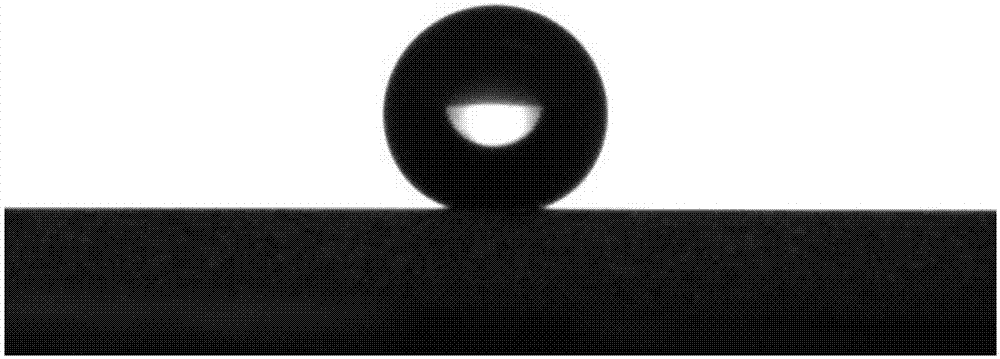
本发明属于光固化涂料
技术领域:
,具体涉及一种适合在玻璃上使用的具有高耐久性、抗水滴冲刷、超疏水自清洁纳米透明涂层及其制备方法。
背景技术:
:紫外光(uv)固化涂料第一份专利诞生在1947年,经过半个多世纪的发展,紫外光(uv)固化涂料已经成为较为成熟的技术,特别是随着人们环保意识的提高,生产和研究人员更加注意uv固化涂料的开发和应用。上世纪60年代末,拜耳公司基于不饱和树脂和安息香体系开发研究出一种新型环保节能的紫外光固化涂料。近年来,随着人们对能源利用以及环境保护等方面问题的不断重视,世界各国都在对传统挥发性有机化合物voc排放严重的溶剂型涂料进行限制和改进,更加重视基于绿色环保理念的涂层技术开发。目前,中国已发展成为继美国、日本之后,全球第三大辐射固化产品产地,这其中又以光固化涂料产量最大。在过去的几年中,紫外光(uv)固化涂料在光纤涂层、激光唱片(cd)涂层、数字化视频光盘(dvd)粘合剂、信用卡、木材、饮料罐、食品包装、杂志封面、医疗器械和汽车行业中都有着十分迅速的发展。由于疏水和超疏水表面独特的表面特性使其在自清洁表面、微流体系统和生物相容性等方面存在着潜在的应用,在国防、日常生活和众多工业领域有着广泛的市场前景,现已成为各大行业公司的研究热点。公开号cn103587185a的专利文献中公开了用纳米颗粒与树脂混合制备的超疏水涂层,该超疏水涂层虽然具备了一定抗刮擦性能,但无法实现涂层的透光性。公开号cn104987520a的专利文献中公开了一种适合玻璃基材的光学透明超疏水涂层,但是却无法保证涂层在玻璃上的有效硬度,限制了其涂层商业化的应用。目前材料表面疏水技术仍未能实现大规模化应用,究其原因在于超疏水涂层中存在大量的低表面能纳米颗粒无法与整体涂层起化学反应,导致在保证超疏水效果的同时涂层强度不够高,通常在玻璃基材中应用的涂层材料对透光性又提出了更高的要求。如何在保证超疏水涂层性能的前提下,实现涂层的高透光性,对研发人员提出了更高的要求。技术实现要素:针对现有技术中存在的问题,本发明提供一种紫外光固化超疏水透明耐磨涂层及其制备方法,所述制备方法具有高效、适应性广、经济、节能和环境友好等特点,同时制备所得到的紫外光固化超疏水透明耐磨涂层具有表面自清洁、表面防腐、疏水、防雾性、抗结冰等特点,具有对基材有良好的附着力。本发明提供的紫外光固化超疏水透明耐磨涂层的制备方法,具体步骤如下:第一步,透明基材活化预处理:透明基材表面预处理完后,将1~5%质量浓度的硅烷偶联剂加入到第一种有机溶剂中,然后将透明基材浸泡其中进行活化,在透明基材表面接枝上可参与反应的活性基团;所述的活性基团为含有不饱和官能团的丙烯酰氧基结构。第二步,按照重量百分比,将0.5~10%纳米颗粒和2~6%硅烷偶联剂加入到第二种有机溶剂中,在ph3~9的环境下进行水解反应,生成含有活性纳米颗粒的分散液。第三步,在含有活性纳米颗粒的分散液中加入活性氟单体、活性稀释剂和光引发剂,然后均匀施涂在经过第一步活化预处理后的透明基材上,在获得紫外光能量作用下固化得到超疏水透明耐磨涂层。