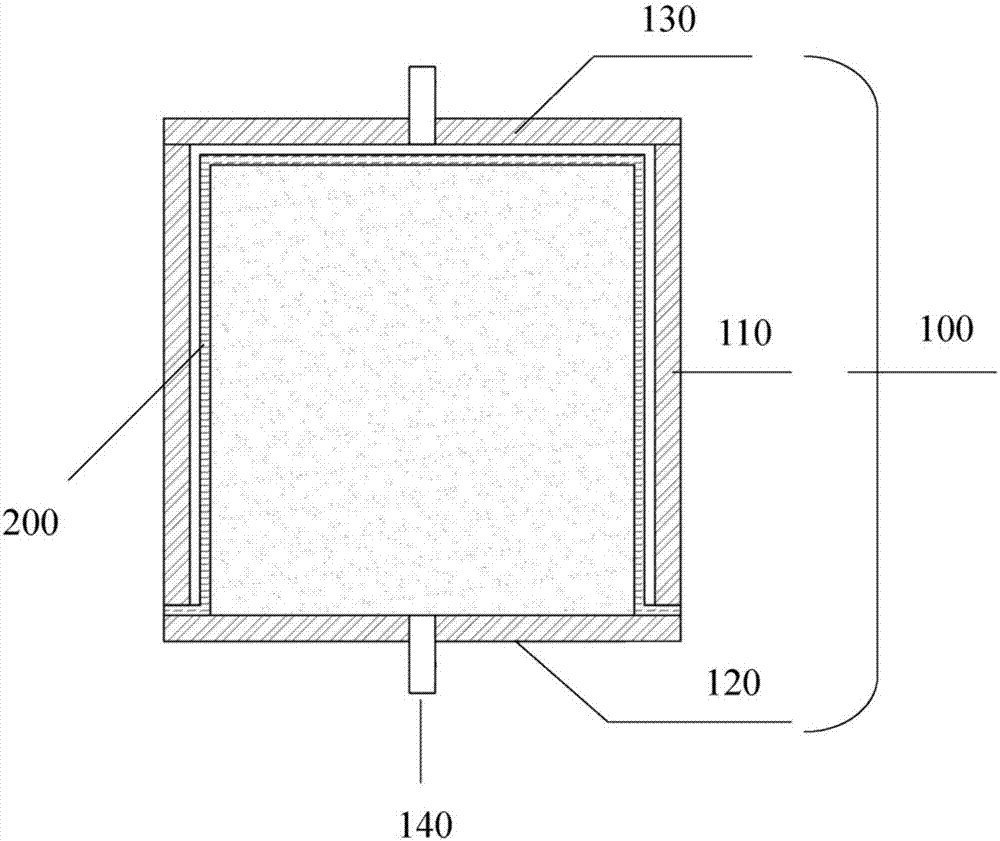
本发明涉及浮力材料制备
技术领域:
,特别是涉及一种组合模具及应用其制备固体浮力材料的方法。
背景技术:
:随着海洋开发科学的兴起和发展,人类对海底世界的探索越来越多,潜入深度越来越深,迫切需要能应用于深海的浮力材料,以保证深水设备的安全使用。所以,从20世纪60年代就开始,国内外就开始了对高强度浮力材料的研究。专利200610043524.4公开了一种深海用可加工固体浮力材料及其制备方法。该方法是将空心玻璃微珠和环氧树脂在80-100℃下于捏合机中搅拌混合,放入模具中加压升温固化,其适用深度为4000米。专利200910174576.9公开了一种可加工固体浮力材料及其制备方法。在加热条件下将环氧树脂、固化剂等和空心玻璃微珠混合,糅合后填入模具中固化,固化时间需40小时。上述制备浮力材料的方法中,均需要将捏合后的物料转移到模具中;加压压至成型后在模具中加压固化,脱模。由于固化需在模具中进行,即使把模具抛光并涂抹脱模剂,固化后的环氧树脂等树脂仍然会与模具的一些区域,特别是边角等位置有较强的结合,导致脱模比较困难。而且,固化后脱模,模具上会残留一些固化后的树脂,因此还涉及模具的清洗和抛光过程。因此,上述制备浮力材料的方法的生产效率较低,劳动强度也较大。技术实现要素:本发明实施例的目的在于提供一种模具及应用其制备固体浮力材料的方法,以解决现有的制备浮力材料的方法固化后脱模比较困难,脱模后的模具需要清洗的问题。具体技术方案如下:本发明首先提供了一种组合模具,包括:外模具及模具内衬;所述外模具包括:沿轴向的两端设置有第一端口及第二端口的筒身,与两端口对应的第一端盖及第二端盖;两个端盖上分别设置有用于抽真空用的真空口;所述模具内衬由柔性材料制得,呈筒状,其沿轴向的一端或两端设置有开口;所述模具内衬与外模具彼此相分离,在使用组合模具时,将模具内衬置于外模具内。一种具体实施方式中,还包括:置于两个端盖的内侧端面上的多孔隔板,且所述多孔隔板与真空口相对应。一种具体实施方式中,还包括:置于模具内衬和外模具之间的多孔隔板。一种具体实施方式中,还包括:置于模具内衬和外模具之间的、可充液体的橡胶囊。本发明还提供了一种应用上述的模具制备固体浮力材料的方法,包括:(a)获得用于制备固体浮力材料的原料混合物;(b1)将一端开口的模具内衬置于外模具的筒身内,并将模具内衬开口端的外边缘外翻置于外模具筒身第一端口的外侧;(c1)将物料从模具内衬的开口加入到模具内衬中,用第一端盖密封第一端口和模具内衬的开口,用第二端盖密封第二端口;或(b2)将两端开口的模具内衬置于外模具筒身内,并将模具内衬一端开口的外边缘外翻置于外模具筒身第一端口的外侧;(c2)用第一端盖密封第一端口和模具内衬的开口,将物料从模具内衬的另一端开口加入到模具内衬中并密封该开口,用第二端盖密封第二端口;(d)通过第二端盖的真空口对外模具内部抽真空处理,当外模具内部的真空度达到第一阈值后,通过第一端盖的真空口对模具内衬内部抽真空处理,当模具内衬内部的真空度达到第二阈值后,通过第二端盖的真空口使外模具内部与大气连通;将第二端盖与外模具的筒身分离;(e)对模具内衬包裹的原料混合物施加压力,当压力达到第三阈值时,得到成型的坯体;将成型的坯体与外模具及模具内衬分离;(f)将坯体固化处理,得到所述固体浮力材料。