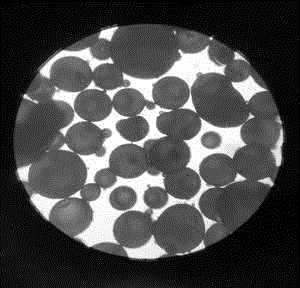
本发明涉及环氧树脂粉末涂料改性方法
技术领域:
,特别是涉及一种石墨烯微片基耐腐蚀环氧树脂粉末涂料的制备方法。
背景技术:
:粉末涂料是以固体树脂和颜料、填料及助剂等组成的固体粉末状合成树脂涂料。与普通溶剂型涂料及水性涂料不同,粉末涂料无溶剂污染,存储方便,而且成膜后具有优异的耐久性。相比传统的溶剂涂料、水性涂料,粉末涂料的应用领域和范围更宽。粉末涂料有热塑性和热固性两大类。热塑性粉末涂料的涂膜外观(光泽和流平性)较差,与金属之间的附着力也差,所以在金属涂装领域中应用极少。金属涂装一般采用热固性粉末涂料,热固性粉末涂料是以热固性合成树脂为成膜物质,在烘干过程中树脂先熔融,再经化学交联后固化成平整坚硬的涂膜。该种涂料形成的漆膜外观和各种机械性能及耐腐蚀性均能满足汽车涂饰的要求。鉴于粉末涂料良好的环保特性以及适合在金属表面固化成膜,因此,粉末涂料作为金属防腐层具有巨大的发展空间。特别是热固性粉末涂料质地坚硬,适合用于机械设备、车辆等的外层涂料。热固性粉末涂料一般由树脂、固化剂、颜料、填料和助剂组成。它是以热固性树脂作为成膜物质,加入起交联反应的固化剂经过加热以后形成的质地坚硬的涂层。它在具有很好的装饰性的同时由于低分子量的预聚物经固化以后,可以形成网状交联的大分子,在喷涂时良好的流平性、润湿性,能牢固的粘附于金属表面,与基底结合紧密,从而形成优异的装饰层和耐腐性,因此它是优异的金属防腐涂料。环氧粉末涂料是一种具有耐腐蚀性和坚韧性的热固性粉末涂料,应用最早,快速发展,环氧粉末涂料的制备是采用国际通用生产热固性粉末涂料的唯一方法,即熔融混合挤出法--混合、熔融混合挤出、粉碎。环氧树脂粉末涂料具有优异的粘和性,在金属表面喷涂热固化后得到坚硬的涂层,具有较好的防腐蚀性能。然而随着对防腐蚀性能要求和装饰性能的提高,现有热固性粉末涂料急需改进以提升其耐腐蚀性。由于热固性环氧树脂对室外紫外线敏感,容易发生老化和腐蚀。中国专利cn201610502926.x公开了直缝焊管表面专用防腐涂层料,通过在环氧粉末基料中加入稀土氧化物、纳米级粉料等,使得防腐层在受到冲击时,防腐层只会发生变形不会发生剥离现象。由于稀土氧化物、纳米级粉料的防腐蚀效果并不好,虽然防腐层不会变形脱落,但是其耐腐蚀性能并不优良,并不能很好的演唱直缝焊管的使用寿命。中国专利cn104109450a公开了一种石墨烯防腐粉末涂料,制得粉末涂料具有优异的防腐性能。但是由于石墨烯在聚合物中分散效果不理想,反而会影响漆膜的性能。此外石墨烯具有导电性能,会影响粉末涂料静电涂装的性能。中国专利cn102604533a公开了一种基于聚苯胺与石墨烯复合材料的防腐涂料及制备方法。该发明的防腐涂料,可以实现金属基材的钝化和缓蚀,同时避免了可以导致环境污染的锌等重金属的使用。但其制备过程复杂,在制备过程中使用了苯胺,毒性较大,对操作人员的健康损伤较大,不适宜工业化大规模生产。石墨烯作为优异的耐腐蚀性材料,成为改进环氧树脂耐腐蚀性的最佳选择。目前已有将石墨烯用于环氧树脂来提升耐腐蚀性。然而由于石墨烯分散性较差,如果不能有效的将石墨烯分散在涂料中,使得粉末墨烯界面难以形成致密的耐腐蚀层。因此最为迫切的是解决石墨烯微分散问题。技术实现要素:鉴于以上所述现有技术的缺点,本发明的目的在于提供一种石墨烯微片基耐腐蚀环氧树脂粉末涂料的制备方法,用于解决现有技术中环氧树脂粉末涂料耐腐蚀和耐老化性能不足以及石墨烯难以分散形成致密的耐腐蚀层的问题。