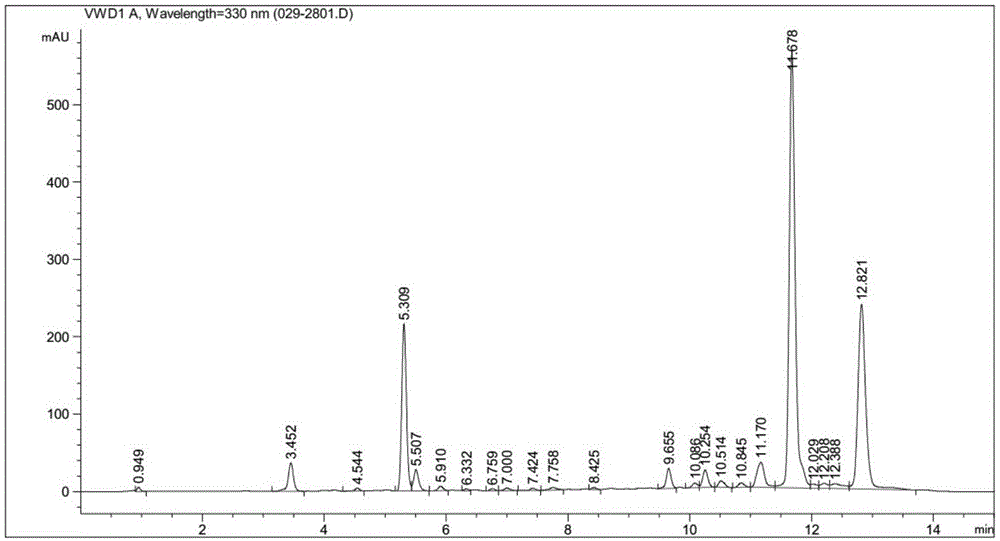
本发明属于植物提取物
技术领域:
,涉及一种同步高效制备甜叶菊绿原酸和甜菊糖苷的工业化方法。
背景技术:
:甜叶菊(steviarebaudiana)属菊科多年生草本植物,原产于南美巴拉圭和巴西,是目前已知甜度较高的糖料植物之一,已成为继蔗糖、甜菜糖之后的第三种天然糖源。目前,中国是世界最大的甜菊糖苷生产及供应国,占全球总量的80%以上。甜叶菊中除甜菊糖苷外还含有较高含量的酚类,且这些酚类物质具有重要的生物活性,在其发源地作为甜茶、药茶饮用已有一百多年的历史。甜菊糖苷为甜叶菊中的甜味成分,为贝壳杉烯二萜苷类物质,分子中含有多个糖基片段,易溶于水,是一种零热量的高倍甜味剂(其热量为蔗糖的300-500倍)。gb8270-2014中规定的指标成分主要包括:甜菊苷、瑞鲍迪苷a、瑞鲍迪苷b、瑞鲍迪苷c、瑞鲍迪苷d、瑞鲍迪苷f、杜克苷a、甜茶苷、甜菊双糖苷等9种成分。甜叶菊中的酚类物质的主要为绿原酸(原料含量4-6%,hplc),其中二咖啡酰基取代的异绿原酸占总酸比例达80%。研究表明,异绿原酸具有抗氧化(j.agric.foodchem.,2004,52(15),4893),抗炎(j.nat.prod.,1995,58(5),639),抗菌、抗病毒(jashs,2008,133(4),492;fitoterapia,2012,83,1281;plosone,2011,6(4),18127;j.ethnopharmacol,2006,106(2),187)等多种重要的生物功效。传统甜菊行业均采用水提取,但提取过程中异绿原酸易发生水解,如图1-3所示,水提取液中异绿原酸(二咖啡酰奎宁酸)占比大幅降低、单咖啡酰基奎宁酸及咖啡酸比例大幅升高,该专利技术所得产品所含异绿原酸比例和原料接近。对于甜叶菊中的酚类物质和甜菊糖苷的分离多通过树脂分离实现,如专利200710111313.4和201610745221,均是利用甜叶菊中酚类物质和糖苷极性差异,通过树脂环节实现了两类成分的分离,采用该方法,甜叶菊酚类物质和糖苷之间存在竞争吸附,吸附过程甜叶菊绿原酸占用部分甜菊糖苷吸附位点,使甜菊糖苷的树脂吸附量降低,导致生产效率降低、生产成本升高。而该申请专利技术,在吸附树脂前实现了甜叶菊绿原酸和甜菊糖苷的分离,避免了该类问题的发生。相较于单咖啡酰基绿原酸,异绿原酸极性较小,脂溶性增强(单咖啡酰基绿原酸易溶于水,25℃水中溶解度为4%,极微溶于醋酸乙酯,难溶于亲脂性有机溶剂)。该专利技术利用甜叶菊绿原酸的溶解特性,通过萃取将其和甜菊糖苷分离。专利cn102617667b中采用了有机溶剂萃取对甜叶菊中绿原酸成分进行了分离。但绿原酸在水中仍具有一定的溶解性,如直接萃取,效果不理想,只能得到部分绿原酸产品,如对比专利cn102617667b中,从专利cn102617667b所得产品谱图附图1看,17.808min对应的峰为主要成分(占比约40%),但产品谱图(附图2和3)中并未得到该成分。如前所述,甜叶菊绿原酸具有重要的生物功效,截止目前为止,市场上仍然没有相关的产品推出,主要原因:(1)传统水提取过程,甜叶菊中异绿原酸发生水解,且该过程受酶及温度等多种因素影响,过程不易控制,甜叶菊异绿原酸含量降低,产品质量稳定性差。(2)甜菊糖苷和甜叶菊绿原酸极性接近分离困难。