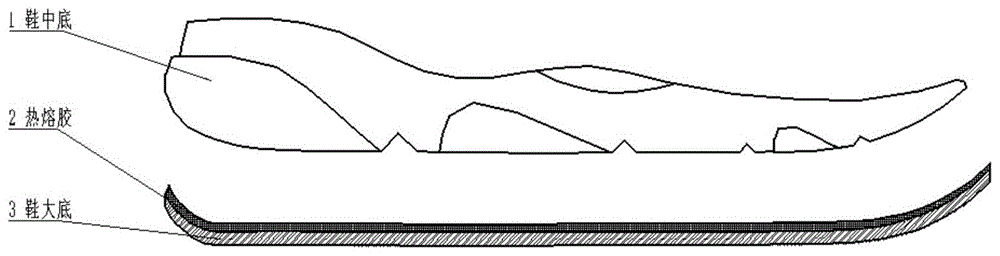
本发明涉及鞋材
技术领域:
,尤其涉及一种tpu发泡颗粒的鞋中底与鞋大底一体成型的成型工艺。
背景技术:
:热塑性聚氨酯材料(tpu)因具有高耐磨,高弹性,耐化学性等诸多优点,因此在很多行业应用广泛,而tpu发泡材料质量轻、弹性好,广泛应用于鞋材、汽车内饰等领域。当前市场上的tpu发泡颗粒的中底成型依赖蒸汽模压成型,完全定型后采用热融胶和大底进行粘合,工艺过程较多,诸多细节处理仍然依赖人工手动完成,自动化程度低下。例如,中底与大底之间需要对准,若采用人工处理的方式,耗费大量时间,还容易产生差错。因此,本领域的技术人员致力于开发一种tpu发泡颗粒的鞋中底与鞋大底一体成型的成型工艺,将中底模压成型以及和大底粘合的步骤简化至一步成型,以提高生产效率。技术实现要素:有鉴于现有技术的上述缺陷,本发明所要解决的技术问题是提高生产效率,以减少大量贴合的人工操作。为实现上述目的,本发明提供了一种tpu发泡颗粒的鞋中底与鞋大底一体成型的成型工艺,包括以下步骤:步骤一、涂胶:预先制成鞋大底,在大底的贴合面上均匀地涂上一层热融胶,然后将涂胶的大底装入母模后放到蒸汽模压成型机内;步骤二、合模:调节模缝,将tpu发泡颗粒吸入模具内部,并充满整个模具,合模后向模具内通入高温的蒸汽进行蒸汽穿透;步骤三、二次合模:tpu发泡颗粒在模具中再次通过蒸汽穿透,使高温高压的蒸汽将tpu发泡颗粒表面进行微熔,并将刷在大底上方的热融胶进行了加热使其熔化,使模具内部的表面微熔的tpu发泡颗粒相互加压粘合在一起,并经由热融胶与下面的大底粘合在一起;步骤四、定型:将经模压成型后的产品进行水冷定型处理,开模后得到一体成型的tpu发泡颗粒的鞋底。进一步地,步骤一中,热融胶的涂覆厚度为0.1-0.5mm。优选地,热熔胶为pu胶。进一步地,采用的蒸汽模压成型机为立式成型机,其模具为上下开合。进一步地,步骤二中,模缝为5-25mm。进一步地,合模时的蒸汽压力为0.05-0.4mpa,蒸汽穿透的时间为10-60s。更进一步地,合模时的蒸汽压力设置为0.15-0.25mpa,蒸汽穿透时间为10-30s。优选地,合模时的蒸汽压力设置为0.2mpa,蒸汽穿透时间为30s。进一步地,水冷定型的时间为60-150s。更进一步地,在水冷定型前先自然冷却至40-50℃。技术效果:(1)本发明的鞋子中底与鞋子大底一体成型的工艺,将事先涂好热融胶放入模具内,然后再吸入tpu发泡颗粒进行蒸汽穿透成型,这样避免了后期进行大底贴合所造成的成本高、效率低等问题;(2)本发明只需消耗较少的热熔胶即可实现同等强度的粘合效果,节约了成本,也减少了热熔胶加热后排出的有害气体的排放,对操作人员以及环境的危害也得到降低;(3)本发明的一体成型技术可以广泛的运用在tpu发泡颗粒所成型的鞋子领域,可大量减少后期大底贴合所需要的人工及设备,并且大大提高了生产效率。以下将结合附图对本发明的构思、具体结构及产生的技术效果作进一步说明,以充分地了解本发明的目的、特征和效果。附图说明图1是本发明产品中的鞋底部分的组成示意图。图中,1鞋中底,2热熔胶,3鞋大底。具体实施方式如图1所示为本发明的产品的鞋底示意图,该鞋底是由tpu发泡颗粒模压所成的鞋中底1与鞋大底3之间通过热熔胶2粘合而成。如果采用人工手动作业,自动化程度低下,还需要将中底的轮廓与大底上的安装位置对准,而本发明的一体成型的工艺就可以减少上述的繁琐步骤,以下为具体的实施例。实施例1本实施例的tpu发泡颗粒的鞋中底与鞋大底一体成型的成型工艺,步骤如下:将橡胶大底与中底贴合的一面均匀的涂上厚度为0.5mm的一层pu胶水,然后放入鞋中底成型的下方母模内,放到立式蒸汽模压成型机内,该成型机的模具是上下开合;调节模缝至10mm,并开启设备,将tpu发泡颗粒吸入模具内部,并填充满整个模具,合模后向模具内通入蒸汽,模具内温度为100-130℃;随后开始二次合模,再次通过蒸汽穿透,高温蒸汽将颗粒表面进行微溶并粘合在一起,tpu发泡颗粒之间相互挤压,空隙被填充,同时大底上涂的胶水溶化,与tpu颗粒粘合在一起,中底与大底紧密贴合,蒸汽穿透的蒸汽压力设置为0.15mpa,蒸汽穿透时间为50s;随后,自然冷却至40-50℃后进行水冷定型,水冷时间设置为90s,开模,得到最终的成型制品。