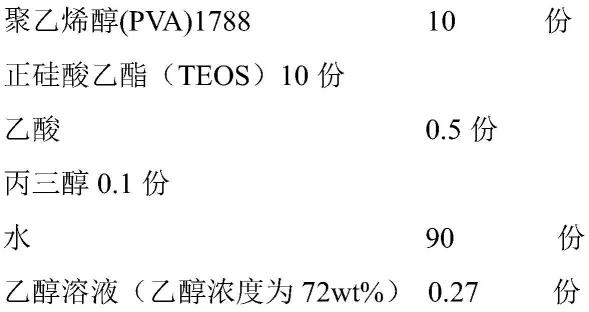
pvd镀腔内壁构件用涂层组合物、pvd镀腔内壁构件及其制备方法和清洗方法
技术领域
1.本发明涉及pvd镀膜技术领域,更具体地,涉及一种pvd镀腔内壁构件用涂层组合物、pvd镀腔内壁构件及其制备方法和清洗方法。
背景技术:2.在pvd真空镀膜设备中,镀腔内壁构件的表面在镀膜过程中也被沉积镀层金属的杂质层,一方面,杂质层随着镀膜时间的累积越来越厚,易脱落,污染镀件,另一方面,杂质层不易去除,现有技术主要采用物理和化学途径去除杂质层,首先通过物理方式敲打、剐蹭,随后通过化学方式(例如硝酸)将杂质层反应掉,待将杂质层反应完后及时取出镀腔内壁构件,中止反应,然而,这种处理方法不仅费时费力,而且损伤镀腔内壁构件。
技术实现要素:3.本发明的目的在于克服现有技术存在的上述缺陷,提供一种pvd镀腔内壁构件用涂层组合物、pvd镀腔内壁构件及其制备方法和清洗方法,通过在镀腔内壁构件本体表面形成一层主要由聚乙烯醇构成的水凝胶涂层,该涂层不仅能增强与杂质层的结合力,防止杂质层脱离,而且清洗时易溶于水,不仅便于清洗镀腔内壁构件,而且不损伤镀腔内壁构件。
4.为实现上述目的,本发明的一技术方案如下:
5.一种pvd镀腔内壁构件用涂层组合物,所述涂层组合物的原料包括以下质量份数的组分:
6.3份~10份的聚乙烯醇、0.5份~10份的交联剂和0.03份~0.1份的多元醇增塑剂;
7.所述交联剂包括水性封闭型异氰酸酯交联剂或硅氧烷交联剂。
8.本发明还公开了一种pvd镀腔内壁构件,包括镀腔内壁构件本体和形成于所述镀腔内壁构件本体上的涂层,所述涂层包括上述的涂层组合物。
9.本发明还公开了上述pvd镀腔内壁构件的制备方法,包括以下过程:
10.对被杂质层污染后的所述pvd镀腔内壁构件进行水洗,所述水洗过程中,所述杂质层和所述涂层均被去除,得到清洗后的镀腔内壁构件本体。
11.实施本发明实施例,将具有如下有益效果:
12.一实施方式中,本发明提供一种涂层组合物,包括聚乙烯醇、交联剂和增塑剂,聚乙烯醇主要提供胶黏性,增强涂层与镀腔内壁构件和杂质层的结合力,避免涂层和杂质层脱落,污染镀件,交联剂主要对聚乙烯醇进行耐高温和机械强度改性,使得固化后的涂层不仅具有一定机械强度,能保护镀腔内壁构件,而且在pvd的高温工艺过程中能保持稳定性,增韧性主要对聚乙烯醇进行增韧改性,降低涂层的脆性,避免涂层脱落。
13.另一实施方式中,通过将涂层形成于镀腔内壁构件本体的表面,不仅利用涂层隔离保护镀腔内壁构件本体,而且利用涂层易溶于水的特性,便于水洗去除涂层以及沉积在涂层上的镀层金属的杂质层,水洗不仅有利于环保,而且便于回收杂质层的镀层金属。
具体实施方式
14.下面将结合本发明实施例,对本发明实施例中的技术方案进行清楚、完整地描述,显然,所描述的实施例仅仅是本发明一部分实施例,而不是全部的实施例。基于本发明中的实施例,本领域普通技术人员在没有作出创造性劳动前提下所获得的所有其他实施例,都属于本发明保护的范围。