本发明通过预先将石墨烯微片分散在酚醛改性环氧树脂中固化形成微球,以此作为负载石墨烯微片的填料,直接作为填料加入环氧树脂复合粉末中制备改性的环氧树脂粉末涂料;其中预先负载固化后利于将石墨烯微片分散在环氧树脂中更容易分散,再通过强气流冲击的同时高温固化形成球形微粒,利于填料负载石墨烯微片。为实现上述目的及其他相关目的,一种石墨烯微片基耐腐蚀环氧树脂粉末涂料的制备方法,包括如下步骤:步骤一、将石墨烯微片和酚醛改性环氧树脂按照重量份配比为1:(5~10)加入密炼机中捏合分散至少5min,得到石墨烯微片与酚醛改性环氧树脂分散物;再向石墨烯微片与酚醛改性环氧树脂分散物中加入固化剂a、云母粉和硫酸钡继续捏合分散至少5min,得到疏松状混合物料待用;步骤二、将步骤一中疏松状混合物料加入高速气流冲击机中,高温固化为球形微粒;步骤三、将步骤二中的球形微粒、环氧树脂复合粉末和表面活性剂按照重量份配比(10-15):(30~60):(2~6)加入高速搅拌机中,搅拌分散即得石墨烯微片基耐腐蚀环氧树脂粉末涂料。石墨烯微片基耐腐蚀环氧树脂粉末涂料的制备方法是先通过将石墨烯微片与酚醛改性环氧树脂加入密炼机捏合分散,然后加入固化剂a、云母粉(云母粉的添加量是过量的,除了作为隔离剂外还可以作为无机填料提高整体强度)和硫酸钡分散,在过量云母粉、硫酸钡隔离作用下物料分散为疏松状,进一步利用强气流在高温下冲击悬浮物料,悬浮物料在强气流冲击的同时高温固化形成球形微粒;最后通过将球形微粒、环氧树脂复合粉末和表面活性剂分散后制得的石墨烯微片基耐腐蚀环氧树脂粉末涂料。通过预先将石墨烯微片分散在酚醛改性环氧树脂中固化形成微球,以此作为负载石墨烯微片的填料,可以直接作为填料加入环氧粉末中制备粉末涂料;一方面,如果直接将石墨烯微片加入环氧树脂其分散难度较大,但是采用预先负载固化后利于将石墨烯微片分散在环氧树脂,可以明显提高石墨烯微片在环氧树脂中的分散性能;另一方面,将预先负载了石墨烯微片的疏松状混合物料,在强气流冲击的同时高温固化形成球形微粒,球形微粒利于负载石墨烯微片,球形微粒此外还具有良好的分散性和流动性,将球形微粒加入环氧粉末中易于制备流平性较好的涂料层。通过将球形微粒、环氧树脂粉末和表面活性剂分散后制得的石墨烯微片基耐腐蚀环氧树脂粉末涂料,在喷涂时具有良好的流平性、能牢固的粘附于金属表面,涂层与金属基底结合紧密,石墨烯微片在涂层中均匀分散,涂层具有优异的耐腐蚀。与现有的环氧树脂粉末涂料相比,石墨烯微片基耐腐蚀环氧树脂粉末涂料、在具有优良的耐热性的同时,还具有优异的耐腐蚀性,在各种使用环境下具有更加长久的寿命。进一步地,所述步骤一中酚醛改性环氧树脂中包括质量分数为35~40%的一阶热固性酚醛树脂和质量分数为60~65%的二酚基丙烷环氧树脂;所述步骤一中石墨烯微片与酚醛改性环氧树脂分散物、固化剂a、云母粉和硫酸钡的重量份配比为(40~70):(1~5):(4~12):(15~25)。进一步地,所述步骤一中固化剂a为乙二胺、二乙烯三胺、三乙烯四胺中的至少一种。进一步地,所述步骤一中石墨烯微片与酚醛改性环氧树脂分散物、固化剂a、云母粉和硫酸钡的重量份配比为(50~60):(1~5):(6~10):20;所述石墨烯微片与酚醛改性环氧树脂分散物中石墨烯微片和酚醛改性环氧树脂的重量份配比为1:(6~8)。进一步地,所述步骤一中密炼机的混炼温度为80~90℃,转速为35~45r/min。进一步地,所述步骤二中高速气流冲击机的处理温度为200~230℃,空气压力为1.2~1.8mpa。利用强气流在高温下冲击悬浮物料,悬浮物料在强气流冲击的同时高温固化形成球形微粒。