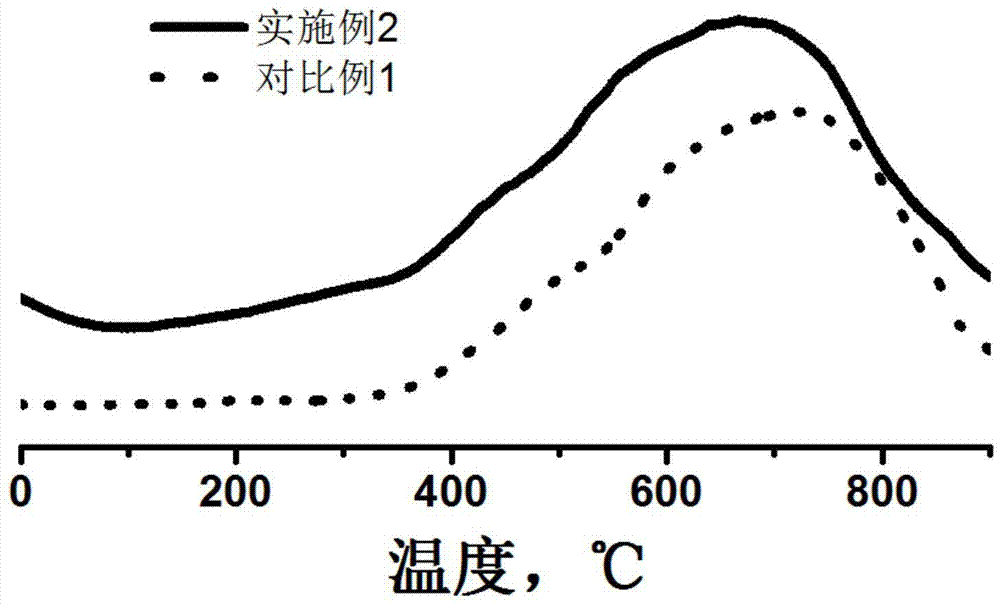
本发明为催化剂领域,涉及一种加氢催化剂及其制备方法。
背景技术:
:随着我国执行的汽柴油质量标准日益严格,以及环境保护法规的不断严苛,目前炼厂的加氢处理装置已经非常普及。加氢处理催化剂作为加氢处理装置的核心,其活性的高低直接影响加氢处理装置产品质量的高低,同时也影响炼厂的能耗、物耗。目前开发高活性加氢处理催化剂成为行业的热点,高活性加氢处理催化剂的开发主要包括载体制备及活性相的研究等,通过文献调研及实验研究发现,通过超声强化及一段分散的方法能够提高加氢处理催化剂活性组分的高度分散,从而提高了催化剂的加氢活性。专利cn100457271c公开了一种负载型催化剂的干燥方法,以及一种中油型加氢裂化催化剂的制备方法,在干燥过程中使用适宜条件的超声波辐射,使催化剂的活性和选择性得到提高。专利cn100594059c公开了超声波辅助制备nib非晶态合金催化剂的方法,在超声波输出功率为40-300w的条件下,所制备的nib非晶态合金催化剂具有活性组分尺度小,分散度好,催化剂活性高,且使用安全等优点。专利cn1393523a公开了一种加氢裂化催化剂的处理方法,其载体为分子筛材料,同时提高了催化剂的裂化和异构性能。专利cn102284300a中公开了一种w-mo-ni-p为活性相的加氢处理催化剂,其主要是添加了稀土、碱金属等助剂,并在载体中添加了硅铝,其催化剂活性得到提高,同时增加了催化剂制造成本。专利cn105419858a公开了一种第vib族金属和第viii族金属元素,并含有分子筛材料,进行水热处理来提高催化剂的加氢活性。专利cn1065457223a公开一种采用独特的金属石煅烧方法,此方法制备的加氢催化剂具有更低的重量百分比烧失重,更高的活性和更长的寿命。专利cn106268782a采用氧化镁、二氧化锰及氧化镧为活性组分,纳米氧化铝为载体,提高了催化剂的利用率。专利cn106238029a公开了一种氧化铝与聚乙烯醇的混合物再与金属元素混合制得加氢处理催化剂的方法。专利cn106582694a公开一种添加助剂的三元金属加氢处理催化剂的制备方法,以聚乙二醇为分散剂,达到提高催化剂的深度加氢脱硫效果。zl200410091490.7公开了一种含分子筛的加氢脱硫催化剂,催化剂的载体采用氧化铝(催化剂重量的20.0wt%~80.0wt%)和ets-10分子筛(催化剂重量的0.5wt%~50.0wt%)进行制备,通过调整载体中的氧化铝和ets-10分子筛相对含量,并对ets-10分子筛进行改性来制备加氢脱硫催化剂载体,可提高常规加氢脱硫催化剂的脱硫活性。cn105772109a公开了一种载体制备方法为:首先将高硅铝比的小颗粒的y分子筛进行硝酸铵接触交换;然后将交换的y分子筛进行锆改性,得到锆改性y分子筛;将该锆改性y分子筛与拟薄水铝石、助挤剂、粘结剂进行混合,然后再挤条烘干焙烧,制备得到加氢脱硫催化剂的载体。该发明提供的加氢脱硫催化剂的载体具有锆改性y分子筛,该载体制备的加氢脱硫催化剂脱硫活性高,脱硫效果好;并且该载体制备的加氢脱硫催化剂用于加氢脱硫反应,柴油的收率均在100%以上。cn103480408a公开了一种含稀土的柴油馏分油加氢催化剂及其制备和应用;该催化剂是由稀土改性的usy分子筛、无定型硅铝、大孔氧化铝和加氢活性组分组成,其中加氢活性组分为第viii族金属,催化剂中含稀土改性的usy分子筛5-60wt%,含无定型硅铝5-80wt%,含第viii族金属0.1-10wt%,余量为大孔氧化铝;该催化剂具有较佳的加氢、异构和芳烃选择性开环活性,处理fcc加氢精制柴油馏分油时,在较缓和的反应条件下,能显著提高十六烷值,降低凝点,提高产品质量,并保持柴油收率95%以上,稀土元素的加入提高催化剂的活性和寿命,特别适合于柴油两段加氢改质中第二段的芳烃深度加氢饱和继而选择性开环。