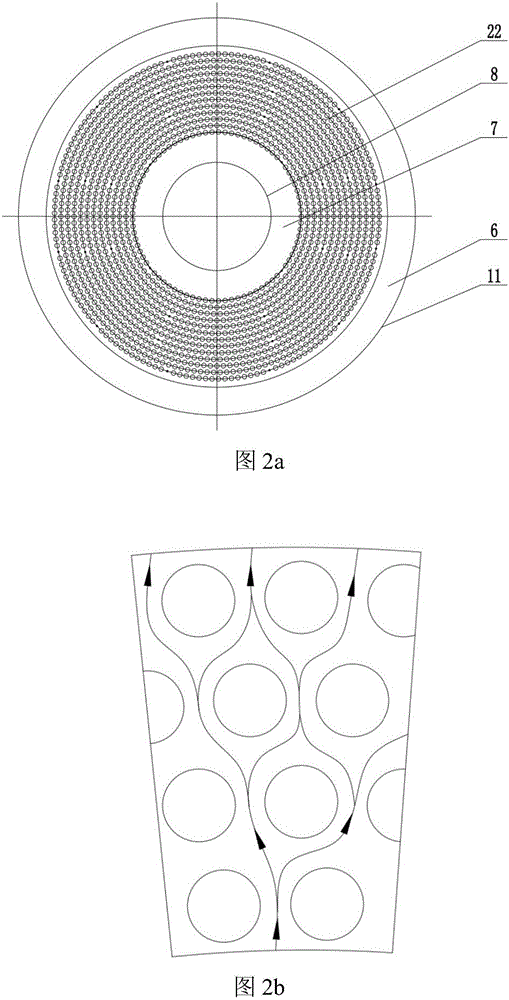
本发明属涉及一种用于正丁烷法顺酐和苯法顺酐生产装置的低压降径向等温反应器。
背景技术:
:顺丁烯二酸酐简称顺酐,又名马来酸酐,是一种重要的有机化工原料,是仅次于苯酐和醋酐的世界第三大有机酸酐,广泛用于石油化工、食品加工、医药、建材等行业。目前,按原料路线,顺酐的生产方法可分为苯氧化法、正丁烷氧化法。其中,正丁烷氧化法在顺酐生产中占主导地位,其生产能力约占世界顺酐总生产能力的80%。国际上顺酐主要采用正丁烷氧化法生产,我国的顺酐则主要采用苯氧化法生产,但由于正丁烷法具备原料价廉,污染相对较轻,碳原子利用率高和顺酐生产成本低等优点,近年来正丁烷法顺酐的产能不断增加,并有逐步取代苯氧化法的趋势。目前,在顺酐工艺领域的研究基本集中在催化剂和后处理工艺上,对于反应器的研究几乎全部以轴向列管式固定床反应器为基础。例如浙江大学的专利CN103071433A提出的一种用于正丁烷氧化制顺酐的固定床反应器的气体预分布器,该分布器由水平导流片、导流管、锥形帽组成,可以减少低气速区域的面积,并且改善对分布板局部冲击不均的影响,提高操作的稳定性。天津市化工设计院的专利CN102423666A提出了一种正丁烷法顺酐固定床氧化反应温度调节控制装置及方法:在反应器与熔盐冷却器之间设置有滑阀,通过精确控制滑阀的开启度,实现反应器壳程熔盐温度的稳定,解决和克服反应温度波动,使氧化反应顺酐重量收率提高0.5~1.0%,降低了反应生成物中的副产物。中国蓝星哈尔滨石化有限公司的专利CN202983655U提出了一种顺酐装置氧化反应器熔盐回流管结构,采用该结构可以加大顺酐苯氧化反应器熔盐的回流效果,延长了顺酐苯氧化反应器的使用寿命。尽管轴向列管式固定床反应器已在苯法顺酐装置和正丁烷法顺酐装置应用多年,技术成熟,但顺酐氧化器采用轴向列管式固定床反应器仍然存在许多问题,例如:1.目前还无法更好的解决超大直径列管式反应器(直径6~10m)壳侧载热流体的均匀分布问题,对于超大直径的反应器,熔盐在反应器径向方向的温差尚不能控制在2~3℃以内,这使得反应器内各管的移热性能差异较大,直接影响反应温度的控制,造成顺酐收率下降、反应管结焦堵塞,甚至温度失控等后果,因而,目前国内生产的轴向列管式固定床反应器最大直径仍在6m左右,这直接限制了顺酐反应器的生产规模,对于大规模的生产只能采用多个小规模反应系统并联的方式来解决;2.由于反应器最大直径的限制,流体经过反应器的流通面积也受到限制,因而催化剂的床层高度被限制,造成了现今工业化的顺酐反应器内催化剂床层高径比大,反应流体流过催化剂床层时的压降较大,导致了风机必须采用更高的出口压力,使得风机的电耗大幅上升,成为整个顺酐生产装置的能耗大户;3.轴向列管式固定床反应器中的列管较多,例如2.5万吨/年正丁烷法顺酐装置的氧化器内约有24000根管子,这使得整个氧化器列管内的催化剂填充均匀性难于得到保证,各个管子填充催化剂量有差别,使得操作时各管内的空速不同,这将导致有些管内的反应转化率不达要求,而有些管内的副反应较多,产生较多结焦物,最终堵塞反应管;4.反应管内径向方向上存在温度梯度,反应管中心的温度始终比反应管四周高,这导致反应管中心的反应温度较高,副反应较多,进而影响顺酐的整体反应选择性。为了改善和解决上述问题,研究者们做了一些努力,文献化学工程2009年3月第37卷第3期P20-22,26《列管反应器中环形分布器内流体均布的探讨》一文中对列管式反应器内的环形分布器内的流体流动的动量方程进行了修正,试图更准确地描述流体在列管反应器壳侧的流动行为。