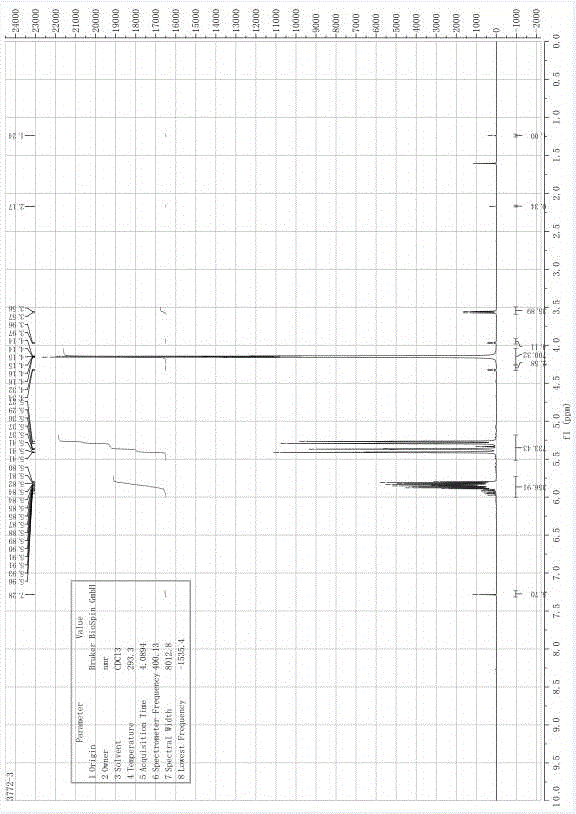
本发明属于化工医药中间体领域,具体涉及一种制备异硫氰酸烯丙酯的方法。
背景技术:
:异硫氰酸烯丙酯常称芥子油,它是一种含硫化合物,是带有异常刺激性气味液体,这类脂类化合物被广泛应用在防癌症、治疗心脏病以及杀虫剂等药物的合成中,也可用于合成多种类型的杂环化合物,在农药上作用杀菌、杀虫剂、除草剂等,在医药上用于抗菌消炎以及癌症等疾病治疗,是常见有机合成试剂。目前有报道的异硫氰酸烯丙酯的合成方法主要是水相法来合成,该方法的缺点非常明显,第一,废水特别多,大约1吨产品可以产生4-5吨废水,特别是反应后处理废水,全部是高盐高cod废水,废水很难处理,并处理成本很高;第二,水相法合成的异硫氰酸烯丙酯产品品质很难保证,特别是产品水分很难控制。由于产品是从水相中拿出来的,所以要保证产品的水分小于0.1%,必须经过除水操作才可以,而通常情况下,除水有两种途径,无机盐除水(无水硫酸钠等)以及溶剂共沸除水,而这样做也增加了后续的废弃物排放,不利于环保;第三,水相法后处理步骤比较繁琐,要经过几次碱洗、水洗操作,同时增加了废水量;第四,由于反应是两相反应,为了避免原料烯丙基氯水解的量,必须提高相转移催化剂的投料量,从而加快反应速度,提高产品的收率。因此,发明一种新的合成方法,使得合成及后处理过程更加简便、清洁环保,并且产品品质更加稳定,做到零废水排放,还能利于满足越来越严的环保要求,并且反应生成的副产氯化钠可以作为副产盐进行外卖,产生一定效益。技术实现要素:为了克服上述类似技术的不足,本发明提出一种制备异硫氰酸烯丙酯的方法,所述的制备方法简洁、环保并可以工业化操作,并且含量能达到98%以上。制备方法为:先将硫氰酸钠、溶剂、催化剂加入釜内,然后滴加烯丙基氯,在此反应过程中,利用有机溶剂进行反应,反应结束后,过滤除去生成的氯化钠,滤液直接脱溶,减少了后处理洗涤、干燥的过程,而且没有废水排放,所制备的异硫氰酸烯丙酯标定含量能达到98%以上,并且溶剂可以有效的套用。为了达到上述目的,本发明提出如下技术方案:所述的异硫氰酸烯丙酯的制备方法的具体步骤为:向反应釜中投入硫氰酸钠、溶剂、催化剂,反应体系升温至30-70℃,开始缓慢滴加烯丙基氯,反应过程中用氮气保护,滴加结束后,反应体系保温反应12-15小时,最终得到异硫氰酸烯丙酯;合成结束后体系降温后过滤,过滤后得到固体氯化钠和滤液。所述的制备方法还包括异硫氰酸烯丙酯的精馏,精馏的步骤如下:a、回收溶剂:将异硫氰酸烯丙酯转入精馏釜中,加热升温,先常压回收溶剂,常压回收溶剂结束后继续减压回收溶剂,回收溶剂可以套用于下一批反应。b、精馏:回收溶剂结束后,精馏釜继续升至外温100-120℃,全回流1小时,控制回流比2:1,真空度为60-80mmhg,并取样检测瞬时样异硫氰酸烯丙酯含量,当异硫氰酸烯丙酯标定含量大于98%时收集异硫氰酸烯丙酯成品。所述的溶剂为甲苯、1,2-二氯乙烷、丙酮、乙酸乙酯、乙腈。