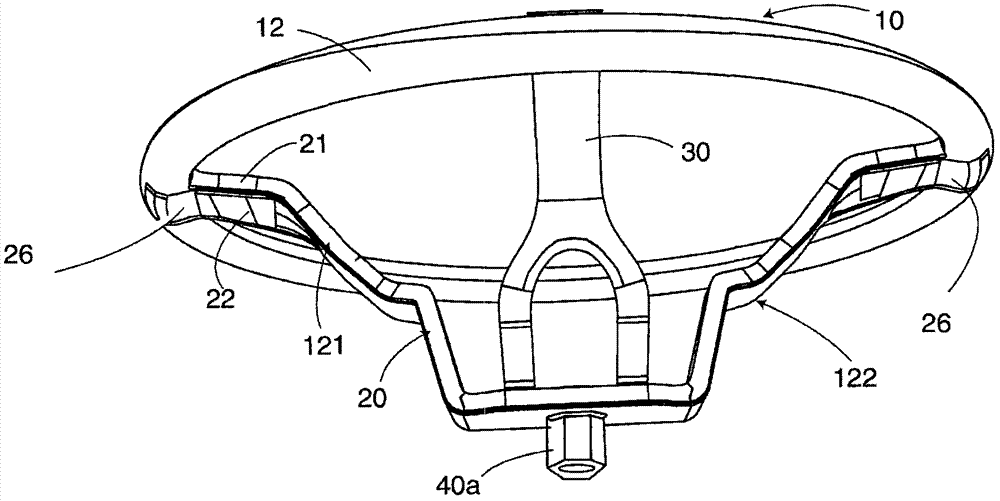
本发明总地涉及方向盘和方向盘支架,并具体地涉及一种带有重量轻、成本低的改进的方向盘支架的方向盘。
背景技术:方向盘组件是一种相当复杂的、要求特别的稳定性和功能性的结构。方向盘的位于下方的主要机械结构通常被称作骨架芯部(skeletoncore)或支架。所述方向盘骨架或支架具有如下主要组件:环形轮缘,多个轮辐和一个中心轮毂。中心轮毂具有装到车辆转向轴上的开口。多年来,已经提出了各种用于制造支架的方法。一些方法包括用轻质的合金,如镁或铝合金来浇铸方向盘。这些支架可以被制造得耐用并且通常质量较轻。主要的缺点为该结构材料成本较高。大多数情况下,支架包封于塑料合成材料内,并且上面可覆盖有另一种材料,如皮革。现有技术中,为降低成本一些方向盘(通常为手轮)由钢板金属预制件制成。在US1,411,239中,两个冲压金属板接合以形成间隔开的、带有用于接纳轮辐的插孔的中心区域;在组装时,整个或大部分结构被包封于赛璐珞中,其为一种当时常用的塑料材料。后来在1993年美国专利1,915,769授权,其中,制成一件式金属板的方向盘,并且该方向盘具有连续的轮缘、轮毂以及连接轮缘和轮毂的轮辐。轮缘和轮辐都是管状的。该方向盘是轻质结构并且据说其坚固,构造简单,且制造成本低。再后来,US6,622,590公开了一种由两个相对的壳体制成的、用于方向盘的芯杆(corebar)。每个壳体都有凸台部分和相互面对、但不联接的第一半壳和第二半壳。这些半壳形成了轮缘和轮辐部分的上半部和下半部,且半壳之间限定出轮辐中空部分。由于包含了轮缘,现有技术装置在形成方向盘时需要使用较大板材。这从本质上使得在压制出所需形状之前冲压板材时近乎50%的板材完全被丢弃。其次,这些设计在附连位置明显具有缺陷,其从结构上有效地削弱了方向盘,从而产生频率问题,扭转弱化和弯曲刚度不足。尽管如此,使用低成本钢材的理念作为目前使用的更高成本合金的替代方式仍然十分有吸引力。本发明的方向盘支架实现的这些和其它目标益处在下文中皆有描述。
技术实现要素:方向盘支架包括中心轮毂,轮缘和轮辐组件(或依据需要从中心区域延伸的各个轮辐)。轮辐组件从轮缘的第一位置向内延伸到中心轮毂,并向外延伸到轮缘的通常与第一位置相对的第二位置。轮辐组件是两件式焊接结构,该结构具有焊接在一起以形成中空的管状结构的上轮辐构件和下轮辐构件,优选地在从横截面看时其呈大致矩形形状。在另一个实施例中,上下轮辐构件或下轮辐构件之一在中央轮毂和轮缘之间部分地延伸。在一个实施例中,轮辐组件具有沿上轮辐构件和下轮辐构件的前缘和后缘延伸的、面对的焊接凸缘。上轮辐构件的焊接凸缘与下轮辐构件的焊接凸缘对准并且与其焊接。轮辐组件的中空的管状结构具有在焊接好的凸缘的前端和后端之间延伸的高度尺寸和U形形状以控制支架刚度,其中凸缘之间测量的高度与宽度之比可以改变,以控制轮辐组件或特定的轮辐构件的扭转刚度,同时控制轮辐组件或特定的轮辐构件的弯曲刚度。轮辐组件具有在第一位置和与之相对的第二位置处刚性地固定到轮缘的远端。轮辐组件可以在轮缘所在的并诸如通过焊接或其它方式刚性连结的每个远端处弯曲。轮辐组件具有位于轮辐组件中心区域内的中心轮毂孔,该中心轮毂孔延伸通过上轮辐构件和下轮辐构件。中心轮毂延伸通过该轮毂孔。中心轮毂具有多个焊接凸缘,从而在其顶部形成花瓣状结构,每个焊接凸缘被焊接到轮辐组件的部分上。