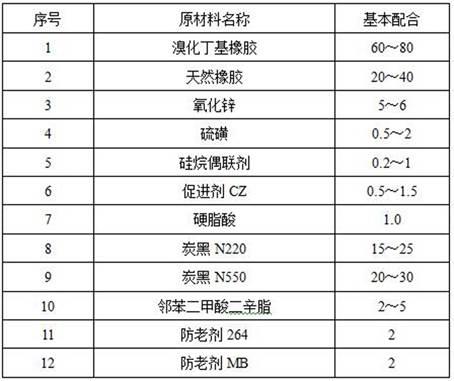
1.本发明涉及防护面具的制备技术领域,具体为一种利用溴化丁基橡胶和天然橡胶共混胶材料制备防护面具罩体的工艺方法。
背景技术:2.目前我国防毒面具开始采用溴化丁基橡胶和天然橡胶共混胶作为罩体材料,以进一步提高罩体材料的回弹性和佩戴舒适性。由于溴化丁基橡胶中的c-br键能较小,决定了溴化丁基橡胶硫化活性高、硫化速率快,导致溴化丁基橡胶贮存安全性低、易焦烧。制备的溴化丁基橡胶和天然橡胶共混胶为保证混炼的均匀性,较溴化丁基橡胶材料混炼时间长,薄通遍数多,导致共混胶存放过程中极易发生自硫,夏季储存期超过2天,防毒面具注射成型时就会出现波纹,表面不光滑。针对上述问题,共混胶料对硫化体系和注射成型工艺进行了设计,以解决溴化丁基橡胶和天然橡胶储存期短易自硫的问题。
技术实现要素:3.本发明目的是提供一种防毒面具共混胶料配方和成型工艺设计,使其能够延长溴化丁基橡胶和天然橡胶共混胶的储存期,同时对注射工艺参数进行优化后,改善共混胶的成型工艺。
4.本发明是采用如下技术方案实现的:一种利用溴化丁基橡胶和天然橡胶共混胶材料制备防护面具罩体的工艺方法,包括如下步骤:(1)、溴化丁基橡胶和天然橡胶共混胶材料的重量份组分:溴化丁基橡胶 60~80份,天然橡胶 20~40份,氧化锌 5~6份,硫磺 0.5~2份,硅烷偶联剂 0.2~1份,促进剂cz 0.5~1.5份,硬脂酸 1.0份,炭黑n220 15~25份,炭黑n550 20~30份,邻苯二甲酸二辛脂 2~5份,防老剂264 2份,防老剂mb 2份。
5.(2)胶料混炼过程混炼胶料采用xk-400mm开放式炼胶机,滚筒速比为1:1.25;橡胶混炼时前辊辊温为45℃~50℃,后辊辊温为50℃~55℃;混炼工艺如下:
①
天然橡胶塑炼,可塑度为0.42~0.52;
②
调节辊筒间距至1.0mm~1.5mm,将溴化丁基橡胶加入天然橡胶塑炼胶中,混合均匀;
③
辊距调至1.5mm~2.0mm,加入防老剂264、防老剂mb、促进剂cz以及一半硬脂酸,混合均匀;
④
辊距调至3mm~4mm加入炭黑n220、炭黑n550、邻苯二甲酸二辛脂,混炼过程中加入另一半硬脂酸;
⑤
待配合剂完全加入胶料后,每边割刀5次,将胶料混合均匀;
⑥
加入硫化剂氧化锌、硫磺和硅烷偶联剂,混炼均匀;
⑦
辊距调至1.5mm~2.0mm,前后薄通3次;
⑧
辊距调至所需厚度,出片,冷却。
6.(3)注射硫化过程
①
将胶料剪成10cm宽长条,便于胶料从进料口进入;
②
将注射机塑化油温设定为65℃,采用慢/快/慢的三段式塑化方法,塑化速度分别为50%、80%和40%,对应的压力为80bar、120bar和60bar,塑化量为210ml,使胶料通过螺杆旋转由进料口进入注射腔体内;
③
注射罩体前检查防毒面具模具有无损伤,操作顶针下,将模具内芯落下,速度为30%,压力为40bar;
④
待模具内芯落下后,采用芯入工艺,将模具的哈弗块闭合,包裹住模芯,速度为35%,压力为50bar;
⑤
采用移模入工艺,将底模由操作位移动到注射机中央,移模采用先快后慢的工艺设计,速度分别为40%和20%,压力为50bar和30bar;
⑥
