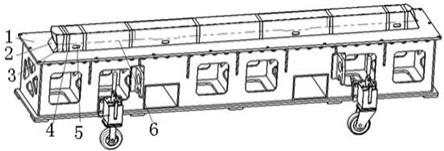
[0001]
本发明涉及一种一侧有负角度的复合材料细长盒型梁的成型模具,属于热压罐成型技术领域。
背景技术:[0002]
复合材料作为一种先进的材料,因其高的比强度、比模量,优良的抗疲劳性能、抗化学腐蚀性能、低膨胀性能等被广泛应用于航空、航天及民生方面。飞机上梁作为主要的承力结构之一,其结构形式有]字形梁、j形梁、工字梁、盒型梁等。梁等零件是飞机大部件的内部构件,在完成梁等构件后存在与飞机其它零件的胶接工序,因此在制造过程中需严格控制梁的形状变化。模具对复合材料构件制造的重要性是不言而喻的。因此复合材料构件的模具从选材到结构设计都必须针对不同对象做出具体的组合。一种盒型梁长度约2600mm,宽约162mm,高约72mm,属于典型的长跨度的细长盒型梁,并且在盒型梁的一侧型面存在较大的负角度(见图1和图2)。根据梁的构造和精度要求,盒型梁成型模具设计存在一定的复杂性和加工难度,细长盒型梁在成型过程中,型面较易发生变形,影响梁表面质量和装配精度。在成型此类细长盒型梁时,要合理地设计模具结构,不仅要考虑梁成型过程中的变形情况及受热受压传递均匀与否,还要注意梁成型完之后是否容易从模具中取出。
技术实现要素:[0003]
本发明的目的是解决现有技术中存在的问题,提供一种能降低模具制造难度,同时又能保证模具精度、提高生产效率的一侧有负角度的复合材料细长盒型梁的成型模具。
[0004]
为了实现上述目的,本发明采用如下技术方案:一种一侧有负角度的复合材料细长盒型梁的成型模具,所述成型模具包括梁成型模具、梁均压板成型模具,梁成型模具的贴模面为盒型梁的内型面,用于成型盒型梁,梁均压板成型模具的贴模面为盒型梁的外型面,用于成型盒型梁的均压板;梁成型模具包括凸模ⅰ、凸模ⅱ和底部支撑,凸模ⅰ、凸模ⅱ的分型面与底部支撑垂直,底部支撑作为盒型梁成型的底面,凸模ⅰ、凸模ⅱ定位在底部支撑上,且与底部支撑分体制造。
[0005]
优选的,凸模ⅱ靠近负角度一侧,在其底部开设有凹槽,在底部支撑上固定有凸型定位块,凹槽与凸型定位块适配并与之接触定位。
[0006]
优选的,在凸模ⅱ的一侧设置楔形块,用于定位凸模ⅱ的侧面。
[0007]
优选的,在凸模ⅰ内部设置有若干减轻槽,减轻槽沿凸模ⅰ主体的长度方向均匀分布,其开口朝向底部支撑。
[0008]
优选的,在相邻减轻槽间的连接筋板上开设有通风槽。
[0009]
优选的,凸模ⅰ远离负角度一侧,在其主体上沿其长度方向设置有零件边缘线,作为盒型梁的边缘基准线。
[0010]
优选的,在零件边缘线的下方开设有若干让开槽,让开槽沿凸模ⅰ主体的长度方向均匀分布。
[0011]
优选的,底部支撑为框架结构。
[0012]
优选的,梁成型模具和梁均压板成型模具的主体结构一致。
[0013]
提供两套模具用于成型一侧有负角度的复合材料细长盒型梁,两套模具分别是梁成型模具和梁均压板成型模具。均压板顾名思义就是把材质压制均匀,梁均压板成型模具用于成型梁的均压板,成型面取的是梁的外型面,用于制成等厚约12mm的玻璃钢材质的均压板;梁成型模具用于成型盒型梁,把成型好的均压板放置在梁的表面,用于控制梁的表面质量及厚度。梁均压板成型模具和梁成型模具的主体结构一致,梁均压板成型模具的贴模面是梁的外型面,梁成型模具的贴模面是梁的内型面。
[0014]
与现有技术相比,本发明具有如下优点:1、凸模与框架结构采用分体制造,再焊接的方法,既保证了模具精度又降低了模具制造难度,提高了生产效率;2、凸模一分为二,再采用凸型定位块定位的方式,解决了盒型梁负角度难定位、难成型的问题;3、凸模ⅰ上开有让开槽,方便车间工人把盒型梁从模具上取出;4、凸模ⅰ上开有减轻槽和通风槽,保证了模具在成型过程中,空气流通,受热受压均匀,也减轻了模具重量,保证了凸模的质量;5、盒型梁的表面质量和厚度均得到了有效控制,提高了盒型梁的成型合格率。
附图说明
[0015]
