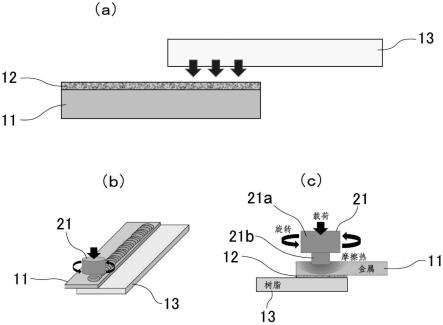
1.本发明涉及复合构件的制造方法及复合构件。
背景技术:2.作为将金属与树脂焊接的方法,近年来,对使树脂熔融并使其与金属表面进行熔接的直接焊接方法进行了大力研究(例如,参照非专利文献1)。作为这种直接焊接方法,例如提出了如下方法:在金属表面上通过化学蚀刻处理形成微细的孔蚀或通过激光照射形成凹凸图案之后,利用热压或注射成型对该微细结构填充熔融树脂,并使树脂冷却、固化,由此制造利用锚固效应牢固焊接的复合构件(例如,参照专利文献1、非专利文献2~4)。现有技术文献非专利文献
3.非专利文献1:堀内伸,“樹脂-金属異種材料複合体接合特性
の
評価試験方法
の
国際基準”,制御
と
計測,2015年,54,p.743-747非专利文献2:瀬戸雅宏、朝見芳弘、板倉雅彦、田中宏明、山部昌,“樹脂-金属接合射出成形品
の
接合強
さに
与
える
成形条件
の
影響”,成形加工,2015年,27,p.68-74非专利文献3:堀内伸、花田剛、宮前孝行、山中忠衛、大隅光悟朗、安藤直樹、成富正徳,
“エネルギーフィルター
透過型電子顕微鏡法
による
金属/樹脂接合界面
の
解析”,日本接着学会誌,2012年,48,p.322-330非专利文献4:b.henriques,“laser surface structuring of ti6al4vsubstrates for adhesion enhancement in ti6al4v-peek joints”,materials science and engineering:c,2017,79,p.177-184专利文献
4.专利文献1:日本特开2019-177704号公报
技术实现要素:本发明要解决的技术问题
5.然而,对于专利文献1及非专利文献2~4中记载的基于直接焊接的复合构件的制造方法,在利用了激光照射的情况下,存在以下技术问题:在与通过激光照射所形成的孔垂直的方向上的牵引较弱,树脂容易发生剥离。并且还存在以下技术问题:控制激光照射时所涉及的参数的数量较多,制造工序繁琐,装置价格也较高。此外,在利用了化学蚀刻处理的情况下,存在以下技术问题:在浸渍于腐蚀溶液中时,需要多次循环重复金属表面的清洗及脱脂等预清洁,并且还需要使用化学溶液进行清洗处理及废液处理,因此制造效率较差。
6.本发明着眼于上述技术问题,本发明的目的在于提供一种能够以低廉的价格高效地制造焊接强度高的复合构件的复合构件的制造方法及复合构件。解决技术问题的技术手段
7.为了实现上述目的,本发明的复合构件的制造方法的特征在于,通过在将含树脂
构件按压在形成于金属构件表面的金属制多孔膜上的状态下,对所述金属构件进行加热,将所述金属构件与所述含树脂构件焊接。
8.本发明的复合构件的特征在于,其具有金属构件、形成于所述金属构件表面的多孔膜、及设置在所述多孔膜的与所述金属构件相反一侧的含树脂构件,通过使所述含树脂构件的一部分进入所述多孔膜的孔隙中,将所述金属构件与所述含树脂构件焊接。
9.本发明的复合构件的制造方法能够适合制造本发明的复合构件。本发明的复合构件的制造方法能够通过加热金属构件,使含树脂构件熔融或软化,进而使其进入多孔膜的孔隙中。此时,由于多孔膜的孔隙不像通过激光照射所形成的孔那样朝向一个方向,含树脂构件不易发生剥离,能够制造焊接强度高的复合构件。