本发明的中心轮毂与现有技术中目前使用的那些在功能上等同。在本发明中,轮毂由金属板组成,但是中心轮毂可以由锻造的或机加工的坯件制成。在一种型式中,中空的中心轮毂具有平行的圆柱形侧壁,其内表面上具有花键以便于与转向柱的端部匹配。在另一个实施例中,中心轮毂侧壁的下部分向外渐缩,以便于与另一类型的转向柱设计匹配。在该第二实施例中,通常不使用花键。在一个优选实施例中,轮辐组件形成为中空的管状结构,其具有箱状的矩形横截面,其中上轮辐构件是成形为大致U形横截面的冲压金属板,该U形横截面具有向外延伸形成一组相对的凸缘的侧壁。U形横截面具有在侧壁之间延伸的顶部。下轮辐构件是冲压板材,最简单的形式是具有较薄、平坦的横截面形状,但是下板可以包括各种的凹槽和脊部,以使下轮辐构件的刚度更大或更小。方向盘支架可以进一步具有一个或多个自轮缘向中心轮毂或轮辐组件中心延伸的中间轮辐。中间轮辐典型地对称布置在轮辐组件的两个远端之间。中间轮辐可由成形为合适形状的平坦冲压金属板制成。中间轮辐可以与其它轮辐构件一样具有中空的横截面构造。在所示实施例中,单个中间轮辐具有一对内部支脚,一个支脚附连于轮辐组件的相对于中心孔的每一侧。在一个实施例中,轮缘可由实心棒料制成。替代地,轮缘可由弯成环形的连续环的中空管制成,其中轮缘支承于轮辐组件上。轮辐组件连接到轮缘的连接点可以变化。在许多示出的实施例中,连接点位于约3-4点钟位置和8-9点钟位置范围内。如果轮缘成形为管,则轮缘优选地由管壁厚度在约0.5至约2mm范围内的钢管制成。优选厚度为0.75mm。上轮辐构件和下轮辐构件优选分别由具有约0.5至约2mm的相同范围内的厚度的金属板制成。优选的厚度约为1mm,且当焊接时焊接凸缘处的结合厚度优选为2mm。中间轮辐优选地由厚度在相同范围内的单个钢板制成。上轮辐构件冲压而成,其中侧壁在凸缘上方延伸一定高度(h)和一定宽度(w)。高度(h)和宽度(w)共同控制方向盘沿特定轮辐的整个长度和轮辐的相邻区域之间的扭转刚度和弯曲刚度。将看出,宽度(w)可以沿特定轮辐的径向尺寸变化,这使轮辐的相邻部分的扭转系数和弯曲系数能够变化。轮缘的刚度可通过在其内包含压平部分和切去部分来改变,所述压平部分和切去部分起到控制轮缘挠曲的位置和挠曲程度的应力提升件的作用。在其它的实施例中,轮辐构件和/或轮缘由多于一种材料制成。附图说明借助示例并结合附图对本发明进行描述,其中:图1是本发明的优选实施例的方向盘支架的分解立体图。图2是依据本发明的优选实施例、从方向盘支架的底部向上朝方向盘支架组件的轮缘看的立体图。图3是本发明的方向盘支架的俯视图。图4是沿本发明的图3的剖线A-A剖取的、示出为焊接到轮毂上的、方向盘组件上轮辐的剖视图。图4a是图4所示的本发明的另一个实施例的剖视图。图5是轮辐组件沿图3的剖线A-A剖取的剖视图,其示出了焊接到轮毂的上轮辐和焊接到轮毂和上轮辐凸缘上的下轮辐。图5a是图5所示的本发明的另一个实施例的剖视图。图5b示出上轮辐顶部和与该顶部相邻的焊接区域的相对尺寸。图5c示出机械连结的上轮辐和下轮辐构件。图5d示出本发明的另一个实施例。图6示出剖过所述支架的一部分的径向剖视图。图6a和6b示出本发明的另一个变型。图7,7a和7b示出方向盘轮缘的变型。图8,8a,8b和8c示出本发明的轮缘和轮辐的构造的各种变型。图8d示出本发明的另一个实施例。图9是沿图3的剖线A-A的剖视图,其示出了锥形的轮毂。图10示出了本发明的另一个实施例。