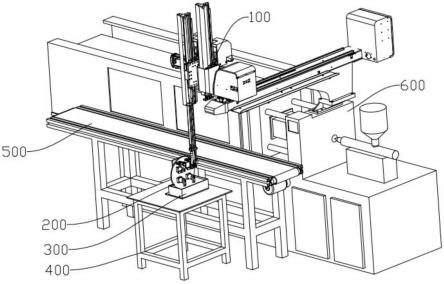
1.本实用新型涉及分丝辊支座定型技术领域,尤其是一种分丝辊支座自动化定型生产装置。
背景技术:2.现有技术中,分丝辊支座a采用注塑工艺成型,在注塑成型出模后由于内槽中没有支持结构,分丝辊支座a容易收缩变形,影响最终的产品质量。
3.为了避免分丝辊支座a注塑成型出模后的收缩变形,需要将刚出模的分丝辊支座a快速进行冷却定型。目前,一般采用人工的方式拿取出模的分丝辊支座a浸入水中进行冷却,不仅费时费力,工作效率较低,而且容易造成工人的烫伤事故,对人体造成危害。
技术实现要素:4.本技术针对上述现有生产技术中的缺点,提供一种结构合理的分丝辊支座自动化定型生产装置,能够自动实现分丝辊支座的快速冷却定型,保证了分丝辊支座的产品质量,提高了工作效率,避免对工人造成烫伤事故。
5.本实用新型所采用的技术方案如下:
6.分丝辊支座自动化定型生产装置,包括定型组件和机械手,所述定型组件一侧设置冷却水箱,所述冷却水箱内置入冷取水;所述定型组件包括旋转盘,所述旋转盘下半部设置在冷却水箱中并浸没在冷却水中,旋转盘一侧表面固定多个定型板,多个定型板分成两组对称设置在旋转盘一侧表面上下部,定型板结构和分丝辊支座的内槽结构相互吻合,所述旋转盘另一侧表面中心位置连接旋转气缸的驱动端,旋转气缸固定在安装板侧面,安装板竖直设置在固定底板上,固定底板上固定冷却水箱;所述机械手位于定型组件上方,机械手固定在注塑机上端。
7.进一步的,定型组件和冷却水箱固定在底座上。
8.进一步的,定型板侧面设置压紧气缸,压紧气缸固定在旋转盘上,压紧气缸的驱动端连接压紧板,压紧气缸能够带动压紧板将分丝辊支座压紧在定型板上。
9.进一步的,机械手包括水平设置的固定座,固定座设置在注塑机上,固定座上端面设置两个相互平行的x轴滑轨,两个x轴滑轨上共同滑动连接第一移动座,第一移动座上设置x轴驱动电机,x轴驱动电机的驱动端连接第一齿轮,固定座上端面设置x轴齿条,x轴齿条和x轴滑轨相互平行,第一齿轮和x轴齿条啮合连接,第一移动座一侧端面设置两个相互平行的y轴滑轨,y轴滑轨和x轴滑轨相互垂直,两个y轴滑轨上共同滑动连接两个第二移动座,第二移动座上设置y轴驱动电机,y轴驱动电机的驱动端连接第二齿轮,第二移动座上端面设置y轴齿条,y轴齿条和y轴滑轨相互平行,第二齿轮和y轴齿条啮合连接,第二移动座一侧设置升降架,升降架左右两侧分别设置升降滑轨,两个升降滑轨上共同滑动连接第二移动座,升降架上设置升降齿条,升降齿条和两个升降滑轨相互平行,第二移动座上固定升降驱动电机,升降驱动电机的驱动端连接升降齿轮,升降齿轮和升降齿条啮合连接,升降架上固
定抓取支座,抓取支座下端连接抓取组件。
10.进一步的,抓取组件包括翻转气缸安装座,翻转气缸安装座下部左右两侧通过销轴铰接翻转架一侧端面,翻转气缸安装座内固定翻转气缸,翻转气缸的驱动端通过销轴铰接两个联动板一端,两个联动板另一端共同通过销轴铰接翻转架另一侧端面,翻转架前端固定抓取气缸安装座,抓取气缸安装座一侧端面上并排设置两个抓取气缸。
11.进一步的,定型组件一侧设置皮带输送机,皮带输送机能够将完成定型的分丝辊支座输送下线。
12.本实用新型的有益效果如下:
13.本实用新型结构紧凑、合理,操作方便,机械手能够带动分丝辊支座从注塑机直接转移到定型工装上,旋转盘能够带动分丝辊支座轮流浸没在水中进行快速冷却定型,保证了分丝辊支座的产品质量,提高了工作效率,避免对工人造成烫伤事故。
附图说明
14.图1为本实用新型立体示意图。
15.图2为定型组件背面立体图。
16.图3为定型组件正面立体图。
17.图4为机械手第一视角立体图。
18.图5为机械手第二视角立体图。
19.图6为抓取组件第一视角立体图。
20.图7为抓取组件第二视角立体图。
21.其中:100、机械手;101、固定座;102、x轴滑轨;103、x轴齿条;104、x轴驱动电机;105、第一移动座;106、y轴齿条;107、y轴驱动电机;108、y轴滑轨;109、第二移动座;110、升降驱动电机;111、升降齿条;112、升降滑轨;113、升降架;114、抓取支座;115、翻转气缸安装座;116、翻转气缸;117、抓取气缸安装座;118、抓取气缸;119、翻转架;120、联动板;200、定型组件;201、固定底板;202、安装板;203、旋转气缸;204、旋转盘;205、定型板;206、压紧气缸;207、压紧板;300、冷却水箱;400、底座;500、皮带输送机;600、注塑机;a、分丝辊支座。
具体实施方式
22.下面结合附图,说明本实用新型的具体实施方式。