技术实现要素:由于上述缺陷,本发明提供了一种同步高效制备甜叶菊绿原酸和甜菊糖苷的工业化方法,克服了上述技术困难,在保证甜菊糖苷质量和甜叶菊绿原酸功效成分不被破坏的前提下,可同时实现甜叶菊绿原酸和甜菊糖苷的工业化生产,对推动甜菊资源的综合利用奠定基础。此外,和传统的水提取工艺相比,该工艺还有效的降低了生产水耗,减少污水及絮凝渣的排放,为一种高效益的绿色生产工艺,可大幅度推进行业进步。发明人于研究中发现,传统甜菊行业均采用水提取,但提取过程中异绿原酸易发生水解,水提取液中绿原酸占比大幅降低、单咖啡酰基奎宁酸及咖啡酸比例大幅升高,且该过程受酶及温度等多种因素影响,过程不易控制,使甜叶菊绿原酸含量降低,产品质量稳定性差。为提高甜叶菊综合利用价值、加快其综合利用进程,本发明提供了一种同步制备甜叶菊绿原酸和甜菊糖苷的工业化方法。为实现上述发明目的,本发明采用以下技术方案予以实现:一种同步制备甜叶菊绿原酸和甜菊糖苷的工业化方法,包括如下步骤:以甜叶菊作为原料,经醇提后,调节料液状态,使绿原酸呈自由分子状态,再用与水不互溶的中极性的有机溶剂萃取分离,得到富集绿原酸的有机层以及富集甜菊糖苷的水层。所述调节料液状态使绿原酸呈自由分子状态,是以pka<4.7的试剂对料液进行调整,至绿原酸呈自由的分子状态;优选地,所述pka<4.7的试剂选自nah2po4、h3po4、hcl、nahso4、h2so4、h2co3、hno3、枸橼酸、蚁酸、草酸、琥珀酸、苯甲酸中的一种或几种的组合。所述醇提是以含1-3个碳原子的短链醇水溶液进行提取;优选地,所述短链醇水溶液的浓度至少75%;更优选地,在40-60℃进行提取。优选地,所述与水不互溶的中极性的有机溶剂的极性为2.0-4.5,更优选选自醋酸乙酯、二氯甲烷、氯仿、乙醚、丙醚中的一种或几种;进一步优选地,所述有机溶剂的体积用量是待萃取溶液的0.8-1.5倍。本发明所述的方法,在萃取前,以所述短链醇浸提甜叶菊,料液比为1:(3-7);优选地,所述醇提的步骤重复1-3次。进一步地,在醇提后、调整料液状态前,在温度50-60℃,真空度-0.08mpa条件下对醇提液进行浓缩;优选浓缩5-10倍。通过上述方法提取得到的富集甜叶菊绿原酸的提取物中,活性成分的比例和甜叶菊原料相接近,可知对活性物质几乎没有浪费。利用本发明所述的工业化方法,所得的富集甜叶菊绿原酸的提取物中,甜叶菊总异绿原酸纯度>60%。所述萃取分离得到的水层经树脂吸附分离后即得甜菊糖苷;所述树脂为低极性二乙烯苯型吸附树脂,所述树脂包括t28、ads-750、69m、dm30、201-h等;优选地,所述树脂的用量为分离所得水层重量的0.5-1倍。优选地,在树脂吸附前,对分离得到的水层调固含量至8-12%。调节固含量能够节省用水,减少污水。本发明所述的甜菊糖苷制备方法中,所述树脂吸附分离包括:甜菊糖吸附树脂、脱盐、脱色、精脱树脂分离纯化;优选地,所述吸附时的吸附流速为0.1-0.4bv/h。吸附完成后,进行后续水洗、解析,解析液经甜菊糖脱盐、脱色、精脱,干燥得甜菊糖苷产品。优选地,所述解析时选用短链醇溶液,其中,解析用短链醇溶液的浓度低于提取用短链醇溶液的浓度;进一步地,解析用短链醇溶液的浓度控制在70-75%;用量为1-2bv,解析时的流速为1-2bv/h。作为优选,本发明所述的同步制备甜叶菊绿原酸和甜菊糖苷方法包括如下步骤:(1)将甜叶菊粉末以短链醇提取,得提取液;(2)将提取液浓缩回收短链醇溶液,得浓缩液;(3)调节料液状态使绿原酸呈自由分子状态;(4)对(3)所得溶液萃取分离,取有机层得到甜叶菊绿原酸提取物;(5)对(4)所得水层进行树脂吸附,得到甜菊糖苷提取物。