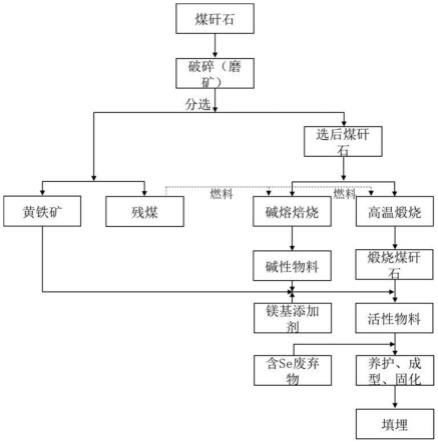
一种煤矸石基活性粉体制备及固化核素se的方法
技术领域
1.本发明涉及煤基固废综合利用及放射性固废安全处置领域,具体涉及一种煤矸石基活性粉体制备及固化核素se的方法。
背景技术:2.煤矸石是煤炭开采和洗选加工过程中产生的固体废弃物,大量堆存不仅会占据大量的土地资源,而且其中的有害物质会污染土壤、水源及大气。此外,煤矸石山堆放不规范、结构疏松,稳定性差,在无序开挖和自然雨水冲刷的情况下,极易引发滑坡、崩塌、泥石流等地质灾害,给当地人员的生命和财产安全构成严重威胁。因此,亟需开展煤矸石的资源化综合利用工作。
3.另外,
79
se是铀的长寿命裂变产物之一,半衰期长达2.8
×
105年,是乏燃料后处理过程中备受关注的放射性核素。自然环境中,se的主要化合价态有se(vi)、se(iv)、se(0)和 se(-ii)。
79
se(iv)和
79
se(vi)是
79
se在核废料中常见的价态形式,在酸性或碱性环境中均具有很强的流动能力。一旦
79
se被排放至人类环境中,将会导致大面积的土壤或水体污染,势必会给人类带来巨大的灾难。因此,针对富含
79
se的废弃物,需要无害化处置。
技术实现要素:4.为了解决现有技术存在的上述技术问题,本发明提供了一种变废为宝、环保经济、性能优越的煤矸石基活性粉体制备及固化核素se的方法,以解决现有煤矸石废弃物得到不妥善处理的问题。
5.为实现上述目的,本发明提供了一种煤矸石基活性粉体制备及固化核素se的方法,其包括以下步骤:
6.1)以富含高岭石的煤矸石为原料,经过破碎或磨矿,分选得到黄铁矿、残煤和选后煤矸石三种产物;
7.2)将步骤1)得到的选后煤矸石中的一部分与碱性物料混合后,以步骤1)中的残煤为供热热源进行碱熔焙烧,得到碱熔物料,所述碱性物料为氢氧化钠、碳酸钠、氢氧化钾中的一种或多种;
8.3)将步骤1)得到的选后煤矸石中的另一部分以步骤1)中的残煤为供热热源进行高温煅烧,以将含有的高岭土转变为偏高岭土,得到矸石煅烧物料;
9.4)将步骤2)得到的碱熔物料与步骤3)得到的矸石煅烧物料,以及镁基添加剂和黄铁矿按质量比为1-3:5-7:0.5-0.8:0.3-0.5混合、研磨,得到煤矸石基活性粉体材料;
10.5)将含se废弃物与步骤4)得到的煤矸石基活性粉体材料混合,含se固废的含量控制在30%以内,加水反应,经过养护、成型,形成将含se废弃物中的核素se固化在其中的地质聚合物固化体,然后地质填埋。
11.作为本发明的进一步优选技术方案,步骤1)中的破碎处理采用颚式破碎机和/或球磨机,破碎的煤矸石粒度小于0.25mm。
12.作为本发明的进一步优选技术方案,步骤1)中采用两段浮选法进行分选,具体为,一段浮选选出残煤,二段浮选选出黄铁矿和选后煤矸石。
13.作为本发明的进一步优选技术方案,所述两段浮选法中,一段浮选采用烃类复配药剂作为捕收剂,仲辛醇作为起泡剂进行浮选,二段浮选采用硫酸调节ph和硫酸铜作为活化剂,黄药作为捕收剂,2号油作为起泡剂进行浮选。
14.作为本发明的进一步优选技术方案,步骤2)中,碱熔焙烧的温度为500~850℃,时间为1.5~5h。