与现有技术相比,本发明的优点在于:(1)本发明中的活性稀释剂、活性纳米颗粒、硅氧烷之间通过互相交叉反应形成共价键,有效提高超疏水涂层的耐磨性和硬度,克服传统超疏水涂层方法在直接喷涂到透明基材后,由于纳米颗粒在受到外力冲击后,从涂层表面脱落,导致超疏水效果失效的问题。(2)本发明构筑的微纳结构由于涂层体系中不含大分子树脂成分,得到的膜层厚度可以有效控制,保证了涂层的光学透明性。(3)本发明研究和制备的uv固化超疏水透明耐磨涂层推动超疏水涂层在应用化道路上的迈进步伐,市场前景广阔。附图说明图1为本发明制备的超疏水透明耐磨涂层结构示意图,在玻璃表面通过反应接枝硅氧烷化学基团和纳米颗粒。图2为在光学显微镜下观察到水滴(3μl)在超疏水透明耐磨涂层上呈现出球状。图3为本发明实施例1制备的超疏水透明耐磨涂层在可见光区域(390nm~780nm)的透光率曲线。图4a和图4b分别是实施例1和对比例1所制得涂层通过接触角测量仪分别测得的接触角。具体实施方式为了便于本领域技术人员的理解,下面结合附图和实施例对本发明作进一步的描述。本发明提供一种紫外光固化超疏水透明耐磨涂层的制备方法,具体步骤如下:第一步,透明基材活化预处理。本发明中对使用的透明基材没有特别的限定,可从现有光学透明特性(透光率大于80%)的材料中选择使用。本发明中使用的透明基材可为玻璃、透明陶瓷、ito(铟锡氧化物半导体透明导电膜)、聚对苯二甲酸乙二酯、聚对苯二甲酸丁二酯和聚萘二甲酸亚乙酯、聚乙烯、聚丙烯、玻璃纸、二乙酰基纤维素、三乙酰基纤维素、丁酸乙酰基纤维素、聚氯乙烯、聚偏氯乙烯、聚乙烯醇、乙烯-醋酸乙烯酯共聚物、聚苯乙烯、聚碳酸酯、聚甲基戊烯、聚砜、聚醚醚酮、聚醚酰亚胺、聚酰亚胺、氟树脂或聚酰胺中的任意一种,优选使用玻璃基材。本发明中使用的透明基材,在需要使用时可对透明基材的表面进行预处理,以便增强反应基团与透明基材表面的反应结合力。例如利用电晕放电处理,等离子体(plasma)处理,利用铬酸的处理(湿法),利用火焰的处理,利用加热空气的处理,或在臭氧存在下利用紫外线的照射处理,利用食人鱼溶液(piranha溶液,98%浓硫酸和30%过氧化氢以体积比为7:3的混合液)清洗。表面预处理根据透明基材的种类进行适当的选择,通常从作用和可操作性考虑。优选地,所述的预处理可以是等离子体(plasma)处理,次选为食人鱼溶液(piranha溶液)清洗。预处理完后,将1~5%质量浓度的硅烷偶联剂加入到第一种有机溶剂(此处为99%浓度的无水甲醇,乙醇,正丙醇,异丙醇中的一种)中,然后将透明基材浸泡其中进行活化,在透明基材表面接枝上可参与反应的活性基团。所述的活性基团为含有不饱和官能团的丙烯酰氧基结构。第二步,按照重量百分比,将0.5~10%纳米颗粒和2~6%硅烷偶联剂加入到第二种有机溶剂中,在ph3~9的环境下进行水解反应,生成含有活性纳米颗粒的分散液。本发明所述的纳米颗粒包括蓝宝石、氮化硅、白炭黑、碳化硅、氧化硅、氧化铝、氧化锆、氧化钛、玻璃料、氧化硅玻璃、纳钙玻璃、单元素或多元素氧化物,例如al2o3、ito、sno2、sio2、tio2、zro2、zno、bi2o3、v2o5、zns、coo、cofeo、mnfeo或bafeo。任意一种或者更多种纳米颗粒的组成都可变化,且不要求所有的纳米颗粒包括相同的组成。纳米颗粒可具有任意形状和表面结构。