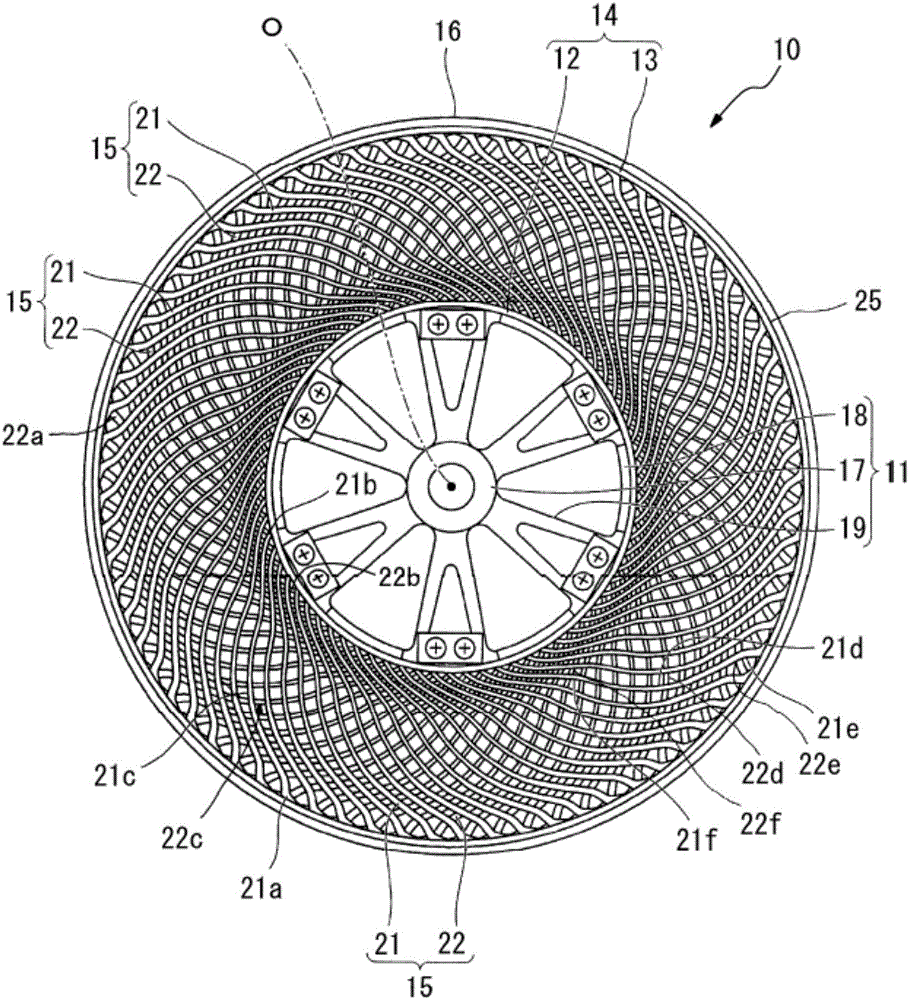
本发明涉及可以在不填充有加压空气的情况下使用的非充气轮胎。
背景技术:
:对于需要在使用时填充有加压空气且通常保持在恒定的内部气压下的充气轮胎,传统上已经采取各种对策来防止导致其中内部气压不能保持恒定的这样的状态的刺破。然而,充气轮胎的结构使刺破不可避免。鉴于此,近年来已经提出“非空气压力轮胎”作为不需要填充有加压空气的轮胎。例如,“非空气压力轮胎”包括:支承结构体,其用于支承来自车辆的负荷;带束层(可省略的),其设置在支承结构体的外周侧;和胎面层,其设置在带束层的外侧(外周侧),其中作为一个实例,支承结构体可以使用树脂一体成形(参见专利文献(PTL)1)。在该“非空气压力轮胎”中,带束层通过层叠覆盖有橡胶的钢丝帘线等的层来形成,并且接合至由树脂制成的支承结构体的外周侧。引用列表专利文献PTL1:JP2011-219009A技术实现要素:发明要解决的问题已知的是,安装至车轴且传送驱动力至其上的支承结构体与在传统的“非空气压力轮胎”中用作接地面的胎面层之间的接合状态显著影响轮胎的行驶功能。也已知的是,根据形成支承结构体的树脂构件的种类,要接合支承结构体的形成胎面层(或带束层)的橡胶构件的粘接性显著变化。因此,特别地,在支承结构体由不具有良好的与橡胶构件的粘接性的类型的树脂构件组成的情况下,非常困难的是改善树脂构件与橡胶构件之间的粘接性同时确保轮胎的必要的行驶功能。由此会有帮助的是提供改善了形成安装至车轴的结构体的树脂构件与用作接地面的胎面构件之间的粘接性同时确保必要的行驶功能的非充气轮胎。用于解决问题的方案为了实现该目的,本发明的非充气轮胎包括:安装体,其安装至车轴;环构件,其包括外装于所述安装体的内筒体和从轮胎径向的外侧围绕所述内筒体的外筒体;多个连接构件,其在所述内筒体与所述外筒体之间沿轮胎周向配置且使所述内筒体和所述外筒体彼此连接;和胎面构件,其由硫化橡胶制成且设置在所述环构件的所述外筒体的轮胎径向的外侧,其中所述外筒体的至少一部分和所述多个连接构件由合成树脂材料一体形成,并且包含氰基丙烯酸酯系粘接剂的粘接层设置在所述胎面构件与所述环构件的所述外筒体之间,所述外筒体在其表面具有氨基。在此结构的情况下,可以改善形成安装至车轴的结构体的树脂构件与胎面构件之间的粘接性同时确保必要的行驶功能。优选地,在本发明的非充气轮胎中,所述合成树脂材料包含以下物质之一或两种以上的混合物:尼龙12、尼龙66、聚对苯二甲酸丁二醇酯(PBT)、聚苯硫醚(PPS)、热塑性聚酰胺系弹性体(TPAE)、丙烯腈-丁二烯-苯乙烯共聚物、聚醚醚酮(PEEK)、间规聚苯乙烯(SPS)、聚缩醛(POM)、聚芳酯(PAR)、聚醚硫烷(PES)、聚碳酸酯(PC)、聚酰胺(PA)、聚砜(PSF)的聚合物或共聚物、和烯属聚合物。在此结构的情况下,可以得到非充气轮胎特性(刚性和韧性)。优选地,在本发明的非充气轮胎中,所述合成树脂材料包含聚苯硫醚(PPS)、聚碳酸酯(PC)和聚酰胺(PA)之一或两种以上的混合物。在此结构的情况下,可以进一步提高耐冲击性。优选地,在本发明的非充气轮胎中,所述外筒体的与所述胎面构件的粘接部分的表面粗糙度(Ra)是0.02μm至0.5μm。