10.本发明的复合构件的制造方法可以利用任意方法形成多孔膜,但特别优选通过冷喷涂法使金属粉末撞击所述金属构件的表面,从而形成所述多孔膜。通过利用冷喷涂法,能够在几乎不存在原料金属粉末的氧化及分解而使金属粉末彼此良好地焊接的状态下,形成含有大量气孔的多孔膜。通过利用冷喷涂法形成多孔膜,无需如利用激光照射时的高价装置,能够以低廉的价格制造复合构件。此外,通过冷喷涂法,能够在短时间内对广范围的面形成多孔膜,且无需如利用化学蚀刻处理时那样进行清洗处理或废液处理等,因此能够在短时间内高效地制造复合构件。
11.在本发明的复合构件的制造方法及复合构件中,所述金属构件与所述多孔膜可以由相同的金属构成,也可以由不同的金属构成。金属构件可以由任意金属构成,例如可以由铝或铝合金构成。多孔膜可以由铝、铝合金、不锈钢、钛、钛合金等任意金属构成,但若通过冷喷涂法形成,则优选由钛或钛合金构成。此时,能够将钛粉或钛合金用作金属粉末,形成牢固的多孔膜。
12.本发明的复合构件的制造方法可以在使所述含树脂构件与所述多孔膜接触的状态下,将所述金属构件朝向所述含树脂构件进行按压,并同时摩擦所述金属构件,从而对所述金属构件进行加热。此时,例如利用摩擦搅拌焊接(fsw),自与多孔膜相反一侧,一边旋转一边按压紧贴金属构件表面的圆柱状焊接工具,由此能够将金属构件与含树脂构件焊接。
13.在本发明的复合构件的制造方法及复合构件中,所述含树脂构件可以根据所要求的特性或用途由任意材料构成,例如可以具有热塑性树脂材料或加热固化前的热固性树脂材料。此外,含树脂构件可以仅由树脂构成,也可以一部分为树脂。当含树脂构件具有热塑性树脂材料时,优选以低于该热塑性树脂材料的熔点的温度对金属构件进行加热。此时,能够不使含树脂构件熔融而进行焊接,能够比较容易地制造复合构件。此外,作为热塑性树脂材料,例如为强度较高的peek(聚醚醚酮)或pa6(聚酰胺6)等。当含树脂构件具有加热固化前的热固性树脂材料时,优选以高于该热固性树脂材料的熔点的温度对金属构件进行加热。此时,含树脂构件例如可以由预浸料等具有纤维状的增强材料与树脂的热固性构件构成。
14.在本发明的复合构件的制造方法及复合构件中,所述多孔膜的孔隙率优选为4%以上,优选为30%以下。此外,所述多孔膜的膜厚优选为25μm以上,优选为280μm以下。在上述情况下,金属构件与含树脂构件的焊接部的强度高,已焊接的金属构件与含树脂构件不易分离。进一步,多孔膜的孔隙率优选为6%以上,进一步优选为27%以下。此外,多孔膜的膜厚优选为35μm以上,优选为150μm以下。在上述情况下,由于多孔膜的强度进一步增高,已
焊接的金属构件与含树脂构件特别不易分离。发明效果
15.根据本发明,能够提供一种能够以低廉的价格高效地制造焊接强度高的复合构件的复合构件的制造方法及复合构件。
附图说明
16.图1中的(a)为示出本发明的实施方案的复合构件的制造方法中的、按压含树脂构件,利用加热器等加热金属构件,从而将金属构件与含树脂构件焊接的方法的侧面图;图1中的(b)为示出本发明的实施方案的复合构件的制造方法中的、利用摩擦搅拌焊接(fsw),通过摩擦热加热金属构件,从而将金属构件与含树脂构件焊接的方法的立体图;图1中的(c)为(b)的焊接方法的侧面图。图2为示出通过本发明的实施方案的复合构件的制造方法制造的复合构件的、形成多孔膜时所使用的各金属粉末及各多孔膜成膜条件下的、焊接界面附近的剖面的光学显微镜照片(左图);多孔膜的孔隙率(porosity);浸入有含树脂构件的孔隙率(filled by peek);及含树脂构件的浸入率(filling rate)(右图)。图3为示出通过本发明的实施方案的复合构件的制造方法制造的复合构件的、形成多孔膜时所使用的各金属粉末及各多孔膜成膜条件下的、焊接界面附近的剖面的光学显微镜照片(左图);多孔膜的孔隙率(porosity);浸入有含树脂构件的孔隙率(filled by peek);及含树脂构件的浸入率(filling rate)(右图)。