文献华东理工大学2012年硕士学位论文《列管式固定床反应器的模拟与设计》一文中提出了一个关于列管式反应器壳程的二维小池模型,并将该模型用于不同壳程结构(弓形折流板和圆盘-圆环形折流板)列管式固定床反应器的模拟和设计。这些研究的目的在于了解轴向列管式固定床反应器壳侧的熔盐流动特性,设计更好的熔盐分布器和收集器,采用更适宜的折流板,以减小径向的温度差,使制造更大直径的反应器成为可能。而对于降低顺酐反应器压降、改善催化剂的充填均匀性、提高顺酐的反应收率方面和研究还比较少。技术实现要素:本发明的目的是提供一种制备顺酐的方法和低压降径向等温反应器,以克服现有技术存在的缺陷。本发明制备顺酐的方法,是在一种设有套管式熔盐换热管和开有分气孔的中心分气管的低压降径向等温反应器中实现的;原料气正丁烷或苯,与空气由进气口进入反应器,反应后的物料从出气口排出;反应温度为380~420℃,反应压力为0.05~0.15MPa,停留时间为1.0~3.0秒,催化剂为V-P-O体系5或V-Mo-O体系。优选的:以正丁烷为原料时,正丁烷的转化率为80~85%,顺酐的选择性为66~73%,以苯为原料时,苯的转化率为98~99%,顺酐的选择性为70~78%;以正丁烷为原料时,反应温度为380~420℃,反应压力为0.08~0.15MPa,正丁烷的停留时间为1.8~2.25秒,催化剂为V-P-O体系,主要成分为V2O5-P2O5;以苯为原料时,反应温度为350~400℃,反应压力为0.06~0.15MPa,正丁烷的停留时间为1.4~1.8秒,催化剂为V-Mo-O体系,主要成分为V2O5-MoO3;以正丁烷为原料时,原料气正丁烷:空气=1:54.5~61.5vol;以苯为原料时,原料气苯:空气=1:65.7~83vol;上述的催化剂均为现有技术,如2012年《当代化工》41卷第七期“顺酐生产用VPO催化剂的研究进展”一文中报道的催化剂。本发明的方法,有益效果在于:反应器规模易于放大,可用于0.2~10万吨/年顺酐生产规模;反应器压降大幅降低,仅为5~20kPa;催化剂填充在换热管外侧,易于保证催化剂填充的均匀性,大降低局部区域反应恶化生焦的可能;附图说明图1为用于强放热反应的低压降径向等温反应器结构示意图。图2a为布管示意图;图2b为反应物料在本专利发明的管间流动时的流向示意图;图3为熔盐换热管的剖视结构图。图4为气体分布器外壁与底边之间的配合图。具体实施方式本发明制备顺酐的方法,是在一种设有套管式熔盐换热管22和开有分气孔的中心分气管8的低压降径向等温反应器中实现的;原料气正丁烷或苯,与空气由进气口15进入反应器,反应后的物料从出气口5排出,反应温度为380~420℃,反应压力为0.05~0.15MPa,停留时间为1.0~3.0秒,催化剂为V-P-O体系5或V-Mo-O体系。其中以正丁烷为原料时,正丁烷的转化率为80~85%,顺酐的选择性为66~73%,以苯为原料时,苯的转化率为98~99%,顺酐的选择性为70~78%;以正丁烷为原料时,反应温度为380~420℃,反应压力为0.08~0.15MPa,正丁烷的停留时间为1.8~2.25秒,催化剂为V-P-O体系,主要成分为V2O5-P2O5;以苯为原料时,反应温度为350~400℃,反应压力为0.06~0.15MPa,正丁烷的停留时间为1.4~1.8秒,催化剂为V-Mo-O体系,主要成分为V2O5-MoO3;以正丁烷为原料时,原料气正丁烷:空气=1:54.5~61.5vol;以苯为原料时,原料气苯:空气=1:65.7~83