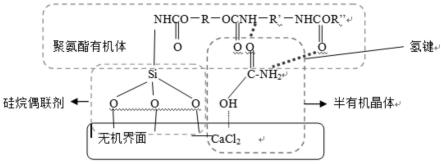
1.本发明属于单组分聚氨酯防水涂料技术领域,更具体地,涉及一种硅烷改性单组分聚氨酯防水涂料及其制备方法。
背景技术:2.单组分聚氨酯防水涂料是由多元醇、异氰酸酯经聚合反应生成的含有异氰酸酯基团的预聚体,与填料、多种功能助剂在反应釜中经过化学反应、物理混合而成。该防水涂料成品为单一组分,施工时无须搅拌混合,直接涂刷使用,具有综合性能优异、施工便捷的特点。
3.目前市场上的单组分聚氨酯防水涂料主要有两种技术方案:
4.其一,湿固化体系,涂料中的异氰酸酯基团直接与空气中的水汽反应,从而交联固化,该过程中会释放出二氧化碳,造成涂膜中有大量气泡,施工后性能差,存在漏水的风险。
5.其二,潜固化体系,在涂料配方中添加潜固化剂,施工后,涂料中的潜固化剂优先与空气中的水汽反应,释放出含有活性氢的氨基,氨基再与涂料中的异氰酸酯基团反应,达到交联固化的目的。因潜固化剂与水的反应、氨基与异氰酸酯的反应均不生成气体,故在固化过程中从根本上避免了气泡的产生。
6.因潜固化体系固化速度快,反应不产生气泡,所以现在市场上单组分聚氨酯防水涂料绝大多数属于潜固化体系。潜固化体系虽然成膜速度快,不产生气泡,但是在使用过程中依然存在着缺点,尤其是在南方,南方因降水较多,地面在做防水施工时,基层往往是潮湿状态,无法达到聚氨酯施工要求的干燥基层,而潜固化剂体系的单组分聚氨酯防水涂料在潮湿基层环境下,潜固化剂会迅速与基层的湿气进行反应,在聚氨酯和基层处形成交联,无法使得聚氨酯涂膜渗透到基层,导致与基层的粘接力特别差,做完防水施工后无法形成与基层的粘接强度,最终导致鼓包,甚至与基层脱离的现象。
7.湿固化体系固化速度慢,所以涂料体系可以长时间渗透到基层,在潮湿基层上的粘接力比潜固化体系要优异,但是由于湿固化本身固化速度慢,容易起泡,在市场上的占比较低,也不易被人们接受。
技术实现要素:8.本发明的目的是提供一种硅烷改性单组分聚氨酯防水涂料及其制备方法,使得制备的聚氨酯防水涂料与潮湿基层具有良好的粘接强度。
9.为了实现上述目的,本发明的一方面提供一种硅烷改性单组分聚氨酯防水涂料的制备方法,该制备方法包括:(1)将部分端羟基聚醚和改性硅烷偶联剂进行接触反应,得到硅烷改性的聚醚多元醇;
10.(2)将剩余的端羟基聚醚、所述硅烷改性的聚醚多元醇、增塑剂、其他助剂和分散剂混合均匀;
11.(3)将步骤(2)得到的混合物料、填料、半有机晶体和任选的颜料混合均匀;
12.(4)将步骤(3)得到混合物料进行真空脱水;
13.(5)将步骤(4)得到的混合物料与溶剂混合,然后加入多异氰酸酯,进行反应;
14.(6)将经过步骤(5)反应后的物料、潜固化剂和催化剂混合均匀,然后进行真空脱气,得到所述硅烷改性单组分聚氨酯防水涂料。
15.根据本发明,优选地,以重量份数计,所述端羟基聚醚的用量为20-40份、所述改性硅烷偶联剂的用量为0.5-5份、所述增塑剂的用量为5-25份、所述分散剂的用量为0.08-0.5份、所述其他助剂的用量为0.1-1.5份、所述填料的用量为25-55份、所述半有机晶体的用量为0.05-5份、所述溶剂的用量为5-15份、所述多异氰酸酯的用量为3-15份、所述潜固化剂的用量为0.5-5份、所述催化剂的用量为0.03-0.5份和所述颜料的用量为0-1份。
16.本发明中,通过减少潜固化剂的用量,降低体系的黏度,提高其储存稳定性,同时也有利于渗透潮湿基层,提高其粘接性能。
17.根据本发明,优选地,以重量份数计,所述其他助剂包括:消泡剂0.1-1份、流平剂0-0.2份和防尘剂0-0.3份。
18.根据本发明,优选地,所述改性硅烷偶联剂为异氰酸酯基硅烷偶联剂;
