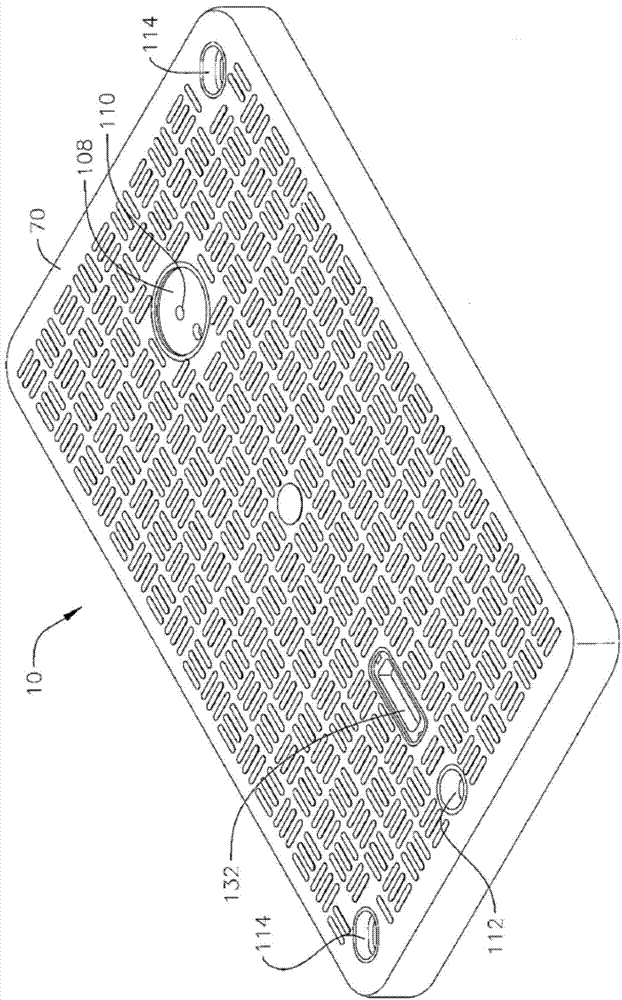
本发明涉及用于多种地下产业中的地下或地面库的热固性聚合物盖或罩及其制造方法。
背景技术:
:设施、安全和铁路行业、或其他产业中使用的地下或埋置的库、坑、室、或箱可包括同轴纤维或光纤、铜缆以及天然气和电力的线路和其他管道、工业阀门、无线天线等。为了进行修理或加强服务,常常需要打开用于地下设施的库和坑。通常,设施库和坑包括混凝土盖、聚合物混凝土盖、铸铁盖、镀锌钢盖或塑料盖,所述盖通过在一端具有钩的工具或镐打开。钩通过盖或罩中的孔插入并且用于将盖或罩从其在库或坑顶上的开口撬开。由于地下设施库或坑经常需要位于人行道、右边路、小巷的路和街、或其他高交通区域中,所以罩必须构造成承受大量载荷。因此,当前的盖或罩的构造由混凝土、聚合物混凝土、和铸铁制成以承受所需载荷。这些罩材料可以承受大量载荷并且具有用于多种交通区域中所需的耐用性程度。这些罩类型的缺点在于其相当重,根据具体应用重量超过100磅或更大。因此,由于其重量,对于在容纳于设施库或坑内的设备内的修理、维护、或增加附加服务,所述罩难以移出。在罩的移出和重新安装期间,重的罩可对工人造成伤害或其他背部问题。设施库和坑的罩还由塑料制成,但是这些具有在其承受较少载荷的区域中使用的受限应用,即绿化带或庭院应用。塑料盖的问题在于,由于其不能承受大量载荷,所以其具有受限的适用性,并且与聚合物盖相比,塑料盖在润湿时提供较小的摩擦系数。因此,需要新的设施库和坑的罩设计,所述罩重量轻,但由于其可以承受大量载荷而耐用,并且相对于目前可用的罩提供改善的防滑性。技术实现要素:本发明在一个实施方案中提供了改进的设施库的罩或盖,其由玻璃纤维增强聚合物基体材料制成,产生了重量减小且强度增加的罩,其与现有的罩设计相比更轻、强度更高、具有改善的uv特性和防滑性、并且制造成本更低。所述盖或罩用于库、坑、室或箱,并且为了易于表示在本文中全部称为库。库被用于多个产业,包括设施、安全防卫、天然气、和铁路,例如,其中所述库在地下、被埋置、或在地面。玻璃纤维增强聚合物基体(frpm)材料是由不饱和聚酯热固性树脂基体、玻璃纤维增强材料、和无机或矿物填料组成的纤维增强聚合物材料。另外的成分是低量添加剂,包括uv抑制剂、固化引发剂、增稠剂、加工助剂、和脱模剂。该制剂当在热和压力下固化时经历交联反应。用于罩的纤维增强聚合物材料在宽的温度范围内保持其原始材料性质和尺寸精度。所述罩平均比混凝土罩和聚合物混凝土罩轻50%,并且比铸铁盖轻65%。纤维增强聚合物材料被制备成连续的片材,其中将树脂糊料转移至刮刀箱(doctorbox),在刮刀箱处将所述树脂糊料沉积到从正下方通过的移动载体膜上。将玻璃纤维粗纱供应至在经树脂覆盖的载体膜上面的旋转切割器中。使短切纤维随机地沉积到树脂糊料上。用树脂糊料涂覆第二载体膜,并且将其树脂侧向下地铺在短切纤维之上。然后将这些层运送通过一系列压实辊,在压实辊处使玻璃纤维与树脂糊料固结并且将空气从片材中移除。使纤维增强聚合物材料片材保持在室温直至达到期望的模制粘度。当聚合物材料准备好进行模制时,将其切割成预定尺寸的片。然后将经切割的片堆叠并组装成装料模料(chargepattern),其为填充模腔的最佳形状和体积。然后封闭模具并压紧聚合物材料。使模具保持封闭预定量的时间以允许罩固化。固化之后,打开模具并使用集成的排出销将罩从模具下表面排出。在任何必需的机械加工之前使所述罩冷却至室温。制造过程可以通过使用机器人技术来自动化。制造方法包括低压模制与并入蒸汽罐以加热模具的模具设计相结合,产生较低的模具成本、较低的材料成本和较快的循环时间。模具设计允许提供较快循环时间的低压模制,产生较低的生产成本,同时产生重量减小且性能改善的盖。所述罩包括最上表面,所述最上表面是平坦的并且在其安装在库上的状态中与地面相平。罩或盖的底侧具有外缘与凹入的内部区域或腔。所述腔包括允许所需的配件与通孔附着的特征。盖的底部具有在腔中间隔排列的连续支承肋材以转移载荷并使在向外缘施加载荷下的挠曲最小化。