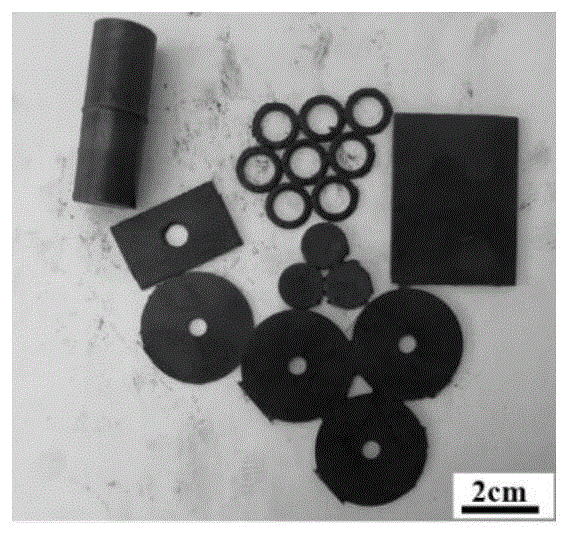
本发明涉及材料回收
技术领域:
,尤其涉及一种带胶带油泥钕铁硼废料回收再利用的预处理方法。
背景技术:
:钕铁硼作为当今应用最为广泛的永磁材料,其需求量和产量都在逐年递增。随着稀土资源的日益紧缺,价格不断上涨,对钕铁硼废料的回收再利用迫在眉睫。近年来,短流程回收技术作为一种资源循环率高、节能、环保的方法在钕铁硼废料的回收再利用过程中备受青睐。与传统湿法冶金相比,短流程回收技术无需将废料经酸溶、碱沉、焙烧等工艺先提取成稀土氧化物、氯化物或稀土元素,而是直接将收集的废料经过适当的表面处理后转变为表面质量高、杂质含量低的钕铁硼合金,然后经传统的氢爆、烧结工艺即可制备再生钕铁硼磁体。但是,钕铁硼在生产过程中会产生许多类型的废料,主要有熔炼废料、成型废料、烧结废料、机加工废料、电镀废料等,在这些废料中,有一部分形态较好、杂质含量少,例如烧结废料、机加工不合格品等,其经过简单的表面处理即可进行短流程回收利用。但是还有一些废料,例如机加工产生的料皮、料头废料等(见图1),与其他废料相比其主要特点是:形状较为复杂,表面有机加工过程中附着的切削液、油渍以及为方便加工而在磁体表面涂覆的一层520胶体,这种废料表面质量差、杂质成分多、形状复杂,必须进行适当的表面处理,才能够进行后续短流程回收。目前,各单位和企业对钕铁硼机加工废料的处理和回收已经做了很多研究。专利cn104190943a公开了一种烧结钕铁硼废料回收利用的方法,先将废料分类收集,在废料中加入白刚玉磨料和金属清洗液进行振动光饰清洗,然后进行短流程利用,但是该专利选取的废料为不合格品和后加工产生的边角料,一般表面只含有少量的油泥和氧化皮,并不能处理带胶和氧化皮较多的料皮料头;专利cn108435676a公开了一种烧结钕铁硼的除胶设备和方法,将废料放置于特定滚筒装置中,在装置内加入除胶液,在高温下去除废料表面的胶体,该专利虽然可以去除废料表面的胶体,但是装置较为复杂,成本高,且高温处理不仅会对磁体本身造成损伤,还会恶化工作环境,造成污染;专利cn109003798a公开了一种烧结钕铁硼混废料的回收再利用方法,在混合废料中加入除油剂和水进行搅拌处理,去除油污和泥浆,并在惰性气氛下烘干,然后进行研磨和磁选,再制备粘接磁体,该方法对废料的要求低,大多数废料都可适用,但是该方法处理后的废料总体质量不高,性能较低,只用于生产粘接磁体,未能将废料最大化利用。技术实现要素:本发明的目的在于提供一种带胶带油泥钕铁硼废料回收再利用的预处理方法,可处理机加工产生的带胶带油泥的料皮料头废料,通过表面的预处理,可有效去除废料表面的油泥、胶体和氧化皮,使废料能够通过短流程制备高性能的再生烧结磁体。本发明方法使用的试剂成本较低、试剂温和、无需加热,对环境和磁体本身的影响较小,且处理后的磁体表面质量好,整体的回收材料品质高。为了实现上述发明目的,本发明提供以下技术方案:本发明提供了一种带胶带油泥钕铁硼废料回收再利用的预处理方法,包括以下步骤:将带胶带油泥钕铁硼废料、表面清洗液和研磨球放入研磨机中进行球磨,将球磨后的废料进行第一超声清洗,磁选后得到第一废料;以质量份数计,每100份表面清洗液中包括:烷基酚聚氧乙烯醚3~5份、乙二醇丁醚醋酸酯10~15份、n,n二甲基乙酰胺5~10份、乙酸异戊酯5~10份、稳定剂2~5份和水余量;所述稳定剂为碳酸钠和碳酸氢钠;所述表面清洗液的ph值为7.5~9.5;将所述第一废料放入稀硝酸溶液中进行第二超声清洗,得到第二废料;所述稀硝酸溶液的浓度为0.01~0.25mol/l;所述稀硝酸溶液中含有0.01~0.5wt.