19.所述改性硅烷偶联剂优选为3-异氰酸酯基丙基三甲氧基硅烷和/或3-异氰酸酯基丙基三乙氧基硅烷。
20.根据本发明,优选地,所述半有机晶体为甘氨酸型半有机晶体;
21.所述甘氨酸型半有机晶体选自甘氨酸-氯化钙半有机晶体、甘氨酸-硫酸镁半有机晶体和甘氨酸-溴化钙半有机晶体中的至少一种。
22.本发明中,通过异氰酸酯基硅烷偶联剂对单组分聚氨酯防水涂料进行接枝改性,改性后的聚氨酯预聚体末端含有机硅原子和异氰酸酯,有机硅可以在有机材料与无机材料间发生化学键合(偶联),所以在潮湿基层施工时,依靠预聚体末端的有机硅和半有机晶体在聚氨酯涂膜和混凝土基层之间形成化学键合,提高其潮湿基层的粘接能力。
23.加入半有机晶体材料,其中氨基成分与聚氨酯预聚体形成氢键,钙类和/或镁类无机盐成份与水泥基层的相容性更好,使得有机硅在聚氨酯预聚体有机料与水泥基层无机材料之间通过半有机晶体有更多的结合度,使得潮湿基层粘接强度更大。
24.本发明中,所述半有机晶体可以通过商购获得,也可以自己合成获得;当自己合成时,可以按照如下方法获得:
25.选择甘氨酸型半有机晶体,将甘氨酸与氯化钙、硫酸镁或溴化钙按反应方程式的摩尔比进行称量,加水溶解,在50℃下参照氯化钙、硫酸镁或溴化钙各自的溶解度曲线配制出甘氨酸与氯化钙、硫酸镁或溴化钙的饱和溶液,匀速搅拌降温至室温,通过蒸发得到晶体后,再进行重结晶两到三次,即得到甘氨酸型半有机晶体。
26.其中,甘氨酸-氯化钙半有机晶体是甘氨酸与氯化钙按照2:1的摩尔比混合,反应方程式如下:
27.2nh2ch2cooh+cacl2+4h2o
→
[cacl2(nh
3+
ch2coo-)2]
·
4h2o
[0028]
甘氨酸-硫酸镁半有机晶体是甘氨酸与硫酸镁按照1:1的摩尔比混合,反应方程式如下:
[0029]
nh2ch2cooh+mgso4·
7h2o
→
mg[nh2ch2cooh]so4·
7h2o
[0030]
甘氨酸-溴化钙半有机晶体是甘氨酸与溴化钙按照2:1的摩尔比混合,反应方程式
如下:
[0031]
2nh2ch2cooh+cabr2+4h2o
→
[cabr2(nh
3+
ch2coo-)2]
·
4h2o。
[0032]
本发明选择成份接近于水泥砂浆成份的钙盐和/或镁盐合成半有机晶体,由氨基酸合成的半有机晶体,表面会含有大量的氨基,可以与聚氨酯氨酯羰基形成大量氢键,而无机物钙盐和/或镁盐,与水泥基层的成份类似,更容易渗透在基层内部。
[0033]
根据本发明,优选地,所述端羟基聚醚选自ppg类聚醚多元醇、pop类聚合物聚醚多元醇和ptmeg类聚四氢呋喃型聚醚多元醇中的至少一种;
[0034]
所述聚醚多元醇选自聚醚二元醇、聚醚三元醇和聚醚四元醇中的至少一种;
[0035]
所述端羟基聚醚的重均分子量为500-5000,羟值为40-400mg koh/g。
[0036]
本发明的制备方法中,当所用的端羟基聚醚为多种时,步骤(1)中的部分端羟基聚醚可以只选择多种端羟基聚醚的一种取一部分用来制备硅烷改性的聚醚多元醇;也可以选择多种端羟基聚醚中的多种或全部,然后分别取一部分共同用来制备硅烷改性的聚醚多元醇。例如,所用端羟基聚醚为聚醚二元醇和聚醚三元醇时,可以仅选择部分聚醚二元醇用来制备硅烷改性的聚醚多元醇;也可以选择部分聚醚二元醇和部分聚醚三元醇,共同用来制备硅烷改性的聚醚多元醇。
[0037]
根据本发明,优选地,所述多异氰酸酯为甲苯二异氰酸酯(tdi)和/或二苯基甲烷二异氰酸酯;
[0038]
所述潜固化剂为亚胺型潜固化剂和/或恶唑烷型潜固化剂。
[0039]
根据本发明,优选地,所述催化剂选自二月桂酸二丁基锡、辛酸亚锡、异辛酸铅、脂肪胺类催化剂、脂环胺类催化剂、芳香胺类催化剂和醇胺催化剂中的至少一种;
