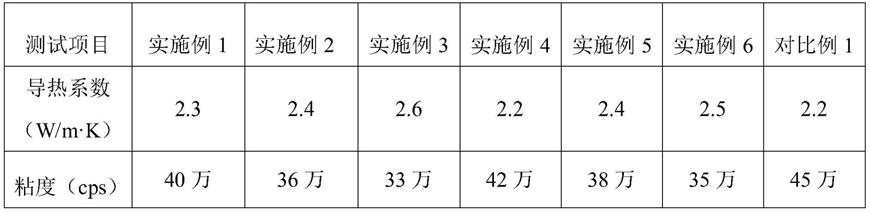
1.本发明涉及导热膏的制备方法,特别是涉及一种采用分步投料制备导热膏的方法。
背景技术:2.当前增强电子元件散热性能是重要的研究课题。在导热膏中加入高填充量的粉体,可以快速增加导热系数,但是随着导热粉体的加入,粘度也会急速上升,导致导热膏的涂覆性、浸润性、与界面的形状配合性降低,反而会导致导热膏使用时的接触热阻抗增大。性能好的导热膏不仅需要具备较高的导热系数,同时需要具备良好的粘度。现有技术中主要集中于导热系数,对于粘度的关注比较少。在理想的散热状态中,热源和散热器能够紧密的贴合在一起能使热源传输更多的热量,但是在真实的环境中,热源与散热器间会存在一些缝隙,其中存在空气,而空气的导热系数仅为0.026w/m
·
k,是热的不良导体,从而影响传热效果。因此需要研究多种类型的热界面材料来填补热源和散热器间的微观空隙及表面凹凸不平的孔洞,从而减少传热的阻抗,提高系统散热能力。现有技术中通常采用一步法,但一步投料法是将填料混合均匀需要耗费更长的时间,同时生产出的导热膏,批次稳定性较差,不利于生产的要求。
技术实现要素:3.发明目的:本发明提供一种采用分步投料制备导热膏的方法。
4.技术方案:本发明所述的采用分步投料制备导热膏的方法,将导热粉体的一种或多种与表面处理剂的一种或多种,混合,得到复合导热粉料,分多步将复合导热粉体与基体混合、真空除泡。
5.优选地,所述的基体选择二甲基硅油、乙烯基硅油的一种或多种,粘度100~1000cps。
6.优选地,所述的表面处理剂选择硅烷偶联剂、硅烷交联剂、钛酸酯偶联剂及铝酸酯偶联剂中的一种或多种。
7.优选地,所述的导热粉体选择氧化铝、氮化铝、氧化锌和氮化硼的一种或多种。
8.优选地,所述的填料形状选择球状、类球状、四足状、柱状及片状的一种或多种。
9.优选地,所述的填料粒径选择氧化铝粒径15~40μm。氮化硼粒径10~35μm。氧化锌粒径0.5~3μm。
10.优选地,所述的粒径15~40μm、10~35μm和0.5~3μm填料比例为6∶1∶1。
11.优选地,所述的复合粉料制备,采用搅拌转速30~80rpm/min,分散转速800~2000rpm/min,时间为1~6h。
12.优选地,所述分步投料的特征在于,分一步及以上将基体与粉料混合,每一步混合后复合粉体含量占总质量的5%~75%,最后一步投料结束后,粉体填料占总质量的80%~90%。
13.优选地,分步投入后在行星搅拌器内混合,特征在于搅拌转速30~80rpm/min,分散转速30~2000rpm/min,时间为1~6h,真空度
‑
0.02~
‑
0.05mpa。制备出导热膏。
14.有益效果:本发明与现有技术相比,具有如下优势:
15.本方法采用了分步投料的方法,能够将原材料混合的更加充分,一定程度上避免粉体的团聚。增加了分散,从而产生更多的导热通路,提高了导热。同时加入了氮化硼,由于其自身的高导热率,能够为成品导热膏提供较高的导热系数。球状的填料粉体,粉体间的摩擦更小,能够具有更好的流动性,易于产品的融合,提高性能。
具体实施方式
16.实施例1
17.导热膏制备
18.(1)分别称量质量为120g的球形氧化铝,粒径分布在15~40μm,20g球形氮化硼,粒径分布在10~35μm,20g氧化锌,粒径分布0.5~3μm,投入行星搅拌器内混合均匀。
19.(2)在上述复合粉体中加入1.6g的kh560硅烷偶联剂后,进行混合,搅拌转速40rpm/min,分散转速2000rpm/min,时间为1h,制备改性的导热粉体。
20.(3)在空的行星搅拌罐内添加24g的二甲基硅油,加入81g上述改性导热粉体,进行搅拌,搅拌转速40rpm/min分散转速2000rpm/min,保持罐内真空度
‑
0.02mpa,时间为1.5h。