cn102284300a公开了一种劣质柴油加氢催化剂及制备方法;该催化剂以w-mo-ni-p为活性组分,以碱金属、碱土金属或稀土金属为助剂,以硅铝为载体,按重量百分比,碱金属、碱土金属或稀土金属为0.2~10%、wo3为5%~25%、moo3为8~20%、nio为2~9%、p为1.0~5%,余量为硅铝氧化物载体;用于评价原料油为催化裂化和焦化柴油的混合油,该催化剂在条件及稳定性试验中表现出良好的反应活性和稳定性,能脱除劣质混合柴油中90%以上的硫、氮。cn102211029a公开了一种柴油加氢脱硫硫化物催化剂的制备方法,以金属ni或co和mo和ru为活性组分,al2o3为载体,配置钼酸铵的乙二胺溶液,加入载体浸渍后,加入0.1mol/l的kbh4溶液,mo∶b的摩尔比为1∶4,将所得沉淀水洗后,在110℃烘箱中烘干得到催化剂前躯体;配置硝酸镍和硝酸钌的乙二胺混合溶液,向溶液中加入催化剂前躯体进行等体积浸渍,所得沉淀再自然晾干,120℃烘干,在450℃焙烧,在h2s气氛下350℃下硫化得催化剂;按催化剂重量比mo为3~20%;ni或co为3~10%;ru为0.1~3%;al2o3为余量;催化剂具有高的加氢脱硫活性,用于加氢精制和原料预精制加氢脱硫。cn200810113646.5公开了一种柴油加氢精制催化剂,该催化剂由载体和活性组分构成,所述活性组分为第vib族金属和第viii族金属中的一种或多种,其中所述载体由具有一维孔道的sapo-5、sapo-11、zsm-22、zsm-23分子筛的一种或多种和γ-al2o3组成。该发明还在公开上述柴油加氢精制加氢催化剂的基础上进一步公开了上述催化剂的制备方法。使用上述制备方法制备得到的柴油加氢精制催化剂能够在防止柴油馏分裂解、实现劣质柴油芳烃加氢饱和的同时,有效实现对劣质柴油进行脱硫和脱氮。cn200910188174.4公开了一种体相超深度加氢脱硫催化剂及其制备方法。该催化剂组成包括复合氧化物nixwyoz、moo3、氧化铝及微孔和中孔复合分子筛。该方法是在ni、w和al沉淀过程中加入适量的水溶性含氮化合物,成胶后,加入复合分子筛浆液,经老化,再与moo3打浆后,经成型、活化而制得。该方法不但改善了催化剂的孔结构,使更多的金属活性位暴露在催化剂的表面,提高了活性金属的利用率,而且还使复合分子筛和加氢活性金属均匀、充分地接触,并与加氢活性金属更好的配合,充分发挥复合分子筛的性能,达到柴油超深度脱硫的效果,尤其在处理大分子含量较多的馏分油时效果更明显,可以将柴油的硫含量降到10μg/g以下。201110197778.2公开了一种具有贯通的大中孔的催化剂载体的制备方法,该方法包括:在催化剂载体制备或成型过程中加入固体纤维丝,使固体纤维丝分散在催化剂载体中,然后经成型、焙烧除去固体纤维丝,即得到具有贯通的大中孔的催化剂载体。该发明还提供了将该载体进一步担载活性组分制备催化剂的方法,还提供了按照该发明的方法制备得到的载体与催化剂。利用该发明的方法,固体纤维丝的加入极大地改善了载体中孔道的贯通性能。纤维丝产生的贯通大孔提供了反应分子的快速扩散通道,从而降低了催化反应过程的传质阻力。本方法适用于制备反应速度受内扩散控制的各种催化剂,例如石油馏份(特别是重质油馏份)加氢催化剂。以上专利分别采用不同的制备方法及改性方法来制备柴油深度加氢脱硫催化剂,但是均未改善减少催化剂负载时浸渍法所带来的浸渍效应及活性组分团簇作用。