图4为示出通过本发明的实施方案的复合构件的制造方法制造的复合构件的、形成多孔膜时所使用的各金属粉末及各多孔膜成膜条件下的、焊接界面附近的剖面的光学显微镜照片(左图);多孔膜的孔隙率(porosity);浸入有含树脂构件的孔隙率(filled by peek);及含树脂构件的浸入率(filling rate)(右图)。图5为本发明的实施方案的复合构件的制造方法的比较例的、未形成多孔膜而仅通过喷砂处理进行了制造的复合构件的焊接界面附近的剖面的光学显微镜照片,其中,(a)为喷砂处理中所使用的氧化铝颗粒为#24时的光学显微镜照片;(b)为喷砂处理中所使用的氧化铝颗粒为#60的光学显微镜照片;(c)为喷砂处理中所使用的氧化铝颗粒为#120时的光学显微镜照片。图6为示出通过本发明的实施方案的复合构件的制造方法制造的复合构件的、多孔膜的孔隙率与拉伸剪切强度的关系的图表。图7为通过本发明的实施方案的复合构件的制造方法制造的复合构件的、形成多孔膜时的各横移速度(ts)及有无喷砂处理时的焊接界面附近的剖面的光学显微镜照片及多孔膜的膜厚。图8为示出图7中所示的复合构件的多孔膜的膜厚与拉伸剪切强度的关系的图表。图9为示出通过本发明的实施方案的复合构件的制造方法制造的、多孔膜的孔隙率大于图7所示的复合构件的复合构件的多孔膜的膜厚与拉伸剪切强度的关系的图表。图10为本发明的实施方案的复合构件的制造方法的比较例的、未形成多孔膜且通过热压对金属构件表面填充熔融树脂而制造的复合构件的、焊接界面附近的剖面的光学显微镜照片,其中,(a)为金属构件为进行了喷砂处理的金属构件时的光学显微镜照片;(b)为
金属构件为通过激光照射以40%的面积率形成了细孔的金属构件时的光学显微镜照片;(c)为金属构件为通过激光照射以70%的面积率形成了细孔的金属构件时的光学显微镜照片。图11中的(a)为涉及本发明的实施方案的复合构件的制造方法的、示出用于研究多孔膜的强度的拉伸试验的试验方法的立体图;图11中的(b)为涉及本发明的实施方案的复合构件的制造方法的、用于该拉伸试验的所形成的多孔膜的剖面的光学显微镜照片。图12为示出通过图11中的(a)所示的拉伸试验得到的、多孔膜的厚度与拉伸强度的关系的图表。图13中的(a)为涉及本发明的实施方案的复合构件的制造方法的、在冷喷涂法中喷射金属粉末时的压缩气体的气体压力为312kpa时的多孔膜的孔隙率的分布;图13中的(b)为(a)的多孔膜的剖面的扫描式电子显微镜照片;图13中的(c)为涉及本发明的实施方案的复合构件的制造方法的、在冷喷涂法中喷射金属粉末时的压缩气体的气体压力为483kpa时的多孔膜的孔隙率的分布;图13中的(d)为(c)的多孔膜的剖面的扫描式电子显微镜照片;图13中的(e)为涉及本发明的实施方案的复合构件的制造方法的、在冷喷涂法中喷射金属粉末时的压缩气体的气体压力为620kpa时的多孔膜的孔隙率的分布;图13中的(f)为(e)的多孔膜的剖面的扫描式电子显微镜照片。图14为示出通过图11中的(a)所示的拉伸试验得到的、在冷喷涂法中喷射金属粉末时的压缩气体的气体压力与多孔膜的拉伸强度的关系的图表。
具体实施方式
17.以下,基于附图及实施例等对本发明的实施方案进行说明。图1~图14示出本发明的实施方案的复合构件的制造方法及复合构件。如图1所示,在本发明的实施方案的复合构件的制造方法中,首先,在金属构件11的表面形成金属制多孔膜12。此时,可以通过任意方法形成多孔膜12,但在图1所示的一个具体实例中,通过冷喷涂法使金属粉末撞击金属构件11的表面,从而形成多孔膜12。金属构件11优选为板状,并在一侧表面形成多孔膜12。