[0040]
所述增塑剂选自为环己烷1,2-二甲酸二异壬基酯、氯化石蜡、尼龙酸甲酯和柠檬酸酯类中的至少一种;
[0041]
所述分散剂为酸性分散剂,所述酸性分散剂优选为聚硅氧烷类有机分散剂;
[0042]
所述填料为高岭土、重钙、轻钙、氧化镁、氧化钙、硅灰石、纳米碳酸钙、硅微粉和滑石粉中的至少一种;
[0043]
所述颜料为炭黑、钛白粉、靛蓝、铁黄和铁棕中的至少一种;
[0044]
所述溶剂为芳烃类溶剂油、100#溶剂油、120#溶剂油、150#溶剂油和200#溶剂油中的至少一种。
[0045]
本发明中,所用的增塑剂与聚氨酯相容性好,基本不迁移或很少迁移,稳定性和协同性显著。
[0046]
根据本发明,优选地,所述部分端羟基聚醚和所述剩余的端羟基聚醚的质量比为1:(0.5-5);
[0047]
步骤(1)中,所述接触反应的温度为75-85℃;
[0048]
步骤(3)中,混合的温度为45-55℃;
[0049]
步骤(4)中,在-0.09至-0.1mpa的真空下进行真空脱水,真空脱水的温度控制在105-110℃,当水分≤0.02%时,停止脱水;
[0050]
步骤(5)中,当温度为80-70℃时,将步骤(4)得到的混合物料与溶剂混合;当温度为68-60℃时,加入多异氰酸酯,搅拌10-20min后升温至80-90℃,在80-90℃下反应2-3h;
[0051]
步骤(6)中,当温度为65-70℃时,将经过步骤(5)反应后的物料、潜固化剂和催化
剂混合均匀,然后当温度为55-50℃时,在-0.09至-0.1mpa的真空下脱气30-40min。
[0052]
本发明中,硅烷改性聚氨酯防水涂料的反应原理如下:
[0053]
涉及的反应原理,由异氰酸酯基硅烷偶联剂对其进行改性,反应如下:
[0054][0055]
端羟基聚醚与多异氰酸酯反应,生成聚氨酯预聚体,反应如下:
[0056][0057]
本发明中,如图1所示,硅烷改性单组分聚氨酯防水涂料采用异氰酸酯基的硅烷偶联剂对部分聚醚多元醇进行单侧封端,其余部分的聚醚多元醇由多异氰酸酯进行封端,在潮湿基层施工时,封端的硅烷偶联剂可以水解形成硅醇(si(oh)3),而与无机物质结合,形成硅氧烷。可在聚氨酯涂膜和基层之间形成分子桥,把两种材料连接在一起。其中,半有机晶体是由有机物甘氨酸和无机物(钙盐或者镁盐)合成,其中无机物离子可渗透到水泥基层中,而无机物表面的氨基可以和聚氨酯氨酯羰基形成强烈的氢键,使得聚氨酯有机涂膜与无机基层粘接性更强,同时硅烷也可与半有机晶体在基层中形成键合力,经过硅烷和半有机晶体的复合作用,可以使得聚氨酯涂膜在潮湿基层有很强的粘接性能。
[0058]
本发明中,端羟基聚醚、多异氰酸酯:在合成过程中发生化学反应,形成具有网状交联结构的预聚体,形成涂料的基本骨架;增塑剂:液体填料,降低体系的粘度,同时提高涂膜的耐低温性能及柔韧性;固体填料:能加强涂膜的耐磨性能和耐压性能;催化剂:催化预聚体合成的反应速度和干燥速度;消泡剂:消除搅拌带入的气泡及反应过程中产生的少量气泡;潜固化剂:与水快速反应释放出活性氨基,一方面该氨基与预聚体反应,交联固化,另一方面催化涂膜干燥;酸性分散剂:一方面加强填料的分散效果,降低产品的粘度,另一方面,在一定程度上起抑制作用,与潜固化剂的催化作用相互配合,控制涂膜的干燥时间,有利于气泡从涂料中溢出,达到消泡的目的。改性硅烷偶联剂:对聚氨酯预聚体进行硅烷改性,提高其对潮湿基层的粘接能力;半有机晶体:提高硅烷偶联剂在有机体与无机体之间的结合度,增强潮湿基层粘接能力。
[0059]
本发明的另一方面提供上述制备方法制备的硅烷改性单组分聚氨酯防水涂料。