所述的催化剂为四丁基溴化铵、四丁基氯化铵、tbab。所述的反应温度为30℃-70℃。所述的制备异硫氰酸烯丙酯的方法的最佳步骤为:(1)异硫氰酸烯丙酯的合成a、向反应釜中投入硫氰酸钠、溶剂、催化剂,反应体系升温至30-70℃,开始缓慢滴加烯丙基氯,反应过程中用氮气保护,滴加结束,开始保温反应。b、保温反应12-15小时后开始取样检测,控制烯丙基氯小于1%合格,反应合格后,体系降温后过滤,过滤后得到固体氯化钠和滤液。(2)异硫氰酸烯丙酯精馏a、回收溶剂:滤液转入精馏釜中,加热升温,先常压回收溶剂,常压回收溶剂结束后继续减压回收溶剂,回收溶剂可以套用于下一批反应。b、精馏:回收溶剂结束后,精馏釜继续升至外温100-120℃,全回流1小时,控制回流比2:1,真空度为60-80mmhg,并取样检测瞬时样异硫氰酸烯丙酯含量,当异硫氰酸烯丙酯标定含量大于98%时收集异硫氰酸烯丙酯成品。描述:本发明以硫氰酸钠、溶剂、催化剂为起始原料,通过滴加烯丙基氯进行反应,反应过程生成副产氯化钠和我们需要的产品异硫氰酸烯丙酯,溶剂法生成副产氯化钠是以固体形式存在,通过过滤得到,固体氯化钠可以作为工业副产盐进行外卖,产生效益;而水相法此处生成氯化钠是溶解在大量水中,会产生大量高盐高cod的工业废水,废水处理困难,成本较高。溶剂法合成产品品质较高,特别是水分很低,而水相法由于产品是从水中拿出来的,产品水分较高,必须经过盐洗、干燥等操作才能保证产品水分合格。所以溶剂法后处理上清洁、简便、环保。有益效果:1.本发明以硫氰酸钠、溶剂、催化剂为起始原料,通过滴加烯丙基氯进行反应,反应过程简单、清洁,反应转化率高,产品品质好,避免了采用水作为溶剂,大大减少了废水排放量,降低了工业化生产中废水处理的难点。2.本发明用有机溶剂代替了水进行反应,反应结束后直接过滤,得到固体氯化钠和滤液,滤液进行脱溶、精馏得到合格产品;避免了用水做反应,反应结束后产生大量废水,后处理还需要碱洗、水洗、干燥等操作步骤等缺点,产生的高盐高cod废水很难处理,环保压力大。3.本工艺可以有效降低废水量,从而从源头就避免了废水的产生,不但大大减少了废水排放量,还减少了废水处理带来的环保压力,所制备的异硫氰酸烯丙酯含量能达到98%以上,可以达到异硫氰酸烯丙酯含量优等品标准。附图说明图1为异硫氰酸烯丙酯的核磁谱1;图2为异硫氰酸烯丙酯的核磁谱2。具体实施方式下面将结合本发明的实施例,对本发明实施例中的技术方案进行清楚、完整地描述,下面我们所描述的实施例仅仅是本发明一部分实施例,而不是全部的实施例,基于本发明中的实施例,本领域普通技术人员在没有作出创造性劳动前提下所获得的所有其它实施例,都属于本发明保护的范围。所述的制备异硫氰酸烯丙酯的方法的具体步骤为:(1)异硫氰酸烯丙酯的合成a、向反应釜中投入硫氰酸钠、溶剂、催化剂,反应体系升温至30-70℃,开始缓慢滴加烯丙基氯,滴加结束后,开始保温反应。b、反应体系保温反应12-15小时,反应液取样检测,控制烯丙基氯小于1%合格,反应合格后体系降温、过滤,得到固体氯化钠和滤液,氯化钠为副产盐。