%的氟化钠;将所述第二废料放入水中进行第三超声清洗,将清洗后的废料烘干。优选的,所述表面清洗液与带胶带油泥钕铁硼废料的质量比为(0.1~0.5):1。优选的,所述带胶带油泥钕铁硼废料与研磨球的质量比为(1.2~2):1。优选的,所述研磨球为棕刚玉研磨球、陶瓷研磨球和塑料研磨球,所述研磨球的直径为2~10mm。优选的,所述带胶带油泥钕铁硼废料的平均厚度>5mm时,所述研磨球包括50wt.%棕刚玉研磨球、40wt.%陶瓷研磨球和10wt.%塑料研磨球;每种研磨球的尺寸分布为:50wt.%的研磨球的直径满足:10mm≥直径>7mm,20wt.%的研磨球的直径满足:2mm≤直径<5mm,剩余30wt.%的研磨球直径为5~7mm;所述带胶带油泥钕铁硼废料的平均厚度<3mm时,所述研磨球包括30wt.%棕刚玉研磨球、40wt.%陶瓷研磨球和30wt.%塑料研磨球;每种研磨球的尺寸分布为:20wt.%的研磨球的直径满足:10mm≥直径>7mm,50wt.%的研磨球的直径满足:2mm≤直径<5mm,剩余30wt.%的研磨球直径为5~7mm;所述带胶带油泥钕铁硼废料的平均厚度为3~5mm时,所述研磨球包括40wt.%棕刚玉研磨球、40wt.%陶瓷研磨球和20wt.%塑料研磨球;每种研磨球的尺寸分布为:30wt.%的研磨球的直径满足:10mm≥直径>7mm,30wt.%的研磨球的直径满足:2mm≤直径<5mm,剩余40wt.%的研磨球直径为5~7mm。优选的,所述球磨的时间为1~3h。优选的,所述第一超声清洗的频率为60~100khz,采用的洗液为去离子水。优选的,所述第二超声清洗的频率为40~80khz,时间为0.5~5min。优选的,所述烘干的温度为40~70℃,时间为10~20min。优选的,所述第三超声清洗的频率为40~100khz,时间为1~5min。本发明提供了一种带胶带油泥钕铁硼废料回收再利用的预处理方法,包括以下步骤:将带胶带油泥钕铁硼废料、表面清洗液和研磨球放入研磨机中进行球磨,将球磨后的废料进行第一超声清洗,磁选后得到第一废料;以质量份数计,每100份表面清洗液中包括:烷基酚聚氧乙烯醚3~5份、乙二醇丁醚醋酸酯10~15份、n,n二甲基乙酰胺5~10份、乙酸异戊酯5~10份、稳定剂2~5份和水余量;所述稳定剂为碳酸钠和碳酸氢钠;所述表面清洗液的ph值为7.5~9.5;将所述第一废料放入稀硝酸溶液中进行第二超声清洗,得到第二废料;所述稀硝酸溶液的浓度为0.01~0.25mol/l;所述稀硝酸溶液中含有0.01~0.5wt.%的氟化钠;将所述第二废料放入水中进行第三超声清洗,将清洗后的废料烘干。本发明不使用高温蒸煮和特殊设备,仅利用表面清洗液和研磨作用即可清除带胶带油泥钕铁硼废料表面的油泥、胶体和氧化皮,选用的试剂成本较低,基本无毒,废液可降解性好,可常温使用,且清理效果明显;酸洗时选用较低浓度的硝酸,稀硝酸的酸性较弱,不会过度腐蚀废料中的富钕相,造成稀土的浪费,氟化钠可改善废料表面的活性,减少其氧化,使处理后的废料表面更整洁、光亮;经上述预处理方法处理后的废料完全满足后续短流程方法制备高性能再生磁体的要求。