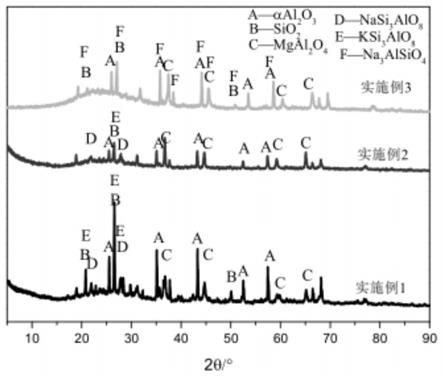
1.本发明涉及一种多孔陶瓷材料的制备方法,具体涉及一种以铝灰为主要原料,搭配垃圾焚烧飞灰和残渣以及电镀污泥等危险废物共同烧制制备多孔陶瓷材料的方法及多孔陶瓷材料,属于固体废物资源化利用技术领域。
背景技术:2.铝灰是铝工业产生的一种危险废物,《国家危废名录(2021年版)》规定铝灰危废代码为hw48,包括321-023-48~321-026-48及321-034-48,其危险特性主要为毒性(toxicity,t)及反应性(reactivity,r)。原因在于铝灰中含有含量较高的如锌(zn)、铅(pb)、砷(as)、汞(hg)、铜(cu)、铬(cr)等重金属以及氟(f)、氯(cl)等卤素,上述因子可污染水体及土壤,危害人畜健康;同时,其主要成分包括al、aln、al4c3和al2s3与水或潮湿的空气接触会迅速反应生成h2、nh3、ch4和h2s等有毒有害和易燃性气体而具有较强的危险性。中国每年铝灰的产生量已达400万吨,且90%以上的铝灰采用粗放的填埋与堆存方式进行处置,《国家危废名录(2021年版)》的实施,铝灰的出路问题成为了铝灰产生企业的头等难题,部分大型铝灰产生企业已出现铝灰爆仓现象,严重影响及制约企业的正常生产。此外,铝灰中金属铝含量为5wt.~20wt.%,氧化铝含量为20wt.~50wt.%,具有良好的回用价值,如果作为固体废弃物处理,会造成极大的资源浪费。
3.现有铝灰综合利用技术主要集中于对一次铝灰中金属铝的回收。提铝后的二次铝灰只有少部分做到了无害化与资源化利用,主要包括用传统的“湿法”工艺制备聚合氯化铝(净水剂)以及“火法”工艺制备如水泥,炼钢脱硫剂(铝酸钙) 等。但湿法处理铝灰工艺存在产生有毒有害和易燃性气体造成安全隐患。铝灰水泥窑协同处置可以对铝灰中有害物质进行高温氧化分解、固溶等,但水泥熟料中 cl-含量应满足≤0.06%,na和k含量(碱含量)应满足r2o≤0.6%,铝灰中f、cl、na和钾含量较高,若采用该方法,铝灰掺量极低,无法实现大规模综合利用;采用铝灰替代高铝矾土生产铝酸钙,可有效降低铝酸钙生产成本,但该工艺需在1400℃下进行,且高温所产生煅烧过程污染较重,包括颗粒物、氟化物、氮氧化物等,若处置不当易造成设备腐蚀,引发环境污染。
4.焚烧处置残渣(hw18)是焚烧炉尾气处理过程中所产生固体废物,包括生活垃圾焚烧、危险废物焚烧所产生的残渣,目前主要以无害化后填埋的方式处置。但因焚烧处置残渣具有较高的重金属浸出毒性以及一定量的二噁英等有毒污染物,采用固化稳定化的填埋方式,其赋存的有毒有害物质可能发生迁移转化,对生态环境造成潜在威胁。少部分生活垃圾焚烧飞灰的资源化利用主要集中于制备陶粒,并实现了工业化生产。其他如危险废物焚烧处置产生的残渣目前尚未得到合理化的处置利用。
技术实现要素:5.针对现有技术对铝灰处理方法存在的缺陷,本发明的目的是在于提供一种将二次铝灰搭配焚烧处置飞灰、焚烧处置炉渣、电镀污泥及含硅固废等固废经过一步高温固相反
应制备多孔陶瓷材料的方法,该方法操作简单,制备过程无水参与,规避了铝灰遇水反应释放有害气体,且原料全部采用固废,无需额外添加商品化学试剂,成本低廉,且制备的多孔陶瓷材料容重小,强度高,对重金属固化效果好,无二次污染。
6.本发明的第二个目的是在于提供一种容重小、强度高,对重金属固化效果好的铝灰基多孔陶瓷材料。
7.为了实现上述技术目的,本发明提供了一种铝灰基多孔陶瓷材料的制备方法,该方法是将包含二次铝灰、焚烧处置飞灰、焚烧处置炉渣、电镀污泥及含硅固废在内的原料依次经过混合球磨、高压干法成型和烧制,得到铝灰基多孔陶瓷材料。
