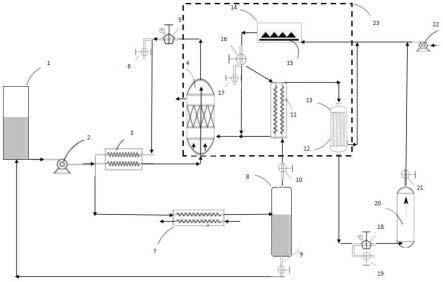
:
1.本发明涉及氢能技术领域,具体涉及一种自供热自增压的高效氨分解制氢系统及其制氢方法。
背景技术:2.氢能具有储量丰富、来源广泛、能量密度高、可循环利用、具有零碳排放及无污染物排放等特点。
3.氢气与氧气反应的唯一产物就是水,结合燃料电池技术、内燃机技术、燃气轮机技术,可以实现高效的能量转换。但应用过程中氢气的低体积能量密度和运输过程中的危险性是氢能应用实现商业化的一大阻碍,无论是高压鑵氢、液氢、还是固体金属储氢方案都无法解决用氢难题,这一瓶颈可以利用高含氢量的储氢载体,通过现场制氢的方法来解决。目前现场制氢主要有电解水制氢、甲醇制氢、和氨制氢。
4.电解水制氢由于成本太高难以推广,且需用到电,完全不适用于移动现场制氢;甲醇是碳基储氢载体,甲醇制氢依然会产生碳排放,不符合零碳新能源发展方向,而且伴生的少量co也易使质子交换膜燃料电池中毒导致氢纯化复杂困难;氨是非碳基储氢载体,具有较高的氢含量(17.65%)、较高的体积能量密度(液氢的1.5倍)、易于储存和运输、工业基础设施齐备、生产规模大、价格低廉等优点,因此被认为是最具有潜在应用前景的新型能源载体,近年来引起氢能领域浓厚的兴趣,氨催化分解制氢有望成为现场制取绿氢的主流,特别是交通运输移动制氢领域。
5.目前氨制氢在工业生产及燃料电池汽车上,广泛采用外供热常压制氢再增压技术。液氨汽化,进入填装有催化剂的传统反应器,外加热至450-700℃的较高温度下发生气相裂解反应,产生h2、n2、和少量未反应的nh3混合气体,混合气经变压吸附净化系统或膜分离器除去n2、nh3等杂质气体,获得高纯氢气,再经氢压机增压后储存于高压容器中,为质子交换膜(pemfc)燃料电池提供氢燃料,或作其它用途。因此,氨制氢不仅反应装置体积较大、响应慢、纯化单元复杂而昂贵,所需能耗也较大,使得其应用受到极大的限制。
6.因此,经济高效的、零碳排放的现场氨制氢系统和方法开发,仍然是氢能领域亟待解决的难题。
技术实现要素:7.本发明的目的是提供一种自供热自增压的高效氨分解制氢系统及其制氢方法,该系统结构紧凑、构思巧妙、快速启停、静默无噪音、节能高效,液氨在高压平流泵作用下进入氨分解器发生分解反应产生氢气和氮气,自增压产生10-50atm的可调控压力,氢气和氮气和未反应的氨气一起,在自增压的压差下依次进入冷却器、气液分离器经冷却和气液分离,积聚于气液分离器底部的液氨送回液氨原料罐循环使用,含有氮气及少量氨气的粗氢气经第一交换器加热后进入膜分离器,纯化后的氢气进入金属储氢罐,无需增压单元,实现了静默无噪音移动式供氢;含氢氨氮余气进入催化燃烧器供热,产生的热气流加热氨分解器和
进入膜分离器前的含有氮气及少量氨气的粗氢气,无需外界供热,不但能简化设备,还能节能减排,通过自增压方式实现了氨原料循环高效利用,大幅度提高产氢速率,达到了质子交换膜燃料电池对质量储氢密度、体积储氢密度、氢气成本及震动噪音等实际应用指标的要求,解决了氨制氢不仅反应装置体积较大、响应慢、纯化单元复杂而昂贵,所需能耗也较大的问题。
8.本发明是通过以下技术方案予以实现的:
