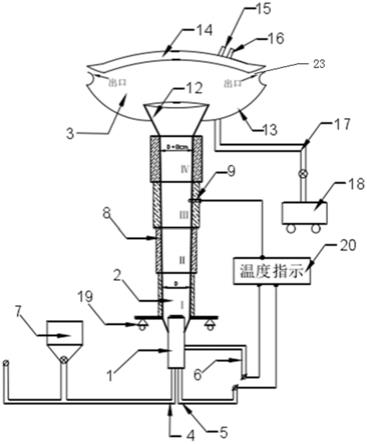
1.本实用新型涉及一种球形玻璃的制备装置,具体涉及一种大颗粒球形玻璃的制备装置。
背景技术:2.球形玻璃材料是一种具有一定粒度且完整光滑表面的球形材料,是一种新型无机硅酸盐材料。球形玻璃材料的出现,迄今已经有近百年的历史,最早大规模的生产由美国波特工业有限责任公司于20世纪40年代开始。球形玻璃质材料具有许多独特的性能,如良好的圆度、均匀度、透明度、硬度、光反射特性和优异的化学稳定性等,目前,球形玻璃材料早已经成为日常生活中不可或缺的材料,并广泛应用在航空航天、海洋、电子、医学、高速公路、汽车标识、化工等领域,在现代工业中起到非常重要的作用。
3.目前,市场上制备玻璃球形材料的方法有粉末法,熔液法,火焰漂浮法等。但其主要制备直径小于1mm的玻璃球或微球或微珠。而直径大于1mm的大颗粒球形玻璃目前主要采用二次成形工艺,该工艺是将固体玻璃质材料粉碎成合适的形状和粒径范围,然后在高温下利用材料的表面张力自动成球。例如,us3597i77介绍了一种二次成形工艺,该工艺将玻璃经过破碎到一定的粒度后,和石墨粉等混合均匀后,进入一旋转的高温窑炉中,玻璃粉和石墨粉的混合物被加热到900℃左右,再经过一定的时间,玻璃粉在表面张力的作用下成球,这时玻璃球和石墨粉经过冷却后,再进行筛分去除石墨粉,在经过对玻璃球的表面进行处理,得到合格的玻璃球。该工艺后续还要对玻璃球进行表面清洗和烘干,优点是玻璃球圆度高,缺点是,工艺复杂,成本高,玻璃球表面接触石墨表面平整度低。
技术实现要素:4.本实用新型的目的在于提供一种大颗粒球形玻璃的制备装置,利用本实用新型的制备装置所制备的玻璃球为直径大于1mm的大尺寸玻璃球,且一次成圆率达98%,表面不粘连石墨,不用二次清洗烘干,玻璃球表面光亮,微珠的硬度与抗压强度均达到国家标准,该装置生产效率高,产量大,生产时间短,并且生产投资小设备简易高效,能够在提高生产率的同时降低生产成本。
5.为达到上述目的,本实用新型的装置包括自下而上依次设置的火焰燃烧器,高温炉体和收集罩;
6.所述的火焰燃烧器侧壁上连通有氧气管道,底端连通有压缩空气管道和天然气管道,压缩空气管道还与放料漏斗相连通;
7.所述的高温炉体下端与火焰燃烧器的出口端相连通、上端出口设置有喇叭状端口,高温炉体由下向上直径逐段增大,高温炉体的中心处出插有用于测量炉管温度的热电偶,热电偶、天然气、氧气开关均与控制天然气、氧气开度的温度指示器相连;
8.所述的收集罩套装在喇叭状端口上,收集罩上部固定连接有顶盖,下端开设有收集管道。
9.所述高温炉体底部为漏斗状结构,火焰燃烧器前端约1/4长度插入高温炉体的漏斗状底部。
10.所述高温炉体由合金炉管组成,炉体高度为6~16米,炉体外部自下而上保温层分四段逐级加厚包裹,采用逐级保温,ⅰ段保温层厚度2cm,ⅱ段保温层厚度4cm,ⅲ段保温层厚度6cm,ⅳ段保温层厚度8cm。
11.所述保温层的保温材料采用硅酸铝纤维棉,且在保温层的外侧安装有厚度为1mm 的铁皮外壳。
12.所述高温炉体下端固定连接有可旋转调节炉体与地面夹角控制成球颗粒落地方向的地脚。
13.所述收集罩为锥形结构,且在收集罩与顶盖之间对称开设有两个气体出口。