一种具体实施方式中,所述原料混合物包括:树脂基料和空心微珠,优选地,所述树脂基料包括环氧树脂及其固化剂。一种具体实施方式中,所述第一阈值为-0.08~-0.1mpa,所述第二阈值为-0.08~-0.1mpa;所述第三阈值0.2-3mpa。一种具体实施方式中,当组合模具还包括置于模具内衬和外模具之间的、可充液体的橡胶囊时,在步骤(d)之后,还包括:向橡胶囊内部填充压力值达到第四阈值的液体,优选地,所述第四阈值为0.2-3mpa。一种具体实施方式中,在步骤(d)之后,还包括:向筒身与模具内衬的缝隙中填塞填料。采用本发明提供的模具制备固体浮力材料,其无须在模具中加压固化,可以在固化前脱膜,避免了固化后脱模比较困难的问题,同时外模具没有直接与物料接触,无需清洗和抛光;而模具内衬因为其中的物料收缩后尺寸小于模具内衬,在物料压制形成坯体后,很容易和模具内衬分离,无需清理。进一步地,在本发明的技术方案中,因为物料有多向收缩的过程,物料之间有较大的位移和错动,所制得的固体浮力材料缺陷少,吸水率小。附图说明为了更清楚地说明本发明实施例或现有技术中的技术方案,下面将对实施例或现有技术描述中所需要使用的附图作简单地介绍,显而易见地,下面描述中的附图仅仅是本发明的一些实施例,对于本领域普通技术人员来讲,在不付出创造性劳动的前提下,还可以根据这些附图获得其他的附图。图1为本发明提供的一种组合模具使用时的结构示意图。具体实施方式本发明提供了一种组合模具,如图1所示,可以包括:外模具100及模具内衬200;所述外模具100包括:沿轴向的两端设置有第一端口及第二端口的筒身110,与两端口对应的第一端盖120及第二端盖130;两个端盖上分别设置有用于抽真空用的真空口140;所述模具内衬200由柔性材料制得,呈筒状,其沿轴向的一端或两端设置有开口;所述模具内衬200与外模具100彼此相分离,在使用组合模具时,将模具内衬200置于外模具100内。需要说明的是,本发明中的外模具,其所形成的模腔的具体形态可以参照现有的制备固体浮力材料时使用的模具来实现;模腔的具体形态不构成对本发明的限定。例如,模腔的具体形态可以为圆筒形、方筒形及其它异形结构;外模具的材质可以采用与其它的固体浮力材料制备方法所采用的模具相同的材质,如钢、铁等硬质金属。在本申请的具体实施方式中,第一端盖及第二端盖与筒身彼此可以是分离的。在需要的情况下,可以将第一端盖及第二端盖覆盖在筒身的两端口,以实现对两端口的密封。当然,第一端盖及第二端盖与筒身彼此也可以活动连接,例如铰接等;只要第一端盖及第二端盖保证其既可以充分暴露筒身的两端口,也可以密封两端口即可。在本发明中,所说的柔性材料可以理解为在制备固体材料所采用的真空度或压力下,例如在-0.01~-0.1mpa真空度下,0~5mpa压力下,其可以任意产生形变的材料。