进一步的,在研磨过程中本发明根据废料的整体形态调节各研磨球的成分比例以及研磨球尺寸大小的比例,在保证研磨效果的同时,减少废料的破碎和氧化,提高回收率,利于后续短流程再生磁体制备。附图说明图1为多种形状的带胶带油钕铁硼机加工料皮料头废料的外观图;图2为实施例1中废料表面经处理前后的对比图,其中,a)处理前,a)处理后;图3为实施例2中废料表面经处理前后的对比图,其中,b)处理前,b)处理后;图4为实施例3中废料表面经处理前后的对比图,其中,c)处理前,c)处理后。具体实施方式本发明提供了一种带胶带油泥钕铁硼废料回收再利用的预处理方法,包括以下步骤:将带胶带油泥钕铁硼废料、表面清洗液和研磨球放入研磨机中进行球磨,将球磨后的废料进行第一超声清洗,磁选后得到第一废料;以质量份数计,每100份表面清洗液中包括:烷基酚聚氧乙烯醚3~5份、乙二醇丁醚醋酸酯10~15份、n,n二甲基乙酰胺5~10份、乙酸异戊酯5~10份、稳定剂2~5份和水余量;所述稳定剂为碳酸钠和碳酸氢钠;所述表面清洗液的ph值为7.5~9.5;将所述第一废料放入稀硝酸溶液中进行第二超声清洗,得到第二废料;所述稀硝酸溶液的浓度为0.01~0.25mol/l;所述稀硝酸溶液中含有0.01~0.5wt.%的氟化钠;将所述第二废料放入水中进行第三超声清洗,将清洗后的废料烘干。本发明将带胶带油泥钕铁硼废料、表面清洗液和研磨球放入研磨机中进行球磨,将球磨后的废料进行第一超声清洗,磁选后得到第一废料。在本发明中,所述带胶带油泥钕铁硼废料表面附着有胶类物质和油类物质。本发明对所述胶类物质和油类物质的具体组成没有特殊要求,均为本领域熟知的成分,胶类物质包括但不局限于α-氰基丙烯酸乙酯丙烯,油类物质包括但不局限于切削液的残留物。在本发明中,所述带胶带油泥钕铁硼废料的形状较为规整,其中圆柱体、圆环状和长方体的质量含量优选>50wt.%。在本发明中,以质量份数计,每100份表面清洗液中包括:烷基酚聚氧乙烯醚3~5份、乙二醇丁醚醋酸酯10~15份、n,n二甲基乙酰胺5~10份、乙酸异戊酯5~10份、稳定剂2~5份和水余量;所述稳定剂为碳酸钠和碳酸氢钠;所述表面清洗液的ph值为7.5~9.5。以质量份数计,每100份表面清洗液中包括烷基酚聚氧乙烯醚3~5份,优选为4~5份。在本发明中,所述烷基酚聚氧乙烯醚优选为op-10。在本发明中,所述烷基酚聚氧乙烯醚作为乳化剂,具有润湿、渗透、乳化、分散的作用,与各物质协同作用可显著提高清洗效率。以质量份数计,每100份表面清洗液中包括乙二醇丁醚醋酸酯10~15份,优选为11~14份,更优选为12~13份。在本发明中,所述乙二醇丁醚醋酸酯作为清洗剂使用,能够洗去废料表面的油渍。以质量份数计,每100份表面清洗液中包括n,n二甲基乙酰胺5~10份,优选为6~9份,更优选为7~8份。在本发明中,所述n,n二甲基乙酰胺作为胶体清除剂,具有稳定性好、低毒性、溶解力强等特点,可以增强对油渍和胶体的溶解。以质量份数计,每100份表面清洗液中包括乙酸异戊酯5~10份,优选为6~9份,更优选为7~8份。