纳米颗粒的结构和聚集形貌可变化,且本发明的几何形貌和/或结构,形貌可以是球形、椭圆形、多面体、片状、多空、呈现晶体类结构,纳米颗粒表面可以是平滑的、粗糙的、有序的、无序的或图案化的。纳米颗粒可具有不同的尺寸或分布,或者对于一种的尺寸或分布,纳米颗粒的平均直径是5纳米~10000纳米,优选为10~100nm。所述的纳米颗粒的加入量优选为1~8%。本发明所述的硅烷r1nsi(or2)4-n,其中n=0~2;r1可以是cnh2n-1(n=1~18)的烷基,优选自四乙氧基硅烷、甲基三甲氧基硅烷、丙基三甲氧基硅烷、十八烷基三甲氧基硅烷、3-甲基丙烯酰氧丙基三甲氧基硅烷、3-甲基丙烯酰氧丙基三乙氧基硅烷、3-甲基丙烯酰氧丙基甲基二甲氧基硅烷、3-甲基丙烯酰氧丙基甲基二乙氧基硅烷、乙烯基三乙氧基硅烷、乙烯基三甲氧基硅烷、乙烯基三-(2-甲氧乙氧基)-硅烷、3-氨丙基三乙氧基硅烷、3-氨丙基三甲氧基硅烷、n-(2-氨乙基)-3-氨丙基三甲氧基硅烷、n-(2-氨乙基)-3-氨丙基三乙氧基硅烷、3-氨丙基甲基二甲氧基硅烷、n-正丁基-3-氨丙基三甲氧基硅烷、n-正丁基-3-氨丙基三乙氧基硅烷、3-脲丙基三甲氧基硅烷、3-二乙胺基丙基三甲氧基硅烷、3-(2,3-环氧丙氧)丙基三甲氧基硅烷、3-(2,3-环氧丙氧)丙基三乙氧基硅烷、3-(2,3-环氧丙氧)丙基甲基二甲氧基硅烷、3-(2,3-环氧丙氧)丙基甲基二乙氧基硅烷中的一种或者多种。所述的硅烷为一种含丙烯酰氧基的硅烷,优选γ-(甲基丙烯酰氧)丙基三甲氧基硅烷(商业名为kh570)或者3-甲基丙烯酰氧丙基甲基二甲氧基硅烷(商业名为kh572)作为光固化用的偶联剂,硅烷偶联剂在本反应体系中的作用非常重要,在纳米颗粒与透明基材、活性稀释剂、活性氟单体之间起着连接桥梁的作用。本发明所述的第二种有机溶剂,包括苯、甲苯、二甲苯、苯乙烯、丁基甲苯、乙烯基甲苯、二硫化碳、磷酸三邻甲酚、戊烷、己烷、辛烷、正已烷、环己烷、汽油、煤油、正己酮、环己酮、甲苯环己酮、氯苯、氯仿、二氯苯、二氯甲烷、三氯甲烷、全氯甲烷、二氯乙烯、三氯乙烯、全氯乙烯、甲醇、乙醇、正丙醇、异丙醇、n,n-二甲基丙烯酰胺、乙醚、环氧丙烷、甲酸甲酯、甲酸乙酯、甲酸丙酯、甲酸丁酯、甲酸戊酯、醋酸甲酯、醋酸乙酯、醋酸丙酯、醋酸丁酯、醋酸戊酯、丙酮、丁酮、甲基丁酮、甲基异丁酮、乙二醇单甲醚、乙二醇单乙醚、乙二醇单丁醚、乙烯乙二醇醚、呋喃、乙腈、吡啶、苯酚等。第三步,在含有活性纳米颗粒的分散液中加入活性氟单体、活性稀释剂和光引发剂,然后均匀施涂在经过第一步活化预处理后的透明基材上,在获得紫外光能量作用下固化得到超疏水透明耐磨涂层。通过以上三步方案在透明基材表面得到透明超疏水结构如图1所示,最上层为含氟低表面能层,中间为纳米颗粒结构层,最下层为硅氧烷基材接枝层。本发明采用的施涂方式包括:浸涂、旋涂、刮涂、喷涂、物理气相沉积、化学气相沉积、真空过滤、蒸镀、火焰喷涂、电喷雾、喷雾沉积、原位生长、微波辅助化学气相沉积法。所述的紫外光能量可以从高压汞灯获得,通常用于照射的紫外光剂量在200~400mj/cm2的范围内。所述的活性氟单体为高活性、含氟量高且具有较低表面活性氟单体,成膜过程中能够在涂层表面富集,形成致密、稳定的疏水保护膜层。