具体实施方式参考图1,2和3。图1示出了本发明的方向盘支架10的分解图。整个组件10(亦如图2和3所示)包括如下基本部件:轮缘12,轮辐组件20,和轮毂40,轮辐组件20包括上轮辐构件21,下轮辐构件22,中间轮辐30。为降低支架成本,为轮辐组件选用冲压钢作为材料。但是,型钢或冲压钢的组合、铝或镁或其合金可以单独或组合地来使用。图1示出了本发明使用的两种类型的中心轮毂40和40a。第一中心轮毂40呈圆锥形,而另一个轮毂40a具有圆柱形外壁。轮毂40和40a表示生产时所用的轮毂,尽管它们存在不同。每个轮毂40或40a包括延伸的凸缘41,其可以向下弯曲形成花瓣状结构。轮毂凸缘41可以在所述轮辐组件装配之前预弯曲,但也可以在中心轮毂40,40a插入上轮辐构件21之后完成弯曲。参考图2和3,本发明的方向盘支架10以最终的组装状态示出。从底部向上朝轮缘12看的立体图示出钢制轮毂40a通过中心孔24,24a插入轮辐组件20的中心区域20a。轮辐组件20通过将上轮辐构件21和下轮辐构件22焊接在一起而形成。当上轮辐和下轮辐构件装配到一起时,它们形成第一轮辐121和第二轮辐122。当这样构造时,轮辐组件20形成并且具有中空内部,即通过两个轮辐构件形成中空的结构,以控制轮辐组件20的扭转和弯曲系数。所述轮辐组件的很多部段设计成具有高扭转和弯曲系数,而其它部段具有低扭转和弯曲系数。该结构形成非常有效和刚性的构件,其令所使用的薄钢板有效地形成比在其它情况下形成的结构坚固得多的结构。参考图3,其示出支架的俯视图。轮辐组件20在方向盘支架10上大约3点和9点的时针位置经由中间轮辐30与轮缘12接触,中间轮辐30显示在正6点位置。该组件形成相当独特的方向盘支架结构10。在初装方向盘支架10时形成上轮辐构件21和下轮辐构件22的金属板部件。将轮辐构件21的远端指定为26,同时将轮辐构件22的远端指定为28。这些金属板材料可以是冲切的,然后使用模具来成形和冲压,以形成用于上轮辐构件21和下轮辐构件22的独特形状。通常,方向盘的中心区域20a和轮缘12位于不同的平面内。为了实现这种定向,轮辐或轮辐构件需要被弯曲。根据需要对每个轮辐构件进行切割和弯曲,该轮辐构件具有对应于形成于另一轮辐构件内的弯曲部的互补的弯曲部,因此在两构件连结时它们可以良好地装配在一起。通过在上轮辐构件21的每侧上提供焊接区域或凸缘27和在下轮辐构件每侧上提供焊接区域或凸缘29,可以加强装配,因而,当连结时,这些焊接凸缘27,29可以被焊接在一起,从而形成有效地加强整个轮辐组件20的中空的箱形结构。轮辐组件20的两侧的一个或两个焊接区域或凸缘可以用焊缝取代。在图4和4a中,上轮辐构件21和下轮辐构件22示出为通过圆柱形外壁附连于中心轮毂40a(见图1)。剖视图中示出了轮毂40a的一部分。上轮辐构件21具有中心孔24并显示为U形横截面,该U形横截面具有向下弯曲形成圆形凸缘23的平顶部21T,圆形凸缘23形成开口或孔24。轮毂40a向下滑动到直径稍大于轮毂40a的直径的开口或孔24。如图所示,上轮辐构件21在凸缘23处被焊接(参见标记23a)到轮毂40a,轮毂40a的轮毂凸缘41在图示位置被焊接(参见标记23a)到平顶部21T。轮毂40a具有形成于内表面上的花键连接部43。在图4a中,取消中心向下的凸缘23,轮毂40a和上轮辐构件31被点焊或线焊到一起(见焊接点23a)。