进一步地,所述步骤二中球形微粒的粒径为25~50μm。进一步地,所述步骤三中环氧粉末的制备过程为:将环氧树脂、固化剂b、流平剂和颜料按照重量份的配比为30:(1~3):(3~4):(1~2)混合后加入双螺杆挤出机中,在温度为90~100℃下挤出压片得到环氧树脂片材,再将环氧树脂片材加入粉碎机中粉碎至粒径≤50μm,即得环氧树脂复合粉末。进一步地,所述环氧树脂为环氧树脂e-12;所述流平剂为硅丙烯酸酯,所述颜料为钛白粉;固化剂b为双氰胺与葵二酸二酰肼以质量比1:1的复合物。进一步地,所述步骤三中表面活性剂为烷基苯磺酸钠;所述高速混合机的搅拌速度为750~800r/min,搅拌时间为30~40min。烷基苯磺酸钠是阴离子表面活性剂中最重要的一种,也是中国合成洗涤剂的主要活性成分。烷基苯磺酸钠去污力强、起泡力和泡沫稳定性以及化学稳定性好,而且原料来源充足、生产成本低,有着广泛的用途。十二烷基苯磺酸钠是一种性能优良的合成阴离子表面活性剂,它比肥皂更易溶于水,是一种黄色油状液体。它有很好的脱脂能力并有很好的降低水的表面张力和润湿、渗透和乳化的性能。它的化学性质稳定,在酸性或碱性介质中以及加热条件下都不会分解,与次氯酸钠过氧化物等氧化剂混合使用也不会分解。它可以用烷基苯经过磺化反应制备,原料来源充足,成本低,制造工艺成熟,产品纯度高。有益效果:通过预先将石墨烯微片分散在酚醛改性环氧树脂中固化形成微球,以此作为负载石墨烯微片的填料,可以直接作为填料加入环氧粉末中制备粉末涂料;一方面,如果直接将石墨烯微片加入环氧树脂其分散难度较大,但是采用预先负载固化后利于将石墨烯微片分散在环氧树脂,可以明显提高石墨烯微片在环氧树脂中的分散性能;另一方面,将预先负载了石墨烯微片的疏松状混合物料,在强气流冲击的同时高温固化形成球形微粒,球形微粒利于负载石墨烯微片,球形微粒此外还具有良好的分散性和流动性,将球形微粒加入环氧粉末中易于制备流平性较好的涂料层。通过将球形微粒、环氧粉末和表面活性剂分散后制得的石墨烯微片基耐腐蚀环氧树脂粉末涂料,在喷涂时具有良好的流平性、能牢固的粘附于金属表面,涂层与金属基底结合紧密,石墨烯微片在涂层中均匀分散,涂层具有优异的耐腐蚀。与现有的环氧树脂粉末涂料相比,石墨烯微片基耐腐蚀环氧树脂粉末涂料、在具有优良的耐热性的同时,还具有优异的耐腐蚀性,在各种使用环境下具有更加长久的寿命。附图说明图1显示为一种石墨烯微片基耐腐蚀环氧树脂粉末涂料的制备方法中球形微粒的1600倍显微图。图2显示为一种石墨烯微片基耐腐蚀环氧树脂粉末涂料的制备方法的流程图。具体实施方式以下通过具体实施方式对本发明作进一步的详细说明,但不应将此理解为本发明的范围仅限于以下的实例。在不脱离本发明上述方法思想的情况下,根据本领域普通技术知识和惯用手段做出的各种替换或变更,均应包含在本发明的范围内。实施例1一种石墨烯微片基耐腐蚀环氧树脂粉末涂料的制备方法,包括如下步骤:步骤一、将石墨烯微片和酚醛改性环氧树脂按照重量份配比为1:5入密炼机中捏合分散5min,密炼机的混炼温度为90℃,转速为45r/min,得到石墨烯微片与酚醛改性环氧树脂分散物;再向石墨烯微片与酚醛改性环氧树脂分散物中加入固化剂乙二胺、云母粉和硫酸钡继续捏合分散5min,石墨烯微片与酚醛改性环氧树脂分散物、固化剂乙二胺、云母粉和硫酸钡的重量份配比为40:1:4:15,密炼机的混炼温度为90℃,转速为45r/min,得到疏松状混合物料待用;其中,酚醛改性环氧树脂中包括质量分数为35%的一阶热固性酚醛树脂和质量分数为65%的二酚基丙烷环氧树脂;步骤二、将步骤一中疏松状混合物料加入高速气流冲击机中,处理温度为200℃,空气压力为1.8mpa,高速冲击悬浮25min,,高温固化为球形微粒,球形微粒的粒径约在为25~50μm;如附图1所示为得到的球形微粒的1600倍显微图,具有良好的球形。