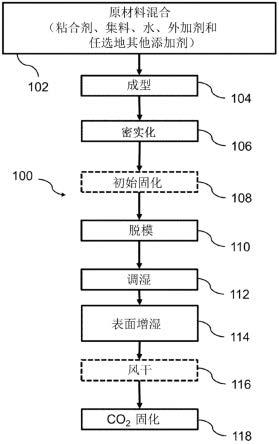
用于制造具有增强的耐久性的碳酸化预制混凝土产品的方法
1.相关申请的交叉引用
2.本技术要求于2020年6月3日提交的美国专利申请第63/034,037号的优先权,其通过引用整体并入本文。
技术领域
3.本公开一般地涉及预制混凝土产品,例如但不限于混凝土管、交通障碍物、墙、箱、涵洞、瓦、铺路材料(paver)、空心板、天井板、台阶、路缘、挡土墙和混凝土砌块。更特别地,本公开涉及碳酸化预制混凝土产品及其制造方法。
背景技术:4.预制混凝土已在建筑行业中被广泛采用。预制混凝土是在受控的工厂条件下被浇铸到可重复使用的模具或模型中的建筑产品。其在工厂中的受控固化环境中固化。在固化之后,然后其被运送至建筑工地。
5.预制混凝土具有广泛的结构应用和建筑应用。一些常见的实例包括铺路材料、地基、板、梁、地板、柱、墙、挡土墙、人孔、污水管、块材、模块化箱、桥面等。
6.传统上,波特兰(portland)水泥在预制混凝土产品的制造中被用作粘合剂。然而,已知波特兰水泥的制造具有不期望的环境影响。对于每生产一吨波特兰水泥,释放约一吨co2。波特兰水泥的获取涉及采石、排放大气污染物并且需要使用需要大量能源的大型窑。
7.基于水泥的预制产品依赖于水泥的水合来获得令人满意的强度。热和蒸汽固化技术已作为标准固化方法被广泛采用,以加速传统的基于水泥的预制混凝土产品的早期强度发展。
8.在富co2环境中对预制混凝土进行固化可以提供预制混凝土的环境影响的降低。这被称为碳酸化预制混凝土。虽然这样的碳酸化预制混凝土具有某些环境优点,但是仍然需要改善碳酸化预制混凝土的其他物理特性,例如其更好地耐受冻融循环和磨损的能力。
技术实现要素:9.在一个方面中,提供了用于制造碳酸化预制混凝土产品的方法,所述方法包括:获得包含至少一种粘合剂材料、集料和水的混合物;将混合物模制成模制中间体;对模制中间体进行脱模以获得经脱模的中间体,经脱模的中间体具有第一水:粘合剂比率;对经脱模的中间体进行调湿以提供经调湿的制品,所述经调湿的制品具有小于经脱模的中间体的第一水:粘合剂比率的第二水:粘合剂比率;用水性介质对经调湿的制品的至少一个表面进行增湿,从而引起经调湿的制品增重并提供经增湿的产品,经增湿的产品的第一部分具有大于经增湿的产品的剩余部分的第四水:粘合剂比率的第三水:粘合剂比率;以及用二氧化碳对经增湿的产品进行固化以获得碳酸化预制混凝土产品。
10.在另一个方面中,提供了用于制造碳酸化预制混凝土产品的方法,所述方法包括:获得包含至少一种粘合剂材料、集料和水的基底混合物,以及包含至少一种第二粘合剂材
料、第二集料和水的外层混合物;将基底混合物和外层混合物模制成具有外层和基底的多层模制中间体;对多层模制中间体进行脱模以获得经脱模的多层中间体,经脱模的多层中间体具有基底的第一水:粘合剂比率和外层的第二水:粘合剂比率;对经脱模的多层中间体进行调湿以提供经调湿的多层制品,相对于具有第一水:粘合剂比率和第二水:粘合剂比率的经脱模的多层中间体的水量,所述经调湿的多层制品具有减少的水量;用水性介质对经调湿的多层制品的外层的至少一个表面进行增湿以引起外层增重,从而提供其中外层具有大于第二水:粘合剂比率的第三水:粘合剂比率的经增湿的多层产品;以及用二氧化碳对经增湿的多层产品进行固化以获得碳酸化预制混凝土产品。
11.在又一个方面中,提供了用于制造碳酸化预制混凝土产品的方法,所述方法包括:由包含至少一种粘合剂材料、集料和水的模制混合物获得经脱模的中间体,经脱模的中间体具有第一水:粘合剂比率;对经脱模的中间体进行调湿以提供经调湿的制品,所述经调湿的制品具有小于经脱模的中间体的第一水:粘合剂比率的第二水:粘合剂比率;用水性介质对经调湿的制品的至少一个表面进行增湿以引起经调湿的制品增重,从而提供经增湿的产品,经增湿的产品的第一部分具有大于经增湿的产品的剩余部分的第四水:粘合剂比率的第三水:粘合剂比率;以及用二氧化碳对经增湿的产品进行固化以获得碳酸化预制混凝土产品。
12.如本文和以上所述的方法还可以全部或部分地以及以任意组合包括以下另外的特征和/或步骤中的一者或更多者。
13.在某些实施方案中,对至少一个表面进行增湿包括使用选自以下的施加方法来施加水性介质:将至少一个表面部分或全部浸入含水液体中;向至少一个表面喷洒水性介质;或者用辊装置向至少一个表面施加水性介质。
14.在某些实施方案中,对经调湿的制品的至少一个表面进行增湿包括对至少一个表面进行增湿直到经调湿的制品实现至少10g/m2的增重。
15.在某些实施方案中,施加水性介质包括在至少一个表面上施加水、基于水的溶液和/或基于水的浆料。
16.在某些实施方案中,施加水性介质包括施加在15℃至25℃的温度下的水性介质。
17.在某些实施方案中,对经脱模的中间体进行调湿包括对经脱模的中间体进行调湿直到经脱模的中间体的初始含水量的20重量%至70重量%被除去。
18.在某些实施方案中,获得混合物包括:获得干燥部分和液体部分,干燥部分具有至少一种集料材料和至少一种粘合剂材料,液体部分具有水;以及将干燥部分与液体部分混合以获得混合物。
19.在某些实施方案中,所述方法包括将添加剂与干燥部分和液体部分混合。
20.在某些实施方案中,所述方法包括将微纤维与干燥部分混合。
21.在某些实施方案中,获得混合物包括获得具有至少一种粘合剂材料的混合物,所述至少一种粘合剂材料为非胶凝的。
22.在某些实施方案中,获得混合物包括获得具有至少一种粘合剂的混合物,所述至少一种粘合剂包含钢渣和水泥,钢渣与水泥的重量比为1:20至20:1。
23.在某些实施方案中,获得混合物包括获得具有集料的混合物,集料与混合物的总重量的重量比为0.3至0.8。
24.在某些实施方案中,获得混合物包括获得其中添加剂与混合物的总重量的重量比为0.005至0.010的混合物。
25.在某些实施方案中,获得混合物包括获得包含外加剂的混合物。
26.在某些实施方案中,外加剂为防水外加剂。
27.在某些实施方案中,外加剂为塑化剂(plasticizer)、高效塑化剂(superplasticizer,高效减水剂)或基于聚羧酸酯/盐的减水剂。
28.在某些实施方案中,对混合物进行模制包括将混合物成型为成型中间体。
29.在某些实施方案中,对混合物进行模制包括使成型中间体密实化以提供模制中间体。
30.在阅读本公开之后,关于本改进的许多另外的特征及其组合对于本领域技术人员而言将是明显的。
附图说明
31.图1是示出了用于制造碳酸化预制混凝土产品的方法的流程图;
32.图2是具有贯穿其厚度的两个不同层的预制混凝土产品的示意图;
33.图3是示出了用于制造如图2中所示的双层碳酸化预制混凝土产品的方法的流程图;
34.图4是具有贯穿其厚度的三个层的预制混凝土产品的示意图;
35.图5是示出了预制混凝土产品在使用本公开的方法制造的不同阶段的平均含水量的图;以及
36.图6是示出了用样品a的混合设计制备的预制混凝土样品在调湿之后(实线)然后在表面增湿之后(虚线)贯穿其厚度测量的含水量变化的图。
具体实施方式
37.用于制备碳酸化预制混凝土产品的本方法可以需要较少的水泥,以及在一些情况下可以不需要水泥,并且可以允许混凝土将co2储存在产品内。本公开的碳酸化预制混凝土产品可以有利地具有改善的抗物理侵蚀性,例如对冻融循环和磨损的抗性。碳酸化固化也提供了引入工业废料作为水泥替代品的可能性。这些废料包括例如钢渣。本公开的方法不仅可以能够减少混凝土的co2足迹,而且由于使用目前未充分利用的低成本工业废料如钢渣和底灰,还可以允许以更负担得起的方式制造预制混凝土产品。钢渣是炼钢的副产品,并且在炼钢炉中将钢水与杂质分离期间产生。钢渣以熔融液态熔体出现,并且为在冷却之后凝固的包含硅酸盐和氧化物的溶液。底灰为从炉的底部收集的煤燃烧的粗糙粒状不燃性副产物。
38.可以使用本文所述方法生产的预制混凝土产品的实例包括但不限于混凝土管、交通障碍物、墙(包括挡土墙)、箱(包括模块化箱)、涵洞、瓦、铺路材料、地基、板(包括空心板)、天井板、台阶、路缘、混凝土砌块、梁、地板、柱、人孔、污水管、铁路枕木、以及其他预制混凝土产品。
