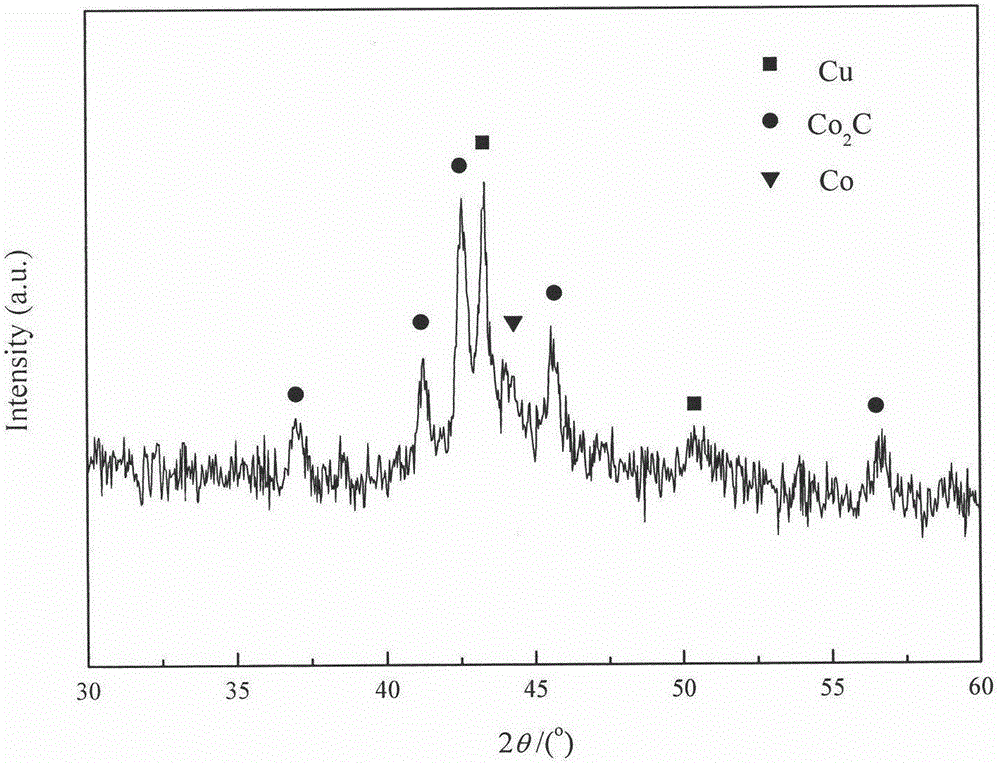
本发明涉及一种催化转化合成气制液体燃料或化工产品的技术,属能源化工领域。特别涉及合成气催化转化制混合醇及液体烃类用催化剂及其制备方法。
背景技术:
:低碳混合醇(简称低碳醇)是指由C1-C6直链醇组成的液体混合物,可用作替代燃料,洁净汽油添加剂或者化学品及化工原料。由合成气直接合成低碳醇的研究始于19世纪20年代。上世纪70年代的两次石油危机的影响和人们环保意识的增强,使以煤,天然气或生物质为原料经合成气制取低碳醇的研究课题受到了人们极大地重视。上世纪初以来,研究者开发出了多种不同的合成低碳醇催化剂体系,其中具有代表性的有以下四种:(1)改性高温(高压)甲醇合成催化剂。由ZnO/Cr2O3加入碱性助剂(如Cs,K)改性而得。该类催化剂主要产物为甲醇和支链异丁醇,反应条件较为苛刻(压力14-20MPa,温度350-450℃)。(2)改性低温(低压)甲醇合成催化剂。在低温合成甲醇铜基催化剂(Cu/ZnO/Al2O3或Cu/ZnO/Cr2O3)中加入碱性助剂如(如Cs,K)改性同样可以提高反应产物中低碳醇的选择性。该类催化剂反应条件温和,但活性组分Cu易烧结,而且产物中甲醇含量高。以上两类参见相关专利EP-0034338-A2,USPatent4513100等。(3)Cu-Co催化剂。法国石油研究院(IFP)首先开发了Cu-Co共沉淀低碳醇催化剂,目前已获得了多个专利(USPatent4122110,4291126),该类催化剂操作条件比较温和,主要产物为直链正构醇,反应活性和C2+醇的选择性较高,但总醇选择性较低且产物中水较多。(4)钼基催化剂。典型的钼基催化剂可见USPatent4882360。钼基催化剂一般具有独特的抗硫性能且不易积碳,产物含水量少,可加入碱金属助剂以及其他金属组分进行优化,可使醇的C2+/C1比例较为合理,但此催化体系对合成气比例要求苛刻,而且助剂钴极易与一氧化碳形成羰基钴造成钴流失。由于高碳醇(6个碳原子以上的一元醇,可用于合成增塑剂,洗涤剂,表面活性以及其他精细化学品)的附加值高,而且由合成气直接制备高碳醇的反应路线短,因此近年来由合成气直接制备高碳醇的催化剂开始出现。国内专利CN101310856A曾报道以活性炭为载体,Co和Co2C为活性组分的合成高碳醇的催化剂及其制备方法,可一步合成C1-C18直链高碳醇,其中总醇选择性为38.3%。美国专利USPatent4504600报道了一种铊助剂的铁基催化剂,由合成气合成的烃类产物中可得C6-C12的高碳醇,重量占总烃类的5-10%。中国专利CN103433046A报道了一种采用共沉淀法制备的“CoCuM”催化剂体系,其中M为一种或多种助剂,该体系的总醇质量选择性最高为64.3%,其中甲醇在总醇中的含量为18.4-64.3%,C6+醇在总醇中占13.2-31.5%。以上报道的各专利中,有的总醇选择性高,但是甲醇在总醇中所占比重较大;有的总醇选择性较好,而且甲醇含量低,但是醇的分布宽,主要醇组分不突出。