外缘通过库、框架、或其他类型的支承凹槽来支承。在一个实施方案中,肋材在腔至边缘的跨度中不间断以向盖提供强度。罩盖的最上表面具有由不同深度处的特征模式产生的纹理或表面状态。平坦表面的深度变化产生向该表面的轻微凸起以将材料的玻璃组分推离该表面,产生富含树脂的表面。上表面还具有一系列凸部(boss),所述凸部具有不同高度的形状以允许产生盖的表面中的凸出转变。这些形状以这样的模式布置:允许另外的边缘表面抓紧可以接触罩顶的移动表面。uv抑制剂、凸部设计、和表面纹理化的组合产生改善的uv特性并防止玻璃纤维起霜。凸部的高度、间距、和角度与表面纹理化一起增加了抓紧面(grippingsurface)的摩擦系数,产生改善的防滑性。将罩或盖设计成允许安装“l型螺栓”或“贯穿螺栓”以将盖固定至库。还可以并入自锁的锁定组合件。所述盖还并入这样的特征:允许安装用于将盖从库中移出的镐孔保持槽(pickholeretainingcup)。通过参照以下的详细说明和附图,将更全面地理解本发明的这些和其他特征。附图说明图1是本发明的纤维增强聚合物材料设施库或坑的罩或盖的一个实施方案的透视图;图2是用于制造玻璃纤维增强聚合物材料的混配过程的图;图3是用于制造盖的模具的横截面视图;图4是图3模具的细节图;图5是图3模具的细节图;图6是图3模具的细节图;图7是位于设施库上的盖的透视图;图8是盖的底表面的透视图;图9是图7的横截面侧视图;图10是另一底视图盖设计的透视图;图11是图8的横截面视图;图12是盖的上表面的细节图;图13是图12的盖的表面的横截面细节;图14是盖的透视图;图15是用于盖的l型螺栓连接件的细节图;图16是用于连接盖的凸缘的细节图;图17是用于盖的自锁连接机构的细节图;图18是盖的镐孔保持槽的细节图;并且图19是自动化制造方法的示意图。具体实施方式参照图1,本发明的一个实施方案是纤维增强聚合物材料设施库或坑的罩或盖10,所述罩或盖10由不饱和聚酯热固性树脂基体、玻璃纤维增强材料、和无机或矿物填料组成。应理解,本发明是盖或罩,并且这些术语贯穿本说明书可互换地用于设施库或坑,库或坑贯穿本说明书也是可互换使用的术语。所述基体还包含低量添加剂、固化引发剂、增稠剂、加工助剂、和脱模剂。所述添加剂包括uv抑制剂。另外的组分用于提高材料的可加工性和盖的性能。低于约30%的玻璃纤维增强聚合物基体制剂是包含不饱和聚酯树脂和热塑性添加剂的石油基产品,剩余部分是无机或矿物填料、和切成例如1英寸长度的增强玻璃纤维。矿物填料可包括例如三水合氧化铝、碳酸钙、滑石或粘土。聚合物材料当在热和压力下固化时经历交联反应。良好的耐热性是所有热固性材料的特性,并且其与热塑性材料的不同之处在于,一旦该化合物固化成刚性固体,则其不会在升高的温度下软化或者在较低温度下变脆。所述盖在宽的温度范围内保留了其原始材料性质和尺寸精度。通过使用邻苯二甲酸系树脂、作为用于收缩控制的低量添加剂的聚苯乙烯、和三水合氧化铝填料的组合,使uv耐性最佳化,产生对抗风化的最好结果。低水平的有机材料与使用无机填料如三水合氧化铝的结合导致材料具有高阻燃性。使用ulbulletin94方案作为量度,该材料表现出最高可能的5v易燃性等级。参照图2,将玻璃纤维增强聚合物基体制造成连续的片材12。将经混合的树脂糊料14转移至刮刀箱16,其中使树脂糊料14沉积到从刮刀箱正下方通过的移动载体膜18上。刮刀箱控制施加至载体膜的树脂糊料的量。将玻璃纤维粗纱20供应至经树脂覆盖的载体膜上面的旋转切割器22中。使短切玻璃纤维24随机地沉积到树脂糊料上。所沉积的短切玻璃纤维的量通过切割器和载体膜速度来控制。在切碎操作的下游,第二载体膜26通过第二刮刀箱16也用树脂糊料14涂覆,并且将其树脂侧向下地铺在短切纤维24之上。该过程产生了树脂糊料和玻璃纤维的夹心层,然后将所述夹心层运送通过一系列压实辊28,其中玻璃纤维被树脂糊料浸湿并且将空气从片材12中挤出,以产生玻璃纤维和树脂的均匀片材。在玻璃纤维增强聚合物基体片材可用于模制之前,其必须熟化。