39.碳酸化预制混凝土产品的制造与传统基于水泥的预制混凝土的制造的不同之处主要在于碳酸化固化过程期间二氧化碳的施加和适当粘合剂源(例如,水泥)的更广泛选
择。碳酸化预制混凝土主要通过在混合物中足量水的帮助下引入的二氧化碳气体与粘合剂中的钙和/或镁的氧化物和/或氢氧化物之间的反应来获得其强度。当暴露于高浓度或低浓度的co2中时,包含这样的矿物的预制件通常经历快速硬化。
40.冻融耐久性和磨损耐久性
41.在一些情况下,某些现有混凝土结构缺乏耐久性可能导致严重且有害的损害,使得产品不适用于其预期应用。本公开涉及这样的方法,通过所述方法可以制造具有改善的耐久性,更具体地改善的冻融耐久性和磨损耐久性的混凝土产品。在一些情况下,所公开的方法可以改善其他机械/物理特性。
42.冻融损害是由于重复的冷冻和解冻循环而积累的内部拉伸应力所引起的。水的膨胀和未冻结水颗粒的膨胀力的液压促成由冻融循环引起的损害。当冻融过程中存在除冰盐时,对预制混凝土造成的损害可能加剧。
43.表面损耗是由于重复的磨耗循环而引起的混凝土表面的逐渐质量损失。磨损是主要的表面损耗机理之一,并且是指沿混凝土表面移动的其他固体物体的磨耗。磨损的来源取决于预制混凝土的应用。
44.预制混凝土产品的耐久性通过一系列标准测试来测量。测试和要求根据产品类型及其应用而变化。作为实例,以下给出了用于预制混凝土铺路材料和挡土墙的标准测试的概述。本公开涉及多个标准(例如,astm标准)。应理解,这些标准对应于在本专利申请的提交日可获得的版本。
45.存在数种用于评估预制混凝土的耐磨性的方法。除了由astm c936规定的用于评估混凝土铺路材料的耐磨性的喷砂测试法(astm c418)之外,旋转切割机法(rotating-cutter method)(astm c944)也可以用于测量预制混凝土产品的耐磨性。在旋转切割机法中,测试设备由钻床和旋转切割器组成。将混凝土样品放置在旋转切割器下方,并向使切割器旋转的主轴施加98n的恒定垂直载荷。以200rpm的速度使样品经受摩擦损耗持续两分钟时间,并计算质量损失率(astm,2019a)。
46.根据如astm c936所要求的csa a231.2或astm c1645测试预制混凝土铺路材料的冻融耐久性。在测试期间,将预制混凝土样品完全浸没在3%的氯化钠溶液中。使其经受循环24小时时间的冷冻和解冻,其中16小时冷冻,8小时解冻。在28次冻融测试循环之后,预制混凝土的质量损失不应超过225g/m2总表面积,或者在49次冻融测试循环之后,预制混凝土的质量损失不应超过500g/m2总表面积(astm,2019b,astm,2018a,csa,2005)。
47.根据astm c1262测试预制混凝土挡土墙的冻融耐久性。在测试期间,将挡土墙样品正面朝下放置在深度为13
±
2mm的水中(astm,2018b)。在100次冷冻和解冻循环之后,一组五个样品的重量损失不应超过其初始重量的1%,或者在150次循环之后,五个样品中的四个样品的重量损失不应超过其初始重量的1.5%(astm,2017)。一个冷冻和解冻循环定义为完全冷冻循环后接完全解冻循环。也可以将挡土墙样品部分浸没在3%的氯化钠溶液中。在这种情况下,小于1%质量损失的要求通常减少至40次冻融测试循环。
48.碳酸化混凝土可能表现出低的抗冻融性,因此使其不适用于诸如铺路材料和挡土墙的应用。此外,碳酸化预制混凝土在磨损条件下可能表现不佳,使其不适合用于铺路材料应用。
49.使用传统方法,在碳酸化固化之前,预制混凝土的表面上通常存在缺水现象
(moisture starvation)。认为虽然这种表面缺水现象不会显著影响碳酸化预制混凝土的抗压强度,但是碳酸化混凝土产品的某些其他特性例如产品的弯曲强度、表面硬度和表面耐久性(包括耐磨性和抗冻融性中的至少一者)受到损害。因此,碳酸化预制混凝土产品通常不满足预期使用其的应用的某些耐久性要求。
50.已经发现,本文所公开的方法可以改善碳酸化预制混凝土产品的至少某些耐久性特性,如通过抗冻融性和耐磨性所测量的。还观察到如此制造的碳酸化预制混凝土产品可以随着时间和冻融循环保持其强度。
51.本公开涉及制造碳酸化预制混凝土产品的方法。用于制造碳酸化预制混凝土的主要组分包括粘合剂、集料和水。根据原材料的类型和关于碳酸化预制混凝土的规范,可以包括其他添加剂。
52.粘合剂
53.碳酸化预制混凝土中的胶凝和/或非胶凝粘合剂包括以下可碳酸化材料中的任一者及其组合:普通波特兰水泥、其他类型的水泥、非水硬性水泥、水硬性水泥、磨细粒化高炉矿渣粉(ground granulated blast-furnace slag,ggbfs)、钢渣、飞灰、底灰、不锈钢渣、以及富含cao和/或mgo和/或钙硅酸盐含量的其他材料。可以使用两种或更多种粘合剂的任何合适的组合。在一些情况下,可以使用单一粘合剂。在一些实施方案中,粘合剂为胶凝粘合剂,并且可以包括普通波特兰水泥、其他类型的水泥、非水硬性水泥、水硬性水泥、及其组合。在一些实施方案中,粘合剂为非胶凝粘合剂,并且可以包括钢渣、飞灰、底灰、不锈钢渣、以及富含cao和/或mgo、钙硅酸盐含量的其他材料,及其组合。在一个具体实例中,粘合剂为非胶凝粘合剂,并且包含小于5重量%、小于4重量%、小于3重量%、小于2重量%、或小于1重量%的水泥。
54.例如,钢渣在本文中可以用作粘合剂的唯一组分或者与一定比例的水泥一起用作粘合剂的主要组分(如果需要的话),以允许生产碳酸化预制混凝土产品,其中二氧化碳被用作固化剂。换言之,全部或大部分的水泥被钢渣替代。二氧化碳也被用于提升强度、固化并活化炉渣。
55.在一个实施方案中,粘合剂由钢渣组成。在一些情况下,粘合剂包含钢渣和另外的合适组分。
56.在一个实施方案中,粘合剂基本上由钢渣组成。在一个实例中,如本文所使用的术语“基本上由
……
组成”可以意指至少90重量%、至少91重量%、至少92重量%、至少93重量%、至少94重量%、至少95重量%、至少96重量%、至少97重量%、或至少98重量%。在一些情况下,粘合剂可以包含大部分(例如,大于50重量%)的钢渣。
57.在一个实施方案中,粘合剂包含钢渣和水泥,钢渣与水泥的重量比为约1:20、约1:15、约1:10、1:5、约1:20至约20:1、约1:10至约10:1、或约1:5至约5:1。或者,在一些实施方案中,钢渣与水泥的重量比为约20:1、或约15:1、或约10:1、或约5:1。
58.在另一个实施方案中,尤其是在如本文所限定的多层产品中,顶/外层中的粘合剂由钢渣组成或者基本上由钢渣组成,或者以约1:20至约20:1的重量比包含钢渣与水泥,或者钢渣与水泥的重量比为约20:1、或约15:1、或约10:1、或约5:1。
59.在一个实施方案中,粘合剂(例如钢渣、水泥和其他可碳酸化材料中的任意者或全部)与包含集料+粘合剂+水+添加剂的组合物的总重量的重量比在约0.20至约0.60,优选地
约0.25至约0.50,或者更优选地约0.30至约0.50的范围内。
60.水泥
61.在本公开中,可以使用以下非限制性水泥清单来生产碳酸化预制混凝土:波特兰水泥(i型至v型);波特兰石灰石水泥;快硬水泥;快凝水泥;低热水泥;高炉矿渣水泥;波特兰矿渣水泥;高铝水泥;白色水泥;彩色水泥;火山灰水泥(波特兰-火山灰水泥);加气水泥;水道水泥(hydrographic cement);非水硬性水泥和三元共混水泥。
62.如本文所用,有用的水泥为包含钙硅酸盐相特别是c3s的水泥,所述钙硅酸盐相在与水反应时使水泥能够获得强度。钙硅酸盐相的存在保证了短期和长期的强度改善。
63.钢渣和不锈钢渣
64.本文中的“钢渣”是指由炼钢产生的炉渣副产品。钢渣可以包括由碱性氧气转炉(basic oxygen furnace,bof)产生的炉渣,也称为来自氧气顶吹转炉炼钢(linz-donawitz,ld)法的炉渣,ld炉渣。钢渣还可以包括由电弧炉(electric arc furnace,eaf)产生的炉渣。如本文所使用的钢渣还可以包括钢包渣。钢渣可以为以上炉渣的组合。应理解,如本文所使用的“钢渣”不包括通常在铁生产期间产生并且可以用于制造水泥的铁渣和高炉矿渣,例如火山灰矿渣。