在此结构的情况下,粘接性能可以通过锚固效果进一步改善。在本发明中,“表面粗糙度(Ra)”是基于JISB0601(1994)的算术平均表面粗糙度(Ra)(单位:μm)。优选地,在本发明的非充气轮胎中,所述外筒体的与所述胎面构件的粘接部分的最大高度(Ry)是3μm以下。在此结构的情况下,粘接剂更清洁地附着至合成树脂和硫化橡胶的表面。在本发明中,“最大高度(Ry)”是基于JISB0601(1994)的最大高度(Ry)(单位:μm)。优选地,在本发明的非充气轮胎中,根据JISK6850即粘接剂-刚性被粘物的拉伸剪切粘接强度的试验方法(Adhesives-Determinationoftensilelap-shearstrengthofrigid-to-rigidbondedassemblies)而测量的所述粘接层的粘接强度在25℃的温度下为1.0MPa以上。在此结构的情况下,可以更成功地维持粘接强度。优选地,在本发明的非充气轮胎中,根据JISK6850即粘接剂-刚性被粘物的拉伸剪切粘接强度的试验方法而测量的所述粘接层的粘接强度在80℃的温度下为0.3MPa以上。在此结构的情况下,可以更成功地维持轮胎行驶期间高温下的粘接强度。发明的效果由此可以提供改善了形成安装至车轴的结构体的树脂构件与胎面构件之间的粘接性同时确保必要的行驶功能的非充气轮胎。附图说明在附图中:图1是表明从轮胎侧面看到的根据一个公开的实施方案的非充气轮胎的结构的说明图;图2是图1中轮胎的一部分的放大图;图3A是根据其它实例的由连接构件连接的内筒体和外筒体的正视图;图3B是由该连接构件连接的内筒体和外筒体的透视图;图4是图1中在环构件与胎面构件之间设置的粘接层的部分放大图。具体实施方式以下参考附图描述了一个公开的实施方案。图1是表明从轮胎侧面看到的根据一个公开的实施方案的非充气轮胎的结构的说明图。图2是图1中轮胎的一部分的放大图。在图2中,出于清楚的目的,下述的多个第一弹性连接板21和多个第二弹性连接板22中,仅一个第一弹性连接板21和一个第二弹性连接板22以实线强调而表明。如图1和2中表明,本实施方案中的非充气轮胎10包括:安装体11,其安装至车轴(未示出);环构件14,其包括外装于安装体11的内筒体12和从轮胎径向的外侧围绕内筒体12的外筒体13;多个连接构件15,其在内筒体12与外筒体13之间沿轮胎周向配置且使内外筒体12和13彼此连接;和胎面构件16,其由硫化橡胶制成且一体覆盖环构件14的外周。安装体11、内筒体12、外筒体13和胎面构件16具有相同的轴作为共用轴线(commonaxis)或它们在轮胎宽度方向上的中央部彼此一致。将该共用轴线称作“轴线O”,将与轴线O垂直的方向称作“轮胎径向”,并且将环绕轴线O的方向称作“轮胎周向”。安装体11包括:安装筒部17,其中安装车轴的前端部;外环部18,其从轮胎径向的外侧围绕安装筒部17;和多个肋19,其连接安装筒部17和外环部18(参见图1和2)。安装筒部17、外环部18和肋19由如铝合金等金属材料一体形成。安装筒部17和外环部18各自形成为圆筒状并关于轴线O同轴地配设。多个肋19在周向上等间隔地配置。各连接构件15包括:使在环构件14中的内筒体12和外筒体13彼此连接的第一弹性连接板21和第二弹性连接板22。