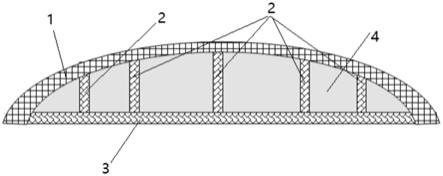
1.本实用新型属于汽车保险杠技术领域,具体涉及一种热塑性树脂作为基体、碳纤维增强的复合材料制备汽车用保险杠。
背景技术:2.公开该背景技术部分的信息仅仅旨在增加对本实用新型的总体背景的理解,而不必然被视为承认或以任何形式暗示该信息构成已经成为本领域一般技术人员所公知的现有技术。
3.汽车保险杠是吸收缓和外界冲击力、防护车身前后部件的安全装置。随着汽车轻量化设计的研发工作的不断深入,对于汽车保险杠的轻质安全结构设计和材料替代设计成为研究的重点工作。传统的汽车保险杠基本上都是金属材料,在汽车保险杠的面板采用轻质耐冲击金属合金,用以提高低速冲击过程中保险杠面板的能量吸收效率;保险杠的后置刚性横梁采用特殊u型刚性结构设计,以提高保险杠整体抵抗变形的能力;在前置面板和后置横梁之间采用轻质缓冲芯层结构保证冲击过程的能量的最大程度吸收保证安全性。
4.随着燃油价格上升和废气排放量,汽车制造呈现轻量化趋势,采用碳纤维等复合材料有助于减轻车体自重,节约燃油。现有研究表明,将碳纤维应用于保险杠的制备,不仅能够减轻车身重量,尤其在面临高速碰撞等情形,碳纤维相比钢材料具有更加优异的碰撞性能。
技术实现要素:5.现有研究表明,纤维的取向及不同材料的配合作用对于碳纤维复合材料杠梁的强度具有明显的影响。本实用新型目的在于提供一种制备工艺更为简便,同时满足使用强度的汽车安全装置。经本实用新型研究表明,采用树脂作为基体与碳纤维材料通过编织形成的复合材料具有良好的比强度比吸能比刚度等特性;进一步的,本实用新型调整树脂材料与碳纤维材料作为保险杠横梁、碳纤维加强泡沫层作为吸能夹芯层的配合方式,作为一种保险杠进行应用,可同时实现制备工艺简单、质轻和优异的防撞性能。
6.基于上述技术效果,本实用新型提供以下技术方案:
7.本实用新型第一方面,提供一种汽车保险杠,所述汽车保险杠包括前置面板、横梁、支撑骨架及泡沫材料;所述前置面板为弧形板状,所述横梁为长方形板状,其边缘与前置面板的边缘处接壤围成弧形部;所述前置面板与横梁之间具有条状的支撑骨架,支撑骨架将弧形部分割形成的若干区域内填充泡沫材料。
8.上述一个或多个技术方案的有益效果是:
9.所述保险杠制备的工艺较为简便,采用三维编织技术即可完成大部分制备工作,相比传统的模压成型工艺,避免了模具设计这一技术难题,制备工艺更加灵活。另外,耐冲击材料、吸能材料和刚性复合材料的配合能够实现轻量化和优秀的防撞性能,具有良好的应用前景。
附图说明
10.构成本实用新型的一部分的说明书附图用来提供对本实用新型的进一步理解,本实用新型的示意性实施例及其说明用于解释本实用新型,并不构成对本实用新型的不当限定。
11.图1为实施例1中所述汽车保险杠的结构示意图;
12.其中,1为前置面板,2为支撑结构,3为横梁,4为泡沫材料。
具体实施方式
13.应该指出,以下详细说明都是例示性的,旨在对本实用新型提供进一步的说明。除非另有指明,本文使用的所有技术和科学术语具有与本实用新型所属技术领域的普通技术人员通常理解的相同含义。
14.需要注意的是,这里所使用的术语仅是为了描述具体实施方式,而非意图限制根据本实用新型的示例性实施方式。如在这里所使用的,除非上下文另外明确指出,否则单数形式也意图包括复数形式,此外,还应当理解的是,当在本说明书中使用术语“包含”和/或“包括”时,其指明存在特征、步骤、操作、器件、组件和/或它们的组合。
15.正如背景技术所介绍的,针对现有技术中存在的不足,本实用新型提出了一种热塑性复合材料制备的汽车保险杠。
16.本实用新型第一方面,提供一种汽车保险杠,所述汽车保险杠包括前置面板、横梁、支撑骨架及泡沫材料;所述前置面板为弧形板状,所述横梁为长方形板状,其边缘与前置面板的边缘处接壤围成弧形部;所述前置面板与横梁之间具有条状的支撑骨架,支撑骨架将弧形部分割形成的若干区域内填充泡沫材料。
17.优选的,所述前置面板为一种耐冲击复合材料,所述耐冲击复合材料采用树脂材料作为基体,与高强度碳纤维通过三维编织构成所述耐冲击复合材料。
18.进一步优选的,所述树脂材料的含量为40~60%。