65.如本文所使用的“钢包渣”是指一类钢渣。钢包渣作为副产品由钢包精炼作业产生。在各种炼钢方法中,eaf或bof法中所生产的钢水基于期望的钢的品质经历另外的精炼过程。
66.如本文所使用的“ebh炉渣”是指eaf-bof混杂物,其是由eaf产生的炉渣和bof产生的炉渣的混合物形成的一种类型的钢渣。
67.不锈钢渣可以包括由不锈钢生产产生的炉渣。不锈钢渣主要由氩氧脱碳(argon oxygen decarburization,aod)和/或钢包冶金(ladle metallurgy,lm)法产生。
68.钢渣的化学组成:
69.在一个实施方案中,本文所使用的钢渣具有至少约15重量%的累积钙硅酸盐含量(例如:cs+c2s+c3s相浓度)。
70.在一个实施方案中,本文所使用的钢渣具有至少约20重量%的累积钙硅酸盐含量(例如:cs+c2s+c3s相浓度)。
71.在一个实施方案中,本文所使用的钢渣具有至少约30重量%的累积钙硅酸盐含量(例如:cs+c2s+c3s相浓度)。
72.在一个实施方案中,本文所使用的钢渣具有至少约40重量%的累积钙硅酸盐含量(例如:cs+c2s+c3s相浓度)。
73.在一个实施方案中,本文所使用的钢渣具有至少约6重量%或更优选地至少约15重量%的sio2含量。
74.不锈钢渣的化学组成:
75.在一个实施方案中,本文所使用的不锈钢渣具有至少约15重量%或更优选地至少约20重量%的sio2含量。
76.在一个实施方案中,本文所使用的不锈钢渣具有至少约30重量%或更优选地至少约35重量%的氧化钙含量。
77.钢渣的物理特性:
78.钢渣可以包括粗渣块和细渣块的混合物。粗渣块可以具有小于约50m2/kg的布莱恩(blaine)细度,以及细渣块可以具有大于约50m2/kg的布莱恩细度。作为来自典型的炼钢过程的结果,粗渣块、细渣块或二者均可以被填埋。接收的源自废物(例如填埋物和/或工业废物)的钢渣可以任选地被精炼。
79.对钢渣进行精炼可以包括对接收的钢渣进行过滤以将细渣块与粗渣块分离。
80.替代地或另外地,对接收的钢渣进行精炼还可以包括将钢渣粉碎成细粉末。在一些示例性实施方案中,将经过滤的细块粉碎,而不粉碎较粗的块。例如,对于eaf钢渣,可以将炉渣粉碎成至少50m2/kg并且优选地约180m2/kg的布莱恩细度。例如,对于ebh钢渣(eaf和bof的混合物以及钢包渣),可以将炉渣粉碎成至少100m2/kg并且优选地约240m2/kg的布莱恩细度。在另一些示例性实施方案中,可以将钢渣粉碎成更细的尺寸。在另一个实例中,至少50%的磨碎炉渣小于100微米,d(50)《100微米。
81.集料
82.集料可以为正常重量和轻质的天然来源材料或人造材料。根据集料的尺寸,可以将其分为粗集料和细集料。粗集料和细集料的类型、比例和尺寸随着其可用性、成本和级配而变化,并且还随着混凝土混合物所需的和易性(workability)以及碳酸化预制混凝土期望的表面质地和特性而变化。在一些实施方案中,细集料具有少于5%的直径大于3/8”的颗粒。在一些实施方案中,粗集料具有大于1/4”的直径。在另一个实施方案中,粗集料具有大于1/2”的直径。在一些实施方案中,如本文所使用的术语“正常重量”是指比重为约2.7的来自石灰石、花岗岩等的天然存在的或经压碎的砾石或砂。在一些实施方案中,如本文所使用的术语“轻质集料”是指比重在约0.3至约1.9的范围内的天然或人造颗粒。在本文中,表述“约”意味着值的正负10%的变化。
83.在一个实施方案中,集料与包含集料+粘合剂+水+添加剂的组合物的总重量的重量比在约0.3至约0.8,优选地约0.4至约0.7,或者更优选地约0.40至约0.65的范围内。
84.添加剂
85.用于本文的添加剂包括但不限于加气外加剂、减水外加剂、减缩外加剂、腐蚀抑制外加剂、速凝或缓凝外加剂、粘度调节剂、颜料、防水外加剂以及其他天然或化学添加剂。另外的成分/添加剂包括纤维(例如euclid的psi multi-mix 80),所述纤维可以在配制碳酸化预制混凝土时根据其最终应用添加。添加剂还可以为矿物外加剂。
86.向混凝土混合物中添加减水外加剂是为了提高抗压强度,降低水含量,减小孔隙率,并降低透水性。减水外加剂被分为塑化剂或高效塑化剂(即基于聚羧酸酯/盐的减水剂)。能够将所需水含量降低多达约50%或者将抗压强度提高多达约60%的任何减水外加剂均可以用作当前创新中的减水剂。本创新中所使用的外加剂应符合astm c494(用于混凝土的化学外加剂的标准规范(standard specification for chemical admixtures for concrete),astm国际,west conshohocken,pa,2019)的要求。
87.防水外加剂被设计成通过影响水进出混凝土的毛细作用为混凝土提供整体防水性。防水外加剂可以用作静态孔隙堵塞物,从而产生更困难的水迁移路径,或者可以用作反应性化学品,从而形成不仅堵塞孔隙而且从混凝土表面化学排斥水的“原位”疏水性材料。
88.在本公开的某些实施方案中,根据本文描述的添加剂存在于经调湿的脱模产品(即经调湿的制品)或其一部分中,旨在经历如本文所述的表面增湿步骤,并且所述添加剂
为加气外加剂。
89.在一个实施方案中,作为添加剂的加气外加剂与包含集料+粘合剂+水+添加剂的组合物的总重量的重量比在约0.0001至约0.001、或约0.0002至约0.0008、或约0.0004至约0.0006的范围内。
90.在某些实施方案中,防水外加剂仅存在于经调湿的脱模产品(即经调湿的制品)或其一部分中,例如多层产品中,不旨在/不需要经历如本文所述的表面增湿步骤。
91.在某些实施方案中,防水外加剂以至少约0.005、或至少约0.006,优选地至少约0.007、或至少约0.008、或至少约0.009、或至少约0.010的重量比(相对于组合物的总重量)存在于包含粘合剂、集料和水的组合物中。
92.在某些实施方案中,防水外加剂以至少约0.005且多至约0.009至0.010的重量比(相对于组合物的总重量)存在于包含粘合剂、集料和水的组合物中。
93.水:粘合剂比率
94.水:粘合剂比率取决于制造工艺(湿铸法或干铸法)、粘合剂和集料的含量、以及混合设计中减水剂的使用和剂量。通常,水:粘合剂比率从约0.10至约0.50(按重量计(weight basis)比率)变化。
95.在一个实施方案中,水:粘合剂比率在约0.10至约0.25的范围内。
96.在一个实施方案中,水:粘合剂比率可以为至少约0.10、或至少约0.11、或至少约0.12、或至少约0.13、或至少约0.14、或至少约0.15、或至少约0.20、或至少约0.25。
97.在一个实施方案中,水与包含集料+粘合剂+水+添加剂的组合物的总重量的重量比在约0.01至约0.10,优选地约0.05至约0.10或者更优选地约0.06至约0.08的范围内。
98.参照图1,提供了根据本公开的用于制造碳酸化预制混凝土产品的方法100。如以下将更详细描述的,方法100包括将原材料混合的步骤102,所述原材料包含粘合剂、集料、水和一些任选的添加剂。方法100包括将至少一种粘合剂、集料和水的混合物模制成模制中间体。在所示的实施方案中,将混合物模制成模制中间体包括:用于将混合物成型以获得成型中间体的步骤104;以及使成型中间体密实化以获得密实化中间体的步骤106,所述密实化中间体可以对应于模制中间体。可以进行对模制中间体进行初始固化的任选步骤108。进行对模制中间体进行脱模以获得经脱模的中间体的步骤110。经脱模的中间体具有第一水:粘合剂比率。对经脱模的中间体进行调湿以提供具有第二水:粘合剂比率的经调湿的制品的步骤112。经调湿的制品的第二水:粘合剂比率小于经脱模的中间体的第一水:粘合剂比率。对经调湿的制品的表面进行增湿以获得经增湿的产品的步骤114。增湿步骤114引起经调湿的制品增重。经增湿的产品的第一部分具有大于经增湿的产品的剩余部分的第四水:粘合剂比率的第三水:粘合剂比率。在一些实施方案中,具有第三水:粘合剂比率的第一部分可以对应于经增湿的产品的外层或外表面,以及具有第四水:粘合剂比率的经增湿的产品的剩余部分可以对应于经增湿的产品的被外层或外表面至少部分包围或覆盖的芯。还可以包括对经增湿的产品进行风干的任选步骤116,然后是用二氧化碳对经增湿的产品进行固化的步骤118。任选步骤在图1中用虚线示出。下文更详细地描述了步骤102至118中的每一者。