多个第一弹性连接板21沿轮胎周向配置在轮胎宽度方向上的一个位置处,并且多个第二弹性连接板22沿轮胎周向配置在与上述轮胎宽度方向上的一个位置不同的轮胎宽度方向上的另一个位置处。例如,设置总计60个第一弹性连接板21和第二弹性连接板22。换言之,多个第一弹性连接板21沿轮胎周向配置在轮胎宽度方向上的相同位置处,并且多个第二弹性连接板22沿轮胎周向配置在轮胎宽度方向上与第一弹性连接板21分开的、在轮胎宽度方向上的相同位置处。多个连接构件15在环构件14中的内筒体12与外筒体13之间相对于轴线O轴对称。全部连接构件15具有相同的形状和相同的尺寸。各连接构件15的宽度小于外筒体13在轮胎宽度方向上的宽度。在轮胎周向上相邻的第一弹性连接板21彼此不接触,并且在轮胎周向上相邻的第二弹性连接板22彼此不接触。在轮胎宽度方向上相邻的第一弹性连接板21和第二弹性连接板22彼此不接触。第一弹性连接板21和第二弹性连接板22具有相同的宽度。第一弹性连接板21和第二弹性连接板22也具有相同的厚度。第一弹性连接板21的与外筒体13连接的一端部21a设置在与第一弹性连接板21的连接至内筒体12的另一端部21b相比更靠近轮胎周向上的一侧,并且第二弹性连接板22的与外筒体13连接的一端部22a设置在与第二弹性连接板22的连接至内筒体12的另一端部22b相比更靠近轮胎周向上的另一侧。在外筒体13的内周面上,第一弹性连接板21和第二弹性连接板22的各端部21a和22a在轮胎宽度方向上的位置不同并且连接至在轮胎周向上的相同位置。在表明的实例中,在从轮胎宽度方向看到的轮胎10的轮胎侧视图中,沿连接板21的延伸方向,在一端部21a与另一端部21b之间的第一弹性连接板21的中间部分21c中,形成在轮胎周向上弯曲的多个弯曲部21d至21f。同样地,在从轮胎宽度方向看到的轮胎10的轮胎侧视图中,沿连接板22的延伸方向,在一端部22a与另一端部22b之间的第二弹性连接板22的中间部分22c中,形成在轮胎周向上弯曲的多个弯曲部22d至22f。在连接板21中的多个弯曲部21d至21f中,在延伸方向上相邻的弯曲部以彼此相反的方向弯曲。在连接板22中的多个弯曲部22d至22f中,在延伸方向上相邻的弯曲部以彼此相反的方向弯曲。在第一弹性连接板21中形成的多个弯曲部21d至21f由以下组成:第一弯曲部21d,其弯曲成朝向轮胎周向上的另一侧突出;第二弯曲部21e,其设置在第一弯曲部21d与一端部21a之间且弯曲成朝向轮胎周向上的一侧突出;和第三弯曲部21f,其设置在第一弯曲部21d与另一端部21b之间且弯曲成朝向轮胎周向上的一侧突出。在第二弹性连接板22中形成的多个弯曲部22d至22f由以下组成:第一弯曲部22d,其弯曲成朝向轮胎周向上的一侧突出;第二弯曲部22e,其设置在第一弯曲部22d与一端部22a之间且弯曲成朝向轮胎周向上的另一侧突出;和第三弯曲部22f,其设置在第一弯曲部22d与另一端部22b之间且弯曲成朝向轮胎周向上的另一侧突出。在表明的实例中,在轮胎侧视图中,第一弯曲部21d和22d分别与第二弯曲部21e和22e以及第三弯曲部21f和22f相比曲率半径较大。第一弯曲部21d和22d分别位于在第一弹性连接板21和第二弹性连接板22的延伸方向上的中央部。两种弹性连接板21和22具有相同的长度。