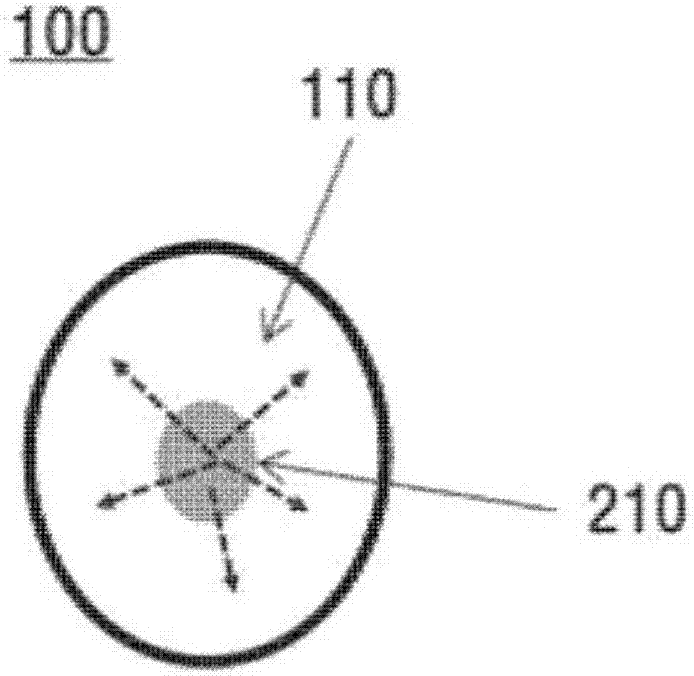
本发明涉及一种吸附剂,更具体地说,涉及一种具有改善的微波吸收性能的吸附剂。
背景技术:
:由于对大气环境的关注随着生活质量的提高而增加,对各种工业加工、涂覆设备、污水处理厂或焚烧厂中产生的挥发性有机化合物(voc)等空气污染物的排放规范条例进行了修订。对违反此类条例的公司施加强制性的行政措施例如暂停营业。因此,已经对去除这些挥发性有机化合物进行了大量研究。用于除去挥发性有机化合物的典型传统技术包括使用活性炭的吸附塔系统、蒸发系统、再生催化氧化(rco)系统和再生热氧化(rto)系统。然而,由于需要对其进行周期性更换,所以使用吸附塔导致维护成本增加。此外,蒸发系统和rco系统以及rto系统具有低能量效率的问题。为了解决上述现有技术问题,已经开发了使用微波去除挥发性有机化合物的技术。具体地说,使用微波除去挥发性有机化合物的技术包括将挥发性有机化合物吸附到吸附剂上并通过将挥发性有机化合物从吸附剂中解吸来除去挥发性有机化合物。在这种情况下,可以半永久地使用吸附剂,因为可以通过吸附和解吸来使吸附剂再生。为了使这种使用微波去除挥发性有机化合物的技术的效率最大化,需要对作为除去目标的有机化合物具有高吸附强度和高吸收微波的能力的吸附剂。同时,随着能源需求每年迅速增加,同时强调需要大量能源的技术的重要性,能源问题作为全球紧迫的问题出现。特别地,用于半导体和lcd工艺中的转子式除湿系统是消耗大量能量的代表性技术。为了解决这些能源相关问题,已经尝试开发能够使用微波来提高能量效率的节能除湿系统。在这种使用微波的除湿系统的情况下,还需要开发对水分具有优异的吸附强度并具有优异的吸收微波能力(吸附剂被用微波照射以再生)的吸附剂,从而进一步提高能量效率。技术实现要素:技术问题本发明旨在解决现有技术的问题,因此本发明的目的是提供一种具有优异的吸附微波(吸附剂被用微波辐射以将吸附材料脱附)性能对吸附材料具有优异的吸附强度的吸附剂。技术方案根据本发明的一个方面,提供一种具有微波吸收性能的吸附剂,其特征在于,该吸附剂具有核-壳结构,包括布置在其中的碳化硅珠粒以及布置在该碳化硅珠粒外部的吸附材料。在这种情况下,该吸附材料可以选自由沸石、活性氧化铝及其混合物组成的组。该碳化硅珠粒可以具有0.5mm至1.5mm的直径。当该吸附剂被用1kw的功率的微波照射60秒至90秒时,该吸附剂的温度升高可以在30℃至50℃的范围内。该吸附剂可以进一步包括分散并布置在该吸附材料中并且直径为1μm至10μm的多个碳化硅颗粒。基于100重量%的该吸附剂,可以以10重量%至15重量%的含量包括该碳化硅颗粒。当该吸附剂被用1kw的功率的微波照射60秒至90秒时,该吸附剂的温度升高可以在40℃至60℃的范围内。该吸附剂可以与阳离子进行离子交换。该阳离子可以是选自由钾(k)、银(ag)、钠(na)、钡(ba)、锂(li)、镁(mg)、锶(sr)、磷(p)、锰(mn)、钙(ca)和铁(fe)组成的组中的至少一种材料。该吸附剂可用于吸附挥发性有机化合物。该吸附剂中所含的吸附材料可以选自由si/al比为10-300的疏水性沸石、活性氧化铝及其混合物组成的组。该吸附剂可用于吸附水分。该吸附剂中所含的吸附材料可以选自由si/al比为1-10的亲水性沸石、活性氧化铝及其混合物组成的组。有益效果根据本发明的一个示例性实施方式的吸附剂能够用于提高解吸效率,这是由于对微波的反应性高,吸附剂可以通过微波被快速加热以达到解吸温度。