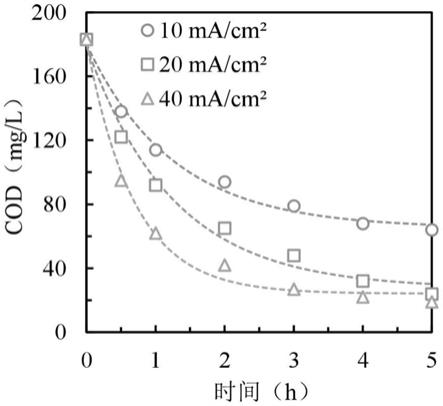
1.本发明属于工业废水处理领域,具体涉及一种用于煤化工行业反渗透浓水的电催化氧化联合正渗透处理方法。
背景技术:2.煤化工是以煤为原料,经过化学加工使煤转化为气体、液体和固体产品或半产品,而后进一步加工成化工、能源产品的过程,包括煤制天然气、煤制焦、煤制半焦、煤制甲醇、煤制烯烃、煤制乙二醇和煤制油等。煤化工废水的处理包括物化预处理、生化处理和深度处理,经过以上步骤处理后的出水有机物浓度大大降低,但盐度仍然较高。为提高水资源利用率,上述出水通常和洗涤废水、循环水排污水、脱盐水站排水等其他废水混合,经过以超滤+反渗透“双膜法”为核心的回用处理工艺,可以实现约70%的水回收率,但同时也产生了30%的反渗透浓水。该浓水的溶解性总固体浓度高,超过10000mg/l、且含有难降解有机污染物,企业通常会采用蒸发器和结晶器对其做进一步减量化处理,然后进入最终处置或盐回收阶段,但却面临着运行成本及能耗高等问题。高效反渗透、膜蒸馏、电渗析等方法对该浓水具有一定的处理效果,却依然面临能耗高、膜污染和结垢严重等问题。
技术实现要素:3.本发明为解决现有煤化工行业反渗透浓水的处理方法运行成本和能耗高、以及膜污染和结垢严重的技术问题,而提供了一种用于煤化工行业反渗透浓水的电催化氧化联合正渗透处理方法。
4.本发明的一种用于煤化工行业反渗透浓水的电催化氧化联合正渗透处理方法按以下步骤进行:
5.步骤1:采用石灰-纯碱对反渗透浓水进行软化处理,处理至出水ca
2+
《20mg/l、mg《30mg/l、sio2《10mg/l;
6.步骤2:对步骤1软化处理出水进行电催化氧化处理,以亚氧化钛网状电极为阳极,以不锈钢网为阴极,极板间距2cm~5cm,阴、阳极浸没于步骤1软化处理出水中,直流稳压电场模式下进行电催化氧化;
7.步骤3:电催化氧化出水进入正渗透膜单元进行再浓缩,得到二次浓水和稀释后的汲取液;
8.步骤4:二次浓水通过热法或膜法浓缩得到工业盐,稀释后的汲取液通过热法或膜法浓缩得到回用水和再生的汲取液。
9.进一步限定,步骤1中所述ca(oh)2的投加量为0.8g/l~1.2g/l,所述na2co3的投加量为4g/l~5g/l。
10.进一步限定,步骤2中所述电流密度为(0.025cod+17)ma/cm2。
11.进一步限定,步骤2中所述电流密度为10ma/cm2~40ma/cm2。
12.进一步限定,步骤2中所述亚氧化钛网状电极制备方法为:
①
将5~10目的钛丝网依次用甲醇、乙醇预处理,然后在去离子水中进行超声清洗作为基底;
②
将白色金红石型二氧化钛粉末在氢气氛下于1020℃还原处理120min,得到黑色球形亚氧化钛粉末;
③
通过等离子喷涂的方式将黑色球形亚氧化钛粉末均匀喷涂于步骤
①
得到的基底上。
13.进一步限定,步骤2中所述亚氧化钛网状电极的开孔比例为12%~15%。
14.进一步限定,步骤3中所述正渗透膜由活性层和支撑层构成,活性层为三醋酸纤维素(cta),支撑层为聚对苯二甲酸乙二醇酯(pet)。
15.进一步限定,步骤3中正渗透膜活性层一侧为电催化氧化出水,正渗透膜支撑层一侧为汲取液,汲取液为3mol/l~4mol/l的nacl溶液。
16.进一步限定,步骤3中正渗透再浓缩过程的产水量控制在70%以内。
17.进一步限定,步骤3中正渗透再浓缩过程中水通量下降10%时对正渗透膜进行清洗。
18.进一步限定,对正渗透膜进行清洗的清洗剂为三聚磷酸钠和edta的复合清洗剂,其中三聚磷酸钠的质量分数为2%,edta的质量分数为0.8%。
19.本发明的一种用于煤化工行业反渗透浓水的电催化氧化联合正渗透处理方法用于催化降解煤化工行业反渗透浓水中的长链甲基烷烃、甲基苯酚、吡啶、吲哚、二辛脂类有机污染物。
20.本发明与现有技术相比具有的显著效果:
21.1、本发明的处理方法前置软化处理解决了膜结垢问题,然后通过原位利用水中的高离子强度,生成
·
oh、活性氯(hclo和clo-,其中clo-占所有氯活性物质的99.9%以上,可达2mmol/l)有效解决了有机污染物导致的膜污染,电催化氧化过程中无需添加电解质溶液,节省费用。最后利用正渗透过程再浓缩,减少进入下游热法或膜法盐分离和回收过程的水量,节约运行费用。
22.2、本发明可以直接应用于煤制气、煤制甲醇等新型煤化工项目的废水处理过程,将本发明的处理方法置于反渗透浓缩工序后、蒸发结晶或纳滤分盐工序前,可以再次回收反渗透浓水的70%,并提高后续分盐工艺的效率和产品质量。
附图说明
23.图1为实施例1-3步骤2电催化氧化过程中有机物随电化学氧化时长和电流密度的变化趋势曲线图;