在本发明中,所述乙酸异戊酯是一种食品添加剂级的溶剂,乙酸异戊酯不仅可以增强对油脂和胶体的溶解,还富有清香气味,改善工作环境。以质量份数计,每100份表面清洗液中包括稳定剂2~5份,优选为3~4份。在本发明中,所述稳定剂为碳酸钠和碳酸氢钠。在本发明中,所述稳定剂的作用是调节表面清洗液的ph值为7.5~9.5,优选为8~9。本发明对所述碳酸钠和碳酸氢钠的配比没有特殊要求,能够使得表面清洗液的ph值在上述范围即可。在本发明的实施例中,所述碳酸钠和碳酸氢钠的质量比为1:2。本发明使表面清洗液保持在一个弱碱性环境,有利于提高对油污的清洗效果;且碳酸钠和碳酸氢钠对油污也有一定的清理效果。以质量份数计,每100份表面清洗液中包括水余量,在本发明中,所述水优选为去离子水。在本发明中,所述表面清洗液优选在常温下使用。本发明对所述表面清洗液的制备没有特殊要求,直接将各组分混合均匀即可。在本发明中,所述表面清洗液与带胶带油泥钕铁硼废料的质量比优选为(0.1~0.5):1,更优选为(0.2~0.4):1,进一步优选为(0.25~0.35):1。在本发明中,所述研磨球优选为棕刚玉研磨球、陶瓷研磨球和塑料研磨球,所述研磨球的直径优选为2~10mm。本发明优选根据废料的整体形态调节各研磨球的成分比例以及研磨球尺寸大小的比例。具体的:当所述带胶带油泥钕铁硼废料的平均厚度>5mm时,所述研磨球优选包括50wt.%棕刚玉研磨球、40wt.%陶瓷研磨球和10wt.%塑料研磨球;每种研磨球的尺寸分布优选为:50wt.%的研磨球的直径满足:10mm≥直径>7mm,20wt.%的研磨球的直径满足:2mm≤直径<5mm,剩余30wt.%的研磨球直径为5~7mm;当所述带胶带油泥钕铁硼废料的平均厚度<3mm时,所述研磨球优选包括30wt.%棕刚玉研磨球、40wt.%陶瓷研磨球和30wt.%塑料研磨球;每种研磨球的尺寸分布优选为:20wt.%的研磨球的直径满足:10mm≥直径>7mm,50wt.%的研磨球的直径满足:2mm≤直径<5mm,剩余30wt.%的研磨球直径为5~7mm;当所述带胶带油泥钕铁硼废料的平均厚度为3~5mm时,所述研磨球优选包括40wt.%棕刚玉研磨球、40wt.%陶瓷研磨球和20wt.%塑料研磨球;每种研磨球的尺寸分布优选为:30wt.%的研磨球的直径满足:10mm≥直径>7mm,30wt.%的研磨球的直径满足:2mm≤直径<5mm,剩余40wt.%的研磨球直径为5~7mm。在本发明中,所述带胶带油泥钕铁硼废料的厚度指的是以带胶面为底(每个废料只有一个带胶面),高度方向即为厚度。在研磨过程中本发明根据废料的整体形态调节各研磨球的成分比例以及研磨球尺寸大小的比例,在保证研磨效果的同时,减少废料的破碎和氧化,提高回收率,利于后续短流程再生磁体制备。在本发明中,所述带胶带油泥钕铁硼废料与研磨球的质量比优选为(1.2~2):1,更优选为(1.5~1.8):1,进一步优选为(1.6~1.7):1。在本发明中,所述研磨机优选为振动式研磨机。在本发明中,所述球磨的时间优选为1~3h,更优选为2~3h。本发明对所述球磨的转速没有特殊要求,采用本领域熟知的转速即可。本发明在所述球磨过程中,利用球磨作用和表面清洗液的作用,使得带胶带油泥钕铁硼废料表面杂质(包括胶体和油渍)脱落和溶解。