该熟化时间是允许相对低粘度的树脂进行化学增稠所必需的。将片材保持在室温下直至达到期望的模制粘度。当片材准备好进行模制时,将其切割成预定尺寸的片。如图3所示,然后将所切割的片堆叠并组装成装料模料30,所述装料模料30是填充模具31中的模腔的最佳形状和体积。然后对装料模料进行称重以校验正确的装料重量。然后在预定位置中,将预组装的装料放置在经加热的模具表面34上。模具31是包括腔模32和芯模36的机构钢模的匹配套件。模腔位于腔模与芯模之间。加热模具,例如通过蒸汽加热。在将装料放置在模腔中之后,封闭模具并压紧装料。纤维增强聚合物基体材料是可流动的混配物,并且在热和压力下从稠的糊料转化成粘弹性状态的极低和经优化的粘度的液体。材料流动以填充模腔。如图4所示,腔模32和芯模36通过叠缩式剪切边缘38接合,所述叠缩式剪切边缘38提供芯模与腔模之间的间隙以允许芯模进入腔模。叠缩式剪切边缘允许在该过程的模制或压紧阶段期间控制材料。剪切边缘处的间隙允许在材料的流动前端之前的空气逸出。剪切边缘的小间隙允许空气通过,但是其太小而不允许大量聚合物材料通过。将模具保持封闭预定量的时间以使罩固化。在固化之后,打开模具并使用集成的排出销将罩从芯的模具表面排出。将经热模制的盖放置在冷却架中并在机械加工操作之前允许其冷却至室温。再次参照图3,模具31包括用于排出成品模制部件的排出器系统40。模具可以由例如a-36工具钢制成,但是也可使用其他材料。芯模和腔模通过工具中的构件(例如,对准销和对准衬套)对准。止动垫用于控制部件厚度。如图5所示,芯模和腔模设置有控制区块温度的装置。例如,可以并入蒸汽罐41。通过热电偶42监测模具的温度。蒸汽罐是这样的密封腔44:所述密封腔44具有由外周边48包围的内支承件46且用另外的板50密封以维持压力和控制蒸汽。蒸汽罐用于芯模和腔模两者中并且允许使用蒸汽向模具表面34提供持续且均匀的热传递。与钻孔线相比,蒸汽罐腔的表面区域允许产生用于传递的增加的表面区域。控制区块温度的其他装置可包括与油或电加热元件一起使用的钻通的孔或槽。参照图6,排出器系统40包括用于在模制过程结束时将模制部件从芯模36中推出的排出销52。排出器系统包括推动一组排出销的排出器板54,所述排出销与芯模的顶部或从芯模中抬起的部件的底部齐平。排出销52通过保持板56保持在排出器板54上,所述保持板56具有卡住排出销头的埋头孔(counterboredhole)。排出器板组合件通过导销58和衬套60来引导。排出器板通过受模制循环控制的液压缸61(图3)来驱动。排出器板的驱动可以通过设备中的其他装置如链杆或脱模杆(knockoutbar)来实现。排出器板组合件由栏杆62、支承柱64和底板66来支承。排出器板还为加热模具提供了用于蒸汽的钻孔。模具组合件的顶部、底部和侧部可以是隔热的以保持该过程所需的热。其还隔绝来自制造部件的机器或液压机的热。用于本发明一个实施方案的示例性制造方法混合和储存将聚合物制剂输入自动化递送系统中。该系统负责将所有成分混合在一起,储存聚合物基体,然后将其递送至混配机,例如schmidtandheinzmann(s&h)混配机。将制剂混合以确保材料是均匀的。控制器操纵添加的顺序、停留时间、叶片速度和混合温度。糊料基体混合循环完成后,进行数个测试以确认糊料在释放至容纳槽之前是正确的。容纳槽的主要功能是储存。在储存过程期间,通过低剪切混合叶片搅动糊料基体。如果天气低于65℉,则使用水毯以确保糊料不损失温度。该损失可影响增稠响应并且不利地影响材料的可模制性。将容纳槽放置在天平上,并且在制造期间按重量连续计量送入混配机中。聚合物基体仍然不具有颜色或增稠剂(聚合物增量剂)。分开添加这些成分中的两者以确保没有由于维护不恰当而产生的任何颜色的交叉污染或不利的增稠。测试“b级料”组分以在其释放至生产之前确认期望的制剂。当需要制剂的柔性时,通常使用分批混合。当用一种制剂制造盖时,可采用连续法。这允许混合过程适应一种具体制剂。所有成分被连续地供应至混合器(通常为挤出机)中。将其在挤出机中共混在一起并引入混配机中。