如图2中表明,在轮胎侧视图中,在内筒体12的外周面上,弹性连接板21和22的另一端部21b和22b分别连接至从在轮胎径向上面对一端部21a和22a的位置起绕着轴线O向轮胎周向上的另一侧和一侧离开相同角度(例如,20°以上且135°以下)的位置处。在第一弹性连接板21和第二弹性连接板22中,第一弯曲部21d和22d沿轮胎周向以彼此反向的方向突出并且具有相同的尺寸,第二弯曲部21e和22e沿轮胎周向以彼此反向的方向突出并且具有相同的尺寸,并且第三弯曲部21f和22f沿轮胎周向以彼此反向的方向突出并且具有相同的尺寸。因而,如从图2中以实线强调而表明的一对第一弹性连接板21和第二弹性连接板22可见的,在轮胎侧视图中的各连接构件15的形状相对于沿轮胎径向延伸且经过连接板21和22的各一端部21a和22a的假想线L呈线对称。在各连接板21和22中,从在延伸方向上的中央部至一端部21a或22a的一端侧部分与从该中央部至另一端部21b或22b的另一端侧部分相比较厚。这提高了在各第一弹性连接板21和第二弹性连接板22中易于在重负荷下的一端侧部分的强度,同时防止连接构件15的重量增大并且确保连接构件15的柔软性。这里,一端侧部分和另一端侧部分在没有任何水平差的情况下平滑地连接在一起。环构件14可以例如在轮胎宽度方向上的中央部处分割为在轮胎宽度方向上的一侧的一侧分割环构件和在轮胎宽度方向上的另一侧的另一侧分割环构件。在此情况下,一侧分割环构件可以与第一弹性连接板21一体形成,并且另一侧分割环构件与第二弹性连接板22一体形成。一侧分割环构件和第一弹性连接板21可以通过注射成形一体形成,并且另一侧分割环构件和第二弹性连接板22通过注射成形一体形成。环构件14以内筒体12安装至安装体11上的状态固定至安装体11。在本实施方案中,由内筒体12和外筒体13组成的环构件14和多个连接构件15全部由合成树脂材料一体形成,并且包含氰基丙烯酸酯系粘接剂的粘接层25设置在胎面构件16与环构件14的外筒体13之间。合成树脂的弯曲弹性模量优选为1.5GPa至5GPa。例如,合成树脂材料包含以下物质之一或两种以上的混合物:尼龙12、尼龙66、聚对苯二甲酸丁二醇酯(PBT)、聚苯硫醚(PPS)、热塑性聚酰胺系弹性体(TPAE)、丙烯腈-丁二烯-苯乙烯共聚物(ABS)、聚醚醚酮(PEEK)、间规聚苯乙烯(SPS)、聚缩醛(POM)、聚芳酯(PAR)、聚醚硫烷(PES)、聚碳酸酯(PC)、聚酰胺(PA)、聚砜(PSF)的聚合物或共聚物、和烯属聚合物。其中,由于良好的耐冲击性,特别期望聚苯硫醚(PPS)、聚碳酸酯(PC)和聚酰胺(PA)之一或两种以上的混合物。合成树脂材料可以是包含一种以上的前述树脂材料和一种以上的除了上述那些以外的弹性体的混合物,并且可以进一步包含如抗氧化剂、增塑剂、填料和颜料等添加剂。在本实施方案的非充气轮胎10中,胎面构件16是圆筒状的,并且完全地覆盖环构件14的外筒体13的整个外周面。为了耐磨耗性等,胎面构件16由通过将包含例如天然橡胶的橡胶组合物硫化获得的硫化橡胶制成。以下描述使内筒体12和外筒体13连接的连接构件15的其它实例。图3A和3B分别是在其它实例中由连接构件连接的内筒体和外筒体的正视图和透射图。