9.一种自供热自增压的高效氨分解制氢系统,该系统包括经管道和阀门依次连通的液氨原料罐、高压平流泵、氨分解器、冷却器、气液分离器、第一热交换器、膜分离器和金属储氢罐,气液分离器底部的液相出口连通液氨原料罐,形成一个循环回路;此外还包括催化燃烧器,催化燃烧器为氨分解器和第一热交换器供热;所述氨分解器为微通道反应器,其结构为横竖双側不互通内换热式管程,其中,竖向管程为反应通道,反应通道内填充氨裂解催化剂颗粒构成催化床,反应通道进料口设在氨分解器底部,反应通道出气管设在氨分解器反应通道顶端;横向壳程为热流体加热通道,加热通道两側分别设置热流体进口和出口,热流体进口跟催化燃烧器的燃烧气输出管连通;液氨原料罐的液氨在高压平流泵作用下从氨分解器底部的反应通道进料口进入氨分解器在双側不互通的微通道反应器反应通道内,通过跟横向壳程热流体加热通道对流换热,加热升温到150-550℃发生催化分解反应产生氢气和氮气,自增压产生10-50atm的可调控压力,氢气和氮气和未反应的氨气一起,在自增压的压差下从氨分解器反应通道顶端反应通道出气管进入冷却器降温到15-30℃,然后经气液分离器分离,积聚于气液分离器底部的液氨在压差作用或液泵作用下定时排出返回液氨原料罐循环使用,含有氮气及少量氨气的粗氢气则从气液分离器顶端通过第一热交换器加热到350-450℃然后进入膜分离器,大部分氢气得到纯化;纯化后的氢气进入金属储氢罐,无需增压单元,实现了静默无噪音移动式供氢;氢纯化后的含氢氨氮余气进入催化燃烧器燃烧供热除去氢气和氨气,出口排出氮气及少量水蒸气,用来加热氨分解器和进入膜分离器前的含有氮气及少量氨气的粗氢气。
10.所述冷却器为水冷型或气冷型,将输出的氢气和氮气和未反应的氨气冷却至常温(15-30℃范围),输入气液分离器。
11.优选地,催化燃烧器也跟金属储氢罐连通,接受来自金属储氢罐的氢燃料作初始启动之用。
12.优选地,氨分解器和第一热交换器设置控温设备。
13.氨分解器与气液分离器通过背压阀连接,适于将氨分解器内生成的氢气、氮气和未反应的氨气输送至气液分离器内进行气液分离,背压阀出口设有旁路阀,适于采集生成的反应气进行流量测定、组份色谱分析等。
14.所述气液分离器通过控制阀依次连接第一热交换器和膜分离器,适于将分离气加热后送入膜分离器进行氢气分离纯化;所述气液分离器通过电磁阀连接液氨原料罐,适于将冷却分离的液氨回收循环使用。
15.所述膜分离器通过背压阀和金属储氢鑵连接,适于将纯氢送入金属储氢鑵,背压阀进气端设置有旁路阀,适于将纯氢送入其它地方;膜分离器余气输出管和催化燃烧器连接,适于将余气送入催化燃烧器;催化燃烧器的燃烧气输出管通过三路控制阀分别跟氨分解器的横向加热通道热流体进口、第一热交换器和旁路阀连接,分别对应用于为氨分解器
供热、将进入膜分离器前的氢气加热和排出多余的热流体;所述金属储氢鑵通过控制阀和催化燃烧器连接,适于将金属储氢鑵的氢气输送至催化燃烧器,进行无焰燃烧启动系统;金属储氢鑵和催化燃烧器中间设有空气泵,适于提供氧和脱氧催化剂进行无焰燃烧。
16.特别地,对于制氢反应温度和膜分离温度相近的情形(350-450℃),氨分解器、第一热交换器、膜分离器、催化燃烧器可绝热密封在一起,构成紧凑高温区。
17.优选地,为实现系统工作时的热能有效利用,还包括第二热交换器,第二热交换器的冷管跟高压平流泵连通,第二热交换器的热管跟氨分解器反应通道顶端的反应通道出气管通过背压阀连通,液氨原料罐的液氨在高压平流泵作用下连续进料,经过第二热交换器气化预热,然后从氨分解器底部的反应通道进料口进入氨分解器,氢气和氮气和未反应的氨气一起,在自增压的压差下进入第二热交换器,与高压平流泵作用下输送的液氨原料进行热交换,将输入的氨气预热的同时将输出的氢气和氮气和未反应的氨气初步冷却,然后进入冷却器进一步冷却。
18.所述膜分离器设有钯膜管束。
19.一种自供热自增压的高效氨分解制氢方法,采用上述装置,包括以下步骤:
20.1)氨催化分解制氢:液氨原料罐的液氨在高压平流泵作用下进入氨分解器,在双側不互通的微通道反应器反应通道内,通过跟横向壳程热流体加热通道对流换热,加热升温到150-550℃发生催化分解反应,自增加产生10-50atm的氢气和氮气;催化剂的活性成分为钌;
21.2)分离纯化:步骤1)得到的氢气和氮气和未反应的氨气一起,在自增压的压差下进入冷却器降温到15-30℃,然后经气液分离器分离,积聚于气液分离器底部的液氨在压差作用或液泵作用下定时排出返回液氨原料罐循环使用,含有氮气及少量氨气的粗氢气则通过第一热交换器加热到350-450℃然后进入膜分离器,大部分氢气得到纯化进入金属储氢罐;
22.3)余气燃烧供热:步骤2)纯化后的含氢氨氮余气进入催化燃烧器燃烧除去氢气和氨气,产生的热气为氮气及少量水蒸气,用来加热氨分解器和进入膜分离器前的含有氮气及少量氨气的粗氢气。
23.特别地,启动时,催化燃烧器利用来自金属储氢罐的氢燃料作初始之用。
24.特别地,催化燃烧器中催化剂是复方铬、pt/sio2。
25.氨催化分解制氢方应方程式为:2nh3→
3h2+2n2δh=+45.9kj mol
–1(弱吸热可逆反应)
26.氨催化分解制氢是弱吸热反应,氨分解制氢需消耗热能,氨本身虽是燃料却不易燃,但含氢氨气容易燃烧。利用氢纯化后的含氢余气燃烧供热,可消除外供热系统,不但能简化设备,还能节能减排。通常氨制氢在常压下进行,再经氢压机增压应用各种需压场景,氢压机昂贵耗能(压缩1公斤氢气至70兆帕耗能~6kwh,产生碳排1.3公斤),本技术自增压氨制氢无需氢压缩系统,起到简化设备、节能减排的效果。氨催化分解是体积增大反应,升高制氢压力会降低氨转化率,但产氢速率会大幅提高。
27.本发明的有益效果如下:
28.1)本发明系统结构紧凑,实现原料循环和热量回收利用,零碳零污,高效节能;
29.2)微通道反应器的使用改善传热传质,提高了产氢速率和缩短了响应时间;
30.3)自增压气液分离实现原料氨循环使用,无需追求高转化率就大幅度提高产氢速率;
31.4)钯膜分离不但得到纯氢,而且得到可燃的、燃烧后只含氮气的含氢氨氮混合气体;
32.5)含氢余氨无焰催化燃烧简化了加热单元,降低了系统能耗,提高了系统安全性;
33.6)绝热密封高温区集成使系统更紧凑、安全、节能。
34.总之,本发明制氢系统结构紧凑、快速启停、静默无噪音,实现原料循环和热量回收利用,零碳零污,不产生二氧化碳排放及毒化质子交换膜电池的一氧化碳,环保节能高效;通过自增压方式实现了氨原料循环高效利用,大幅度提高产氢速率,达到了质子交换膜燃料电池对质量储氢密度、体积储氢密度、氢气成本及震动噪音等实际应用指标的要求,克服因过分追求氨接近完全转化带来的系列难题。
附图说明:
35.图1是本发明自供热自增压的高效氨分解制氢系统的结构示意图;
36.其中,1、液氨原料罐,2、高压平流泵,3、第二热交换器,4、氨分解器,5、背压阀,6、旁路阀,7、冷却器,8、气液分离器,9、电磁阀,10、控制阀,11、第一热交换器,12、膜分离器,13、钯膜管束,14、催化燃烧器,15、脱氧催化剂,16、三路控制阀,17、旁路阀,18、背压阀,19、旁路阀,20、金属储氢鑵,21、控制阀,22、空气泵,23、绝热高温区。
具体实施方式:
37.以下是对本发明的进一步说明,而不是对本发明的限制。