18.金属构件11与多孔膜12可以由相同的金属构成,也可以由不同的金属构成。金属构件11可以由任意金属构成,例如由铝或铝合金构成。多孔膜12可以由任意金属构成。例如,可以将钛粉或钛合金粉末用作金属粉末,并通过冷喷涂法形成由钛或钛合金构成的牢固的多孔膜12。
19.在形成多孔膜12之后,在按压含树脂构件13的状态下,加热金属构件11,由此将金属构件11与含树脂构件13焊接。此时,含树脂构件13可以根据所要求的特性或用途由任意材料构成。此外,含树脂构件13可以仅由树脂构成,也可以一部分为树脂。含树脂构件13例如可以由强度较高的peek(聚醚醚酮)或pa6(聚酰胺6)等热塑性树脂材料构成,也可以由预浸料等具有纤维状的增强材料与树脂的热固性构件构成。
20.加热金属构件11的方法可以为任意方法,例如可以为如下方法:如图1中的(a)所示,在按压含树脂构件13的状态下,利用加热器等加热金属构件11的方法;如图1中的(b)及(c)所示,在使含树脂构件13与多孔膜12接触的状态下,利用摩擦搅拌焊接(fsw),一边旋转一边按压紧贴金属构件11的与多孔膜12相反一侧的表面的圆柱状焊接工具21,通过摩擦热
加热金属构件11的方法。另外,摩擦搅拌焊接的焊接工具21通常形成为在圆柱形状的肩部21a的中央部具有突出的探针21b的形状,但优选包含突出量极小的探针21b,以抑制金属构件11的变形而使焊接界面尽可能地平坦。
21.通过以上述方式加热金属构件11,能够使含树脂构件13熔融或软化,进而使其进入多孔膜12的孔隙中。由此,能够制造将金属构件11与含树脂构件13焊接而成的本发明的实施方案的复合构件。另外,在加热金属构件11时,当含树脂构件13含有热塑性树脂材料时,通过以低于含树脂构件13的熔点的温度进行加热,能够不使含树脂构件13熔融而进行焊接,能够比较容易地制造复合构件。
22.根据本发明的实施方案的复合构件的制造方法,通过利用冷喷涂法,能够在几乎不存在原料金属粉末的氧化及分解而使金属粉末彼此良好地焊接的状态下,形成含有大量气孔的多孔膜12。由于多孔膜12的孔隙不像通过激光照射所形成的孔那样朝向一个方向,含树脂构件13不容易发生剥离,能够制造焊接强度高的复合构件。
23.此外,通过利用冷喷涂法形成多孔膜12,无需如利用激光照射时的高价装置,能够以低廉的价格制造复合构件。此外,通过冷喷涂法,能够在短时间内对广范围的面形成多孔膜12,且无需如利用化学蚀刻处理时那样进行清洗处理或废液处理等,因此能够在短时间内高效地制造复合构件。实施例
24.实施例1通过图1中的(b)及(c)所示的本发明的实施方案的复合构件的制造方法,在利用冷喷涂法形成多孔膜12之后,利用摩擦搅拌焊接(fsw),将金属构件11与含树脂构件13焊接。将a5052铝合金的压延材料用作金属构件11。金属构件11为矩形板状,其长边方向为压延方向,其长度为200mm,宽度为50mm,厚度为5mm。此外,以0.3mpa的压力对金属构件11的一侧表面(焊接面)喷射氧化铝粉(粒径为侧表面(焊接面)喷射氧化铝粉(粒径为),从而进行表面粗糙化处理。将作为热塑性树脂材料的peek用作含树脂构件13。含树脂构件13为矩形板状,其长度为200mm,宽度为50mm,厚度为5mm。
25.通过冷喷涂法形成多孔膜12时,使用低压型冷喷涂装置(inovati公司制造的“km-cds 3.0”)。在冷喷涂法中,使用表1所示的金属粉末。表1中还针对各金属粉末示出了成膜条件[有无预处理(blast(喷砂))、粉末的供给速度(powder feed rate)、压缩气体的压力(gas pressure)、工艺气体的温度(gas temp.)、喷雾喷嘴的横移速度(traverse speed)]。
