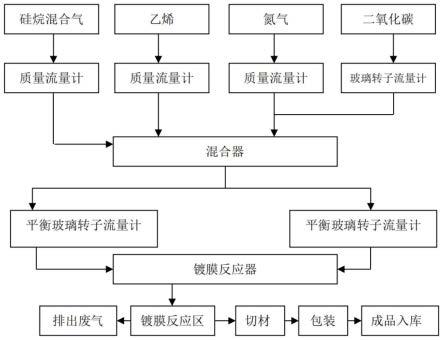
1.本发明涉及玻璃生产加工技术领域,具体是指超大板宽浮法玻璃在线硅质阳光镀膜系统。
背景技术:2.在线阳光镀膜是改善浮法玻璃性能的一项重要技术,既降低遮阳系数提高遮阳性能起到节能作用,也提高了浮法玻璃表面硬度及抗腐蚀性,在线阳光镀膜玻璃还可以增加建筑美感,从而满足了人们日益增长的物质和精神需求。
[0003][0004]
2018年全国在线阳光膜镀膜生产线保持在25条左右,生产板宽3300mm或3660mm镀膜玻璃,市场需求较为稳定,一个镀膜生产周期大约在12小时左右。但由于没有宽板玻璃镀膜生产技术,许多超大板宽的生产线不能生产镀膜玻璃,制约了企业市场开拓和提升效益,因此迫切需要研究开发在线阳光膜镀膜超大板宽生产技术,使在线阳光膜镀制技术在超大板宽方面有飞跃性进步。
[0005]
近年来浮法玻璃生产有了突破性的进展,浮法玻璃生产线向大吨位熔窑及薄玻璃发展。浮法玻璃板面越来越宽,合格板4880mm成为常规板宽。而市场上主要是可生产3300mm和3660mm板宽的镀膜器,只有中国玻璃公司在临沂生产过合格板4200mm的镀膜系统。大板宽玻璃生产的常规化倒逼在线镀膜技术必须加快创新。
技术实现要素:[0006]
本发明针对上述问题,提供了一种超大板宽浮法玻璃在线硅质阳光镀膜系统。
[0007]
本发明提供的技术方案为:超大板宽浮法玻璃在线硅质阳光镀膜系统,包括锡槽、镀膜反应器、混合器、硅烷供气室、乙烯供气室、氮气供气室、二氧化碳供气室和配气室,所述镀膜反应器设于锡槽内部且位于玻璃正上方,所述混合器设于配气室内部,所述混合器分别与硅烷供气室、乙烯供气室、氮气供气室、二氧化碳供气室连通,所述混合器与硅烷供气室、乙烯供气室、氮气供气室连通的管道上均设有质量流量计,所述混合器与二氧化碳供气室连通的管道上设有玻璃转子流量计,所述混合器的出气端通过若干个给气管道与镀膜反应器连接,所述给气管道上均设有平衡玻璃转子流量计,所述镀膜反应器还连接设有废气处理装置。
[0008]
进一步的,所述废气处理装置包括燃烧室和设于锡槽内部的废气稀释系统,所述燃烧室内部设有废气泄压系统,所述燃烧室内部设有废气管路吹扫系统。
[0009]
进一步的,所述乙烯供气室和配气室内部均安装设有可燃气体探测器,用于探测乙烯泄漏,规避乙烯的泄漏隐患。
[0010]
进一步的,所述硅烷供气室、乙烯供气室、氮气供气室、二氧化碳供气室和配气室内部均设置防爆通风机及轴流风机事故排风系统,事故通风换气次数≮12次/h。
[0011]
进一步的,所述硅烷供气室内部安装硅烷可燃气体探测器和火焰探测器,用于探
测硅烷泄漏。
[0012]
进一步的,所述乙烯供气室和配气室安装有氧源探测器,探测氮气及二氧化碳泄漏。
[0013]
进一步的,所述锡槽的边梁增设有10mm纵向方钢,用来加大方钢的承载力,所述锡槽的边梁上弓0.5mm,增加横向力,减少重力变形,所述锡槽的边梁设置保温层,通过加强保温,减少锡槽温度对边梁的影响。
[0014]
进一步的,所述镀膜反应器在生产时根据锡槽玻璃板横向温差和试镀进行压弯镀膜反应器,使镀膜反应器中间呈弓形,为了防止压弯时石墨接缝受力,从而导致膜层外观缺陷,设置石墨压弯点。
[0015]
进一步的,所述石墨接缝处采用石墨粉和高温胶结合,结合后的石墨经过高温固化,加强结合处强度。
[0016]
本发明与现有技术相比,具备以下有益效果:
[0017]
(1)通过将镀膜机组垂直方向的冷却梁加高,加弓,增加横向力,减少重力变形。同时加强保温,减少热变形。
[0018]
(2)重新设计压弯装置,将压弯重心远离石墨接缝处,减少接缝受力。通过在高温胶里掺杂石墨粉,使粘结材质接近石墨,减少产生碳化硅的可能。
[0019]
(3)设计了废气稀释系统、废气泄压系统及废气管路吹扫系统,减少废气爆炸、燃烧可能性及爆炸后应急。