本发明克服了诸多技术困难(包括甜叶菊绿原酸提取过程易水解,以及甜菊糖苷和甜叶菊绿原酸无法分离的现状),提供了高效制备甜叶菊绿原酸和甜菊糖苷的工业化方法,在保证甜菊糖苷质量和甜叶菊绿原酸功效成分不被破坏的前提下,可同时实现甜叶菊绿原酸和甜菊糖苷的工业化生产,对推动甜菊资源的综合利用奠定基础。此外,和传统的水提取工艺相比,该工艺还有效的降低了生产水耗,减少污水及絮凝渣的排放,为一种高效益的绿色生产工艺,可大幅度推进行业进步。本发明同时提供依据上述任一项技术方案所制备得到的甜叶菊绿原酸提取物和甜菊糖苷提取物。优选地,所述甜叶菊绿原酸提取物中,异绿原酸纯度(含量)>60%。采用上述技术方案所产生的有益效果是:(1)较传统水提取工艺,该专利公布的提取技术可防止甜叶菊异绿原酸成分的水解,以保证甜叶菊绿原酸产品的有效成分含量及功效。(2)该工艺在不影响甜菊糖苷产品质量和生产效率的前期下,实现了甜叶菊绿原酸的有效分离,生产效率大幅提高,所得产品所含异绿原酸比例和原料接近。(3)和传统的水提取工艺相比,该工艺大幅降低了生产水耗,减少污水及絮凝渣的排放,为一种高效益的绿色生产工艺,可大幅度推进行业进步。附图说明图1为甜叶菊原料中绿原酸谱图;图2为甜叶菊水提取液中绿原酸谱图;图3为实施例2所得产品中绿原酸谱图。具体实施方式以下实施例用于说明本发明,但不用来限制本发明的范围。实施例1本发明提供一种制备甜叶菊绿原酸的工业化方法及所得产品,具体步骤如下:(1)称取甜叶菊粉末1kg,85%的乙醇水溶液为提取液,料液比分别为1∶5/3.5/3.5,50℃提取三次,第1遍提取时间为1.5h,2、3遍提取时间均为1h,合并滤液作为提取液。(2)提取液水浴60℃、真空-0.08mpa条件下10倍浓缩回收乙醇。(3)使用电位滴定仪进行在线监测,使用h3po4水溶液调整料液状态,且过程中不断搅拌,至电极电位发生突跃时停止加液。(4)使用等体积氯仿对上一工艺步骤所得料液萃取3次,有机相浓缩、树脂纯化后得到78.5g甜叶菊绿原酸产品,甜叶菊总绿原酸82%,异绿原酸含量为65%。实施例2本发明提供一种制备甜叶菊绿原酸的工业化方法及所得产品,具体步骤如下:(1)称取甜叶菊粉末1kg,95%的甲醇水溶液为提取液,料液比分别为1∶6/4.5,50℃提取两次,第1遍提取时间为1.5h,第2遍提取时间均为1h,合并滤液作为提取液。(2)提取液水浴60℃、真空-0.08mpa条件下10倍浓缩回收乙醇。(3)使用phs-3cph计进行在线监测,使用h2so4水溶液调整料液状态,且过程中不断搅拌,至电极电位为180mv停止加液。(4)使用等体积醋酸乙酯对上一工艺步骤所得料液萃取3次,有机相浓缩、树脂纯化后得到75.2g甜叶菊异绿原酸产品,甜叶菊总绿原酸含量为84%,异绿原酸含量为66.4%。实施例3本发明提供一种制备甜叶菊绿原酸的工业化方法及所得产品,具体步骤如下:(1)称取甜叶菊粉末1kg,75%的丙醇水溶液为提取液,料液比分别为1∶6/4.5,50℃提取两次,第1遍提取时间为1.5h,第2遍提取时间均为1h,合并滤液作为提取液。(2)提取液水浴60℃、真空-0.08mpa条件下10倍浓缩回收乙醇。(3)使用phs-3cph计进行在线监测,使用蚁酸水溶液,且过程中不断搅拌,至ph3.0停止加液。(4)使用等体积乙醚对上一工艺步骤所得料液萃取3次,有机相浓缩后、树脂纯化得到72.8g甜叶菊绿原酸产品,甜叶菊总绿原酸含量为90%,异绿原酸含量为73%。