具体地,所述的活性氟单体,包括全氟烷基乙醇聚氧乙烯醚、全氟烷基乙醇聚氧乙烯醚、丙烯酸六氟丁酯、甲基丙烯酸三氟乙酯、甲基丙烯酸十二氟庚酯、六氟丙烯三聚体、六氟丙烯二聚体、4,4′-(六氟异亚丙基)二酚、4,4-(六氟异丙烯)二酞酸酐、十二氟庚醇、全氟正己烷、全氟辛基磺酰氟、全氟环醚、2-(三氟甲基)丙烯酸、全氟辛醇丙烯酸酯、全氟丁基乙基碘、全氟(2-甲基-3-氧杂己基)氟化物、全氟辛基乙基丙烯酸酯、1-碘全氟癸烷、2,5-双(三氟甲基)-3,6-二氧杂十一氟代壬酰氟、2-(2-碘-四氟乙氧基)四氟乙基硫酰氟、2-全氟辛基乙基醇、全氟己基乙基醇、全氟辛基溴、全氟辛酸、全氟己酸、全氟己基溴、2-全氟烷基乙基醇、2-氟丙烯酸甲酯、六氟异丙醇、六氟丁醇、3-全氟己基丙醇、四氟丙醇、2,2,3,3,4,4,5,5-八氟-1-戊醇、2,2,3,3,3-五氟-1-丙醇、2-(全氟辛基)乙基甲基丙烯酸酯、2-(全氟己基)乙基甲基丙烯酸酯、全氟丁基乙基丙烯酸酯、1h,1h,2h-全氟-1-癸烯、三乙氧基-1h,1h,2h,2h-十三氟-n-辛基硅烷、全氟丁基乙基醇、全氟丁基乙烯、六氟磷酸钾、全氟碘代丁烷、2-全氟烷基乙基丙烯酸酯、全氟己基碘烷、全氟甲基环己烷、全氟碘辛烷、2-(全氟丁基)乙基甲基丙烯酸酯、全氟辛基乙基碘、全氟己基乙烯、全氟己基乙基碘。所述的活性氟单体优选含有官能性丙烯酰氧基全氟单体任意一种或者多种。特别的说明,含有丙烯酰氧基官能团的化合物可由紫外光照引起自由基交联反应,活化的自由基和可经历自由基引发的起交联反应的组分起反应。所述的活性氟单体的加入量为按照重量百分比为0.01~5%,优选加入量为0.1~3%。所述的活性稀释剂是一类含有丙烯酰氧基官能团的单体,可含有丙烯酰氧基、甲基丙烯酰氧基、乙烯基和烯丙基的任意一种或者多种官能团,在涂层uv固化成膜后期参与交联反应,改善固化后膜层的强度、附着力、耐候性等性能。另一方面,低分子量的丙烯酰氧基官能团的单体赋予uv固化膜层良好的透光性。本发明所述的活性稀释剂为新戊二醇二丙烯酸酯,三羟甲基丙烷三丙烯酸酯、季戊四醇三丙烯酸酯、甲基丙烯酸甲酯、丙烯酸甲酯、二缩三丙二醉二丙烯酸酯、二季戊四醇六丙烯酸酯、己二醇二丙烯酸酯、邻苯二甲酸二甘醇二丙烯稀酸酯、新戊二醇二丙烯酸酯、季戊四醇三丙烯酸酯、三羟甲基丙烷三丙烯酸酯、乙氧基化三羟甲基丙烷三丙烯酸酯、异冰片丙烯酸酯、甲基丙烯酸异冰片酯、二丙二醇二丙场酸酯、丙氧基化三羟甲基丙烷三丙烯酸酯、季戊醇四丙烯酸酯、1,3-丁二醇二丙烯酸酯中的任意一种或者多种。所述的活性稀释剂的加入量为重量百分含量0.001~5%。本发明所述活性稀释剂在光固化成膜过程中起到连接玻璃基材上的活性基团,活性纳米颗粒表面和含丙烯酰氧基全氟单体成交联网络结构,所述的活性稀释剂含量优选为0.05~5%,进一步优选含量为0.1~3%。本发明所述的光引发剂是本反应中的关键组分,它对光固化速度起着决定性作用,在吸收紫外光能量后能激发引起光化学变化,产生具有引发聚合能力的活性中间体。本发明所述的光引发剂为2-羟基-2-甲基-1-苯基丙酮,1-羟基环己基苯基甲酮,2-甲基-2-(4-吗啉基)-1-[4-(甲硫基)苯基]-1-丙酮,2,4,6-三甲基苯甲酰基-二苯基氧化膦,2,4,6-三甲基苯甲酰基苯基膦酸乙酯,2-二甲氨基-2-苄基-1-[4-(4-吗啉基)苯基]-1-丁酮,2-羟基-2-甲基-1-[4-(2-羟基乙氧基)苯基]-1-丙酮,苯甲酰甲酸甲酯中的任意一种。