图1为本发明实施例中盒型梁的等轴视图1;图2为本发明实施例中盒型梁的等轴视图2;图3为本发明实施例的等轴视图;图4为本发明实施例的等轴视图(不含楔形块);图5为本发明实施例中框架和凸型定位块的等轴视图;图6为本发明实施例中凸模ⅱ和凸型定位块的等轴视图;图7为本发明实施例中凸模ⅱ的等轴视图;图8为本发明实施例中凸模ⅰ的等轴视图;图9为本发明实施例中凸模ⅰ上的通风槽的等轴视图;图10为均压板放置在梁成型模具的简图;图中,1、框架;2、楔形块;3、凸模ⅱ;4、凸模ⅰ; 5、让开槽;6、零件边缘线;7、凸型定位块;8、减轻槽;9、通风槽。
具体实施方式
[0016]
下面结合附图1-9对本发明的技术方案进行清楚、完整地描述,本领域普通技术人员应该理解的是,所描述的实施例是本发明的一部分实施例,而不是全部的实施例。在本发明的实施例的基础上,在没有做出创造性劳动前提下所获得的所有其他实施例,都属于本发明保护的范围。
[0017]
一种一侧有负角度的复合材料细长盒型梁的成型模具,提供两套模具用于成型一侧有负角度的复合材料细长盒型梁,两套模具分别是梁成型模具和梁均压板成型模具。均
压板顾名思义就是把材质压制均匀,梁均压板成型模具用于成型梁的均压板,成型面取的是梁的外型面,用于制成等厚约12mm的玻璃钢材质的均压板。梁成型模具用于成型盒型梁,把成型好的均压板放置梁的表面(如图10所示,从里至外依次是梁成型模具、铺贴的梁、均压板),用于控制梁的表面质量及厚度。梁均压板模具和梁成型模具的主体结构一致,唯一的差别就是梁均压板模具的贴模面是梁的外型面,梁成型模具的贴模面是梁的内型面(贴膜面也就是接下来要提到的凸模ⅰ和凸模ⅱ的成型型面)。因此,接下来,以梁成型模具为例来说明模具的结构。
[0018]
如图1-4所示,用于成型一侧有负角度的复合材料细长盒型梁的梁成型模具主要由框架1、凸模ⅰ4、凸模ⅱ3、楔形块2、凸型定位块7组成。由于盒型梁的尺寸跨度大(如图1-2所示),为了让盒型梁在成型过程中受热受压快速均匀,故采用框架式结构。盒型梁成型采用凸模的形式,为了方便车间制造,凸模与框架1采用分体制造,再焊接的方法,既保证了模具精度又降低了模具制造难度,提高了生产效率。由于梁的一端头有负角度,故凸模一分为二:凸模ⅰ4、凸模ⅱ3,凸模ⅰ4、凸模ⅱ3的分型面保证和模具底面(框架1)垂直。
[0019]
如图5-7所示,凸型定位块7焊接在框架1上定位,凸模ⅱ3上开有凹槽,凹槽与凸型定位块7适配,凸模ⅱ3通过凸型定位块7接触定位,a面和b面分别定位住凸模ⅱ3和凸型定位块7的两个面,再采用楔形块2定位凸模ⅱ3的侧面,凸模ⅱ3的另一面(c面)与凸模ⅰ4(c面)接触定位,这样就完全定位住凸模ⅱ3。
[0020]
如图8-9所示,凸模ⅰ4上设有让开槽5、零件边缘线6、减轻槽8、通风槽9,零件边缘线6设置在凸模ⅰ主体上且沿其长度方向延伸,作为盒型梁铺贴的梁的边缘基准线;为了方便车间工人把盒型梁从模具上取出,在零件边缘线6的下方开设让开槽5,让开槽5为腰形槽,沿凸模ⅰ主体的长度方向均匀分布;由于盒型梁的尺寸跨度大,为了让盒型梁在成型过程中受热受压快速均匀,也为了减轻模具的重量,故在凸模ⅰ4上均匀开有减轻槽8,减轻槽8沿凸模ⅰ主体的长度方向均匀分布,其开口朝向框架1;由于模具受热受压,在盒型梁成型时,模具会膨胀,为保证凸模ⅰ4的质量,故在凸模ⅰ4上均匀开有通风槽9,通风槽9开设在相邻减轻槽8间的连接筋板上,且位于减轻槽8与框架1接触的底端,从而保证成型时空气的流通。
[0021]
细长盒型梁的成型方法:首先在梁均压板上成型均压板,梁均压板从模具中取出时,把2#楔形块从4#凸模ⅰ旁移走,取出梁均压板的同时把3#凸模ⅱ一起取出,这样就能安全有效地把梁均压板从模具上取出。在梁成型模模具上,在凸模ⅰ和凸模ⅱ上铺贴好要成型的梁,如图10所示,把均压板放置在铺贴好的梁的表面,用于控制梁的表面质量及厚度,和梁成型模具一起进热压罐成型。在盒型梁成型好之后,盒型梁从模具上取出时,把2#楔形块从4#凸模ⅰ旁移走,取出盒型梁的同时把3#凸模ⅱ一起取出,这样就能安全有效地把盒型梁从模具上取出。
[0022]
本成型模具的工作环境为真空压力:不小于0.096mpa,0.8mpa外压,200
°
c温度,保温3h即实现产品成型。