实施例4本实施例提供一种制备甜菊糖苷的工业化方法及所得产品,具体步骤如下:将实施例1中的步骤(4)中所得料液萃取3次后的水层调固含量10%后进行t28树脂吸附,树脂用量为1.5l,吸附流速0.2bv/h,吸附完成后2bv水洗,第1bv流速0.2bv/h,第2bv流速1bv/h。水洗完成后使用2bv70%的乙醇水溶液进行解析,解析流速1bv/h。解析液浓缩后进行脱盐、脱色、精脱、干燥,得99g甜菊糖苷产品,产品为白色粉末,tsg为94.3%,420nm透光度90.8%,1%浓度370nm比吸光0.012。实施例5本实施例提供一种制备甜菊糖苷的工业化方法及所得产品,具体步骤如下:将实施例2中的步骤(4)中所得料液萃取3次后的水层调固含量8%后进行201-h树脂吸附,树脂用量为1.5l,吸附流速0.25bv/h,吸附完成后2bv水洗,第1bv流速0.25bv/h,第2bv流速1bv/h。水洗完成后使用2bv70%的乙醇水溶液进行解析,解析流速1bv/h。解析液浓缩后进行脱盐、脱色、精脱、干燥,得100.5g甜菊糖苷产品,产品为白色粉末,tsg为92.9%,420nm透光度90.3%,1%浓度370nm比吸光0.015。实施例6本实施例提供一种制备甜菊糖苷的工业化方法及所得产品,具体步骤如下:将实施例3中的步骤(4)中所得料液萃取3次后的水层调固含量6%后进行dm30树脂吸附,树脂用量为1.5l,吸附流速0.3bv/h,吸附完成后2bv水洗,第1bv流速0.3bv/h,第2bv流速1bv/h。水洗完成后使用2bv70%的乙醇水溶液进行解析,解析流速1bv/h。解析液浓缩后进行脱盐、脱色、精脱、干燥,得99.7g甜菊糖苷产品,产品为白色粉末,tsg为93.6%,420nm透光度90.6%,1%浓度370nm比吸光0.010。对比例1本对比例提供一种制备甜菊糖苷和绿原酸的方法,采用中国专利公开号cn105001281b所提供的方法进行操作。所得提取物的绿原酸谱图见附图2。对比例2本对比例提供一种甜叶菊酚类和甜菊糖苷的分离方法,采用中国专利公开号cn106236808b所提供的方法进行操作。试验例1本试验例提供实施例2和对比例1(传统水提法)所提取得到的甜叶菊绿原酸部分成分的含量对比,如表1所示。其中甜叶菊原料的绿原酸谱图如附图1所示;甜叶菊水提物(对比例1)中绿原酸谱图如附图2所示;实施例2所得到的提取物中绿原酸谱图如附图3所示。表1试验例2本试验例提供实施例4-6和对比例1-3所提供的分离/制备甜菊糖苷的技术效果对比,如表2所示。表2检测指标对比例1对比例2实施例4实施例5实施例6tsg%909194.392.993.6透光度(420nm)818390.890.390.6比吸光(370nm)0.0310.0350.0120.0150.01本申请中总苷含量采用gb8270-2014方法进行测定,透光度为uv检测的14%固形物浓度420nm下的透光度,1%浓度的甜菊糖苷在370nm比吸光采用gb8270-1999方法进行测定,总绿原酸的含量及各成分比例采用t/cccmhpie1.17-2016方法进行测定。虽然,上文中已经用一般性说明、具体实施方式及试验,对本发明作了详尽的描述,但在本发明基础上,可以对之作一些修改或改进,这对本领域技术人员而言是显而易见的。因此,在不偏离本发明精神的基础上所做的这些修改或改进,均属于本发明要求保护的范围。当前第1页12