完成所述球磨后,本发明将所述球磨后的废料取出,进行第一超声清洗,磁选后得到第一废料。在本发明中,所述第一超声清洗采用的洗液优选为去离子水。本发明对所述去离子水的用量没有特殊要求,能够将球磨后的废料完全浸没即可。在本发明中,所述第一超声清洗的功率优选为60~100khz,更优选为80~100khz。本发明对所述第一超声清洗的时间没有特殊要求,能够使得废料表面附着的杂质脱离即可。本发明采用较高频率超声可加速对污渍的清洗。本发明优选进行第一超声清洗1~2次,从而使废料表面的杂质脱离彻底。本发明对所述磁选的过程没有特殊要求,采用本领域熟知的磁选过程即可。本发明利用磁选将钕铁硼废料筛选出来的同时,可以有效脱除杂质成分。得到第一废料后,本发明将所述第一废料进行放入稀硝酸溶液中进行第二超声清洗,得到第二废料;所述稀硝酸溶液的浓度为0.01~0.25mol/l;所述稀硝酸溶液中含有0.01~0.5wt.%的氟化钠。在本发明中,所述稀硝酸溶液的浓度优选为0.05~0.20mol/l,更优选为0.10~0.15mol/l。在本发明中,所述稀硝酸溶液中优选含有0.05~0.4wt.%的氟化钠,更优选为0.1~0.3wt.%。本发明对所述稀硝酸溶液的用量没有特殊要求,能够将第一废料完全浸没即可。本发明选用较低浓度的硝酸,稀硝酸的酸性较弱,不会过度腐蚀废料中的富钕相,造成稀土的浪费,氟化钠可改善废料表面的活性,减少其氧化,使处理后的废料表面更整洁、光亮。在本发明中,所述第二超声清洗的频率优选为40~80khz,更优选为40~60khz。本发明采用较低频率超声可以在保证清洗效果的同时,减少酸液对磁体的腐蚀。本发明中在所述第二超声清洗过程中洗去深层氧化皮,当第一废料由灰色变为银白色时,取出,得到第二废料。得到第二废料后,本发明将所述第二废料放入水中进行第三超声清洗,将清洗后的废料烘干。在本发明中,所述水优选为去离子水。本发明对所述水的用量没有特殊要求,能够将第二废料完全浸没即可。在本发明中,所述第三超声清洗的频率优选为40~100khz,优选为60~80khz;时间优选为1~5min,更优选为2~4min。本发明利用第三超声清洗使得第二废料表面的杂质脱离。在本发明中,所述烘干的温度优选为40~70℃,更优选为50~60℃;时间优选为10~20min,更优选为13~18min,进一步优选为15min。下面结合实施例对本发明提供的带胶带油泥钕铁硼废料回收再利用的预处理方法进行详细的说明,但是不能把它们理解为对本发明保护范围的限定。实施例11)配制100份表面清洗液,成分为:1份碳酸钠和2份碳酸氢钠,ph值调为8.5,5份烷基酚聚氧乙烯醚op-10,12份乙二醇丁醚醋酸酯,8份n,n-二甲基乙酰胺,8份乙酸异戊酯,余量为去离子水。2)将厚度为5~8mm的圆柱状带胶带油泥料皮料头放入振动研磨机中,按废料量与研磨球质量比1.5:1的比例加入研磨球,成分为50wt.%棕刚玉,40wt.%陶瓷研磨球和10wt.%塑料研磨球,且每种研磨球的尺寸分布为:50wt.%的研磨球的直径满足:10mm≥直径>7mm,20wt.%的研磨球的直径满足:2mm≤直径<5mm,剩余30wt.%的研磨球直径为5~7mm;再放入配制的表面清洗液(为废料质量的0.3倍),研磨2.5h后取出。