该方法消除了b边料的进料和混合所需的另外的设备。基体和b级料的递送自动化递送系统将确定制造所需的泵速率。该系统将基于基体比重、产物重量、玻璃百分比和片材重量来确定每小时递送至混配机中的糊料的量。基体与b边料通过穿过一系列高剪切罩型混合叶片或静态混合器来组合。然后将经混合的材料储存在缓冲槽(surgetank)中并用stater泵递送至混配机中。混配机上的刮片内侧是高度传感器。通过自动化递送系统控制刮刀箱中材料的高度。混配混配机器的许多变量可以改变,例如:表1机器优选值范围带速度5m/分钟3m/分钟至20m/分钟切割器速度167rpm100rpm至668rpm进料辊2.5巴1巴至5巴橡胶辊3.5巴1巴至5巴振动2.0巴1巴至5巴卷绕计量器250rpm100rpm至300rpm容纳槽温度95℉±5℉60℉至120℉最终混合器槽温度95℉±5℉60℉至120℉刮刀箱下板高度0.069"0.050"至0.120"上板高度0.069"0.050"至0.120"板侧高度0.065"0.020"至0.100"水平sp#138mm20mm至80mm水平sp#238mm20mm至80mm多层膜上膜张力6.0巴2巴至10巴下膜张力6.0巴2巴至10巴片材宽度341/2"10"至80"偏转器宽度351/8"8"至82"压实单元带张力(上)4巴2巴至10巴带张力(下)4巴2巴至10巴浸渍桥接器下限9.5巴4巴至12巴塔式卷绕器4巴2巴至8巴压平辊上/下上上/下由于材料的比重是已知的,所以可以基于材料的产物重量来确定刮片的高度。混配物的产物重量通过每单位面积的重量来测量。通常,重量以克/ft2为单位来测量。也可以测量玻璃纤维组分。切碎器的rpm随着玻璃纤维的重量线性改变。混配物的产物重量为545g/ft2。在整个作业中提取糊料样品(基体和b边料一起)并用粘度计进行测量。典型的测量在最初、24小时、和36小时至60小时时进行。当确定增稠曲线时考虑数个变量:温度、最初粘度和模制粘度。在之前的混配和材料试验的基础上对这些值进行优化。当树脂或增稠剂的批号改变时,进行增稠研究以确定是否需要改变水平。材料的目标模制粘度为20mmcps至45mmcps。粘度测量用brookfielddv-ii进行。在将聚合物基体引入玻璃纤维中之后,然后在蛇纹辊之间将片材挤压在一起以浸湿玻璃纤维。由于该过程产生了结构部件,所以使用ft2模板切割材料样品。如果其落入预定范围内,则材料适于释放。收集产物重量样品并将其用于模制实验室面板。在模制期间,传感器检测材料的介电性质并且确定材料的凝胶化和固化时间。然后将经固化的面板切割成多个样品用于测试。典型的测试包括拉伸强度、弯曲强度、比重、玻璃纤维含量和吸水性。表2制造之后24小时在模制的0.120"厚的面板上测量物理性质。模制条件:在330℉下3分钟。模制压力=200psi。覆盖率=60%一旦材料达到品质测试的预定值,就将材料释放至生产中。模制方法frpm●将纤维增强聚合物基体(frpm)混配物递送至辊车(rollercart)上的自对准驱动模具(saam)区域,所述辊车容纳各自重量约为200磅至500磅或者在箱中为500磅至6000磅的混配物的(8)个辊。●每个辊具有标识制造日期、配方、批次#、辊#和重量的标签。不释放材料,直至其通过如混配部分中所详述的所有qc要求。●所述车进入自动化纵切器位于其中的frpm切割区域。●参照saam生产模制操作手册(saamproductionmoldingoperationnotebook),其示出用于待模制的特定盖的装料尺寸和重量。●一旦片材位置正确,切割片材并且纵切器设定为自动切割装料以改变混配物的尺寸并使其脱膜。●然后将经切割的装料片材称重至正确的装料重量并且堆叠成完整的独立装料堆以准备制造。saam压机●saam系统能够在不需要安装坑的情况下设计&安装大压板面积的压机。也可使用其他压机类型。●自对准压机的使用通过翻转供应压榨吨位(pressingtonnage)的液压缸来实现。