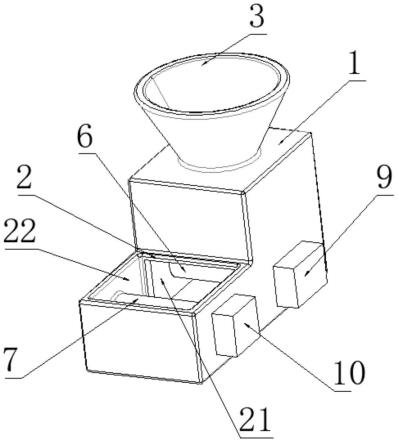
1.本实用新型涉及复合材料浸润技术领域,尤其是涉及一种用于制备柔性热塑预浸料的装置。
背景技术:2.热塑复合材料由于其低孔隙率、加工周期短、低吸水性、高抗损伤性和韧性、可室温下储存等优点使得越来越多地使用于船舶、航空航天、石油管道等工业领域。热塑织物复合材料由高性能纤维织物和热塑性树脂复合而成,可分为短纤维增强和连续纤维增强两大类。其中使用高性能纤维编织的织物预浸料可用于非常大的连续结构,例如飞机尾部升降机、襟翼和前缘等。
3.目前,利用热塑织物预浸料成型异型结构件的方式以冲压成型为主,即将片状热塑织物预浸料裁切成坯料,然后在加热器内将坯料加热软化,装入模内,快速合模加压,冷却脱模。冲压成型工艺对设备、加工条件要求较高,且由于传统的热塑织物预浸料为具有一定硬度的片材,在成型成小尺寸、多造型、高纵深的零件时存在诸多困难。柔性热塑织物预浸料是一种柔软、延展性高,有加工可塑性大、低成本、适用范围广解决当前国内的冲压成型热塑织物预浸料存在的成本高、多造型结构件成型困难等问题,此种柔性热塑预浸料,具有柔软、延展性高,有加工可塑性大、低成本、适用范围广等特点。现有颗粒物料的播撒,由于缺少均匀播撒的方法和装置。其不足之处在于:播撒出的颗粒物料易堆积成尖顶形即上小下大,导致播撒不均匀。
4.中国专利cn108099052a涉及一种连续性热塑树脂基体纤维预浸料的制备生产线,按照纤维纱的走向,所述制备生产线由碳纤维丝束扩展设备、碳纤维丝束纱筒架、导向辊、第一牵引装置、热浸装置、压延机构、喷涂机构、辊压机构、导出辊、冷却箱、第二牵引装置、预浸料厚度检测机构、收卷辊依次衔接构成;热浸装置包括热浸槽,热浸槽内部设有若干整理辊;压延机构包括一对第一热轧辊;辊压机构包括一对第二热轧辊;一对所述第二热轧辊之间的距离大于一对所述第一热轧辊之间的距离,且一对所述第二热轧辊的表面温度低于一对所述第一热轧辊表面的温度。本专利能够克服预浸料中树脂分布不均、树脂含量不好控制且含量低、强度低、制得的预浸料宽幅较小等问题。但该专利是通过热浸槽加热机构整理辊、第一热轧辊、第二热轧辊、空压机等组合结构对树脂粉末进行下料,结构较为复杂,且无法有效控制均匀下料。
5.因此,为方便控制树脂含量并使树脂颗粒均匀铺洒,解决传统热塑织物预浸料的柔软性和延展性问题,需要设计一种用于柔性热塑预浸料制备的装置。
技术实现要素:6.为了解决现有中树脂颗粒不能有效均匀铺洒的技术问题,本实用新型提供了一种用于制备柔性热塑预浸料的装置。
7.为了实现本实用新型的目的,本实用新型采用的技术方案如下:
8.一种用于制备柔性热塑预浸料的装置,包括外壳体、内壳体、料仓、筛网和辊组件;
9.所述外壳体上端设有料仓;
10.外壳体内部设有内壳体,内壳体内部设有筛网,且筛网位于料仓下端;
11.所述筛网下方设有挡板,挡板下方设有辊组件;
12.所述辊组件包括加热辊和冷却辊;所述加热辊位于挡板的正下方,且加热辊与内壳体内壁面之间还设有隔料板,隔料板一端设置在加热辊的外圆周表面,防止树脂颗粒洒出,隔料板另一端焊接在内壳体的内壁面上。
13.基于上述技术方案,更进一步地,所述内壳体内部设有第一腔体和第二腔体,第一腔体和第二腔体连通,且连通位置所在的横向水平面处安装有两个隔料板。
14.基于上述技术方案,更进一步地,所述筛网、挡板都嵌固在第一腔体内,所述加热辊放置在第一腔体内。