3)将研磨后的废料在100khz的超声波中进行第一超声清洗,共清洗2遍,并通过磁选,将杂质成分去除,得到第一废料。4)配制浓度为0.05mol/l的硝酸和0.05wt.%的氟化钠表面调节剂的混合溶液,作为酸洗液。5)将磁选后的废料放入配制的酸洗液中,进行第二超声清洗,超声频率60khz,清洗1min。6)观察清洗后废料,若表面残留少量氧化皮等杂质,再次将废料放入配制的酸洗液中,超声频率40khz,清洗0.5min,直至废料呈现银白色,得到第二废料。7)将所述第二废料放入去离子水中超声0.5min,取出后烘干。按实施例1,废料表面经处理前、后的对比见图2,图2中a)为处理前,a)为处理后。由图2可知,采用实施例1的方法处理后,钕铁硼废料表面干净,无杂质残留。对比例1~71)对比例1与实施例1相比,除第一步将配置的清洗液不含有碳酸钠和碳酸氢钠,其余步骤相同。2)对比例2与实施例1相比,除第一步将配置的清洗液不含有乳化剂烷基酚聚氧乙烯醚,其余步骤相同。3)对比例3与实施例1相比,除第一步将配置的清洗液不含有乙二醇丁醚醋酸酯,其余步骤相同。4)对比例4与实施例1相比,除第一步将配置的清洗液不含有n,n二甲基乙酰胺,其余步骤相同。5)对比例5与实施例1相比,除第一步将配置的清洗液不含有乙酸异戊酯,其余步骤相同。6)对比例6与实施例1相比,除第一步将配置的清洗液换为去离子水,其余步骤相同。7)对比例7与实施例1相比,将实施例1中的1)、2)和3)改为直接将收集的废料放入5w.%的氢氧化钠碱性溶液中煮沸后取出,后续处理与实施例1相同。表1为实施例1和对比例1~7的处理结果,杂质去除率为处理后减少的质量与原质量的比值。表1实施例1及对比例1~7的杂质去除率编号不同的除油、除胶试剂杂质去除率(%)实施例1配制清洗液3.1对比例1不含碳酸钠和碳酸氢钠的清洗液2.1对比例2不含烷基酚聚氧乙烯醚的清洗液2.2对比例3不含乙二醇丁醚醋酸酯的清洗液2.1对比例4不含n,n二甲基乙酰胺的清洗液1.8对比例5不含乙酸异戊酯的清洗液2.3对比例6去离子水1.5对比例7煮胶3.8由表1可以看出,实施例1的杂质去除率为3.1%,对比例1~6由于废料表面的油泥和胶体没有去除干净,导致最终废料表面仍有杂质残留;对比例7在煮胶的过程中虽然可以出去表面的油泥和胶体,但是高温会损伤磁体,造成废料表面的氧化,酸洗时会导致过多的质量损失。对比例8~11为使用不同的研磨球处理废料:1)对比例8与实施例1相比,除第二步研磨时的研磨球全部为棕刚玉研磨球,其余步骤相同。2)对比例9与实施例1相比,除第二步研磨时的研磨球全部为陶瓷研磨球,其余步骤相同。3)对比例10与实施例1相比,除第二步研磨时的研磨球全部为塑料研磨球,其余步骤相同。4)对比例11与实施例1相比,除第二步研磨时不添加研磨球,其余步骤相同。表2实施例1及对比例8~11的处理效果编号研磨球种类杂质除去率(%)废料破损率(%)实施例1混合研磨球3.120对比例8棕刚玉4.560对比例9陶瓷研磨球3.740对比例10塑料研磨球2.010对比例11无1.515废料破损率的计算为:抽取一定数量处理后的废料,观察统计断裂、破损数量,再除去抽取样品的数量。