8.本发明技术方案通过各种危险固废和普通固废之间的协同配伍,在无需外加商品化助剂的条件下即可完成多孔陶瓷材料的制备,实现了各种固废的资源化利用,降低了多孔陶瓷材料的生产成本。本发明技术方案在多孔陶瓷材料制备过程中采用的是干法成型,避免了铝灰遇水反应所带来的环境危害及生产安全隐患,且在高温固相反应过程中不但完成各种固废的解毒,且利用高温下释放的小分子进行发泡,无需额外发泡剂,高温固相反应生成的陶瓷相能将各种重金属固封,防止二次污染,特别是制备的多孔陶瓷的容重小,强度高,满足应用要求。
9.作为一个优选的方案,所述原料包括以下质量百分比组分:二次铝灰20~45%,焚烧处置飞灰5~20%,焚烧处置炉渣10~20wt%,电镀污泥2~6wt%、含硅固废 9~63wt%,以总质量为100%计量。本发明铝灰基多孔陶瓷材料制备过程中各组分的合理配伍对于铝灰基多孔陶瓷材料的制备是十分重要的,原料之间的合理配伍,既可保证陶瓷矿物相的生成,又可保证在低能耗下实现矿物相重构,且还可保证多孔陶瓷产品具有完整的力学支撑骨架、均一的孔结构及满足标准要求的容重。二次铝灰和焚烧处置炉渣的含量对多孔陶瓷材料的生成影响较大,如二次铝灰含量低于20%,则陶瓷矿物相无法生成,二次铝灰含量高于45%时,陶瓷矿物相中主要为氧化铝结构,同样无法获得多孔陶瓷产品。另外,焚烧处置飞灰含量高于20%时,配伍中碱金属含量过高,共熔点温度低,会出现发泡量大,陶瓷骨架结构坍塌,产物挂壁严重等情况,焚烧飞灰含量低于5%,配伍中碱金属含量过低,在烧成制度下,坯料发泡量小,使陶瓷材料孔隙小,出现闭孔等现象,且烧成温度需要提高;焚烧处置炉渣含量高于20%,配伍中sio2含量过高,材料的烧成温度过高,产品烧成能耗大幅增加,焚烧处置炉渣含量低于10%时,陶瓷材料的骨架所需的sio2不足,产品硬度不够。电镀污泥含量对陶瓷矿相重构气孔均一性也存在较大影响,电镀污泥含量由2%增加至6%时,发泡陶瓷在冷却阶段逐渐产生析晶行为,产品孔隙均匀性改善,气孔圆形度增加,电镀污泥含量大于6%时,发泡陶瓷孔结构在高温下快速形成大量的液相,导致气孔孔径增大,气孔稳定性减弱。
10.作为一个优选的方案,所述二次铝灰为321-023-48~321-026-48、321-034-48 中至少一种。优选的二次铝灰为单质铝含量低于5%的二次铝灰,这部分铝灰对于单质铝的回收价值不大,而满足本发明多孔陶瓷材料的制备要求。
11.作为一个优选的方案,所述焚烧处置飞灰为hw18焚烧处置飞灰。进一步优选的烧处置飞灰为772-002-18和772-004-18中至少一种。焚烧处置飞灰占原料质量的5~20%
12.作为一个优选的方案,所述焚烧处置残渣为hw18焚烧处置残渣。进一步优选的焚烧处置炉渣为772-003-18和772-005-18中至少一种。焚烧处置飞灰占原料质量的10~
20%。
13.作为一个优选的方案,所述电镀污泥为hw17表面处理废物。优选的电镀污泥有利于改善多孔陶瓷的孔结构。进一步优选,电镀污泥占原料质量的3~5%。
14.作为一个优选的方案,所述含硅固废为玻璃行业、半导体或太阳能行业产生的含硅固体废物。优选的含硅固废为一般固废,主要提供硅源。
15.作为一个优选的方案,所述原料还包含hw08废矿物油和/或含矿物油废物作为粘结剂。优选hw08废矿物油和/或含矿物油废物作为粘结剂可以避免二次铝灰遇水释放有害气体,同时有利于各种固废原料的粘结成型。
16.作为一个优选的方案,所述粘结剂质量为原料质量的1~7%。