●使用自对准压机还允许压机位置的任何改变,以满足生产需求的任何改变,以在对生产设施最小破坏的情况下进行。●为了支持saam生产模制系统,开发专门的低压模制混配物(lpmc)并且frpm(纤维增强聚合物材料)为lpmc的一种形式。●platensaam系统允许钢制工具(模具)以正常方式互换。●目前的工具如下:●15"圆形物(1400)●13"×24"盖模具(1324)●17"×30"盖模具(1730)●24"×36"盖模具(2436)●24"×48"盖模具(2448)●分割式30"×48"盖模具(3048)●典型的saam操作压力:3,000psi●缸内径:12英寸●棒直径:5.5英寸●缸的有效面积:89.34平方英寸●在3,000psi液压下,缸产生268,017磅的力●因此,四(4)个缸产生总计1,072,068磅/536吨的力●17"×30"盖具有17"×30":510平方英寸的平面视图表面积●1,072,068磅的力除以510平方英寸等于2,102psi的模制压力●24"×36"盖具有24"×36":864平方英寸的平面视图表面积●1,072,068磅的力除以864平方英寸等于1,241psi的模制压力●24"×30"盖具有24"×30":720平方英寸的平面视图表面积●1,072,068磅的力除以720平方英寸等于1,489psi的模制压力。●当在同一saam中进行双联模制时,模制压力减半。●因为平面视图表面积小于总表面积,所以当使用平面视图面积时,使用约400psi的模制压力。模制过程●将压机预热以确保合适的设定。●在主控制设定(mastercontrolsettings)手册中查询用于待模制的特定盖的片材并且将屏幕1和2设置为合适的控制设定。该主控制设定记录表显示出以下中每一个的合适设定:●操作者查看主控制板上的温度指示器以看到模具是否升高至合适的温度,上部工具为325℉至270℉并且下部工具为320℉至265℉。●检查屏幕后,操作者取手持温度计并验证模具温度匹配由热电偶得到的屏幕读数。还验证了上部模具总是比下部模具热,以避免任何叠缩式剪切边缘模具撞击。●验证了温度后,然后操作者目视检查模具表面的清洁度,以及碎片或浮渣的任何迹象。如果看见任何迹象,则用黄铜工具和空气流除去。●然后将压机设定为自动模式并准备好用于模制第一部件。模制操作●检查并测量所递送的装料以确保其是正确的尺寸和重量。将第一装料放在天平上并记下重量。在过程数据&参数主控制设定记录表(processdata¶metersmastercontrolsettingsrecordsheet)中,有标题“装料尺寸(chargedimensions)”。在该标题下是以下行项目,包括关于装料(例如,17×30(1730)装料)的合适信息:●一旦确定装料满足规格,按下绿色“循环启动(cyclestart)”按钮以启动自动模制循环并且模具降至装载位置(loadposition)。●一旦模具停止至装载位置,就通过装载装置将装料递送至模具并使装料精确地定位在下部模具上,在每个方向上都居中。●装载工具一退出模具参数,操作者就再次按下绿色“循环启动”按钮并且压机从“减速位置(slowdownposition)”降至“封闭位置(closedposition)”。一旦压机传感器确定每个角落均在全部封闭位置,就开始“固化时间(curetime)”循环。●当自动化循环启动时,操作者检查下一个装料并将其放置在天平上,再次验证重量。●在固化时间循环完成之后,空气提升阀自动启动并且压机打开至慢速(slowspeed)位置,然后打开至快速(fastspeed)并返回至循环的打开位置(openposition)设置。●当压机打开至打开位置,并且模具清除了排出销的全部延长尺寸并达到预设间隙高度时,启动排出器系统并且部件从下模具表面上升高至排出销的全部高度。●排出器达到全部高度后,将卸载工具(unloadtool)插入部件之下并且排出棒自动降低。●一旦排出器回到完全静止位置,卸载工具就延伸至压机的前面并且将部件递送至操作者以进行目视检查,去除飞边并放置在冷却车中。