[0026]
[表1]
[0027]
另外,作为预处理,对表面粗糙化处理后的金属构件11的焊接面进行使用了氧化铝颗粒(#24)的喷砂(blast)处理。此外,作为工艺气体,使用氦气。此外,为了控制多孔膜12的孔隙率与厚度,将横移速度变更为如表1所示。此外,为了提高金属构件11与多孔膜12的密合力,有时会进行成膜后的热处理。热处理使用马弗炉并在大气气氛下进行。在使用al粉的情况下,热处理温度为500℃,保持时间为30分钟,在使用ti-20、ti-45、ti-20+ti-45、ti-20+al2o3粉末的情况下,热处理温度为600℃,保持时间为4小时(仅在使用ti-20的情况下,部分为600℃、2小时或14小时),但均为空气冷却。
[0028]
进行金属构件11与含树脂构件13的焊接时,使用高刚性摩擦搅拌焊接装置(nitto seiki co.,ltd.制造的“tu-01”)。将金属构件11与含树脂构件13的重叠宽度设为20mm,作为焊接工具21,使用skd61制的焊接工具。焊接工具21形成为在工具直径为15mm的圆柱状的肩部21a的中心部突出有1.4mm的直径为5mm的探针21b的形状。将焊接时的焊接工具21的焊接速度设为10.0mm/s,将焊接工具21的转速设为1200rpm,将焊接工具21对金属构件11的插入深度设为1.1mm,将焊接工具21的前进角设为3
°
。
[0029]
使用表1所示的各金属粉末形成多孔膜12,针对各金属粉末及各多孔膜12的成膜条件,将使金属构件11(al合金)与含树脂构件(peek)13焊接而制造的复合构件的、焊接界面附近的剖面的光学显微镜照片,示于图2~4的左图。另外,以“ht”表示在多孔膜12成膜后进行了热处理。此外,以“bl(blast less(未喷砂))”表示在多孔膜12成膜前未进行喷砂处理。
[0030]
利用点计数法,根据各光学显微镜照片测定各多孔膜12的孔隙率(porosity)、浸入有含树脂构件13的孔隙率(filled by peek),由各孔隙率计算出含树脂构件13的浸入率(filling rate)。将该结果分别示于图2~4的右图。各图的横轴为多孔膜12的距含树脂构件13侧表面的深度的比率,0%为多孔膜12与含树脂构件13的界面,100%为多孔膜12与金属构件11的界面。此外,根据各光学显微镜照片求出各多孔膜12的厚度及孔隙率的平均值并示于表2。
[0031]
[表2]
[0032]
如图2~4及表2所示,含树脂构件13以一定程度浸入存在于多孔膜12内部的孔隙中,即使对于例如sus316l这种孔隙率较小的多孔膜12,也确认到含树脂构件13的浸入。此外,确认到该浸入率随着多孔膜12的距含树脂构件13侧表面的距离的增大而逐渐减小。由此认为,对于含树脂构件13的浸入深度而言,存在一定的极限。
[0033]
另外,为了进行比较,将a5052铝合金的压延材料(无表面粗糙化处理、无预处理)用作金属构件11,且不形成多孔膜12,并通过摩擦搅拌焊接将金属构件11与含树脂构件(peek)13焊接。其结果,确认到含树脂构件13在焊接后立刻从金属构件11上剥离,几乎无法焊接。
[0034]
进一步,为了进行比较,将使用氧化铝颗粒(#24、#60、#120)对a5052铝合金的压延材料的表面进行了喷砂处理而成的构件用作金属构件11,且不形成多孔膜12,并通过摩擦搅拌焊接将金属构件11与含树脂构件(peek)13焊接,从而制造复合构件。将该复合构件的焊接界面附近的剖面的光学显微镜照片示于图5。如图5所示,含树脂构件13浸入通过喷砂处理所形成的金属构件11表面的微细凹凸结构的内部,确认到金属构件11与含树脂构件13无缝隙地紧密贴合。