vol;参见图1~图4,所述径向等温反应器包括立式的外筒体11、上管板17、下管板16、固定板18、外侧壁开有通气孔的径向反应筐12、开有分气孔的中心分气管13和套管式熔盐换热管22;所述的下管板16内置在所述的外筒体11的下部,所述的上管板17设置在所述的下管板16的上方,所述的固定板18设内在所述的外筒体11的上部,所述的上管板17和下管板16的两端与所述的外筒体11的内壁固定连接,下管板16与外筒体11底部之间为进熔盐腔2,上管板17和下管板16之间为出熔盐腔4,所述出熔盐腔4处的外筒体11上设有熔盐出口3,优选的,设有两个对称设置的熔盐出口3,外筒体11的底部设有熔盐进口1;所述的径向反应筐12与外筒体11同轴,下端固定设置在所述上管板17上,上端与所述的固定板18的两端相连接,径向反应筐12与外筒体11间的环隙为集气腔6;所述中心分气管13设置在径向反应筐12中部,上端与设置在外筒体11顶部的进气口15连接,下端与上管板17连接,所述分气管13内设有气体分布器8,中心分气管13与气体分布器8之间为分气腔7;出气口5设置在所述的外筒体11的下部,与径向反应筐12相连通;优选的,所述的气体分布器8为上小下大的梯形管,与所述的外筒体11同轴设置,下端固定在上管板17上;优选的,所述的气体分布器8外壁与底边之间的夹角α为85~89°;优选的,中心分气管13外壁上的分气孔的孔径为2~25mm,开孔率为20~40%;优选的,所述的外筒体11和径向反应筐12为圆柱形;所述的径向反应筐12的高径比为2~6,径向反应筐12上的通气孔的的孔径为2~25mm,开孔率为20~40%;所述套管式熔盐换热管22设置在中心分气管13与径向反应筐12外壁之间,一端与出熔盐腔4连通,另一端与进熔盐腔2连通;优选的,所述套管式熔盐换热管22由外套管9和内管10构成,所述外套管9与所述内管10之间有环隙,外套管9上端封闭,并固定在所述的固定板18上,下端与出熔盐腔4连通,内管10上端敞开,下端与进熔盐腔2连通;优选的,所述的熔盐换热管22排列方式为同心圆、三角形或正方形;优选的,所述的外筒体11的顶部设有通过法兰连接的顶盖14,进气口15设置在顶盖14上;优选的,所述的顶盖14上设有催化剂装卸口19和用于消除死区的氮气口20;由上述的结构可见,由于本发明的径向等温反应器的熔盐在管侧流动,熔盐的分布问题不再像轴向列管反应器壳侧那样成为反应器直径的限制,制造出6~10m直径的反应器成为可能,反应器的生成规模也随着增加;由于径向反应器中气体流经催化床层时的流通面积比轴向反应器大许多,因而催化剂床层流向高度及流体流速相比轴向床都有显著降低,因而催化床层的压降也明显降低,甚至低至5~10kPa。这能显著降低空气压缩机的出口压力,不仅降低了空压机的设备投资,也大幅降低了空压机的操作成本,提高了装置的能量利用率。催化剂填装在换热管外侧,在反应筐内为一个整体,填充均匀性更容易得到保证,即使填充有不均匀情况,相比轴向列管式反应器的单管,也是呈大范围区域性质,这将填充不均匀的影响大幅平均,使得反应气体在催化剂床层的空速基本保持一致,避免了轴向列管反应器中某些管子中副反应过多的问题。如图2b所示,反应气体在催化剂床层中流动时,呈现升温----降温的循环,即与催化剂床层接触时发生反应,产生反应热使反应气体升温,而流向换热管时,热量向换热管内传递,反应气体降温。由于该循环的存在,反应气体在催化剂床层没有明显的、不可改善的高温区,这能降低CO、CO2、H2O等副产品;由于径向反应器中气体流经催化床层时的流通面积比轴向反应器大许多,因而催化剂床层流向厚度相比轴向固定床都有显著降低,因而催化床层的压降也明显降低,对于本发明的实施例1,仅为10kPa。