●一旦将部件和卸载工具从压机参数中除去,操作者目视检查模具表面并且用空气流清除碎片。循环重新开始,重复每个所记录的步骤。机械加工●每个冷却车处理多个部件。当所述车被填满时,将其从saam区域中移出并放置在暂存区(stagingarea)以冷却和稳定。在此期间,通过qc随机检查部件并且验证其符合尺寸、重量和外观的品质规格。●在对部件进行任何机械加工之前,需要将部件冷却至低于150℉。该冷却过程确保了部件在机械加工之前的尺寸稳定性和平坦度(flatness)。●机械加工操作者将查看计算机数控(cnc)操作手册中包括的启动检查表,一旦检查表完成,就将机器设定为与待机械加工的具有一定尺寸的盖相对应的适当的机械加工程序。●cnc被编程为一次机械加工一个部件。每个盖具有其特有的程序。●操作者将部件从冷却车中移出并将其放置在指定位置用于进行机械加工循环。●一旦部件定位,操作者就启动真空以保持部件在合适位置。操作者按下绿色循环启动按钮并且cnc验证真空被启动并且然后从中心原位移动以验证部件在合适位置,一旦由机器验证,其将自动地在cnc床外侧端上开始部件的机械加工。●当完成该机械加工时,操作者将下一个部件放置在其在cnc床内侧端上的位置。●一旦机械加工完成,cnc将返回至中心静止(centerrest)位置并且在完成的部件上释放真空。操作者在下一个部件上再次启动真空并且然后按下绿色循环启动按钮。●在机械加工期间,操作者将移出先前经机械加工的部件,进行目视检查,擦拭,吹扫并放置在平台上以运输用于最终的组装。再次参照图1,盖或罩10包括最上表面70,其基本上是平坦的并且当安装在库或坑上时与地表面持平。如图8所示,底侧74具有包围盖周边的外缘76与凹入的内部区域或腔78。该腔具有允许连接附件(本文随后将更详细地讨论)的特征80和82以及用于连接至库的通孔84。多个连续支承肋材86在腔内从外缘的相对侧延伸。使支承肋材间隔开以转移载荷并且使盖在对外缘施加载荷下的挠曲最小化。如图9所示,外缘通过库的外壁90中的横挡(ledge)88支承。虽然显示出盖通过库壁中的横挡88来支承,但是也考虑了库的其他类型的支承凹部以支承盖。肋材86(例如,三个)不间断地横向延伸以跨越边缘周边的相对侧之间的腔。如图10所示,测试了另外的设计以确定盖94的腔92内另外的支承结构的效果。肋材86(如图8所示)优于并入了延伸腔长度或部分的交叉肋材96的另外的设计。图10的盖还并入有交叉枢纽98,并且通过测试显示出单独的肋材86就改善了承载能力并因此交叉肋材96和枢纽98是不必要的。表3所示的测试结果说明:当移除交叉肋材96、枢纽98和小肋材100时,包含本文所公开的聚合物材料的图8所示的盖设计产生了更大的承载能力。表3此外,图11所示的更深的肋材86产生最大的承载能力。肋材86还可具有弯曲外半径102,使肋材在中心具有比在外缘的接合处更高的高度。如图12和13所示,上表面70包括由模具表面中不同深度处的特征模式产生的纹理化表面104或表面条件。纹理化表面104包括平坦表面的深度变化,其向所述表面产生轻微凸起105,以在模制期间将材料的玻璃纤维24推离该表面,产生富含树脂的表面107。使玻璃纤维24远离纹理化表面增加了盖的长期耐气候性。例如,纹理化表面是科林斯式纹理。使用saej2527测试,当暴露500小时时,纹理和uv稳定性的组合产生小于9.0的δe值。上表面70还包括一系列不同高度的凸部106以产生抓紧表面。在不同高度下模制凸部106以允许产生盖的表面中的凸出转变。凸部以交替组的模式布置,以允许另外的边缘表面抓紧可与盖顶部接触的移动表面,例如车辆轮胎。凸部产生了更多的表面区域用于接触柔性材料。凸部的结果是所述表面使盖满足防滑性要求。虽然图12示出了三个具有圆端的棒的交替系列的凸部图案,但是应理解,其他几何形状和尺寸以及布置也可产生需要的胎面图案或防滑性表面。