此外,根据本发明的一个示例性实施方式的吸附剂能够用于保持完全吸附能力,而不会对吸附量产生影响,这是因为将碳化硅珠粒布置在吸附剂的内核中。此外,当将根据本发明的一个示例性实施方式的吸附剂应用于使用微波除去有机化合物的传统系统或除湿系统时,该吸附剂能够被半永久地使用,并且与在传统系统中使用的吸附剂相比也可以具有将能量效率提高30%以上的效果。然而,本发明的技术目的不限于此,对于本领域普通技术人员来说,本文中未公开的本发明的其它目的将通过详细描述本发明的示例性实施方式而变得更加显而易见。附图说明图1是示出根据本发明的一个示例性实施方式的具有改善的微波吸收性能的吸附剂的示意图,该吸附剂包括碳化硅珠粒。图2是示出根据本发明的一个示例性实施方式的微波能量被吸收到碳化硅珠粒中的流程的示意图。图3是示出根据本发明的一个示例性实施方式的具有改善的微波吸收性能的吸附剂的示意图,该吸附剂包括碳化硅珠粒和多个碳化硅颗粒。图4是示出根据本发明的另一个示例性实施方式的微波能量被吸收到碳化硅珠粒和碳化硅颗粒中的流程的示意图。图5是示出通过比较在本发明的实施例1和实施例2以及比较例1和比较例2中制备的吸附剂的微波吸收性能而得到的结果的图。图6是示出通过比较在本发明的实施例3和实施例4以及比较例3和比较例4中制备的吸附剂的微波吸收性能而得到的结果的图。图7是示出通过比较在本发明的实施例5和比较例5中制备的voc吸附剂的微波吸收性能而得到的结果的图。图8a和图8b是示出通过比较在本发明的实施例1和实施例2以及比较例3和比较例4中制备的吸附剂的微波吸收性能和吸附量而得到的结果的图。具体实施方式在下文中,将参照附图详细描述本发明的优选实施方式。虽然在附图中示出了本发明的某些示例性实施方式并且在下面进一步进行了详细描述,但是应当显而易见的是,可以对某些示例性实施方式进行各种改变和修改。然而,应当理解,本发明的范围并非旨在限于所公开的特定形式,并且本发明涵盖落入由所附权利要求限定的本发明的精神和范围内的所有修改、等价方案和替代方案。在附图中,为了便于说明,层和区域的厚度可能被夸大或缩小。在整个说明书中,相同或相应的元件具有相同或相似的附图标记。用于表示在本说明书中使用的吸附量的单位“mmol/g”和“kg/kg”可以是指相对于单位重量吸附剂的待吸收材料(例如,ipa或h2o)的量。本发明可以提供具有改善的微波吸收性能的吸附剂,其特征在于,所述吸附剂具有核-壳结构,包括布置在其内核中的碳化硅珠粒和布置在内核外部的吸附材料。吸附材料可以由对于气体或颗粒材料具有高吸附性能的材料构成,并且吸附材料可以是具有多个细孔的多孔材料。具体地,吸附材料可以选自由沸石、活性氧化铝及其混合物组成的组。已知沸石是其中硅(si)和铝(al)通过四个交联氧原子连接的三维(3d)无机聚合物。这里,由于铝与四个氧原子结合并带负电,所以沸石中存在多种阳离子以补偿这些负电荷。更具体地,由于阳离子存在于微孔内,并且其它空间通常充满水分子,所以阳离子在微孔中具有相对自由的迁移率,并且可以容易地与其它阳离子进行离子交换。此外,通过加热而被脱水的沸石的类型具有吸收尺寸不同的小分子(其能够通过微孔的入口)例如水分子的性能,并且用分子填充内部空的空间。因此,脱水沸石已被广泛用作吸附剂或吸收剂。通常,根据硅和铝的结构或比例,沸石的类型可分为β-沸石、a-沸石、zsm-5型沸石、x-沸石、y-沸石和l-沸石。在本发明中,可以根据吸附剂的使用目的来选择和使用能够容易地吸附待吸附材料的沸石的类型。具体地,根据本发明的一个示例性实施方式,可以使用β-沸石作为吸附挥发性有机化合物的材料,并且y-沸石可以用作用于吸附水分的材料。