15.作为本发明的进一步优选技术方案,步骤3)中,煅烧温度为500~700℃,时间为3~ 12h。
16.作为本发明的进一步优选技术方案,步骤4中,镁基添加剂为氧化镁或氢氧化镁。
17.作为本发明的进一步优选技术方案,步骤4)中,研磨后得到的煤矸石基活性粉体材料的粒度为40微米以下。
18.作为本发明的进一步优选技术方案,步骤5)中,养护的条件为:首先在室温下密封养护一天,之后脱模,再在温度为20-80℃,湿度为85-95%的条件下继续养护3-28天。
19.本发明的煤矸石基活性粉体制备及固化核素se的方法,采用上述技术方案,可以达到如下有益效果:
20.1)煤矸石作为产量较大的大宗固废之一,本发明可以有效地消纳煤矸石,解决煤矸石堆积的环境问题,同时将制备的活性粉体材料应用于固化含se固废,实现“以废治废”的理念,降低含se固废处理成本;
21.2)利用煤矸石中硅、铝主要成分制备成活性粉体材料,类似水泥材料,通过加水反应即可实现固化,反应过程涉及到硅、铝主要成分的解聚、键合,形成以硅、铝组分为主的三维网状结构的地质聚合物固化体,解决了传统制备地质聚合物工艺中的碱液使用问题;
22.3)充分利用煤矸石中的化学组分,将黄铁矿加入,有针对性的对高化合价se废弃物设计物料组分,其目的是利用二价铁的还原性将高化合价se还原为低价,实现se的稳定固化。
附图说明
23.下面结合附图和具体实施方式对本发明作进一步详细的说明。
24.图1为本发明煤矸石基活性粉体制备及固化核素se的方法提供的一实例的流程图;
25.图2为本发明地质聚合物固化体的微观结构及固化se的机理图。
26.本发明目的实现、功能特点及优点将结合实施例,参照附图做进一步说明。
具体实施方式
27.下面将结合附图以及具体实施方式,对本发明做进一步描述。较佳实施例中所引用的如“上”、“下”、“左”、“右”、“中间”及“一”等用语,仅为便于叙述的明了,而非用以限定本发明可实施的范围,其相对关系的改变或调整,在无实质变更技术内容下,当亦视为本发明可实施的范畴。
28.本技术鉴于煤矸石中硅、铝的主要成分,以煤矸石为原料制备作为固化材料的煤
矸石基活性粉体,并应用到含se固废的安全处置,实现“以废治废”的理念。
29.如图1所示,本发明提供了一种煤矸石基活性粉体制备及固化核素se的方法,其包括以下步骤:
30.步骤1)、以富含高岭石的煤矸石为原料,经过破碎、浮选,分选得到黄铁矿、残煤和选后煤矸石三种产物。
31.具体实施中,破碎处理采用颚式破碎机和/或球磨机,破碎的煤矸石粒度小于0.25mm,实现残煤和黄铁矿的有效解离。浮选处理采用两段浮选法,其中,一段浮选选出残煤,二段浮选选出黄铁矿和选后煤矸石。
32.优选地,两段浮选法中,一段浮选采用烃类复配药剂作为捕收剂,仲辛醇作为起泡剂进行浮选,二段浮选采用硫酸调节ph和硫酸铜作为活化剂,黄药作为捕收剂,2号油作为起泡剂进行浮选。
33.步骤2)、将步骤1)得到的选后煤矸石中的一部分与碱性物料混合后,并以步骤1)中的残煤为燃料进行碱熔焙烧,得到碱熔物料,所述碱性物料为氢氧化钠、碳酸钠、氢氧化钾中的一种或多种。