本发明的盖满足的其他测试要求如下:与聚合物盖相关的规格:以行业公认的标准测试盖:耐化学性,根据:telcordiar3-14和astmd543-06紫外光暴露,根据:astmg154防霉性,根据:astmg21可燃性,根据:ul94-5va和astmd635-06吸水性,根据:astmd570-05以行业公认的标准测试盖:as4586:2013新人行表面材料的防滑分类(slipresistanceclassificationofnewpedestriansurfacematerials)–附录a。ansi/scte77-2010,地下围护完整性规范(specificationforundergroundenclosureintegrity),scte,2010gr-902-core,手孔及其他地下接合库的一般要求(genericrequirementsforhandholesandotherbelow-groundsplicevaults),telcordia,2013astmc857-11,地下预铸混凝土设施结构的最小结构设计负荷的标准规程(standardpracticefor分钟imumstructuraldesignloadingforundergroundprecastconcreteutilitystructures),astm,2011as39962006,入口盖和格栅(accesscoversandgrates)bsen124:1994合并修正案no.1车辆和人行区域的沟渠盖和探孔盖–设计要求、型号试验、标志、质量控制(gullytopsandmanholetopsforvehicularandpedestrianareas–designrequirements,typetesting,marking,qualitycontrol)如图1所示,上表面70具有用于连接标识构件109(例如,图14所示的所有权标记)的凹部108。所有权标记具有延伸到孔110中的立柱。如果要改变盖的所有权,则可以移动并交换标识标记。再次参照图1,盖包括延伸穿过盖的孔112和114,以允许进行拧紧螺栓或固定锁定的方法以将盖连接至库。如图14所示,l型螺栓116或者贯穿螺栓118穿过孔112或114并旋转以接合位于如图15所示的库的壁中的凹槽120。l型螺栓116保留在壳体122中,壳体122连接至位于盖底侧的紧固特征82。如图16所示,凸缘124连接至紧固表面80,接合库的壁90中的凹槽126。除了申请人的美国专利no.7,547,051(其内容通过引用整体并入本文)中所示的l型螺栓结构以外,还可使用其他类型的紧固机构。例如,盖可以使用图17中所示并且在申请人的美国专利no.8,220,298(其内容通过引用并入本文)中详细说明的用于将盖连接至库的自锁和锁定组合件127。没有用于特定连接系统的任何未使用的孔112、114可用可拆卸插塞130(图14)封闭,所述可拆卸插塞130可以在任何时间被移除以并入不同的固定方法。如图1所示,盖包括用于将盖从库中提起的镐孔132。如图18所示,镐孔保持槽134(也在图8中示出)位于镐孔132中,所述镐孔132具有跨过开口位于凹部中的杆136,其可以被钩接合以将盖从库中提起。如图14所示,盖包括防止碎片在使用期间在镐孔内聚集的镐孔帽138。申请人的美国专利no.8,708,183(其全部内容通过引用并入本文)中说明了用于将盖从库中提起的镐孔保持槽的另外的特性和特征。如图19所示,可通过使用机器人技术140使模制和机械加工操作自动化。具有可编程逻辑控制器的机器人142从中间位置移动至装料装载站144,在装料装载站144中操作者将装料模料146装载在位于机器人臂150一端的装载机148上。然后,机器人的可编程逻辑控制器将装载机移动至面向模具压机31的中间位置。机器人在中间位置等待直到模具压机打开并且控制器确保部件已卸载并且模具的排出设备缩回。然后机器人移动至打开的压机并且将装料装载机148放到模具31的腔43中。控制器使装载机启动以使装料落在模腔中并且将装载机从模具中缩回。在模制过程完成和将经模制的罩从模具中排出时,机器人包括叠缩器(retractor)152,所述叠缩器包括板154和一系列吸盘156。