活性氧化铝通常由热处理的水合氧化铝产生,因此具有高的耐热性和宽的比表面积。特别地,由于活性氧化铝具有强吸湿力,所以活性氧化铝是被广泛用于除去压缩空气中的水分的吸附剂。图1是示出根据本发明的一个示例性实施方式的具有改善的微波吸收性能的吸附剂的示意图,该吸附剂包括碳化硅珠粒。参考图1,根据本发明,具有这种优异的吸附能力的吸附材料110可以布置在碳化硅珠粒210外部,碳化硅珠粒210布置在吸附剂100的内核中。具体地,碳化硅珠粒210可以由球形、珠状或不规则形状的碳化硅构成。碳化硅具有吸收微波的性质,并且在本发明中可以使用碳化硅的这种吸收微波的性质,使得碳化硅珠粒210布置在吸附剂100的内核中,从而改善吸附剂100的微波反应性。碳化硅珠粒210可以具有约0.5mm至1.5mm的直径。具体地说,当碳化硅珠粒210的直径小于0.5mm时,可能会降低碳化硅珠粒210吸收微波并将其加热至解吸温度的速度。另一方面,当碳化硅珠粒210的直径大于1.5mm时,吸附剂100中的吸附材料110的面积非常小,因此使吸附强度降低。结果,可以使用直径在该范围内的碳化硅珠粒210。如上所述,具有布置在其内核中的碳化硅珠粒和布置在其外部的吸附材料的吸附剂可以吸附诸如水分或挥发性有机化合物的各种待吸附材料。根据另一个示例性实施方式,该吸附剂可以以其能够被涂覆在载体上的任何形式形成。载体可以是金属泡沫、陶瓷泡沫或具有蜂窝结构的陶瓷,但是本发明不特别限于此。此外,该吸附剂可以通过使用各种加热装置对吸附到吸附剂上的材料进行解吸来再生,因此其可以被半永久地使用。具体地,根据本发明的一个示例性实施方式,用于使吸附剂解吸的加热装置可以是微波。具体地说,可以通过如下来使吸附剂再生:用微波加热吸附剂直到吸附剂被加热到可以将吸附到吸附剂上的材料从吸附剂解吸的预定范围内的解吸温度。例如,照射到吸附剂的微波可以具有约3kw或5kw的功率,并且可以根据吸附剂的类型被适当地改变和施加,但是本发明不特别限于此。在这种情况下,布置在吸附剂的内核中的碳化硅珠粒可以吸收辐射到吸附剂的微波以使吸附材料解吸。因此,辐射到吸附剂的微波可以通过具有吸收微波的性能的碳化硅珠粒和吸附剂的表面将微波能量从吸附剂的内核转移至布置在碳化硅珠粒外部的吸附材料。具体地说,如图2中所示,吸收到在吸附剂100的内核中布置的碳化硅珠粒210中的微波能量被转移至布置在碳化硅珠粒210外部的吸附材料110。在这种情况下,由于转移的微波能量,吸附剂100的整体温度可能快速增加,从而改善吸附剂的解吸效率。这解决了使用微波的传统吸附系统中的问题,其中辐射到吸附剂的微波由于吸附在吸附剂表面上的材料而聚集在吸附剂的表面上,因此需要大量的能量和时间来将吸附剂加热到解吸温度。根据本发明的一个示例性实施方式,当用1kw的功率的微波照射吸附剂60秒至90秒时,吸附剂的温度升高可以在30℃至50℃的范围内。如上所述,由于辐射到布置在吸附剂的内核中的碳化硅珠粒的微波的能量迅速转移至布置在内核外部的吸附材料,因此微波能量可以容易地转移至吸附剂整体。因此,只有该范围内的微波能量可以用于将吸附剂的温度提高到50℃至70℃的温度。在下文中,将参考以下实施例和附图详细描述具体内容。根据一个示例性实施方式,吸附剂可以进一步包括直径为1μm至10μm的多个碳化硅颗粒。在这种情况下,碳化硅粒子分散且布置在吸附材料中。图3是示出根据本发明的一个示例性实施方式的具有改善的微波吸收性能的吸附剂的示意图,该吸附剂包括碳化硅珠粒和多个碳化硅颗粒。参考图3,多个碳化硅颗粒230是指由细粉末形式的碳化硅(sic)构成的颗粒。