23.如图1所示的实施例中,分丝辊支座自动化定型生产装置包括定型组件200,定型组件200用于放置分丝辊支座a,定型组件200一侧设置冷却水箱300,冷却水箱300内置入冷却水,定型组件200能够将上面放置的分丝辊支座a浸没在冷却水箱300的冷却水中进行冷却定型。定型组件200和冷却水箱300固定在底座400上。
24.如图2和图3所示的实施例中,定型组件200包括旋转盘204,旋转盘204下半部设置在冷却水箱300中并浸没在冷却水中。旋转盘204一侧表面固定多个定型板205,多个定型板205分成两组对称设置在旋转盘204一侧表面上下部,定型板205结构和分丝辊支座a的内槽结构相互吻合,使得分丝辊支座a的内槽能够贴合设置在定型板205上,避免分丝辊支座a在冷却定型过程中内槽发生收缩变形。
25.如图2和图3所示的实施例中,旋转盘204另一侧表面中心位置连接旋转气缸203的
驱动端,旋转气缸203固定在安装板202侧面,安装板202竖直设置在固定底板201上,固定底板201上同时固定冷却水箱300。旋转气缸203能够带动旋转盘204转动,使得旋转盘204一侧表面设置的多个定型板205能够轮流浸没在冷却水中进行冷却定型。
26.为了避免分丝辊支座a从定型组件200上脱落,如图3所示的实施例中,定型板205侧面设置压紧气缸206,压紧气缸206固定在旋转盘204上,压紧气缸206的驱动端连接压紧板207,压紧气缸206能够带动压紧板207将分丝辊支座a压紧在定型板205上。
27.为了将分丝辊支座a从注塑机快速搬运到定型组件200上,如图1所示的实施例中,分丝辊支座自动化定型生产装置还包括机械手100,机械手100位于定型组件200上方,机械手100固定在注塑机600上端,机械手100能够抓取注塑机600内注塑成型的分丝辊支座a,并将其转移到定型组件200上进行冷却定型。
28.如图4和图5所示的实施例中,机械手100包括水平设置的固定座101,固定座101设置在注塑机600上,固定座101上端面设置两个相互平行的x轴滑轨102,两个x轴滑轨102上共同滑动连接第一移动座105,第一移动座105上设置x轴驱动电机104,x轴驱动电机104的驱动端连接第一齿轮,固定座101上端面设置x轴齿条103,x轴齿条103和x轴滑轨102相互平行。第一齿轮和x轴齿条103啮合连接。第一移动座105一侧端面设置两个相互平行的y轴滑轨108,y轴滑轨108和x轴滑轨102相互垂直。两个y轴滑轨108上共同滑动连接两个第二移动座109,第二移动座109上设置y轴驱动电机107,y轴驱动电机107的驱动端连接第二齿轮,第二移动座109上端面设置y轴齿条106,y轴齿条106和y轴滑轨108相互平行,第二齿轮和y轴齿条106啮合连接。第二移动座109一侧设置升降架113,升降架113左右两侧分别设置升降滑轨112,两个升降滑轨112上共同滑动连接第二移动座109,升降架113上设置升降齿条111,升降齿条111和两个升降滑轨112相互平行。第二移动座109上固定升降驱动电机110,升降驱动电机110的驱动端连接升降齿轮,升降齿轮和升降齿条111啮合连接。升降架113上固定抓取支座114,抓取支座114下端连接抓取组件,抓取组件能够抓取分丝辊支座a。
29.如图6和图7所示的实施例中,抓取组件包括翻转气缸安装座115,翻转气缸安装座115下部左右两侧通过销轴铰接翻转架119一侧端面。翻转气缸安装座115内固定翻转气缸116,翻转气缸116的驱动端通过销轴铰接两个联动板120一端,两个联动板120另一端共同通过销轴铰接翻转架119另一侧端面。翻转架119前端固定抓取气缸安装座117,抓取气缸安装座117一侧端面上并排设置两个抓取气缸118。在工作时,两个抓取气缸118抓取分丝辊支座a,翻转气缸116工作时能够带动翻转架119翻转90
°
,实现抓取的分丝辊支座a的位置的变化。
30.如图1所示的实施例中,定型组件200一侧设置皮带输送机500,皮带输送机500能够将完成定型的分丝辊支座a输送下线。
31.本实用新型的工作原理是:在使用时,首先由注塑机600将分丝辊支座a注塑成型,然后由机械手100抓取分丝辊支座a并将其输送到定型组件200上,定型板205结构和分丝辊支座a的内槽结构相互吻合,使得分丝辊支座a的内槽能够贴合设置在定型板205上,避免分丝辊支座a在冷却定型过程中内槽发生收缩变形。同时,压紧气缸206带动压紧板207将分丝辊支座a压紧在定型板205上。然后由旋转气缸203带动旋转盘204旋转,使得旋转盘204一侧表面设置的多个定型板205能够轮流浸没在冷却水中进行冷却定型。冷却后的分丝辊支座a再由机械手100抓取输送到皮带输送机500上,由皮带输送机500输送下线。
32.以上描述是对本实用新型的解释,不是对实用新型的限定,本实用新型所限定的范围参见权利要求,在本实用新型的保护范围之内,可以作任何形式的修改。