控制器在正确的循环时间打开压机并且启动罩排出机构,其中机器人将叠缩器152放在经模制的罩上,使得吸盘156可以接合罩并将经模制的罩移动至输送机系统158并将罩释放到输送机系统上。然后,输送机系统将模制的罩递送至机械加工站160,所述机械加工站160包括多个旋转的刷162以去掉经模制的罩的毛刺。机械加工站还包括钻出用于库连接机构的孔。罩的最终组装包括:将镐孔杆放置在镐孔槽的凹部中,以及将槽和帽固定至盖,将标识标记固定至盖,通过螺栓或自锁机构与保持凸缘一起固定l型螺栓,以及用帽堵塞未使用连接机构的孔。虽然本发明关于本文的多个实施方案已进行了说明和描述,但是应理解,在其中可以做出改变和修改,所述改变和修改在本文要求保护的本发明的全部预期范围内。本发明还涉及以下实施方案:1.一种用于库的纤维增强聚合物材料盖,包含不饱和聚酯热固性树脂基体、纤维增强材料和无机填料,并且用片材模制方法制造。2.根据实施方案1所述的盖,还包含低量添加剂、固化引发剂、增稠剂、加工助剂和脱模剂。3.根据实施方案1所述的盖,还包含uv稳定颜料。4.根据实施方案1所述的盖,其中所述树脂基体包含uv抑制剂。5.根据实施方案1所述的盖,其中聚酯树脂是邻苯二甲酸系树脂。6.根据实施方案5所述的盖,其中所述邻苯二甲酸系树脂占所述纤维增强聚合物材料的约10%至约40%。7.根据实施方案1所述的盖,其中所述树脂基体包含聚苯乙烯。8.根据实施方案7所述的盖,其中所述聚苯乙烯占所述纤维增强聚合物材料的约5%至约30%。9.根据实施方案1所述的盖,其中所述纤维增强材料是短切玻璃纤维。10.根据实施方案9所述的盖,其中所述短切玻璃纤维占所述纤维增强聚合物材料的约5%至约60%。11.根据实施方案1所述的盖,其中无机材料占所述纤维增强聚合物材料的约15%至约50%。12.根据实施方案1所述的盖,其中无机材料是矿物。13.根据实施方案12所述的盖,其中所述矿物是三水合氧化铝。14.一种用于设施坑的纤维增强聚合物材料罩,包括:基本上平坦的上表面;具有外周边缘与凹入的内部腔的底表面;至少一个连续支承肋材,其由所述外周边缘的相对侧延伸穿过所述凹入的内部腔,以转移置于所述罩上的载荷并使向所述外周边缘施加载荷下的挠曲最小化。15.根据实施方案14所述的罩,其中所述至少一个支承肋材不间断地延伸穿过所述腔并且不包括任何交叉的支承肋材。16.根据实施方案14所述的罩,其中所述基本上平坦的上表面是纹理化的。17.根据实施方案16所述的罩,其中所述罩包含耐uv不饱和聚酯热固性树脂基体和玻璃纤维增强材料,其中纹理化的上表面包括向所述上表面中的凸起,在所述玻璃纤维增强材料上产生富含树脂的层。18.根据实施方案17所述的罩,其中所述纹理化的上表面是科林斯式纹理。19.根据实施方案14所述的罩,其中所述基本上平坦的上表面包含在所述基本上平坦的上表面之上延伸的凸部图案。20.根据实施方案19所述的罩,其中所述凸部具有多个不同的高度。21.根据实施方案14所述的罩,其中所述平坦的上表面具有用于使标识标记附着的凹部。22.根据实施方案14所述的罩,其中所述罩具有用于将所述罩固定至所述设施坑的装置。23.根据实施方案22所述的罩,其中用于将所述罩固定至所述设施坑的装置包括延伸穿过通过所述罩的凹部的螺栓。24.根据实施方案22所述的罩,其中用于将所述罩固定至所述设施坑的装置包括自锁的锁定组合件。25.根据实施方案14所述的罩,还包括用于将所述罩从所述设施坑中移出的提罩槽。26.一种用于库的盖,包含:玻璃纤维增强聚合物材料层,设置其大小以放置在所述库的开口上;在所述玻璃纤维增强聚合物材料层中的uv抑制剂;以及基本上平坦的上表面,其具有延伸到所述平坦的上表面中的凸起纹理,在所述玻璃纤维增强聚合物材料的各个玻璃纤维上产生富含树脂的层。27.根据实施方案26所述的盖,还包含在所述基本上平坦的上表面之上延伸的凸部图案。28.根据实施方案27所述的盖,其中所述凸部包括纹理并且具有至少两个不同的高度。当前第1页12