在这种情况下,多个碳化硅颗粒230可以分散且布置在吸附材料中。像碳化硅珠粒210那样,碳化硅颗粒230可以吸收被辐射的微波能量以使吸附剂100解吸。因此,碳化硅颗粒230可以与布置在内核的碳化硅珠粒210一起容易地将微波能量转移至吸附材料110。具体地,如图4中所示,当用微波照射吸附剂100时,首先,一些微波能量被吸收到布置在吸附剂100的内核中的碳化硅珠粒210中,并且所吸收的微波能量可以转移至布置在碳化硅珠粒210周围的吸附材料110和碳化硅颗粒230。此外,当用微波照射吸附剂100时,一些微波能量也被吸收到布置在碳化硅珠粒210外部的碳化硅颗粒230中,并且所吸收的微波能量可以转移至布置在碳化硅颗粒230周围的吸附材料110。如上所述,因为由于这样的结构特征,辐射到吸附剂100的微波能量可以快速地转移到吸附剂100的整个区域,所以吸附剂100可以快速升温至解吸温度,从而促进吸附剂100的解吸速率的提高。更具体地,多个碳化硅颗粒230可以具有1μm至10μm的直径。当碳化硅颗粒的直径小于1μm时,碳化硅颗粒可能被吸附在吸附剂上的材料容易地分离。另一方面,当碳化硅颗粒的直径大于10μm时,当吸附剂中的吸附材料的面积较小时,吸附强度可能降低。因此,可以使用直径在该范围内的碳化硅颗粒。根据本发明的一个示例性实施方式,基于100重量%的吸附剂,可以以10重量%至15重量%的含量包括碳化硅颗粒。具体地说,当碳化硅颗粒的含量低于10重量%时,难以将碳化硅颗粒均匀地分散且布置在吸附剂中。另一方面,当碳化硅颗粒的含量高于15重量%时,可能减少吸附面积。因此,在吸附剂中可以包含在该含量范围内的碳化硅颗粒。根据本发明的一个示例性实施方式,将碳化硅珠粒布置在吸附剂的内核中,并且将吸附材料布置在碳化硅珠粒210的外部。在这种情况下,当其中分散布置有多个碳化物颗粒的吸附剂被用1kw的微波照射60秒至90秒时,吸附剂的温度升高可以在40℃至60℃的范围内。如上所述,由于辐射到吸附剂的微波可以通过布置在吸附剂的内核中的碳化硅珠粒从吸附剂的内核迅速转移到布置在内核外部的吸附材料,只有在该范围内的微波能量可用于将吸附剂的温度升高至60℃至80℃的温度。在下文中,将参考以下实施例和附图详细描述具体内容。根据一个示例性实施方式,吸附材料可以与阳离子进行离子交换。具体地说,阳离子可以是选自由钾(k)、银(ag)、钠(na)、钡(ba)、锂(li)、镁(mg)、锶(sr)、磷(p)、锰(mn)、钙(ca)和铁(fe)组成的组中的至少一种材料。如上所述,与阳离子进行离子交换的吸附材料可以具有增加的对微波的反应性,从而改善微波吸收力。例如,当使用沸石作为吸附材料并与钾进行离子交换时,随着沸石的结构从钠泡沫转化为钾泡沫,吸收剂的微波吸附能力可以提高。因此,沸石可以与辐射到吸附材料或由碳化硅珠粒和碳化硅颗粒转移到吸附材料的微波反应,以迅速升高吸附材料的温度。在下文中,将参考以下实施例和附图详细描述具体内容。根据本发明的一个示例性实施方式,吸附剂可用于吸收挥发性有机化合物。具体地,挥发性有机化合物可包括乙炔、乙醛、苯、1,3-丁二烯、丁烷、1-丁烯、2-丁烯、环己烷、乙烯、甲醛、正己烷、异丙醇、甲醇、甲乙酮、氧化丙烯、乙基苯、盐酸(hcl)、甲苯、二甲苯、苯乙烯或其混合物,但本发明并不特别限于此。当吸附剂用于吸收挥发性有机化合物时,吸附剂的吸附材料可以由能够容易地吸收挥发性有机化合物的材料组成。具体地说,吸附剂中所含的吸附材料可以是si/al比为15-300的疏水性沸石、活性氧化铝或其混合物。根据本发明的另一个示例性实施方式,吸附剂可用于吸收水分。