采用锁模工艺,将底模由下向上与上模闭合,锁模过程采用慢/快/慢的工艺设计,速度为50%、60%和30%,压力为60bar、80bar和40bar;合模后有一个增压的过程,速度为50%,压力为100bar,增压时间4s;
⑦
此时模具完成闭合,开始注射过程,使胶料由注射腔体进入模具腔体;注射油温设定为65℃,注射过程采用慢/快/慢的三段式注射方法,速度分别为50%、80%和30%,对应的压力为60bar、110bar和100bar,使胶料在30s内完成注射,避免焦烧;
⑧
此时胶料进入硫化过程,硫化温度设定为160℃,时间为720s;硫化过程中为避免模具压力下降,开启保压工艺设计,速度为50%和50%,压力设计为100bar和120bar,使压力在硫化过程中保持在120bar,保证防毒面具的密实度;
⑨
采用后塑化工艺,时间设计为600s;
⑩
720s后胶料硫化完成后,开启模具;采用速度50%、压力140bar的参数设计先卸压,然后按照慢/快/慢的工艺过程,将底模与上模分离,速度为25%、50%和20%,压力为50bar、70bar和30bar;
⑪
采用移模出工艺,将底模由注射机中央移动到操作位,移模采用先快后慢的工艺设计,速度分别为40%和20%,压力为40bar和20bar;
⑫
待移模过程完成后,采用芯出工艺,将模具的哈弗块打开,速度为35%,压力为70bar;
⑬
待哈弗块完全打开后,操作顶针上,将模具内芯顶起,速度为30%,压力为60bar;
⑭
将硫化完成后的防毒面具由模具内芯上卸下,完成防毒面具的注射硫化过程;
⑮
然后重复
③
~
⑭
的动作过程,进行防毒面具连续硫化。
7.本发明方法的关键设计如下:一、溴化丁基橡胶常用的硫化剂包括氧化锌、硫磺、过氧化物、酚醛树脂等,天然橡胶主要采用硫磺作为硫化剂,通过对比可知硫磺是两者的共同硫化剂,但是单独采用硫磺作为溴化丁基橡胶的硫化剂,获得的混炼胶易发生硫化返原,而且性能也较差,一般采用硫磺与氧化锌共用的方式。因此该技术方案也以氧化锌和硫磺作为主硫化剂,保证共混胶硫化速度和罩体材料的力学性能。
8.优化后的橡胶配方如下:共混胶胶料配方二、以中速促进剂cz为促进体系,以硅烷偶联剂作为硫给予体替代部分硫磺参与橡胶的硫化,减缓硫化速度,延长共混胶的焦烧时间。
9.混炼时先加入防老剂、补强剂、软化剂和促进剂等辅料,加料完毕后,每边割刀5次,混炼均匀,加入氧化锌、硫磺和硅烷偶联剂,加料完毕后薄通3次,缩短混炼过程中的焦烧时间。
10.三、注射成型主要包括硫化工艺参数和注射机工艺参数的设计:(1)硫化工艺参数主要包括:温度、时间和压力。
11.a)时间和温度成反比,温度越高、时间越短,因此为提高生产效率,在满足工艺要求的情况下,尽量提高硫化温度。本发明中选用了160℃,较常规天然橡胶的140℃~150℃有显著提升;时间为12min,与溴化丁基橡胶常用的15min-18min相比,时间明显缩短。因此通过对共混胶配方的优化,有效的提升了胶料的硫化效率。
12.b)压力选用的100bar(10mpa),可以满足罩体材料的硫化压力需要,保证材料的致密性。
13.(2)注射机工艺参数的设计主要包括:塑化温度、注射温度、开模参数、锁模参数、塑化工艺以及射胶工艺等。