17.作为一个优选的方案,所述球磨的条件为:球料比为3:1~6:1,球磨转速为 200~400rpm,球磨时间为10~25min。通过球磨可以实现固废原料的表面活化,有利于后续的高温固相反应,同时可以将各种固废原料的均混,以获得孔结构越均一,容重可控的多孔陶瓷产品。
18.作为一个优选的方案,所述高压干法成型的条件为:压铸压强为5~15mpa,压铸时间为2~6min。
19.作为一个优选的方案,所述烧制的条件为:温度为1150~1220℃,时间为 30~90min。烧制过程的条件控制也是影响多孔陶瓷材料产品性能的关键,烧制温度过高会导致液相产生过多,无法维持坯料成型时的形貌及形成均一的孔径结构,温度过低则液相形成量少,矿物相重构不彻底,孔结构形成少,材料容重高。所述烧制的条件进一步优选为:温度为1160~1200℃,时间为30~60min。
20.作为一个优选的方案,所述烧制过程中,在1000℃以下的升温速率控制在 8~12℃/min,达到1000℃是升温速率控制在3~5℃/min。在1000℃以下,保持较快的升温速率,多孔陶瓷膨胀量更大,孔隙结构更均匀。作为更进一步的优选,所述升温过程1000℃以下升温速率为10~12℃/min。
21.作为一个优选的方案,烧制完成后,冷却温度为5~20℃/min。
22.作为一个优选的方案,混合方式采用机械搅拌,机械搅拌时间为10~25min。
23.作为一个优选的方案,球磨后的原料可以进一步进行震荡处理,提高物料的均匀性,震荡时间为15~30min。
24.本发明还提供了一种铝灰基多孔陶瓷材料,其由所述的制备方法得到。
25.相对现有技术,本发明技术方案带来的有益技术效果:
26.本发明提供了一种铝灰协同焚烧处置飞灰和炉渣、电镀污泥等危险废物及其他一般固体废物来制备铝灰基多孔陶瓷材料的新方法,其创新地基于危险废物及一般工体废物的原料特征,进行合理配伍,铝灰中的al、aln、al4c3等具有反应性的活性物质在焙烧过程中转化为al2o3,进而与焚烧处置残渣和其他一般固废中的sio2和铝灰主体的al2o3一起构成多孔陶瓷的基本骨架,焚烧处置残渣中的na2o,k2o等碱土金属作为焙烧的助熔组分,可在焙烧过程中降低熔点,产生液相,促进矿物之间的反应进行,且铝灰及其他固废中高温中产生的小分子用于多孔陶瓷膨胀发泡,降低产品的密度,提高产品性能。
27.1、本发明的铝灰基多孔陶瓷材料制备过程中固废原料采用的干法成型,充分避免了铝灰与水接触产生有毒危险气体的特性,既完成了生料均化,又确保了整个制备过程安
全性;
28.2、本发明的铝灰基多孔陶瓷材料制备过程中各固废原料配伍设计合理,在无需使用化学添加助剂的条件下,可使多源固体废物在较低温度下(1150~1200℃) 就能实现矿物相重构,减小能源消耗;
29.3、本发明的铝灰基多孔陶瓷材料制备过程中在高温反应条件下,铝灰中的含量较多的aln发生焙烧氧化还原反应,产生的气体可大部分向无毒无害气体 n2转化,其他微量的具有遇水反应性的活性物质如al4c3和al2s3等也在烧制过程中消除了反应性危害,同时无需额外加入使用常规方法制备发泡陶瓷时所加的如sic等昂贵发泡剂,节约生产成本;
30.4、本发明的铝灰基多孔陶瓷材料制备过程中,铝灰、焚烧处置残渣、电镀污泥等有毒污染因子可实现晶格固化,消除上述危险废物毒性,同时烧制温度的合理控制,可避免含f-、cl-盐升华释放而腐蚀设备;
31.5、本发明的铝灰基多孔陶瓷材料制备过程中实现了多源固体废物协同处置,所有原料均为固体废物,且掺量大,其中所有组分均可实现全量深度资源化利用,生产过程中无废水及其他新生固体废弃物产生,不会造成环境的二次危害;