所述的光引发剂的加入量的重量百分比为0.001~2%,优选为0.01~1%。实施例1将玻璃基材浸泡在食人鱼洗液中清洗,除去表面残留的有机溶剂,烘干留用。取10份硅烷偶联剂加入到100份甲醇中,将洗净的玻璃基材浸泡其中并在室温下保持10h,烷基活化玻璃基材表面结构。取5份气相纳米氧化铝,尺寸粒径分布在50~80nm,加入到100份甲醇中;另外调节溶液ph值为3~4,30~45℃水浴条件下搅拌反应12h,最终得到活性纳米颗粒的分散液。取50份分散液,加入0.5份2-全氟辛基乙基甲基丙烯酸酯,1.5份三羟甲基丙烷三丙烯酸酯,0.25份1-羟基环己基苯基甲酮,搅拌混合均匀,制得涂布液。将所制涂布液喷涂到事先活化的透明玻璃基材表面上,在60~80℃之间对形成的涂层干燥10分钟之后,以300mj/cm2的紫外线照射剂量对干燥的涂层进行固化,形成紫外光固化超疏水透明耐磨涂层,涂层透明性如图3所示。实施例2将玻璃基材用乙醇溶剂清洗烘干,然后放入到等离子体清洗机中进行等离子体预处理玻璃表面结构。取10份硅烷偶联剂加入到100份乙醇中,将预处理后的玻璃片室温下浸泡10h,烷基活化玻璃片表面结构。取5份纳米zno粉,尺寸粒径分布在20~40nm,加入到100份正丙醇中,另外调节溶液ph值为3~4,40~50℃水浴条件下搅拌反应24h,最终得到活性纳米颗粒的分散液。取50份分散液,加入0.5份全氟丁基乙基丙烯酸酯,1.5份甲基丙烯酸甲酯,0.25份2-羟基-2-甲基-1-苯基丙酮,搅拌混合均匀,制得涂布液。将所制涂布液喷涂到烷基化的透明玻璃上,在60~80℃之间对形成的涂层干燥10分钟之后,以300mj/cm2的紫外线照射剂量对干燥的涂层进行固化,形成紫外光固化超疏水透明耐磨涂层。实施例3将玻璃基材用乙醇溶剂清洗烘干,然后放入到等离子体清洗机中进行等离子体预处理玻璃表面结构。取10份硅烷偶联剂加入到100份甲醇中,将洗净的玻璃片室温下浸泡8h,烷基活化玻璃片表面结构。取5份纳米sio2粉,尺寸粒径分布在10~30nm,加入到100份醋酸乙酯中,另外调节溶液ph值为4~5,40~50℃水浴条件下搅拌反应12h,最终得到活性纳米颗粒的分散液。取50份分散液,加入0.5份2-氟丙烯酸甲酯,1份二季戊四醇六丙烯酸酯,0.5份2,4,6-三甲基苯甲酰基-二苯基氧化膦,搅拌混合均匀,制得涂布液。将事先活化的透明玻璃浸渍到涂布液中浸泡10分钟,然后夹出在60~80℃之间对形成的涂层干燥5分钟之后,以300mj/cm2的紫外线照射剂量对干燥的涂层进行固化,并形成紫外光固化超疏水透明耐磨涂层。实施例4将玻璃片浸泡在食人鱼洗液中清洗,除去表面残留的有机溶剂,烘干留用。取10份硅烷偶联剂加入到100份甲醇中,将洗净的玻璃片室温下浸泡10h,烷基活化玻璃片表面结构。取6份纳米氧化铟锡粉,尺寸粒径分布在80~100nm,加入到100份异丙醇中,另外调节溶液ph值为8~9,40~50℃水浴条件下搅拌反应18h,最终得到活性纳米颗粒的分散液。