如图3A和3B中表明,不像包括第一弹性连接板21和第二弹性连接板22的连接构件15,各连接构件23仅包括第一弹性连接板21。各自构成连接构件23的多个第一弹性连接板21在内筒体12与外筒体13之间沿轮胎周向配置,并且使内外筒体12和13彼此连接。其它结构和功能与连接构件15的那些相同。图4是图1中在环构件14与胎面构件16之间设置的粘接层25的部分放大图。在本实施方案中,将环构件14的外筒体13(特别是至少环构件14的外筒体13面对胎面构件16的外周面)使用胺化合物来预处理。如图4中表明,粘接层25设置在如上所述预处理的环构件14的外筒体13与胎面构件16之间从而调节外筒体13与胎面构件16之间的接合,并且包含氰基丙烯酸酯系粘接剂。因而,在本实施方案中,包含氰基丙烯酸酯系粘接剂和胺化合物的粘接层25设置在使用胺化合物预处理的环构件14的外筒体13与胎面构件16之间。这确保了使用前述合成树脂材料与多个连接构件15一体形成的环构件14与使用硫化橡胶形成的胎面构件16之间的接合。氰基丙烯酸酯系粘接剂的实例包括ThreeBondCo.,Ltd.的(ThreeBond是日本、其它国家或二者中的注册商标)1757以及ToagoseiCo.,Ltd.的Aron(AronAlpha是日本、其它国家或二者中的注册商标)221。胺化合物的实例包括聚酰胺和四甲基己烷二胺。换言之,粘接性可以通过将包含氰基丙烯酸酯系粘接剂的粘接层25配置在环构件14与胎面构件16之间来改善。此外,通过将合成树脂材料使用具有高的耐热性的胺化合物来表面处理作为通过氰基丙烯酸酯系粘接剂的粘接作用的预处理,粘接部可以更成功地在轮胎行驶温度下维持高的粘接强度。预处理由此进一步改善氰基丙烯酸酯系粘接剂对胎面材料的粘接性。具体地,将环构件14和胎面构件16通过以下方法来粘接。以下列出表面处理方法的实例。在合成树脂材料是聚苯硫醚的情况下,四甲基己烷二胺溶解在正己烷中从而获得作为处理剂的约2%的溶液。将要进行粘接的部位刷有该溶液,然后干燥溶剂以去除。之后,在要进行粘接的部位和胎面材料之间注入氰基丙烯酸酯系粘接剂,将粘接剂放置固化。粘接剂固化所需要的时间依赖于环境湿度和温度,但几分钟是充分的。特别是在聚苯硫醚(PPS)用作合成树脂材料的情况下,难以改善的聚苯硫醚(PPS)与硫化橡胶的胎面材料之间的粘接性可以经由包含氰基丙烯酸酯系粘接剂和含氨基的化合物的粘接层25而显著改善。这尤其确保了环构件14与胎面构件16之间的接合同时确实地维持轮胎的必要的行驶功能。根据粘接剂-刚性被粘物的拉伸剪切粘接强度的试验方法(JISK6850)而测量的粘接层25的粘接强度在25℃的温度下优选为1.0MPa以上。因而,可以更成功地确保和维持在25℃的温度下充分的粘接强度。根据粘接剂-刚性被粘物的拉伸剪切粘接强度的试验方法(JISK6850)而测量的粘接层25的粘接强度在80℃的温度下优选为0.3MPa以上,并且更优选0.6MPa以上。因而,可以更成功地确保和维持在80℃的温度下,即在轮胎行驶期间的高温下的充分的粘接强度。特别优选的是满足粘接层25的粘接强度的全部前述两个条件。外筒体13的与胎面构件16的粘接部分,即,外筒体13面对胎面构件16的外周面的算术平均粗糙度(Ra)优选为0.02μm以上,并且更优选0.04μm以上,并且优选0.5μm以下,并且更优选0.45μm以下。