32.6、本发明的铝灰基多孔陶瓷材料制备工艺适应性强,对不同来源的铝灰、焚烧处置残渣、电镀污泥等危险废物及含硅较多的一般固体废物均可实现资源化利用,突破了当前危险废物处理处置“卡脖子”技术难题,减少固体废物填埋和堆存(特别是焚烧处置残渣),缓解土地压力及环境安全隐患;同时,所得产品具有轻质高强等特点,可替代砂石料广泛应用于道路,建筑等领域,还可应用于水处理等环保领域,市场前景广阔;具有显著的环境效益与经济效益。
附图说明
33.图1为实施例1、实施例2和实施例3所得铝灰基多孔陶瓷材料的xrd图谱。
34.图2为对比例1、对比例2所得铝灰基多孔陶瓷材料的xrd图谱。
具体实施方式
35.为了更好地解释本发明的技术方案及优点,下面结合实施例,对本发明内容做进一步的详细说明。有必要在此指出的是以下实施例只用于对本发明内容作进一步说明,不能理解为对本发明权利要求的保护范围的限制,该领域的技术熟练人员根据上述本发明内容对本发明做出一些非本质的改进和调整,仍属于本发明的保护范围。
36.实施例1
37.将铝灰、焚烧处置飞灰、焚烧处置炉渣、电镀污泥、其他固废(废玻璃)按 25wt%,10wt%,12wt%、6wt%,47wt%的比例(以烘干后的固体物质计,危废原料主要化学组成如表1所示),外掺5%废矿物油置入球磨机中,按照球料比4:1,球磨20min。将粉磨所得粉体在压铸强度7mpa,压铸时间3min压铸成型。将成型后的坯料置入高温炉,按照升温速率8℃/min升温至1000℃,再按5℃ /min升温至1150℃,烧制30min后,以10℃/min冷却至室温,得到铝灰基多孔陶瓷材料。
38.表1危废原料主要化学组成
[0039][0040][0041]
所烧制的铝灰基多孔陶瓷材料体积膨胀显著,其剖面具有均匀微小的球形化泡孔结构。材料质轻高强,容重仅为0.75g/cm3,筒压强度达到5.0mpa。
[0042]
按照《hj1091-2020固体废物再生利用污染防治技术导则》6.3规定:利用固体废物生产砖瓦、轻骨料、集料、玻璃、陶瓷、陶粒、路基材料等建材过程的污染控制执行相关行业污染物排放标准,相关产品中有害物质含量参照gb30760 的要求执行。参照《水泥窑协同处置固体废物技术规范》gb30760-2014和《轻集料及其试验方法第2部分轻集料》gb-t 17431.2-2010,产品重金属及氯含量浸出浓度如表2所示。产品中重金属及氯含量浸出浓度满足国家相关标准要求。
[0043]
表2产品重金属及氯含量浸出浓度
[0044][0045]
实施例2
[0046]
铝灰、焚烧处置飞灰、焚烧处置炉渣及电镀污泥成分参照实施例1。
[0047]
将铝灰、焚烧处置飞灰、焚烧处置炉渣、电镀污泥、其他固废(废玻璃)按 35wt%,15wt%,15wt%,5wt%,30wt%的比例(以烘干后的固体物质计),外掺6%废矿物油置入球磨机中,按照球料比5:1,球磨15min。将粉磨所得粉体在压铸强度6mpa,压铸时间2min压铸
成型。将成型后的坯料置入高温炉,按照升温速率10℃/min升温至1000℃,再按5℃/min升温至1180℃,烧制40min 后以20℃/min冷却至室温,得到铝灰基多孔陶瓷材料。
[0048]
所烧制的铝灰基多孔陶瓷材料体积膨胀显著,其剖面具有均匀微小的球形化泡孔结构。材料质轻高强,容重仅为0.65g/cm3,筒压强度达到5.5mpa。
[0049]
参照《水泥窑协同处置固体废物技术规范》gb30760-2014和《轻集料及其试验方法第2部分轻集料》gb-t 17431.2-2010,产品重金属及氯含量浸出浓度如表3所示。产品中重金属及氯含量浸出浓度满足国家相关标准要求。
[0050]