技术实现要素:本发明的主要目的在于提供一种加氢催化剂及其制备方法,以克服现有技术中催化剂负载时浸渍带来的浸渍效应及活性组分团簇作用。为了达到上述目的,本发明提供了一种加氢催化剂的制备方法,该制备方法包括如下步骤:步骤1,将催化剂载体浸渍活性组分,该浸渍在超声波下进行,超声波频率为20~150khz,声强为0.2~1.0w/cm2,浸渍时间为0.25~3.0小时,然后进行干燥。本发明所述的加氢催化剂的制备方法,其中,所述活性组分优选为钼、钨、钴和镍所组成群组中的一种或几种,所述钼以三氧化钼计,所述钨以三氧化钨计,所述钴以氧化钴计,所述镍以氧化镍计,以加氢催化剂的总质量为基准,所述活性组分的质量含量为小于或等于20%。其中,步骤1所述超声波频率优选为20~80khz,声强优选为0.2~0.6w/cm2,浸渍时间优选为0.25~1.0小时。其中,步骤1所述干燥的温度优选为250℃~380℃,干燥的时间优选为5~6小时。本发明所述的加氢催化剂的制备方法,其中,所述活性组分优选为钼、钨、钴和镍所组成群组中的一种或几种,所述钼以三氧化钼计,所述钨以三氧化钨计,所述钴以氧化钴计,所述镍以氧化镍计,以加氢催化剂的总质量为基准,所述活性组分的质量含量为大于20%,该加氢催化剂的制备方法还包括步骤2:步骤2,将步骤1干燥后的催化剂载体加入分散剂溶液中进行再次浸渍,该再次浸渍在超声波下进行,超声波频率为20~50khz,声强为0.2~0.4w/cm2,浸渍时间为0~3.0小时,最后进行干燥得到加氢催化剂。其中,所述步骤1中超声波频率为80~150khz,声强为0.6~1.0w/cm2,浸渍时间为1.0~3.0小时,干燥的温度优选为120℃~170℃,干燥的时间优选为4~8小时,步骤2所述干燥的温度优选为320℃~430℃,干燥的时间优选为4~6小时。本发明所述的加氢催化剂的制备方法,其中,所述分散剂溶液中包括分散剂,所述分散剂优选为柠檬酸、乙二胺四乙酸、酒石酸和草酸所组成群组中的一种或几种,所述分散剂溶液的浓度优选为所述活性组分的质量含量的0.0002~0.001倍。本发明所述的加氢催化剂的制备方法,其中,所述催化剂载体优选为单组分氧化物载体、复合氧化物载体或介孔沸石材料载体;所述单组分氧化物载体为:γ-氧化铝、tio2、zro2或sio2,所述复合氧化物载体为:zro2-al2o3、mgo-al2o3、或tio2-γ-al2o3-sio2,所述介孔沸石材料载体为:mey、usy或介孔分子筛。为了达到上述目的,本发明还提供了上述的加氢催化剂的制备方法制备的加氢催化剂。本发明的有益效果:1、本发明公开了一种加氢催化剂的制备方法,该方法主要将活性组分的含量与活性组分浸渍时超声波条件相结合,再将超声分散与分散剂分散相结合,并严格控制干燥条件,从而有效地避免了浸渍过程中的浸渍效应和活性组分团聚作用,有效提高了加氢催化剂活性组分的分散性能。2、本发明方法制备的催化剂不进行高温焙烧,只需依据催化剂上活性组分的范围,选择不同的超声参数,不同浓度范围的分散剂,不同的干燥温度及时间,经处理后催化剂的活性组分分散性提高,加氢活性剂稳定性提高。附图说明图1为实施例2与对比例1催化剂tpr对比图;图2为实施例6与对比例2催化剂tpr对比图。具体实施方式以下对本发明的实施例作详细说明:本实施例在以本发明技术方案为前提下进行实施,给出了详细的实施方式和过程,但本发明的保护范围不限于下述的实施例,下列实施例中未注明具体条件的实验方法,通常按照常规条件。