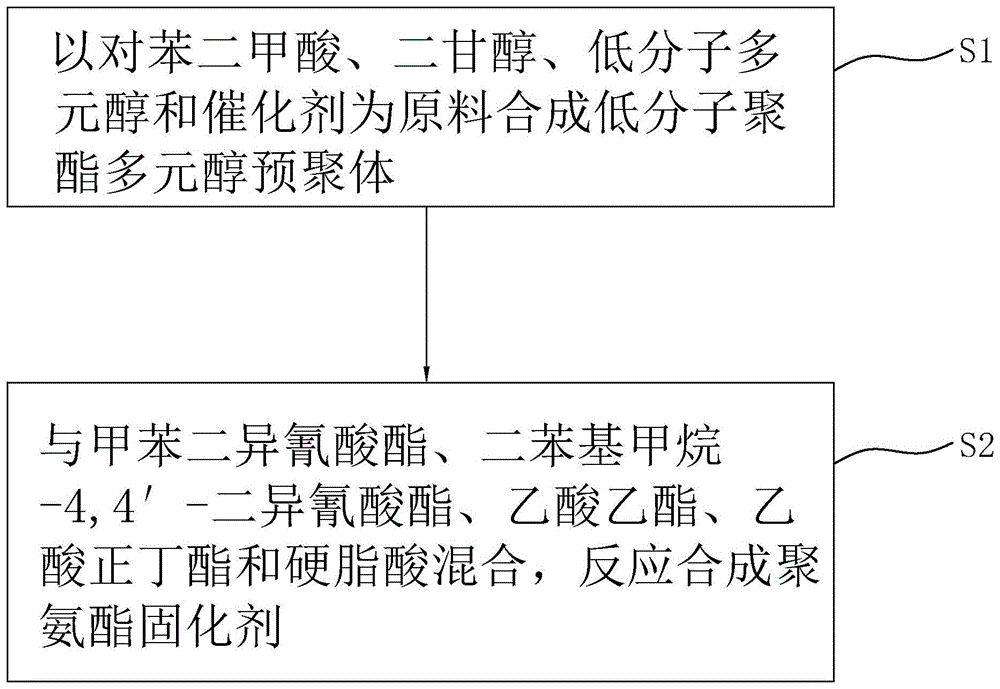
本发明涉及固化剂
技术领域:
,更具体地说,它涉及一种聚氨酯固化剂及其制备方法。
背景技术:
:聚氨酯涂料是目前较常见的一类涂料,可以分为双组分聚氨酯涂料和单组分聚氨酯涂料;双组分聚氨酯涂料一般是由异氰酸酯预聚物和含羟基树脂两部分组成,通常称为固化剂组分和主剂组分;其中固化剂又称为熟化剂或交联剂。聚氨酯涂料固化剂在常温是可以与树脂长期稳定共存,在热处理时该固化剂释放出来的异氰酸酯(-nco)基团与树脂分子链上羟基、羧基、氨基等基团反应形成交联网络,所得漆膜的交联度得以提高,使体系具有较高的抗性和耐性。在申请公布号为cn106589305a的中国发明申请专利中公开了一种甲苯二异氰酸酯-三羟甲基丙烷聚氨酯固化剂合成方法,其以甲苯二异氰酸酯和三羟甲基丙烷为主要加成原料,并加入其他氧化剂、溶剂等助剂合成聚氨酯固化剂,并提供了简单、方便操作的合成方法,得到的聚氨酯固化剂性能大大提高,安全可靠且配漆性能良好。但是甲苯二异氰酸酯和三羟甲基丙烷的价格较高,导致聚氨酯固化剂的合成成本大大提高。因此,需要提出一种新的方案来解决上述问题。技术实现要素:针对现有技术存在的不足,本发明的目的一在于提供一种聚氨酯固化剂,其具有性能优良、价格低廉的优点。本发明的目的二在于提供一种聚氨酯固化剂的制备方法,具有合成方法简单、操作方便的优点。为实现上述目的一,本发明提供了如下技术方案:一种聚氨酯固化剂,包括如下重量份数的组分:对苯二甲酸:5-10份;低分子多元醇:8-13份;二甘醇:5-8份;乙酸乙酯:10-15份;乙酸正丁酯:10-15份;甲苯二异氰酸酯:15-20份;二苯基甲烷-4,4′-二异氰酸酯:15-20份;催化剂:0.5-1份;分散剂:1-3份。通过采用上述技术方案,本发明预先合成一定支化度的低分子聚酯多元醇作为预聚体,代替常用的三羟甲基丙烷使用,再与二异氰酸酯进行加成反应,此外二异氰酸酯采用价格低且毒性小的二苯基甲烷-4,4′-二异氰酸酯与甲苯二异氰酸酯进行复配使用,既能改善性能,又能降低成本、减小污染。采用上述方式制得的聚氨酯固化剂除了具有传统固化剂相近的性能外,还具有价格低廉的优点。进一步优选为,所述低分子多元醇为1,4-丁二醇和蓖麻油的混合物,两者重量比为2:1。通过采用上述技术方案,低分子多元醇的羟基越多,固化剂对涂膜的附着力提升越大,但同样,涂膜的粘度较大,溶解性能不佳,通过采用1,4-丁二醇和蓖麻油复配使用,使得制成的固化剂性能较好,使用后涂膜的附着力较大,粘结强度高。进一步优选为,所述催化剂采用重量比为1:1的二月桂酸二丁基锡、二乙酸二丁基锡的组合物。通过采用上述技术方案,二乙酸二丁基锡的催化速度比二月桂酸二丁基锡快,采用二月桂酸二丁基锡与二乙酸二丁基锡复配使用时,在可以实现较快的催化速度的同时,也能降低体系中的醋酸气味。进一步优选为,所述分散剂为硬脂酸。通过采用上述技术方案,硬脂酸别名为十八碳烷酸,安全无毒,不会对人体健康造成影响,可以降低固化剂原料在反应合成时的团聚现象,提高原料之间的相容性和在溶剂中的溶解性。进一步优选为,所述聚氨酯固化剂还包括1-3重量份的三氧化二锑。通过采用上述技术方案,三氧化二锑具有良好的阻燃性,其加入到固化剂中可赋予涂膜良好的阻燃性。