在具体实施过程中,柔性材料可以采用橡胶、弹性体及塑料膜等。当模具内衬两端设置有开口时,可以采用塑料膜筒或橡胶膜筒,当模具内衬一端设置有开口时,可以采用塑料袋或橡胶袋等。可以理解的是,当采用橡胶材质的模具内衬时,因为其中的物料收缩后尺寸小于模具内衬,在物料压制形成坯体后,很容易和模具内衬分离,无需清理。当采用塑料膜材质的模具内衬时,一方面因为其中的物料收缩后尺寸小于模具内衬,在物料压制形成坯体后,很容易和模具内衬分离,无需清理,另一方面,当采用比较廉价的塑料膜材质的模具内衬,例如常用的塑料袋时,可以每次压制后进行更换,由于塑料袋成本极低,并不会明显增加成本。在本发明中,所说的术语“真空度”可以理解为相对真空度,是指被测对象的压力与测量地点大气压的差值,其数值为负数。可以用普通真空表测量;在没有真空的状态下(即常压时),真空表的表的初始值为0。当测量真空度时,它的值介于0到-101.325kpa之间。在一种具体实施方式中,下述制备固体浮力材料过程中,为了防止原料混合物堵塞第一端盖的真空口,可以在第一端盖的内侧端面上设置有多孔隔板;可以理解的是,由于制备固体浮力材料的原料混合物中树脂基料等基体材料所占体积比一般较小,使得原料混合物流动性很差,因此一般带孔的板状物,能够保证顺利抽真空的均可以。多孔隔板具体可以是多孔硬隔板或带有缝隙的软垫等。相似的道理,下述制备固体浮力材料过程中,为了防止模具内衬在抽真空时堵塞第二端盖的真空口,可以在第二端盖的内侧端面上设置有多孔隔板。可以理解的是,真空口必然是贯穿各端盖的,因此所说的孔隔板的位置与真空口相对应,可以理解为多孔隔板在端盖的内侧格挡住真空口。在一种具体实施方案中,下述固体浮力材料的制备过程中,在通过第二端盖的真空口使外模具内部与大气连通时,为了保证模具内衬侧壁同时受到大气压力,以使原料混合物受力、变形更均匀,可以在模具内衬和外模具之间设置多孔隔板。在一种具体实施方案中,下述固体浮力材料的制备过程中,在对模具内衬包裹的原料混合物施加压力时,为了保证原料混合物的横向也能均匀受压,进一步提升产品的品质,例如减少固化后出现的孔隙、裂纹等缺陷,降低吸水率,可以在模具内衬和外模具之间设置可充液体的橡胶囊;当对模具内衬包裹的原料混合物施加压力时,可以同时向橡胶囊中充液体,进而挤压原料混合物,从而使得原料混合物除了受到轴向的压力外,还可以受到周向或横向的压力。具体实施过程中,橡胶囊可以通过导管与液压泵等液压设备连接,从而实现向橡胶囊中充液体。基于前述的组合模具,本发明还提供了制备固体浮力材料的方法,可以包括:(a)获得用于制备固体浮力材料的原料混合物;(b1)将一端开口的模具内衬置于外模具筒身内,并将模具内衬开口端的外边缘外翻置于外模具筒身第一端口的外侧;(c1)将物料从模具内衬的开口加入到模具内衬中,用第一端盖密封第一端口和模具内衬的开口,用第二端盖密封第二端口;(d)通过第二端盖的真空口对外模具内部抽真空处理,当外模具内部的真空度达到第一阈值时,通过第一端盖的真空口对模具内衬内部抽真空处理,当模具内衬内部的真空度达到第二阈值后,通过第二端盖的真空口使外模具内部与大气连通;将第二端盖与外模具的筒身分离;(e)对模具内衬包裹的原料混合物施加压力,当压力达到第三阈值时,得到成型的坯体;将成型的坯体与外模具及模具内衬分离;(f)将坯体固化处理,得到所述固体浮力材料。