由表2可以看出,实施例1的杂质去除率为3.1%,破损率为20%,对比例8和对比例9由于研磨球硬度较大,研磨过程中挤压较为严重,造成废料破损率较高,较小颗粒会在磁选和酸洗过程中消耗掉,使废料的损失率大大提高;对比例10中塑料研磨球硬度较低,虽然可以减少破损率,但废料表面的除杂效果较差;对比例11中不添加研磨球,虽然破损率较低,但是废料表面杂质除去不充分,有较多残留。对比例12~14为使用不同尺寸的研磨球处理废料:1)对比例12与实施例1相比,除第二步研磨时的研磨球尺寸都大于7mm小于10mm,其余步骤相同。2)对比例13与实施例1相比,除第二步研磨时的研磨球尺寸在5~7mm之间,其余步骤相同。3)对比例14与实施例1相比,除第二步研磨时的研磨球尺寸都小于5mm大于2mm,其余步骤相同。表3实施例1及对比例12~14的处理效果由表3可以看出,实施例1的杂质去除率为3.1%,破损率为20%,对比例12和对比例13由于研磨球尺寸较大,研磨过程造成废料破损率较高,破损的较小颗粒会在磁选和酸洗过程中消耗掉,使废料的损失率提高;对比例14中研磨球硬尺寸太小,虽然可以减少破损率,但是能量较小,研磨不充分,造成废料表面的除杂效果较差。实施例2与实施例1相比,钕铁硼废料为厚度为小于3mm的长方形粘结料头,研磨球配比为30wt.%棕刚玉、40wt.%陶瓷研磨球和30wt.%塑料研磨球;每种研磨球的尺寸分布为:20wt.%的研磨球满足10mm≥直径>7mm,50wt.%的研磨球满足2mm≤直径<5mm,剩余30wt.%的研磨球直径为5~7mm。其余步骤与实施例1相同。按实施例2,废料表面经处理前后的对比见图3,图3中b)为处理前,b)为处理后。实施例3与实施例1相比,钕铁硼废料厚度为小于3mm的圆环状粘结料头,研磨球配比为30wt.%棕刚玉、40wt.%陶瓷研磨球和30wt.%塑料研磨球;每种研磨球的尺寸分布为:20wt.%的研磨球满足10mm≥直径>7mm,50wt.%的研磨球满足2mm≤直径<5mm,剩余30wt.%的研磨球直径为5~7mm。其余步骤与实施例1相同。按实施例3,废料表面经处理前后的对比见图4,图4中c)为处理前,c)为处理后。实施例4与实施例1相比,实施例4处理较为简单的机加工废料,该类废料表面仅含有少量油泥及氧化皮。本实施例具体处理的废料为机加工不良品,平均厚度为4~5mm,所选研磨球的比例为40wt.%棕刚玉、40wt.%陶瓷球和20wt.%塑料研磨球;且每种研磨球的尺寸分布为:30wt.%的研磨球的直径满足:10mm≥直径>7mm,30wt.%的研磨球的直径满足:2mm≤直径<5mm,剩余40wt.%的研磨球直径为5~7mm,研磨时间为2h,其他工艺参数与实施例1相同,也能得到很好的效果。由以上实施例和对比例可知,本发明提供了一种带胶带油泥钕铁硼废料回收再利用的预处理方法,可处理机加工产生的带胶带油泥的料皮料头废料,通过表面的预处理,可有效去除废料表面的油泥、胶体和氧化皮,使废料能够通过短流程制备高性能的再生烧结磁体。本发明方法使用的试剂成本较低、试剂温和、无需加热,对环境和磁体本身的影响较小,且处理后的磁体表面质量好,整体的回收材料品质高。以上所述仅是本发明的优选实施方式,应当指出,对于本
技术领域:
的普通技术人员来说,在不脱离本发明原理的前提下,还可以做出若干改进和润饰,这些改进和润饰也应视为本发明的保护范围。当前第1页12