为实现上述目的二,本发明提供了如下技术方案:一种聚氨酯固化剂的制备方法,其特征在于,包括以下步骤:s1,按照相应的重量份数,将对苯二甲酸、二甘醇、低分子多元醇和催化剂投入到反应罐中,通氮气10min,并在氮气氛围下加热搅拌,控制温度230-250℃,每隔0.5h取样测定酸值,当酸值低于0.5mgkoh/g后,降温至25℃出料,得到低分子聚酯多元醇预聚体;s2,将甲苯二异氰酸酯、二苯基甲烷-4,4′-二异氰酸酯、乙酸乙酯、乙酸正丁酯和分散剂加入到反应罐中,搅拌升温至50-60℃,然后加入低分子聚酯多元醇预聚体,反应2-3h,升温至75℃,再加入催化剂,反应1-2h,降温至25℃出料,得到聚氨酯固化剂。通过采用上述技术方案,采用上述方式,先合成低分子聚酯多元醇的预聚体,然后再使其与二异氰酸酯反应合成,到了反应后期升温并加入催化剂,能够有效催化-nco与羟基的反应,提高转化率,进一步降低固化剂的粘度。采用上述合成方式,操作简单,用到合成设备较少,且合成的聚氨酯固化剂性能较为优良。进一步优选为,所述低分子聚酯多元醇的酸酯为0.3-0.5mgkoh/g。通过采用上述技术方案,端羧基与异氰酸酯反应生成酰胺并放出二氧化碳,不仅造成链终止,还形成气泡,而且聚酯中残留的酸还会对聚氨酯反应产生不良影响,降低聚氨酯的水解稳定性,所以低分子聚酯多元醇的酸酯控制较低,处在0.3-0.5mgkoh/g之间,此时合成的固化剂粘度较小。综上所述,与现有技术相比,本发明具有以下有益效果:(1)本发明预先合成一定支化度的低分子聚酯多元醇作为预聚体,代替常用三羟甲基丙烷使用,再与二异氰酸酯进行加成反应合成聚氨酯固化剂,所用原料价格低廉,且固化剂性能优良;(2)本发明的二异氰酸酯采用价格低且毒性小的二苯基甲烷-4,4′-二异氰酸酯与甲苯二异氰酸酯进行复配使用,既能改善性能,又能降低成本、减小污染;(3)本发明还提供了一种操作简单,所用设备较少的聚氨酯固化剂合成方法,反应条件易控,转化率较高,得到的固化剂附着力高,粘度低。附图说明图1为实施例1中聚氨酯固化剂的合成工艺流程图。具体实施方式下面结合附图1和实施例,对本发明进行详细描述。实施例1:一种聚氨酯固化剂,各组分及其相应的重量份数如表1所示,并通过如下步骤制备获得:s1,按照表1中相应的重量份数,将对苯二甲酸、二甘醇、低分子多元醇和催化剂依次投入到反应罐中,通氮气10min,以排出罐内空气,并在氮气氛围下进行加热搅拌,且反应温度为230℃,搅拌速度为100r/min,然后每隔0.5h取样测定酸值,当酸值低于0.5mgkoh/g后,本实施例中的反应体系酸酯测得为0.4mgkoh/g,降温至25℃出料,得到低分子聚酯多元醇预聚体,本实施例中,且得到的低分子聚酯多元醇预聚体的羟值为130mgkoh/g,;s2,按照表1中相应的重量份数,将甲苯二异氰酸酯、二苯基甲烷-4,4′-二异氰酸酯、乙酸乙酯、乙酸正丁酯和硬脂酸加入到反应罐中,在100r/min转速下,搅拌升温至50℃,然后加入低分子聚酯多元醇预聚体,反应3h,升温至75℃,再加入催化剂,反应1h,降温至25℃出料,得到聚氨酯固化剂,本实施例中,合成的聚氨酯固化剂的nco含量为12.13%。实施例2-6:一种聚氨酯固化剂,与实施例1的不同之处在于,各组分及其相应的重量份数如表1所示。表1实施例1-6中各组分及其重量份数实施例7:一种聚氨酯固化剂,与实施例6的不同之处在于,s2步骤具体设置为:将甲苯二异氰酸酯、二苯基甲烷-4,4′-二异氰酸酯、乙酸乙酯、乙酸正丁酯和硬脂酸加入到反应罐中,搅拌升温至60℃,然后加入低分子聚酯多元醇预聚体,反应2h,升温至75℃,再加入催化剂,反应2h,降温至25℃出料,得到聚氨酯固化剂。