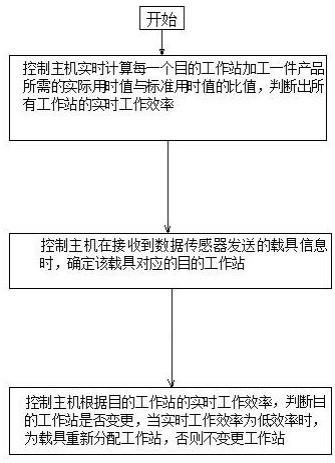
[0001]
本发明涉及吊挂输送领域,更具体地说涉及一种基于工作站效率而变更目的地的吊挂系统及工作方法。
背景技术:[0002]
在吊挂系统例如制衣吊挂系统中,通常设置有多个工作站,每个工作站均承担着相应的职能,只有这些工作站相互配合才能够有效生产出完整的产品。当承载有货品的载具由一个工作站导出时,需要将该载具导入另一个工作站内,从而继续进行加工。而通过主轨将载具由一个工作站输送至另一个工作站内时需要经过一定的时间,在这段时间之内,目的工作站的状态可能已经发生变化,这就需要及时更换目的工作站。
[0003]
申请人在先申请的申请号为2020106559537名称为一种吊挂系统及目的站变更控制方法的专利中,在目的工作站发生异常(包括工作站满站、工作站故障、人员暂时离开等异常情况)且不能工作的情况下,可以重新为载具分配工作站,防止载具在异常工作站积累,从而达到改善系统工作效率的目的。然而,该系统并未考虑到工人的工作状态,在实际工作时,工人的工作状态也会严重影响到工作站的加工效率,进行影响到整个吊挂系统的工作效率,当目的工作站处于能够工作但是低效加工时,存在着载具在目的工作站堆积的隐患,一旦堆积后,不仅处在工作站的载具无法进行及时处理,而那些因工作站满载缘故而无法进入到工作站上的载具只能在主轨上循环运转,占用大量的位置,严重影响其余类型的载具进入到主轨上,降低了整个吊挂系统的加工效率。因此,就需要设置相应的系统及控制方法来确保整个吊挂系统的加工效率。
技术实现要素:[0004]
针对现有技术的不足之处,本发明的目的是提供一种基于工作站效率而变更目的地的吊挂系统及工作方法,及时将低效率状态的目的工作站所对应的并正在主轨上运行的载具重新分配到其他工作站,防止载具在目的工作站上堆积,并降低在主轨上空间的占用,确保其余类型的载具能够顺利进入到主轨上,提升了整个吊挂系统的运行效率以及加工效率。
[0005]
本发明的上述技术目的是通过以下技术方案得以实现的:一种基于工作站效率而变更目的地的吊挂系统,包括主轨、载具、目的工作站、多个数据传感器,控制主机;所述目的工作站,用于加工并记录每一次加工的实际用时值;多个所述数据传感器,和控制主机通讯连接,并依次分布在主轨上,用于获取载具信息并将该载具信息输至控制主机;所述控制主机,用于实时计算所有目的工作站上实际用时值与标准用时值的比值,当所述比值大于预设数值时,则判定该目的工作站为低效率工作站,并为该目的工作站对应的载具重新分配工作站,当比值小于等于预设数值时,则不变更工作站。
[0006]
本技术方案,控制主机不断地对所有目的工作站的工作效率进行判断,当数据传感器检测到载具时,及时将低效率状态的目的工作站所对应的并正在主轨上运行的载具重新分配到其他工作站,防止载具在目的工作站上堆积,并降低在主轨上空间的占用,确保其余类型的载具能够顺利进入到主轨上,提升了整个吊挂系统的运行效率以及加工效率。
[0007]
多个数据传感器,包括靠近于工作站处的传感器,该靠近于工作站处的传感器的设置,能够提升系统分配工作站的准确性,而控制主机在实时计算效率的前提下,直接根据效率决定是否为载具重新分配工作站,为工作站处的执行机构即控制载具在不同轨道之间转移的变轨装置提供足够的执行时间,若提供的执行时间欠缺,原本理应进入到工作站的载具不能够进入到工作站,或者原本理应进入新工作站的载具还是能够进入到原工作站。