实施例2本实施例的tpu发泡颗粒的鞋中底与鞋大底一体成型的成型工艺,步骤如下:将橡胶大底与中底贴合的一面均匀的涂上厚度为0.3mm的一层pu胶水,然后放入鞋中底成型的下方母模内,放到立式蒸汽模压成型机内,该成型机的模具是上下开合;调节模缝至25mm,并开启设备,将tpu发泡颗粒吸入模具内部,并填充满整个模具,合模后向模具内通入蒸汽,模具内温度为100-130℃;随后开始二次合模,再次通过蒸汽穿透,高温蒸汽将颗粒表面进行微溶并粘合在一起,tpu发泡颗粒之间相互挤压,空隙被填充,同时大底上涂的胶水溶化,与tpu颗粒粘合在一起,中底与大底紧密贴合,蒸汽穿透的蒸汽压力设置为0.05mpa,蒸汽穿透时间为60s;然后自然冷却至40-50℃,之后进行水冷定型,水冷时间设置为60s,开模,得到最终的成型制品。实施例3本实施例的tpu发泡颗粒的鞋中底与鞋大底一体成型的成型工艺,步骤如下:将橡胶大底与中底贴合的一面均匀的涂上厚度为0.2mm的一层pu胶水,然后放入鞋中底成型的下方母模内,放到立式蒸汽模压成型机内,该成型机的模具是上下开合;调节模缝至5mm,并开启设备,将tpu发泡颗粒吸入模具内部,并填充满整个模具,合模后向模具内通入蒸汽,模具内温度为100-130℃;随后开始二次合模,再次通过蒸汽穿透,高温蒸汽将颗粒表面进行微溶并粘合在一起,tpu发泡颗粒之间相互挤压,空隙被填充,同时大底上涂的胶水溶化,与tpu颗粒粘合在一起,中底与大底紧密贴合,蒸汽穿透的蒸汽压力设置为0.4mpa,蒸汽穿透时间为10s;然后自然冷却至40-50℃,之后进行水冷定型,水冷时间设置为150s,开模,得到最终的成型制品。实施例4本实施例的tpu发泡颗粒的鞋中底与鞋大底一体成型的成型工艺,步骤如下:将橡胶大底与中底贴合的一面均匀的涂上厚度为0.3mm的一层pu胶水,然后放入鞋中底成型的下方母模内,放到立式蒸汽模压成型机内,该成型机的模具是上下开合;调节模缝至12mm,并开启设备,将tpu发泡颗粒吸入模具内部,并填充满整个模具,合模后向模具内通入蒸汽,模具内温度为100-130℃;随后开始二次合模,再次通过蒸汽穿透,高温蒸汽将颗粒表面进行微溶并粘合在一起,tpu发泡颗粒之间相互挤压,空隙被填充,同时大底上涂的胶水溶化,与tpu颗粒粘合在一起,中底与大底紧密贴合,蒸汽穿透的蒸汽压力设置为0.2mpa,蒸汽穿透时间为30s;然后自然冷却至40-50℃,之后进行水冷定型,水冷时间设置为100s,开模,得到最终的成型制品。性能评估1、耐折性能评估将上述各个实施例的成型后的制品按照gb/t3903.1进行耐折性能的测试。经测试,各个实施例的耐折均>200000次,无裂纹,且鞋中底与鞋大底之间结合良好,无开裂。2、鞋底结合强度评估将上述各个实施例的制品,按照gb/t532进行检测,在制品上截取大底与中底结合段作为试样,每个试样截取相同尺寸,宽度为25±0.5mm,夹持大底和中底的各一侧后向相反的方向分离,用剥离法测定粘合界面分离所需的力。上述性能测试的结果如下表所示:实施例耐折次数有无开裂粘合强度实施例1>200000无41.9n/cm实施例2>200000无40.5n/cm实施例3>200000无39n/cm实施例4>200000无44.2n/cm通过一体成型的工艺制得的成品的鞋大底贴合强度均不低于39n/cm。通过上述结果,本发明的工艺,相对人工手动涂胶的方式,厚度相对于传统方式(涂胶厚度大于0.5mm)有所减小,提高了环保性,采用鞋子中底与鞋子大底一体成型的工艺,加工效率高,产品具有高的耐折性能和较强的粘合强度。以上详细描述了本发明的较佳具体实施例。应当理解,本领域的普通技术人员无需创造性劳动就可以根据本发明的构思作出诸多修改和变化。因此,凡本
技术领域:
中技术人员依本发明的构思在现有技术的基础上通过逻辑分析、推理或者有限的实验可以得到的技术方案,皆应在由权利要求书所确定的保护范围内。当前第1页12