或本发明还提供的制备固体浮力材料的方法,可以包括:(a)获得用于制备固体浮力材料的原料混合物;(b2)将两端开口的模具内衬置于外模具的筒身内,并将模具内衬一端开口的外边缘外翻置于外模具筒身第一端口的外侧;(c2)用第一端盖密封第一端口和模具内衬的开口,将物料从模具内衬的另一端开口加入到模具内衬中并密封该开口,用第二端盖密封第二端口;(d)通过第二端盖的真空口对外模具内部抽真空处理,当外模具内部的真空度达到第一阈值时,通过第一端盖的真空口对模具内衬内部抽真空处理,当模具内衬内部的真空度达到第二阈值后,通过第二端盖的真空口使外模具内部与大气连通;将第二端盖与外模具的筒身分离;(e)对模具内衬包裹的原料混合物施加压力,当压力达到第三阈值时,得到成型的坯体;将成型的坯体与外模具及模具内衬分离;(f)将坯体固化处理,得到所述固体浮力材料。需要说明的是,在上述步骤(a)中,所获得的原料混合物可以为本领域用于制备浮力材料所采用的任意的原料混合物;一般地,原料混合物包括:树脂基料和空心微珠,进一步具体的,所述树脂基料可以包括环氧树脂及其固化剂,当然也可以根据需要添加其它助剂,例如促进剂等。所用的空心微珠可以采用玻璃微珠、陶瓷微珠等。原料混合物的具体成分及比例本发明在此不进行限定。发明人在实验过程中,意外地发现,要想实现本发明的目的,得到密实、吸水率小的固体浮力材料,一个必要的条件是在步骤(d)中,先通过第二端盖的真空口对外模具内部抽真空处理,当真空度达到第一阈值时,再通过第一端盖的真空口对模具内衬内部抽真空处理;如果采用相反的抽真空步骤,则因原料混合物内部气体不能排净,所获得的浮力材料中会含有气孔、裂纹等宏观缺陷。在步骤(d)中,所说的“外模具内部”可以理解为外模具内部且模具内衬外部的区域。而当外模具内部与大气连通后,由于第一端盖仍然在抽真空,所以模具内衬中的原料混合物及模具内衬会在大气压力下收缩,使得模具内衬的四周及与第二端盖对应的端部产生空隙。优选地,模具内衬内部的真空度达到第二阈值后,可以继续进行抽真空处理一段时间,例如2-3分钟,以便更为彻底的将原料混合物内部气体排出。在步骤(e)中,可以通过压力机等常规的压力设备从与第二端盖对应的筒身端口,沿轴向对内衬包裹的原料混合物施加压力。在加压的过程中,第一端盖的真空口仍然处于抽真空的状态;在得到坯体后,可以撤去压力并通过第一端盖的真空口使外模具内部与大气连通;然后将坯体连同模具内衬从外模具中推出,再撤去模具内衬,实现坯体与外模具及模具内衬分离;在上述制备方法的具体实施过程中,所述第一阈值为-0.08~-0.1mpa,所述第二阈值为-0.08~-0.1mpa;所述第三阈值0.2~3mpa,优选为0.5~2mpa。