[0008]
优选的,加工一件产品所需的实际用时值等于最近一次加工的耗时值。此设置,适用于加工耗时较长的产品,这是因为:加工这类产品的标准用时值较大,相应地,在预设数值一定的情况下,实际用时值可以允许更大,因此,个别加工中出现的因修正占时、适当地休息占时等正常因素完全可以计入到实际用时值而不超出最大允许的实际用时值,也就是说,加工过程中出现的因修正占时、适当地休息占时等因素不会影响到最终的加工效率,将最近一次加工的耗时值作为加工一件产品所需的实际用时值完全可行,而且大大降低了控制主机提取目的工作站的数据提取量,控制主机的计算效率更高。
[0009]
优选的,加工一件产品所需的实际用时值为最后若干次加工的平均耗时值。此设置,适用于加工耗时较短的产品,这是因为:加工这类产品的标准用时值较小,相应地,在预设数值一定的情况下,实际用时值可以允许更小,因此,个别加工中出现的因修正占时、适当地休息占时等正常因素在计入到实际用时值会超出最大允许的实际用时值,如果仅根据这种个别出现的情形作为判定为工作站加工效率低下的理由,显然不是很精准,因此,实际用时值取最后若干次加工的平均耗时值,可以更为精准地体现出工作站最近的加工状态与加工效率。
[0010]
优选的,所述预设数值为自定义编辑。通过自定义编辑,预设数值可实现按需调整,使得工作站加工不同种类的产品时,控制主机还是能够准确判定工作站的加工效率。
[0011]
优选的,所述数据传感器包括射频读取器、扫码器。
[0012]
优选的,所述预设数值为1。
[0013]
值得注意的是,随着加工流程的复杂程度的增加,通常需要将一整个流程分成多道工序分别进行加工,每个工序可对应一个或多个工作站。
[0014]
在其中之一的优选实施方式中,对应于同一工序的目的工作站数量为多个;为载具重新分配的工作站为对应于同一工序的所有目的工作站中的工作效率较高的其中一个工作站。
[0015]
在另一优选实施方式中,所述目的工作站数量为一个;为载具重新分配的工作站为该系统中除目的工作站之外的缓存站或者帮工站或者全能站。其中,缓存站起到缓存作用,防止唯一的目的工作站因为工作效率低下的缘故导致载具在目的工作站堆积等现象的发生;帮工站在工作站未能及时处理时,有能力分担工作站的部分工作;全能站,由全能工操作,及时消化工作站未能消化的工作。
[0016]
一种基于工作站效率而变更目的地的吊挂系统的工作方法,适用于上述技术方案中的吊挂系统,包括如下步骤:
s1:所有目的工作站的实时工作效率判断:控制主机实时计算每一个目的工作站加工一件产品所需的实际用时值与标准用时值的比值,判断出所有工作站的实时工作效率。
[0017]
s2:目的工作站的确定:控制主机在接收到数据传感器发送的载具信息时,确定该载具对应的目的工作站;s3:判断目的工作站是否变更:控制主机根据目的工作站的实时工作效率,判断目的工作站是否变更,当实时工作效率为低效率时,为载具重新分配工作站,否则不变更工作站。
[0018]
通过上述步骤,将低效率状态的目的工作站所对应的载具及时重新分配到高效率的工作站,提升了整个吊挂系统的加工效率。
[0019]
进一步的,对应于同一工序的目的工作站数量为多个;步骤s3中分配工作站的方法为:将载具分配到对应于同一工序的所有目的工作站中的工作效率较高的其中一个工作站。
[0020]