步骤三、将步骤二中的球形微粒、环氧树脂复合粉末和表面活性剂十二烷基苯磺酸钠按照重量份配比10:30:2加入高速搅拌机中,750r/min,搅拌时间为40min,搅拌分散即得石墨烯微片基耐腐蚀环氧树脂粉末涂料。具体地,环氧粉末的制备过程为:将环氧树脂e-12、固化剂b(双氰胺与葵二酸二酰肼以质量比1:1的复合物)、流平剂硅丙烯酸酯和颜料钛白粉按照重量份的配比为30:1:3:1混合后加入双螺杆挤出机中,在温度为90℃下挤出压片得到环氧树脂片材,再将环氧树脂片材加入粉碎机中粉碎至粒径≤50μm,即得环氧树脂复合粉末。实施例2一种石墨烯微片基耐腐蚀环氧树脂粉末涂料的制备方法,包括如下步骤:步骤一、将石墨烯微片和酚醛改性环氧树脂按照重量份配比为1:10加入密炼机中捏合分散8min,密炼机的混炼温度为80℃,转速为35r/min,得到石墨烯微片与酚醛改性环氧树脂分散物;再向石墨烯微片与酚醛改性环氧树脂分散物中加入固化剂二乙烯三胺、云母粉和硫酸钡继续捏合分散8min,石墨烯微片与酚醛改性环氧树脂分散物、固化剂二乙烯三胺、云母粉和硫酸钡的重量份配比为60:5:10:20,密炼机的混炼温度为80℃,转速为35r/min,得到疏松状混合物料待用;酚醛改性环氧树脂中包括质量分数为40%的一阶热固性酚醛树脂和质量分数为60%的二酚基丙烷环氧树脂;步骤二、将步骤一中疏松状混合物料加入高速气流冲击机中,处理温度为230℃,空气压力为1.2mpa,气流高压冲击悬浮处理30min,高温固化为球形微粒,球形微粒的粒径为25~50μm;步骤三、将步骤二中的球形微粒、环氧树脂复合粉末和表面活性剂十二烷基苯磺酸钠按照重量份配比12:60:6加入高速搅拌机中,800r/min,搅拌时间为30min,搅拌分散即得石墨烯微片基耐腐蚀环氧树脂粉末涂料。具体地,环氧树脂复合粉末的制备过程为:将环氧树脂e12、固化剂b(双氰胺与葵二酸二酰肼以质量比1:1的复合物)、流平剂硅丙烯酸酯和颜料钛白粉按照重量份的配比为30:3:4:2混合后加入双螺杆挤出机中,在温度为100℃下挤出压片得到环氧树脂片材,再将环氧树脂片材加入粉碎机中粉碎至粒径≤50μm,即得环氧树脂复合粉末。实施例3一种石墨烯微片基耐腐蚀环氧树脂粉末涂料的制备方法,包括如下步骤:步骤一、将石墨烯微片和酚醛改性环氧树脂按照重量份配比为1:10加入密炼机中捏合分散8min,密炼机的混炼温度为80℃,转速为35r/min,得到石墨烯微片与酚醛改性环氧树脂分散物;再向石墨烯微片与酚醛改性环氧树脂分散物中加入固化剂二乙烯三胺、云母粉和硫酸钡继续捏合分散8min,石墨烯微片与酚醛改性环氧树脂分散物、固化剂二乙烯三胺、云母粉和硫酸钡的重量份配比为60:5:10:20,密炼机的混炼温度为80℃,转速为35r/min,得到疏松状混合物料待用;酚醛改性环氧树脂中包括质量分数为40%的一阶热固性酚醛树脂和质量分数为60%的二酚基丙烷环氧树脂;步骤二、将步骤一中疏松状混合物料加入高速气流冲击机中,处理温度为230℃,空气压力为1.2mpa,气流高压冲击悬浮处理30min,高温固化为球形微粒,球形微粒的粒径为25~50μm;步骤三、将步骤二中的球形微粒、环氧树脂复合粉末和表面活性剂十二烷基苯磺酸钠按照重量份配比15:60:6加入高速搅拌机中,800r/min,搅拌时间为30min,搅拌分散即得石墨烯微片基耐腐蚀环氧树脂粉末涂料。