本发明可以在得到坯体后撤去组合模具,将单独的坯体进行固化处理,因此可以避免现有的浮力材料制备方法所存在的问题。与坯体分离后的模具内衬无需清理,可以直接用于后续的制备过程,使得生产效率大在提高。需要说明的是,固化处理可以根据所使用的原料混合物采用现有的固化工艺来实现,本发明在此不进行限定。发明人在研究现有的浮力材料制备方法时发现,因为制备固体浮力材料时原料混合物中树脂基料所占体积比一般较小,原料混合物流动性较差,用这些方法所得到的浮力材料通常含有较多宏观气孔、裂纹等缺陷,吸水率较大。而采用本发明的方法所制得的浮力材料,由于物料有多向收缩的过程,物料之间有较大的位移和错动,压制后基本不含有宏观气孔,同时也减少了裂纹等缺陷,提升了产品的品质,降低了吸水率。根据前面所说的组合模具,当组合模具还包括置于模具内衬和外模具之间的、可充液体的橡胶囊时,在步骤(d)之后,上述方法还可以包括:向橡胶囊内部填充压力值达到第四阈值的液体,优选地,所述第四阈值为0.2-3mpa。如前所述,这可使得原料混合物除了受到轴向的压力外,还可以受到周向或横向的压力,使原料混合物多方向受力,受力更均匀,形变也更均匀,同时也能防止原料混合物横向形变过大,进一步提升产品的品质。作为橡胶囊的一种替代方式,在步骤(d)之后,上述方法还可以包括:可以向筒身与模具内衬的缝隙中填塞填料。填料具体可以是硬板等。下面对本发明实施例中的技术方案进行清楚、完整地描述,显然,所描述的实施例仅仅是本发明一部分实施例,而不是全部的实施例。基于本发明中的实施例,本领域普通技术人员在没有做出创造性劳动前提下所获得的所有其他实施例,都属于本发明保护的范围。实施例1将环氧单体(tta21)、固化剂(四氢苯酐)、催化剂(kh560)和促进剂(n,n-二甲基苄胺)按质量比100:140:1.5:1的比例称量,与空心玻璃微珠(美国3m公司,hgs8000x,密度0.42g/cm3)混合,使空心玻璃微珠与环氧体系(包括环氧单体、固化剂、催化剂和促进剂)的体积比为70:30。将经初混后的空心玻璃微珠与环氧体系投入真空捏合机,在真空条件下捏合15分钟后备用。利用两端开口的塑料膜筒作为模具内衬,将模具内衬衬于同样两端开口的外模具筒身中。将模具内衬一端开口的外边缘外翻套在外模具第一端口的外侧上,然后压在带有抽真空口的第一端盖上,保证密闭不漏气。将上述用真空捏合后的物料装入模具内衬,然后把模具内衬另一端口扎紧,保证其不漏气。用第二端盖密封第二端口,通过第二端盖的真空口对外模具内部抽真空处理。待外模具内部的真空度达到-0.095mpa时,通过第一端盖的真空口对模具内衬内部抽真空处理;当模具内衬内部的真空度达到-0.09mpa后,继续抽真空2~3分钟,然后通过第二端盖的真空口使外模具内部与大气连通。此时模具内物料将因大气压力而收缩。撤去第二端盖,换上压力机的压头,对模具内衬包裹的原料混合物施加压力,当加压到2mpa后,将成型的坯体连同模具内衬一起从外模具中推出。将坯体与外模具及模具内衬分离后,将坯体放入烘箱置于烘箱中,于90℃预固化3小时,然后于160℃固化3小时,得到固体浮力材料。