参考图5,实施组装的第二步,即如图所示下轮辐构件22被安装到轮毂40a的周围,然后被焊接到轮毂40a和上轮辐构件。在图5中,下轮辐构件的围绕其开口24’的中心部形成有向下延伸并焊接到轮毂40a的圆形凸缘24a。一旦完成,上轮辐构件和下轮辐构件21和22的凸缘27,29对齐并焊接到一起,从而在轮辐组件20的每一侧形成紧密的焊缝。如图所示,这使得轮辐组件20和轮毂40的结构非常坚固并且轻质。考虑到许多焊接机的条件限制,凸缘27和29的焊接区域的宽度w4在大约5mm范围内。在实践中,焊接区域27,29的宽度w4越窄越好。如图3所示,可改变横跨上轮辐构件21的平顶部21T的宽度(w1,w2,w3等),以控制轮辐121或122的各部段的挠曲和弯曲特性。这些部段的扭转系数和弯曲系数可随着上轮辐构件的宽度(和高度)的变化而变化。在所示的本发明的实施例中,上轮辐构件的高度(h)通常保持不变,不过也是可以改变的。图5b举例示出了剖过B-B部分的剖视图。上轮辐构件20的侧面的下部分250与具有焊接凸缘27和29的实施例相比缩短。下轮辐构件的每个对应的侧边252弯曲到各下部分250上,以实现机械连结。在图5d中,上轮辐构件和下轮辐构件的侧面不包括焊接凸缘,并且通常相互覆盖。标记23a表征了接口焊或线焊。图6示出了沿剖线A-A的径向定向的局部剖视图。图6示出了轮毂40a的各部分、轮辐组件20的中心区域和上轮辐构件21和下轮辐构件22的各部分。图6a和图6b示出了本发明的另一个实施例,其中轮辐121和122由多于一种材料制成。在图6a中,上轮辐构件和下轮辐构件21和22的接近轮辐组件(和轮毂40a)的中心区域20a的部分与本发明的上述实施例相比缩短了,并也例如由冲压钢制成。附连于缩短的部分321和322并从部分321和322延伸的延伸部324由另一种材料制成,如铝板或镁板,它们一起构成了上轮辐121和下轮辐122的其余部分。延伸部324形成了相当于箱形的横截面,上轮辐构件326和下轮辐构件328的安装方式与钢制的上轮辐构件326和下轮辐构件328的安装方式相同。为了便于将由新材料制成的轮辐构件326和328连接到冲压钢制成的上轮辐构件和下轮辐构件,新材料制成的轮辐构件包括收缩(neck-down)部分340,其如图6b所示滑动到缩短的钢制的上轮辐构件和下轮辐构件21和22形成的开口端内。图6b是沿剖线6b-6b的横截面。图6a中虚线的椭圆区域226示出了这些金属应连结在一起的位置。可以使用铆钉、螺栓,和其它的机械紧固装置,如TOX紧固件。简要地参考图7,7a和7b,这些图示意地示出支架10的轮缘12的构造的变形。作为加工过的方向盘,轮缘12上覆盖有塑料涂层覆盖材料200,通常为聚氨脂泡沫,软塑料,或者类似材料。在图7中,轮缘12包括多个槽202,其用于控制轮缘受力时最可能弯曲的位置。此外,如果移除槽202,图7中的轮缘示意地示出图1,2和3中的轮缘。如下附图示出控制轮缘12a受力时如何弯曲的其它方法。在图7a中,轮缘12a的部段204被压平以促进轮缘12a在这些位置弯曲。轮缘12a可以沿径向或沿垂直于径向的方向被压平。各轮缘12和12a可以是管状的或实心的。图7b中,轮缘12b本质上是复合物;例如轮缘12b的诸如206的一部分可以是钢制弯管,实心杆或管208插入管206的开口端210。开口端210形成的管206的壁在轮缘12b被材料200覆盖之前被夹紧或以其它方式变形,以固定杆或管208。杆或管208可以由与管206硬度不同的钢制成,或者由诸如铝或镁的不同材料制成。