14.所述顶盖为中空的不锈钢结构,且在顶盖上开设有对顶盖进行冷却降温的进水口和出水口。
15.所述放料漏斗和压缩空气管道上均安装有开关。
16.一种依据以上装置制备大颗粒球形玻璃的方法,包括以下包括:
17.首先,通过控制温度指示器,打开天然气管道开关,通入天然气后使用明火点燃,接着控制温度指示器打开氧气管道开关通入氧气,同时手动打开压缩空气管道开关通入压缩空气,通过开关闭合程度来调节空气,天然气,氧气的流量,直至火焰长度刚好冲到顶盖,待高温炉体温度达到设定的温度后保温30min,待高温炉体内部温度均匀;
18.然后,打开放料漏斗的开关,通过不锈钢钢管向压缩空气管道放入配好的玻璃料,玻璃料随压缩空气从火焰燃烧器喷入高温炉体,经过预热段,收缩段,熔融后进入收集罩,碰到顶盖后落入收集罩中;
19.最后,将收集罩中的物料经收集管道后收集到料车中,待球料冷却至室温既得到球形玻璃。
20.所述的璃料是将所需成球的玻璃料熔融后在搅拌下水淬后平铺在盘中并放入烘箱内于100℃下烘干5h,用破碎机将烘干后的水淬玻璃料进行破碎,破碎完成后将其依次过10目筛、30目筛,留下中间尺寸的水淬玻璃料。
21.相比于现有技术,本实用新型具有以下有益效果:
22.本实用新型采用气料共喷成球工艺,玻璃成球过程中,不与其他材料接触,表面光滑,不用二次处理和清洗。高温炉出口采用喇叭状火焰结构,保证了玻璃料的低温动能基础上,增加了高温段静压,使得玻璃料在充分接受加热的同时,强化了气体和固体玻璃球的高温分离。采用富氧增强燃烧火焰,增加了火焰的刚度,保证了燃烧过程的气氛,使得玻璃颜色稳定。采用了气体与炉温的联动控制技术,保证了产品质量,降低了生产成本。采用了炉体结构逐级保温技术,充分实现了高温温度不降低,低温温度不升高,同时节约了成本,增加了生产效率。顶盖采用水冷却,实现了环保的同时,充分增加了该装备的使用寿命。
23.进一步的,物料放送流量可有压缩空气的压力与放料开关的闭合来进行调节,方便根据料性控制成球量。
24.进一步的,炉体采取逐级保温,对火焰根部和高温段根据温度来包裹保温,针对性增加保温棉厚度,节省物料并确保温度不流失与对保温棉的浪费。
25.进一步的,通过调节天然气与氧气管道开关的闭合程度来控制火焰的温度,然后
使用热电偶来测量炉管内成球段的温度,并从温度指示器显示出来,这样一来可以通过联动效应方便控制成球工艺,精准调节成球温度。
26.进一步的,在后端加上一个收集罩,成球收集一体化,加大了效率,减少了人工作业,也防止了高温微珠飞溅的危险性。
27.进一步的,收集罩外部夹层增添了循环水的装置,保护了被火焰喷射的收集罩上层,并且收集罩上的出口增加火焰的虹吸效应,在成球时火焰能时刻包裹微球。
28.进一步的,整个炉体可以通过地脚进行一定的旋转,调节炉体与地面的夹角,控制成球颗粒的落地方向,方便定向收集。