本发明提供了一种加氢催化剂的制备方法,该加氢催化剂包括催化剂载体和活性组分,活性组分为钼、钨、钴和镍,钼以三氧化钼计,钨以三氧化钨计,钴以氧化钴计,镍以氧化镍计,以加氢催化剂的总质量为基准,活性组分的质量含量为小于或等于20%,该制备方法包括如下步骤:步骤1,将催化剂载体浸渍活性组分,该浸渍在超声波下进行,超声波频率为20~150khz,声强为0.2~1.0w/cm2,浸渍时间为0.25~3.0小时,然后进行干燥。其中,超声波频率优选为20~80khz,声强优选为0.2~0.6w/cm2,浸渍时间优选为0.25~1.0小时。其中,干燥的温度优选为250℃~380℃,干燥的时间优选为5~6小时。本发明还提供了一种加氢催化剂的制备方法,该加氢催化剂包括催化剂载体和活性组分,活性组分为钼、钨、钴和镍,钼以三氧化钼计,钨以三氧化钨计,钴以氧化钴计,镍以氧化镍计,以加氢催化剂的总质量为基准,所述活性组分的质量含量为大于20%,该加氢催化剂的制备方法包括如下步骤:步骤1,将催化剂载体浸渍活性组分,该浸渍在超声波下进行,超声波频率为20~150khz,声强为0.2~1.0w/cm2,浸渍时间为0.25~3.0小时,然后进行干燥。步骤2,将步骤1干燥后的催化剂载体加入分散剂溶液中进行再次浸渍,该再次浸渍在超声波下进行,超声波频率为20~50khz,声强为0.2~0.4w/cm2,浸渍时间为0~3.0小时,最后进行干燥得到加氢催化剂。其中,步骤1中超声波频率优选为80~150khz,声强优选为0.6~1.0w/cm2,浸渍时间优选为1.0~3.0小时。步骤1干燥的温度优选为120℃~170℃,干燥的时间优选为4~8小时。步骤2干燥的温度优选为320℃~430℃,干燥的时间优选为4~6小时。其中,分散剂溶液中包括分散剂,分散剂优选为柠檬酸、乙二胺四乙酸、酒石酸和草酸所组成群组中的一种或几种,所述分散剂溶液的浓度为所述活性组分质量分数的0.0002~0.001倍。本发明的催化剂载体可以为单组分氧化物载体、复合氧化物载体或介孔沸石材料载体;单组分氧化物载体为:γ-氧化铝、tio2、zro2或sio2,复合氧化物载体为:zro2-al2o3、mgo-al2o3、或tio2-γ-al2o3-sio2,介孔沸石材料载体为:mey、usy或介孔分子筛。本发明采用上述加氢催化剂的制备方法能够提高加氢催化剂活性组分的分散性能。该方法主要是通过在催化剂载体多次浸渍活性组分过程中超声波强化处理,增加活性组分的分散,还同时辅助二次浸渍分散剂超声强化,进一步分散活性组分,该方法制备的催化剂不进行高温焙烧,只需依据催化剂上活性组分的范围,选择不同的超声参数,不同浓度范围的分散剂,不同的干燥温度及时间。经处理后催化剂的活性组分分散性提高,加氢活性剂稳定性提高。本发明的一种加氢处理催化剂活性组分高度分散的制备方法,该方法通过超声波手段强化活性组分浸渍过程及依据活性组分总量的高低,进一步采取分散手段,同时辅以超声波强化,活化阶段采用高温干燥,避免了大于500℃的焙烧,使处理后的加氢处理催化剂的活性组分实现高度分散,进而提高了催化剂的加氢处理活性。为了进一步说明本发明,列举以下实施例,但它并不限制各附加权利要求所定义的发明范围。实施例中的浸渍方式均采用等体积浸渍的方式进行。实施例1:以催化剂-1的总质量为基准,催化剂-1活性组分的质量含量设计值为15wt%(其中,氧化钨为8wt%,氧化钼为4wt%,氧化镍为3wt%),催化剂载体为γ-氧化铝,催化剂-1的活性组分的质量含量≤20%,采用一段浸渍后活化的工序对催化剂进行处理,一段浸渍阶段的超声波频率为20khz,超声波声强为0.2w/cm2,超声时间为0.25小时,活化工序的干燥温度为250℃,干燥时间为5小时,制得催化剂-1。