15.基于上述技术方案,更进一步地,所述冷却辊放置在第二腔体内。
16.基于上述技术方案,更进一步地,所述筛网上开设有若干个孔隙,且每个孔隙的孔径范围都设为0.25mm-1.5mm。
17.基于上述技术方案,更进一步地,所述筛网和挡板之间设有间隙,间隙范围为2-3cm。
18.基于上述技术方案,更进一步地,还包括加热机构,所述加热机构安装在外壳体外部,且加热机构与加热辊连接。
19.基于上述技术方案,更进一步地,还包括冷却机构,所述冷却机构安装在外壳体外部,且冷却机构与冷却辊连接。
20.基于上述技术方案,更进一步地,所述料仓顶部为喂料口,料仓内部还设有搅拌机构,搅拌机构外接驱动机构,且喂料口下端与内壳体内部连通。
21.基于上述技术方案,更进一步地,所述搅拌机构上设有若干个搅拌叶片,搅拌叶片数量设为10-15个。
22.基于上述技术方案,更进一步地,所述加热辊的加热温度为热塑性树脂融化温度,其温度范围为190℃-380℃。
23.基于上述技术方案,更进一步地,热塑性树脂包括但不限于pe、pp、pa6、pa66、pc、pps、peek、pekk。
24.基于上述技术方案,更进一步地,所述加热辊的转速为1m/min。
25.基于上述技术方案,更进一步地,所述冷却辊的冷却温度为10-25℃。
26.基于上述技术方案,更进一步地,所述冷却辊的转速为1m/min。
27.与现有技术相比,本实用新型的有益效果具体体现在:
28.(1)本实用新型通过设置料仓、筛网、挡板和辊组件的组合结构,实现了撒料、材料预热及收卷一体化,提高了生产效率;
29.(2)本实用新型可以根据需求通过电机驱动筛网进行振动,根据筛网振动频率和搅拌机构转速控制下料量,并控制树脂含量;且本实用新型可适用于各种半浸润材料,适用范围较广。
附图说明
30.图1为本实用新型用于制备柔性热塑预浸料的装置的整体结构示意图;
31.图2为本实用新型用于制备柔性热塑预浸料的装置的俯视图;
32.图3为本实用新型用于制备柔性热塑预浸料的装置的剖面图;
33.附图标记:1.外壳体;2.内壳体;21.第一腔体;22.第二腔体;3.料仓;4.筛网;5.挡板;6.加热辊;7.冷却辊;8.隔料板;9.加热机构;10.冷却机构;11.搅拌机构。
具体实施方式
34.为使本实用新型的目的和技术方案更加清楚,下面将结合实施例,对本实用新型的技术方案进行清楚、完整地描述。
35.需要说明的是,术语“中心”、“上”、“下”、“水平”、“左”、“右”、“前”、“后”、“横向”、“纵向”等指示的方位或位置关系为基于附图所示的方位或位置关系,仅是为了便于描述本实用新型和简化描述,并不是指示或暗示所指的装置或元件必须具有特定的方位、以特定的方位构造和操作,因此不能理解为对本实用新型的限制。
36.实施例1
37.如图1-图3所示的一种用于制备柔性热塑预浸料的装置,包括外壳体1、内壳体2、料仓3、筛网4和辊组件。外壳体1上端设有料仓3;料仓3顶部为喂料口,料仓3内部还设有搅拌机构11,搅拌机构11外接驱动机构,且喂料口下端与内壳体2内部连通。搅拌机构11上设有若干个搅拌叶片,搅拌叶片数量优选为10-15个。外壳体1内部设有内壳体2,内壳体2内部设有筛网4,内壳体2内部设有第一腔体21和第二腔体22,第一腔体21和第二腔体22连通,且连通位置所在的横向水平面处安装有两个隔料板8。