29.本实用新型采用气料共喷成球工艺所生产的玻璃微球表面光滑,一次成圆率达 98%,表面不粘连石墨,不用二次清洗烘干,玻璃球表面光亮,微珠的硬度与抗压强度均达到国家标准。采用喇叭状火焰结构,保证了玻璃料的低温动能基础上,增加了高温段静压,使得玻璃料在充分接受加热的同时,强化了气体和固体玻璃球的高温分离,增加成球效率。采用富氧增强燃烧火焰,增加了火焰的刚度,保证了燃烧过程的气氛,使得玻璃颜色稳定。采用了气体与炉温的联动控制技术,保证了产品质量,降低了生产成本。采用了炉体结构逐级保温技术,充分实现了高温温度不降低,低温温度不升高,同时解决成本,增加了生产效率。顶盖采用水冷却,实现了环保的同时,充分增加了该装备的使用寿命。大颗粒微珠的生产繁琐且效率低,本实用新型设计出简易操作并效果良好的球形玻璃成球设备,最重要的是改成球设备不限于玻璃系统,可根据微球物理化学性能选择不同的系统,根据系统灵活调整工艺,生产出所需性能的大颗粒球形玻璃。
附图说明
30.图1为成球装置结构图;
31.图2为燃烧器结构图;
32.图3为炉体剖面图;
33.图4为顶盖结构图;
34.图5为火焰形状示意图。
35.其中,1-火焰燃烧器;2-高温炉体;3-收集罩;4-压缩空气管道;5-天然气管道; 6-氧气管道;7-放料漏斗;8-保温层;9-热电偶;10-保温材料;11-铁皮外壳;12
‑ꢀ
喇叭状端口;13-收集器;14-顶盖;15-进水口;16-出水口;17-收集管道;18-料车; 19-活动地脚;20-温度指示器;21-火焰;22-玻璃颗粒;23-气体出口。
具体实施方式
36.下面结合附图对本实用新型作进一步详细说明。
37.参见图1,本实用新型的装置包括自下而上依次设置的火焰燃烧器1,高温炉体 2和收集罩3;
38.参见图2,所述的火焰燃烧器1侧壁上连通有带有开关的氧气管道6,底端连通有带有开关的压缩空气管道4和天然气管道5,压缩空气管道4还与带有开关的放料漏斗7相连通;
39.所述的高温炉体2由合金炉管组成,炉体高度为6~16米(可以根据玻璃种类及玻
璃颗粒度调节),参见图3,炉体外部自下而上保温层8分四段逐级加厚包裹,采用逐级保温,ⅰ段保温层厚度2cm,ⅱ段保温层厚度4cm,ⅲ段保温层厚度6cm,ⅳ段保温层厚度8cm,保温层8的保温材料10采用硅酸铝纤维棉,且在保温层8的外侧安装有厚度为1mm的铁皮外壳11,且高温炉体2底部为漏斗状结构,火焰燃烧器1 前端约1/4长度插入高温炉体2的漏斗状底部,高温炉体2上端出口设置有喇叭状端口12,高温炉体2的中心处出插有用于测量炉管温度的热电偶9,热电偶9、天然气、氧气开关均与控制天然气、氧气开度的温度指示器20相连;该热电偶9与氧气,天然气阀门进行联动,控制炉体内的温度。
40.参见图4,所述的收集罩3为锥形结构套装在喇叭状端口12上,收集罩3上部固定连接有中空的不锈钢结构顶盖14,且在顶盖上开设有对顶盖进行冷却降温的进水口15和出水口16,在收集罩3与顶盖14之间对称开设有两个气体出口23,下端开设有收集管道17与料车18相连。
41.图5为运行过程火焰及颗粒的示意图,压缩空气带着物料高速喷入高温炉体2,成型的玻璃颗粒22随火焰21冲向顶盖14。
42.制备方法如下:
43.首先,将所需成球的玻璃料熔融后在搅拌下水淬后平铺在盘中并放入烘箱内于 100℃下烘干5h,用破碎机将烘干后的水淬玻璃料进行破碎,破碎完成后将其依次过10目筛、30目筛,留下中间尺寸的水淬玻璃料;