实施例2:以催化剂-2的总质量为基准,催化剂-2活性组分的质量含量设计值为18wt%(其中,氧化钼为15wt%,氧化镍为3wt%),催化剂载体为zro2-al2o3,则催化剂-2的活性组分的质量含量≤20%,采用一段浸渍后活化的工序对催化剂进行处理,一段浸渍阶段的超声波频率为50khz,超声波声强为0.5w/cm2,超声时间为0.5小时,活化工序的干燥温度为350℃,干燥时间为5.5小时,制得催化剂-2。实施例3:以催化剂-3的总质量为基准,催化剂-3活性组分的质量含量设计值为20wt%(其中,氧化钴为3wt%,氧化钼为14wt%,氧化镍为3wt%),催化剂载体为tio2-γ-al2o3-sio2,则催化剂-3的活性组分的质量含量≤20%,采用一段浸渍后活化的工序对催化剂进行处理,一段浸渍阶段的超声波频率为80khz,超声波声强为0.6w/cm2,超声时间为1.0小时,活化工序的干燥温度为380℃,干燥时间为6.0小时,制得催化剂-3。实施例4:以催化剂-4的总质量为基准,催化剂-4活性组分的质量含量设计值为24wt%(其中,氧化钨为19wt%,氧化镍为5wt%),催化剂载体为γ-氧化铝与介孔分子筛复合,则催化剂-4的活性组分的质量含量>20%,采用一段浸渍、一段干燥再一段分散强化后活化的工序对催化剂进行处理。一段浸渍阶段的超声波频率为90khz,超声波声强为0.8w/cm2,超声时间为1.0小时,一段干燥温度为120℃,一段干燥时间为4小时。分散剂采用柠檬酸配制,分散剂溶液中柠檬酸的浓度为0.012g/ml,一段分散时超声波频率为20khz,超声波声强为0.2w/cm2,超声时间为0.25小时,活化工序的干燥温度为320℃,干燥时间为4.0小时,制得催化剂-4。实施例5:以催化剂-5的总质量为基准,催化剂-5活性组分的质量含量设计值为28wt%(其中,氧化钨为24wt%,氧化镍为4wt%),催化剂载体为sio2-γ-氧化铝,则催化剂-5的活性组分的质量含量>20%,采用一段浸渍、一段干燥再一段分散强化后活化的工序对催化剂进行处理。一段浸渍阶段的超声波频率为120khz,超声波声强为0.9w/cm2,超声时间为2.0小时,一段干燥温度为150℃,一段干燥时间为5小时。分散剂采用乙二胺四乙酸与草酸1:1配制,分散剂溶液的浓度为0.021g/ml,一段分散时超声波频率为40khz,超声波声强为0.3w/cm2,超声时间为0.5小时,活化工序的干燥温度为390℃,干燥时间为5.0小时,制得催化剂-5。实施例6:以催化剂-6的总质量为基准,催化剂-6活性组分的质量含量设计值为32wt%(其中,氧化钨为19wt%,氧化钼为8wt%,氧化镍为5wt%),催化剂载体为sio2-γ-氧化铝,则催化剂-6的活性组分的质量含量>20%,采用一段浸渍、一段干燥再一段分散强化后活化的工序对催化剂进行处理。一段浸渍阶段的超声波频率为150khz,超声波声强为1.0w/cm2,超声时间为3.0小时,一段干燥温度为170℃,一段干燥时间为8小时。分散剂采用柠檬酸与酒石酸1:1配制,分散剂溶液的浓度为0.032g/ml,一段分散时超声波频率为50khz,超声波声强为0.4w/cm2,超声时间为1.0小时,活化工序的干燥温度为430℃,干燥时间为6.0小时,制得催化剂-6。对比例1:与实施例2进行对比,以催化剂-d1的总质量为基准,催化剂-d1活性组分的质量含量设计值为18wt%(其中,三氧化钼为15wt%,氧化镍为3wt%),催化剂载体为γ-氧化铝,采用等体积浸渍(浸渍4小时,静置8小时),然后干燥活化,干燥温度为150℃,干燥时间为4小时,活化温度为500℃,活化时间为4小时,得到催化剂-d1。