(2)异硫氰酸烯丙酯精馏a、回收溶剂:将滤液转入精馏釜中,加热升温,先常压回收溶剂,常压回收溶剂结束后继续减压回收溶剂,回收溶剂可以套用于下一批反应。b、精馏:回收溶剂结束后,精馏釜继续升至外温100-120℃,全回流1小时,控制回流比2:1,真空度为60-80mmhg,并取样检测瞬时样异硫氰酸烯丙酯含量,当异硫氰酸烯丙酯标定含量大于98%时收集异硫氰酸烯丙酯成品。实施例1所述的制备异硫氰酸烯丙酯的方法的具体步骤为:(1)异硫氰酸烯丙酯的合成a、向反应釜中投入硫氰酸钠100kg、甲苯200kg、催化剂tbab0.5kg,反应体系开始缓慢升温至70℃,然后在氮气保护情况下滴加93kg烯丙基氯,滴加结束后开始保温反应。b、当保温反应15小时后,取样检测,要求控制烯丙基氯小于1%合格,反应合格后体系降温、过滤,得到固体氯化钠和滤液,氯化钠为副产盐。检测的分析方法如下:(2)异硫氰酸烯丙酯精馏a、回收溶剂:将滤液酯转入精馏釜中,加热升温,并回收溶剂,当反应釜温度达到110℃时,停止回收溶剂,共回收190kg甲苯,回收溶剂可以套用于下一批反应。b、精馏:回收溶剂结束后,精馏釜继续升至外温120℃,全回流1小时,控制回流比2:1,真空度为80mmhg,并取样检测瞬时样异硫氰酸烯丙酯含量,当异硫氰酸烯丙酯标定含量大于98%时收集异硫氰酸烯丙酯成品,最终得到120kg含量99.3%异硫氰酸烯丙酯成品。附图1和附图2即实施例1中异硫氰酸烯丙酯的核磁谱,产品经过核磁检测,确认了产品结构,其数据如下:hnmr(brukerav-400):δ(ppm),4.08(2h,=c-ch2),5.24(2h,=ch2),5.73(1h,=ch-c)实施例2所述的制备异硫氰酸烯丙酯的方法的具体步骤为:(1)异硫氰酸烯丙酯的合成a、向反应釜中投入硫氰酸钠100kg、1,2-二氯乙烷200kg、催化剂tbab0.5kg,反应体系开始缓慢升温至60℃,然后在氮气保护情况下滴加93kg烯丙基氯,滴加结束后开始保温反应。b、当保温反应15小时后,取样检测,要求控制烯丙基氯小于1%合格,反应合格后体系降温、过滤,得到固体氯化钠和滤液,氯化钠为副产盐。(2)异硫氰酸烯丙酯精馏a、回收溶剂:将滤液转入精馏釜中,加热升温,并回收溶剂,当反应釜温度达到110℃时,停止回收溶剂,共回收180kg1,2-二氯乙烷,回收溶剂可以套用于下反应。b、精馏:回收溶剂结束后,精馏釜继续升至外温120℃,全回流1小时,控制回流比2:1,真空度为80mmhg,并取样检测瞬时样异硫氰酸烯丙酯含量,当异硫氰酸烯丙酯标定含量大于98%时收集异硫氰酸烯丙酯成品,最终得到122kg含量99.5%异硫氰酸烯丙酯成品。实施例3所述的制备异硫氰酸烯丙酯的方法的具体步骤为:(1)异硫氰酸烯丙酯的合成a、向反应釜中投入硫氰酸钠100kg、乙酸乙酯200kg、催化剂tbab0.5kg,反应体系开始缓慢升温至50℃,然后在氮气保护情况下滴加93kg烯丙基氯,滴加结束后开始保温反应。