38.如图1所示为本发明优选的一种自供热自增压的氨分解制氢系统,包括液氨原料罐1、高压平流泵2、氨分解器4、第二热交换器3、冷却器7、气液分离器8、第一热交换器11、膜分离器12和金属储氢罐20,气液分离器8底部的液相出口连通液氨原料罐1,形成一个循环回路;此外还包括催化燃烧器14,催化燃烧器14为氨分解器4和第一热交换器11供热;所述高压平流泵2工作泵压为10-100atm,高压平流泵2和液氨原料罐1相连,适于将液氨原料罐1的氨送入氨分解器4;所述系统各个部件的承压均不小于50atm,其区域压力和启停由各自控制阀设定。所述氨分解器4为微通道反应器,其结构为横竖双側不互通内换热式管程,其中,竖向管程为反应通道,反应通道内填充氨裂解催化剂颗粒构成催化床,反应通道进料口设在氨分解器4底部,反应通道出气管设在氨分解器4反应通道顶端;横向壳程为热流体加热通道,加热通道两側分别设置热流体进口和出口,热流体进口跟催化燃烧器14的燃烧气输出管连通;氨分解器4出口与气液分离器8进口通过背压阀5和反应气输送管连接,适于将氨分解器4内生成的氢气、氮气和未反应的氨气的反应气输送至气液分离器8内进行气液分离,背压阀5出口设有旁路阀6,适于采集生成的反应气进行流量测定,组份色谱分析等。氨分解器4通过背压阀5依次连接第二热交换器3、冷却器7和气液分离器8,适于将氨分解4器内生成的氢气、氮气和未反应的氨气冷却后输送至气液分离器8内进行气液分离,背压阀5出口设有旁路阀6,适于采集生成的反应气进行流量测定,组份色谱分析等。
39.所述气液分离器8通过控制阀10依次连接第一热交换器11和膜分离器12,适于将分离气加热后送入膜分离器12进行氢气分离纯化;所述气液分离器8通过电磁阀9连接液氨
原料罐1,适于将冷却分离的液氨回收循环使用。
40.所述膜分离器12通过背压阀18和金属储氢鑵20连接,适于将纯氢送入金属储氢鑵20,背压阀18进气端设置有旁路阀19,适于将纯氢送入其它地方;所述膜分离器12余气输出管和催化燃烧器14连接,适于将余气送入催化燃烧器14;催化燃烧器14的燃烧气输出管通过三路控制阀16分别跟氨分解器4的横向加热通道热流体进口、第一热交换器11和旁路阀17连接,分别用于为氨分解器供热、将进入膜分离器12的氢气加热和排出多余的热流体;所述金属储氢鑵20通过控制阀21和催化燃烧器14连接,适于将金属储氢鑵20的氢气输送至催化燃烧器14,进行无焰燃烧启动系统;金属储氢鑵20和催化燃烧器14中间设有空气泵22,适于提供氧和脱氧催化剂15进行无焰燃烧。
41.液氨原料罐1的液氨在高压平流泵2作用下经过第二热交换器3气化预热,从氨分解器4底部的反应通道进料口进入氨分解器4在双側不互通的微通道反应器反应通道内,通过跟横向壳程热流体加热通道对流换热,加热升温到150-550℃发生催化分解反应产生氢气和氮气,自增压产生10-50atm的可调控压力,氢气和氮气和未反应的氨气一起,在自增压的压差下从氨分解器4反应通道顶端反应通道出气管进入第二热交换器3,与高压平流泵2作用下输送的液氨原料进行热交换,将输入的氨气预热的同时将输出的氢气和氮气和未反应的氨气初步冷却,然后进入冷却器7进一步冷却,降温到15-30℃,然后经气液分离器8分离,积聚于气液分离器8底部的液氨在压差作用或液泵作用下定时排出返回液氨原料罐1循环使用,含有氮气及少量氨气的粗氢气则从气液分离器8顶端通过第一热交换器11加热到350-450℃然后进入膜分离器12,大部分氢气得到纯化;纯化后的氢气进入金属储氢罐20,无需增压单元,实现了静默无噪音移动式供氢;氢纯化后的含氢氨氮余气进入催化燃烧器14燃烧供热除去氢气和氨气,出口排出氮气及少量水蒸气,用于加热氨分解器和进入膜分离器前的含有氮气及少量氨气的粗氢气。