14.a)塑化温度和塑化工艺参数设计是胶料的重要参数之一,是胶料由螺杆进入注射腔体的过程。塑化温度低,塑化时胶料升温快,容易出现焦烧;塑化温度高,胶料也容易出现焦烧,因此本发明对塑化温度和塑化速度进行了匹配性设计。将塑化油温由50℃提高到65℃,增加胶料塑性,加快进料速度,缩短螺杆对胶料的送料时间;塑化速度分三段,分别为50%、80%和40%,对应的压力为80bar、120bar和60bar,最后由于胶料已基本塑化完毕,因此速度最小。
15.b)注射温度和注射工艺参数主要控制胶料由注射腔体进入模具腔体的过程,注射过程中胶料温度要适中,焦烧时间要大于注射时间,否则产品在合模线处会出现分层,结合强力较低。本发明选用的注射温度为65℃,注射速度分三段,分别为50%、80%和30%,对应的压力为60bar、110bar和100bar,最后由于胶料己基本注射完毕,因此速度最小。
16.c)开模参数主要是保证模具可以正常开启,所以遵循“慢-快-慢”的过程,速度为25%、50%和20%。合模参数主要是保证模具锁紧,避免注射过程中出现漏胶的问题,所以增压到100bar:锁模过程也遵循“慢-快-慢”的过程,速度为50%、60%和30%。
17.具体注射成型工艺参数如下:硫化时间:720s排气次数:0温度参数:开模参数:锁模参数:保压参数:顶针参数:行芯参数:
移模参数:排气次数:0塑化参数:塑化延时:600s射胶参数:通过该方法改进后,胶料的储存期由2天延长至10天左右,大大提高了胶料的操作工艺性能。该胶料在储存期内采用注射成型工艺硫化了防毒面具罩体,并进行了性能测试,结果如下:通过试验结果可知,该胶料经过防焦烧和注射成型工艺参数设计后,注射罩体在老化前后性能差别较小,有效延长了胶料的储存性能。
具体实施方式
18.下面对本发明的具体实施例进行详细说明。
19.一种利用溴化丁基橡胶和天然橡胶共混胶材料制备防护面具罩体的工艺方法,包括如下步骤:(1)、溴化丁基橡胶和天然橡胶共混胶材料的重量份组分:溴化丁基橡胶 60~80份,天然橡胶 20~40份,氧化锌 5~6份,硫磺 0.5~2份,硅烷偶联剂 0.2~1份,促进剂cz 0.5~1.5份,硬脂酸 1.0份,炭黑n220 15~25份,炭黑n550 20~30份,邻苯二甲酸二辛脂 2~5份,防老剂264 2份,防老剂mb 2份。
20.本发明实施例1至5采用如下配方设计:(2)胶料混炼过程混炼胶料采用xk-400mm开放式炼胶机,滚筒速比为1:1.25;橡胶混炼时前辊辊温为45℃~50℃左右,后辊辊温为50℃~55℃左右;混炼工艺如下:
①
天然橡胶塑炼,可塑度为0.42~0.52。
21.②
调节辊筒间距至1.0mm~1.5mm,将溴化丁基橡胶加入天然橡胶塑炼胶中,混合均匀。
22.③
辊距调至1.5mm~2.0mm,加入防老剂264、防老剂mb、促进剂cz以及一半硬脂酸,混合均匀。
23.④
辊距调至3mm~4mm加入炭黑n220、炭黑n550、邻苯二甲酸二辛脂,混炼过程中加入另一半硬脂酸。
24.⑤
待配合剂完全加入胶料后,每边割刀5次,将胶料混合均匀。
25.⑥
加入硫化剂氧化锌、硫磺和硅烷偶联剂,混炼均匀。
26.⑦
辊距调至1.5mm~2.0mm,前后薄通3次。