19.进一步优选的,所述树脂材料为聚酰胺、聚苯硫醚、聚醚酮、聚醚醚酮、聚甲醛、聚丙烯、聚碳酸酯中的任意一种或几种的组合。
20.进一步优选的,所述高强度碳纤维为t300、t700、t800、t1000中的任意一种或多种组合。
21.进一步优选的,所述三维编织为三维四向、三维五向、三维六向、三维七向中的任意一种编织结构。
22.优选的,所述横梁为一种刚性复合材料,所述刚性复合材料采用树脂作为基体,与混合碳纤维通过三维编织构成;所述混合纤维为高强度碳纤维与高模量碳纤维混杂构成。
23.进一步优选的,所述树脂为聚酰胺、聚苯硫醚、聚醚酮、聚醚醚酮、聚甲醛、聚丙烯、聚碳酸酯中的任意一种或几种的组合。
24.进一步优选的,所述高模量纤维为m40、m60、m55、m40j、m60j中的任意一种或几种的组合。
25.进一步优选的,所述高强度碳纤维为t300、t700、t800、t1000中的任意一种或几种的组合。
26.进一步优选的,所述三维编织为三维四向、三维五向、三维六向、三维七向中的任
意一种。
27.优选的,所述弧形部采用一种吸能材料作为填充;所述吸能材料采用泡沫材料作为主体材料,相邻泡沫材料之间通过碳纤维缝编连接;所述吸能材料表面具有热塑树脂层。
28.进一步优选的,所述泡沫材料为聚甲基丙烯酰亚胺(pmi)、铝蜂窝、pvc泡沫中的任意一种或几种的组合。
29.进一步优选的,所述泡沫材料为多层层状泡沫材料重叠构成。
30.进一步优选的,所述碳纤维为绳状碳纤维。
31.进一步优选的,所述碳纤维为t300、t700、t800、t1000中的任意一种或几种的组合。
32.进一步优选的,所述热塑树脂为环氧树脂、酚醛树脂、不饱和聚酯树脂、有机硅树脂中的任意一种或几种的组合。
33.进一步优选的,所述热塑树脂含量为40~60%。
34.进一步优选的,所述支撑骨架为所述吸能材料中的碳纤维。
35.进一步优选的,所述支撑骨架的数量为奇数个,更为优选的,为3~7个。
36.在一些具体的实施方式中,所述保险杠俯视截面的对称轴处具有支撑骨架,其余支撑骨架于对称轴两侧对称分布。
37.为了使得本领域技术人员能够更加清楚地了解本实用新型的技术方案,以下将结合具体的实施例详细说明本实用新型的技术方案。
38.实施例1
39.本实施例中,提供一种汽车保险杠,所述汽车保险杠结构如附图1所示,汽车保险杠包括前置面板1、横梁3、支撑骨架2及泡沫材料4;所述前置面板1为弧形板状,所述横梁3为长方形板状,其边缘与前置面板1的边缘处接壤围成弧形部;所述前置面板1与横梁3之间具有条状的支撑骨架2,支撑骨架2将弧形部分割形成的若干区域内填充泡沫材料4。
40.所述支撑骨架2的数量为5个,彼此间等距分布,其中一个支撑骨架位于保险杠俯视截面的对称轴处,其余4个支撑骨架对称分布于对称轴两侧。
41.其中,前置面板1采用耐冲击复合材料制备,所述耐冲击复合材料采用聚酰胺树脂材料作为基体,与t300碳纤维通过三维编织机采用三维四向编织构成。所述聚氨酯纤维在耐冲击复合材料中所占的比例为50%。
42.横梁2采用刚性复合材料,所述刚性复合材料采用基体树脂含量60%的聚碳酸酯通过三维七向编织结构的3:1混杂比例的m40碳纤维和t300碳纤维匹配的混杂纤维增强构成后置热塑性复合材料刚性横梁。
43.所述弧形部填充吸能材料,所述吸能材料采用三维编织的t300碳纤维骨架将三层吸能轻质pmi芯材缝编构成整体;其中,t300碳纤维构成支撑骨架,支撑骨架将弧形部分割形成的区域内填充吸能轻质pmi芯材。导入聚碳酸酯树脂,使树脂充分浸渍碳纤维骨架及泡沫铝芯材,在烘箱中使其固化成型,即可得到所述吸能材料。
44.实施例2
45.本实施例中,提供一种汽车保险杠,所述汽车保险杠包括前置面板1、横梁3、支撑骨架2及泡沫材料4;所述前置面板1为弧形板状,所述横梁3为长方形板状,其边缘与前置面板1的边缘处接壤围成弧形部;所述前置面板1与横梁3之间具有条状的支撑骨架2,支撑骨
架2将弧形部分割形成的若干区域内填充泡沫材料4。
46.所述支撑骨架2的数量为5个,支撑骨架自对称轴向边缘处间距逐渐缩小,,其中一个支撑骨架位于保险杠俯视截面的对称轴处,其余4个支撑骨架对称分布于对称轴两侧。