[0035]
接着,对所制造的各复合构件进行拉伸剪切试验。该试验使用万能试验机(instron制造)并在室温下以1.0mm/分钟的十字头速度(crosshead speed)而实施。该试验中,使用由各复合构件切出的宽度为20~25mm的短条状的试验片,该试验片通过沿垂直于焊接方向的方向对复合构件进行裁切而获得。此外,由各复合材料切出3个试验片,并分别进行拉伸剪切试验,用所得到的各断裂载荷除以焊接面积,并对由此计算出的值取平均,将该平均值作为各复合材料的拉伸剪切强度。将求出的各复合材料的拉伸剪切强度示于表3。
[0036]
[表3]
[0037]
此外,为了进行比较,以相同的方式对图5所示的不具有多孔膜12的复合构件也进行拉伸剪切试验。其结果,拉伸剪切强度为7.9~8.7mpa,并确认到随着金属构件11的表面变得平滑,强度下降。如表3所示,具有多孔膜12的复合构件的拉伸剪切强度为9.62~15.8mpa,确认到其强度高于不具有多孔膜12的复合构件。
[0038]
此外,对拉伸剪切试验后的断裂面进行观察,确认到使用al、ti-20、ti-45、ti-20+ti-45、ti-20+al2o3各粉末形成多孔膜12的复合构件,在金属构件11与多孔膜12的界面处发生了断裂。此外,还确认到使用ti-45粉末并进行了热处理的复合构件,在多孔膜12中发生
了断裂。此外,还确认到使用除ti-45粉末以外的粉末并进行了热处理的复合构件及使用了sus316l粉末的复合构件,在多孔膜12与含树脂构件13的界面处发生了断裂。
[0039]
在进行拉伸剪切试验时,对于在多孔膜12与含树脂构件13的界面处发生了断裂的复合构件,求出多孔膜12的孔隙率与拉伸剪切强度的关系,并将其示于图6。如图6所示,确认到随着孔隙率的增大,拉伸剪切强度逐渐增大。此外,还确认到即使孔隙率为6.8%左右,仍具有12mpa左右的拉伸剪切强度,具有充分高的强度。
[0040]
接着,为了测定多孔膜12的膜厚与强度的关系,对使用ti-20粉末以各种横移速度(travers speed;ts)形成多孔膜12并在成膜后进行了热处理的复合构件,测定拉伸剪切强度。另外,该测定针对使用了进行了作为预处理的喷砂处理的金属构件11的复合构件、及使用了未进行喷砂处理的金属构件11的复合构件而实施。此外,通过改变横移速度来改变多孔膜12的膜厚。将进行了测定的复合构件的焊接界面附近的剖面的光学显微镜照片及多孔膜12的膜厚示于图7。此外,将多孔膜12的膜厚与拉伸剪切强度的关系示于图8。
[0041]
如图7及图8所示,虽然拉伸剪切强度随着多孔膜12的膜厚的增大而变大,但确认到其在某种程度的膜厚下以一定的强度而饱和。此外,还确认到即使多孔膜12的膜厚为38μm,仍具有12mpa以上的拉伸剪切强度,具有非常高的强度。
[0042]
为了研究多孔膜12的孔隙率的差异对多孔膜12的膜厚与强度的关系所造成的影响,以与图7及图8相同的方式,对使用ti-20+ti-45粉末以各种横移速度形成多孔膜12并在成膜后进行了热处理的复合构件,测定拉伸剪切强度。将多孔膜12的膜厚与拉伸剪切强度的关系示于图9。另外,使用ti-20+ti-45粉末所形成的多孔膜12的孔隙率大于使用了ti-20粉末的多孔膜12的孔隙率。
[0043]