可以理解的是,轮缘12b易于在较软的材料处弯曲。可以在管206的下部区域内放置另一根杆或管。图8,8a,8b,8c示出本发明的轮辐的构造变型。图8是沿图3中C-C部段的剖视图,其分别示出上轮辐构件21和下轮辐构件22的终止于管状轮缘12的顶部和底部的远端28和26。在图8a中,实心轮缘12d取代了管状轮缘12。如前所述,轮辐构件的构造提供了一种控制方向盘刚度的手段。在图8b中,上轮辐构件21被缩短并且不是延伸直至轮缘12。通过移除上轮辐构件21的该部分,下轮辐构件22a将显示出与和上轮辐构件21的相应部件匹配时相比更大的灵活度,其示出了另一个用于控制轮辐组件20的挠曲的机构。图8c示出了覆盖有塑料覆盖材料200的、图8中的轮缘12和上轮辐构件以及下轮辐构件的一部分。方向盘通常包括诸如220的中心盖,其代表位于方向盘的轮毂和轮辐组件20的一部分上方的气囊盖。物件222代表覆盖方向盘支架的下部分的装饰覆盖物。本发明提供了另一种控制方向盘的轮辐121和122的刚度的方法。再次参考图8和标记224,224是代表注模到上轮辐构件和下轮辐构件21和22之间的空间226内的材料。参考图9,其示出了另一个示例性的轮毂40,其中,中心轮毂40带有扩开的或锥形的底部41a。在这种情况下,轮毂40的焊接凸缘41最初被轴向安置,因此轮毂可以穿过轮辐构件的开口24和24'安装。下轮辐构件22在轮毂40上滑动并焊接到轮毂40(见焊接点23a)。然后,上轮辐构件21在轮毂40上滑动并焊接。轮毂40的凸缘41被弯曲到并焊接到上轮辐21的顶部21T。图5所示的轮辐构件构造也可以与该轮毂40一起使用。如图所示,参考图3的方向盘支架的俯视图,在6点钟位置连接到轮缘12的中间轮辐30作为单个钢板向内延伸,该钢板具有在趋近中心轮毂40或40A时呈“U”形的两个支脚31,32。支脚31,32跨骑在中心轮毂40,40A的每一侧,并且可以定位于轮辐组件20的凸缘上并焊接到凸缘上。上轮辐构件21和下轮辐构件22在轮辐组件20支承轮缘12的位置被焊接到轮缘12上。如前所述,轮缘12可以由壁厚0.75mm的薄壁钢管制成。简要地参考图8d;在该实施例中,上轮辐构件的末端或远端同样在轮缘下方延伸,并且位于轮缘和下轮辐构件的末端或远端之间,从而在轮辐组件和轮缘的附连点处形成了多层构造。参考图3和其它图,所示中间轮辐30在远端36处具有类似凹陷部以在6点钟位置支承轮缘12;中间轮辐30和轮缘12被焊接到一起。例如,中间轮辐30是厚2mm的钢板材料。在不改变支架结构的情况下,支架10的轮缘12的直径可以在380mm到400mm之间变化。这是事实,因为轮辐121,122和30能以如下方式偏转(deflect),即在组装时略向内或向外延伸;由于管状轮缘直径的限制,该支架10一旦被焊接就可以被永久地固定。再参见钢制轮毂40或40A,很重要的是认识到所示的钢制轮毂40或40A可以具有厚约2mm的壁,这使得整个支架10极为轻质,其中组件10的整个中心区域20a通常由轮辐组件20组成。再次参考图4,5和9,下轮辐构件22具有凸缘23,其向下朝中心轮毂40或40A延伸,从而为将钢制轮毂40或40A焊接到下轮辐22提供额外的表面。这些在孔24处与轮毂40或40A并排延伸的凸缘附件为将钢制轮毂焊接到轮辐组件20提供了最佳的焊接位置,因此组件20比简单地由端接焊接制成的组件坚固得多。