[0060]
本发明的技术方案具有如下有益效果:本发明的硅烷改性单组分聚氨酯防水涂料既解决了湿固化体系的外观气泡、干燥速度慢的问题,又解决了潜固化体系储存性能差、潮湿基层粘接不劳的问题,可适用于南方潮湿基层的施工应用,是一种综合性能优异的新体系单组分聚氨酯防水涂料。
[0061]
本发明的其它特征和优点将在随后具体实施方式部分予以详细说明。
附图说明
[0062]
通过结合附图对本发明示例性实施方式进行更详细的描述,本发明的上述以及其它目的、特征和优势将变得更加明显,其中,在本发明示例性实施方式中,相同的参考标号通常代表相同部件。
[0063]
图1示出了本发明的以甘氨酸-氯化钙半有机晶体为示例的硅烷改性单组分聚氨酯防水涂料的粘接原理示意图。
具体实施方式
[0064]
下面将更详细地描述本发明的优选实施方式。虽然以下描述了本发明的优选实施方式,然而应该理解,可以以各种形式实现本发明而不应被这里阐述的实施方式所限制。相反,提供这些实施方式是为了使本发明更加透彻和完整,并且能够将本发明的范围完整地传达给本领域的技术人员。
[0065]
以下通过实施例进一步说明本发明:
[0066]
以下各实施例和对比例中:
[0067]
所用的甘氨酸-氯化钙由如下方法制得:将甘氨酸与氯化钙按反应方程式的摩尔比进行称量,加水溶解,在50℃下参照氯化钙的溶解度曲线配制出甘氨酸与氯化钙的饱和溶液,匀速搅拌降温至室温,通过蒸发得到晶体后,再进行重结晶两到三次,即得到甘氨酸-氯化钙;
[0068]
所用的甘氨酸-溴化钙由如下方法制得:将甘氨酸与溴化钙按反应方程式的摩尔比进行称量,加水溶解,在50℃下参照溴化钙的溶解度曲线配制出甘氨酸与溴化钙的饱和溶液,匀速搅拌降温至室温,通过蒸发得到晶体后,再进行重结晶两到三次,即得到甘氨酸-溴化钙;
[0069]
其中,甘氨酸-氯化钙半有机晶体是甘氨酸与氯化钙按照2:1的摩尔比混合,反应方程式如下:
[0070]
2nh2ch2cooh+cacl2+4h2o
→
[cacl2(nh
3+
ch2coo-)2]
·
4h2o
[0071]
甘氨酸-溴化钙半有机晶体是甘氨酸与溴化钙按照2:1的摩尔比混合,反应方程式如下:
[0072]
2nh2ch2cooh+cabr2+4h2o
→
[cabr2(nh
3+
ch2coo-)2]
·
4h2o。
[0073]
所用的聚醚二元醇为ppg类聚醚多元醇,购自万华公司,牌号为c2020;聚醚三元醇为ppg类聚醚多元醇,购自万华公司,牌号为f3135;
[0074]
3-异氰酸酯基丙基三甲氧基硅烷购自日本信越公司,牌号为kbe-9007;
[0075]
dinp购自上海昆瑞化工公司,牌号为dinp;
[0076]
tdi购自basf公司,牌号为t-80;
[0077]
酸性分散剂为聚硅氧烷类有机分散剂,购自毕克公司,牌号为byk-at203;
[0078]
催化剂为二月桂酸二丁基锡,购自赢创公司,牌号为t-12;
[0079]
潜固化剂为亚胺型潜固化剂,购自艾利特公司,牌号为alt-401;
[0080]
消泡剂购自毕克公司,牌号为byk-065;
[0081]
流平剂购自埃夫科纳公司,牌号为afcona-3033;
[0082]
溶剂油为150#溶剂油。
[0083]
实施例1-3
[0084]
实施例1-3提供了一种硅烷改性单组分聚氨酯防水涂料,具备制备方法如下,所用的原料及用量见表1;
[0085]
(1)称取部分聚醚二元醇,在四口烧瓶中升温至80℃,加入异氰酸酯基硅烷偶联剂(3-异氰酸酯基丙基三甲氧基硅烷),在80
±
2℃下反应2h,形成硅烷改性的聚醚多元醇;
[0086]