34.具体实施中,碱熔焙烧是使部分煤矸石转变为可溶态硅铝,作为激发剂使用。碱熔焙烧的温度为500~850℃,时间为1.5~5h。
35.步骤3)、将步骤1)得到的选后煤矸石中的另一部分以步骤1)中的残煤为燃料进行高温煅烧,以将含有的高岭土转变为偏高岭土,得到矸石煅烧物料。
36.具体实施中,煅烧是使高岭土变为偏高岭土,使煤矸石具有活性。煅烧温度为500~ 700℃,时间为3~12h。
37.步骤4)、将步骤2)得到的碱熔物料与步骤3)得到的矸石煅烧物料,以及镁基添加剂和黄铁矿按质量比为1-3:5-7:0.5-0.8:0.3-0.5混合、研磨,得到煤矸石基活性粉体材料(流程图中简称为活性物料)。
38.具体实施中,镁基添加剂为氧化镁或氢氧化镁。研磨后得到的煤矸石基活性粉体材料的粒度为40微米以下,较细的粒度,有利于后续的成型及固化过程中加快反应进行。
39.优选地,黄铁矿的加入,可利用黄铁矿在加水环境中进行氧化还原反应,以在后续的固化过程中,将高化合价se还原为低价,增加固化稳定性。同时,黄铁矿的添加量相对较低,不会影响整体材料的强度及稳定性,即通过少许两的添加,即可满足设计需求。
40.步骤5)、将含se固废与步骤4)得到的煤矸石基活性粉体材料混合,含se固废的含量控制在30%以内,加水反应,经过养护、成型,形成将含se废弃物中的核素se固化在其中的地质聚合物固化体,然后地质填埋。
41.具体实施中,养护的条件为:首先在室温下密封养护一天,之后脱模,再在温度为 20-80℃,湿度为85-95%的条件下继续养护3-28天。
42.本发明提出的煤矸石基活性粉体制备及固化核素se的方法,以煤炭开采和洗选加工过程中产生的固体废弃物(煤矸石)作为初始原料,合理地利用煤矸石中硅铝主要成分来制备地质聚合物,通过对固化有核素se的地质聚合物固化体进行研究,结果表明,se含氧阴离子可以以静电力的形式赋存于地质聚合物三维网状结构中。在固化过程中,将煤矸石中黄铁矿作为还原性添加剂,使煤矸石基活性粉体材料具备了还原特性,可将高价se还原为更为稳定的低价se,从而提高固化稳定性。在固化核素se的过程中,将添加有黄铁矿与未添
加黄铁矿的样品进行比较,其中添加有黄铁矿的情况下可使浸出率降低20%以上;此外,镁基添加剂的加入,进一步使得地质聚合物结构致密(如表1所示)。在固化核素se的过程中,将添加有镁基添加剂与未添加镁基添加剂的样品进行比较,其中添加有镁基添加剂的情况下可使浸出效率降低35%以上。
43.表1.地质聚合物固化体样品的比表面积、孔体积及密实度数据
[0044][0045]
为了进一步研究本发明的地质聚合物固化体的结构特性,通过在电镜下观察,可以看到其地质聚合物呈现三维网状空间结构,将核素se固化在该地质聚合物固化体中,则钠离子以键桥的方式将se含氧阴离子与铝氧四面体负电荷平衡,使得se含氧阴离子在地质聚合物中以静电力形式赋存,如图2所示。
[0046]
虽然以上描述了本发明的具体实施方式,但是本领域熟练技术人员应当理解,这些仅是举例说明,可以对本实施方式做出多种变更或修改,而不背离本发明的原理和实质,本发明的保护范围仅由所附权利要求书限定。