如上所述,主要的是注意到图示的轮辐构件的连结是顺序的。替代地,可以制成其它的焊接件,其中在附连轮毂40之前预组装轮辐组件20,或替代地轮毂40和轮辐组件20可以作为副组件进行生产,其中在安装管状轮缘12之前,它们与中间轮辐30一起形成。一旦被组装,整个支架10可以依需要使用塑料材料镀膜,模塑,或者浸渍,然后依需要使用任何必要的人造革或皮革材料。如图3的俯视图所示,顶部孔25设置在两个轮辐构件21,22内。这些孔25对准,并且如果有需要的话则为附连气囊模块提供螺栓进入的安装位置。如图所示,本发明的方向盘支架10在进行多种测试时显示基于行业标准所要求的、具有吸引力的刚度和频率性能。例如,静力弯曲测试的目标值为小于15mm偏转;本发明的支架的测试结果为偏转13.7mm,胜过推荐值。轮缘测试的目标值为8500个循环;本发明的钢制轮缘测试时通过了这一要求。施加于轮缘12的扭转弯曲的目标值在给定负荷下为200000个循环;该方向盘支架10轻松地通过了该要求。固有频率的目标值为大于40Hz;所示的本发明的所得示例性方向盘支架10的测试结果达到了50.8Hz,很好地落入要求范围内。本发明的方向盘支架10的优势为,上轮辐构件和下轮辐构件21,22的轮辐组件20在沿匹配的凸缘边缘27,29形成和焊接时形成具有极大的刚度的箱形结构。该刚度随着轮辐构件21,22的形状和尺寸高度而变化。理想地,仅仅需要对上轮辐构件21进行制造和塑形,以使其具有成对的侧壁21S,顶部21T的形状。使用两个凸缘27,29可以提供额外的益处。当下轮辐构件22为一个扁平结构并且具有与上轮辐构件21对准的互补弯曲部时,调整下轮辐构件22使其在相对于上轮辐构件21定位时具有如此定向的凸缘27,29,即,它们可以从轮缘到轮缘附件位置横跨轮辐组件20延伸地焊接。这是有益的,因为箱形结构在整个轮辐组件20上有效地保持,而沿此整条线没有厚的或实心结构。通过提高上轮辐侧壁21S的高度可以改变尺寸刚度。如果确定对于某一刚度需要过大的高度,则上轮辐构件和下轮辐构件21和22可成形为下轮辐构件可以与扁平结构相对地具有凹陷部。在这种情况下,两个轮辐构件21和22的组合将在凸缘27,29之间形成空腔或中空的空间,其足够高可以形成非常大的惯性力矩。该构造使扭转和弯曲刚度增大,进而使得两个轮辐结构在如图所示焊接到一起时难以扭转和/或弯曲。当远端26,28被完全焊接到用于支承轮缘12的凹陷部处时,轮缘12变成结构部件,其有助于轮辐构件21,22维持在适当位置并阻止其进一步向内或向外运动。设置在六点钟位置处的中间轮辐30类似地提供在支架10的下部区域内的附加刚度。该轮辐30可以是不需要凹陷部的单个材料板。替代地,轮辐可以是具有与所述轮辐组件中示出的类似的横截面形状的上轮辐构件和下轮辐构件的组件。该中间轮辐也可以省除。参考图8d中所示的构造,有利地,轮缘12的上部分本质上未被支承,并且可以在事故中任何冲击负荷发生时进行一定的偏转。这是有益的,因为当乘客撞击轮缘时其可以部分地吸收乘客的能量。理想地,支架结构10适于在性能、刚度、弯曲和频率方面进行调整,因此形成的支架10可以被调整以满足任何客户需求,并根据那些需求确定最适合轮辐组件20的横截面形状。所示轮辐组件20具有大致呈矩形的横截面形状。其在中心轮毂区域可以更宽一些,中心轮毂区域20a与轮缘12平行定向。于是当轮辐组件向外延伸时,其从第一弯曲位置向上弯曲到第二弯曲位置。