(2)在装有温度计、真空系统、搅拌系统的四口烧瓶中加入剩余的聚醚二元醇、聚醚三元醇、所述硅烷改性的聚醚多元醇、增塑剂(氯化石蜡和dinp)、消泡剂、流平剂、酸性分散剂,加完后开启搅拌并升温,转速300r/min;
[0087]
(3)加热至50℃时,称量并加入一定量的填料(滑石粉和重钙)、半有机晶体,搅拌0.5h,经均质机循环0.5h;
[0088]
(4)在四口烧瓶中升温至105℃时,开启真空系统,在-0.09至-0.1mpa的真空下脱水,温度控制在105-110℃,脱水2h,当水分≤0.02%时,停止脱水,开始降温;
[0089]
(5)当温度降至80℃时,加入溶剂油;当温度降至65℃时,加入tdi,搅拌10min后升温至85℃,在85
±
2℃下反应2h;
[0090]
(6)降温至65℃,加入潜固化剂、催化剂,搅拌30min;降温至50℃,在-0.1mpa的真空下脱气30min,即得硅烷改性单组分聚氨酯防水涂料;
[0091]
其中,部分端羟基聚醚(部分聚醚二元醇)和所述剩余的端羟基聚醚(剩余的聚醚二元醇和聚醚三元醇)的质量比分别为:1:2.23(实施例1中);1:1.16(实施例2中);1:1.05(实施例3中)。
[0092]
对比例1
[0093]
本对比例提供一种湿固化体系的单组分聚氨酯防水涂料,具体原料见表1,制备方法如下:
[0094]
(1)在装有温度计、真空系统、搅拌系统的四口烧瓶中加入聚醚二元醇、聚醚三元醇、增塑剂(氯化石蜡和dinp)、消泡剂、流平剂、酸性分散剂,加完后开启搅拌并升温,转速300r/min;
[0095]
(2)加热至50℃时,称量并加入一定量的填料(滑石粉和重钙),搅拌0.5h,经均质机循环0.5h;
[0096]
(3)在四口烧瓶中升温至105℃时,开启真空系统,在-0.09至-0.1mpa的真空下脱水,温度控制在105-110℃,脱水2h,当水分≤0.02%时,停止脱水,开始降温;
[0097]
(4)当温度降至80℃时,加入溶剂油;当温度降至65℃时,加入tdi,搅拌10min后升温至85℃,在85
±
2℃下反应2h;
[0098]
(5)降温至65℃,加入催化剂,搅拌30min;降温至50℃,在-0.1mpa的真空下脱气30min,即得单组分聚氨酯防水涂料。
[0099]
对比例2
[0100]
本对比例提供一种潜固化体系的单组分聚氨酯防水涂料,具体原料见表1,制备方法如下:
[0101]
(1)在装有温度计、真空系统、搅拌系统的四口烧瓶中加入聚醚二元醇、聚醚三元醇、增塑剂(氯化石蜡和dinp)、消泡剂、流平剂、酸性分散剂,加完后开启搅拌并升温,转速300r/min;
[0102]
(2)加热至50℃时,称量并加入一定量的填料(滑石粉和重钙),搅拌0.5h,经均质机循环0.5h;
[0103]
(3)在四口烧瓶中升温至105℃时,开启真空系统,在-0.09至-0.1mpa的真空下脱水,温度控制在105-110℃,脱水2h,当水分≤0.02%时,停止脱水,开始降温;
[0104]
(4)当温度降至80℃时,加入溶剂油;当温度降至65℃时,加入tdi,搅拌10min后升温至85℃,在85
±
2℃下反应2h;
[0105]
(5)降温至65℃,加入潜固化剂、催化剂,搅拌30min;降温至50℃,在-0.1mpa的真空下脱气30min,即得单组分聚氨酯防水涂料。
[0106]
表1(表1中各原料用量单位均为g)
[0107][0108][0109]
测试例1
[0110]
按照gb/t19250-2013标准对实施例和对比例进行性能测试,具备测试结果见表2。
[0111]
表2
[0112][0113]
