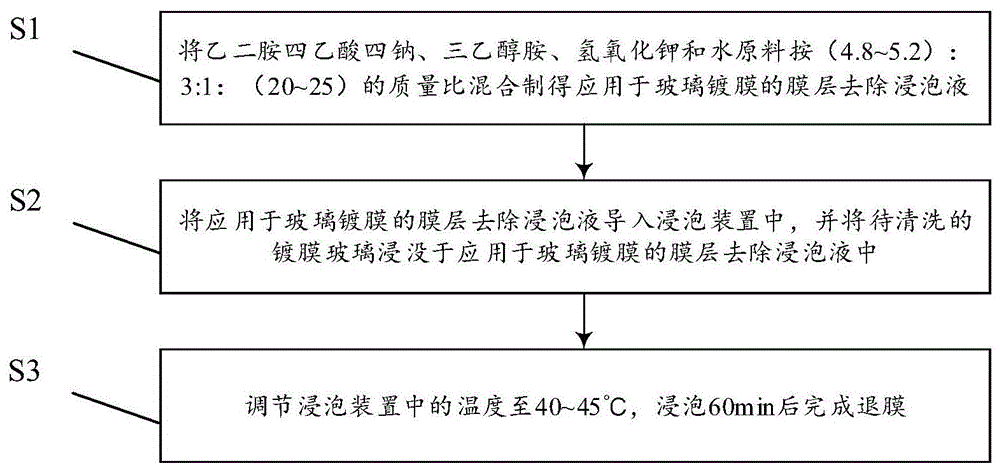
本发明涉及显示器件制备领域,特别是一种应用于玻璃镀膜的膜层去除浸泡液及其应用方法。
背景技术:
:液晶显示器是当前充满活力的电子产品,它的应用十分广泛,现已成为技术密集、资金密集型的高新技术产业。透明导电玻璃是lcd的三大主材之一。液晶显示器之所以能显示特定的图形,就是利用导电玻璃上的透明导电膜,经过刻蚀制成特定形状的电极。上下两片导电玻璃制成液晶盒后,在这些电极上加适当电压信号,使液晶的特性改变,就可显示出与电极形状相对应的图形。目前氧化物导电膜中,以掺sn的in2o3(简称ito)薄膜及纳米掺锑二氧化锡、锑锡氧化物(简称ato)薄膜为主。随着电子行业的不断发展,相应的镀氧化物导电膜tft-lcd面板产能需求也不断提高,虽然氧化物导电膜的镀膜技术逐步成熟带来的产能显著提高,但是生产过程中因人员操作及设备异常导致的膜层不良同步提高,氧化物导电膜的类型不同其成分及特性差异较大,现镀膜行业内面对不同的膜层采用不同的强酸洗剂多次擦拭腐蚀去除,其缺点在于:(1)不同膜层对应不同的强酸洗剂,备货不便;(2)因清洗剂为强酸性,刺激性强易对操作人员造成伤害;(3)产品便面残酸不易去除再次镀膜会影响膜层不良;(4)传统的除去过程需要人工完成,人工作业效率慢、擦拭不到易残留、擦拭产品易破损。面对产能的不断提高,这种传统采用强酸强碱进行人工清洗的方式已经不能适应大规模工厂生产的需求,故需要提出一种新的高效去除薄膜的方法,用于解决上述问题。技术实现要素:本发明的目的在于,提供一种应用于玻璃镀膜的膜层去除浸泡液,用于解决现有技术中强酸碱清洗去除薄膜的方式会造成损伤且人工作业效率低的问题。为解决上述技术问题,本发明提供了第一解决方案为:一种应用于玻璃镀膜的膜层去除浸泡液由乙二胺四乙酸四钠、三乙醇胺、氢氧化钾和水按(4.8~5.2):3:1:(20~25)的质量比混合制得。优选的,应用于显示器件镀膜的膜层去除浸泡液配置过程中,乙二胺四乙酸四钠为粉末状原料。优选的,应用于显示器件镀膜的膜层去除浸泡液配置过程中,三乙醇胺为液体原料。优选的,应用于显示器件镀膜的膜层去除浸泡液配置过程中,氢氧化钾为晶体颗粒原料。为解决上述技术问题,本发明提供了第二解决方案为:一种应用于玻璃镀膜的膜层去除浸泡液的应用方法,该应用方法所采用的是第一解决方案中应用于玻璃镀膜的膜层去除浸泡液,其步骤包括:将乙二胺四乙酸四钠、三乙醇胺、氢氧化钾和水原料按(4.8~5.2):3:1:(20~25)的质量比混合制得应用于玻璃镀膜的膜层去除浸泡液;将应用于玻璃镀膜的膜层去除浸泡液导入浸泡装置中,并将待清洗的镀膜玻璃浸没于应用于玻璃镀膜的膜层去除浸泡液中;调节浸泡装置中的温度至40~45℃,浸泡60min后完成退膜。本发明的有益效果是:区别于现有技术的情况,本发明提供了一种应用于玻璃镀膜的膜层去除浸泡液及其应用方法,以乙二胺四乙酸四钠、三乙醇胺、氢氧化钾和水混合制成复合组分的浸泡液,具有优异的薄膜退除效果,去除薄膜时间短,去除后玻璃表面的光滑程度显著提高。附图说明图1是本发明中应用于玻璃镀膜的膜层去除浸泡液的应用方法一实施方式的流程图。具体实施方式下面将结合本发明实施例,对本发明实施例中的技术方案进行清楚、完整地描述,显然,所描述的实施例仅仅是本发明一部分实施例,而不是全部的实施例。基于本发明中的实施例,本领域普通技术人员在没有做出创造性劳动前提下所获得的所有其他实施例,均属于本发明保护的范围。对于本发明中所提出的第一解决方案来说,提供了一种应用于玻璃镀膜的膜层去除浸泡液由乙二胺四乙酸四钠、三乙醇胺、氢氧化钾和水按(4.8~5.2):3:1:(20~25)的质量比混合制得。本实施方式中,在应用于显示器件镀膜的膜层去除浸泡液配置过程中,乙二胺四乙酸四钠优选为粉末状原料,三乙醇胺优选为液体原料,氢氧化钾优选为晶体颗粒原料。具体地,对本发明中应用于玻璃镀膜的膜层去除浸泡液的组分作用机理及优势进行阐述:(1)上述组分中,乙二胺四乙酸四钠具有清除有机膜层的作用,而对于三乙醇胺来说,一方面可以作为乳化剂,配合乙二胺四乙酸四钠使用在清除有机膜层的同时,还可提高处理后玻璃表面的光滑度,另一方面三乙醇胺在弱碱条件下能够增强其除去有机膜层的效果。