这形成了理想地适于接纳上述气囊单元的较小的中心凹穴。每个轮辐构件21,22都设有附加的第二弯曲部,该第二弯曲部具有向外朝向轮缘12延伸的微小曲率。当这些上轮辐构件和下轮辐构件向外和向上延伸时,它们又弯曲成大致在该处张开,然后轮辐组件20在远端26和28处延伸到压平的型面(profile)。该凹陷部为轮缘12提供支承。该组合提供了上述的支架10,并使工程师能够调整方向盘支架10的形状和结构以满足客户在方向盘性能方面的需要。如进一步所述,轮缘附件位置示出为略微偏离三点钟和九点钟位置,换句话说,它们略微扩张到相对于时针的大约3:30和8:30的位置的下部位置。然而,如果使用中间轮辐30,该中间轮辐被精确定位在另两个轮缘附件位置的中心的六点钟位置,以实现所需的稳定作用。产生轮缘和轮辐组件附件如所示向内从中心轮毂向下至3:30和8:30的位置移位能使组件10在轮缘12的下部分略更刚硬并在上部分略更挠性。这使轮缘12的上部分形成细微的、但有利的挠性弯曲;其次,除非两个上轮辐构件和下轮辐构件之间没有空腔,否则即使中间轮辐30的厚度与轮辐组件20的厚度相同,由于中间轮辐30是单个板材,所以轮缘12的下部分在一定程度上是挠性的。因此,是厚度2mm的平板的中间轮辐30比同样厚2mm的轮辐组件20相对更具挠性,然而,通过上和下两轮辐构件之间形成的凹陷部或空腔可以调整该厚度。如图所示,作为轮辐组件20设置的上和下轮辐构件21,22可调整成其形状可以改变,并且其形状可设有椭圆形横截面或变平为大致矩形的横截面,或者是上和下轮辐组件的组合20,两者的尺寸形状使得两轮辐之间形成间隔,因而下轮辐22可以不是一个平坦的轮辐,而是其替代地设有与上轮辐21类似的凹陷部并翻转成当它们连结时形成甚至更厚的复合结构。在上述的本发明的范围之内的所有这些和其它的替代形式都是可以考虑的。所示设计是由原则上不昂贵的钢冲压而成的。如图所示,轮缘12本身是由管状挤出或实心杆制成的。这些都是使用必要的元件来构成方向盘支架10的最便宜和最廉价的形式。可以清楚地看出,冲压的上轮辐构件和下轮辐构件21,22是以如下方式设计的,它们可以被冲压,从而由单件板材形成许多元件而不过度浪费材料。这非常重要,因为试图包含轮缘的大多数冲压的方向盘支架都以废弃材料的代价来完成。本发明尤其适合,这是因为由管(或杆)构成的轮缘12实际上没有废料,同时冲压的部件也只产生少量的废料。此外,用于气囊单元的孔25在使用时类似地产生一定面积的废料;但是,这些也可以具有向内偏转以提供结构刚度的凸缘孔。因此,上述设计提供了高效的机械结构,其能符合方向盘支架的所有的设计要求,并且比现行的镁和合金结构大幅地降低了成本。图10示出了轮辐组件320的一个替代的实施例。轮辐组件320包括上轮辐构件321和下轮辐构件322,它们分别具有凸缘27和29。凸缘29在图10中不可见但是以虚线29示出。上轮辐构件321包括多个孔340,下轮辐构件322包括与相应的孔340对准的多个类似的开口342。去除轮辐构件材料而形成这些孔减轻了支架的重量。考虑到上述轮辐组件320的构造,引入这些孔对于支架的强度几乎没有影响。根据此处提供的描述,可以对本发明进行各种变形。尽管为描述发明主题已示出一些代表性的实施例和细节,但对本领域技术人员而言显而易见的是在不背离本发明范围的情况下可以对本发明进行各种改型和修改。因此可以理解,在后附的附属权利要求所限定的全部发明范围内,可以对上述的具体实施例进行改型。