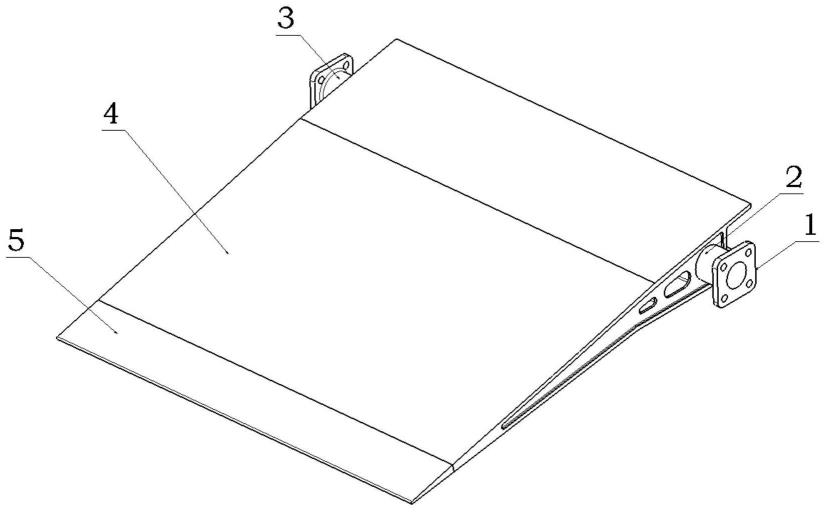
1.本发明涉及一种飞机进气道唇口及降温隔热方法,属于冷板散热器设计领域。
背景技术:2.超高音速飞机在飞行时,由于机体表面气动加热,进气道唇口前缘等区域的机表温度可达600℃以上,且持续时间长,唇缘为尖薄结构,结构高度低,设计空间小,设计难度大。目前,采用的普遍方法是在结构表面增加高温陶瓷或者喷涂耐高温涂料,当飞机的飞行速度较低时(低于4ma时),气流温升没有那么大,使用耐高温材料或喷涂耐高温涂料可以满足要求,但是,当飞机的飞行速度继续提高时,气流温升的情况大幅增加,前述方法就不能很好地解决唇口与机体连接部分温度仍然偏高的问题。
3.作为另一种思路,中国专利“基于磁流体能量旁路的空天飞机主动冷却系统”(cn110318878a,2019-10-11)中利用碱金属高温热管对飞行器进气道前缘、唇口等高温部位进行主动冷却。当飞行速度超过8ma以上时,打开超声速进气道主动冷却高温热管上的控制阀门,将含有碱金属的燃料喷入进气道。但是,这种方式的实现结构相对复杂,成本高。
技术实现要素:4.本发明旨在提供一种飞机进气道唇口及降温隔热方法,改变传统的涂层或涂料等降温隔热方式,采用功能一体化设计,将唇口结构与冷板散热器相结合,利用飞机上的燃油作为冷却工质对唇口结构进行降温,带走热量,使唇口结构温度达到材料允许的温度范围内,解决唇口结构与机体连接部分温度偏高的难题。
5.为了实现上述目的,本发明采用以下技术方案:
6.一种飞机进气道唇口,所述唇口的唇缘为尖薄结构,唇口远离唇缘的一端与飞机机体连接,唇口包括,
7.唇口结构,所述唇口结构为中空结构,中空结构内设置有散热芯体,唇口结构的第一端与飞机机体连接;
8.唇缘前端,所述唇缘前端为实心的尖薄结构,且唇缘前端与唇口结构的第二端相连,且唇缘前端与散热芯体不连通;
9.冷却工质,所述冷却工质在散热芯体中流动,且冷却工质为飞机自身携带的燃油。
10.进一步,飞机进气道唇口还包括,
11.进口管道,所述进口管道连接在唇口结构的第一侧面;
12.出口管道,所述出口管道连接在唇口结构的第二侧面;
13.所述第一侧面和第二侧面为唇口结构上两个相对的表面,且冷却工质经进口管道流入唇口结构中的散热芯体,从出口管道流出散热芯体。
14.进一步,飞机进气道唇口还包括两块安装板,
15.其中一块安装板与进口管道的入口端相连,进口管道为等截面圆管;
16.另一块安装板与出口管道的出口端相连,出口管道为等截面圆管。
17.进一步,所述散热芯体包括多条独立的流道,流道的入口端与进口管道连通,流道的出口端与出口管道连通。
18.进一步,所述散热芯体包括相互并联的上层流道和下层流道,所述相互并联为上层流道的入口与下层流道的入口相连,上层流道的出口与下层流道的出口相连,上层流道紧贴唇口结构的上表面,下层流道紧贴唇口结构的下表面。
19.进一步,所述上层流道和下层流道均为肋板式,上层流道和下层流道均包含四个流程。目前,散热结构主要分为肋板式、板翅式和列管式,这里采用了肋板式,其是在基材上通过机械加工形成流道,可参考口琴管的结构。
20.进一步,所述上层流道和下层流道的肋板开孔,且开孔位置贴近上、下翼面的同一侧。
21.进一步,所述上层流道和下层流道中相邻流程的流道之间为圆弧形过渡。
22.作为一种选择,所述安装板、进口管道、出口管道和唇口结构为d打印一体成型,最后与唇缘前端焊接相连。
23.一种飞机进气道唇口降温隔热方法,在唇口内设置换热结构,并将唇口拆分为带有换热结构的第一部分和不带换热结构的第二部分,其中第一部分与机身相连,第二部分作为唇缘,且换热结构中流动的介质为飞机自身携带的燃油,通过燃油热交换对第一部分降温,第一部分与第二部分均采用耐高温材料,且第二部分的耐高温性能优于第一部分。
24.本发明中,冷却工质经进口管道流入唇口结构中的散热芯体,当散热芯体包含流道时,冷却工质经散热芯体(唇口结构)的流道发生热交换,并从出口管道流出,带走热量,最终降低唇口结构温度。
25.本发明利用飞机自身携带的燃油作为冷却工质,降低唇口结构温度,使唇口结构温度达到材料允许的温度范围内唇口结构成为了唇口前端与机身之间的隔热结构。