b、当保温反应15小时后,取样检测,要求控制烯丙基氯小于1%合格,反应合格后体系降温、过滤,得到固体氯化钠和滤液,氯化钠为副产盐。(2)异硫氰酸烯丙酯精馏a、回收溶剂:将滤液转入精馏釜中,加热升温,并回收溶剂,当反应釜温度达到110℃时,停止回收溶剂,共回收165kg乙酸乙酯,回收溶剂可以套用于下反应。b、精馏:回收溶剂结束后,精馏釜继续升至外温120℃,全回流1小时,控制回流比2:1,真空度为80mmhg,并取样检测瞬时样异硫氰酸烯丙酯含量,当异硫氰酸烯丙酯标定含量大于98%时收集异硫氰酸烯丙酯成品,最终得到115kg含量99.5%异硫氰酸烯丙酯成品。实施例4所述的制备异硫氰酸烯丙酯的方法的具体步骤为:(1)异硫氰酸烯丙酯的合成a、向反应釜中投入硫氰酸钠100kg、丙酮200kg、反应体系开始缓慢升温至40℃,然后在氮气保护情况下滴加93kg烯丙基氯,滴加结束后开始保温反应。b、当保温反应15小时后,取样检测,要求控制烯丙基氯小于1%合格,反应合格后体系降温、过滤,得到固体氯化钠和滤液,氯化钠为副产盐。(2)异硫氰酸烯丙酯精馏a、回收溶剂:将滤液转入精馏釜中,加热升温,并回收溶剂,当反应釜温度达到110℃时,停止回收溶剂,共回收160kg丙酮,回收溶剂可以套用于下反应。b、精馏:回收溶剂结束后,精馏釜继续升至外温120℃,全回流1小时,控制回流比2:1,真空度为80mmhg,并取样检测瞬时样异硫氰酸烯丙酯含量,当异硫氰酸烯丙酯标定含量大于98%时收集异硫氰酸烯丙酯成品,最终得到121kg含量99.5%异硫氰酸烯丙酯成品。实施例5所述的制备异硫氰酸烯丙酯的方法的具体步骤为:(1)异硫氰酸烯丙酯的合成a、向反应釜中投入硫氰酸钠100kg、乙腈200kg、催化剂tbab0.5kg,反应体系开始缓慢升温至40℃,然后在氮气保护情况下滴加93kg烯丙基氯,滴加结束后开始保温反应。b、当保温反应15小时后,取样检测,要求控制烯丙基氯小于1%合格,反应合格后体系降温、过滤,得到固体氯化钠和滤液,氯化钠为副产盐。(2)异硫氰酸烯丙酯精馏a、回收溶剂:将滤液转入精馏釜中,加热升温,并回收溶剂,当反应釜温度达到110℃时,停止回收溶剂,共回收164kg乙腈,回收溶剂可以套用于下反应。b、精馏:回收溶剂结束后,精馏釜继续升至外温120℃,全回流1小时,控制回流比2:1,真空度为80mmhg,并取样检测瞬时样异硫氰酸烯丙酯含量,当异硫氰酸烯丙酯标定含量大于98%时收集异硫氰酸烯丙酯成品,最终得到122kg含量99.5%异硫氰酸烯丙酯成品。实施例6所述的制备异硫氰酸烯丙酯的方法的具体步骤为:(1)异硫氰酸烯丙酯的合成a、向反应釜中投入硫氰酸钠100kg、丙酮200kg、催化剂tbab0.5kg,反应体系开始缓慢升温至50℃,然后在氮气保护情况下滴加93kg烯丙基氯,滴加结束后开始保温反应。b、当保温反应15小时后,取样检测,要求控制烯丙基氯小于1%合格,反应合格后体系降温、过滤,得到固体氯化钠和滤液,氯化钠为副产盐。