如图9所示,与图8相同,确认到拉伸剪切强度随着多孔膜12的膜厚的增大而变大,但其在某种程度的膜厚下以一定的强度而饱和。然而,确认到相较于图8,其饱和强度更高,表现出饱和强度时的膜厚也更大。认为这是由于随着孔隙率增大,确保了含树脂构件13的剪切强度。
[0044]
[利用了激光照射的比较例]如非专利文献4中所记载地,通过激光照射在金属构件11的表面形成许多细孔,并通过热压对金属构件11的表面填充熔融树脂,使树脂冷却、固化,从而制造复合构件。将ti合金用作金属构件11,将peek用作树脂。此外,通过激光照射所形成的细孔的孔径约为270μm,热压的温度为300℃。将使金属构件11表面上的细孔的面积率为40%及70%时的、复合构件的焊接界面附近的剖面的光学显微镜照片,分别示于图10中的(b)及(c)。
[0045]
另外,为了进行比较,将作为金属构件11使用未进行激光照射且使用氧化铝颗粒(粒径为250μm)对表面进行了喷砂处理的金属构件而进行了制造的复合构件的焊接界面附近的剖面的光学显微镜照片,示于图10中的(a)。如图10中的(a)~(c)所示,确认到所有复合构件的树脂均浸入金属构件11表面的凹凸或细孔的内部,金属构件11与树脂无缝隙地紧密贴合。此外,如图10中的(b)及(c)所示,确认到通过激光照射所形成的细孔仅沿垂直于金属构件11表面的方向延伸。
[0046]
以与实施例1相同的方式对图10中的(a)~(c)所示的复合构件进行拉伸剪切试验。其结果,图10中的(a)所示的经过了喷砂处理的复合构件的拉伸剪切强度为11mpa,图10中的(b)所示的通过激光照射所形成的细孔的面积率为40%的复合构件的拉伸剪切强度为
25mpa,图10中的(c)所示的通过激光照射所形成的细孔的面积率为70%的复合构件的拉伸剪切强度为51mpa。将该结果与表3所示的结果进行比较可知,利用了激光照射的复合构件的拉伸剪切强度大于通过冷喷涂法形成了多孔膜12的复合构件的拉伸剪切强度。然而,如图10中的(b)及(c)所示,由于通过激光照射所形成的孔仅沿垂直于金属构件11表面的方向延伸,因此利用了激光照射的复合构件在与金属构件11表面垂直的方向上的树脂的牵引较弱,认为其在剥离方面弱于通过冷喷涂法形成了多孔膜12的复合构件。实施例2
[0047]
将a5052铝合金的压延材料用作金属构件11,将热塑性树脂材料的pa6用作含树脂构件13,通过图1中的(b)及(c)所示的本发明的实施方案的复合构件的制造方法,在利用冷喷涂法形成多孔膜12之后,利用摩擦搅拌焊接(fsw)将金属构件11与含树脂构件13焊接。在冷喷涂法中,使用ti粉。在摩擦搅拌焊接中,将焊接工具21的焊接速度设为13mm/s,将焊接工具21的转速设为1000rpm,将焊接工具21对金属构件11的插入深度设为1.0mm。其他制造条件则与实施例1相同。
[0048]
以与实施例1相同的方式对所制造的复合构件进行拉伸剪切试验。其结果,拉伸剪切强度为10mpa,确认到拉伸剪切强度高于图5所示的无多孔膜12的复合构件。另外,所制造的复合构件的多孔膜12的膜厚约为130μm。实施例3
[0049]
将a5052铝合金的压延材料用作金属构件11,将pa6用作含树脂构件13,通过图1中的(a)所示的本发明的实施方案的复合构件的制造方法,在利用冷喷涂法形成多孔膜12之后,在按压含树脂构件13的状态下,使用加热器加热金属构件11,从而将金属构件11与含树脂构件13焊接。使用手动压力机将含树脂构件13按压在金属构件11上,金属构件11的加热温度为300℃。
[0050]
以与实施例1相同的方式对所制造的复合构件进行拉伸剪切试验。其结果,拉伸剪切强度为7mpa以上。另外,所制造的复合构件的多孔膜12的膜厚约为270μm。实施例4