15.本发明公开了一种pvd镀腔内壁构件用涂层组合物,涂层组合物的原料包括以下质量份数的组分:3份~10份的聚乙烯醇、0.5份~10份的交联剂和0.03份~0.1份的多元醇增塑剂;交联剂包括水性封闭型异氰酸酯交联剂或硅氧烷交联剂。
16.在上述方案中,聚乙烯醇主要提供胶黏性,增强涂层与镀腔内壁构件和杂质层的结合力,避免涂层和杂质层脱落,污染镀件,交联剂主要对聚乙烯醇进行耐高温和机械强度改性,使得固化后的涂层不仅具有一定机械强度,能保护镀腔内壁构件,而且在pvd的高温工艺过程中能保持稳定性,增韧性主要对聚乙烯醇进行增韧改性,降低涂层的脆性,避免涂层脱落。
17.在一些实施例中,硅氧烷交联剂包括正硅酸乙酯、甲基三乙氧基硅烷、γ-氨丙基三乙氧基硅烷和γ-甲基丙烯酰氧基丙基三甲氧基硅烷中的至少一种。
18.在一些实施例中,水性封闭型异氰酸酯交联剂包括hdi/三羟甲基己基内酯交联聚合物(北京华美互利生物化工生产)、ipdi三聚体/聚乙二醇单甲醚(山东摩尔化工有限公司生产,产品名称为:异氰酸酯固化剂d41)和氨基磺酸盐改性hdi三聚体(广州增茂化工科技有限公司生产,型号:zs-2606)中的至少一种。
19.在一些实施例中,多元醇增塑剂包括丙三醇、季戊四醇和甘露醇中的至少一种。
20.在一些实施例中,聚乙烯醇包括聚乙烯醇1788、聚乙烯醇1792和聚乙烯醇1799中的至少一种。
21.在上述实施方式中,硅氧烷交联剂、水性封闭型异氰酸酯交联剂以及多元醇增塑剂均含有较多羟基,不仅提高胶黏性,而且易于用水清洗。
22.在一些实施例中,涂层组合物的最大热分解速率温度为300℃~400℃,该温度高于pvd工艺的温度,即涂层能在pvd工艺的高温环境下保持稳定。
23.本发明还公开了一种pvd镀腔内壁构件,包括镀腔内壁构件本体和形成于镀腔内壁构件本体上的涂层,涂层包括上述的涂层组合物。
24.在一些实施例中,涂层的厚度为100μm~500μm。
25.本发明还公开了上述pvd镀腔内壁构件的制备方法,包括以下步骤:
26.s1:将上述涂层组合物用溶剂分散,得到涂层浆料。
27.在本步骤中,在一些实施例中,溶剂的质量份数为90份~96份,涂层组合物的原料包括以下质量份数的组分:3份~10份的聚乙烯醇、0.5份~10份的交联剂和0.03份~0.1份的多元醇增塑剂。涂层浆料的浓度不易过大,否则导致涂层过厚,易脱落。
28.在一些实施例中,溶剂包括乙醇和/或水,乙醇可以是无水乙醇或乙醇溶液,乙醇溶液的质量浓度可以为60%、72%或90%等。
29.在本步骤中,可以先用溶剂溶解聚乙烯醇,形成聚乙烯醇溶液,以及用溶剂溶解交联剂,形成交联剂溶液,然后将聚乙烯醇溶液、交联剂溶液和增塑剂相混合,得到涂层浆料,便于各组分的充分分散。混合时,可以采用超声混合等方式提高混合均匀度。
30.s2:将涂层浆料形成于镀腔内壁构件本体的表面,使涂层浆料发生交联反应,固化后形成涂层。
31.当交联剂包括水性封闭型异氰酸酯交联剂时,使涂层浆料发生交联反应的温度大于水性封闭型异氰酸酯交联剂的解封温度,水性封闭型异氰酸酯交联剂解封与聚乙烯醇以及多元醇增塑剂发生交联反应。
32.当交联剂包括硅氧烷交联剂时,使涂层浆料发生交联反应的过程中还加入0.5份~10份质量份数的酸催化剂,酸催化剂能促进硅氧烷交联剂水解,形成羟基,促进硅氧烷交联剂和聚乙烯醇以及多元醇增塑剂发生交联反应。