21.(4)上述步骤结束后,加入剩余改性导热粉体,后进行混合,搅拌转速40rpm/min,分散转速2000rpm/min,保持罐内真空度
‑
0.02mpa,时间为1.5h。制备出导热膏。
22.实施例2
23.导热膏制备
24.(1)分别称量质量为120g的球形氧化铝,粒径分布在15~40μm,20g球形氮化硼,粒径分布在10~35μm,20g氧化锌,粒径分布0.5~3μm,投入行星搅拌器内混合均匀。
25.(2)在上述复合粉体中加入1.6g的kh560硅烷偶联剂后,进行混合,搅拌转速40rpm/min,分散转速2000rpm/min,时间为1h,制备改性的导热粉体。
26.(3)在空的行星搅拌罐内添加24g的二甲基硅油,加入53g上述改性导热粉体,进行混合,搅拌转速40rpm/min,分散转速2000rpm/min,保持罐内真空度
‑
0.02mpa,时间为1h。
27.(4)上述步骤结束后,继而在搅拌罐内投入53g改性导热粉体,进行混合,搅拌转速40rpm/min,分散转速2000rpm/min,保持罐内真空度
‑
0.02mpa,时间为1h。
28.(5)上述步骤结束后,加入剩余改性导热粉体,后进行混合,搅拌转速40rpm/min,分散转速2000rpm/min,保持罐内真空度
‑
0.02mpa,时间为1h。制备出导热膏。
29.实施例3
30.导热膏制备。
31.(1)分别称量质量为120g的球形氧化铝,粒径分布在15~40μm,20g球形氮化硼,粒径分布在10~35μm,20g氧化锌,粒径分布0.5~3μm,投入行星搅拌器内混合均匀。
32.(2)在上述复合粉体中加入1.6g的kh560硅烷偶联剂后,进行混合,搅拌转速40rpm/min,分散转速2000rpm/min,时间为1h,制备改性的导热粉体。
33.(3)在空的行星搅拌罐内添加24g的二甲基硅油,加入40g上述改性导热粉体,进行混合,搅拌转速40rpm/min,分散转速2000rpm/min,保持罐内真空度
‑
0.02mpa,时间为
45min。
34.(4)上述步骤结束后,继而在搅拌罐内投入40g改性导热粉体,进行混合,搅拌转速40rpm/min,分散转速2000rpm/min,保持罐内真空度
‑
0.02mpa,时间为45min。
35.(5)上述步骤结束后,加入40g导热粉体,后进行混合,搅拌转速40rpm/min,分散转速2000rpm/min,保持罐内真空度
‑
0.02mpa,时间为45min。
36.(6)上述步骤结束后,加入剩余的改性导热粉体,后进行混合,搅拌转速40rpm/min,分散转速2000rpm/min,保持罐内真空度
‑
0.02mpa,时间为45min。制备出导热膏。
37.实施例4
38.导热膏制备。
39.(1)分别称量质量为120g的球形氧化铝,粒径分布在15~40μm,20g球形氮化硼,粒径分布在10~35μm,20g氧化锌,粒径分布0.5~3μm,投入行星搅拌器内混合均匀。
40.(2)在上述复合粉体中加入1.6g的kh560硅烷偶联剂后,进行混合,搅拌转速40rpm/min,分散转速2000rpm/min,保持罐内真空度
‑
0.02mpa,时间1h。(3)上述步骤结束后,在改性好的粉体内加入12g的二甲基硅油,进行混合,搅拌转速40rpm/min,分散转速2000rpm/min,保持罐内真空度
‑
0.02mpa,时间为1.5h。
41.(4)上述步骤结束后,在改性好的粉体内加入12g的二甲基硅油,进行混合,搅拌转速40rpm/min,分散转速2000rpm/min,保持罐内真空度
‑
0.02mpa,时间为1.5h。
42.实施例5
43.导热膏制备
44.(1)分别称量质量为120g的球形氧化铝,粒径分布在15~40μm,20g球形氮化硼,粒径分布在10~35μm,20g氧化锌,粒径分布0.5~3μm,投入行星搅拌器内混合均匀。