综上所述,本发明具有以下有益效果:1:本发明,控制主机不断地对所有目的工作站的工作效率进行判断,当数据传感器检测到载具时,及时将低效率状态的目的工作站所对应的并正在主轨上运行的载具重新分配到其他工作站,防止载具在目的工作站上堆积,并降低在主轨上空间的占用,确保其余类型的载具能够顺利进入到主轨上,提升了整个吊挂系统的运行效率以及加工效率;2:本发明,预设数值为自定义编辑,预设数值可实现按需调整,使得工作站加工不同种类的产品时,控制主机还是能够准确判定工作站的加工效率;3:本发明,在同一工序对应多个目的工作站时,将载具重新分配到同一工序的所有目的工作站中的工作效率较高的其中一个工作站,这样,既充分利用了工作站原有的设备,还充分了利用了高效工作的工人;4:本发明,在工序仅对应一个目的工作站时,将载具分配到缓存站或者帮工站或者全能站。
附图说明
[0021]
图1为吊挂系统的结构示意简图;图2为吊挂系统的工作流程图。
具体实施方式
[0022]
下面将结合附图,通过具体实施例对本发明作进一步说明。
[0023]
实施例:如图1所示,一种基于工作站效率而变更目的地的吊挂系统, 包括主轨、载具、目的工作站、多个数据传感器,控制主机,载具内设置有芯片,芯片绑定有载具信息,载具信息与货品信息绑定,载具种类为多个,每种载具绑定不同的货品信息,目的工作站为多个,沿着主轨延伸方向进行分布,多个工作站完成多道加工工序,配合完成整个产品的加工,数据传感器可以为射频读取器、扫码器等。
[0024]
特别指出的是,在该系统中,所述目的工作站,在加工过程中记录每一次加工的实际用时值;多个所述数据传感器,和控制主机通讯连接,并依次分布在主轨上,用于获取载具信息并将该载具信息输至控制主机;
所述控制主机,用于实时计算所有目的工作站上实际用时值与标准用时值的比值,当所述比值大于预设数值时,则判定该目的工作站为低效率工作站,并为该目的工作站对应的载具重新分配工作站,当比值小于等于预设数值时,则不变更工作站。并且,所述预设数值优选为1。
[0025]
本技术方案的吊挂系统,控制主机不断地对所有目的工作站的工作效率进行判断,当数据传感器检测到载具时,及时将低效率状态的目的工作站所对应的并正在主轨上运行的载具重新分配到其他工作站,防止载具在目的工作站上堆积,并降低在主轨上空间的占用,确保其余类型的载具能够顺利进入到主轨上,提升了整个吊挂系统的运行效率以及加工效率。
[0026]
多个数据传感器,包括靠近于工作站处的传感器,该靠近于工作站处的传感器的设置,能够提升系统分配工作站的准确性,并且,控制主机在实时计算效率的前提下,直接根据效率决定是否为载具重新分配工作站,为工作站处的执行机构即控制载具在不同轨道之间转移的变轨装置提供足够的执行时间,若提供的执行时间欠缺,原本理应进入到工作站的载具不能够进入到工作站,或者原本理应进入新工作站的载具还是能够进入到原工作站。
[0027]
对于实际用时值的确定,需要根据不同的产品而定。在其中之一实施例中,对于加工耗时较长的产品而言,加工一件产品所需的实际用时值等于最近一次加工的耗时值。这样设定是因为:加工这类产品的标准用时值较大,相应地,在预设数值一定的前提下,实际用时值可以允许更大,因此,个别加工中出现的因修正占时、适当地休息占时等正常因素完全可以计入到实际用时值而不超出最大允许的实际用时值,也就是说,加工过程中出现的因修正占时、适当地休息占时等因素不会影响到最终的加工效率,将最近一次加工的耗时值作为加工一件产品所需的实际用时值完全可行,而且大大降低了控制主机提取目的工作站的数据提取量,控制主机的计算效率更高。