47.其中,前置面板1采用耐冲击复合材料制备,所述耐冲击复合材料采用基体树脂含量60%的聚碳酸酯通过三维七向编织结构的3:1混杂比例的m40碳纤维和t300碳纤维匹配的混杂纤维增强构成耐冲击复合材料。
48.横梁2采用刚性复合材料,所述刚性复合材料采用基体树脂含量55%的聚醚醚酮通过三维五向编织结构的4:1混杂比例的m60j碳纤维和t800碳纤维匹配的混杂纤维增强构成。
49.所述弧形部填充吸能材料,所述吸能材料采用三维七向编织的t1000碳纤维骨架将四层吸能轻质泡沫铝芯材缝编构成。导入聚醚醚酮树脂,使树脂充分浸渍碳纤维骨架及泡沫铝芯材,在烘箱中使其固化成型,即可得到所述吸能材料。
50.实施例3
51.本实施例中,提供一种汽车保险杠,所述汽车保险杠包括前置面板1、横梁3、支撑骨架2及泡沫材料4;所述前置面板1为弧形板状,所述横梁3为长方形板状,其边缘与前置面板1的边缘处接壤围成弧形部;所述前置面板1与横梁3之间具有条状的支撑骨架2,支撑骨架2将弧形部分割形成的若干区域内填充泡沫材料4。
52.所述支撑骨架2的数量为5个,支撑骨架自对称轴向边缘处间距逐渐缩小,,其中一个支撑骨架位于保险杠俯视截面的对称轴处,其余4个支撑骨架对称分布于对称轴两侧。
53.其中,前置面板1采用耐冲击复合材料制备,所述耐冲击复合材料采用基体树脂含量50%的聚醚酮通过三维六向编织结构的t700碳纤维进行增强构成。
54.横梁2采用刚性复合材料,所述刚性复合材料采用基体树脂含量44%的聚醚醚酮通过三维五向编织结构的2:1混杂比例的m55碳纤维和t1000碳纤维匹配的混杂纤维增强构成。
55.所述弧形部填充吸能材料,所述吸能材料采用三维五向编织的t800碳纤维骨架将2层吸能轻质pvc芯材缝编构成整体。导入聚醚醚酮树脂,使树脂充分浸渍碳纤维骨架及泡沫铝芯材,在烘箱中使其固化成型,即可得到所述吸能材料。
56.实施例4
57.本实施例中,提供一种汽车保险杠,所述汽车保险杠包括前置面板1、横梁3、支撑骨架2及泡沫材料4;所述前置面板1为弧形板状,所述横梁3为长方形板状,其边缘与前置面板1的边缘处接壤围成弧形部;所述前置面板1与横梁3之间具有条状的支撑骨架2,支撑骨架2将弧形部分割形成的若干区域内填充泡沫材料4。
58.所述支撑骨架2的数量为5个,支撑骨架自对称轴向边缘处间距逐渐缩小,,其中一个支撑骨架位于保险杠俯视截面的对称轴处,其余4个支撑骨架对称分布于对称轴两侧。
59.其中,前置面板1采用耐冲击复合材料制备,所述耐冲击复合材料采用基体树脂含量55%的聚丙烯通过三维六向编织结构的t1000碳纤维进行增强构成。
60.横梁2采用刚性复合材料,所述刚性复合材料采用基体树脂含量47%的聚酰胺通过三维七向编织结构的5:1混杂比例的m60j碳纤维和t1000碳纤维匹配的混杂纤维增强构成。
61.所述弧形部填充吸能材料,所述吸能材料采用三维五向编织的t300碳纤维骨架将6层吸能轻质pmi芯材缝编构成整体。导入聚酰胺树脂,使树脂充分浸渍碳纤维骨架及泡沫铝芯材,在烘箱中使其固化成型,即可得到所述吸能材料。
62.实施例5
63.本实施例中,提供一种汽车保险杠,所述汽车保险杠采用玻璃纤维替代实施例1中的碳纤维,其余设置方式与实施例1中相同。
64.实施例6
65.本实施例中,提供一种汽车保险杠,所述汽车保险杠采用芳纶纤维代替实施例1中的树脂纤维,其余设置方式与实施例1中相同。
66.实施例7
67.本实施例中,提供一种汽车保险杠,所述汽车保险杠采用芳纶纤维代替实施例1中的树脂纤维,其余设置方式与实施例1中相同。
68.通过ansys进行仿真,利用ls-dyna对实施例1-7中所述汽车保险杠进行碰撞模拟,模拟结果显示前置面板最大位移及平均位移结果如下表1所示:
69.表1
[0070][0071]
以上所述仅为本实用新型的优选实施例而已,并不用于限制本实用新型,对于本领域的技术人员来说,本实用新型可以有各种更改和变化。凡在本实用新型的精神和原则之内,所作的任何修改、等同替换、改进等,均应包含在本实用新型的保护范围之内。