实施例2将环氧单体(tta21)、固化剂(四氢苯酐)、催化剂(kh560)和促进剂(n,n-二甲基苄胺)按质量比100:140:1.5:1的比例称量,与空心玻璃微珠(美国3m公司,hgs8000x,密度0.42g/cm3)混合,使空心玻璃微珠与环氧体系(包括环氧单体、固化剂、催化剂和促进剂)的体积比为67:33。将经初混后的空心玻璃微珠与环氧体系投入真空捏合机,在真空条件下捏合15分钟后备用。利用两端开口的塑料膜筒作为模具内衬,将模具内衬衬于同样两端开口的外模具筒身中。将模具内衬一端开口的外边缘外翻套在外模具第一端口的外侧上,然后压在带有抽真空口的第一端盖上,保证密闭不漏气。将上述用真空捏合后的物料装入模具内衬,然后把模具内衬另一端口扎紧,保证其不漏气。用第二端盖密封第二端口,通过第二端盖的真空口对外模具内部抽真空处理。待真空度达到-0.09mpa时,通过第一端盖的真空口对模具内衬内部抽真空处理,当真空度达到-0.09mpa后,继续抽真空2~3分钟,然后通过第二端盖的真空口使外模具内部与大气连通。此时模具内物料将因大气压力而收缩。撤去第二端盖,换上压力机的压头,对模具内衬包裹的原料混合物施加压力,当加压到1.5mpa后,将成型的坯体连同模具内衬一起从外模具中推出。将坯体与外模具及模具内衬分离后,将坯体放入烘箱置于烘箱中,于90℃预固化3小时,然后于160℃固化3小时,得到固体浮力材料。实施例3将环氧单体(e44)固化剂(t31)按质量比4:1的比例称量,与空心玻璃微珠(美国3m公司,k20,密度0.20g/cm3)混合,使空心玻璃微珠与环氧体系(包括环氧单体和固化剂)的体积比为68:32。将经初混后的空心玻璃微珠与环氧体系投入真空捏合机,在真空条件下捏合15分钟后备用。利用一端开口的塑料袋作为模具内衬,将模具内衬衬于两端开口的外模具筒身中。将模具内衬开口的外边缘外翻套在外模具第一端口的外侧上,将上述用真空捏合后的物料装入模具内衬,然后用带有抽真空口的第一端盖密封第一端口,保证密闭不漏气。用第二端盖密封第二端口,通过第二端盖的真空口对外模具内部抽真空处理。待真空度达到-0.08mpa时,通过第一端盖的真空口对模具内衬内部抽真空处理,当真空度达到-0.08mpa后,继续抽真空2~3分钟,然后通过第二端盖的真空口使外模具内部与大气连通。此时模具内物料将因大气压力而收缩。撤去第二端盖,换上压力机的压头,对模具内衬包裹的原料混合物施加压力,当加压到0.5mpa后,将成型的坯体连同模具内衬一起从外模具中推出。将坯体与外模具及模具内衬分离后,将已成型的坯体于室温固化24小时,得到固体浮力材料。对比例1将环氧单体(tta21)、固化剂(四氢苯酐)、催化剂(kh560)和促进剂(n,n-二甲基苄胺)按质量比100:140:1.5:1的比例称量,与空心玻璃微珠(美国3m公司,hgs8000x,密度0.42g/cm3)混合,使空心玻璃微珠与环氧体系(包括环氧单体、固化剂、催化剂和促进剂)的体积比为70:30。