当吸附剂用于吸收水分时,吸附剂的吸附材料可以由能够容易吸收水分的材料组成。具体地,吸附剂中所含的吸附材料可以是si/al比为1-10的亲水性沸石、活性氧化铝或其混合物。如上所述,在根据本发明的一个示例性实施方式的吸附剂中,吸附材料可以根据待吸收材料的类型(即,挥发性有机化合物或水分)而变化,以提供对待吸收的材料的优异的吸附强度。此外,由于通过碳化硅珠粒和/或碳化硅颗粒可以增强对微波的反应性,和/或如上所述与阳离子的离子交换,吸附剂可以积极地用于使用微波除去挥发性有机化合物的系统或除湿系统。实施例在下文中,提供优选实施方式以有助于理解本发明。然而,应当理解,本文提供的详细描述仅旨在提供对本发明的更好理解,并非旨在限制本发明的范围。[实施例]<实施例1:制备包括碳化硅珠粒的voc吸附剂>制备直径为1mm的碳化硅珠粒,并且通过使用无机吸附粘合剂例如10%-15%的铝溶胶用作为吸附材料的si/al比为112的β-沸石涂覆碳化硅珠粒的外部而将吸附剂成型以致吸附剂具有核-壳结构。将成型的吸附剂在110℃下干燥,并在550℃下煅烧以烧除粘合剂,从而制得直径为3mm的珠状voc吸附剂,其中沸石和碳化硅以9:1的重量比混合。<比较例1:制备不含碳化硅珠粒的voc吸附剂>制备由si/al比为112的β-沸石作为吸附材料构成的直径为3mm的珠状voc吸附剂。<实施例2:制备含有碳化硅珠粒的水分吸附剂>制备直径为1mm的碳化硅珠粒,并且通过使用无机吸附粘合剂例如10%-15%的铝溶胶用作为吸附材料的si/al比为5的y-沸石涂覆碳化硅珠粒的外部而将吸附剂成型以致吸附剂具有核-壳结构。将成型的吸附剂在110℃下干燥,并在550℃下煅烧以烧除粘合剂,从而制得直径为3mm的珠状水分吸附剂,其中沸石和碳化硅以9:1的重量比混合。<比较例2:制备不含碳化硅珠粒的水分吸附剂>制备由si/al比为5的y-沸石构成的直径为3mm的珠状voc吸附剂。图5是示出通过比较在本发明的实施例1和实施例2以及比较例1和比较例2中制备的吸附剂的微波吸收性能而得到的结果的图。更具体地,将100g各吸附剂加入到烧杯中,用1kw功率的微波照射吸附剂1分钟,比较反应后的吸附剂的温度,并在图中示出。具体地,结果如下表1所列。[表1]项目比较例1实施例1比较例2实施例2反应前温度(℃)25252525反应后温度(℃)40585072温度变化(℃)15332547ipa或h2o吸附量0.8mmol/g0.78mmol/g0.12kg/kg0.11kg/kg参考图5和表1,通过比较在比较例1中制备的voc吸附剂和在实施例1中制备的含碳化硅珠粒的voc吸附剂的微波吸收性能,可以看出用微波照射后比较例1中制备的voc吸附剂的温度为40℃,表明与用微波照射前的温度相比,voc吸附剂的温度升高了约15℃。另一方面,可以看出实施例1中制备的吸附剂(在其内核中布置有碳化硅珠粒)在用微波照射后的温度为58℃,表明与用微波照射前的温度相比,吸附剂的温度增加约33℃。此外,使相同量的异丙醇(ipa)吸附到吸附剂上以比较voc吸附量。结果,可以看出,比较例1的voc吸附剂的ipa吸附量为0.8mmol/g,实施例1的voc吸附剂的ipa吸附量为0.78mmol/g。此外,将在比较例2中制备的水分吸附剂和在实施例2中制备的包括碳化硅珠粒的水分吸附剂的微波吸收性能进行了比较。结果,可以看出,在比较例2中制备的吸附剂在用微波照射后的温度为50℃,表明吸附剂的温度升高了约25℃。另一方面,可以看出,在实施例2中制备的吸附剂(在其内核中布置有碳化硅珠粒)在用微波照射之后的温度为72℃,表明吸附剂的温度增加约47℃。