38.筛网4位于料仓3下端;筛网4下方设有挡板5,挡板5下方设有辊组件;辊组件包括加热辊6和冷却辊7,筛网4上开设有若干个孔隙,且每个孔隙的孔径范围都设为0.25mm-1.5mm;加热辊6位于挡板5的正下方,且加热辊6与内壳体2内壁面之间还设有隔料板8,隔料板8一端设置在加热辊6的外圆周表面,防止树脂颗粒洒出,隔料板8另一端焊接在内壳体2的内壁面上。加热辊6的加热温度为热塑性树脂融化温度,其温度范围为190℃-380℃,其中,该热塑性树脂包括但不限于pe、pp、pa6、pa66、pc、pps、peek、pekk。本装置还包括加热机构9和冷却机构10,加热机构9安装在外壳体1外部,且加热机构9与加热辊6连接。冷却机构10安装在外壳体1外部,且冷却机构10与冷却辊7连接。筛网4、挡板5都嵌固在第一腔体21内,加热辊6放置在第一腔体21内。冷却辊7放置在第二腔体22内。筛网4和挡板5之间设有间隙,间隙范围为2-3cm。
39.本装置的工作原理为:
40.将400g/m2的玻纤布卷装在加热辊6上,设置加热温度为260℃,加热辊6转速为1m/min,料仓3内放置适量直径为0.5mm的pc树脂颗粒,料仓3开启后,根据树脂含量50%-55%进行均匀下料,设置该比例,一方面是为了保证树脂颗粒足够多以熔化后完全浸润编织布;另一方面是为了保证柔性热塑复合材料的强度,树脂含量不可过高,筛网4与挡板5同时振动,使得树脂颗粒分布均匀后,移开挡板5,均匀下料。冷却辊7温度设置为10℃,转速为1m/min,将制备好的半浸润材料均匀收卷。当pc树脂颗粒进入下壳体部分时,pc树脂颗粒会先落入第一腔体21区域,此时设置的隔料板8,是为了当树脂颗粒进入下壳体后,由于隔料板8
一端焊接在内壳体2上,防止筛网4下料时,树脂颗粒由于重力作用全部堆积在加热辊6两侧。而加热辊6和冷却辊7之间不直接连接,当柔性热塑复合材料制备时,编织布收卷在热辊上,当进行加工时,成品直接在冷却辊7上收卷。
41.本装置生产出的材料与传统工艺所用的热塑性预浸料相比,具有良好的延展性和柔软性,可适用于各种尺寸及形状制品,用相同规格织物(同经纬密及线密度)分别用传统工艺和本装置制备热塑织物预浸料,并分别裁切具有相同长10cm、宽3cm的矩形样条,用拉力试验机夹持样品进行直线拉伸试验,直至样品拉伸至断裂,测试试验后的样品的长度l1cm,计算试验前后长度变化值(l1-10)cm,计算延伸率:(l1-10)/10*100%,如下表1所示的,使用本装置和传统工艺制备的延伸率对比情况,
42.表1
[0043][0044][0045]
从表1内容可以看出,使用本装置后的延伸率远远高于使用传统工艺后的延伸率,而延伸率越高表示延展性越好;而柔软性具体是体现在:将两种工艺制备样品粘贴到金属板上,然后弯折金属板对折后,通过4倍放大镜观测样品表面是否破裂或出现裂纹,而在实际操作实验对比后发现,使用本装置所制备柔性预浸料弯折处不产生裂痕,而传统工艺所制备预浸料弯折处出现明显裂痕,也即是,本装置所生产预浸料的柔软性效果强于传统的制备工艺。
[0046]
以上仅为本实用新型的实施方式,其描述较为具体和详细,但并不能因此而理解为对本实用新型专利范围的限制。应当指出的是,对于本领域的普通技术人员来说,在不脱离本实用新型构思的前提下,还可以做出若干变形和改进,这些均属于本实用新型的保护范围。