99.组分的混合
100.用至少一种粘合剂材料、集料、水和任选的添加剂例如外加剂进行混合步骤102。
在一个实施方案中,在混合步骤102之前,所述方法包括步骤a)提供干燥部分和液体部分,所述干燥部分包含至少一种集料材料和至少一种粘合剂材料,以及所述液体部分包含水和任选的添加剂;以及将干燥部分和液体部分合并。
101.在一些实施方案中,可以将添加剂和另外的成分任选地引入到混合物中,并且如果需要,随混凝土产品的预期用途而改变。
102.成型和密实化
103.成型步骤104包括通过任何已知的手段向模具中添加足够量的包含粘合剂、合适的集料、水和任选的添加剂的混合材料以将组分成型为期望的形状。虽然本文使用了“模具”或“模制”,但是该表述考虑了用于提供诸如框架/模具的形状的任何中空模型或基体,然后任选地整平。换言之,混合物可以以如限定内腔的这样的方式模制。
104.密实化步骤106包括例如使用振动或压实或压缩或组合力来将成型中间体密实化至期望的厚度、形状和密度。期望的厚度、形状和密度可以根据如本领域已知的期望应用来选择。
105.成型步骤104和密实化步骤106在本文中可以一起被称为对产品进行模制。换言之,成型步骤104和密实化步骤106可以被视为对混合物进行模制的步骤的两个子步骤。
106.在一个实施方案中,在成型步骤104之前,所述方法包括将至少一种粘合剂材料、集料、水和任选的添加剂混合以提供基底混合物的另外的步骤,其中所述混合可以在混合步骤102之前进行、与混合步骤102同时进行或者在混合步骤102之后进行。在一个实施方案中,所述方法包括将所述基底混合物成型以提供成型中间体的步骤,其中所述成型步骤可以在步骤104之前进行、与步骤104同时进行或者在步骤104之后进行。在另一个实施方案中,可以重复进行步骤102和步骤104中的一者或更多者将基底混合物混合并将基底成型。在另一些实施方案中,至少一种粘合剂材料、集料、水和任选的添加剂的所述混合物中的每一者可以包含相同或不同比率的这些组分。然而,这些混合物中的至少一者尤其是经历表面增湿步骤114的混合物包含除水泥之外的粘合剂,例如矿渣粘合剂,或者优选钢渣。在以上实施方案中,模制产品(即模制中间体)、经脱模的产品(即经脱模的中间体)、经调湿的脱模产品(即经调湿的制品)、经增湿的预固化模制产品(即经增湿的产品)和碳酸化预制混凝土产品中的每一者将是多层的(例如双层或更多层产品)。
107.初始固化(任选的)
108.在一些情况下,尤其是在用湿铸法制造预制混凝土时,任选地进行对模制中间体进行初始固化的步骤108以在110时将模制中间体从模具中取出之前给予其令人满意的初始强度。预制混凝土依赖于粘合剂的水合/凝固或其他物理/化学/活化以在该初始固化阶段实现期望的强度增益,该初始固化阶段例如持续2小时至几天。
109.调湿(减少经脱模的预制混凝土中的水量)
110.虽然可以紧接在将预制混凝土脱模之后进行碳酸化固化,但是通常在引入二氧化碳气体之前对密实化混凝土进行一定时间段的调湿。该调湿步骤112在对模制中间体进行脱模的步骤114之后并且在用co2对经脱模的中间体进行固化的步骤118之前开始。调湿步骤112涉及过量的水的受控去除。其主要目的是通过除去过量的水来促进混凝土内快速且均匀的碳酸化反应。过剩的水可能通过阻止co2扩散到反应物中而限制反应,而不足的水含量可能导致缺水,从而使反应停止。因此,为了最佳的碳酸化,可以在碳酸化之前实现最佳
的水含量。
111.在脱模步骤110之后,对经脱模的中间体(任选地在初始固化之后)产品进行调湿步骤112。调湿步骤112可以在室温、15℃至25℃的温度和30%至60%的湿度下以及在有或没有强制空气循环的帮助下进行。调湿的持续时间可以从10分钟至24小时或更长变化。调湿步骤的该步骤112可以通过水蒸发来帮助降低预制混凝土的含水量。释放的水分在密实化的预制混凝土内部留下许多孔隙,这对于在整个预制混凝土产品中实现均匀的碳酸化以及期望的co2吸收可能是至关重要的。相对大的co2吸收和均匀的碳酸化分布对于碳酸化预制混凝土产品的物理-机械特性可能非常重要。在一个实施方案中,在调湿步骤112结束时,从预制混凝土中除去混合物中的初始水分的20重量%至70重量%,优选地30重量%至60重量%,特别地40重量%至50重量%。在调湿步骤期间可以替代地使用其他已知的减少水分的方法,例如加热。
112.将产品的表面暴露于水性介质
113.本公开的方法100包括对经调湿的制品的表面进行增湿的步骤114。增湿步骤114包括将所述经调湿的制品的至少一个表面暴露于水性介质以引起增重。在对模制产品进行调湿112之后,预制混凝土的含水量或换言之水与粘合剂的比率降低。基体中足够的含水量可以允许均匀的二氧化碳渗透和令人满意的co2吸收以及关于碳酸化预制混凝土的令人满意的性能。然而,存在如现有技术中所描述的与调湿相关的缺点,即模制产品的外(暴露)表面比预制混凝土的内部快得多地失去水分。这被认为导致当内部的含水量处于理想水平时,外表面上的含水量较低。外表面上的水分短缺使得外表面上随后的碳酸化固化过程不完全,因为固化需要足够量的水来促进二氧化碳与钙硅酸盐相或者钙和镁的氧化物或氢氧化物之间的反应。
114.在操作本文所限定的过程时,期望在碳酸化固化之前,将外表面的表面含水量提高至足够的水平。这可以确保可以贯穿预制混凝土产品的整个体积实现令人满意的碳酸化反应程度。
115.在通过将所述经调湿的制品的表面暴露于水性介质来对经调湿的制品的表面进行增湿的步骤114时,可以通过向经调湿的制品的至少一个表面施加水性介质(即含水材料或含水相)来提高表面含水量。该水性介质可以为单独的水、或基于水的溶液、或基于水的浆料。当将该含水材料应用于表面增湿过程中时,对其温度没有特别要求,尽管优选接近于室温(即约15℃至约25℃)的温度。用于本文中的引起经调湿的制品的表面增重的水性介质包括任何含水方式(悬浮体/溶液或其他相/材料),所述含水方式包含足够量的cao/ca(oh)2/mgo,能够将水分输送至表面,并且适用于混凝土制造。浓度为1%至25%的水溶性化学溶液例如硅酸钠(水玻璃)也可以用于表面增湿。固体含量为1%至80%的水合水泥、钢渣、ggbfs、不锈钢渣、石灰、非水合水泥、飞灰、或包含足够量的cao/ca(oh)2/mgo的任何材料的浆料也可以用于表面增湿。当使用浆料时,其固体含量可以为基于质量的1%至25%,尽管优选5%至10%的固体含量。浆料可以通过在室温(15℃至25℃)下在配备有搅拌器的容器中将富cao和/或mgo物质添加到成比例量的水例如自来水中来制备。在浆料制备和表面增湿过程中,搅拌器应保持运转以保持一致的固体含量。制备的水性介质的ph值应为6.5至13.5。
116.水性介质可以使用各种施加方法来施加,包括但不限于将表面部分或全部浸入含
水液体中,或者向表面喷洒水性介质,或者使用辊或类似装置向表面施加水性介质。如果选择浸渍,则预制混凝土在含水液体中的浸没持续时间可以为1秒至5小时,优选为3秒至5秒。
117.无论选择何种类型的施加方法,在表面增湿处理完成之后,经增湿的产品在增湿步骤114期间均可以实现至少10g/m2的增重,优选地至少50g/m2,优选地50g/m2至350g/m2或75g/m2至325g/m2(基于预制混凝土的总增湿表面积)。
118.co2固化和任选的风干