由于活性炭负载的钴基催化剂具有甲醇含量低的的特点,而“CoCu”基催化剂具有高的总醇选择性的特点,并且这两种催化剂体系均容易采用助剂调变,因此本发明通过活性炭负载的钴催化剂与“CoCu”基催化剂复合并采用Mn物种调变,得到活性炭负载的“CoCuMn”催化剂,与以上催化剂体系相比,本发明具有催化剂的活性较高,总醇的选择性较好,甲醇组分含量低,低碳醇组分(C2-C5)含量高的特点。技术实现要素:本发明的目的主要是针对活性炭负载的钴基催化剂总醇选择性不高,且醇的分布不集中的问题,以及“CoCu”催化剂虽然总醇选择性高但是甲醇组分含量过高的问题,提供一种具有独特结构的催化剂及其制备方法和应用,同时获得高的总醇选择性,低的甲醇含量,以及较集中分布的醇组分。该类催化剂制备过程简单,成本低廉,具有优良的合成醇选择性和较高的C2+醇组分含量,具有明显的应用价值。本发明主要包括活性组分,助剂,负载和催化剂反应条件。催化剂的制备以椰壳活性炭为载体,将其制成80-100目的活性炭颗粒,首先采用自来水洗去表面浮灰,然后采用去离子水洗10次。采用共浸渍法将硝酸钴,硝酸铜和硝酸锰的混合水溶液浸渍到活性炭AC载体上,保持1h,之后将样品于空气中60℃烘干12h;在惰性气氛下于350℃焙烧,得到催化剂的前驱体。将4mL催化剂前驱体至于反应器内,通入压力为0.1MPa的纯氢气,空速为1000h-1,以5℃/min的升温速率升温至430℃,保持4h,还原结束后降温到室温;然后切入H2与CO体积比为2的混合气体,升压至3MPa,空速为500h-1,以1℃/min升温至220℃,反应稳定24h后,间隔24h取样。本发明所述的空速为单位时间内通入气体的体积与催化剂体积之比。本发明的优点(1)以廉价的硝酸钴,硝酸铜,硝酸锰为原料。(2)合成的催化剂具有:总醇的选择性较高,甲醇组分含量低,C2+醇的组分含量高,醇集中分布在C2-C5醇之间。附图说明图1是实施例1制备的催化剂经反应后的XRD图;图2是实施例2制备的催化剂经反应后的XRD图;图3是实施例3制备的催化剂经反应后的XRD图;图4是实施例4制备的催化剂经反应后的XRD图;图5是实施例2制备的催化剂经反应后的高分辨透射电镜(TEM)图;图6是实施例3制备的催化剂经反应后的高分辨透射电镜(TEM)图;图7是实施例4制备的催化剂经反应后的高分辨透射电镜(TEM)图。具体实施方式下面结合实施例对本发明作进一步的说明,本发明包括但不限于下面的实施例实施例1称取3.704g硝酸钴(Co(NO3)2·6H2O)与0.755g硝酸铜(Cu(NO3)·3H2O),放入盛有5mL水溶液的50mL烧杯中,搅拌至硝酸钴与硝酸铜完全溶解,加入0.324g50%的硝酸锰溶液混溶。取5gAC载体,将载体浸渍于含有活性组分的浸渍液中,静止1h,使其活性组分和助活性组分通过毛细作用负载于载体上,再经过60℃空气中烘干12h,所得样品在Ar气氛中于350℃恒温焙烧4h,然后降温至室温,得到黑色样品。