此外,使相同量的水分吸附到吸附剂上。结果,可以看出,比较例2的吸附剂的水分吸附量为0.12mmol/g,实施例2的吸附剂的水分吸附量为0.11mmol/g。如上所述,表明在本发明实施例1中制备的voc吸附剂和在实施例2中制备的水分吸附剂包括具有微波吸附能力的碳化硅结构,即其中碳化硅珠粒布置在其内核中的结构,从而使吸附剂的内核能够吸收微波能量。此外,微波能量能够容易地从内核转移到内核的外部,使得吸附剂具有改善的微波吸收性能。因此,voc吸附剂在解吸时对于辐射到吸附剂的微波具有高反应性,因此与在比较例1和比较例2中制备的吸附剂相比,吸附剂的温度能够升高到更高的程度。结果,解吸温度能够使用少量的微波能量而迅速升高。此外,在本发明的实施例1中制备的voc吸附剂和在实施例2中制备的水分吸附剂具有其内核中布置有具有微波吸收能力的碳化硅珠粒的结构,但实施例2的水分吸附剂具有与传统吸附剂相似的吸附或除湿量。如上所述,确认了在本发明的实施例1中制备的voc吸附剂和在实施例2中制备的水分吸附剂能够在保持吸附剂的吸附能力的同时具有改善的解吸效率,从而提高使吸附剂再生的能量效率。<实施例3:制备包含碳化硅珠粒和分散的碳化硅颗粒的voc吸附剂>制备直径为1mm的碳化硅珠粒,将直径为10μm的碳化硅颗粒与作为吸附材料的si/al比为112的β-沸石物理混合。然后,使用无机吸附粘合剂例如10%-15%的铝溶胶,通过将混合有沸石和碳化硅颗粒的混合物涂覆在碳化硅珠粒的外部而将吸附剂成型使得吸附剂具有核-壳结构,将成型的吸附剂在110℃下干燥,并在550℃下煅烧以烧除粘合剂,从而制得直径为3mm的珠状voc吸附剂。<实施例4:制备包括碳化硅珠粒和分散的碳化硅颗粒的水分吸附剂>制备直径为1mm的碳化硅珠粒,将直径为10μm的碳化硅颗粒与作为吸附材料的si/al比为5的y-沸石物理混合。然后,使用无机吸附粘合剂例如10%-15%的铝溶胶,通过用沸石和碳化硅颗粒的混合物涂覆碳化硅珠粒的外部而将吸附剂成型使得吸附剂具有核-壳结构,将成型的吸附剂在110℃下干燥,并在550℃下煅烧以烧除粘合剂,从而制得直径为3mm的珠状水分吸附剂。图6是示出通过比较在本发明的实施例3和实施例4以及比较例1和比较例2中制备的吸附剂的微波吸收性能而得到的结果的图。更具体地,将100g各吸附剂加入到烧杯中,用1kw功率的微波照射吸附剂1分钟,比较反应后的吸附剂的温度并在图中示出。具体地,结果如下表2中所示。[表2]参考图6和表2,将在比较例1中制备的voc吸附剂和在实施例3中制备的包括碳化硅珠粒和碳化硅颗粒的voc吸附剂的微波吸收性质进行比较,可以看出,在比较例1中制备的voc吸附剂在用微波照射后的温度为40℃,表明与用微波照射前的温度相比,voc吸附剂的温度升高了约15℃。另一方面,可以看出,在实施例3中制备的吸附剂(其中在其内核中布置有碳化硅珠粒并且在吸附材料中分散有碳化硅颗粒)在用微波照射后的温度为74℃,表明与用微波照射前的温度相比,吸附剂的温度升高了约49℃。此外,使相同量的异丙醇(ipa)吸附到吸附剂上以比较voc吸附量。结果,可以看出,比较例1的voc吸附剂的ipa吸附量为0.8mmol/g,实施例3的voc吸附剂的ipa吸附量为0.61mmol/g。此外,将在比较例2中制备的水分吸附剂与在实施例4中制备的包括碳化硅珠粒和碳化硅颗粒的水分吸附剂的微波吸收性能进行了比较。结果,可以看出,在比较例2中制备的吸附剂在用微波照射后的温度为50℃,表明吸附剂的温度升高了约25℃。