27.⑧
辊距调至所需厚度,出片,冷却。
28.对实施例1-5进行性能测试,结果如下:
(3)注射硫化过程
①
将胶料剪成10cm宽长条,便于胶料从进料口进入。
29.②
将注射机塑化油温设定为65℃,采用“慢-快-慢”的三段式塑化方法,塑化速度分别为50%、80%和40%,对应的压力为80bar、120bar和60bar,塑化量为210ml,使胶料通过螺杆旋转由进料口进入注射腔体内。
30.③
注射罩体前检查防毒面具模具有无损伤,操作顶针下,将模具内芯落下,速度为30%,压力为40bar。
31.④
待模具内芯落下后,采用芯入工艺,将模具的哈弗块闭合,包裹住模芯,速度为35%,压力为50bar。
32.⑤
采用移模入工艺,将底模(即模芯和哈弗块)由操作位移动到注射机中央,移模采用先快后慢的工艺设计,速度分别为40%和20%,压力为50bar和30bar。
33.⑥
采用锁模工艺,将底模由下向上与上模闭合,锁模过程采用“慢-快-慢”的工艺设计,速度为50%、60%和30%,压力为60bar、80bar和40bar,为保证模具锁紧,避免注射过程中出现漏胶的问题,合模后有一个增压的过程,速度为50%,压力为100bar,增压时间4s。
34.⑦
此时模具完成闭合,开始注射过程,使胶料由注射腔体进入模具腔体。注射油温设定为65℃,注射过程采用“慢-快-慢”的三段式注射方法,分别为50%、80%和30%,对应的压力为60bar、110bar和100bar,使胶料在30s内完成注射,避免焦烧。
35.⑧
此时胶料进入硫化过程,硫化温度设定为160℃,时间为720s。硫化过程中为避免模具压力下降,开启保压工艺设计,速度为50%和50%,压力设计为100bar和120bar,使压力在硫化过程中保持在120bar,保证防毒面具的密实度。
36.⑨
采用后塑化工艺,时间设计为600,主要是避免胶料在注射腔体内发生焦烧问题。
37.⑩
720s后胶料硫化完成后,开启模具。采用速度50%,压力140bar的参数设计先卸压,然后按照“慢一快-慢”的工艺过程,将底模与上模分离,速度为25%、50%和20%,压力为50bar、70baf和30bar。
38.⑪
采用移模出工艺,将底模(即横芯和哈弗块)由注射机中央移动到操作位,移模
采用先快后慢的工艺设计,速度分别为40%和20%,压力为40bar和20bar。
39.⑫
待移模过程完成后,采用芯出工艺,将模具的哈弗块打开,速度为35%,压力为70bar。
40.⑬
待哈弗块完全打开后,操作顶针上,将模具内芯顶起,速度为30%,压力为60bar。
41.⑭
将硫化完成后的防毒面具由模具内芯上卸下,完成防毒面具的注射硫化过程。
42.⑮
然后重复
③
~
⑭
的动作过程,进行防毒面具连续硫化。
43.本发明首次采用硅烷偶联剂和提高塑化温度对溴化丁基橡胶和天然橡胶共混胶的防焦烧性能和成型工艺进行设计,使其能够延长溴化丁基橡胶和天然橡胶共混胶的储存期,同时对注射工艺参数进行优化后,改善共混胶的成型工艺。
44.以上所述仅为本发明的实施例,并不因此限制本发明的专利范围,凡是利用本发明说明书内容,对本发明的技术方案进行修改或者等同替换,均同理包括在本发明的专利保护范围内。