119.在表面增湿步骤114之后,可以对经增湿的产品进行固化(碳酸化)。固化步骤118可以紧接在增湿步骤114之后进行。在固化步骤118时,这是用二氧化碳完成的。在一些实施方案中,考虑到碳酸化预制混凝土制造过程中所需的等待时间,例如输送经表面增湿的预制混凝土并将其装载至碳酸化固化室,在固化步骤118之前可以任选地进行在增湿步骤114之后对经增湿的产品进行风干的步骤116。该阶段可以持续长达1小时,优选地5分钟至20分钟。在此期间,经表面增湿的预制混凝土不应暴露于过热、过干或风过大的环境中。如果需要多于1小时的风干时间,则应延迟表面增湿活动。否则,应将经表面增湿的预制混凝土用塑料片或类似材料覆盖以防止在碳酸化固化之前水分进一步流失。在一些实施方案中,空气温度在15摄氏度至40摄氏度的范围内,优选为约22摄氏度。相对湿度可以在30%至90%的范围内,优选为约50%。气流速度可以为0.1m/秒至100m/秒,优选为约2m/秒。
120.在一些实施方案中,将经表面增湿的预制混凝土放入压力室中,在压力室中进行碳酸化固化。向密封的压力室中引入纯度为5%至99.9%的二氧化碳气体。用处于大气压或高于大气压的气体对混凝土进行固化。在高于大气压的情况下,在持续至少5分钟,优选地2小时至24小时的碳酸化固化过程期间,将室内二氧化碳气体的压力调节成0.07mpa至0.689mpa(0.1psi至100psi)。
121.层状碳酸化产品结构
122.如本文所讨论的,本公开的方法100可以对碳酸化预制混凝土产品的某些机械特性和耐久性特性,具体地耐磨性和抗冻融性提供积极影响。因此,这样的方法100可以具有提供具有组合的有益特性的产品的能力。例如,可以制备层状碳酸化产品结构。本公开考虑了根据需要在给定产品中制造/使用多层。碳酸化产品可以包含根据产品或构造可以被认为是外覆层的至少第一/外/顶层以及根据产品或构造可以被称为第二/内/底/基底层的第二层。关于粘合剂(尽管预期至少应优选使用本文中的粘合剂)、集料、混合物比例、添加剂和其他任选的组分,两个层的组成可以不同。所述层可以另外具有不同的厚度,并因此它们的相对尺寸比例可以不同。两个层可以具有不同的特性,并且相对于第二/内/底/基底层,第一/外/顶层至少具有一种改善的特性,所述特性为耐磨性和抗冻融性中的至少一者。
123.如图2中所示,碳酸化预制混凝土产品1的一个示例性实施方案可以由沿其厚度的两个不同层10、20构成。顶部为更致密且更坚固/更耐久的预制混凝土层10。在顶层10下面为基底层20。在一个实施方案中,顶层10的厚度可以小于混凝土产品1的总厚度的一半。
124.在顶层的实施方案中:1)其厚度可以为5mm至20mm,优选为6mm至13mm;2)其可以使用与基底层20相同类型的粘合剂;其也可以使用与基底层20不同类型的粘合剂;3)如果其使用与基底层20相同类型的粘合剂,则顶层10可以使用与基底层20相同的粘合剂含量,但是具有更高的第一水:粘合剂比率,顶层10还可以使用比基底层20更大的粘合剂含量,但是第一水:粘合剂比率与后者相似或大于后者;这样的配比实践可以有利于改善碳酸化预制
混凝土的耐磨性;4)在调湿过程完成之后任选地建议向预制混凝土的该层或整个部分施加上述表面增湿步骤;5)如果施加表面增湿步骤214,则为了促进吸水过程,不应向预制混凝土混合物中添加防水外加剂;以及6)其被设计成作为在使用碳酸化预制混凝土期间用于承受主要损耗和撕裂作用的表面。基底层20的实施方案为:1)添加至少0.1%的粘合剂质量,优选地1.5%至2.0%的防水外加剂;2)粘合剂含量不大于顶层10,以节省材料成本;3)以质量/质量计的水:粘合剂比率低于顶层10,以补偿二氧化碳气体在更致密的顶层10中的降低的渗透性;以及4)厚度大于顶层10的厚度。高剂量的防水外加剂可以改善基底层20的抗冻融性和吸水性二者。其还可以提供尺寸稳定的基底,这对于相对薄的顶层的耐久性可能是重要的。
125.在一个实施方案中,提供了用于制造碳酸化预制混凝土产品的方法,所述方法包括:
126.1)将至少一种粘合剂材料、集料、水和任选的添加剂混合,优选地,粘合剂由水泥组成或者基本上由水泥组成,或者包含约1:20至约20:1的水泥与钢渣或其他可碳酸化材料的比率,或者水泥与钢渣或其他可碳酸化材料的重量比为约20:1、或约15:1、或约10:1、或约5:1;
127.1a)将至少一种粘合剂材料、集料、水和任选的添加剂混合以提供基底混合物,优选地,粘合剂由钢渣和/或任何其他可碳酸化材料组成,或者基本上由钢渣组成,或者包含约1:20至约20:1的钢渣与水泥的比率;
128.其中所述步骤1a)在步骤1)之前进行、与步骤1)同时进行或在步骤1)之后进行;
129.2)将步骤1)的混合的至少一种粘合剂材料、集料、水和任选的添加剂成型以提供成型产品;
130.2a)将所述基底混合物成型以提供成型基底混合物,其中所述步骤2a)可以在步骤2)之前进行、与步骤2)同时进行或在步骤2)之后进行;
131.其中任选地重复步骤1)和步骤2)和/或步骤1a)和步骤2a)中的一者或更多者,并且任选地,所述混合的至少一种粘合剂材料、集料、水和任选的添加剂中的每一者可以包含相同或不同比率的相同或不同组分;
132.3)将步骤2)和步骤2a)的成型产品密实化成具有第一水:粘合剂比率的模制产品;
133.4)对步骤3)的具有所述第一水:粘合剂比率的所述模制产品进行脱模,以提供经脱模的产品;
134.5)对步骤4)的所述经脱模的产品进行调湿以提供经调湿的脱模产品,所述经调湿的脱模产品相对于具有第一水:粘合剂比率的模制产品具有减少的水量;以及
135.6)用二氧化碳对步骤5)的所述经调湿的脱模产品进行固化。
136.现在参照图3,提供了用于制造具有基底层和顶层的碳酸化预制混凝土产品的方法300。如以下将更详细描述的,方法300包括:将用于基底层(基底混合物)的粘合剂、集料、水、外加剂和其他添加剂混合的步骤302a,以及将用于顶层(顶层或外层混合物)的粘合剂、集料、水、外加剂和其他添加剂混合的步骤302b。将具有来自基底混合物的基底层和具有顶层混合物的顶层的混凝土产品(多层混凝土产品)成型以获得多层模制中间体的步骤304。使多层模制中间体密实化以获得多层密实化中间体的步骤306。对多层密实化中间体进行初始固化的任选步骤308。对多层密实化中间体进行脱模以获得经脱模的多层中间体的步
骤310。经脱模的多层中间体具有基底的第一水:粘合剂比率和顶层的第二水:粘合剂比率。对经脱模的多层中间体进行调湿以获得经调湿的多层制品的步骤312。在312时调湿期间,经调湿的多层制品的至少顶层的水:粘合剂比率降低。在一些情况下,在对经脱模的多层中间体进行调湿的步骤312之后,基底和顶层二者的水:粘合剂比率降低至低于它们各自的第一水:粘合剂比率和第二水:粘合剂比率。对经调湿的多层制品的至少一个表面(例如顶层)进行增湿以获得经增湿的多层产品的步骤314。在对顶层进行增湿的步骤314之后,顶层具有大于第二水:粘合剂比率的第三水:粘合剂比率。对经增湿的多层产品进行风干的任选步骤316。以及用二氧化碳对经增湿的多层产品进行固化的步骤318。任选步骤在图3中用虚线示出。下文更详细地描述了步骤302a/302b至步骤318中的每一者。