26.本发明散热芯体(唇口结构)中流道的设计经仔细计算和验证,通过控制冷却工质的入口温度和流量,可以有效降低唇口结构的温度,温度分布均匀,使唇口结构温度达到材料允许的温度范围内。
附图说明
27.图1为本发明的飞机进气道唇口结构示意图;
28.图2为图1的右视图;
29.图3为本发明的安装板、进口管道、唇口结构(含散热芯体)、出口管道采用3d打印一体成型的结构示意图;
30.图4为图3的俯视图及a-a、b-b截面剖视图;
31.图5为本发明散热芯体中肋板式流道(4流程)示意图;
32.图6为本发明的唇缘前端结构示意图;
33.图中:1—安装板、2—进口管道、3—出口管道、4—唇口结构、5—唇缘前端、6—小孔、7—凹槽。
具体实施方式
34.下面结合附图和具体实施例对本发明作进一步的说明,但不应就此理解为本发明
所述主题的范围仅限于以下的实施例,在不脱离本发明上述技术思想情况下,凡根据本领域普通技术知识和惯用手段做出的各种修改、替换和变更,均包括在本发明的范围内。
35.如图1~图6所示,本实施例中,飞机进气道唇口包括安装板1、进口管道2、出口管道3、唇口结构4(内含散热芯体)和唇缘前端5。飞机进气道唇口的安装板1、进口管道2、出口管道3和散热芯体(唇口结构)4通过3d打印一体成型,然后和实心的、尖薄结构的唇缘前端5通过焊接连接形成唇口。飞机进气道唇口通过凹槽7与飞机的机身连接。
36.如图3所示,为安装板1、进口管道2、出口管道3和唇口结构4(内含散热芯体)通过3d打印一体成型的结构;
37.如图6所示,实心的、尖薄结构的唇缘前端5通过焊接与唇口结构4(内含散热芯体)进行连接;
38.如图4、图5所示,为通过3d打印形成的散热芯体内部结构,流道为上、下两层并联式布局,每层四个流程,上层流道紧贴唇口结构4的上表面,下层流道紧贴唇口结构4的下表面。上层流道和下层流道均为板肋式结构,图5中画出了类似“w”形的流道,形成四个流程,相邻流程之间转向时通过弧形流道连接,图5中肋板式结构包括沿着冷却工质流动方向的肋结构(“w”形),以及水平和竖直方向延伸的肋结构(图5中有3条水平方向和3条竖直方向的肋结构),其中水平方向的3条肋结构上均开有小孔6,可参考图4中标注的位置。上层流道和下层流道的横向肋板上开小孔6,且小孔6的位置贴近上、下翼面的同一侧,即要么统一靠近上翼面一侧开孔,要么统一靠近下翼面一侧开孔,小孔6用于冷却工质的流动,靠近同一侧是为了便于整体成型后(例如3d打印)内部支撑材料的清洗。
39.如图1所示,唇口结构4(内含散热芯体)与唇缘前端5采用焊接进行连接,唇口的温度分布从唇缘前端5往唇口结构4(内含散热芯体)呈逐步降低的趋势,唇口结构4(内含散热芯体)材料使用tc4钛合金,唇缘前端5材料使用更加耐高温的ti60钛合金。
40.如图3所示,安装板1为两个法兰状平板,中间位置开有圆孔,唇口结构4(内含散热芯体)、进口管道2、出口管道3和安装板1采用3d打印一体成型,飞机进气道唇口通过凹槽7安装在飞机上。
41.如图4和图5所示,飞机上的燃油作为冷却工质,通过进口管道2流经唇口结构4中的散热芯体,在流动过程中,冷却工质与唇口结构4大面积接触,并发生热交换,将唇口结构4的热量带走,从出口管道3流出。散热芯体4中分为上层流道和下层流道,上层流道和下层流道中均由多条独立的流道构成,上层流道和下层流道均为四流程(四个平行的直线流程,相邻流程中冷却工质的流向相反),流道相邻流程之间采用圆弧形流道过渡,有利于冷却工质流动,流道采用上、下并联式结构(即上层流道的入口与下层流道的入口连接,上层流道的出口与下层流道的出口连接),能够增大冷却工质与唇口结构4的接触面积,提高热交换效率。流道设计为肋板式,使散热芯体和唇口结构4保持足够的强度和刚度。
42.如图6所示,唇缘前端5为带翼型弧度的薄板(尖薄结构),为了承受高温,采用了ti60钛合金材料,与唇口结构4通过焊接连接。
43.上述实施例并不用于限定本发明的保护范围,凡在本发明的技术方案基础上所做出的变形、修饰或等同替换等,均应落入本发明的保护范围内。