由上表可知:(1)3个实施例的性能均符合国标要求。(2)实施例与对比例1相比,硅烷改性单组分聚氨酯防水涂料的表干、实干时间比湿固化体系的快,潮湿基层粘接强度与湿固化体系相当;实施例与对比例2相比,表实干固化速度相当,但是潮湿基层的粘接强度远远高于潜固化体系和湿固化体系。(3)实施例与对比例1相比,硅烷改性单组分聚氨酯体系的涂膜外观无气泡、无针眼,而湿固化的外观有较多的小气泡和针眼,影响涂膜的密实性。(4)实施例2、3与实施例1相比,减少了半有机晶体的加入量,潮湿基层粘接强度降低了20%,说明半有机晶体能起到促进聚氨酯与基层粘接的复合作用。(5)综合比较:硅烷改性单组分聚氨酯防水涂料同时具有湿固化体系和潜固化体系的优点,表实干速度快,涂膜外观良好,无针眼及气泡,而且在潮湿基层粘接强度优异。
[0114]
测试例2
[0115]
本测试例为储存粘度测试,具体测试方法为:5个试样,装在5个相同、密封性优异的1000ml铁罐中,放置在50℃烘箱中储存一定时间,然后在25℃下测试涂料的运动粘度,以此来评价其储存性能。具体测试结果见表3。
[0116]
表3实施例及对比组在50℃热储存时的粘度变化(单位:mpa.s)
[0117]
储存时长实施例1实施例2实施例3对比例1对比例2初始值582062606700720082001周8700821084507960124002周97201070098008070158003周1120012100115007900195004周135001560013400820023400
[0118]
由上表可知:实施例与对比例1、对比例2相比,湿固化体系的涂料在50℃储存时,粘度基本无变化,略有增长。硅烷改性单组分聚氨酯的粘度随热储存时间延长,粘度在小幅
度的增长。潜固化体系,在热储存过程中,粘度大幅度增长。因粘度较大,施工性能差,严重影响产品保质期,潜固化体系涂料储存性能极差。故硅烷改性单组分聚氨酯防水涂料较潜固化体系有较好储存稳定性。
[0119]
测试例3
[0120]
本测试例为常温储存拉伸性能测试,按照gb/t19250-2013标准,对常温储存下的防水涂料进行拉伸性能测试,具体测试结果见表4。
[0121]
表4实施例与对比组在常温储存时的拉伸性能变化(单位:mpa)
[0122][0123]
由上表可知:(1)实施例与对比例1、对比例2相比,硅烷改性单组分聚氨酯防水涂料在常温储存下,随着储存时间延长,拉伸强度几乎无变化,略呈下降的趋势;湿固化体系和潜固化体系的拉伸强度随储存时间延长,拉伸强度明显下降,甚至不合格(≤2.00mpa)。(2)实施例与对比例1、对比例2相比,硅烷改性单组分聚氨酯防水涂料在常温储存下,随着储存时间延长,伸长率呈下降的趋势,但6个月后仍符合国标(伸长率≥500%)。湿固化体系的和潜固化体系的随着储存时间延长,伸长率极速衰减,储存三个月后已不符合国标要求(伸长率≤500%)。故,硅烷改性单组分聚氨酯防水涂料的储存性能明显优于湿固化体系和潜固化体系。
[0124]
综上,由测试例1-3可知:(1)在外观上,硅烷改性单组分聚氨酯防水涂料外观无气泡、无针眼,明显优于湿固化体系;(2)在储存性能上,硅烷改性单组分聚氨酯防水涂料的储存性能明显优于湿固化体系、潜固化体系;储存6个月后,涂膜表面仍密实无气泡、无针眼,力学性能仍符合国标gb/t19250-2013。(3)在潮湿基层粘接测试数据下,硅烷改性单组分聚氨酯防水涂料粘接强度明显优于湿固化体系和潜固化体系。
[0125]
以上已经描述了本发明的各实施例,上述说明是示例性的,并非穷尽性的,并且也不限于所披露的各实施例。在不偏离所说明的各实施例的范围和精神的情况下,对于本技术领域的普通技术人员来说许多修改和变更都是显而易见的。