具体地,环氧树脂复合粉末的制备过程为:将环氧树脂e12、固化剂b(双氰胺与葵二酸二酰肼以质量比1:1的复合物)、流平剂硅丙烯酸酯和颜料钛白粉按照重量份的配比为30:3:4:2混合后加入双螺杆挤出机中,在温度为100℃下挤出压片得到环氧树脂片材,再将环氧树脂片材加入粉碎机中粉碎至粒径≤50μm,即得环氧树脂复合粉末。实施例4一种石墨烯微片基耐腐蚀环氧树脂粉末涂料的制备方法,包括如下步骤:步骤一、将石墨烯微片和酚醛改性环氧树脂按照重量份配比为1:8加入密炼机中捏合分散5min,密炼机的混炼温度为85℃,转速为40r/min,得到石墨烯微片与酚醛改性环氧树脂分散物;再向石墨烯微片与酚醛改性环氧树脂分散物中加入固化剂三乙烯四胺、云母粉和硫酸钡继续捏合分散5min,石墨烯微片与酚醛改性环氧树脂分散物、固化剂三乙烯四胺、云母粉和硫酸钡的重量份配比为70:5:12:26,密炼机的混炼温度为85℃,转速为40r/min,得到疏松状混合物料待用;具体地,酚醛改性环氧树脂中包括质量分数为36%的一阶热固性酚醛树脂和质量分数为64%的二酚基丙烷环氧树脂;步骤二、将步骤一中疏松状混合物料加入高速气流冲击机中,处理温度为220℃,空气压力为1.3mpa,高速气流冲击悬浮处理25min,高温固化为球形微粒,球形微粒的粒径为25~50μm;步骤三、将步骤二中的球形微粒、环氧树脂复合粉末和表面活性剂十二烷基苯磺酸钠按照重量份配比10:54:4加入高速搅拌机中,780r/min,搅拌时间为35min,搅拌分散即得石墨烯微片基耐腐蚀环氧树脂粉末涂料。具体地,环氧粉末的制备过程为:将环氧树脂e-12、固化剂b(双氰胺与葵二酸二酰肼以质量比1:1的复合物)、流平剂硅丙烯酸酯和颜料钛白粉按照重量份的配比为30:2:3:2混合后加入双螺杆挤出机中,在温度为95℃下挤出压片得到环氧树脂片材,再将环氧树脂片材加入粉碎机中粉碎至粒径≤50μm,即得环氧树脂复合粉末。实施例5一种石墨烯微片基耐腐蚀环氧树脂粉末涂料的制备方法,包括如下步骤:步骤一、将石墨烯微片和酚醛改性环氧树脂按照重量份配比为1:7加入密炼机中捏合分散7min,密炼机的混炼温度为80℃,转速为45r/min,得到石墨烯微片与酚醛改性环氧树脂分散物;再向石墨烯微片与酚醛改性环氧树脂分散物中加入固化剂乙二胺、云母粉和硫酸钡继续捏合分散7min,石墨烯微片与酚醛改性环氧树脂分散物、固化剂乙二胺、云母粉和硫酸钡的重量份配比为55:3:8:20,密炼机的混炼温度为80℃,转速为45r/min,得到疏松状混合物料待用;具体地,酚醛改性环氧树脂中包括质量分数为37%的一阶热固性酚醛树脂和质量分数为63%的二酚基丙烷环氧树脂;步骤二、将步骤一中疏松状混合物料加入高速气流冲击机中,处理温度为210℃,空气压力为1.5mpa,悬浮处理45min高温固化为球形微粒,球形微粒的粒径为25~50μm;步骤三、将步骤二中的球形微粒、环氧树脂复合粉末和表面活性剂十二烷基苯磺酸钠按照重量份配比10:45:4加入高速搅拌机中,800r/min,搅拌时间为35min,搅拌分散即得石墨烯微片基耐腐蚀环氧树脂粉末涂料。具体地,环氧粉末的制备过程为:将环氧树脂e-12、固化剂b(双氰胺与葵二酸二酰肼以质量比1:1的复合物)、流平剂硅丙烯酸酯和颜料钛白粉按照重量份的配比为30:2:3:2混合后加入双螺杆挤出机中,在温度为95℃下挤出压片得到环氧树脂片材,再将环氧树脂片材加入粉碎机中粉碎至粒径≤50μm,即得环氧树脂复合粉末。