这能显著降低空气压缩机的出口压力,不仅降低了空压机的设备投资,也大幅降低了空压机的电耗,降低了顺酐装置的能耗。另一个值得讨论的问题是,本发明的径向等温顺酐反应器在实际操作时,如果熔盐压降过高,造成催化剂床层压降降低而节省的电能小于而熔盐侧压降升高所增加的电能时,本发明的的低压降特性将变得没有意义,因而对于本发明的径向等温顺酐反应器,熔盐系统的压降也是一个必需要考察的因素。本发明的实施例1中,2.5万吨/年正丁烷法顺酐径向等温反应器的熔盐系统压降为113.1kPa,小于传统的同等顺酐生产规模的轴向列管式反应器,这也降低了装置的能耗;催化剂填装在换热管外侧,在反应筐内为一个整体,填充均匀性更容易得到保证,即使客观上无法达到绝对均匀,相比轴向列管式反应器的单管,径向催化剂床层的不均匀性呈大范围区域性质,这将填充不均匀的影响大幅平均化,使得反应气体在催化剂床层的空速基本保持一致,避免了轴向列管反应器中某些反应管内副反应过多、易于生焦堵塞的问题,反应气正丁烷或苯在催化剂床层中流动时,呈现“反应——升温——与换热管接触——降温——再反应”的循环,即与催化剂床层接触时发生反应,产生反应热使反应气体升温,而流向换热管时,热量向换热管内传递,反应气体降温。由于该循环的存在,反应气体在催化剂床层没有明显的、不可改善的高温区,这能降低CO、CO2、H2O等副产品的生成,提高顺酐产品的收率。实施例1采用图1~图4的反应器,2.5万吨/年正丁烷法顺酐。反应器结构参数:所述的气体分布器8外壁801与底边之间的夹角α为87.5°;中心分气管13外壁1301上的分气孔的孔径为25mm,开孔率为30%;外筒体11和径向反应筐12为圆柱形;径向反应筐12的高径比为3,径向反应筐12上的通气孔的的孔径为25mm,开孔率为30%;熔盐换热管22排列方式为同心圆;原料气为正丁烷与空气由进气口15进入反应器,反应后的物料从出气口5排出,其中正丁烷的转化率为83.5%,顺酐的选择性为69.5%;反应温度为420℃,反应进口压力为0.1MPa;正丁烷的停留时间为2秒,催化剂为V2O5-P2O5体系催化剂;原料气在反应器内的压降为10kPa。原料气正丁烷∶空气=1∶54.5vol;本发明实施例径向等温反应器与传统轴向列管式反应器分别用于2.5万吨/年正丁烷法顺酐装置后的性能比较见表1。表1实施例反应器与传统轴向列管式反应器性能比较项目传统轴向列管式反应器本发明反应器床层压降ΔP,kPa60~9010熔盐压降ΔP,kPa~190113.1空压机电耗,kW·h/h~3500~2200顺酐收率,wt%95~101%98~101%实施例2采用图1~图4的反应器,2.5万吨/年苯法顺酐。反应器结构参数:所述的气体分布器8外壁801与底边之间的夹角α为87.8°;中心分气管13外壁1301上的分气孔的孔径为20mm,开孔率为35%;外筒体11和径向反应筐12为圆柱形;径向反应筐12的高径比为3.3,径向反应筐12上的通气孔的的孔径为20mm,开孔率为35%;熔盐换热管22排列方式为正三角形;原料气为苯与空气由进气口15进入反应器,反应后的物料从出气口5排出,其中苯的转化率为98.6%,顺酐的选择性为75%;反应温度为370℃,反应压力为0.09MPa;苯的停留时间为1.5秒,催化剂为V2O5-MoO3体系催化剂;原料气在反应器内的压降为8kPa。原料气苯∶空气=1∶70.5vol。当前第1页1 2 3