对比例2:与实施例6进行对比,以催化剂-d2的总质量为基准,催化剂-d2活性组分的质量含量设计值为32wt%(其中,氧化钨为19wt%,氧化钼为8wt%,氧化镍为5wt%),催化剂载体为sio2-γ-氧化铝,采用等体积浸渍(浸渍4小时,养生8小时),然后进行干燥活化,干燥温度为150℃,干燥时间为4小时,活化温度为500℃,活化时间为4小时,得到催化剂-d2。实施例7本实施例将实施例2、实施例6、对比例1、对比例2得到的催化剂进行对比加氢评价,采用的装置为200ml小型加氢评价装置。反应器中装入催化剂200ml,在氢气气氛下逐渐升温,升温至370℃,用含2.0%cs2的煤油对催化剂进行预硫化,硫化时间40h。原料油为直馏柴油与催化柴油质量比1:1,其中硫含量7000μg/g,氮含量760μg/g。反应条件为:压力6.4mpa,温度:360℃,空速:1.5h-1,氢油体积比:400:1。对比评价结果见表1。表1催化剂在加氢脱硫反应中的性能比较项目催化剂-2催化剂-6催化剂-d1催化剂-d2相对脱硫活性124130100100活性提高,%2430--活性用相对活性表示,即以相应未处理催化剂(如对比例1或对比例2催化剂)运转200小时的活性为100,本发明催化剂与之比较所得的活性表示发明催化剂的相对活性。相对脱硫活性按下列公式计算:相对脱硫活性=100×[(1/sp)0.65-(1/sf)0.65]/[(1/spr)0.65-(1/sfr)0.65]式中sfr、spr分别表示对比例催化剂所用柴油馏分和经对比例催化剂加氢处理后产物的含硫浓度,sf、sp分别表示本发明实施例催化剂所用柴油馏分和经本发明实施例催化剂加氢处理后的产物含硫浓度。程序升温还原(tpr)表征采用康塔仪器公司生产的autosorb-1化学吸附仪,载气为he。对实施例2和对比例1,实施例6和对比例2催化剂进行程序升温还原,结果如图1和图2所示。负载型催化剂上的金属组分大多是以氧化态的形式存在,每一种纯的金属氧化物都具有其特定的还原温度。当金属与载体结合并焙烧后,由于金属与载体间发生的相互作用,其还原温度与纯金属氧化物相比就可能发生变化。当多种金属同时负载在载体表面时,由于金属间还会发生相互作用或是金属氧化物在还原前就有可能发生固相反应,形成金属簇,这时每种氧化物的特征还原温度也会发生变化。通过tpr谱图,可以对这些变化进行表征。对于负载型多金属催化剂,尤其是含贵金属的多金属催化剂,其表面金属负载量一般较低,而且分散度较高。在这种情况下,不仅xrd无法判定金属间是否形成了金属簇,而且xps因为灵敏度的限制也难以给出准确的结论。tpr灵敏度很高,能检测出只消耗8~10molh2的还原反应,因而可以准确的做出判断。tpr谱图的纵坐标代表氢消耗的速度,横坐标代表金属化合物的还原温度,峰的个数代表还原中心的数量,其曲线下的面积表示还原时氢气的消耗量。通过对tpr谱图中上述因素的考察和对比,不仅可以表征新鲜催化剂的还原性质,得到金属与载体相互作用的强弱、金属在载体上的存在状态,还可以判定多金属催化剂中助剂对金属与载体间相互作用的影响,金属组分间的相互作用,以及金属间是否发生了聚集反应。另外,通过再生催化剂与新鲜催化剂还原性质的对比,还可以推论催化剂的失活原因及确定合理的再生温度。通过对图1和图2分析可知,实施例2和6分别相对于对比例1和2,还原温度低,说明本发明的处理方法不但提高了活性金属的分散性,同时减弱了活性金属与载体间的相互强作用,有利于提高催化剂的加氢脱硫活性。当然,本发明还可有其它多种实施例,在不背离本发明精神及其实质的情况下,熟悉本领域的技术人员可根据本发明作出各种相应的改变和变形,但这些相应的改变和变形都应属于本发明权利要求的保护范围。当前第1页12