42.氨分解器4的工作原理:所述氨分解器为微通道反应器,其结构为横竖双通道不互通内换热式,竖側反应通道内填装催化剂,反应室的温度为150-550℃;氨气从竖側反应通道底部进料,受横側热流体加热发生催化分解反应,反应通道内设置控温设备,反应通道顶端连接反应气输送管,通过背压阀跟第二热交换器相连;液氨经高压平流泵输出,经过第二热交换器预热气化,预热后的氨气连续从反应通道底部输入,受横側热流体加热,达到150-550℃温度范围内时,发生氨催化分解反应,自增压产生高达50bar的含氢气、氮气、和氨气的反应气,从反应通道顶部出气管溢出,这是一个多组份、多反应的气固催化反应系统。
43.膜分离器12的工作原理:膜分离器采用商业化的钯膜分离装置,膜分离器12作业时候的温度在400℃左右,在此温度范围内,在压差作用下,氢分子在钯膜一侧离解成氢原子,溶于钯并扩散到另一侧,然后氢原子结合成分子,这样氢气就穿透过钯膜13,而其它气体如氮气,氨气等则无法透过钯膜13,和部分未透过钯膜的氢一起从气流末端排出,达到氢气分离纯化的目的。
44.催化燃烧器14的工作原理:催化燃烧器采用商业化公知产品,所述催化燃烧器14内填脱氧催化剂15,脱氧催化剂15可以是复方铬、pt/sio2或其它脱氧催化剂,适于将余气中的氢氨和来自空气泵22的氧气进行无焰燃烧放热,也适于将来自储氢鑵的氢气进行无焰燃烧。
45.实施例1:
46.以钌基氨分解催化剂为例,此催化剂的活性成分钌为5%,含助剂和载体,工作温度为350-550℃范围。将钌基催化剂20克(60-120目)和等体积sio2石英砂(60-120目)颗粒混均,填充于不锈钢微通道氨分解器4的反应通道内,催化层两端垫有石英玻璃纤维固定防漏。来自金属储氢瓶20的氢和从空气泵22输入的空气混合(混合气含氢2-3%),在催化燃烧器14中燃烧,热流体预热氨分解器4和第一热交换器11至400℃。液氨原料罐1中的液氨以质量空速whsv=150ml gcat-1
min-1
(流速3000ml min-1
),经高压平流泵2连续进料,经热交换器3气化预热,从底部反应通道进料管输入氨分解器,与横向加热通道的热流体对流换热,达到400℃发生氨分解反应制氢,背压阀预设压力为1atm,当反应器内自增压至背压阀预设压力时,产生的混合反应气从背压阀输出,通过旁路阀6连接气相色谱仪分析其组成,计算氨转化率和产氢速率等参数:
47.氨转化率x
nh3
(%)=【(输入nh3总量-输出nh3总量)/输入nh3总量】*100%
48.产氢速率v(mmol
·
gcat-1
·
min-1
)=(氨气流速/22.4)*转化率
nh3
)*1.5/催化剂质量
49.常压下产氢,并不适于后续分离提纯。
50.实施例2:
51.以钌基氨分解催化剂为例,此催化剂的钌分散度为5%,工作温度为250-550℃范围。将钌基催化剂20克(60-120目)和等体积sio2石英砂(60-120目)颗粒混均,填充于不锈钢微通道氨分解器4的反应通道内,催化层两端垫有石英玻璃纤维固定防漏。来自储氢瓶20的氢和从空气泵22输入的空气混合(混合气含氢2-3%),在催化燃烧器14中燃烧,热流体预热氨分解器4和第一热交换器11至400℃。液氨原料罐1中的液氨以质量空速whsv=150ml gcat-1
min-1
(流速3000mlmin-1