最大高度(Ry)优选为3μm以下,并且更优选2.3μm以下。实施例实验地生产多种类型的根据本发明的非充气轮胎作为实施例(实施例1至12),并且与比较例(比较例1至4)的非充气轮胎比较。这些实施例和比较例的非充气轮胎各自具有155/65R13的轮胎尺寸,并且具有图1和2中表明的结构。包含在粘接层中的粘接剂、用于预处理环构件的外筒体的胺化合物、外筒体的外表面的算术平均粗糙度和最大高度、以及粘接层的粘接强度在表1至6中示出。这些实验轮胎在以下试验条件下进行拉伸耐久试验并且评价。(粘接强度的测量)将各类型的树脂材料注射成形为哑铃(dumbbell)(JISK6251,哑铃状No.1)。将获得的哑铃在长度方向在正中处切割为两半,并且用于粘接试验。将硫化橡胶夹在两个切割的哑铃之间,粘接哑铃的表面并且测量粘接强度。作为粘接预处理,使用刷子等施涂预处理液,然后干燥溶剂以去除。之后,使用刷子等施涂粘接剂,将硫化橡胶夹持,并且在将结构体使用夹子等保持以防止错位的同时放置固化。固化时间根据使用的粘接剂的推荐条件来设定。粘接面积是10mm×10mm,并且橡胶厚度为2mm。粘接样品的哑铃部通过卡盘来保持并且在拉伸速度为10mm/min的情况下以相反方向牵引,并且测量破裂时的力。测量的力除以粘接面积,从而测定粘接强度。使用25℃和80℃的两个试验环境温度。(粘接耐久试验)对在前述测量中80℃下的粘接强度为0.2MPa以上的各样品进行粘接耐久试验。将通过上述方法生产的样品使用动态疲劳试验机(Servopulser,ShimadzuCorporation制)在60℃、10Hz的频率和±5kgf的力下进行粘接耐久试验(拉伸耐久试验),并且测量直至样品破裂时的循环数。将实验数据转换为在30000次循环设定为100的情况下的指数。最大循环数是100000。[表1]表1环构件:PPS[表2]表2环构件:PPS[表3]表3环构件:PPS[表4]表4环构件:PPS[表5]表5环构件:聚碳酸酯[表6]表6环构件:聚酰胺实施例11实施例12粘接剂AronAlpha221ThreeBond1757预处理不实施不实施算术平均粗糙度Ra(μm)0.210.22最大高度Ry(μm)1.41.5粘接强度(25℃)MPa1.41.45粘接强度(80℃)MPa10.9拉伸耐久试验(指数)无破裂无破裂如表1至6中示出,非充气轮胎的各实施例的粘接耐久试验(拉伸耐久试验)产生以下结果。在使用聚苯硫醚(PPS)或聚碳酸酯(PC)作为环构件,设置包含胺化合物的粘接层,并且使用胺化合物进行预处理的情况下,能够获得102以上(102至155)的指数(参见表1至5)。在使用聚酰胺(PA)作为环构件并且设置包含胺化合物的粘接层的情况下,即使没有预处理也没有发生破裂(参见表6)。由此可以提供改善了形成安装至车轴的结构体的树脂构件与胎面构件之间的粘接性同时确保必要的行驶功能的非充气轮胎。附图标记说明10非充气轮胎11安装体12内筒体13外筒体14环构件15连接构件16胎面构件17安装筒部18外环部19肋21第一弹性连接板21a一端部21b另一端部21c,22c中间部分21d至21f弯曲部22第二弹性连接板22a一端部22b另一端部22d至22f弯曲部25粘接层当前第1页1 2 3