137.图3示出了另一种制造双层碳酸化预制混凝土产品的方法300。方法300可以用于制造多层产品。方法300包括将基底层20(图2)的组分混合的步骤302a以及将顶层10(图2)的组分混合的步骤302b。如前所述,基底层混合步骤302a和顶层混合步骤302b可以使用不同的粘合剂、不同的粘合剂含量和不同的水:粘合剂比率。此外,基底层20可以具有相对高剂量的防水外加剂。推荐将加气外加剂以随供应商而变化的剂量用于顶层10。然而,由于在基底层20中广泛使用防水外加剂,因此加气外加剂在基底层20中可能不是必需的。任选地,可以将微纤维以0.2%至0.5%(基于原材料的总体积)的剂量添加到顶层10的混合物中。添加微纤维可以降低开裂的可能性,但是可以提高碳酸化预制混凝土的耐磨性。此外,如果实施表面增湿步骤314,则顶层10可以不包含防水外加剂。在分别进行分批处理和混合之后,将顶层10混合物和基底层20混合物输送至成型/模制站。然后接着进行成型步骤304以及通过按照所需的量和顺序将两个层添加到模具中而进行的密实化步骤306。应提及的是,可以首先将顶层混合物添加到模具中,也可以首先将基底层混合物添加到模具中。为了在这两个层10、20之间实现坚固且耐久的结合,第二层混合物应立即被添加到经平整但未经压实的第一层材料上。为了这两个层之间更好的结合,可以实施其他技术,包括在对第二层进行浇铸之前在第一层的顶部上放置网状物或者使第一层表面变粗糙。如本文参照以上参照图1所述的步骤108所述任选地进行初始固化步骤308。此外,如上文参照图1的步骤110和112所述进行脱模步骤310和调湿步骤312。如果顶层10包含胶凝粘合剂例如水硬性水泥,则在调湿步骤312之后,可以使预制混凝土经受碳酸化固化步骤318而无需使用表面增湿步骤314。否则,顶层10或整个预制混凝土均用上文所述方法进行表面增湿步骤314。由于添加大量的防水外加剂,基底层20可以具有非常强的疏水性,使得基底层20不需要表面增湿步骤314。在表面增湿步骤314之后,如果需要,预制混凝土可以任选地在其经受碳酸化固化步骤318之前短暂地经历风干步骤316。该风干阶段的持续时间以及当风干持续时间长于1小时时所采取的行动与先前例如图1的步骤116中描述的那些相同。将具有双层结构的预制混凝土装载至压力室,然后在压力室经受步骤318时的碳酸化固化。碳酸化固化步骤318包括用于具有双层结构的预制混凝土的参数与本文所述的例如图1的步骤118中描述的那些相同。
138.除了增加表面增湿阶段之外,向预制混凝土混合物中添加足够量的防水外加剂也可以是改善碳酸化预制混凝土的抗冻融性的有效方式。如果水或除冰盐溶液不能渗透到碳酸化预制混凝土中,则可以防止冻融损害。通过添加足够量的防水外加剂,可以显著降低碳酸化预制混凝土在饱和状态下的吸水性,从而改善抗冻融性。通常,用于预制混凝土的防水外加剂的建议剂量低于0.4%(基于粘合剂的质量)。这样的低剂量的防水外加剂对混凝土
的抗冻融性可能具有非常有限的作用。本公开的方法可以将防水外加剂的剂量增加至1.0%或更高。
139.在不增加上述表面增湿步骤的情况下,具有这种高防水外加剂剂量的碳酸化预制混凝土可以在冻融测试中表现良好。
140.现在参照图4,可以将上述双层结构设计进一步扩展至三层结构2设计。该设计的顶部和底部为更致密且更坚固/更耐久的预制混凝土层10。在这两个层之间为中心层30。顶层和底层10上的预制混凝土可以用与上文参照图2所述的双层预制混凝土1的第一/外/顶层10相同的方法制备。中心层30可以具有与用于制备如上文参照图2所述的双层结构设计1的第二/内/底/基底层20的原材料来源和混合设计完全不同的原材料来源和混合设计。这样的夹层设计可以给碳酸化预制混凝土带来许多益处,例如除耐久性改善之外还有弯曲性能的改善、良好平衡的结构、调湿和碳酸化固化时间的可能减少、以及其他所需功能的增加。图3中所示的双层碳酸化预制混凝土的制造方法300在对成型顺序稍作修改的情况下可以用于三层碳酸化预制混凝土。因此,多层碳酸化预制混凝土2可以成型为具有多于三个层。
141.在以下实施例中,用以下列出的原材料中的一些或全部配制碳酸化预制混凝土产品:
142.·
钢渣:平均颗粒尺寸(d50)为25μm且估计比重为3.3的eaf和bof炉渣的混合物(ebh炉渣);钢渣具有至少约20%的累积钙硅酸盐含量;其中钢渣具有至少20%的氧化钙含量;其中钢渣具有至少约6%的二氧化硅含量;
143.·
普通波特兰水泥:i型;
144.·
水:自来水;
145.·
集料:比重为2.7的碎石;100%通过4.76mm(4号)筛;0.25%的含水量和0.75%的吸水率;
146.·
加气外加剂(air entraining admixture,aea):由basf供应,产品名称micro air;
147.·
防水外加剂(water repellent admixture,wra):由basf供应,产品名称masterpel 240;
148.·
熟石灰:四氢氧化钙镁白色粉末,由dap canada供应。
149.·
在气缸中的纯度》99.9%的压缩co2被用于碳酸化固化。
150.对制造的碳酸化预制混凝土的特性进行评估,并将其与关于分段式挡土墙构件的astm c1372规范或关于混凝土嵌锁型路面构件(concrete interlocking paving units)的astm c936规范进行比较。这些实施例仅旨在证明通过用本公开的方法制造的碳酸化预制混凝土,可以获得期望的特性。无论是原材料和工艺,还是产品和应用都将不限于实施例中给出的那些。
151.实施例1
152.用下表1a和表1b中所示的混合设计制备预制混凝土样品a
153.表1a:样品a的混合物组成
机械特性和耐久性。
164.表1c:经表面强化的碳酸化预制混凝土和常规碳酸化预制混凝土的关键物理-机械特性和耐久性
[0165][0166]
表2:关于分段式挡土墙构件的astm c1372规范
[0167][0168]
样品a和样品b二者的测试结果汇总在表1c中。将获得的测试结果与astm c1372规范进行比较(表2)。由于通过表面增湿过程强化了表面,样品a具有远优于样品b的抗冻融性和耐磨性。在没有表面增湿步骤的情况下,碳酸化预制混凝土由于其差的抗冻融性而无法被接受用于分段式挡土墙应用,尽管其其他特性满足astm c1372的要求。表面强化效应已使得样品a符合关于混凝土分段式挡土墙的astm c1372的所有要求。
[0169]
监测在样品制造过程的不同阶段预制混凝土的含水量,并且结果示于图5中。在调湿过程结束时预制混凝土的初始水分的约50%已蒸发。表面增湿过程将一些水带回到预制混凝土,使得水分损失为其初始含水量的约40%。不是平均含水量的变化,而是在表面增湿过程之后含水量分布的变化显著改善了碳酸化预制混凝土的内部品质和表面品质或抗冻
融性。测量经调湿的样品b沿其厚度的含水量,并且结果示于图6中。从样品b的顶表面至底部,含水量像略微偏斜的钟形曲线一样分布。在其中心,含水量为3%。作为风扇辅助的调湿过程的结果,该含水量在从中心到外表面的途中不断降低。在样品b的最外部分,含水量降低为低至1%。这样的低含水量使得预制混凝土的碳酸化固化不完全,因为碳酸化反应需要足够的水作为反应物。外表面上的这种不完全碳酸化固化进而制造了碳酸化预制混凝土的脆弱表面。这就是为什么样品b的抗冻融性和耐磨性二者均非常差的原因。
[0170]
通过表面增湿过程,沿预制混凝土厚度的含水量分布完全改进。如图6中所示,在浸没在水中之后,预制混凝土的中心与外表面之间的含水量差异缩小至小于0.5%。这表示横跨样品厚度的水分分布更均匀。更重要的是,在采取表面增湿过程之后,预制混凝土的外表面的含水量从最初的1%提高至约4%。实际上,约4%的含水量被认为是预制混凝土实现最大碳酸化固化程度的最佳值。在预制混凝土的外表面上和附近的足够量的水分的帮助下,碳酸化反应实现其最高潜能。因此,碳酸化预制混凝土的内部品质和表面品质得到改善。这就是为什么样品a具有比样品b大的多的对冻融和磨损变形两者的抗性的原因。
[0171]
实施例2
[0172]
用实施例1的配方和制造方法制造预制混凝土样品,但改变了表面增湿方法。在将经调湿的预制混凝土样品用风扇调湿2小时之后,将其在5%水泥(即与以上混合组成中所述相同的波特兰水泥)浆料(样品c)或5%熟石灰浆料(样品d)中浸渍1秒而不是在水中浸渍。样品c和样品d的调湿引起的水分损失分别为56%和55%。在表面增湿步骤完成之后,它们的增重分别为248g/m2和234g/m2。然后将经表面增湿的样品风干约6分钟,然后使其在0.1mpa(15psi)的压力下经受碳酸化固化24小时。与样品a相同地评估碳酸化预制混凝土样品的抗冻融性和耐磨性,并且结果记录在表3中。与常规碳酸化预制混凝土(表1中的样品b)的测试结果相比,在具有提出的表面增湿步骤的情况下,抗冻融性和耐磨性的改善是明显的。
[0173]
表3:经表面强化的碳酸化预制混凝土的抗冻融性和耐磨性
[0174][0175]
实施例3
[0176]