实施例8:一种聚氨酯固化剂,与实施例1的不同之处在于,s2步骤中,在加入催化剂时还加入1份三氧化二锑。实施例9:一种聚氨酯固化剂,与实施例6的不同之处在于,2步骤中,在加入催化剂时还加入3份三氧化二锑。对比例1:一种聚氨酯固化剂,以申请公布号为cn106589305a的中国发明申请专利中公开的一种甲苯二异氰酸酯-三羟甲基丙烷聚氨酯固化剂作为对比例1。对比例2:一种聚氨酯固化剂,与实施例1的不同之处在于,采用三羟甲基丙烷代替s1步骤得到的低分子聚酯多元醇预聚体。对比例3:一种聚氨酯固化剂,与实施例1的不同之处在于,s1步骤中的反应体系酸值控制为1mgkoh/g。对比例4:一种聚氨酯固化剂,与实施例1的不同之处在于,s1步骤中低分子聚酯多元醇预聚体的羟值控制为100mgkoh/g,s2步骤合成的聚氨酯固化剂的nco含量为6%。对比例5:一种聚氨酯固化剂,与实施例1的不同之处在于,s1步骤中1,4-丁二醇用量为12份,蓖麻油用量为6份。性能测试将实施例1-9和对比例1-5得到的聚氨酯固化剂与拜耳水性羟基丙烯酸树脂2470按nco与oh的摩尔比为1:1的比例进行混合,得到聚氨酯涂料,并测试其性能,测试结果计入表2中。硬度:按照gb/t6739-2006《色漆与清漆铅笔法测定漆膜硬度》进行测试。固化时间:降配制好的聚氨酯涂料涂覆于加热板上,加热板保持120℃恒温,观察试样加热固化时间。附着力:按照gb/t1720-1979《漆膜附着力测定法》,对聚氨酯涂料的附着力进行测试。柔韧性:按照gb/t1731-1993《漆膜柔韧性测定法》进行测试,通过双手将试板漆膜朝上,紧压于规定直径的轴棒上,利用两大拇指的力量在2-3s内,绕轴棒弯曲试板,弯曲后两大拇指应对称于轴棒中心线,弯曲后,用放大镜观察漆膜,检查漆膜是否产生网纹、裂纹即剥落等破坏现象,以不引起漆膜破坏的最小轴棒直径表示漆膜的柔韧性。耐黄变指数:按照gb/t2409-19801《塑料黄色指数试验方法》,对聚氨酯涂料的耐黄变性能进行测试δyi。由表2中测试数据可知由对比例和对比例2测试数据可知,实施例1-9中的聚氨酯涂料具有较高的硬度,较短固化时间,较高的附着力和柔韧性,以及优良的耐黄变性能,说明本发明制备的聚氨酯固化剂同样具有配漆性能,并且本发明所用原料均来源广泛,价格低廉,制备成本低,适合大规模生产。表2性能测试结果检测项目硬度/级固化时间/s附着力/级柔韧性/mm耐黄变指数/δyi实施例15ⅱ8101±0.11.01实施例25ⅱ8001±0.11.02实施例35ⅱ8301±0.11.01实施例45ⅱ8101±0.11.01实施例55ⅱ8201±0.11.01实施例65ⅱ8301±0.11.01实施例75ⅱ8101±0.11.02实施例85ⅱ8501±0.11.02实施例95ⅱ8301±0.11.01对比例15ⅱ8311±0.11.03对比例25ⅱ8201±0.11.02对比例34ⅱ9622±0.11.31对比例43ⅱ9522±0.11.28对比例53ⅱ10522±0.11.33以上所述仅是本发明的优选实施方式,本发明的保护范围并不仅局限于上述实施例,凡属于本发明思路下的技术方案均属于本发明的保护范围。应当指出,对于本
技术领域:
的普通技术人员来说,在不脱离本发明原理前提下的若干改进和润饰,这些改进和润饰也应视为本发明的保护范围。当前第1页12