以上催化剂命名为A,催化剂组成列于表1。催化剂的物性表征结果列于表2。取4mL上述催化剂进行还原处理,所采用条件与步骤为:通入压力为0.1MPa的纯氢气,空速为1000h-1,以5℃/min升温到430℃,保持4h,还原结束后降温到室温。然后对还原后的催化剂进行反应评价,所采用条件与步骤为:切入H2与CO体积比为2的混合气体,相应空速为500h-1,反应经过24h稳定之后,再经过24h取样分析。反应结果列于表3。从XRD谱图可以看出,反应过程中出现了金属钴和金属铜的衍射峰。实施例2称取3.704g硝酸钴(Co(NO3)2·6H2O)与0.755g硝酸铜(Cu(NO3)·3H2O),放入盛有5mL水溶液的50mL烧杯中,搅拌至硝酸钴与硝酸铜完全溶解,加入1.302g50%的硝酸锰溶液混溶。取5gAC载体,将载体浸渍于含有活性组分的浸渍液中,静止1小时,使其活性组分和助活性组分通过毛细作用负载于载体上,再经过60℃空气中烘干12h,所得样品在Ar气氛中于350℃恒温焙烧4h,然后降温至室温,得到黑色样品。以上催化剂命名为B,催化剂组成列于表1。催化剂的物性表征结果列于表2。取4mL上述催化剂进行还原处理,所采用条件与步骤为:通入压力为0.1MPa的纯氢气,空速为1000h-1,以5℃/min升温到430℃,保持4h,还原结束后降温到室温。然后对还原后的催化剂进行反应评价,所采用条件与步骤为:切入H2与CO体积比为2的混合气体,相应空速为500h-1,反应经过24h稳定之后,再经过24h取样分析。反应结果列于表3。从XRD谱图可以看出,反应过程中出现了金属钴和金属铜的衍射峰。从TEM谱图可以看出,较小的圆形金属钴颗粒与金属铜颗粒紧密接触。实施例3称取3.704g硝酸钴(Co(NO3)2·6H2O)与1.51g硝酸铜(Cu(NO3)·3H2O),放入盛有5mL水溶液的50mL烧杯中,搅拌至硝酸钴与硝酸铜完全溶解,加入2.605g50%的硝酸锰溶液混溶。取5gAC载体,将载体浸渍于含有活性组分的浸渍液中,静止1小时,使其活性组分和助活性组分通过毛细作用负载于载体上,再经过60℃空气中烘干12h,所得样品在Ar气氛中于350℃恒温焙烧4h,然后降温至室温,得到黑色样品。以上催化剂命名为C,催化剂组成列于表1。催化剂的物性表征结果列于表2。取4mL上述催化剂进行还原处理,所采用条件与步骤为:通入压力为0.1MPa的纯氢气,空速为1000h-1,以5℃/min升温到430℃,保持4h,还原结束后降温到室温。然后对还原后的催化剂进行反应评价,所采用条件与步骤为:切入H2与CO体积比为2的混合气体,相应空速为500h-1,反应经过24h稳定之后,再经过24h取样分析。反应结果列于表3。从XRD谱图可以看出,反应过程中出现了金属钴和金属铜的衍射峰。从TEM谱图可以看出,较小的圆形金属钴颗粒与金属铜颗粒紧密接触。