另一方面,可以看出,在实施例4中制备的的吸附剂(其中在其内核中布置有碳化硅珠粒并且在吸附材料中分散有碳化硅颗粒)在用微波照射后的温度为85℃,表明吸附剂的温度升高了约60℃。此外,使相同量的水分吸附到吸附剂上。结果,可以看出,比较例2的吸附剂的水分吸附量为0.12kg/kg,实施例4的吸附剂的水分吸附量为0.089kg/kg。如上所述,表明在本发明的实施例3中制备的voc吸附剂和在实施例4中制备的水分吸附剂具有由具有微波吸附能力的碳化硅构成的碳化硅结构,即其中粉末碳化硅颗粒与碳化硅珠粒一起布置在其内核中的结构,从而将布置在吸附剂内核中的碳化硅珠粒中所吸收的微波能量转移至布置在碳化硅珠粒外部的吸附材料。此外,微波能量能够容易地从内核转移至吸收材料,使得吸附剂具有改善的微波吸收性能。碳化硅颗粒本身能够容易地吸收微波,使得吸附剂整体上具有改善的微波吸收性能。因此,如上所述,表明voc吸附剂在解吸时对于辐射到吸附剂的微波具有高反应性,因此与在比较例1和比较例2中制备的吸附剂相比,吸附剂的温度能够升高到更高的程度。结果,解吸温度能够使用少量的微波迅速升高。此外,与在比较例1和比较例2中制备的吸附剂相比,在本发明的实施例3中制备的吸附剂和在实施例4中制备的水分吸附剂的吸附量或除湿量降低了约0.19mmol/g和0.31kg/kg,但是在用微波照射时,实施例3和实施例4的吸附剂的温度比比较例1和比较例2的吸附剂的温度高得多。因此,可以看出,与比较例1和比较例2的吸附剂相比,在实施例3和实施例4的吸附剂的情况下能够进一步节约能量,表明实施例3和实施例4的吸附剂比比较例1和比较例2的吸附剂具有更好的能量效率。<实施例5:与钾进行离子交换的voc吸附剂>向500cc蒸馏水中加入200g作为吸附材料的si/al比为112的β-沸石,注入0.2mkno3溶液,在室温下搅拌24小时。用蒸馏水将搅拌后的吸附剂过滤5次,在110℃下干燥10小时,然后在550℃下煅烧,制得与钾进行了离子交换的直径3mm的珠状voc吸附剂。图7是示出通过比较在本发明的实施例5和比较例1中制备的voc吸附剂的微波吸收性能而得到的结果的图。更具体地,将100g各吸附剂加入到烧杯中,用1kw功率的微波照射吸附剂1分钟,比较反应后的吸附剂的温度,并在图中示出。具体地,结果如下表3所示。[表3]项目比较例1实施例5反应前温度(℃)2525反应后温度(℃)4068温度变化(℃)1543ipa吸附量(mmol/g)0.80.81参考图7,可以看出,在比较例1中制备的voc吸附剂在微波照射后的温度为40℃,表明与用微波照射前的温度相比,voc吸附剂的温度升高了约15℃。另一方面,可以看出,在实施例5中制备的与钾进行了离子交换的voc吸附剂在用微波照射后的温度约为68℃,表明与用微波照射前的温度相比,voc吸附剂的温度升高了约43℃。此外,使相同量的异丙醇(ipa)吸附到吸附剂上以比较voc吸附量。结果,可以看出,比较例1的voc吸附剂的ipa吸附量为0.8mmol/g,实施例5的voc吸附剂的ipa吸附量为0.81mmol/g。如上所述,可以看出,当吸附剂与阳离子例如钾进行了离子交换时,在本发明的实施例5中制备的吸附剂具有改善的微波吸收性能。此外,与在比较例1中制备的吸附剂相比,可以看出在本发明实施例5中制备的吸附剂的吸附量增加了0.01mmol/g。基于这些事实揭示出:当根据本发明的一个示例性实施方式的吸附剂与阳离子进行了离子交换时,借助在本发明中公开的碳化硅结构(碳化硅珠粒和碳化硅颗粒),吸附剂的脱附效率能够得以改善,使得吸附剂具有改善的微波吸收性能。