用实施例1的配方和制造方法制造预制混凝土样品,但表面增湿持续时间增加。将经调湿的预制混凝土样品在水中浸渍3秒(样品e)或5秒(样品f),而不是在水中浸渍1秒。在风扇前调湿2小时之后,样品e和样品f分别损失了其初始含水量的55%和54%。在表面增湿步骤之后,它们分别实现了231g/m2和222g/m2的增重。在表面增湿之后进行约6分钟的风干
之后,用被调节至0.1mpa(15psi)压力的二氧化碳气体将其固化24小时。与样品a相同地评估碳酸化预制混凝土样品的耐磨性,并且结果记录在表4中。与常规碳酸化预制混凝土(表1中的样品b)的测试结果相比,在具有增加的表面增湿步骤的情况下,耐磨性的改善是明显的。
[0177]
表4:经表面强化的碳酸化预制混凝土的耐磨性
[0178][0179]
实施例4
[0180]
用实施例1的配方和制造方法制造预制混凝土样品,但改变了表面增湿方法。将经调湿的预制混凝土样品在25%水泥浆料(样品g)或25%熟石灰浆料(样品h)或25%钢渣浆料(样品i)中浸渍1秒而不是在水中浸渍。在风扇前调湿2小时之后,样品g、样品h和样品i分别损失了其初始含水量的47%、50%和51%。在表面增湿步骤之后,它们分别实现了213g/m2、268g/m2和258g/m2的增重。在表面增湿之后进行约6分钟的风干之后,用0.1mpa(15psi)压力下的二氧化碳气体将其固化24小时。与样品a相同地评估碳酸化预制混凝土样品的耐磨性,并且结果记录在表5中。与常规碳酸化预制混凝土(表1中的样品b)的磨损测试结果相比,在具有增加的表面增湿步骤的情况下,耐磨性的改善是明显的。此外,与使用水泥浆料或熟石灰浆料相比,使用钢渣浆料在改善碳酸化预制混凝土的耐磨性方面更有效。
[0181]
表5:经表面强化的碳酸化预制混凝土的耐磨性
[0182][0183]
实施例5
[0184]
用以下所示的混合设计制备预制混凝土样品:
[0185]
表6a:样品j、k、l和m的混合设计
[0186][0187]
表6b:样品j、k、l和m的组成
[0188][0189]
*:水:粘合剂比率
[0190]
将原材料混合在一起,成型,然后密实化至期望的密度。在脱模之后,将预制混凝土样品在室温下在商业风扇前以43m3/分钟的空气流量调湿2小时。该调湿过程引起样品j和k二者53%的水减少,以及样品l和m二者49%的水减少。之后,通过将预制混凝土样品j在水中完全浸没5秒进行表面增湿,从而实现245g/m2的增重。预制混凝土样品k、l和m通过分别在25%水泥浆料、25%钢渣浆料和25%熟石灰浆料中完全浸没5秒来进行表面增湿,从而分别实现283g/m2、295g/m2和305g/m2的增重。然后,将经表面增湿的预制混凝土样品在环境温度下风干约10分钟,然后将其装载到压力室中以进行碳酸化固化。将被调节至0.1mpa(15psi)压力的二氧化碳气体引入到密封的压力室中。将碳酸化固化的持续时间设定为24小时。在碳酸化固化之后,按照实施例1中描述的方法评估碳酸化预制混凝土样品的密度、吸水率、抗压强度和抗冻融性。获得的结果记录在表6c中。与表2中所示的astm c1372规范相比,样品j、k、l和m全部可以被接受用于挡土墙应用。与常规碳酸化预制混凝土(表1中的样品b)相比,在表面增湿步骤的帮助下,它们具有大得多的抗冻融性。此外,与在钢渣浆料或熟石灰浆料中浸渍相比,在水泥浆料或水中浸渍给予碳酸化预制混凝土更大的抗冻融性。此外,如果将样品j的冻融测试结果与表1中的样品a的冻融测试结果进行比较,则与在水中仅浸渍1秒相比,在水中浸渍5秒给予碳酸化预制混凝土更大的抗冻融性。
[0191]
表6c:经表面强化的碳酸化预制混凝土的关键物理-机械特性和耐久性
[0192][0193]
实施例6
[0194]
用以下所示的混合设计制备预制混凝土样品n。该混合设计的主要特征在于从常规的0.2%至0.4%到2.0%的增加的防水外加剂(wra)剂量,以及二元粘合剂体系(钢渣和普通波特兰水泥的组合使用)。
[0195]
表7a:样品n的混合设计
[0196][0197]
表7b:样品n的组成
[0198][0199]
*:水:粘合剂比率
[0200]
将原材料混合在一起,成型,然后密实化至期望的密度。在脱模之后,将预制混凝土样品n在室温下在商业风扇前以43m3/分钟的空气流量调湿30分钟,从而引起21%的水分损失。之后,将该预制混凝土样品立即装载到压力室中以进行碳酸化固化,不对其施加表面增湿。将被调节至0.1mpa(15psi)压力的二氧化碳气体引入到密封的压力室中。将碳酸化固化的持续时间设定为24小时。在碳酸化固化之后,按照实施例1中描述的方法评估碳酸化预制混凝土样品的密度、吸水率、抗压强度、抗冻融性和耐磨性。获得的结果记录在表7c中。与表2所示的astm c1372规范相比,样品n可以良好地被接受用于挡土墙应用。与常规碳酸化预制混凝土(表1中的样品b)相比,其具有好得多的抗冻融性。与经表面增湿处理的碳酸化预制混凝土(表1中的样品a,表3中的样品c和d,以及表6c中的样品j、k、l和m)相比,其具有更优的抗冻融性。遗憾的是,如果将表7c中的磨损测试结果与表1中样品b的耐磨性进行比较,则在具有高剂量防水外加剂的情况下并没有获得耐磨性的改善。
[0201]
表7c:具有高剂量防水外加剂的碳酸化预制混凝土的关键物理-机械特性和耐久性
[0202][0203]
实施例7
[0204]
将具有包含90%钢渣和10%普通波特兰水泥的二元粘合剂组成的层状结构用于样品o的制造。碳酸化预制混凝土被设计成用于混凝土铺路材料或类似应用。样品o的顶层为6mm厚。其基底层为24mm至45mm厚,随所需的特性测试而变化。以下示出样品o的混合设计:
[0205]
表8a:样品o的混合设计
[0206][0207]
表8b:样品o的组成
[0208][0209]
*:水:粘合剂比率
[0210]
分别制备用于顶层和基底层的混凝土混合物。在将所有原材料混合在一起之后,将基底层混合物成型到模具中并整平,然后添加顶层混合物。然后通过压实和振动将成型材料密实化至期望的密度。在脱模之后,将预制混凝土样品o在室温下在商业风扇前以43m3/分钟的空气流量调湿2小时,从而实现36%的水减少。之后,通过将预制混凝土样品o的顶层部分在水中浸没3秒进行表面增湿,从而实现84g/m2的增重。然后将经表面增湿的预制混凝土在环境温度下风干约10分钟,然后将其装载到压力室中以进行碳酸化固化。将被调节至0.1mpa(15psi)压力的二氧化碳气体引入到密封的压力室中。将碳酸化固化的持续时间设定为24小时。在碳酸化固化之后,评估碳酸化预制混凝土的以下特性:
[0211]
密度、含水量、吸水率和抗压强度
–
根据astm c140;
[0212]
抗冻融性
–
根据astm c1645,使用3% nacl溶液;
[0213]
耐磨性
–
根据astm c944。
[0214]
出于比较的目的,用非常接近于样品o的基底层的混合设计的混合设计制造单层
碳酸化预制混凝土样品p,唯一的区别在于样品p的混合具有0.11的初始水:粘合剂比率,而样品o的基底层的混合具有0.13的水:粘合剂比率。按照与样品n相同的配方和制造方法制造样品p。在碳酸化固化之前,将样品p在室温下在商业风扇前以43m3/分钟的空气流量调湿2小时,从而引起26%的水减少。用样品o所使用的相同的测试方法评估样品p的特性。样品o和样品p二者的测试结果汇总在表8c中。然后将所获得的测试结果与表9中所示的关于混凝土铺路材料的astm c936规范进行比较。
[0215]
astm c936规定了用于测量混凝土铺路材料的耐磨性的喷砂法(astm c418)。面对astm c418的复杂性和可用性问题,选择替代方法astm c944来评估样品o和样品p的耐磨性。
[0216]
为了判断样品o和样品p的耐磨性品质,商业混凝土铺路材料源自home depot,包括4种混凝土嵌锁型路面构件和5种不同类型的铺路板。按照astm c944测试购买的混凝土铺路材料的耐磨性。在测试的商业混凝土铺路材料中,选择最低的磨损导致的质量损失作为用于评估样品o和样品p的耐磨能力的基准,其示于表9中。