取50份分散液,加入1份2-(全氟辛基)乙基甲基丙烯酸酯,1份二缩三丙二醉二丙烯酸酯,0.5份苯甲酰甲酸甲酯,搅拌混合均匀,制得涂布液。将事先活化的透明玻璃浸渍到涂布液中浸泡10分钟,然后夹出在60~80℃之间对形成的涂层干燥5分钟之后,以300mj/cm2的紫外线照射剂量对干燥的涂层进行固化,并形成紫外光固化超疏水透明耐磨涂层。实施例5将玻璃片浸泡在食人鱼洗液中清洗,除去表面残留的有机溶剂,烘干留用。取10份硅烷偶联剂加入到100份甲醇溶液中,将洗净的玻璃片室温下浸泡10h,烷基活化玻璃片表面结构。取6份纳米zro2颗粒,尺寸粒径分布在40~50nm,加入到100份乙醇中,另外调节溶液ph值为8~9,40~50℃水浴条件下搅拌反应20h,最终得到活性纳米颗粒的分散液。取50份分散液,加入1份甲基丙烯酸十二氟庚酯,1.5份二季戊四醇六丙烯酸酯,0.5份2-羟基-2-甲基-1-苯基丙酮,搅拌混合均匀,制得涂布液。将事先活化的透明玻璃浸渍到涂布液中浸泡10分钟,然后夹出在60~80℃之间对形成的涂层干燥1分钟之后,以300mj/cm2的紫外线照射剂量对干燥的涂层进行固化,并形成紫外光固化超疏水透明耐磨涂层。对上述实施例1~5中所提供的紫外光固化超疏水透明耐磨涂层进行性能测试,结果见下表1,经测试均能达到如下技术指标的要求。表1紫外光固化超疏水透明耐磨涂层的性能测试结果项目测试标准测试结果铅笔硬度gb/t6739-2006大于1h附着力gb9286-980级接触角gb/t26490-2011>150°滚动角gb/t30447-2013<5°透光性gb/t2680-1994>90%对比例1本对比例中所述的紫外光固化超疏水透明耐磨涂层所选用的组分与实施例1中所给出的原料组分相同,其区别仅在于按照实施例1的方案各步骤进行操作,但是在最后一步采取将2-氟丙烯酸甲酯的单体含量减为0份,其他条件保持不变。将本对比例同样进行60~80℃热烘干,再进行紫外光固化反应。通过光学照片容易观察到所得的样品,结果如图4所示,所述涂层在紫外光固化过程之后不具有超疏水性能。对比例2本对比例中所述的紫外光固化超疏水透明耐磨涂层所选用的组分与实施例1中所给出的原料组分相同,其区别仅在于按照实施例1的方案进行同样操作后,对体系中的活性纳米颗粒换成degussar812s产品(是一类由亲水气相二氧化硅经六甲基二硅氮烷后处理的疏水型气相法二氧化硅)之后,同样对比例进行60~80℃热烘干之后进行紫外光固化反应。按照国标gb/t6739-2006对实施例1和对比例2用铅笔法测试漆膜硬度。该测试方法是采用已知硬度标号表示涂膜硬度的测定方法。经测试,对比例2中所制备的涂层测试结果为5b远不如实施例1中所制备涂层的1h硬度。本测试结果说明了活性纳米颗粒在整体涂料中与活性稀释剂进行化学反应对提升涂层强度有明显的作用,而r812s纳米气硅外层包裹一层甲基基团在干燥固化的涂层中只有物理结构上的堆积无法有效提高涂层硬度。显然,上述实施例仅仅是为清楚地说明所作地举例,而并非对实施方式的限定。对于所属领域的普通技术人员来说,在上述说明的基础上还可以做出其它不同形式的变化或变动。这里无需也无法对所有的实施方式予以穷举。而由此所引伸出的显而易见的变化或变动仍处于本发明创造的保护范围之中。当前第1页12