<比较例3:制备包括碳化硅颗粒的voc吸附剂>将直径为10μm的碳化硅颗粒与作为吸附材料的si/al比为112的β-沸石物理混合,以制备直径为3mm的珠状voc吸附剂,其中沸石和碳化硅为以9:1的重量比混合。<比较例4:制备包含碳化硅颗粒的水分吸附剂>将直径为10μm的碳化硅颗粒与作为吸附材料的si/al比为5的y-沸石物理混合,制备直径为3mm的珠状voc吸附剂,其中将沸石和碳化硅以9:1的重量比混合。图8a和图8b是示出通过比较在本发明的实施例1和实施例2以及比较例3和比较例4中制备的吸附剂的微波吸收性能和吸附量而获得的结果的图。在这种情况下,将100g各吸附剂加入到烧杯中,用1kw功率的微波照射吸附剂1分钟,比较反应后的吸附剂的温度并在图中示出。具体地,结果如下表4中所列。在图8a和图8b中,这些线表示根据用微波照射的吸附剂的温度变化,条形图表示吸附剂的吸附量。[表4]项目比较例3实施例1比较例4实施例2反应前温度(℃)25252525反应后温度(℃)65587872温度变化(℃)40335347ipa或h2o吸附量0.65mmol/g0.78mmol/g0.089kg/kg0.11kg/kg参考图8a和图8b以及表4,将在比较例3中制备的包括碳化硅颗粒的voc吸附剂和在实施例1中制备的包括碳化硅珠粒的voc吸附剂的微波吸收性能进行比较,可以看出,在比较例3中制备的voc吸附剂在用微波照射后的温度为65℃,表明与用微波照射之前的温度相比,voc吸附剂的温度升高了约40℃。另一方面,可以看出,在实施例1中制备的吸附剂(在其内核中布置有碳化硅珠粒)在用微波照射后的温度为58℃,表明与用微波照射前的温度相比,吸附剂的温度升高了约33℃。此外,使相同量的异丙醇(ipa)吸附到吸附剂上以比较voc吸附量。结果,可以看出,比较例1的voc吸附剂的ipa吸附量为0.65mmol/g,实施例1的voc吸附剂的ipa吸附量为0.78mmol/g。此外,将在比较例4中制备的包括碳化硅颗粒的水分吸附剂和在实施例2中制备的包括碳化硅珠粒的水分吸附剂的微波吸收性能进行了比较。结果,可以看出,在比较例4中制备的吸附剂在用微波照射后的温度为78℃,表明吸附剂的温度升高了约53℃。另一方面,可以看出,在实施例2中制备的吸附剂(在其内核中布置有碳化硅珠粒)在用微波照射之后的温度为72℃,表明吸附剂的温度升高了约47℃。此外,使相同量的水分吸附在吸附剂上。结果,可以看出,比较例4的吸附剂的水分吸附量为0.089kg/kg,实施例2的吸附剂的水分吸附量为0.011kg/kg。如上所述,表明因为在比较例3和比较例4中制备的传统吸附剂(其中碳化硅颗粒与吸附材料物理混合)由于碳化硅颗粒的存在而具有改善的微波反应性,所以在用微波照射时吸附剂的温度更大程度地升高,但是由于碳化硅颗粒在吸附剂中的随机分散使得吸附材料能够被吸附到的吸附面积显著减小。因此,验证了比较例3和比较例4的吸附剂的吸附量比本发明的实施例1和实施例2的吸附剂的吸附量低得多。另一方面,表明在本发明的实施例1中制备的voc吸附剂和在实施例2中制备的水分吸附剂能够具有用于使吸附剂再生的优异的能量效率,因为具有微波吸收能力的碳化硅珠粒被布置在吸附剂的内核中,使得可以提高吸附剂的微波吸收性能,并且可以保持吸附剂的完全吸附和除湿量,如图5中所示。工业适用性已经详细描述了本发明。然而,应当理解,尽管说明了本发明的优选实施方式,但是详细描述和具体实施例仅以说明的方式给出,并且从该详细描述中,在本发明的精神和范围内的各种改变和修改对于本领域技术人员将是显而易见的。当前第1页12