将经初混后的空心玻璃微珠与环氧体系投入真空捏合机,在真空条件下捏合15分钟后备用。将真空捏合后的物料投入圆筒形模具中,在真空条件下施加3mpa的压力。然后,撤去真空,在保持压力的情况下将模具置于烘箱中,于90℃预固化3小时,然后于160℃固化3小时,得到固体浮力材料。对比例2参照对比例1的方法制备浮力材料,对比例2与对比例1的不同之处在于:施加压力后,将物料从模具中推出,坯体置于烘箱中固化。固化过程中坯体处于自由状态,不受压力。对比例3参照对比例1的方法制备浮力材料,对比例3与对比例1的不同之处在于:施加的压力为4mpa。结果发现,空心玻璃微珠被压碎。对实施例1-3及对比例1-3所制得的浮力材料进行各项性能测试,包括:密度及吸水率,测试结果如表1、表2所示。各性性能的测试方法如下:(1)密度:把材料样品用gtqtm5000型精密切割机切出规则的5个长方体块状实验样品,测出各边长度,计算出体积;采用称量精度为0.0001g的电子分析天平(型号:fa2004a)准确称量出长方体块的质量,用质量除以体积即为样品密度。(2)吸水率:每种配比的材料在精密切割机上切割出5个尺寸约为10×10×25mm的长方体块样品,测出原始质量m0。每种配比的样块放入静水压检测装置中,打压至指定压力下保压指定时间,取出擦干表面水分后称量其质量m1。吸水率按照下式计算:吸水率=(m1-m0)/m0×100%表1实施例1-3所制得的浮力材料的性能密度(g/cm3)保压1周吸水率(%)实施例10.5630mpa下,1%实施例20.6270mpa下,0.8%实施例30.4610mpa下,1%表2对比例1-3所制得的浮力材料的性能密度(g/cm3)保压30分钟吸水率(%)对比例10.5530mpa下,2%对比例20.553mpa下,12%对比例30.613mpa下,13%从表1及表2中可以看出,采用本发明的方法制备的浮力材料,因为物料有多向收缩的过程,物料之间有较大的位移和错动,所制得的固体浮力材料吸水率小。需要说明的是,在本文中,诸如第一和第二等之类的关系术语仅仅用来将一个实体或者操作与另一个实体或操作区分开来,而不一定要求或者暗示这些实体或操作之间存在任何这种实际的关系或者顺序。而且,术语“包括”、“包含”或者其任何其他变体意在涵盖非排他性的包含,从而使得包括一系列要素的过程、方法、物品或者设备不仅包括那些要素,而且还包括没有明确列出的其他要素,或者是还包括为这种过程、方法、物品或者设备所固有的要素。在没有更多限制的情况下,由语句“包括一个……”限定的要素,并不排除在包括所述要素的过程、方法、物品或者设备中还存在另外的相同要素。以上对本发明所提供的一种组合模具及应用其制备固体浮力材料的方法进行了详细介绍。本文中应用了具体实施例对本发明的原理及实施方式进行了阐述,以上实施例的说明只是用于帮助理解本发明的方法及其中心思想。应当指出,对于本领域的普通技术人员来说,在不脱离本发明原理的前提下,还可以对本发明进行若干改进和修饰,这些改进和修饰也落入本发明权利要求的保护。当前第1页12