对比例1对比例1:没有将固化后的球形颗粒加入到环氧树脂复合粉中,其余与实施例1一致。由于没有石墨烯微片与酚醛改性环氧树脂均匀分散在粉末涂料中,得到的环氧树脂粉末涂料耐热性与耐腐蚀性较差。对比例2对比例2:没有将石墨烯微片与酚醛改性环氧树脂的疏松物料固化成球形颗粒,将石墨烯微片与酚醛改性环氧树脂中加入固化剂和过量的云母粉、硫酸钡进行分散后就粉碎处理,其余与实施例1一致。由于石墨烯分散在酚醛改性环氧树脂中不够均匀,环氧树脂粉末涂料具有一定的耐腐蚀性但提升不够理想。将实施例1~实施例5以及对比例1~对比例2制备得到的粉末涂料喷涂膜制样。喷膜制备:将金属不锈钢空白样板(50mm×1200mm×0.5mm)经二甲苯洗净,再用丝绸布擦干,试板处理完以后放在喷粉柜中,用高压静电发生器进行喷涂。喷涂厚度为80微米。将喷涂的样品保持垂直,放入恒温干燥箱中进行固化。固化温度为180℃,固化时间30min,然后将样板置于(23±2)℃,相对湿度(50±5)%的恒温恒湿条件下放置24h,即为制板完成。参考国家标准gb1763-89漆膜耐化学试剂性测定法对漆膜进行测试,主要测试在酸、碱、盐中浸泡后的漆膜变化。a、耐酸性测定:将涂料板的2/3分别浸泡在温度为25℃、质量分数为4.5%的硫酸溶液中,每隔24小时后取出,用水清洗涂料板后用吸湿纸擦拭表面,检查漆膜表面有无变色、失光、小泡、斑点、脱落等情况。b、耐碱性测定:将涂料板的2/3分别浸泡在温度为25℃、质量分数为4.5%的氢氧化钠溶液中,每隔24小时后取出,用水清洗涂料板后用吸湿纸擦拭表面,检查漆膜表面有无变色、失光、小泡、斑点、脱落等情况。c、耐盐水测定:将涂料板的2/3浸泡在温度为25℃、质量分数为3%的nacl水溶液中,每隔24小时后取出,用水清洗涂料板后用吸湿纸擦拭表面,检查漆膜表面有无剥落、起皱、起泡、生锈、失光等情况。d、附着力测定:采用百格刀qfh测试,压住刀头划过涂料板,刀头刮起表面涂布物(至底材),再作90度角交叉切割,形成十字型的交叉方格状。划线平滑、网格没有出现涂层剥离现象为0级;网格的交叉部分有少许剥落、小于5%的划格面积受到影响为1级;划线边缘和网格交叉部分均有剥落、大于5%且小于15%的划格面积受到影响为2级;划线边缘有部分或整块剥落、大于15%且小于35%的划格面积受到影响为3级;划线边缘有部分或整片剥落、某些网格有部分或完全剥落、大于35%且小于65%的划格面积受到影响为4级;不能用等级4来划分的记为5级。表格测试项目耐酸性耐碱性耐盐水附着力/级实施例130天无变化,无粉化、溶出现象30天无变化,无粉化、溶出现象30天无变化,无开裂、无起皱1实施例230天无变化,无粉化、溶出现象30天无变化,无粉化、溶出现象30天无变化,无开裂、无起皱1实施例330天无变化,无粉化、溶出现象30天无变化,无粉化、溶出现象30天无变化,无开裂、无起皱1实施例430天无变化,无粉化、溶出现象30天无变化,无粉化、溶出现象30天无变化,无开裂、无起皱1实施例530天无变化,无粉化、溶出现象30天无变化,无粉化、溶出现象30天无变化,无开裂、无起皱1对比例15天后出现溶出现象7天后出变色、失光现象9天后出现起皱、起泡等现象3对比例214天后出现溶出现象16天后出变色、失光现象17天后出现起皱、起泡等现象2对比例1相较于实施例1而言没有将石墨烯微片与酚醛改性环氧树脂均匀分散在粉末涂料中,得到的环氧树脂粉末涂料耐盐雾性与耐腐蚀性较差。对比例2相较于实施例1没有球化处理,由于影响分散,因此虽然耐腐蚀性能提升,但是不能满足工业需求。当前第1页12