[0217]
缺乏层状结构的样品p具有非常差的耐磨性。在磨损测试之后,其质量损失为样品o的25倍高。与样品o相比,样品p还具有略微更低的强度,但具有更优的吸水率和抗冻融性。与表9中所示的astm c936规范和商业混凝土铺路材料的最佳耐磨性相比,样品p不能被接受用于混凝土铺路材料应用,主要是因为其耐磨性差。相反,样品o由于层状结构与表面增湿的表面强化效应相结合而具有几乎等同于最佳等级的商业混凝土铺路材料(表9)的耐磨性。其吸水率、强度和抗冻融性符合astm c936的要求。明显的是,样品o非常适用于混凝土铺路材料应用。
[0218]
表8c:层状结构碳酸化预制混凝土和单层对应物的关键物理-机械特性和耐久性
[0219][0220]
表9:关于混凝土嵌锁型路面构件的astm c936规范和商业混凝土铺路材料的最佳耐磨性
[0221][0222]
从表8c中可以发现,在28次冻融测试循环之后,样品o具有比样品p更大的质量损失。这样的结果可能是由于在样品p中使用了高剂量的防水外加剂。虽然样品o的顶表面通过增加的表面增湿步骤而得到强化,但是这种表面强化效应在抗冻融性方面可能不如高剂量的防水外加剂有效。尽管如此,样品o的冻融导致的质量损失仍然在关于混凝土铺路材料的astm标准的最大允许量之内。
[0223]
实施例8
[0224]
将层状结构用于样品q的制造,其中钢渣作为唯一粘合剂。碳酸化预制混凝土被设计成用于混凝土铺路材料或类似应用。样品q的顶层为6mm厚。其基底层为24mm至45mm厚,随着所需的特性测试而变化。用以下所示的混合设计制备预制混凝土样品:
[0225]
表10a:样品q的混合设计
[0226][0227]
表10b:样品q的组成
[0228][0229]
*:水:粘合剂比率
[0230]
分别制备用于顶层和基底层的混凝土混合物。在将所有原材料混合在一起之后,将基底层混合物成型到模具中并整平,然后添加顶层混合物。然后,将成型材料在压实和振动下密实化至期望的密度。在脱模之后,将预制混凝土样品q在室温下在商业风扇前以43m3/分钟的空气流量调湿2小时,从而损失其初始含水量的41%。之后,通过将预制混凝土的顶层部分在水中浸没3秒进行表面增湿,由于吸水而实现103g/m2的增重。然后将经表面增湿的预制混凝土在环境温度下风干约10分钟,然后将其装载到压力室中以进行碳酸化固化。将被调节至0.1mpa(15psi)压力的二氧化碳气体引入到密封的压力室中。碳酸化固化的持续时间为24小时。在碳酸化固化之后,如实施例7中所述评估碳酸化预制混凝土的物理-机械特性和耐久性。
[0231]
出于比较的目的,用与样品q的基底层相同的配方制造单层碳酸化预制混凝土样品r,但没有表面增湿步骤。在室温下在商业风扇前以43m3/分钟的空气流量调湿2小时之后,样品r失去了其初始含水量的47%。还评估了其特性。样品q和样品r二者的测试结果汇总在表10c中。
[0232]
缺乏层状结构和表面增湿步骤,样品r具有非常差的耐磨性。在磨损测试之后,其质量损失为样品q的9倍高。样品r还具有比样品q更大的吸水率,尽管其强度与样品q相似并
且其抗冻融性略微更优。与表9中所示的astm c936规范和商业混凝土铺路材料的最佳耐磨性相比,样品r不能被接受用于混凝土铺路材料应用,主要是因为其耐磨性差。相反,样品q由于层状结构与表面增湿的表面强化效应相结合而具有优于最佳等级的商业混凝土铺路材料(表9)的耐磨性。其吸水率、强度和抗冻融性符合astm c936的要求。明显的是,样品q非常适用于混凝土铺路材料应用。
[0233]
表10c:层状结构碳酸化预制混凝土和单层对应物的关键物理-机械特性和耐久性
[0234][0235]
参考文献
[0236]
以下参考文献全部通过引用其整体并入本文。
[0237]
aci committee.(2008).201.2r-08:guide to durable concrete durability.michigan,us:american concrete institute.
[0238]
astm.(2017).standard specification for dry-cast segmental retaining wall units(vol.astm c1372-17).west conshohocken,pa:astm international.
[0239]
astm.(2018a).standard specification for solid concrete interlocking paving units(vol.astm c936/c936m-18).west conshohocken,pa:astm international.
[0240]
astm.(2018b).standard test method for evaluating the freeze-thaw durability of dry-cast segmental retaining wall units and related concrete units(vol.astm c 1262/c 1262m-18).west conshohocken,pa:astm international.
[0241]
astm.(2018c).standard test methods for sampling and testing concrete masonry units and related units(vol.astm c140/c140m-18).west conshohocken,pa:astm international.astm.(2019a).standard test method for abrasion resistance of concrete or mortar surfaces by the rotating-cutter method(vol.astm c944/c944m-19).west conshohocken,pa:astm international.
[0242]
astm.(2019b).standard test method for freeze-thaw and de-icing salt durability of solid concrete interlocking paving units(vol.astm c1645-19)
.west conshohocken,pa:astm international.
[0243]
csa.(2005).csa a231.2 precast concrete paving slabs/precast concrete pavers.toronto,ontario:csa.
[0244]
environmental protection agency.(1995).ap 42-compilation of air pollutant emission factors,5
th edition,volume 1.research triangle park,nc:u.s.environmental protection agency.
[0245]
patel,h.,bland,c.,&poole,a.(1995).the microstructure of concrete cured at elevated temperatures.cement and concrete research,25(3),485-490.
[0246]
zhang,d.,ghouleh,z.,&shao,y.(2017).review on carbonation curing of cement-based materials.journal of co2 utilization,21,119-131.doi:10.1016/j.jcou.2017.07.003。