24.图2为实施例1-3步骤2电催化氧化过程中有机物去除率与能耗关系曲线图;
25.图3a为实施例1步骤2电催化氧化5h前的废水对比照片;
26.图3b为实施例1步骤2电催化氧化5h后的废水对比照片;
27.图4a为实施例1步骤2电催化氧化后水中有机物分子量分布图;
28.图4b为实施例1步骤2电催化氧化前水中有机物分子量分布图。
具体实施方式
29.实施例1、本实施例的一种用于煤化工行业反渗透浓水的电催化氧化联合正渗透处理方法按以下步骤进行:
30.步骤1:采用石灰-纯碱对反渗透浓水(原水水质参见表1)进行软化处理,ca(oh)2的投加量为1.0g/l,所述na2co3的投加量为4.6g/l,处理至出水ca
2+
《20mg/l、mg《30mg/l、sio2《10mg/l;经检测:软化处理后出水,ca
2+
为13.0mg/l,mg
2+
为24.1mg/l,sio2为3.5mg/l,cod为183mg/l,tds为14470mg/l;所述煤化工行业反渗透浓水原水中有机物采用液相色谱-质谱联用仪进行测定,结果显示煤化工反渗透浓水原水中有机物为:乙苯,三甲基辛烷,三甲基十二烷,3-甲基5丙基壬烷,邻苯二甲酸二辛脂,苯酚,苯胺,四甲基苯酚,二甲基苯酚,喹啉酮,吡啶;
31.步骤2:对步骤1软化处理出水进行电催化氧化处理,以亚氧化钛网状电极为阳极,以不锈钢网为阴极,极板间距5cm,阴、阳极浸没于步骤1软化处理出水中,直流稳压电场模式下进行进行电催化氧化,电流密度为20ma/cm2,电催化氧化3h;所述亚氧化钛网状电极的开孔比例为13.8%,所述亚氧化钛网状电极制备方法为:
①
将6目的钛丝网依次用甲醇、乙醇预处理,然后在去离子水中进行超声清洗作为基底;
②
将白色金红石型二氧化钛粉末在氢气氛下于1020℃还原处理120min,得到黑色球形亚氧化钛粉末;
③
通过等离子喷涂的方式将黑色球形亚氧化钛粉末均匀喷涂于步骤
①
得到的基底上;
32.步骤3:电催化氧化出水进入正渗透膜单元进行再浓缩,得到二次浓水和稀释后的汲取液;所述正渗透膜由活性层和支撑层构成,活性层为三醋酸纤维素(cta),支撑层为聚对苯二甲酸乙二醇酯(pet),正渗透膜活性层一侧为电催化氧化出水,正渗透膜支撑层一侧为汲取液,汲取液为4mol/l的nacl溶液,正渗透再浓缩过程中水通量下降10%时对正渗透膜进行清洗,清洗剂为三聚磷酸钠和edta的复合清洗剂,其中三聚磷酸钠的质量分数为2%,edta的质量分数为0.8%,清洗后初期水通量可以恢复到99%,连续运行后水通量仍可恢复到95%,正渗透再浓缩过程的产水量(汲取液再生后水回收率)为70%;
33.步骤4:二次浓水通过热法或膜法浓缩得到工业盐,稀释后的汲取液通过热法或膜法浓缩得到回用水和再生的汲取液,其中所述热法、膜法均为现有常规浓缩工艺。
34.本实施例中不计入汲取液再生费用时的小试运行费用为21.0元/m3,其中电能投入为17.3元/m3,药剂投入为3.7元/m3。对比于内蒙古某煤制天然气公司利用碎煤加压气化高浓酚氨废水的生化、中水回用、膜浓缩及氯化钠和硫酸钠分盐结晶的全流程中试试验,其反渗透膜浓缩单元成本11.00元/m3,蒸发结晶单元成本27.46元/m3。用本实施例的方法可以将后续蒸发结晶的处理水量降低70%。
35.实施例2:本实施例与实施例1不同的是:步骤2中所述电流密度为10ma/cm2。其他步骤及参数与实施例1相同。
36.实施例3:本实施例与实施例1不同的是:步骤2中所述电流密度为40ma/cm2。其他步骤及参数与实施例1相同。
37.实施例4:本实施例的一种用于煤化工行业反渗透浓水的电催化氧化联合正渗透处理方法按以下步骤进行:
38.步骤1:采用石灰-纯碱对反渗透浓水(原水水质参见表1)进行软化处理,ca(oh)2的投加量分别为1.0g/l,所述na2co3的投加量为4.6g/l,处理至出水ca
2+
《20mg/l、mg《30mg/l、sio2《10mg/l;经检测:软化处理后出水,ca
2+
为16.2mg/l,mg
2+
为28.2mg/l,sio2为4.2mg/l,cod为262mg/l,tds为18420mg/l;所述煤化工行业反渗透浓水原水中有机物采用液相色谱-质谱联用仪进行测定,结果显示煤化工反渗透浓水原水中有机物为:乙苯,三甲基辛烷,
28mg/l,荧光分析表明,类腐殖酸物质、溶解性微生物产物和类富里酸物质去除率都超过了95%。
45.效果例2:对实施例1步骤2过程中的水进行检测,分子量分布见图4,由图4可以看出,小分子(《1000da)明显增加。