33.进一步的,酸催化剂包括盐酸、乙酸、草酸和柠檬酸中的至少一种。
34.本发明还公开了一种上述pvd镀腔内壁构件的清洗方法,包括以下过程:
35.s1:对被杂质层污染后的pvd镀腔内壁构件进行水洗,水洗过程中,杂质层和涂层均被去除,得到清洗后的镀腔内壁构件本体。
36.在上述实施方式中,镀腔内壁构件本体表面的涂层易溶于水,在水中涂层易与镀腔内壁构件本体和杂质层分离,不仅镀腔内壁构件本体被清洗干净,而且杂质层可以被回收再利用。
37.可以将pvd镀腔内壁构件浸泡于水中进行清洗,也可以采用喷淋的方式清洗pvd镀腔内壁构件。
38.以下为具体实施例。
39.实施例1
40.涂层组合物包括以下质量份数的组分:
[0041][0042]
pvd镀腔内壁构件的制备方法包括以下步骤:
[0043]
1)用称量纸称量10g聚乙烯醇1788,溶解于90g去离子水中,95℃恒温搅拌1h,得到分散均匀的聚乙烯醇溶液。
[0044]
2)依次在烧杯中加入0.27g乙醇溶液、0.5g乙酸、10g teos,在室温下磁力搅拌2h得到硅酸四乙酯溶液。
[0045]
3)将上述步骤1)制得的聚乙烯醇溶液加入步骤2)制得的硅酸四乙酯溶液中,超声分散10分钟,使两者分散均匀,得到涂层浆料。
[0046]
4)将步骤3)制得的涂层浆料均匀喷射在镀腔内壁构件(铝片)表面,厚度为100μm。
[0047]
5)喷射完成后将镀腔内壁构件置于通风良好处室温干燥固化(干燥过程也是在逐渐完成交联过程),即在镀腔内壁构件表面形成涂层。
[0048]
实施例2~6
[0049]
实施例2~6的涂层组合物的组分如表1所示,制备步骤与实施例1相同。
[0050]
实施例7
[0051]
涂层组合物包括以下质量份数的组分:
[0052][0053][0054]
pvd镀腔内壁构件的制备方法包括以下步骤:
[0055]
1)用称量纸称量10g聚乙烯醇1788,溶解于90g去离子水中,95℃恒温搅拌1h,得到分散均匀的聚乙烯醇溶液。
[0056]
2)向步骤1)制得的聚乙烯醇溶液中加入10g hdi/三羟甲基己基内酯交联聚合物和0.1g丙三醇,超声分散10分钟,得到涂层浆料。
[0057]
4)将步骤3)制得的涂层浆料均匀喷射在镀腔内壁构件表面,厚度为100μm。
[0058]
5)喷射完成后将镀腔内壁构件置于85℃的鼓风烘箱中干燥30分钟,之后将烘箱温度升至120℃保持至少15分钟,使hdi/三羟甲基己基内酯交联聚合物发生交联,即在镀腔内壁构件表面形成涂层。
[0059]
实施例8~12
[0060]
实施例8~12的涂层组合物的组分如表1所示,制备步骤与实施例1相同。
[0061]
对比例1
[0062]
对比例1与实施例1的区别在于:涂层组合物中不包括丙三醇,其余都相同。
[0063]
对比例2
[0064]
对比例2与实施例1的区别在于:涂层组合物中不包括交联剂teos,其余都相同。
[0065]
对比例3
[0066]
对比例3与实施例7的区别在于:涂层组合物中不包括丙三醇,其余都相同。
[0067]
对比例4
[0068]