44.其次,通过控制温度指示器20,打开天然气管道5开关,通入天然气后使用明火点燃,接着控制温度指示器20打开氧气管道6开关通入氧气,同时手动打开压缩空气管道4开关通入压缩空气,通过开关闭合程度来调节空气,天然气,氧气的流量,直至火焰长度刚好冲到顶盖14,待高温炉体2温度达到设定的温度后保温30min,待高温炉体2内部温度均匀;
45.然后,打开放料漏斗7的开关,通过不锈钢钢管向压缩空气管道4放入配好的玻璃料,玻璃料随压缩空气从火焰燃烧器喷入高温炉体2,经过预热段,收缩段,熔融后进入收集罩3,碰到顶盖14后落入收集罩3中;
46.最后,将收集罩3中的物料经收集管道17后收集到料车18中,待球料冷却至室温既得到球形玻璃。
47.利用上述成珠装置进行大颗粒球形玻璃的制备,实施例如下:
48.实施例1:
49.步骤一:
50.将钠钙硅玻璃的玻璃料熔融水淬后平铺在盘中并放入烘箱内于100℃下烘干5h,用破碎机将烘干后的水淬玻璃料进行破碎,破碎完成后将其依次过10目筛、30目筛,留下中间尺寸的水淬玻璃料;
51.步骤二:
52.利用成珠装置进行成珠:
53.首先,通过控制温度指示器打开天然气管道开关,通入天然气后使用明火点燃,接着控制温度指示器打开氧气管道开关通入氧气,同时手动打开压缩空气开关通入压缩空气。通过开关闭合程度来调节空气,天然气,氧气的流量,直至火焰长度刚好冲到顶盖。待炉体温度达到900℃后保温30min,待合金炉体内部温度均匀;
54.然后,打开放料漏斗的开关,通过不锈钢钢管向空气管道放入配好的玻璃料,配合
料随空气从火焰燃烧器吹入炉体,经过预热段,收缩段,熔融后进入收集器,碰到顶盖后落入收集器中;
55.最后,将收集器中的物料收集到料车中,待球料冷却至室温既得到钠钙硅玻璃微球,所得微球粒径粒径3-5mm之间,颜色白色透亮,成球率96%,密度2.30g/cm3左右,显微硬度,≥300kg/mm2,抗压强度860kg/cm2,可见光反射率4%。
56.实施例2
57.步骤一:
58.将硼硅酸盐玻璃的玻璃料熔融水淬后平铺在盘中并放入烘箱内于100℃下烘干5 h,用破碎机将烘干后的水淬玻璃料进行破碎,破碎完成后将其依次过10目筛、30 目筛,留下中间尺寸的水淬玻璃料;
59.步骤二:
60.利用成珠装置进行成珠:
61.首先,通过控制温度指示器打开天然气管道开关,通入天然气后使用明火点燃,接着控制温度指示器打开氧气管道开关通入氧气,同时手动打开压缩空气开关通入压缩空气。通过开关闭合程度来调节空气,天然气,氧气的流量,直至火焰长度刚好冲到顶盖。待炉体2温度达到950℃后保温30min,合金炉体内部温度均匀;
62.然后,打开放料漏斗的开关,通过不锈钢钢管向空气管道放入配好的玻璃料,配合料随空气从火焰燃烧器吹入炉体,经过预热段,收缩段,熔融后进入收集器,碰到顶盖后落入收集器中;
63.最后,将收集器中的物料收集到料车中,待球料冷却至室温既得到硼硅酸盐玻璃微球,所得微球粒径粒径3-5mm之间,颜色透亮偏白,成球率98%以上,密度2.23g/cm3左右,显微硬度≥600kg/mm2,抗压强度1500kg/cm2,可见光反射率8%。
64.实施例3
65.步骤一:
66.将高铝玻璃的玻璃料熔融水淬后平铺在盘中并放入烘箱内于100℃下烘干5h,用破碎机将烘干后的水淬玻璃料进行破碎,破碎完成后将其依次过10目筛、30目筛,留下中间尺寸的水淬玻璃料;
67.步骤二:
68.利用成珠装置进行成珠:
69.首先,通过控制温度指示器打开天然气管道开关,通入天然气后使用明火点燃,接着控制温度指示器打开氧气管道开关通入氧气,同时手动打开压缩空气开关通入压缩空气。通过开关闭合程度来调节空气,天然气,氧气的流量,直至火焰长度刚好冲到顶盖。待炉体2温度达到1000℃后保温30min,待合金炉体内部温度均匀;
70.然后,打开放料漏斗的开关,通过不锈钢钢管向空气管道放入配好的玻璃料,配合料随空气从火焰燃烧器吹入炉体,经过预热段,收缩段,熔融后进入收集器,碰到顶盖后落入收集器中;
71.最后,将收集器中的物料收集到料车中,待球料冷却至室温既得到高铝玻璃微球,所得微球粒径粒径3-5mm之间,颜色透亮偏白,成球率98%以上,密度2.40g/cm3,显微硬度≥480kg/mm2,抗压强度1100kg/cm2,反射率6%,可见光反射率10%。
72.实施例4
73.步骤一:
74.将钛钡高折射率玻璃的玻璃料熔融水淬后平铺在盘中并放入烘箱内于100℃下烘干5h,用破碎机将烘干后的水淬玻璃料进行破碎,破碎完成后将其依次过20目筛、 30目筛,留下中间尺寸的水淬玻璃料;
75.步骤二:
76.利用成珠装置进行成珠:
77.首先,通过控制温度指示器打开天然气管道开关,通入天然气后使用明火点燃,接着控制温度指示器打开氧气管道开关通入氧气,同时手动打开压缩空气开关通入压缩空气。通过开关闭合程度来调节空气,天然气,氧气的流量,直至火焰长度刚好冲到顶盖。待炉体2温度达到980℃后保温30min,待合金炉体内部温度均匀;
78.然后,打开放料漏斗的开关,通过不锈钢钢管向空气管道放入配好的玻璃料,配合料随空气从火焰燃烧器吹入炉体,经过预热段,收缩段,熔融后进入收集器,碰到顶盖后落入收集器中;
79.最后,将收集器中的物料收集到料车中,待球料冷却至室温既得到钛钡高折射率玻璃微球,所得微球粒径粒径3-4mm之间,颜色白色偏黄,成球率98%以上,密度 2.70g/cm3,显微硬度≥500kg/mm2,抗压强度1350kg/cm2,可见光反射率11%。
80.实施例5
81.步骤一:
82.将含铅玻璃的玻璃料熔融水淬后平铺在盘中并放入烘箱内于100℃下烘干5h,用破碎机将烘干后的水淬玻璃料进行破碎,破碎完成后将其依次过20目筛、30目筛,留下中间尺寸的水淬玻璃料;
83.步骤二:
84.利用成珠装置进行成珠:
85.首先,通过控制温度指示器打开天然气管道开关,通入天然气后使用明火点燃,接着控制温度指示器打开氧气管道开关通入氧气,同时手动打开压缩空气开关通入压缩空气。通过开关闭合程度来调节空气,天然气,氧气的流量,直至火焰长度刚好冲到顶盖。待炉体2温度达到920℃后保温30min,待合金炉体内部温度均匀;
86.然后,打开放料漏斗的开关,通过不锈钢钢管向空气管道放入配好的玻璃料,配合料随空气从火焰燃烧器吹入炉体,经过预热段,收缩段,熔融后进入收集器,碰到顶盖后落入收集器中;
87.最后,将收集器中的物料收集到料车中,待球料冷却至室温既得到含铅玻璃微球,所得微球粒径粒径3-5mm之间,颜色透亮偏白,成球率97%以上,密度2.21g/cm3,显微硬度≥580kg/mm2,抗压强度1300kg/cm2,可见光反射率7%。