45.(2)在上述复合粉体中加入1.6g的kh560硅烷偶联剂后,进行混合,搅拌转速40rpm/min,分散转速2000rpm/min,时间为1h,制备改性的导热粉体。
46.(3)上述步骤结束后,在改性好的粉体内加入8g的二甲基硅油,进行混合,搅拌转速40rpm/min,分散转速2000r pm/min,保持罐内真空度
‑
0.02mpa,时间为1h。
47.(4)上述步骤结束后,在改性好的粉体内加入8g的二甲基硅油,进行混合,搅拌转速40rpm/min,分散转速2000rpm/min,保持罐内真空度
‑
0.02mpa,时间为1h。
48.(5)上述步骤结束后,在改性好的粉体内加入8g的二甲基硅油,进行混合,搅拌转速40rpm/min,分散转速2000rpm/min,保持罐内真空度
‑
0.02mpa,时间为1h。制备出导热膏。
49.实施例6
50.导热膏制备
51.(1)分别称量质量为120g的球形氧化铝,粒径分布在15~40μm,20g球形氮化硼,粒径分布在10~35μm,20g氧化锌,粒径分布0.5~3μm,投入行星搅拌器内混合均匀。
52.(2)在上述复合粉体中加入1.6g的kh560硅烷偶联剂后,进行混合,搅拌转速40rpm/min,分散转速2000rpm/min,时间为1h,制备改性的导热粉体。
53.(3)上述步骤结束后,在改性好的粉体内加入6g的二甲基硅油,进行混合,搅拌转速40rpm/min,分散转速2000rpm/min,保持罐内真空度
‑
0.02mpa,时间为45min。
54.(4)上述步骤结束后,在改性好的粉体内加入6g的二甲基硅油,进行混合,搅拌转速40rpm/min,分散转速2000rpm/min,保持罐内真空度
‑
0.02mpa,时间为45min。
55.(5)上述步骤结束后,在改性好的粉体内加入6g的二甲基硅油,进行混合,搅拌转速40rpm/min,分散转速2000rpm/min,保持罐内真空度
‑
0.02mpa,时间为45min。
56.(6)上述步骤结束后,在改性好的粉体内加入6g的二甲基硅油,进行混合,搅拌转速40rpm/min,分散转速2000rpm/min,保持罐内真空度
‑
0.02mpa,时间为45min。
57.对比例1
58.(1)导热膏制备分别称量质量为120g的球形氧化铝,粒径分布在15~40μm,20g球形氮化硼,粒径分布在10~35μm,20g氧化锌,粒径分布0.5~3μm,投入行星搅拌器内混合均匀。
59.(2)在上述复合粉体中加入1.6g的kh560硅烷偶联剂后,进行混合,搅拌转速40rpm/min,分散转速2000rpm/min,时间为1h,制备改性的导热粉体。
60.(3)上述步骤结束后,在改性好的粉体内加入24g的二甲基硅油,进行混合,搅拌转速40rpm/min,分散转速2000rpm/min,保持罐内真空度
‑
0.02mpa,时间为3h。制备出导热膏。
61.对实施例1~6和对比例1进行导热系数和粘度进行测试,结果如表1所示:
62.表1不同投料次序对导热膏性能影响
[0063][0064]
从表1中比较实施例1~3和对比例1以及比较4~6与对比例1,可以发现分步投料法制备的导热膏相对于一步投料法,导热系数具有明显的提高。采用分步投料的粘度也明显优于一步投料法。
[0065]
从实施例1~3中不难看出,随着投料步骤从两步增加到四步,导热系数从2.3w/m
·
k增加到2.6w/m
·
k,粘度也从40万cps减小到33万cps。增加投料次数能够较为有效提高导热膏的导热系数,并降低其粘度。类似的规律在实施例4~6中也能够发现。
[0066]
对比实施例1~3与实施例4~6可以看出,将基体分步加入粉料的对于膏体的导热系数与粘度的提升效果相对不突出。而将粉料分步投入基体中,对于导热性能的提升是更为有效的。