(2)异硫氰酸烯丙酯精馏a、回收溶剂:将滤液转入精馏釜中,加热升温,并回收溶剂,当反应釜温度达到110℃时,停止回收溶剂,共回收166kg丙酮,回收溶剂可以套用于下反应。b、精馏:回收溶剂结束后,精馏釜继续升至外温120℃,全回流1小时,控制回流比2:1,真空度为80mmhg,并取样检测瞬时样异硫氰酸烯丙酯含量,当异硫氰酸烯丙酯标定含量大于98%时收集异硫氰酸烯丙酯成品,最终得到120kg含量99.5%异硫氰酸烯丙酯成品。实施例7所述的制备异硫氰酸烯丙酯的方法的具体步骤为:(1)异硫氰酸烯丙酯的合成a、向反应釜中投入硫氰酸钠100kg、甲苯200kg、催化剂四丁基溴化铵0.5kg,反应体系开始缓慢升温至70℃,然后在氮气保护情况下滴加93kg烯丙基氯,滴加结束后开始保温反应。b、当保温反应15小时后,取样检测,要求控制烯丙基氯小于1%合格,反应合格后体系降温、过滤,得到固体氯化钠和滤液,氯化钠为副产盐。(2)异硫氰酸烯丙酯精馏a、回收溶剂:将滤液转入精馏釜中,加热升温,并回收溶剂,当反应釜温度达到110℃时,停止回收溶剂,共回收188kg甲苯,回收溶剂可以套用于下一批反应。b、精馏:回收溶剂结束后,精馏釜继续升至外温120℃,全回流1小时,控制回流比2:1,真空度为80mmhg,并取样检测瞬时样异硫氰酸烯丙酯含量,当异硫氰酸烯丙酯标定含量大于98%时收集异硫氰酸烯丙酯成品,最终得到121kg含量99.3%异硫氰酸烯丙酯成品。实施例8所述的制备异硫氰酸烯丙酯的方法的具体步骤为:(1)异硫氰酸烯丙酯的合成a、向反应釜中投入硫氰酸钠100kg、1,2-二氯乙烷200kg、催化剂四丁基溴化铵0.5kg,反应体系开始缓慢升温至60℃,然后在氮气保护情况下滴加93kg烯丙基氯,滴加结束后开始保温反应。b、当保温反应12-15小时后,取样检测,要求控制烯丙基氯小于1%合格,反应合格后体系降温、过滤,得到固体氯化钠和滤液,氯化钠为副产盐。(2)异硫氰酸烯丙酯精馏a、回收溶剂:将滤液转入精馏釜中,加热升温,并回收溶剂,当反应釜温度达到110℃时,停止回收溶剂,共回收181kg1,2-二氯乙烷,回收溶剂可以套用于下反应。b、精馏:回收溶剂结束后,精馏釜继续升至外温120℃,全回流1小时,控制回流比2:1,真空度为80mmhg,并取样检测瞬时样异硫氰酸烯丙酯含量,当异硫氰酸烯丙酯标定含量大于98%时收集异硫氰酸烯丙酯成品,最终得到121kg含量99.5%异硫氰酸烯丙酯成品。实施例9所述的制备异硫氰酸烯丙酯的方法的具体步骤为:(1)异硫氰酸烯丙酯的合成a、向反应釜中投入硫氰酸钠100kg、乙酸乙酯200kg、催化剂四丁基溴化铵0.5kg,反应体系开始缓慢升温至50℃,然后在氮气保护情况下滴加93kg烯丙基氯,滴加结束后开始保温反应。b、当保温反应12-15小时后,取样检测,要求控制烯丙基氯小于1%合格,反应合格后体系降温、过滤,得到固体氯化钠和滤液,氯化钠为副产盐。(2)异硫氰酸烯丙酯精馏a、回收溶剂:将滤液丙酯转入精馏釜中,加热升温,并回收溶剂,当反应釜温度达到110℃时,停止回收溶剂,共回收168kg乙酸乙酯,回收溶剂可以套用于下反应。