[0051]
为了研究多孔膜12的厚度与强度的关系,通过本发明的实施方案的复合构件的制造方法,利用冷喷涂法形成多孔膜12之后,对该多孔膜12进行拉伸试验。如图11中的(a)所示,在拉伸试验中,将a5052铝合金用作金属构件11。金属构件11为圆柱形状,其直径为25mm,长度为40mm。在冷喷涂法中,使用粒径为1~45μm的ti-45粉末,将压缩气体的压力设为620kpa,将工艺气体的温度设为427℃,将喷雾喷嘴的横移速度设为500mm/s。此外,通过改变冷喷涂法中的层叠数,形成各种厚度的多孔膜12。多孔膜12的孔隙率均为6%以上。将形成在金属构件11的一侧表面上的多孔膜12的剖面的光学显微镜照片的一个例子示于图11中的(b)。
[0052]
如图11中的(a)所示,在拉伸试验中,在所形成的各多孔膜12的表面涂布粘合剂(adhesive)31之后,粘合与金属构件11相同大小的a5052铝合金制基材32。粘合剂31使用了“3m(注册商标)scotch-weld(注册商标)dp-460off-white(3m japan ltd.)”。在用粘合剂进行粘合之后,拉伸金属构件11与基材32,求出对各多孔膜12的拉伸强度。将拉伸试验的结果示于图12。
[0053]
如图12所示,关于拉伸试验的结果,确认到当多孔膜12的厚度为150μm以下时,在
粘合剂的内部发生断裂,拉伸强度为35mpa以上。此外,确认到当多孔膜12的厚度为150μm以上时,在多孔膜12的靠近金属构件11的内部发生断裂,拉伸强度为35mpa以下。由该结果可知,通过将多孔膜12设为150μm以下,多孔膜的强度至少为35mpa以上,在制造复合构件时,已焊接的金属构件11与含树脂构件13不易分离。实施例5
[0054]
为了研究多孔膜12的孔隙率与强度的关系,以与实施例4相同的方式形成多孔膜12并进行拉伸试验。在冷喷涂法中,通过将喷射金属粉末时的压缩气体的气体压力变更为312kpa、483kpa、620kpa,形成孔隙率不同的多孔膜12。将各气体压力下的多孔膜12的距金属构件11表面的距离与孔隙率的关系、及多孔膜12的剖面的扫描式电子显微镜照片示于图13。
[0055]
如图13所示,当气体压力为312kpa时,多孔膜12的孔隙率约为4%~9%,平均为5.58%,当气体压力为483kpa时,多孔膜12的孔隙率约为8%~16%,平均为12.4%,当气体压力为620kpa时,多孔膜12的孔隙率约为6%~20%,平均为13.5%,确认到气体压力越高,则多孔膜12的孔隙率变得越高。认为这是由于当气体压力较低时,金属粉末的撞击力小,因此粒径大的颗粒未进行焊接,而仅是粒径小的金属粉末堆积并填埋颗粒之间的缝隙,但当气体压力较高时,金属粉末的撞击力变大,因此粒径大的颗粒进行焊接,在该颗粒之间容易产生缝隙。
[0056]
将对气体压力不同的各多孔膜12进行拉伸试验的结果示于图14。如图14所示,关于拉伸试验的结果,确认到当气体压力为483kpa、620kpa时,在粘合剂的内部发生断裂,拉伸强度为40mpa以上。此外,还确认到当气体压力为312kpa时,在多孔膜12的内部发生断裂,拉伸强度约为32mpa。由该结果可知,通过将气体压力设为483kpa以上,即通过将多孔膜12的孔隙率设为6%以上,将平均的孔隙率设为12%以上,多孔膜的强度至少为40mpa以上,在制造复合构件时,已焊接的金属构件11与含树脂构件13不易分离。附图标记说明
[0057]
11:金属构件;12:多孔膜;13:含树脂构件;21:焊接工具;21a:肩部;21b:探针;31:粘合剂;32:基材。