(2)上述组分中降低了氢氧化钾的组分占比,即该浸泡液为弱碱环境,在经过浸泡处理后对玻璃表面的损伤也会大幅降低。(3)上述组分中降低了水的组分占比,相较于现有的强碱性清洗液来说,可以大幅降低用水量,节约成本。对于本发明中所提出的第二解决方案,请参阅图1,图1是本发明中应用于玻璃镀膜的膜层去除浸泡液的应用方法一实施方式的流程图。本发明中应用于玻璃镀膜的膜层去除浸泡液的应用方法所采用的是第一解决方案中应用于玻璃镀膜的膜层去除浸泡液,其步骤包括:s1:将乙二胺四乙酸四钠、三乙醇胺、氢氧化钾和水原料按(4.8~5.2):3:1:(20~25)的质量比混合制得应用于玻璃镀膜的膜层去除浸泡液。s2:将应用于玻璃镀膜的膜层去除浸泡液导入浸泡装置中,并将待清洗的镀膜玻璃浸没于应用于玻璃镀膜的膜层去除浸泡液中。s3:调节浸泡装置中的温度至40~45℃,浸泡60min后完成退膜。下面通过具体的实施例对上述应用于玻璃镀膜的膜层去除浸泡液及其应用方法的除去薄膜效果进行详述。设置实施例1~3和对比例1~2,以质量份计,具体组分比例如表1所示。其中,实施例1~3中应用于玻璃镀膜的膜层去除浸泡液均以乙二胺四乙酸四钠、三乙醇胺、氢氧化钾和水为原料混合后制成,且组分比例均在前述配方的范围内,仅对该膜层去除浸泡液的组分进行了调整;对比例1的原料为乙二胺四乙酸四钠、三乙醇胺、氢氧化钾和水,但组分比例不在前述配方的范围内;对比例2的原料为乙二胺四乙酸四钠、氢氧化钾和水。表1实施例1~5原料配比表乙二胺四乙酸四钠三乙醇胺氢氧化钾水实施例115.09374实施例215.39364实施例315.29375对比例122460对比例22/460将实施例1~3和对比例1~2中所制备的膜层去除浸泡液分别导入浸泡装置中,并将待清洗的镀膜玻璃浸没于膜层去除浸泡液中,调节浸泡装置中的温度至40~45℃,浸泡60min后完成退膜;然后对实施例1~3和对比例1~2中所制备的膜层去除浸泡液的效果进行表征,主要为表面粗糙度测试,其结果如表2所示。可以看出实施例1~3均有较好的退除薄膜效果,其中实施例1所制备的膜层去除浸泡液去除薄膜时间最短,且表面粗糙度最低,可以认为实施例1是本发明中的最佳实施例;而对比例1和2虽然能够将薄膜完全退除,但耗时稍微较长且表面粗糙度稍高。表2实施例1~5薄膜去除效果对比表设置对比例3~5,对比例3~4中分别采用乙二胺四乙酸四钠、三乙醇胺、氢氧化钾与水混合后制成相应的浸泡液,并用相同的方法对对比例1~3中浸泡液的退除薄膜效果进行表征,结果如表3中所示,其中配比以质量份计。对比表2和表3可以看出,对比例3~5均经历了较长的薄膜去除时间,耗水比例较大,并存在较多的不足之处,其中对比例4所制备的浸泡液并不具有退除薄膜的作用。而对比例5所制备的浸泡液就是现有技术中常用的强碱型清洗液,该强碱型清洗液虽然可以完全退除薄膜,但是反应时间太长,约为实施例1的四倍时长;并且该强碱型清洗液处理后的玻璃表面粗糙度很高,与实施例1所表现出的光滑程度相差甚远。由此可知,本发明中所制备的应用于玻璃镀膜的膜层去除浸泡液具有优异的薄膜退除效果,去除薄膜时间较短,去除后玻璃表面的光滑程度显著提高。表3对比例1~3薄膜去除效果对比表区别于现有技术的情况,本发明提供了一种应用于玻璃镀膜的膜层去除浸泡液及其应用方法,以乙二胺四乙酸四钠、三乙醇胺、氢氧化钾和水混合制成复合组分的浸泡液,具有优异的薄膜退除效果,去除薄膜时间短,去除后玻璃表面的光滑程度显著提高。需要说明的是,以上各实施例均属于同一发明构思,各实施例的描述各有侧重,在个别实施例中描述未详尽之处,可参考其他实施例中的描述。以上所述实施例仅表达了本发明的实施方式,其描述较为具体和详细,但并不能因此而理解为对发明专利范围的限制。应当指出的是,对于本领域的普通技术人员来说,在不脱离本发明构思的前提下,还可以做出若干变形和改进,这些都属于本发明的保护范围。因此,本发明专利的保护范围应以所附权利要求为准。当前第1页12