,硫酸根含量为0.5wt%;与固体物料在冷却机10换热后的助燃空气温度为190℃,与作为燃料的煤粉一起燃烧后喷入干燥分解反应器8的固体出口以提供热量,燃料与助燃气在1480℃下进行燃烧,产生的1480℃的高温烟气向反应进料器7流动并为破碎后的滤饼接触换热;同时,与作为燃料的煤粉一起喷入 0.5mpa的水蒸汽,水蒸汽的量为助燃空气量的18wt%,水蒸汽量的增加,改变了煅烧气氛,间接增加了氢的含量,氢含量达到0.4%,得到热解气体;
108.(3)将步骤(2)得到的热解气体在干燥分解反应器8内与进料滤饼换热后,温度为280℃,二氧化硫含量为11wt%,先依次经过旋风除尘器11、静电除尘器12、烟气引风机13、湿式除尘器14进行除尘净化,再进入气体干燥塔 15进行脱水干燥,随后进入so2转化器16将so2转化为so3,最后进入硫酸吸收塔17利用水进行吸收,得到98wt%硫酸550kg,尾气达标放空。
109.应用例5
110.本应用例提供了一种利用实施例1所述装置进行工业副产石膏制备硅钙基料与硫酸的方法,具体包括如下步骤:
111.(1)化浆混合:
112.将硫酸钙含量为75wt%、二氧化硅含量为2wt%的磷石膏1000kg,加入到化浆混合器2中;将洗涤水3000kg加入到化浆混合器2中,控制固液比为1:3;将固定碳含量≥80wt%、
二氧化硅含量≤8wt%的焦炭经碳材料粉碎机1粉碎成粒径为200目的焦炭粉,取150kg焦炭粉加入到化浆混合器2中,控制磷石膏中的硫酸钙与焦炭粉的质量比为10:2,即,5:1;搅拌60min进行化浆混合,利用化浆混合泵3将浆液送至固液分离器4中进行固液分离,得到滤饼和滤液;将得到的滤液作为所述洗涤水进行循环利用;
113.(2)将步骤(1)得到的滤饼利用滤饼破碎器5破碎后,经滤饼提升机6 运送至反应进料器7中,准确计量后进入干燥分解反应器8中,与1500℃的高温烟气逆流接触换热实现干燥脱水,然后在干燥分解反应器8内,破碎后的滤饼在1200℃下进行还原热解,控制反应停留时间为60min,使得破碎后的滤饼中的碳和硫酸钙反应生成氧化钙和二氧化硫、二氧化碳;将得到的固体物料导入冷却机10,与助燃风机9吹入的助燃空气进行接触换热,得到冷却至200℃的硅钙基料330kg,所述硅钙基料的氧化钙含量为85wt%,二氧化硅含量为 10wt%,硫酸根含量为0.4wt%;与固体物料在冷却机10换热后的助燃空气温度为200℃,与作为燃料的煤粉一起燃烧后喷入干燥分解反应器8的固体出口以提供热量,燃料与助燃气在1500℃下进行燃烧,产生的1500℃的高温烟气向反应进料器7流动并为破碎后的滤饼接触换热;同时,与作为燃料的煤粉一起喷入0.5mpa的水蒸汽,水蒸汽的量为助燃空气量的20wt%,水蒸汽量的增加,改变了煅烧气氛,间接增加了氢的含量,氢含量达到0.5%,得到热解气体;
114.(3)将步骤(2)得到的热解气体在干燥分解反应器8内与进料滤饼换热后,温度为300℃,二氧化硫含量为12wt%,先依次经过旋风除尘器11、静电除尘器12、烟气引风机13、湿式除尘器14进行除尘净化,再进入气体干燥塔 15进行脱水干燥,随后进入so2转化器16将so2转化为so3,最后进入硫酸吸收塔17利用水进行吸收,得到98wt%硫酸550kg,尾气达标放空。
115.计算上述应用例1-5的石膏分解率,即,硫酸钙热分解率,汇总在表1中。
116.表1
117.项目应用例1应用例2应用例3应用例4应用例5石膏分解率98.5%99.1%99.3%99.5%99.7%
118.综上所述,本发明所述装置及方法利用浆料混合的方式,实现工业副产石膏与碳材料的均匀混合,并且混合原料中并未加入粘土等制备水泥熟料所需的原料,设备极为简单,省略了工业副产石膏的干燥系统、物料均化装置等,大幅度简化了反应原料的处置流程;本发明所述装置仅仅设置了一个干燥分解反应器,将工业副产石膏的干燥与煅烧分解有机耦合,减少了工业副产石膏制备硫酸联产水泥熟料设置的4-6级预热器,进一步简化了装置;本发明所述装置与方法的制备产物为硅钙基料,替代了现有技术中的水泥熟料,使得对反应器的控制从必须保证石膏分解率和水泥熟料烧成率的双重指标,降低为仅仅控制石膏分解率一个指标,控制难度大幅度减低;而且,得到的硅钙基料不仅可以用于生产减碳型水泥熟料,还可以用于酸性土壤调节剂、粘合剂等其他用途,提高产品经济价值;本发明所述装置与方法创造性地将水蒸汽通入干燥分解反应器中,通过改变反应器的反应气氛中水蒸汽的含量,提高了反应器中氢气浓度,从而大幅度降低反应温度并提高分解速率。
119.本发明通过上述实施例来说明本发明的详细结构特征,但本发明并不局限于上述详细结构特征,即不意味着本发明必须依赖上述详细结构特征才能实施。所属技术领域的技术人员应该明了,对本发明的任何改进,对本发明所选用部件的等效替换以及辅助部件
的增加、具体方式的选择等,均落在本发明的保护范围和公开范围之内。
120.以上详细描述了本发明的优选实施方式,但是,本发明并不限于上述实施方式中的具体细节,在本发明的技术构思范围内,可以对本发明的技术方案进行多种简单变型,这些简单变型均属于本发明的保护范围。
121.另外需要说明的是,在上述具体实施方式中所描述的各个具体技术特征,在不矛盾的情况下,可以通过任何合适的方式进行组合,为了避免不必要的重复,本发明对各种可能的组合方式不再另行说明。
122.此外,本发明的各种不同的实施方式之间也可以进行任意组合,只要其不违背本发明的思想,其同样应当视为本发明所公开的内容。