表3产品重金属及氯含量浸出浓度
[0051][0052]
实施例3
[0053]
铝灰、焚烧处置飞灰、焚烧处置炉渣及电镀污泥成分参照实施例1。
[0054]
将铝灰、焚烧飞灰、焚烧炉渣、电镀污泥、其他固废(废玻璃)按40wt%, 20wt%,20wt%,5wt%,15wt%的比例(以烘干后的固体物质计),外掺6%废矿物油置入球磨机中,按照球料比6:1,球磨10min。将粉磨所得粉体在压铸强度5mpa,压铸时间2min压铸成型。将成型后的坯料置入高温炉,按照升温速率15℃/min升温至1000℃,再按3℃/min升温至1150℃,烧制60min后以30℃ /min冷却至室温,得铝灰基多孔陶瓷材料。
[0055]
所烧制的铝灰基多孔陶瓷材料体积膨胀显著,其剖面具有均匀微小的球形化泡孔结构。材料质轻高强,容重仅为0.60g/cm3,筒压强度达到5.8mpa。
[0056]
参照《水泥窑协同处置固体废物技术规范》gb30760-2014和《轻集料及其试验方法第2部分轻集料》gb-t 17431.2-2010,产品重金属及氯含量浸出浓度如表4所示。产品中重金属及氯含量浸出浓度满足国家相关标准要求。
[0057]
表4产品重金属及氯含量浸出浓度
[0058][0059][0060]
对比例1
[0061]
铝灰、焚烧处置飞灰、焚烧处置炉渣及电镀污泥成分参照实施例1。
[0062]
将铝灰、焚烧飞灰、焚烧炉渣、电镀污泥、其他固废(废玻璃)按50wt%, 25wt%,
10wt%,7wt%,8wt%的比例(以烘干后的固体物质计),外掺5%废矿物油置入球磨机中,按照球料比4:1,球磨10min。将粉磨所得粉体在压铸强度7mpa,压铸时间3min压铸成型。将成型后的坯料置入高温炉,按照升温速率8℃/min升温至1000℃,再按5℃/min升温至1 150℃,烧制30min后以10℃/min 冷却至室温,得烧制产品。
[0063]
所烧制的铝灰基多孔陶瓷材料体积有一定膨胀,其剖面孔隙较小。材料容重为1.60g/cm3,筒压强度为4.0mpa。
[0064]
参照《水泥窑协同处置固体废物技术规范》gb30760-2014和《轻集料及其试验方法第2部分轻集料》gb-t 17431.2-2010,产品重金属及氯含量浸出浓度如表5所示。未采用本发明提供的原料配伍设计,产品中ni、zn及cl浸出浓度均超出国家标准要求限值。
[0065]
表5产品重金属及氯含量浸出浓度
[0066][0067]
对比例2
[0068]
铝灰、焚烧处置飞灰、焚烧处置炉渣及电镀污泥成分参照实施例1。
[0069]
将铝灰、焚烧飞灰、焚烧炉渣、电镀污泥、其他固废(废玻璃)按30wt%, 3wt%,10wt%,1wt%,56wt%的比例(以烘干后的固体物质计),外掺5%废矿物油置入球磨机中,按照球料比4:1,球磨10min。将粉磨所得粉体在压铸强度7mpa,压铸时间3min压铸成型。将成型后的坯料置入高温炉,按照升温速率15℃/min升温至1000℃,再按6℃/min升温至1250℃,烧制40min后以10℃ /min冷却至室温,得产品。所烧制的铝灰基多孔陶瓷材料体积无明显膨胀,其剖面孔隙较小。材料容重为1.30g/cm3,筒压强度为2.1mpa。
[0070]
参照《水泥窑协同处置固体废物技术规范》gb30760-2014和《轻集料及其试验方法第2部分轻集料》gb-t 17431.2-2010,产品重金属及氯含量浸出浓度如表6所示。未采用本发明提供的原料配伍设计,产品中ni、zn及cl浸出浓度均超出国家标准要求限值。
[0071]
表6产品重金属及氯含量浸出浓度
[0072]