实施例4称取1.975g硝酸钴(Co(NO3)2·6H2O)与1.51g硝酸铜(Cu(NO3)·3H2O),放入盛有5mL水溶液的50mL烧杯中,搅拌至硝酸钴与硝酸铜完全溶解,加入2.605g50%的硝酸锰溶液混溶。取5gAC载体,将载体浸渍于含有活性组分的浸渍液中,静止1小时,使其活性组分和助活性组分通过毛细作用负载于载体上,再经过60℃空气中烘干12小时,所得样品在Ar气氛中于350℃恒温焙烧4h,然后降温至室温,得到黑色样品。以上催化剂命名为D,催化剂组成列于表1。催化剂的物性表征结果列于表2。取4mL上述催化剂进行还原处理,所采用条件与步骤为:通入压力为0.1MPa的纯氢气,空速为1000h-1,以5℃/min升温到430℃,保持4h,还原结束后降温到室温。然后对还原后的催化剂进行反应评价,所采用条件与步骤为:切入H2与CO体积比为2的混合气体,相应空速为500h-1,反应经过24h稳定之后,再经过24h取样分析。反应结果列于表3。从XRD谱图可以看出,反应过程中出现了金属钴和金属铜的衍射峰。从TEM谱图可以看出,较小的圆形金属钴颗粒与金属铜颗粒紧密接触。本发明所用的分析测试方法:1)催化剂的组成由制备过程中添加的各组分含量经换算而得;2)催化剂的比表面积、孔容及孔径分布测定采用美国麦克公司ASAP2020低温液氮吸附法,比表面积为BET比表面积;3)采用德国布鲁克斯公司(Bruker)的D8AdvanceX-射线粉末衍射仪分析催化剂的物相;4)采用飞利浦公司的C/M300的高倍透射电子显微镜分析催化剂的结构;5)采用美国安捷伦公司的7890气相色谱分析产物组成。表1催化剂组成催化剂编号ABCDAC含量,%83.280.876.180.4Co含量,%12.512.111.46.4Cu含量,%3.33.26.16.4MnO含量,%1.03.96.46.8表2催化剂的性能指标催化剂BET比表面积(m2/g)孔容(ml/g)平均孔径(nm)活性炭载体774.10.442.3A646.50.322.5B656.20.322.6C568.10.282.4D706.10.342.3表3催化剂评价结果催化剂编号ABCDCO转化率,%38.652.256.058.3甲烷选择性,%30.814.18.97.7C2-C4烃类选择性,%37.622.026.122.5CO2选择性,%6.33.85.95.2C5+选择性,%16.236.634.124.5总醇选择性,%9.123.525.040.1甲醇/总醇,%4.06.63.12.7C2-C5醇/总醇,%69.554.268.580.0C6-C14醇/总醇,%26.539.228.417.3注:选择性为各组分在有机产物中的选择性(以碳原子数计)。由以上数据可见,催化剂具有较合理的比表面积,孔体积和孔径分布;催化剂生成醇的活性中心结构为紧密接触的小颗粒Co与大颗粒的Cu;催化剂在上述反应条件下,在固定床反应器内具有较高的反应活性和良好的选择性,所得醇中甲醇含量低,而且醇集中分布在C2-C5醇之间。当前第1页1 2 3