附图说明
[0020]
附图1为本发明的工艺流程图。
具体实施方式
[0021]
下面结合实施例和附图对本发明做进一步的详细说明。
[0022]
实施例
[0023]
超大板宽浮法玻璃在线硅质阳光镀膜系统,包括锡槽、镀膜反应器、混合器、硅烷供气室、乙烯供气室、氮气供气室、二氧化碳供气室和配气室,所述镀膜反应器设于锡槽内部且位于玻璃正上方,所述混合器设于配气室内部,所述混合器分别与硅烷供气室、乙烯供气室、氮气供气室、二氧化碳供气室连通,所述混合器与硅烷供气室、乙烯供气室、氮气供气室连通的管道上均设有质量流量计,所述混合器与二氧化碳供气室连通的管道上设有玻璃转子流量计,所述混合器的出气端通过若干个给气管道与镀膜反应器连接,所述给气管道上均设有平衡玻璃转子流量计,所述镀膜反应器还连接设有废气处理装置。
[0024]
所述废气处理装置包括燃烧室和设于锡槽内部的废气稀释系统,所述燃烧室内部设有废气泄压系统,所述燃烧室内部设有废气管路吹扫系统。
[0025]
所述废气稀释系统采用三级衍射,通过往管路里通入空气稀释粉尘,衍射方式采用大面积接触方式,使粉尘浓度小于爆炸点。
[0026]
所述废气泄压系统采用可泄爆的废气处理系统燃烧室,该燃烧室工作时呈负压状态,一旦燃烧室发生爆炸,超过一定压力,可通过泄压口泄压,减少高压气体造成的人员设备伤害。
[0027]
粉尘在管路里沉积会导致粉尘浓度增大,如遇明火或空气或导致燃耗、爆炸。因此在废气管路设计时设计了吹扫装置。通过分段吹扫及排空将粉尘从管路里吹出来,减少了爆炸隐患。
[0028]
所述乙烯供气室和配气室内部均安装设有可燃气体探测器,用于探测乙烯泄漏,规避乙烯的泄漏隐患;所述硅烷供气室、乙烯供气室、氮气供气室、二氧化碳供气室和配气室内部均设置防爆通风机及轴流风机事故排风系统,事故通风换气次数≮12次/h;所述硅烷供气室内部安装硅烷可燃气体探测器和火焰探测器,用于探测硅烷泄漏;所述乙烯供气室和配气室安装有氧源探测器,探测氮气及二氧化碳泄漏。
[0029]
所述锡槽的边梁增设有10mm纵向方钢,用来加大方钢的承载力,所述锡槽的边梁上弓0.5mm,增加横向力,减少重力变形,所述锡槽的边梁设置保温层,通过加强保温,减少锡槽温度对边梁的影响。
[0030]
所述镀膜反应器在生产时根据锡槽玻璃板横向温差和试镀进行压弯镀膜反应器,使镀膜反应器中间呈弓形,为了防止压弯时石墨接缝受力,从而导致膜层外观缺陷,设置石墨压弯点;所述石墨接缝处采用石墨粉和高温胶结合,结合后的石墨经过高温固化,加强结合处强度。
[0031]
生产工艺流程如下:
[0032]
在线控制镀膜是以硅烷、乙烯、氮气、二氧化碳为原料,浮法锡槽为制备硅质膜提供适合的温度和还原性气氛。硅烷、乙烯、氮气、二氧化碳按一定比例进入安置在玻璃板上面的反应器,并以稳定的层流方式流过玻璃板表面,这时,硅烷借助反应器的特殊结构,并在还原气氛的条件下,温度超过400℃时开始分解,形成的产物是无定形硅,当温度超过600℃时,形成多晶硅。多晶硅沉积在玻璃表面形成硅质膜层,同时硅烷反应后产生的氢被乙烯吸附,生成乙烷和甲烷。这些多余气体和呈褐色的多余硅质粉一起从反应器两侧的排气孔排走,其化学反应式:
[0033]
sih4
→
si+2h2
↑
[0034]
sih4+c2h4
→
si+c2h6
↑
+h2
↑
[0035]
为了保证镀膜的均匀性,将镀膜反应区采用多点进气,使气体能够均匀分布在反应区,通过合理补气,保证了气体喷出的雷诺数。膜层均匀性得到有效控制,成膜效果也得到提高。
[0036]
本发明及其实施方式进行了描述,这种描述没有限制性,附图中所述的也只是本发明的实施方式之一,实际的结构并不局限于此。总而言之如果本领域的普通技术人员受其启示,在不脱离本发明创造宗旨的情况下,不经创造性的设计出与该技术方案相似的结构方式及实施例,均应属于本发明的保护范围。