在另一实施例中,加工耗时较短的产品而言,加工一件产品所需的实际用时值为最后若干次加工的平均耗时值,这样设定是因为:加工这类产品的标准用时值较小,相应地,在预设数值一定的前提下,实际用时值可以允许更小,因此,个别加工中出现的因修正占时、适当地休息占时等正常因素在计入到实际用时值会超出最大允许的实际用时值,如果仅根据这种个别出现的情形作为判定为工作站加工效率低下的理由,显然不是很精准,因此,实际用时值取最后若干次加工的平均耗时值,可以更为精准地体现出工作站最近的加工状态与加工效率。
[0028]
本实施例,所述预设数值为自定义编辑,通过自定义编辑,预设数值可实现按需调整,使得工作站加工不同种类的产品时,控制主机还是能够准确判定工作站的加工效率。
[0029]
值得注意的是,随着加工流程的复杂程度的增加,通常需要将一整个流程分成多道工序分别进行加工,每个工序可对应一个或多个工作站。在其中之一的优选实施方式中,对应于同一工序的目的工作站数量为多个,并且,为载具重新分配的工作站为对应于同一工序的所有目的工作站中的工作效率较高的其中一个工作站,这样,既充分利用了工作站原有的设备,还充分了利用了高效工作的工人。在另一优选实施方式中,所述目的工作站数量为一个;为载具重新分配的工作站为该系统中除目的工作站之外的缓存站或者帮工站或者全能站,其中,缓存站起到缓存作用,防止唯一的目的工作站因为工作效率低下的缘故导致载具在目的工作站堆积等现象的发生,可以为吊挂系统中固定的某一站点,也可以由工
人指定分配,帮工站在工作站未能及时处理时,有能力分担工作站的部分工作,而全能站则由全能工操作,及时消化工作站未能消化的工作。
[0030]
另外,值得注意的是,考虑到现场布置因素,在一个吊挂系统中经常会出现多个吊挂线组合生产的情况,每条吊挂线具有各自的主轨、载具、目的工作站及数据传感器,在关键节点(过桥接时:连接两条吊挂线的站位或者过渡线)设置数据传感器,载具在到达关键节点,吊挂系统重算该载具对应目的工作站的加工效率,根据目的工作站的加工效率判断是否为载具变更工作站,加工效率的算法跟上述的算法一致。
[0031]
一种基于工作站效率而变更目的地的吊挂系统的工作方法,适用于上述技术方案中的吊挂系统,如图2所示,包括如下步骤:s1:所有目的工作站的实时工作效率判断:控制主机实时计算每一个目的工作站加工一件产品所需的实际用时值与标准用时值的比值,判断出所有工作站的实时工作效率。
[0032]
s2:目的工作站的确定:控制主机在接收到数据传感器发送的载具信息时,确定该载具对应的目的工作站;s3:判断目的工作站是否变更:控制主机根据目的工作站的实时工作效率,判断目的工作站是否变更,当实时工作效率为低效率时,为载具重新分配工作站,否则不变更工作站。
[0033]
通过上述步骤,将低效率状态的目的工作站所对应的载具及时重新分配到高效率的工作站,提升了整个吊挂系统的加工效率。
[0034]
对应于同一工序的目的工作站数量为多个;步骤s3中分配工作站的方法为:将载具分配到对应于同一工序的所有目的工作站中的工作效率较高的其中一个工作站。该分配方法既充分利用了工作站原有的设备,还充分了利用了高效工作的工人。
[0035]
上面所述的实施例仅是对本发明的优选实施方式进行描述,并非对本发明的构思和范围进行限定。在不脱离本发明设计构思的前提下,本领域普通人员对本发明的技术方案做出的各种变型和改进,均应落入到本发明的保护范围,本发明请求保护的技术内容,已经全部记载在权利要求书中。