b、精馏:回收溶剂结束后,精馏釜继续升至外温120℃,全回流1小时,控制回流比2:1,真空度为80mmhg,并取样检测瞬时样异硫氰酸烯丙酯含量,当异硫氰酸烯丙酯标定含量大于98%时收集异硫氰酸烯丙酯成品,最终得到116kg含量99.5%异硫氰酸烯丙酯成品。实施例10所述的制备异硫氰酸烯丙酯的方法的具体步骤为:(1)异硫氰酸烯丙酯的合成a、向反应釜中投入硫氰酸钠100kg、丙酮200kg、催化剂四丁基溴化铵0.5kg,反应体系开始缓慢升温至40℃,然后在氮气保护情况下滴加93kg烯丙基氯,滴加结束后开始保温反应。b、当保温反应15小时后,取样检测,要求控制烯丙基氯小于1%合格,反应合格后体系降温、过滤,得到固体氯化钠和滤液,氯化钠为副产盐。(2)异硫氰酸烯丙酯精馏a、回收溶剂:将滤液转入精馏釜中,加热升温,并回收溶剂,当反应釜温度达到110℃时,停止回收溶剂,共回收161kg丙酮,回收溶剂可以套用于下反应。b、精馏:回收溶剂结束后,精馏釜继续升至外温120℃,全回流1小时,控制回流比2:1,真空度为80mmhg,并取样检测瞬时样异硫氰酸烯丙酯含量,当异硫氰酸烯丙酯标定含量大于98%时收集异硫氰酸烯丙酯成品,最终得到119kg含量99.5%异硫氰酸烯丙酯成品。实施例11所述的制备异硫氰酸烯丙酯的方法的具体步骤为:(1)异硫氰酸烯丙酯的合成a、向反应釜中投入硫氰酸钠100kg、乙腈200kg、催化剂四丁基氯化铵0.5kg,反应体系开始缓慢升温至30-40℃,然后在氮气保护情况下滴加93kg烯丙基氯,滴加结束后开始保温反应。b、当保温反应12-15小时后,取样检测,要求控制烯丙基氯小于1%合格,应合格后体系降温、过滤,得到固体氯化钠和滤液,氯化钠为副产盐。(2)异硫氰酸烯丙酯精馏a、回收溶剂:将滤液转入精馏釜中,加热升温,并回收溶剂,当反应釜温度达到110℃时,停止回收溶剂,共回收162kg乙腈,回收溶剂可以套用于下反应。b、精馏:回收溶剂结束后,精馏釜继续升至外温120℃,全回流1小时,控制回流比2:1,真空度为80mmhg,并取样检测瞬时样异硫氰酸烯丙酯含量,当异硫氰酸烯丙酯标定含量大于98%时收集异硫氰酸烯丙酯成品,最终得到120kg含量99.5%异硫氰酸烯丙酯成品。实验分析1.本发明制备的异硫氰酸烯丙酯与标准异硫氰酸烯丙酯的对比:项目指标异硫氰酸烯丙酯含量%≥98.0外观:常温下无色或者淡黄色液体水分:小于0.2%2.实验结果实施例1-6所制备的异硫氰酸烯丙酯均达到表1的要求,符合优等级异硫氰酸烯丙酯的标准。以上对本发明实施例所提供的一种制备异硫氰酸烯丙酯的方法进行了详细介绍,本文中应用了具体个例对本发明的原理及实施方式进行了阐述,以上实施例的说明只是用于本发明主体合成思路及路线;同时,对于本领域在具体实施方式及应用范围上均会有改变之处,综上所述,本说明书内容不应理解为对本发明的限制,是对本发明一种解释与说明。当前第1页12