),经高压平流泵2连续进料,经热交换器3气化预热,从底部反应通道进料管输入氨分解器,与横向加热通道的热流体对流换热,达到400℃发生氨分解反应制氢,背压阀5预设压力为10atm,当反应器内自增压至背压阀预设压力时,产生的混合反应气从背压阀输出,通过旁路阀6连接气相色谱仪分析其组成,计算氨转化率和产氢速率等参数:
52.氨转化率x
nh3
(%)=【(输入nh3总量-输出nh3总量)/输入nh3总量】*100%
53.产氢速率v(mmol
·
gcat-1
·
min-1
)=(氨气流速/22.4)*转化率
nh3
*1.5/催化剂质量。
54.从背压阀输出的混合反应气,在压差作用下进入热交换器3换热预冷、再进入冷却器7降温至15-30℃,在此温度区间,氨气在10atm压力下达到液化,气液混合流体进入气液分离器,经分离积蓄的液氨,在液位计感应下,通过电磁阀9断续送回原料罐1循环使用。
55.富集于气液分离器上端的粗氢气(氢氮体积比为4:1,氨气体积百分比《7%),在压差作用下进入加热器11升温至400℃后进入膜分离器(工作温度350-450℃),膜分离器工作压差(1-5atm)可通过控制阀16调节。氢气的处理工艺设定,可根据粗氢具体组成和流量(m3h-1
)、商业化钯膜参数如透氢量(m
3 m-2
h-1
atm-1
)、工作压差(atm)、钯膜选择性等计算。钯膜分离的氢回收率一般在85-95%范围。纯化后的氢气最后进入金属储氢罐(工作压力10-50atm)。
56.余气(含氢体积百分比5-15%)则和来自空气泵22输入的空气混合(稀释至含氢1-3%)进入催化燃烧器14,在脱氧催化剂15作用下进行无焰催化燃烧,产生的热气流加热氨
分解器4和进入膜分离器前的氢气,氨分解器和加热器设置有温控系统,多余热气流可从旁路阀17排出。
57.实施例3:
58.除背压阀5预设压力为20atm以外,其余和实施例2同。
59.实施例4:
60.除背压阀5预设压力为40atm以外,其余和实施例2同。
61.实施例5:
62.除制氢温度预设为550℃以外,其余和实施例1同。
63.实施例6:
64.除制氢温度预设为550℃以外,其余和实施例2同。
65.实施例7:
66.除背压阀5预设压力为20atm以外,其余和实施例6同。
67.实施例8:
68.除背压阀5预设压力为40atm以外,其余和实施例6同。
69.实施例1-8的氨转化率x(%)和产氢速率v(mmol
·gcat-1
·
min-1
)参见表1。
70.从表1不难看出,氨转化率x(%)和产氢速率v都随制氢温度升高而增大,起活温度(x=50%)低于400℃,常压下550℃时接近完全转化。增大制氢压力会降低氨转化率,但高温条件下降低幅度较小;相反,增大制氢压力会大幅度提高产氢速率,氨转化接近完全时的温度下,产氢速率提高幅度极大。
71.由此可见,通过氨原料循环利用的设计,增大制氢压力来大幅度提高产氢速率,可实现高效氨分解制氢。达到了质子交换膜燃料电池对质量储氢密度、体积储氢密度、氢气成本及震动噪音等实际应用指标的要求。
72.上述结合图1对本发明的具体实施方式进行了描述,但并非对本发明保护范围的限制,所属领域技术人员应该明白,在本发明的技术方案的基础上,不需要付出创造性劳动即可作出的各种等效结构或等效流程的改变,或运用到其他相关的技术领域,仍在本发明的保护范围以内。
73.表1
74.实施例x
nh3
v实施例160.16.58实施例221.119.7实施例317.230.7实施例413.251.5实施例599.010.0实施例692.788.3实施例786.9166.7实施例882.7316.3