对比例4与实施例7的区别在于:涂层组合物中不包括交联剂hdi/三羟甲基己基内酯,其余都相同。
[0069]
上述各实施例和对比例的参数如表1所示,其中铝片是指镀腔内壁构件,铝片为磨砂时,是对光滑铝片进行磨砂处理,提高铝片和涂层的结合力。
[0070]
表1:各实施例和对比例的参数
[0071][0072]
对上述实施例1~12和对比例1~4形成的涂层进行性能测试。
[0073]
对上述实施例1~12和对比例1~4形成的涂层进行附着力测试,涂层与镀腔内壁构件能否良好结合是评价涂层性能的关键因素。采用附着力测试仪进行测试,附着力测试仪又名百格刀,本次测试使用的百格刀型号为qfh-hg600,是根据iso 2409-1992标准设计制造的。该仪器以一定规格的工具,将涂层做格阵图形切割并穿透,划格完成的图形按六级分类,评定涂层从底材分离的附着效果。漆膜划格法的标准有:gb/t 9286-1998《色漆和清漆漆膜的划格试验》、astm d 3359-2002《胶带法测定附着力》、iso 2409-2007《色漆和清漆—划格试验》。测试过程为:首先将涂层的镀腔内壁构件放在平直的台面上,用百格刀垂直于涂层表面均匀用力,平稳的划出至少6条平行切割线,再与在先切割线成90
°
垂直交叉划出平行6条线,形成网格图形,这里需要注意的是所有的切口均需要穿透到底材的表面,然后对网格中的线条进行清洁清理之后,在网格的中央施加胶带,并确保其与涂层完全接触。将胶带提起与涂层形成约60
°
角,连续平稳的将胶带撤离,然后观察网格中涂层的脱落情况。评级方法参考表2。
[0074]
表2:涂层划格试验评级方法
[0075][0076]
对上述实施例1~12和对比例1~4形成的涂层进行tg测试,测试涂层质量随温度的变化关系,得到质量与温度的tg曲线,tg曲线上斜率最大的点对应的温度即为最大热分解速率温度,该温度为涂层发生热分解的温度,结果参见表3。
[0077]
将上述实施例1~12和对比例1~4形成的涂层进行120℃下的持续烘烤0.5h,以模拟pvd工艺的高温环境,观察涂层是否翘边、开裂和脱落,结果参见表3。
[0078]
用去离子水喷洗上述实施例1~12和对比例1~4形成的涂层,对清洗后的镀腔内壁构件的清洁度进行评价,无涂层残留为合格,有涂层残留为不合格,结果参见表3。
[0079]
表3:各实施例和对比例制得的涂层的性能指标
[0080][0081]
从表3可以看到:1)本发明的涂层的附着力等级最高,说明本发明的涂层可以和镀腔内壁构件以及杂质层具有较强的结合力;2)本发明的涂层的最大热分解速率温度均大于300℃,能够满足pvd镀腔内使用的要求;3)本发明的涂层在高温持续烘烤下,均未产生翘边、开裂和脱落的情况,说明具有耐高温稳定性;4)本发明的涂层用水清洗后均无涂层残留,说明涂层易于水洗。
[0082]
以上所述实施例仅表达了本发明的几种实施方式,其描述较为具体和详细,但并不能因此而理解为对申请专利范围的限制。应当指出的是,对于本领域的普通技术人员来说,在不脱离本发明构思的前提下,还可以做出若干变形和改进,这些都属于本发明的保护范围。因此,本发明专利的保护范围应以所附权利要求为准。